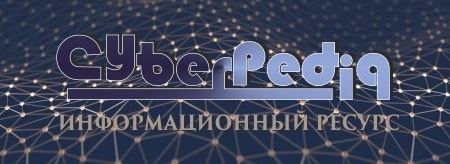
Поперечные профили набережных и береговой полосы: На городских территориях берегоукрепление проектируют с учетом технических и экономических требований, но особое значение придают эстетическим...
Наброски и зарисовки растений, плодов, цветов: Освоить конструктивное построение структуры дерева через зарисовки отдельных деревьев, группы деревьев...
Топ:
Характеристика АТП и сварочно-жестяницкого участка: Транспорт в настоящее время является одной из важнейших отраслей народного хозяйства...
Процедура выполнения команд. Рабочий цикл процессора: Функционирование процессора в основном состоит из повторяющихся рабочих циклов, каждый из которых соответствует...
Оценка эффективности инструментов коммуникационной политики: Внешние коммуникации - обмен информацией между организацией и её внешней средой...
Интересное:
Уполаживание и террасирование склонов: Если глубина оврага более 5 м необходимо устройство берм. Варианты использования оврагов для градостроительных целей...
Принципы управления денежными потоками: одним из методов контроля за состоянием денежной наличности является...
Наиболее распространенные виды рака: Раковая опухоль — это самостоятельное новообразование, которое может возникнуть и от повышенного давления...
Дисциплины:
![]() |
![]() |
5.00
из
|
Заказать работу |
|
|
1. Подбор оптимальных составов технологической среды. Известно что технологическая среда снижает температуру в зоне резания, трение на площадках контакта, охрупчивает металл в зоне пластической деформации и т.д. Правильно подбирая состав технологической среды, можно резко снизить интенсивность изнашивания и улучшить качество обработанной поверхности.
2. Подвод в зону резания дополнительной энергии. Этот способ широко применяется при резании труднообрабатываемых материалов. В частности, производится их обработка в нагретом состоянии, с наложением электрических и магнитных полей, принудительных колебаний строго определенной частоты и т.д. Вследствие этого изменяется интенсивность изнашивания режущих кромок и период стойкости возрастает в несколько раз.
3. Регулирование микроструктуры за счет подбора режимов термической обработки. Для каждой группы материалов можно подобрать такой режим термообработки, который обеспечивает получение строго определенной микроструктуры и уровня механических свойств.
Так, например, стали для хорошей обрабатываемости должны иметь следующую микроструктуру: 1) малоуглеродистые (С < 0,3 %) – пластинчатый перлит и феррит. Резко выраженная строчечность феррита и крупные скопления его ухудшают обрабатываемость;
2) со средним содержанием углерода (С = 0,35...0,55 %) – пластинчатый перлит и феррит в виде сетки или некрупных зерен; 3) высокоуглеродистые конструкционные (С > 0,55 %) и инструментальные стали – зернистый перлит.
Соответствующим образом подбираются виды термообработки (нормализация, отжиг) и их режимы.
Обрабатываемость чугуна можно улучшить графитизирующим или сфероидизирующим отжигом, исключающим появление сетки карбидов и обеспечивающим округлую форму зерен.
|
Термообработка труднообрабатываемых материалов определяет фазовый состав, процентное содержание фаз, их дисперсность и распределение, а также размеры зерен твердого раствора. При этом
требуется выдерживать на строго определенном уровне число упрочняющих избыточных фаз, поскольку от них зависит и обрабатываемость, и жаропрочность материала. Для термообработки рекомендуется использовать двойную закалку с последующим высокотемпературным старением.
4. Введение в состав обрабатываемого материала специальных присадок. Известны два механизма действия присадок, способствующих улучшению обрабатываемости. В первом случае снижается коэффициент трения на контактных площадках и интенсивность изнашивания, поскольку присадки образуют в металле твердые смазочные вещества (сульфиды, селениды, сульфоселениды и др.).
