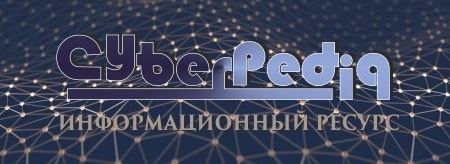
История развития хранилищ для нефти: Первые склады нефти появились в XVII веке. Они представляли собой землянные ямы-амбара глубиной 4…5 м...
Папиллярные узоры пальцев рук - маркер спортивных способностей: дерматоглифические признаки формируются на 3-5 месяце беременности, не изменяются в течение жизни...
Топ:
Техника безопасности при работе на пароконвектомате: К обслуживанию пароконвектомата допускаются лица, прошедшие технический минимум по эксплуатации оборудования...
Эволюция кровеносной системы позвоночных животных: Биологическая эволюция – необратимый процесс исторического развития живой природы...
Проблема типологии научных революций: Глобальные научные революции и типы научной рациональности...
Интересное:
Распространение рака на другие отдаленные от желудка органы: Характерных симптомов рака желудка не существует. Выраженные симптомы появляются, когда опухоль...
Инженерная защита территорий, зданий и сооружений от опасных геологических процессов: Изучение оползневых явлений, оценка устойчивости склонов и проектирование противооползневых сооружений — актуальнейшие задачи, стоящие перед отечественными...
Средства для ингаляционного наркоза: Наркоз наступает в результате вдыхания (ингаляции) средств, которое осуществляют или с помощью маски...
Дисциплины:
![]() |
![]() |
5.00
из
|
Заказать работу |
|
|
Изобретателем конвертерного способа получения стали считают англичанина Г. Бессемера, впервые предложившего и осуществившего в 1854—1856гг. получение стали без расхода топлива, путем продувки воздуха через расплавленный чугун. Предложенный им способ производства стали совершенствовался, видоизменялся другими изобретателями и производственными коллективами. Так возникли и получили применение томасовский процесс, русский процесс и многие другие. В настоящее время получили широкое распространение конвертерные способы, где для продувки вместо воздуха применяют кислород. Конвертером принято называть большую стальную реторту, футерованную огнеупором. Вместимость современных конвертеров достигает 250…400 т. Конвертер имеет цилиндрическую часть, легко заменяемое днище и конусообразную горловину. Цилиндрическая часть конвертера крепится в литом стальном кольце с двумя цапфами, которыми оно опирается на подшипники двух стоек. Поэтому конвертер может поворачиваться вокруг оси цапф, что необходимо для его обслуживания (заливки исходного чугуна, взятия проб, выпуска готовой стали и т. д.). Конвертеры для томассовского и русского процессов принципиально мало отличаются от бессемеровского, хотя и имеют отдельные конструктивные изменения. Так, например, в ряде литейных цехов нередко применяют конвертеры малой вместимости (1,5…2,5 т) с боковым подводом воздуха. Перед применявшимися ранее способами получения стали бессемеровский способ имел два неоспоримых преимущества — очень высокую производительность, отсутствие потребности в топливе. Недостатком бессемеровского процесса является ограниченная гамма чугунов, которые могут перерабатываться этим способом, так как при динасовой футеровке не удается удалить из металла такие вредные примеси, как серу и фосфор, в том случае, если они содержатся в чугуне. Кроме того, получаемая в конвертере сталь хрупка из-за насыщения ее азотом, содержащимся в воздухе.
|
Бессемеровский процесс в 1878г. развил английский металлург С. Дж. Томас. Он внедрил в практику футеровку конвертеров доломитом. Такая футеровка позволяла удалять из чугуна фосфор и частично серу.
Томасовский процесс не устранил всех недостатков бессемеровского процесса. Более того, в металле оказалось повышенным содержание кислорода и азота и он больше загрязнен шлаковыми включениями, поэтому качество металла при томасовском процессе было еще ниже. Футеровка томасовского конвертера редко выдерживает более 400 плавок.
