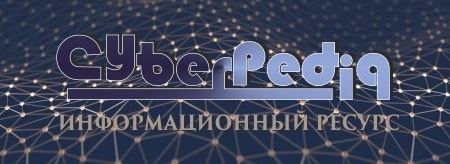
Опора деревянной одностоечной и способы укрепление угловых опор: Опоры ВЛ - конструкции, предназначенные для поддерживания проводов на необходимой высоте над землей, водой...
Индивидуальные и групповые автопоилки: для животных. Схемы и конструкции...
Топ:
Когда производится ограждение поезда, остановившегося на перегоне: Во всех случаях немедленно должно быть ограждено место препятствия для движения поездов на смежном пути двухпутного...
Определение места расположения распределительного центра: Фирма реализует продукцию на рынках сбыта и имеет постоянных поставщиков в разных регионах. Увеличение объема продаж...
Интересное:
Принципы управления денежными потоками: одним из методов контроля за состоянием денежной наличности является...
Средства для ингаляционного наркоза: Наркоз наступает в результате вдыхания (ингаляции) средств, которое осуществляют или с помощью маски...
Национальное богатство страны и его составляющие: для оценки элементов национального богатства используются...
Дисциплины:
![]() |
![]() |
5.00
из
|
Заказать работу |
|
|
Восстановление деталей, резерв экономии материальных ресурсов. Ремонт машин – объективная необходимость. Техническая возможность и экономическая целесообразность ремонта деталей, сборочных единиц и автомобилей.
Ремонт – совокупность управляемых мероприятий связанных с восстановлением свойств, утраченных системой в процессе эксплуатации.
Объективную потребность и необходимость проведения ремонта обуславливает ряд факторов, объединяемые в две группы:
· Технологические
· Экономические
Технологические факторы:
1. Неравномерность изнашивания агрегатов и механизмов машин, узлов и деталей агрегатов, рабочих поверхностей деталей и узлов.
2. Конструктивная прочность и износостойкость базовых дорогостоящих рамно-кузовных и картерно-блоковых деталей и узлов.
3. Организационно-технологические возможности ремонтных органов по восстановлению изношенных поверхностей деталей.
Экономические факторы:
1. Затраты на капитальный ремонт по машине составляет 40-60%, по агрегатам – 25-65%, по деталям – 15-70% от стоимости соответствующих вновь изготовленных изделий.
2. При изготовлении автомобилей, тракторов и др. специальных машин 65-80% затрат приходятся на материалы и комплектующие, при капитальном ремонте эти затраты 20-40%.
Сварка в среде водяного пара. Сущность способа, преимущества и недостатки способа.
1 — сопло горелки; 2 — карман для сбора конденсата
При сварке чугунных деталей в защитной среде водяного пара происходит интенсивное выгорание углерода в сварочной ванне и исключается возможность образования карбидов железа, что обеспечивает хорошую обрабатываемость и прочность сварного соединения. Непрерывный процесс горения дуги создает большой запас тепла в сварочной ванне, а это в свою очередь исключает образование закаленной прослойки в зоне сплавления, характерной для всех способов холодной сварки чугуна. При сварке в среде водяного пара повышается качество наплавки за счет выбора присадочного материала, режима сварки и предварительного подогрева детали. При больших объемах работ в 2—3 раза повышается производительность.
|
Технологический процесс газосварочных работ.
См. также вопрос 4.
Газовая сварка — сварка плавлением, при которой нагрев кромок соединяемых частей деталей производится пламенем газов, сжигаемых на выходе из горелки для газовой сварки. При газовой сварке заготовки 1 и присадочный материал 2 в виде прутка или проволоки расплавляют высокотемпературным пламенем 4 газовой горелки 3:
Газовое пламя чаще всего образуется в результате сгорания (окисления) горючих газов технически чистым кислородом (чистота не ниже 98,5%). В качестве горючих газов используют ацетилен, водород, метан, пропан, пропанобутановую смесь, бензин, осветительный керосин.
Способы резки металлов.
