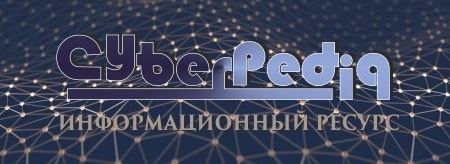
Индивидуальные и групповые автопоилки: для животных. Схемы и конструкции...
История развития пистолетов-пулеметов: Предпосылкой для возникновения пистолетов-пулеметов послужила давняя тенденция тяготения винтовок...
Топ:
Комплексной системы оценки состояния охраны труда на производственном объекте (КСОТ-П): Цели и задачи Комплексной системы оценки состояния охраны труда и определению факторов рисков по охране труда...
Характеристика АТП и сварочно-жестяницкого участка: Транспорт в настоящее время является одной из важнейших отраслей народного хозяйства...
Характеристика АТП и сварочно-жестяницкого участка: Транспорт в настоящее время является одной из важнейших отраслей народного...
Интересное:
Мероприятия для защиты от морозного пучения грунтов: Инженерная защита от морозного (криогенного) пучения грунтов необходима для легких малоэтажных зданий и других сооружений...
Как мы говорим и как мы слушаем: общение можно сравнить с огромным зонтиком, под которым скрыто все...
Уполаживание и террасирование склонов: Если глубина оврага более 5 м необходимо устройство берм. Варианты использования оврагов для градостроительных целей...
Дисциплины:
![]() |
![]() |
5.00
из
|
Заказать работу |
|
|
Для быстрого определения наивыгоднейших сочетаний подач
и скоростей резания, обеспечивающих наименьшие интенсивность износа инструмента или себестоимость обработки, а также для определения износов h о.п.ои h о.п.з разрабатываются специальные номограммы (рис. 114). В основе номограмм лежат параметрические уравнения максимальной размерной стойкости инструмента, полученные на основании стойкостных и температурных испытаний, результаты исследования высоты неровностей обрабатываемой поверхности при оптимальных сочетаниях s и V и экономические расчеты.
Рис. 114. Номограмма для определения подач
и скоростей резания при точении (t = соnst)
Номограмма позволяет по заданной высоте неровностей и принятой величине радиуса R при вершине резца определить максимально допустимую подачу s max. Работа на подачах s > s max не обеспечит требуемой высоты неровностей, а на подачах s < s max нерациональна, так как снижает производительность труда, повышает себестоимость обработки и поверхностный относительный износ h о.п.о (т.е. снижает точность обработки), а также увеличивает расход инструмента.
Для определения требуемых скоростей резания по найденной подаче на номограмме нанесены линии V ои V э. Линия V осоответствует таким сочетаниям подач и скоростей резания, при которых в зоне резания создается оптимальная температура и обеспечивается
минимальный поверхностный относительный износ, определяемый линией h о.п.о. При работе на оптимальных скоростях резания V o
достигается наибольшая размерная стойкость инструмента и наименьшая погрешность обработки, вызываемая износом инструмента. Линия V эсоответствует сочетаниям подач и скоростей резания, при которых обеспечивается наименьшая себестоимость обработки
и наибольшая производительность общественного труда. Поверхностный относительный износ при этом получается более интенсивным и определяется линией h о.п.з.
|
Повышение скорости резания от V o до V эувеличивает технологическую производительность от По до Пэи снижает себестоимость обработки от А одо А э. Поверхностный относительный износ при этом возрастает от h о.п.одо h о.п.з; следовательно, размерная стойкость
и точность обработки снижаются.
Работа на скоростях резания ниже V оснижает производительность обработки и повышает ее себестоимость. Точность обработки и размерная стойкость инструмента при этом снижаются, а расход инструмента, отнесенный к одной детали, повышается. Работа на скоростях больших (выше V э)повышает поверхностный относительный износ, а также себестоимость обработки и снижает производительность общественного труда при некотором повышении технологической производительности труда на данном рабочем месте за счет резкого возрастания расхода инструмента.
Целесообразный диапазон изменения скоростей резания на номограмме заключен между линиями V ои V э. Скорости резания по линии V о следует выбирать при повышенных требованиях к точности обработки деталей, а также при эксплуатации инструмента на многорезцовых и автоматизированных станках. В остальных случаях скорость резания нужно выбирать по линии V э. По полученной скорости резания и диаметру детали находят n. Номограммы одинаково удобны для рабочего и конструктора, технолога и нормировщика, так как они позволяют увязать выбор режимов обработки с параметрами шероховатости, точностью, производительностью, себестоимостью обработки.