Во втором – присадки, являясь концентраторами напряжений, способствуют охрупчиванию обрабатываемого материала, снижают силы резания и уровень температур.
Наиболее характерными присадками являются элементы, относящиеся к VI группе таблицы Менделеева, – сера, селен, теллур, которые образуют в стали неметаллические включения, а также свинец. Примером сталей повышенной обрабатываемости могут служить автоматные с повышенным содержанием серы (А11...А35), серы
и фосфора (А12), серы и свинца (АС14). Свинец в последнем случае присутствует в стали в двух модификациях: в виде мелких обособленных частиц, произвольно расположенных в матрице металла,
и в виде комплексных соединений MnS–Pb. Свинец характеризуется низкой температурой плавления, поэтому, кроме охрупчивающего действия, он может создать на площадках контакта жидкую пленку. Установлено, что для резкого снижения склонности к схватыванию достаточно образования пленки толщиной около 2 мкм.
На состав, форму, размеры и распределение избыточных фаз существенным образом влияет такой этап выплавки стали, как раскисление, для чего используются кремний, алюминий, марганец
и кальций. Кальций позволяет существенно улучшить обрабатываемость сталей. В их структуру входят силикаты или алюминаты кальция в сульфидной оболочке, что резко снижает изнашивание инструмента. Содержание кальция строго определенное. Такие стали успешно применяются на Волжском автозаводе (АЦ20ХГНМ (вместо 20ХГМ), АЦ40Х (вместо 40Х)), обеспечивая повышение периода стойкости до 3 раз.
|
6.1.5. Особенности обрабатываемости резанием
различных материалов
Обрабатываемость сталей. Обрабатываемость сталей следует рассматривать с точки зрения их истирающей способности и уровня температур резания. Влияние химического состава, механических свойств, микроструктуры и других факторов обусловлено их влиянием на k ист и q.
Рассмотрим роль основных химических элементов в обрабатываемости конструкционных и инструментальных сталей.
При обработке материалов с весьма малым содержанием углерода (сталь 08, армко-железо) трудно обеспечить высокое качество обработанной поверхности. Оптимальным с точки зрения периода стойкости инструмента считают содержание углерода 0,10...0,20 %. При его повышении до 0,20...0,30 % и более наблюдается заметное снижение стойкости, обусловленное появлением в микроструктуре абразивных частиц цементита. Улучшить обрабатываемость можно путем изменения микроструктуры.
В легированных сталях влияние углерода более сложное, поскольку связано с образованием карбидов различного состава, их размерами, твердостью и т.д.
Наличие в стали марганца упрочняет феррит, снижает пластичность стали. При сочетаниях С < 0,20 % и Мn < 1,5 % заметно улучшается процесс резания. При высоком содержании марганца (свыше 10 %) сталь приобретает склонность к наклепу под действием сил резания, вследствие чего резко возрастает прочность, снижается пластичность поверхностного слоя детали, по границам зерен образуются железомарганцовистые карбиды, а аустенит частично переходит в мартенсит. Обрабатываемость в этом случае чрезвычайно низкая. Повысить ее можно при нагреве заготовок до температуры 400...600 °С, когда снимаются вредные последствия наклепа. При наличии в стали некоторого содержания серы в ней образуются сульфиды марганца, играющие роль граничной смазки на поверхностях трения.
|
Фосфор, сера, свинец используются как присадки, улучшающие обрабатываемость.
Содержание кремния во всех случаях ухудшает обрабатываемость сталей вследствие образования силикатных абразивных включений.
Наличие молибдена, ванадия, хрома, вольфрама повышает прочность и вязкость сталей, ухудшая их обрабатываемость. Эти элементы образуют твердые растворы с железом и карбиды различного состава и твердости. Как следствие, возрастает истирающая способность материала. Хром, способствуя коагуляции карбидных частиц при отпуске, значительно снижает теплопроводность материала. Кобальт, наоборот, замедляет коагуляцию карбидов, повышая теплопроводность. Он несколько снижает прочность и вязкость стали, образуя твердый раствор с железом. Присутствие никеля в твердом растворе способствует его упрочнению, однако снижает обрабатываемость сталей.
