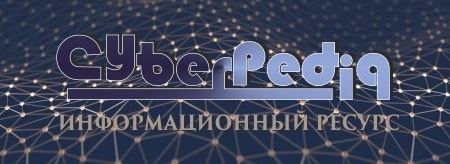
Типы оградительных сооружений в морском порту: По расположению оградительных сооружений в плане различают волноломы, обе оконечности...
Наброски и зарисовки растений, плодов, цветов: Освоить конструктивное построение структуры дерева через зарисовки отдельных деревьев, группы деревьев...
Топ:
Оценка эффективности инструментов коммуникационной политики: Внешние коммуникации - обмен информацией между организацией и её внешней средой...
Характеристика АТП и сварочно-жестяницкого участка: Транспорт в настоящее время является одной из важнейших отраслей народного хозяйства...
Интересное:
Берегоукрепление оползневых склонов: На прибрежных склонах основной причиной развития оползневых процессов является подмыв водами рек естественных склонов...
Финансовый рынок и его значение в управлении денежными потоками на современном этапе: любому предприятию для расширения производства и увеличения прибыли нужны...
Лечение прогрессирующих форм рака: Одним из наиболее важных достижений экспериментальной химиотерапии опухолей, начатой в 60-х и реализованной в 70-х годах, является...
Дисциплины:
![]() |
![]() |
5.00
из
|
Заказать работу |
|
|
Термической обработкой называют процесс обработки изделий из металлов и сплавов путем теплового воздействия с целью изменить их структуру и свойства в заданном направлении. Наиболее широко термическая обработка применяется при изготовлении деталей из стали.
Основоположником теории и разработки рациональных методов термической обработки стали является русский учёный Д.К.Чернов. Приоритет в создании многих методов термической обработки сплавов принадлежит русским учёным.
На результат термической обработки влияют время (скорость) и температура нагрева, время (продолжительность) выдержки и время (скорость) охлаждения.
Таким образом основными факторами термической обработки является температура и время. Поэтому процесс термической обработки обычно изображают в виде графика в координатах температура – время (рис. 11.1). Если термическая обработка состоит только из одной операции, то она называется простой (рис. 11.1, а), а если из нескольких операций — сложной (рис. 11.1, б)
Рис. 11.1 Схема термической обработки;
а – простая; б – сложная
Возможность упрочнения сталей путём термической обработки обусловлена наличием аллотропических превращений в твёрдом состоянии. Охлаждая аустенит с различными скоростями и вызывая тем самым различную степень переохлаждения, можно получить продукты распада аустенита, резко отличающиеся по строению и свойствам.
|
Наглядное представление о распаде переохлажденного аустенита дает диаграмма его изотермического превращения (рис. 11.2).
Кривая 1 графика соответствует началу распада аустенита при различных степенях переохлаждения; левее ее находится переохлажденный аустенит (область А). Кривая 2 показывает окончание процесса распада аустенита на ферритоцементитную смесь (область П). Горизонтальная прямая МН характеризует начало, а прямая МК — конец бездиффузионного превращения аустенита в мартенсит.
На диаграмме показаны кривые скоростей охлаждения стали. Малая скорость V1 охлаждения приводит к образованию грубой смеси феррита и цементита, перлита с твердостью HRC 10. Чем выше скорость охлаждения, тем более мелкодисперсна образующаяся ферритоцементитная смесь.
Рис. 11.2. Диаграмма изотермического
превращения аустенита
Сорбит (первая закалочная структура), получающийся при скорости охлаждения стали V2, представляет собой смесь феррита и цементита; он отличается от перлита более тонкодисперсным строением, твердость сорбита НRС 20. Стали с сорбитной структурой износостойкие, используются для изготовления нагруженных изделий.
Троостит (вторая закалочная структура) получается при скорости охлаждения V3, в результате распада переохлажденного аустенита при 500—550 "С, обладает значительной упругостью; представляет собой тонкодисперсную смесь феррита и цементита. Твердость трoостита составляет НRС 30.
Сталь со структурой троостита отличается высокими значениями прочности и упругости. Ее используют главным образом для изготовления пружин и рессор.
Превращение аустенита в мартенсит происходит при очень быстром охлаждении (V5 > VKP). При этом фиксируется типичная для мартенсита игольчатая структура. Он представляет собой пересыщенный твердый раствор углерода в α-железе.