4.3.12. Характер изнашивания и средние величины
максимально допустимого износа инструментов
Токарные резцы с пластинками твердых сплавов при обработке сталей и чугуна изнашиваются как по задней, так и по передней поверхности. Чаще всего максимальную ширину площадка износа имеет у вершины резца или на переходной задней поверхности, т.е.
в месте резца с наихудшими условиями теплоотвода. Допустимая величина линейного износа h задней поверхности при обработке: стали – 0,8…1 мм; чугуна с подачей £ 0,3 мм/об. – 1,4…1,7 мм; чугуна
с подачей > 0,3 мм/об. – 0,8…1 мм.
|
Винтовые сверла при обработке сталей изнашиваются по передней и задним поверхностям. Изнашивание перемычки считается ненормальным; оно происходит или в результате неправильной заточки сверла, или из-за недостаточной твердости инструментального материала после термообработки. Износ задней поверхности вдоль главного лезвия неравномерен: ширина площадки износа непрерывно возрастает по мере удаления от перемычки сверла. В отличие от резцов лунка износа вдоль всего главного лезвия не образуется. Она возникает у уголка сверла в том месте, где главное лезвие переходит во вспомогательное. Изнашиванию также подвергается вспомогательная задняя поверхность (фаска), на которой появляются штрихи износа у уголка сверла. Допустимая величина износа h сверл из быстрорежущих сталей при диаметре до 20 мм равна 0,6…0,8 мм и при диаметре свыше 20 мм равна 0,8…1 мм. При обработке чугуна передняя поверхность сверла не изнашивается. Износ задней поверхности «соединяется» с износом фаски, что приводит к скруглению уголка сверла. Поэтому лимитирующим износом является скругление h у уголка. Допустимая величина износа h у сверл из быстрорежущих сталей при работе без СОТС при диаметре до 20 мм равна 0,5…0,8 мм и при диаметре свыше 20 мм равна 0,8…1,2 мм.
Метчики при обработке как сталей, так и чугуна изнашиваются только по задней поверхности. Максимальный износ сосредоточивается в месте перехода главного лезвия во вспомогательное. Допустимая величина износа h машинных метчиков при обработке сталей равна 0,125 d o и чугуна – 0,07 d о.
Цилиндрические осевые, концевые и дисковые фрезы изнашиваются только по задней поверхности. Площадка износа задней поверхности расположена вдоль рабочего участка лезвия (рис. 115), постепенно увеличиваясь по ширине от входящей точки лезвия к выходящей. Допустимые величины износов h задней поверхности осевых фрез из быстрорежущих сталей при черновой обработке сталей равны 0,4…0,6 мм, а при чистовой – 0,15…0,25 мм и при черновой обработке чугуна равны 0,5…0,8 мм, а при чистовой – 0,2…0,3 мм.
|
Рис. 115. Схема износа цилиндрической фрезы
Изнашивание торцовых фрез подобно изнашиванию резцов (рис. 116). Фрезы из быстрорежущих сталей и с пластинками твердых сплавов при обработке сталей и чугуна изнашиваются по задней и передней поверхностям. Фрезы из быстрорежущих сталей при обработке чугуна изнашиваются только по задней поверхности. Допустимые износы h фрез из быстрорежущих сталей при черновой обработке сталей и чугуна равны 1,5…2 мм, а при чистовой обработке – 0,3…0,5 мм; фрез с пластинками твердых сплавов при обработке сталей – 1…1,2 мм и при обработке чугуна – 1,5…2 мм. Протяжки изнашиваются только по задней поверхности (рис. 117). С ростом ширины площадки износа одновременно растет радиус округления клина. Ширина площадки износа вдоль главного лезвия в общем случае неодинакова. Наибольшая ширина наблюдается у краев стружкоделительных канавок и в точках пересечения главного лезвия со вспомогательными. Допустимая ширина h з площадки износа при обработке сталей и чугуна у шпоночных и шлицевых протяжек равна 0,3…0,4 мм, а у круглых протяжек – 0,2…0,3 мм. Более объективным показателем изнашивания является округление зубьев протяжки. При достижении радиусом округления определенного значения резко увеличивается шероховатость обработанной поверхности, а на лезвиях
![]() | ![]() |
Рис. 116. Схема износа торцовой фрезы | Рис. 117. Схема износа протяжки |
протяжки появляются следы выкрашивания. При протягивании деталей с 5-м классом чистоты обработанной поверхности предельные величины радиуса округления составляют r = 0,02 мм при подъемах зубьев 0,01…0,02 мм и r= 0,03…0,04 мм
Использование радиуса округления как критерия износа в производственных условиях связано с трудностями вследствие сложности измерения допустимой величины r.