1)Газокислородная. Процесс газокислородной резки металла представляет из себя следующее: происходит нагрев металла в среде кислорода до температуры воспламенения металла, а затем расплавленный металл удаляется из зоны резки режущей струей кислорода.
2)Кислородно-флюсовая. Кислородно-флюсовая резка была разработана для резки материалов, которые плохо поддаются кислородной резке. К ним относятся чугун, легированные стали, цветные металлы и др. Кислородно-флюсовая резка отличается от обычной кислородной резки тем, что помимо подогревающего пламени и струи режущего кислорода в зону реза подается порошок флюса, который обеспечивает процесс резки за счет термического, химического и абразивного действия.
3)Газоэлектрическая:
-кислородно-дуговая. При кислородно-дуговой резке дуга горит между плавящимся электродом и разрезаемым металлом. Сварочный электрод трубчатый и по каналу внутри электрода подается режущий кислород. Дуга обеспечивает нагрев металла, а кислород, интенсивно окисляя железо, обеспечивает его сгорание и выдувание из зоны реза
|
-воздушно-дуговая. Воздушно-дуговая резка представляет собой способ обработки металлов и объединяет два физических процесса: расплавление металла теплом электрической дуги и выдувание жидкого металла струей сжатого воздуха.(плохое качество)
-плазменно-дуговая. Плазменная резка заключается в проплавлении разрезаемого металла за счет теплоты, генерируемой сжатой плазменной дугой, и интенсивном удалении расплава плазменной струей.
17. Газокислородная резка. Сущность. + и –
Газокислородная резка основана на сгорании металла в струе технически чистого кислорода. Смесь кислорода с горючим газом выходит из подогревательного мундштука резака и сгорает, образуя подогревательное пламя. Этим пламенем металл нагревается до температуры начала его горения. После этого по осевому каналу режущего мундштука подается струя режущего кислорода.
Кислород попадает на нагретый металл и зажигает его. При его горении выделяется значительное количество теплоты, которое совместно с теплотой, выделяемой подогревательным пламенем, передается нижележащим слоям металла, которые также сгорают. Образующиеся при этом шлаки (оксиды железа и т.д.) выдуваются струей режущего кислорода из зазора между кромками реза.
Существует несколько ограничений для газовой резки металлов:
температура плавления металла должна быть выше температуры его воспламенения в кислороде;
металл должен обладать хорошей текучестью в жидкой фазе;
низкая теплопроводность металла
При резке стали основное количество теплоты (70... 95 %) образуется при окислении металла. Этим условиям удовлетворяют низкоуглеродистые и низколегированные стали, титановые сплавы. Чугун не режется кислородом вследствие низкой температуры плавления и высокой температуры горения; медь - из-за высокой температуры плавления и малой теплоты сгорания; алюминий - из-за высокой тугоплавкости образующихся оксидов. Высоколегированные стали (хромистые, хромоникелевые и т.д.) не режутся ввиду образования тугоплавких, вязких шлаков
|
Для газокислородной резки пригодны горючие газы и пары горючих жидкостей, дающие температуру пламени при сгорании в смеси с кислородом не менее 1800 гр. Цельсия
Особенно важную роль при резке имеет чистота кислорода. Для резки необходимо применять кислород с чистотой 98,5 - 99,5 %. С понижением чистоты кислорода очень сильно снижается производительность резки и увеличивается расход кислорода.
В качестве горючих газов используют ряд углеводородов и их смесей. По показателям теплоты и температуры горения газокислородного пламени рационально применять ацетилен. Но исходя из технико-экономических показателей для газокислородной резки в качестве горючего газа наиболее широко применяют газы - заменители ацетилена. Их можно разделить на сжиженные, сжатые охлаждением, газовые смеси, растворенные газы, простые газы.
Кислородная резка относительно следующими преимуществами:
• Максимальная толщина разрезаемого материала может достигать 500 мм.;
• Меньшие капитальные затраты;
• Минимальные требования к техническому обслуживанию.
Недостатками технологии кислородной резки по сравнению с плазменной и лазерной резкой являются:
• Меньшая скорость резки;
• Большая зона нагрева;
• Большее образование окалины, что требует дополнительное время на обработку;
• Отсутствие возможности резки нержавеющей стали и алюминия;
• Меньшая производительность.