Конвертерное производство стали постоянно совершенствовалось. Мастера и инженеры уральских заводов разработали оригинальный способ конвертерной переработки чугунов с пониженным содержанием кремния и около 1,5 % марганца. Этот способ затем нашел последователей на многих западноевропейских заводах и получил название русского бессемерования (русский процесс).
Важным этапом, обеспечившим конвертерному способу повсеместное широкое применение, явилась замена воздушного дутья кислородным. Предложения о такой замене поступали давно и возможность применения кислорода для этой цели успешно изучались многими советскими учеными (К. Г. Трубиным, Н. И. Мозговым и др).
В настоящее время имеет место широкое практическое решение этой проблемы.
В ряде стран построены конвертерные цехи, оборудованные 100- и 250-тонными конвертерами, работающими на техническом кислороде.
В современном кислородно-конвертер ном способе получения стали на большинстве заводов используют глуходонные конвертеры 6 (рис. 5.1).
Футеруют эти конвертеры обычно смолодоломитовым или магнезитохромитовым кирпичом. Кислород вдувают в конвертер через вертикальную трубчатую водоохлаждаемую фурму 2, опускаемую в горловину конвертера 3, но не доходящую до уровня металла на 1200—2000 мм.
|
Таким образом, кислород 5 вдувается не под зеркало металла (как воздух в старых конвертерных процессах), а подается к поверхности залитого в конвертер металла. Однако и при таком способе подвода кислорода процесс идет с большим выделением теплоты, что дает возможность перерабатывать чугуны с различным содержанием примесей, а также вводить в конвертер не только жидкий металл, но и добавлять к нему скрап (металлический лом) и железную руду (количество скрапа до 30 % от массы жидкого металла).
Началом очередного цикла в кислородном конвертере является завалка в него лома и других металлических отходов, а иногда и железной руды. Затем в предварительно наклоненный конвертер начинают заливать жидким чугуном, подвозимым из миксера в чугуновозных ковшах. После того как металл займет ~1/5 объема конвертера, его ставят в вертикальное положение. После этого загружают известь, необходимую для связывания фосфора, содержащегося в чугуне и ломе.
В конвертер опускают водоохлаждаемую фурму и подают технический кислород. В конвертере начинается интенсивный процесс окисления металла кислородом с выделением теплоты по реакции
2[Fе] + О2 = 2(FеО) + Q
(У металлургов при описании плавки принято химические элементы и соединения, находящиеся в металле, заключать в квадратные скобки, а находящиеся в шлаке — в круглые.)
Окисляются и примеси, но окисление их возможно не только кислородом, но и закисью железа FеО по реакциям:
. [Si] + O2 = (SiO2) + Q
. [Мп] + (FеО) = [Fе] + (МпО) + Q
2[Р] + 5(FеО) = 5[Fе] + (Р205) + Q
2[С] + О2 = 2СО − Q
Все эти реакции протекают в конвертере с кислородным дутьем одновременно, причем последняя реакция способствует лучшему перемешиванию нижних слоёв металла.
После 15…16-минутной продувки поднимают фурму, наклоняют конвертер, берут пробу металла на экспресс-анализ. Затем скачивают большую часть шлака, на что уходит 7…8 мин; за это время экспресс-анализом определяются основные параметры стали и конвертер вновь ставят в вертикальное положение, опускают фурму и вторично продувают кислородом в течение нескольких минут. Время продувки зависит от данных анализа и заданной марки стали.
В это время продолжаются реакции окисления и интенсивно идут реакции шлакообразования
|
SiO2 + 2СаО = 2СаО• SiO2
Р2O5 + 4СаО = 4СаО• P2O5
В конце вторичной продувки в конвертер вводят раскислители. Раскисление ведут марганцем и кремнием, а точнее их ферросплавами, так как их окислы образуют с окислами железа жидкую шлаковую фазу, помогающую вывести продукты раскисления из металла. Часть раскислителей вводят в конвертер за несколько минут до разливки. | Завершается раскисление обычно в разливочном ковше.
Общий расход технического кислорода на получение 1 т стали в конвертере составляет 50…60 м3, что незначительно превышает теоретически необходимое количество.