Превышение максимально допустимой величины износа резко сокращает число переточек, допускаемых инструментом. Последнее приводит к возрастанию себестоимости операции, выполняемой инструментом, поскольку в сумме затрат, определяющих себестоимость операции, доля расходов, связанных с эксплуатацией инструмента, велика. Поэтому соблюдение в производственных условиях допустимых норм износа является основой рациональной эксплуатации инструмента.
|
4.4. Контрольные вопросы и задания
1. Перечислите требования, предъявляемые к инструментальным материалам.
2. Дайте общую классификацию инструментальных материалов, их маркировки и применения.
3. Каковы причины напряжения в инструменте и износа инструмента?
4. Какова физическая сущность изнашивания инструментов?
5. Что такое стойкость режущих инструментов?
6. Начертите график износа за время работы инструмента.
7. Что такое период стойкости инструмента?
8. Каковы критерии износа-затупления инструмента?
9. Покажите зависимость «скорость резания – стойкость инструмента».
10. Дайте определение положения о постоянстве оптимальной температуры резания.
11. Дайте определение экономической скорости резания и скорости резания, соответствующей максимальной производительности на данном рабочем месте.
12. Как различные факторы влияют на скорость резания и стойкость инструмента?
Глава 5
Влияние условий резания
на качество поверхностного слоя обработанной детали
5.1. Понятие о поверхностном слое,
возникающем при резании
В результате обработки резанием вследствие пластической
деформации тонкий поверхностный слой детали толщиной 0,2…1,0 мм приобретает новые свойства, имеющие значительные отличия от обрабатываемой поверхности и внутренних свойств заготовки. Качество детали после обработки резанием прежде всего определяется:
– точностью размеров;
– геометрическими параметрами качества – шероховатостью, граностью, бочкообразностью, корсетностью и т.д.;
– физическими параметрами – глубиной и степенью наклепа, микроструктурой, остаточными поверхностными напряжениями, дислокационной структурой и т.д.
Установлено, что разрушение материала деталей в процессе эксплуатации машин обычно начинается с поверхности. В процессе механической обработки в поверхностном слое появляются остаточные напряжения, разрывы металла, микротрещины, которые при различных условиях эксплуатации могут привести к росту величины трещин и последующему разрушению. Обеспечение высокой усталостной и длительной прочности, термоусталости, износоустойчивости, коррозионной стойкости и других эксплуатационных требований к деталям ГТД может быть достигнуто и технологическими методами, т.е. назначением соответствующих режимов резания. Поэтому технологу нужно знать особенности образования поверхностного слоя и уметь управлять процессом резания для обеспечения наиболее благоприятных параметров качества поверхностного слоя.
5.2. Основные параметры, определяющие качество
поверхностного слоя
|
|
Автоматическое растормаживание колес: Тормозные устройства колес предназначены для уменьшения длины пробега и улучшения маневрирования ВС при...
Двойное оплодотворение у цветковых растений: Оплодотворение - это процесс слияния мужской и женской половых клеток с образованием зиготы...
Опора деревянной одностоечной и способы укрепление угловых опор: Опоры ВЛ - конструкции, предназначенные для поддерживания проводов на необходимой высоте над землей, водой...
История создания датчика движения: Первый прибор для обнаружения движения был изобретен немецким физиком Генрихом Герцем...
© cyberpedia.su 2017-2024 - Не является автором материалов. Исключительное право сохранено за автором текста.
Если вы не хотите, чтобы данный материал был у нас на сайте, перейдите по ссылке: Нарушение авторских прав. Мы поможем в написании вашей работы!