Кислородно-флюсовая резка
Сущность процесса кислородно-флюсовой резки состоит в том, что в зону реза, подогретую газовым пламенем, вместе со струей режущего кислорода вводят порошок флюса, который сгорает в кислороде, выделяя теплоту, повышающую температуру в зоне реза, - это термическое воздействие флюса. Продукты сгорания флюса образуют с тугоплавкими окислами разрезаемого материала жидкотекучие шлаки, которые удаляются из реза струей режущего кислорода - это химическое действие флюса. И, наконец, частицы порошка флюса сгорают не сразу и, перемещаясь в процессе горения в глубину реза, ударным трением стирают с поверхности кромок тугоплавкие окислы, способствуя их удалению из реза, - это абразивное действие флюса.
|
Схемы установок
- С внешней подачей флюса
- С однопроводной подачей флюса под высоким давлением
- С механической подачей флюса
Смотри раздаточный материал.
Резаки
В зависимости от схемы подачи флюса на два типа:
- Флюс подаётся в смеси с режущим кислородом к центральному каналу мундштука
- Выполнены по схеме с внешней подачей
По принципу смешения горючего газа и кислорода6
- Инжекторные
-с внутресопловым смещением.
При резке кислородом хромистых и хромоникелевых легированных сталей образуются тугоплавкие окислы хрома. Пленка этих окислов, покрывая частицы металла, препятствует его сгоранию в струе кислорода
Кислородная резка чугуна без флюса также затруднена, потому что температура плавления чугуна ниже температуры горения железа в кислороде и чугун начинает раньше плавиться, чем гореть в кислороде
Цветные металлы (медь, латунь, бронза) обладают высокой теплопроводностью и при их окислении кислородом выделяется количество тепла, недостаточное для дальнейшего развития процесса горения металла в месте реза. При кислородной резке этих металлов также образуются тугоплавкие окислы, препятствующие процессу резки. Поэтому кислородная резка чугуна, бронзы и латуни возможна только с применением флюсов.
А так у данного способа такие же недостатки и преимущества, что и у газокислородной.
И при кислородно-флюсовой резке мощность пламени должна быть в два раза больше, а режущее сопло — на один номер больше по сравнению с применяющимися при резке без флюса. Это обусловлено затратой дополнительного тепла на плавление флюса и добавочной энергии режущей струи на удаление большего количества шлаков из места разреза.
Основные условия резки
1. Температура воспламенения металла в кислороде должна быть ниже температуры его плавления. Лучше всех металлов и сплавов этому требованию удовлетворяют низкоуглеродистые стали, температура воспламенения которых в кислороде около 1300°С, а температура плавления около 1500°С. Увеличение содержания углерода в стали сопровождается повышением температуры воспламенения в кислороде с понижением температуры плавления. Поэтому с увеличением содержания углерода кислородная резка сталей ухудшается.
2. Температура плавления окислов металлов, образующихся при резке, должна быть ниже температуры плавления самого металла, в противном случае тугоплавкие окислы не будут выдуваться струей режущего кислорода, что нарушит нормальный процесс резки. Этому условию не удовлетворяют высокохромистые стали и алюминий. При резке высокохромистых сталей образуются тугоплавкие окислы с температурой плавления 2000°С, а при резке алюминия — оксид с температурой плавления около 2050°С. Кислородная резка их невозможна без применения специальных флюсов.
|
3. Количество теплоты, которое выделяется при сгорании металла в кислороде, должно быть достаточно большим, чтобы поддерживать непрерывный процесс резки. При резке стали около 70% теплоты выделяется при сгорании металла в кислороде и только 30% общей теплоты поступает от подогревающего пламени резака.
4. Образующиеся при резке шлаки должны быть жидкотекучими и легко выдуваться из места реза.
5. Теплопроводность металлов и сплавов не должна быть слишком высокой, так как теплота, сообщаемая подогревающим пламенем и нагретым шлаком, будет интенсивно отводиться от места реза, вследствие чего процесс резки будет неустойчивым и в любой момент может прерваться.