Мартенсит — твердая и хрупкая структура; твердость его составляет НRС 62—66.
|
При скорости охлаждения V4 структура стали состоит из троостита и мартенсита.
Рис. 11.3.
Верхний ряд
Структуры (×1000) мартенсита
а – пластина в плоскости шлифа; б – мартенситные иглы
Нижний ряд
Структуры (× 7500) перлита (а), сорбита (б), и троостита (в)
Вопросы для повторения и закрепления:
1. Что называется термической обработкой металла?
2. Какие металлы подвергаются термообработке?
3. Какие основные условия получения закалочных структур: сорбита, троостита и мартенсита?
Отжиг
Отжигом называется процесс термической обработки, заключающийся в нагреве стали до определенной температуры, выдержке и последующем, как правило, медленном охлаждении (в печи) с целью получения более равновесной структуры.
Для отжига применяют камерные и толкательные печи, а также специальные агрегаты.
Отжиг первого рода. Это отжиг, при котором, как правило, не
происходит фазовых превращений (перекристаллизации), а если они имеют место, то не оказывают влияния на конечные результаты.
Различают следующие разновидности отжига первого рода: гомогенизационный, рекристаллизационный и уменьшающий напряжения.
Гомогенизационный отжиг, или гомогенизация, применяется для, выравнивания химической неоднородности (за счет диффузии) зерен твердого раствора, т. е. уменьшения микроликвации в фасонных отливках и в слитках главным образом из легированной стали.
В процессе гомогенизации слитки нагревают до 1100…1200° С, выдерживают при этой температуре 8…15 ч, а затем медленно охлаждают до 200…250°С. Продолжительность отжига 80…110ч.
Рекристаллизационному отжигу подвергают сталь, деформированную в холодном состоянии. Наклеп может оказаться столь большим, что сталь становится мало пластичной и дальнейшая деформация становится невозможной. Для возвращения стали пластичности и возможности дальнейшей деформации изделия проводят рекристаллизационный отжиг.
При нагреве холоднодеформированной (наклепанной) стали до температуры 400…450°С изменений в строении стали не происходит, механические свойства изменяются незначительно и только снимается большая часть внутренних напряжений. При дальнейшем нагреве механические свойства стали резко изменяются: твердость и прочность понижаются, а пластичность повышается. Это происходит в результате изменения строения стали. Вытянутые в результате деформации зерна становятся равноосными.
|
Рекристаллизация начинается с появления зародышей на границах деформированных зерен. В дальнейшем зародыши растут за счет деформированных зерен, в связи с чем происходит образование новых зерен, пока деформированных зерен совсем не останется
Под температурой рекристаллизации подразумевается температура, при которой в металлах, подвергнутых деформации в холодном состоянии, начинается образование новых зерен.
А. А. Бочвар установил зависимость между температурой рекристаллизации и температурой плавления чистых металлов:
Т РЕКР ═ 0,4 ТПЛ,
где Т РЕКР и ТПЛ — соответственно температуры рекристаллизации и плавления в кельвинах по термодинамической шкале.
Температуры рекристаллизации для некоторых металлов таковы:
Молибден............900°С Медь..........270°С.
Железо..........450°С Свинец........... 30°С
В связи с тем что при температуре рекристаллизации процесс образования новых зерен происходит очень медленно, для ускорения процесса холоднодеформированные металлы и сплавы нагревают до более высокой температуры, например углеродистую сталь до 600…700°С, медь до 500…700°С. Эти температуры и являются температурами рекристаллизационного отжига.
В зависимости от степени деформации размер зерна стали после рекристаллизации получается различный. При определенной степени деформации (для стали 7…15 %) после рекристаллизации получаются очень большие зерна. Такая степень деформации называется критической степенью деформации.
Во избежание сильного роста зерна при рекристаллизации деформацию стали заканчивают со степенью обжатия, больше чем критическая степень деформации, или проводят отжиг с полной фазовой перекристаллизацией.
Отжиг, уменьшающий напряжения. Это нагрев стали до температуры 200…700°С (чаще до 350…600°С) и последующее охлаждение
с целью уменьшения внутренних напряжений после технологических операций (литье, сварка, обработка резанием и др.).
|
Отжиг второго рода. Это отжиг, при котором фазовые превращения (перекристаллизация) определяют его целевое назначение. Различают следующие разновидности отжига второго рода: полный, неполный, изотермический, нормализационный (нормализация).
