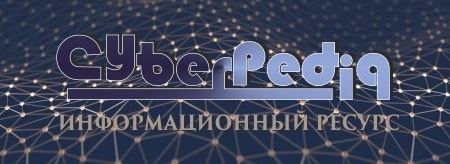
Адаптации растений и животных к жизни в горах: Большое значение для жизни организмов в горах имеют степень расчленения, крутизна и экспозиционные различия склонов...
Опора деревянной одностоечной и способы укрепление угловых опор: Опоры ВЛ - конструкции, предназначенные для поддерживания проводов на необходимой высоте над землей, водой...
Топ:
Процедура выполнения команд. Рабочий цикл процессора: Функционирование процессора в основном состоит из повторяющихся рабочих циклов, каждый из которых соответствует...
Особенности труда и отдыха в условиях низких температур: К работам при низких температурах на открытом воздухе и в не отапливаемых помещениях допускаются лица не моложе 18 лет, прошедшие...
Основы обеспечения единства измерений: Обеспечение единства измерений - деятельность метрологических служб, направленная на достижение...
Интересное:
Мероприятия для защиты от морозного пучения грунтов: Инженерная защита от морозного (криогенного) пучения грунтов необходима для легких малоэтажных зданий и других сооружений...
Принципы управления денежными потоками: одним из методов контроля за состоянием денежной наличности является...
Финансовый рынок и его значение в управлении денежными потоками на современном этапе: любому предприятию для расширения производства и увеличения прибыли нужны...
Дисциплины:
![]() |
![]() |
5.00
из
|
Заказать работу |
Газоэлектрическая резка заключается в использовании подогревающего действия электрической дуги, которая горит между электродом и разрезаемым изделием. Источником тепловой энергии во всех способах электрической резки служит электрический дуговой разряд, происходящий в газовом промежутке между электрическим или угольным электродами
Кислородно-дуговая резка применяется для резки углеродистых сталей и отличается от дуговой тем, что на нагретый до плавления металл подают струю технически чистого кислорода, которая интенсивно окисляет металл и удаляет из разреза образующие окислы. При сгорании металла в струе кислорода образуется дополнительное тепло, которое ускоряет процесс резки металла. В качестве электродов используют стальные трубки наружным диаметром 8 мм, длиной 340—400 мм
Для перехода от сварки к резке сварщику не нужно менять электрододержатель, электрод и режим. Может применяться как переменный, так и постоянный ток
Кислородно-дуговой резкой можно резать углеродистые, легированные, коррозионно-стойкие стали, чугун и цветные металлы. По чистоте получаемого реза он не уступает газокислородной, а по производительности в некоторых случаях превосходит ее.
К недостаткам этого процесса можно отнести:
высокие требования к подготовке водолаза-резчика;
значительный расход кислорода (0,2 - 2,5 м³ на 1 м реза;
частый выход резака из строя при плохой подготовке электрода или неплотном его контакте с токоподводящим элементом (образуется дуга между зажимной цангой и непокрытой частью электрода).
Воздушно-дуговая резка основана на расплавлении металла в месте реза теплом электрической дуги, горящей между угольным или графитизированным электродом и металлом, с непрерывным удалением жидкого металла струей сжатого воздуха
Простота, дешевизна и высокая производительность
Недостатком этого способа является науглероживание поверхностного слоя металла на кромках реза, высокий удельный расход электроэнергии, высокое напряжение холостого хода, создающее опасность при смене электрода, а также высокая стоимость источников питания постоянного тока
Удешевление способа воздушно-дуговой резки возможно при использовании переменного тока. Однако при резке на переменном токе с использованием обычных сварочных трансформаторов дуга часто сдувается воздушной струей и гаснет в момент перехода тока через нулевое значение
Плазма — это газ, состоящий из положительно и отрицательно заряженных частиц в таких пропорциях, что общий заряд равен нулю, т. е. плазма представляет собой смесь электрически нейтральных молекул газа и электрически заряженных частиц, электронов и положительных ионов. Наличие электрически заряженных частиц делает плазму чувствительной к воздействию электрических полей.
Плазма вследствие наличия в ней электрически заряженных частиц является электропроводной, и при действии электрических полей в плазме возникают электрические токи. Чем выше степень ионизации, тем выше электропроводность плазмы. Токи в ней отклоняются под действием магнитных полей. Ускорения, сообщаемые заряженным частицам действием электрических и магнитных полей путем соударения передаются нейтральным частицам газа, и весь объем плазмы получает направленное движение, образуя струю, поток или факел горячего газа.
Плазменно-дуговая резка основана на способности сжатой дуги глубоко проникать в металл, проплавляя его по линии реза дуговым разрядом. Под действием высокой температуры сжатой дуги газ, проходя через дуговой разряд, сильно ионизирует, образуется струя плазмы, которая удаляет расплавленный металл из места реза. Дуга возбуждается между разрезаемым металлом и неплавящимся вольфрамовым электродом, расположенным внутри головки резака. Дуговую газоразрядную плазму называют низкотемпературной (ее температура 5000— 20 000°С)
Электрическая дуга постоянного тока образуется между неплавящимся вольфрамовым электродом и разрезаемым металлом. Электрод расположен внутри медного охлаждаемого водой мундштука, в канал которого подается под давлением плазмообразующий газ: аргон, азот, водород или их смеси, воздух. Струя газа сжимает столб дуги, придавая ей вытянутую форму.