6 Металл или сплав должен быть без пор и раковин, без шлаков и включений.
Ремонт типовых деталей.
Сведение в классы и группы деталей близких по своей конструктивной однородности имеет следующую цель. Упрощения разработки технологических процессов ремонта различных деталей и увеличения эффективности их применения.
Создано девять основных классов, в каждый из которых входят группы деталей.
Объединение деталей происходит на основание их конструкций. Смотри раздаточный материал.
41. Ремонт корпусных деталей на примере блока цилиндров.
К корпусным деталям относятся блок цилиндров, головка блока цилиндров и различные картеры – сцепление, коробки передач и т.д.
Характерным для этих деталей является наличие на них конструкторских, технологических и измерительных баз, привалочных плоскостей, отверстий в соответствии с точным располодением их осей под подшипники валов, плоскостей разъемов, резьбовых отверстий.
При эксплуатации в корпусных деталях бывают следующие дефекты: износ или повреждение баз, не соосность отверстий, трещины на стенках и плоскостях разъемов, поверхностях под подшипники и на опорных поверхностях, обломы шпилек, забитость, срыв или износ резьбы, коробление, забоины или деформация обработанных установочных, привалочных или стыковочных поверхностей, кавитационный износ отверстий, через которые проходит охлаждающая жидкость, выпадание заглушек водяной рубашки блока цилиндров и т.д.
Ремонт блока цилиндров следует начинать с восстановления технологических баз, удаления обломанных шпилек и болтов, повреждений резьбовых отверстий, а также устранения трещин и других повреждений, требующих применения сварочных операций, так как сварка может повлечь за собой коробление обработанных плоскостей деталей.
Коробление устраняется – шлифованием или фрезерованием. Износ внутренней поверхности устраняется:
Посадочные пояски в блоке цилиндров под гильзы растачивают под ремонтный размер.
Поверхности отверстий под толкатели клапанов развертываются под ремонтный размер.
Поверхности под вкладыши и втулки ремонтируются механической обработкой под ремонтный размер или методом наплавки, напыления металла, электроискровой обработкой, гальваническим наращиванием металла, полимерными покрытиями, дополнительными ремонтными деталями.
Трещины в корпусных деталях устраняются заваркой (пайкой) или применением полимерных клеевых композиций. Трещины предварительно ограничивают засверливанием по концам, а затем разделывают под угол 45 и 60 градусов по всей длине, тщательно очищая от загрязнений, масла и следов коррозии и заваривается (запаивается). После этого деталь проверяется на герметичность.
Ремонт деталей класса диски
Типовыми деталями данного класса являются шестерни, маховики, диски сцепления, кольца, муфты и т.д.
Характерными дефектами являются: поверхностные трещины, задиры, риски, износ рабочей поверхности; износ зубьев по профилю и по торцу, выкрашивание, поломка, трещины; износ резьбовых отверстий (при наличии); износ фрикционных накладок (при наличии); износ поверхности отверстия под подшипник (при наличии) и т.д.
Рассмотрим типовой технологический процесс ремонта на примере ведомого диска сцепления.
Удаление изношенных фрикционных накладок (сверлильный станок);
Устранение коробления и погнутости (поверочная плита);
Рассверливание и развёртывание гладких отверстий под ремонтный размер или дрд (сверлильный станок);
Постановка ДРД и её фиксация, окончательная обработка под размер (токарный станок, электросварочный агрегат);
Сверление и нарезание резьб в промежутках между старыми (сверлильные);
Протачивание или шлифование торцовых и цилиндрических рабочих поверхностей трения (токарный, шлифовальный);
Постановка новых накладок (стенд для клёпки);
Статистическая балансировка (установка для балансировки).
Маховик.
Представляет собой сборочную единицу из чугунного диска и стального венца закрепленных с натягом. Происходит ослабление посадки венца и тела. Раскернивание т.е. приваривание вызывает проблемы при последующем ремонте. Целесообразно высверливание отверстия и установка штифта. При поломке зуба – выбраковка. Износ по торцу происходит из-за контакта с шестерней стартера. На плоскости трения ведомого диска образуются риски, что приводит к ухудшению сцепления. Риски устраняются притиранием, для этого создается база (шлицевое отверстие).