Полному отжигу подвергают доэвтектоидеую сталь с целью создания мелкозернистой структуры, понижения твердости и повышения пластичности, снятия внутренних напряжений.
При полном отжиге дозвтектоидную сталь нагревают до температуры на 20—30°С выше критической точки Ас3, т. е. на 20…30 °0 выше линии диаграммы GS железо—цементит (см. рис. 7.1).
Рис. 11.4. Микроструктура доэвтектоидной стали (× 500)
а – до отжига; б – после отжига
При нагреве до такой температуры крупная исходная ферритно-перлитная структура превращается в мелкую структуру аустенита. При последующем медленном охлаждении (в печи со скоростью 100…200°С в час до 500° С и далее на воздухе) из мелкозернистого аустенита образуется мелкая ферритно-перлитная структура (рис. 12.4). При полном отжиге происходит измельчение ферритно-перлитных зерен доэвтектоидной стали.
Заэвтектоидную сталь полному отжигу с нагревом выше критической точки Аст (линия SE на рис. 7.1) не подвергают, так как при медленном охлаждении цементит располагается в виде сетки по границам зерен перлита, ухудшая механические и другие свойства.
Неполному отжигу подвергают заэвтектоидную и. эвтектоидную сталь с целью превращения пластинчатого перлита и сетки цементита в структуру зернистого перлита. Заэвтектоидная сталь со структурой зернистого перлита обладает лучшей обрабатываемостью резанием благодаря более низкой твердости. (Для стали с зернистым перлитом твердость НВ 160…180, для стали с пластинчатым перлитом— НВ 180…250.)
Для получения зернистого перлита заэвтектоидную сталь нагревают до температуры немного, выше точки Ас1 (см. рис. 7.1) до 740…780°С. При нагреве до такой температуры происходит превращение в аустенит только перлита, а цементит остается и образуется структура цементит + аустенит. При последующем медленном охлаждении (в печи со скоростью 20…60°С в час до 700…650°С с дальнейшим охлаждением на воздухе) из аустенита образуется ферритно-цементитная структура с зернистой формой цементита — зернистый перлит (рис. 11.5).
В связи с тем что при этом виде отжига получается зернистая (сфероидальная) форма цементита, этот отжиг называют сфероидизирующим,
Для облегчения образования зернистого перлита нагрев (до 740…780°С) и: охлаждение (до 700…650°С) повторяют несколько раз. Такой отжиг, называют маятниковым или циклическим. При этом образовавшиеся зерна цементита во время первого охлаждения являются дополнительными центрами кристаллизации при втором охлаждении и т. д.
|
Рис. 11.5. Микроструктура перлита (× 1000)
а – пластинчатый; б, в – частично превратившийся в зернистый; в – зернистый
Доэвтектоидные стали неполному отжигу подвергают редко. Это объясняется тем, что в связи с неполной перекристаллизацией (только одного перлита) не происходит измельчения всей структуры (феррит не подвергается перекристаллизации), и в результате структура, и свойства стали получаются хуже, чем после полного отжига. Для доэвтектоидных сталей неполный отжиг применяют для улучшения обрабатываемости резанием благодаря снижению твердости.
Изотермический отжиг. Характерной особенностью изотермического отжига является образование ферритно-перлитной структуры из аустенита при постоянной температуре, а не при охлаждении, как при полном отжиге. Поэтому в отличие от полного отжига доэвтектоидную сталь, например, нагревают до температуры Ас3 + (20…30о С) и после выдержки быстро охлаждают до температуры немного ниже критической точки Ar1 (до 700…680°С). При этой температуре сталь выдерживают в течение времени, необходимого для полного распада аустенита и образования ферритно-перлитной структуры. Затем сталь охлаждают на воздухе.
Изотермический отжиг имеет преимущества по сравнению с полным отжигом: сокращается время отжига и получается более однородная структура (но только при обработке малых садок металла).
Нормализационный отжиг (нормализация) заключается в нагреве до температуры выше точки Ас3 для доэвтектоидной или точки Аст для заэвтектоидной стали с последующим охлаждением на воздухе.
При нагреве до температуры нормализации низкоуглеродистых сталей происходят те же процессы, что и при полном отжиге, т. е. измельчение зерен. Но, кроме того, вследствие более быстрого охлаждения и получающегося при этом переохлаждения строение перлита получается более тонким (дисперсным), а его количество большим. Механические свойства при этом оказываются более высокими.
