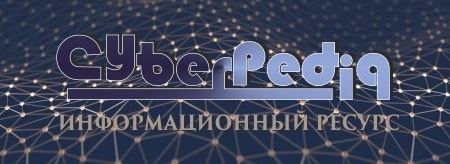
Индивидуальные и групповые автопоилки: для животных. Схемы и конструкции...
История развития хранилищ для нефти: Первые склады нефти появились в XVII веке. Они представляли собой землянные ямы-амбара глубиной 4…5 м...
Топ:
Характеристика АТП и сварочно-жестяницкого участка: Транспорт в настоящее время является одной из важнейших отраслей народного хозяйства...
Отражение на счетах бухгалтерского учета процесса приобретения: Процесс заготовления представляет систему экономических событий, включающих приобретение организацией у поставщиков сырья...
Выпускная квалификационная работа: Основная часть ВКР, как правило, состоит из двух-трех глав, каждая из которых, в свою очередь...
Интересное:
Аура как энергетическое поле: многослойную ауру человека можно представить себе подобным...
Влияние предпринимательской среды на эффективное функционирование предприятия: Предпринимательская среда – это совокупность внешних и внутренних факторов, оказывающих влияние на функционирование фирмы...
Уполаживание и террасирование склонов: Если глубина оврага более 5 м необходимо устройство берм. Варианты использования оврагов для градостроительных целей...
Дисциплины:
![]() |
![]() |
5.00
из
|
Заказать работу |
Одним из развивающихся направлений совершенствования процессов резания является высокоскоростное резание. Высокоскоростным резанием называется резание со скоростями в десятки или сотни раз выше нормативных. Для различных материалов величины этих скоростей значительно отличаются. Для легких цветных сплавов это 1500…3000 м/мин. Для жаропрочных сплавов это 300…400 м/мин. Появление нового метода резания связано с появлением новых скоростных станков и новых марок инструментальных материалов. Физическое обоснование применения высокоскоростного резания заключается в том, что с резким увеличением скорости резания снижается толщина срезаемой стружки, уменьшается работа пластической деформации, снижаются силы резания, все тепло уходит в стружку,
а не в деталь. В результате повышается в несколько раз производительность процесса резания и улучшается качество поверхностного слоя. К недостаткам применения высокоскоростного резания можно отнести возможное появление вибраций из-за неуравновешенности вращающихся масс деталей или инструмента. Для устранения этих недостатков высокоскоростного резания при внедрении в производство разработаны более жесткие станки, приспособления и инструменты и предусмотрена балансировка державок вращающегося инструмента.
7.3. Новые принципы резания
в условиях гибкого производства
На современных многоцелевых обрабатывающих центрах сегодня применяются новые методы резания и новые конструкции инструмента.
Современные многоцелевые обрабатывающие центры (рис. 147) представляют собой гибкие автоматизированные модули. Эти модули содержат в своем составе различные процессы резания. Например, на японских центрах, имеющих два шпинделя на одной оси (рис. 148), имеется возможность обработки детали с двух торцов методами точения, фрезерования, сверления, шлифования, зубонарезания последовательно с одной установки детали. Всем процессом резания управляет система ЧПУ. Поэтому станок может в течение смены обрабатывать деталь по всем поверхностям без вмешательства рабочего. Подключение автоматизированных устройств или роботов к подаче заготовок и смене инструмента создает реальные условия безлюдной технологии. Такой центр может самостоятельно работать непрерывно в течение нескольких суток без перенастройки. Однако
![]() | ![]() |
Рис. 147. Общий вид обрабатывающего центра | Рис. 148. Многоцелевой обрабатывающий центр фирмы Mazak |
здесь необходима постоянная диагностика процесса резания по комплексу показателей – мощности, температуре резания, шуму
и вибрации в зоне резания. При отсутствии такой системы диагностики возможно разрушение инструмента и поломка дорогостоящих частей станка.
Сегодня японская станкостроительная компания Mazak входит в тройку лидеров мирового станкостроения, занимает первое место в Японии по производству токарных и обрабатывающих центров. Mazak всегда стремилась идти на несколько лет впереди требований рынка, общепризнанных представлений о возможностях металообрабатывающих станков. Уже сегодня в конструкторских отделах Mazak разрабатываются модели, намеченные к выпуску в 2019 году. Это будет супермногофункциональная машина, объединяющая обычную механообработку, зубообработку, шлифовку, закалку, лазерную обработку и сборку. При этом машина будет ультраскоростной и ультраточной. Это обрабатывающие центры фрезерно-сверлильно-расточной группы (ОЦ), токарные центры (ТЦ), машины для лазерной резки и многое другое.
При проектировании оборудования Mazak ориентируется на сегодняшние потребности рынка и на тенденции его изменения в будущем. Отсюда вытекают требования к производству и к оборудованию. Разнообразие требований покупателя, сокращение срока службы изделий, постоянные изменения в мировой экономике привели промышленность к концу эры массового производства. Сегодня необходимо изготавливать все более разнообразные и сложные детали малыми партиями. Стало трудно прогнозировать загрузку производства, обострилась конкуренция по ценам. Все это обусловило следующие требования к оборудованию:
– повышение производительности не на 20…30 % за счет увеличения скорости выполнения операций, а в 5…10 раз за счет кардинального изменения технологий и методов обработки;
– переход от специального оборудования к универсальному.