Таким образом, обрабатываемость сталей ухудшается с увеличением содержания углерода и легирующих элементов, поскольку
в этом случае увеличиваются k ист и q. В настоящее время принята классификация сталей по обрабатываемости резанием, приведенная
в табл. 20 (коэффициент K м характеризует снижение уровня скоростей резания VT).
В производственных условиях важно увязывать обрабатываемость материалов с их прочностью и твердостью. В общем случае
существует связь между V и T и механическими свойствами металлов.
Однако никакое из механических свойств не оказывает самостоятельного влияния на относительный уровень скорости резания, поскольку интенсивность изнашивания режущих инструментов не зависит непосредственно от временного сопротивления, твердости, относительного удлинения и т.д.
Таблица 20
Коэффициенты обрабатываемости сталей и чугунов
Материал | Марка | k м |
Сталь конструкционная автоматная, ГОСТ 1414–75 | А11, А12, А20, А30, А35 | 1,2/– |
Сталь углеродистая качественная, ГОСТ 1050–74 | 08, 10, 15, 20…65, 60Г, 65Г, 70Г | 1,0/0,85 |
Сталь конструкционная легированная, ГОСТ 4543–71: | ||
марганцовистая | 15Г…70Г, 10Г2…50Г2 | 1,0/0,85 |
хромистая | 15Х, 15ХА, 20Х…50Х | 1,0/0,85 |
хромоникелевая | 20ХН, 40ХН, 50ХН, 12ХН2, 20ХН3А, 30ХН3А, 12Х2Н4А | 0,9/0,8 |
хромомарганцовистая | 18ХГ, 18ХГТ, 30ХГТ, 20ХГР | 0,8/– |
хромокремнистая | 30ХС, 38ХС, 40ХС | –/0,8 |
хромованадиевая | 15ХФ, 40ХФА | 1,0/0,85 |
хромомолибденовая | 15ХМ…38ХМ, 35Х2МА | 0,8/– |
хромоалюминиевая | 38ХЮ, 35ХЮА, 38Х2Ю | 0,8/– |
хромокремнемарганцовистая и хромокремнемарганцовоникелевая | 20ХГС, 30ХГС, 35ХГСА, 38ХГСА, 30ХГСН2А… | 1,15/0,85 |
|
Окончание табл. 20
Материал | Марка | k м |
хромоникельмолибденовая | 14Х2Н3МА, 20ХН2М, 38Х2Н2МА, 25Х2Н4МА… | 1,15/0,85 |
хромоникельвольфрамовая | 25ХНВА, 30ХНВА | 0,8/0,8 |
хромоникельванадиевая | 20ХНФ, 30ХНВФА | 0,8/0,8 |
хромомолибденванадиевая | 35ХМФА, 30Х3МФ | 0,8/0,8 |
хромомолибденалюминиевая | 38ХМЮА | 0,8/0,8 |
Сталь инструментальная углеродистая, ГОСТ 1435–74 | У7А…У13А | 1,0/– |
Сталь инструментальная легированная, ГОСТ 5950–73 | ХВ5, ХВГ, ХВСГ, 9ХС, ХГС, 6ХВ2С, ХГСВФ… | –/0,85 |
Сталь шарикоподшипниковая, ГОСТ 801–60 | ШХ9, ШХ15, ШХ15СГ | –/0,7 |
Сталь инструментальная быстрорежущая, ГОСТ 19265–73 | Р9, Р18, Р18К5Ф2, Р6М5, Р9К5, Р10К5Ф5… | –/0,85 |
Чугун серый, ГОСТ 1412–85 | СЧ10…СЧ35 | 1,0/0,9 |
Чугун ковкий, ГОСТ 1215–79, и чугун высокопрочный, ГОСТ 7293–85 | КЧ30-6…КЧ35-10… ВЧ38-17…ВЧ60-2… | 0,9/0,7 |
Примечание. В числителе приведены коэффициенты для НВ 179…229, в знаменателе – для НВ 229…269.