Затем фурму вновь поднимают, конвертер наклоняют, берут контрольную пробу металла, термопарой измеряют его температуру, после чего сталь выпускают через боковую фурму 1 в разливочный ковш; после слива металла скачивают оставшийся шлак и заделывают выпускное отверстие. Весь технологический цикл плавки занимает 50…60 мин, а продолжительность продувки кислородом составляет от 18 до 26 мин (рис. 5.2).Поворот конвертера, подъем и опускание водоохлаждаемой кислородной фурмы, загрузку сыпучих добавок и некоторые другие технологические операции осуществляют с пульта управления, расположенного на расстоянии нескольких десятков метров от конвертера. Определение продолжительности и режима дутья, времени взятия пробы и другие параметры плавки на ряде заводов определяют с помощью счетно-решающих устройств. Ведутся исследования по полной автоматизации всего конвертерного передела.
Порядок окисления примесей и последовательность технологических операций может существенно изменяться и отклоняться от вышеизложенного, в зависимости от состава исходных чугунов, характера флюса и металлических добавок (железная руда, стружка, металлический лом и др.).
Благодаря тому что окисление углерода и фосфора в кислородном конвертере идет одновременно, создается возможность остановить процесс на заданном содержании углерода и получать в нем довольно широкую гамму углеродистых сталей при достаточно низком к содержании фосфора и серы в металле, которые удаляются в этом в процессе в шлак с помощью извести.
|
Стали, более чистые по сере и фосфору, в кислородном конвертере удается получить потому, что более горячий ход плавки в таком конвертере позволяет иметь более известковые шлаки. Удаление серы, содержащейся в чугуне и стали, может протекать по следующей схеме:
[Fе] + [S] + (СаО) ↔ (FеО) + (СаS)
Чем больше извести в шлаке, тем больше равновесие реакции смещается вправо, т.е. тем больше серы переходит в шлак. Выпуск металла в современном конвертере проводится не через горловину 3, а через верхнюю летку 1, что также предохраняет металл от поглощения азота, так как вся поверхность стали в конвертере в это время закрыта слоем шлака.
Получение стали завершается ее раскислением, так как этот процесс носит окислительный характер, а окисление примесей всегда одновременно ведет к окислению железа и растворению в нем его закиси. В разных способах получения стали раскисление ведется различно.
Рис.5.2. Получение стали из чугуна в кислородном конвертере:
1 -завалка лома-3мин; 2 - заливка чугуна-5 мин; 3 - загрузка извести-1мин; 4 - продувка (первый период 16 мин, второй- 8 мин); 5 - выпуск стали- 5 мин, 6 - скачка шлака (после первой продувки- 8 мин; после выпуска стали – 3 мин)
Недостатком кислородно-конвертерного способа получения стали является большое пылеобразование, обусловленное обильным окислением и испарением железа. Это требует обязательного сооружения при конвертерах сложных и дорогих пылеочистительных установок.
Вопросы для повторения и закрепления:
1. В чём преимущество кислородного конвертера перед томассовским и бессемеровским способом получения стали?
2. Недостатки кислородно-конвертерного способа получения стали?
3. Цель и способы раскисления стали?
|
|
Механическое удерживание земляных масс: Механическое удерживание земляных масс на склоне обеспечивают контрфорсными сооружениями различных конструкций...
Адаптации растений и животных к жизни в горах: Большое значение для жизни организмов в горах имеют степень расчленения, крутизна и экспозиционные различия склонов...
Эмиссия газов от очистных сооружений канализации: В последние годы внимание мирового сообщества сосредоточено на экологических проблемах...
Общие условия выбора системы дренажа: Система дренажа выбирается в зависимости от характера защищаемого...
© cyberpedia.su 2017-2024 - Не является автором материалов. Исключительное право сохранено за автором текста.
Если вы не хотите, чтобы данный материал был у нас на сайте, перейдите по ссылке: Нарушение авторских прав. Мы поможем в написании вашей работы!