Особо стоит отметить многофункциональные машины серии Integrex, которые объединяют в себе возможности ОЦ и ТЦ и позволяют делать детали самой сложной конфигурации из цельного куска материала без переустановки (рис. 149). Integrex выполняет операции точения, растачивания, фрезерования (до пяти осей), сверления, закалки, шлифовки, зубонарезания и т.д. Заготовка загружается на Integrex один раз, снимается полностью обработанная деталь. При этом возможна обработка из цельного блока материала, соответственно исключается оснастка. Эти станки привели к революции
в механообработке, так как они позволяют эффективно изготавливать партию любого размера. Цель оборудования Integrex – прорыв от серийного производства к производству под заказ. Обеспечиваются минимальные сроки от поступления заказа до изготовления детали.
![]() | ![]() |
Рис. 149. Деталь, обрабатываемая на станках серии Integrex | Рис. 150. Схема обработки детали на ОЦ серии Integrex |
Станки выпускаются как с горизонтальной (рис. 150), так
и с вертикальной осью вращения заготовки. Широкий размерный ряд позволяет изготавливать и мелкие, и крупные детали. Есть модели
с противошпинделем, а также с дополнительной нижней револьверной головкой.
Рассмотрим пример эффективности Integrex на примере коробчатой детали.
Обычная технология:
– проектирование изделия – 230 ч;
– проектирование деревянной оснастки – 270 ч;
– изготовление деревянной оснастки – 880 ч;
– отливка заготовки – 220 ч;
– проектирование УСП – 180 ч;
– изготовление УСП – 430 ч;
– обработка изделия – 560 ч.
Цикл производства: 2 160 ч (3 мес.)
Транспортировка: 152 км.
Задействовано 23 человека.
Технология Integrex – обработка на одном станке из цельного материала.
Цикл производства: 56 ч (сокращение времени в 36,5 раза). Транспортировка: 0,5 км (сокращение в 304 раза). Задействовано 5 человек (сокращение в 4,6 раза).
Это пример кардинального повышения производительности обработки, реализуемого за счет применения принципиально новой концепции станка Integrex.
Также интересны станки повышенной точности – токарный станок Nano Turn позволяет исключить шлифовку; ОЦ сравним по точности с координатно-расточным станком и позволяет вести работу с микронными допусками. Есть у Mazak серия высокоскоростных станков с линейными приводами, обеспечивающих производительность, требуемую в крупносерийном и массовом производстве. При этом станки обладают гибкостью, свойственной обычным станкам с ЧПУ, что позволяет быстро переходить на выпуск новой продукции. На базе таких станков Mazak изготавливает гибкие производственные системы (ГПС), позволяющие работать по безлюдной технологии (рис. 151). Стоит также упомянуть о многочисленных средствах автоматизации станков: паллетные системы, роботы, прутковые загрузчики, магазины, позволяющие автоматизировать работу отдельных станков и создавать на их базе гибкие производственные ячейки (ГПЯ) (рис. 152).
![]() | ![]() |
Рис. 151. Схема расположения оборудования в гибкой производственной системе | Рис. 152. Схема расположения оборудования в гибкой производственной ячейке |
Mazak имеет 7 заводов по производству станков, 3 из них расположены в Японии. Станки, поставляемые в Россию, делаются на японских заводах. Заводы Mazak представляют собой киберпроизводства. Цеха оборудованы ГПС, работающими в безлюдном режиме. Конструкторские бюро (КБ), маркетинг, сбыт, отдел заказов, менеджмент – все эти службы завязаны в единую информационную среду. По мере того как изделие проектируется в КБ и отдельные его узлы уже готовы, начинается разработка управляющих программ, заказывается инструмент, заготовки и начинается обработка. Планирование процесса производства, анализ загрузки оборудования осуществляется с помощью компьютеров. Все это позволяет выпускать станки за 1–2 месяца с момента поступления заказа. При этом обеспечиваются конкурентоспособные цены. Цены на оборудование Mazak, конечно, не такие, как на оборудование более низкого качества, производимое в странах третьего мира, но они весьма приемлемы и не выше цен на качественное оборудование, поставляемое на российский рынок европейскими производителями.
История развития хранилищ для нефти: Первые склады нефти появились в XVII веке. Они представляли собой землянные ямы-амбара глубиной 4…5 м...
Архитектура электронного правительства: Единая архитектура – это методологический подход при создании системы управления государства, который строится...
История создания датчика движения: Первый прибор для обнаружения движения был изобретен немецким физиком Генрихом Герцем...
Историки об Елизавете Петровне: Елизавета попала между двумя встречными культурными течениями, воспитывалась среди новых европейских веяний и преданий...
© cyberpedia.su 2017-2024 - Не является автором материалов. Исключительное право сохранено за автором текста.
Если вы не хотите, чтобы данный материал был у нас на сайте, перейдите по ссылке: Нарушение авторских прав. Мы поможем в написании вашей работы!