Применение алитирования.
Алитирование – это процесс насыщения поверхности детали алюминием.
Есть несколько способов алитирования:
Его проводят в порошкообразных смесях при 1000 °C и выдержке в течение 8 ч образуется слой в 0,4—0,5 мм, насыщенный алюминием.
погружением в расплав алюминия (с 6—8 % кремния (Si)) при 700—800 °C с последующей выдержкой, при этом концентрация алюминия в поверхностной части слоя составляет ~ от 80 % и выше. Толщина слоя 20-1000 мкм в зависимости от длительности нахождения в расплаве. Твердость алитированного слоя (на поверхности) до 500 HV, износостойкость наиболее высокая из всех методов
Металлизацией - на поверхность детали наносят слой алюминиевого порошка и после изоляционной обмазки деталь подвергают диффузионному отжигу
Покраской деталей алюминиевой краской (с последующим диффузионным отжигом в защитной атмосфере);
Алитированный слой обладает лучшим чем цинковый слой сопротивлением коррозии в атмосфере и морской воде. Повышается поверхностная твёрдость. Не происходит окисления материала при работе в высоких температурах, избегается термический удар.
Алитирование применяют при изготовлении клапанов автомобильных двигателей, лопаток и сопел газовых турбин, защиты от коррозии металлоконструкций и т. п.
Алитирование в расплавленном алюминии широко используются вместо горячего цинкования (листы, проволока, трубы, строит, детали).
Контроль осуществляется: внешний осмотр, замер толщины слоя, величина зёрен.
Ремонт зубчатых колёс
Зубчатые колёса относятся к классу диски типовых деталей. Дефектами являются трещины, износ шлицов. Основными же дефектами, которые определяются видом их работы, являются разрушение, выкрашивание зубьев, износ их по профилю и по торцевой поверхности. Из-за больших затрат (экономической нецелесообразности) большинство этих дефектов не восстанавливаются. Единственный восстанавливаемый дефект по торцу. Он возникает при соударение зубьев шестерен в момент ввода их в зацепление. Применяются два способа: электродуговая наплавка, наплавка под слоем флюса.
Суть электродуговой наплавки: зaключaется в тoм, чтo электрoднaя прoвoлoкa из кaссеты непрерывнo пoдaется в зoну свaрки. Тoк к электрoднoй прoвoлoке пoдвoдится через мундштук и нaкoнечник, рaспoлoженные внутри гaзoэлектрическoй гoрелки. При нaплaвке метaлл электрoдa и детaли перемешивaется. В зoну гoрения дуги пoд дaвлением 0,05...0,2 МПa пo трубке пoдaется углекислый гaз, кoтoрый, вытесняя вoздух, зaщищaет рaсплaвленный метaлл oт вреднoгo действия кислoрoдa и aзoтa вoздухa.
Суть наплавки под флюсом: Восстановление происходит путём наплавления электрода на поверхность зуба. Флюс защищает зону наплавления от окисления кислородом воздуха. Форма предаётся с помощью наплавочной формы. Она сделана из меди и заполнена водой в целях предотвращения её расплавления.
Восстановление зуба по профилю можно производить с помощью копировальных станков или же применить электрохимическую обработку наплавленных зубьев. Смысл заключается в пропускание тока между катодом (инструментом) и анодом (деталью) в среде 10-15% раствора едкого натрия NaOH. Происходит вытравливание материала зубьев по форме инструмента.
Шатуны. Ремонт.
К стержням некруглым относятся: штанги реактивные, рычаги коробок, шатуны, сошки и т.д. Шатуны делают из стали легированной 40Л горячей штамповкой, иногда литьем. Основные дефекты: погнутость; коробление; трещины; скручиваемость (изгиб; не параллельность осей); износ верхнего отверстия (отверстия под палец).