Нормализация по сравнению с полным и неполным отжигом — более экономичная операция, так как не требует охлаждения вместе с печью. В связи с указанными преимуществами нормализация получила широкое применение вместо полного отжига низкоуглеродистых и даже среднеуглеродистых сталей. Нормализация применяется также для устранения цементитной сетки в заэвтектоидных сталях. При нагреве заэвтектоидной стали выше критической точки Аст образуется структура аустенита. Если после такого нагрева при медленном охлаждении (при отжиге) цементит выделяется в виде сетки, то ускоренное охлаждение на воздухе (нормализация) препятствует выделению цементита по границам зерен и образуется мелкая ферритно-цементитная смесь.
Вопросы для повторения и закрепления:
1. Что называется отжигом?
2. Какова характерная особенность отжига первого рода?
3. Для каких сталей применяется полный отжиг?
4. Чем принципиально отличается отжиг от нормализации?
Закалка
3акалкой называют процесс термической обработки, состоящий в нагреве стали до оптимальной температуры, выдержке и последующем быстром охлаждении с целью получения неравновесной структуры. В результате закалки повышаются прочность и. твердость и понижается пластичность стали. Основные параметры закалки — температура нагрева и скорость охлаждения.
Температуру закалки для углеродистых сталей можно определить по левой нижней части диаграммы состояния железо—цементит (рис. 7.1).
Доэвтектоидные стали при закалке нагревают до температуры на 30…50°С выше точки Ас3, т. е. выше линии GS. При таком нагреве исходная ферритно-перлитная структура превращается в аустенит, а после охлаждения с высокой скоростью (больше критической) образуется мартенсит.
Заэвтектоидные стали нагревают до температуры на 30…50°С выше точки Ac1 т. е. выше линии SK. Так как эта линия соответствует температуре 727°С, для заэвтектоидной стали можно указать температуру нагрева для закалки в интервале 760…790°С. При таком нагреве перлит полностью превращается в аустенит, а часть вторичного цементита остается нерастворенной — структура состоит из аустенита и цементита. После быстрого охлаждения аустенит превращается в мартенсит. Структура закаленной стали состоит из мартенсита и цементита. Наличие цементита в структуре закаленной заэвтектоидиой стали повышает твердость и износостойкость стали.
Время нагрева. Для экономии времени нагрев стали необходимо вести по возможности быстро, однако, не допуская образования дефектов. Если, например, детали нагревать, сразу помещая их в печь, нагретую до температуры закалки, то возникают значительные внутренние напряжения и в сложных по форме деталях возможно образование трещин. Поэтому детали сложной формы перед помещением в печь для нагрева под закалку предварительно подогревают или температуру в печи вместе с помещенными в нее заранее деталями постепенно повышают.
Общая продолжительность нагрева, т. е. общее время пребывания деталей в нагревающей среде, состоит из двух слагаемых: времени нагрева до заданной температуры и времени выдержки при этой температуре. Как говорилось выше, время нагрева деталей до заданной температуры зависит от температуры, конфигурации деталей, мощности и типа печи, размера садки, способа укладки деталей и других факторов. Время выдержки выбирают так, чтобы полностью завершились фазовые превращения.
Общая продолжительность нагрева в электропечах составляет 1,5…2 мин на 1мм размера сечения.
Скорость охлаждения стали, нагретой до температуры закалки, оказывает решающее влияние на результат закалки.
Поскольку быстрое охлаждение необходимо только в интервале наименьшей устойчивости аустенита, а при дальнейшем понижении температуры, особенно в мартенситном интервале, быстрое охлаждение не только не нужно, но и нежелательно, наилучшей закалочной средой является та, которая способствует быстрому охлаждению от температуры закалки до 200…300°С, а далее в интервале температур мартенситного превращения обеспечивает медленное охлаждение.
Наиболее распространенными закалочными средами являются вода, водные растворы солей, щелочей, масло, воздух, расплавленные соли.
При охлаждении в воде и масле, температура кипения которых ниже температуры охлаждаемых в них деталей, скорость охлаждения различна в начальном (стадия пленочного кипения), среднем (стадия пузырчатого кипения) и конечном (стадия конвективного теплообмена) периодах охлаждения.
Стадия пленочного кипения характеризуется образованием вокруг детали паровой пленки, отделяющей раскаленную поверхность от всей массы жидкости. Поэтому скорость охлаждения на данной стадии сравнительно невелика.