Для возбуждения дуги, горящей между электродом и металлом, используется вспомогательная (дежурная) дуга между электродом и мундштуком. Ток, обеспечивающий горение вспомогательной дуги, от сварочного генератора к мундштуку подводится через добавочное сопротивление. Для облегчения зажигания дуги и повышения устойчивости ее горения используется осциллятор.
Струя плазмы имеет высокую скорость истечения и оказывает механическое действие, удаляя из места реза расплавляемый ею металл. В металле образуется полость реза, по стенке которого опускается активное пятно дуги. При перемещении резака по направлению резки пятно остается на лобовой стенке реза и вместе со столбом плазменной дуги и факелом струи плазмы обеспечивает проплавление металла по всей толщине при одновременном удалении из полости реза расплавленного и испаренного металла.
Положительными свойствами процесса плазменно-дуговой резки являются: высокая скорость резки; малая зона теплового влияния на металл; отсутствие заметного коробления листов при резке; возможность сварки листов непосредственно после резки; сравнительная легкость механизации процесса резки. Наиболее экономична, резка алюминия и его сплавов, меди и высоколегированных сталей (нержавеющих)
Плазменная резка отличается от плазменно-дуговой резки тем, что разрезаемый металл не включен в цепь дуги и резка материала производится косвенной дугой, имеющей кинжалообразную форму.
Рабочий орган аппарата называется плазмотрон.
Постоянный ток от источника подводится: минус — к вольфрамовому электроду, конец которого заточен на конус, плюс — к формирующему дугу медному соплу. Под действием потока газа (аргона, азота, водорода или их смесей), продуваемого через мундштук, образуется кинжалообразный язык плазмы, используемой для проплавления разрезаемого материала. Мундштук и совмещенное с ним сопло охлаждаются водой. Установка для резки состоит из баллона с рабочим газом, источника постоянного тока, распределительного устройства с аппаратурой управления процессом и резака.
Плазменная резка преимущественно используется для резки металлов сравнительно небольшой толщины (3—5 мм) и неэлектропроводных материалов.
Преимущества
обрабатываются любые металлы — черные, цветные, тугоплавкие сплавы и т. д.
скорость резания малых и средних толщин в несколько раз выше скорости газопламенной резки
небольшой и локальный нагрев разрезаемой заготовки, исключающий ее тепловую деформацию
высокая чистота и качество поверхности разреза
безопасность процесса (нет необходимости в баллонах с сжатым кислородом, горючим газом и т. д.)
возможна сложная фигурная вырезка
отсутствие ограничений по геометрической форме.
Недостатки
Относительно скромная максимально допустимая толщина реза, которая даже у мощных аппаратов редко превышает 80-100 мм. В случае же с кислородной резкой максимально допустимая толщина реза для стали и чугуна может достигать 500 мм.
Довольно жесткие требования к отклонению от перпендикулярности реза. В зависимости от толщины детали угол отклонения не должен превышать 10-50°. При выходе за эти пределы наблюдается значительное расширение реза и, как одно из следствий, быстрый износ расходных материалов.
Сложность рабочего оборудования делает практически невозможным одновременное использование двух резаков, подключенных к одному аппарату, что с успехом применяется при резке штучным электродом.
Основные условия резки
1. Температура воспламенения металла в кислороде должна быть ниже температуры его плавления. Лучше всех металлов и сплавов этому требованию удовлетворяют низкоуглеродистые стали, температура воспламенения которых в кислороде около 1300°С, а температура плавления около 1500°С. Увеличение содержания углерода в стали сопровождается повышением температуры воспламенения в кислороде с понижением температуры плавления. Поэтому с увеличением содержания углерода кислородная резка сталей ухудшается.
2. Температура плавления окислов металлов, образующихся при резке, должна быть ниже температуры плавления самого металла, в противном случае тугоплавкие окислы не будут выдуваться струей режущего кислорода, что нарушит нормальный процесс резки. Этому условию не удовлетворяют высокохромистые стали и алюминий. При резке высокохромистых сталей образуются тугоплавкие окислы с температурой плавления 2000°С, а при резке алюминия — оксид с температурой плавления около 2050°С. Кислородная резка их невозможна без применения специальных флюсов.
3. Количество теплоты, которое выделяется при сгорании металла в кислороде, должно быть достаточно большим, чтобы поддерживать непрерывный процесс резки. При резке стали около 70% теплоты выделяется при сгорании металла в кислороде и только 30% общей теплоты поступает от подогревающего пламени резака.
4. Образующиеся при резке шлаки должны быть жидкотекучими и легко выдуваться из места реза.
5. Теплопроводность металлов и сплавов не должна быть слишком высокой, так как теплота, сообщаемая подогревающим пламенем и нагретым шлаком, будет интенсивно отводиться от места реза, вследствие чего процесс резки будет неустойчивым и в любой момент может прерваться.
6 Металл или сплав должен быть без пор и раковин, без шлаков и включений.
Папиллярные узоры пальцев рук - маркер спортивных способностей: дерматоглифические признаки формируются на 3-5 месяце беременности, не изменяются в течение жизни...
Архитектура электронного правительства: Единая архитектура – это методологический подход при создании системы управления государства, который строится...
Механическое удерживание земляных масс: Механическое удерживание земляных масс на склоне обеспечивают контрфорсными сооружениями различных конструкций...
Общие условия выбора системы дренажа: Система дренажа выбирается в зависимости от характера защищаемого...
© cyberpedia.su 2017-2024 - Не является автором материалов. Исключительное право сохранено за автором текста.
Если вы не хотите, чтобы данный материал был у нас на сайте, перейдите по ссылке: Нарушение авторских прав. Мы поможем в написании вашей работы!