При наличии трещины шатун выбраковывается. Погнутость или изгиб устраняются если они находятся в допуске. Устраняется с помощью пресса
Или с перегибом (формирование более сложных остаточных напряжений).
Скручивание – оси не лежат в одной плоскости.
В верхнем отверстии шатуна запрессовывается втулка или палец. При износ ремонт происходит путем расточки до ремонтного размера втулки или пальца.
Другой способ: постановка свернутых втулок. Они представляют собой стальную пластину толщиной 0,6 мм. Развернутая длинна = длине окружности отверстия. Обработка под размер пальца.
Для их фиксации либо нарезка канавки внутри отверстия и обкатывание роликом либо фиксация через масляный канал втулкой заподлицо. Нижняя головка шатуна. Отверстие под наружные вкладыши изнашиваются. Либо гальваническое железнение потом обработка под размер.
Либо снятие металла с крышки и основной части шатуна.
Износ боковой поверхности под гайку (болт) в результате может происходить самоотворацивание. Восстанавливается фрезой. При аварийных режимах работы или при некачественной сборке шатуна (недостаточной затяжке) может происходить разрыв тела болта или срез витков резьбы. После ремонта шатуны подбираются по массе. Допускается разность ≈13-17г. Большой шатун (судовых V образных) нижняя часть не восстанавливается.
Восстановление деталей, резерв экономии материальных ресурсов. Ремонт машин – объективная необходимость. Техническая возможность и экономическая целесообразность ремонта деталей, сборочных единиц и автомобилей.
Ремонт – совокупность управляемых мероприятий связанных с восстановлением свойств, утраченных системой в процессе эксплуатации.
Объективную потребность и необходимость проведения ремонта обуславливает ряд факторов, объединяемые в две группы:
· Технологические
· Экономические
Технологические факторы:
1. Неравномерность изнашивания агрегатов и механизмов машин, узлов и деталей агрегатов, рабочих поверхностей деталей и узлов.
2. Конструктивная прочность и износостойкость базовых дорогостоящих рамно-кузовных и картерно-блоковых деталей и узлов.
3. Организационно-технологические возможности ремонтных органов по восстановлению изношенных поверхностей деталей.
Экономические факторы:
1. Затраты на капитальный ремонт по машине составляет 40-60%, по агрегатам – 25-65%, по деталям – 15-70% от стоимости соответствующих вновь изготовленных изделий.
2. При изготовлении автомобилей, тракторов и др. специальных машин 65-80% затрат приходятся на материалы и комплектующие, при капитальном ремонте эти затраты 20-40%.
Сварка в среде водяного пара. Сущность способа, преимущества и недостатки способа.
1 — сопло горелки; 2 — карман для сбора конденсата
При сварке чугунных деталей в защитной среде водяного пара происходит интенсивное выгорание углерода в сварочной ванне и исключается возможность образования карбидов железа, что обеспечивает хорошую обрабатываемость и прочность сварного соединения. Непрерывный процесс горения дуги создает большой запас тепла в сварочной ванне, а это в свою очередь исключает образование закаленной прослойки в зоне сплавления, характерной для всех способов холодной сварки чугуна. При сварке в среде водяного пара повышается качество наплавки за счет выбора присадочного материала, режима сварки и предварительного подогрева детали. При больших объемах работ в 2—3 раза повышается производительность.
|
|
Состав сооружений: решетки и песколовки: Решетки – это первое устройство в схеме очистных сооружений. Они представляют...
Архитектура электронного правительства: Единая архитектура – это методологический подход при создании системы управления государства, который строится...
Автоматическое растормаживание колес: Тормозные устройства колес предназначены для уменьшения длины пробега и улучшения маневрирования ВС при...
Адаптации растений и животных к жизни в горах: Большое значение для жизни организмов в горах имеют степень расчленения, крутизна и экспозиционные различия склонов...
© cyberpedia.su 2017-2024 - Не является автором материалов. Исключительное право сохранено за автором текста.
Если вы не хотите, чтобы данный материал был у нас на сайте, перейдите по ссылке: Нарушение авторских прав. Мы поможем в написании вашей работы!