Стадия пузырчатого кипения наступает при более низких температурах охлаждаемой поверхности, когда паровая пленка разрушается, создается непосредственный контакт жидкости с деталью; при кипении жидкости возникают многочисленные пузырьки пара, которые, отрываясь, уносят значительное количество теплоты, в связи с чем охлаждение происходит с большой скоростью.
Стадия конвективного теплообмена наступает, когда температура поверхности становится ниже температуры кипения жидкости. Интенсивность теплоотдачи в этой стадии низка и охлаждение протекает с небольшой скоростью.
Вода охлаждает в 6 раз быстрее при 550…650°С и в 28 раз быстрее при 200оС, чем масло. Поэтому вода применяется для охлаждения сталей с большой критической скоростью закалки (углеродистых сталей), а в масле охлаждают стали с малой критической, скоростью закалки (детали малых сечений из легированных или высокоуглеродистых сталей).
Основным недостатком воды как охлаждающей среды является высокая скорость охлаждения при температурах образования мартенсита, что приводит к возникновению больших структурных напряжений и создает опасность возникновения трещин. При нагреве воды ее закаливающая способность снижается в области высоких температур (550…650°С), а скорость охлаждения в области температур мартенситного превращения остается высокой. Поэтому охлаждение в горячей воде не уменьшает возможность образования трещин. Добавление к воде солей, щелочей увеличивает ее закаливающую способность в связи с расширением интервала пузырчатого кипения (почти полностью исключается стадия пленочного кипения). Кроме того, эти растворы при низких температурах в мартенситном интервале охлаждают медленнее, чем вода.
Как указано выше, масло охлаждает значительно медленнее, чем вода. Но зато благодаря повышенной температуре кипения (250…300°С) и соответственно более высокой температуре перехода от пузырчатого кипения к конвективному теплообмену масло обладает небольшой скоростью охлаждения в области температур мартенситного превращения, поэтому при охлаждении в масле опасность образования трещин резко уменьшается. Преимуществом масла является также то, что закаливающая способность не изменяется с повышением температуры масла (до 150…200°С). Недостатки масла — это легкая воспламеняемость, пригорание к поверхности детали; под влиянием высокой температуры охлаждаемых деталей масло постепенно начинает густеть и закаливающая способность его понижается.
Вопросы для повторения и закрепления:
1. Что называется закалкой?
2. С какой целью производится закалка стали?
3. Какие операции включает в себя технологический процесс закалки металла?
Отпуск
Отпуск — нагрев до температуры ниже точки Ас 1с последующим охлаждением с заданной скоростью — проводят для снижения или полного устранения внутренних напряжений, уменьшения хрупкости закаленной стали и получения требуемой структуры и механических свойств. В зависимости от температуры отпуск делят на низкий, средний и высокий.
Низкий отпуск — при 120…250°С на отпущенный мартенсит применяют для термообработки режущего и измерительного инструмента, деталей подшипников.
Средний отпуск — при 350…450°С на троостит отпуска проводят при изготовлении пружин рессор, штампов.
Высокому отпуску — при 450…650 °С на сорбит отпуска, называемому также улучшением, часто подвергают детали из среднеуглеродистой конструкционной стали, например валы, оси, шатуны, зубчатые колеса и др.
Вопросы для повторения и закрепления:
1. С какой целью проводится отпуск металла после закалки?
2. Какие виды отпуска существуют и какие структуры получаются после их применения?
Задание:
1.Составить план ответа на темы «Основы термической обработки металла» и «Отжиг»
2.Составить план ответа на темы «Закалка» и «Отпуск»
|
|
Семя – орган полового размножения и расселения растений: наружи у семян имеется плотный покров – кожура...
Таксономические единицы (категории) растений: Каждая система классификации состоит из определённых соподчиненных друг другу...
Автоматическое растормаживание колес: Тормозные устройства колес предназначены для уменьшения длины пробега и улучшения маневрирования ВС при...
Типы оградительных сооружений в морском порту: По расположению оградительных сооружений в плане различают волноломы, обе оконечности...
© cyberpedia.su 2017-2024 - Не является автором материалов. Исключительное право сохранено за автором текста.
Если вы не хотите, чтобы данный материал был у нас на сайте, перейдите по ссылке: Нарушение авторских прав. Мы поможем в написании вашей работы!