Каждому из этих механических свойств присущ вполне определенный физический смысл, который не дает оснований связывать их со стойкостью инструмента.
Связь между этими показателями и VT существует лишь постольку, поскольку они связаны с основными факторами, обусловливающими интенсивность изнашивания режущих инструментов, а именно истирающей способностью обрабатываемого материала и температурой резания, возникающими при снятии стружки. В частности, увеличение прочности и твердости уменьшает скорость VT, т.к. такому изменению механических свойств сопутствует увеличение истирающей способности и температуры резания. Увеличение вязкости и пластичности обрабатываемого материала снижает истирающую способность, что позволяет повысить скорость VT.
В практике часто пользуются следующими приблизительными зависимостями между VT и механическими свойствами металлов:
или
,
где nv – показатель интенсивности влияния НВ и временного сопротивления s b на VT;
С НВ, С s b – постоянный коэффициент для стандартных условий резания для материалов соответственно из чугуна и стали.
Наряду с химическим составом на истирающую способность материала влияет его микроструктура. Наименьшей истирающей способностью обладает феррит, небольшой коэффициент k ист имеет аустенит; истирающая способность перлита зависит от формы цементита; у пластинчатого перлита она больше, чем у зернистого,
у зернистого – тем меньше, чем меньше зерна цементита; у высоколегированных сталей истирающая способность значительно увеличивается, если карбиды расположены в виде скоплений или сетки.
|
Наибольшая VT достигается при резании феррита, а затем по мере усиления интенсивности затупления инструментов идут зернистый и пластинчатый перлит, сорбит, троостит.
Однако в тех или иных технологических ситуациях используются различные показатели обрабатываемости. Подробная информация о влиянии микроструктуры на эти показатели приведена
в табл. 21.
При обработке деталей на автоматизированном оборудовании серьезное внимание уделяется благоприятному стружкообразованию
и обеспечению требуемой шероховатости обработанной поверхности. Решающее влияние на последнюю оказывает микроструктура: если она состоит из зернистого перлита, сорбита и троостосорбита, зона максимальных микронеровностей смещается в зону меньших скоростей по сравнению с обработкой пластинчатого перлита; высота микронеровностей тем больше, чем больше содержание в структуре сталей свободного феррита; повышение содержания углерода и легирующих элементов способствует уменьшению шероховатости, что наблюдается также по мере увеличения размера зерна перлита. Значительная высота микронеровностей наблюдается при мелком зерне перлита и высоком содержании свободного феррита, а наилучшая – при структурах троостосорбита и сорбита с высокой твердостью.
Обрабатываемость чугунов. Обрабатываемость чугунов определяется в первую очередь их микроструктурой, в зависимости от которой они подразделяются на следующие группы: 1) ферритные, содержащие феррит и графит; 2) перлитные, содержащие перлит
и пластинчатый графит; 3) перлитные ковкие и сверхпрочные, содержащие перлит и сфероидальный графит; 4) половинчатые, содержащие перлит, графит и цементит; 5) белые, содержащие перлит
и цементит. Обрабатываемость чугунов ухудшается по мере того, как углерод из свободного состояния (графит) переходит в связанное (цементит), обладающее повышенной истирающей способностью.
На обрабатываемость чугуна влияет также размер и форма частиц графита и цементита. Наилучшая обрабатываемость достигается при наличии небольших сфероидальных зерен графита. При одинаковой твердости уровень VT для чугунов с пластинчатым графитом всегда меньше. Сетка цементита или крупные его скопления резко снижают обрабатываемость чугунов. Это характерно также для обработки по корке, с окалиной или песком.
Таблица 21
Влияние структуры стали на показатели обрабатываемости
Показатель обрабатываемости | Структура стали | |||||||
зернистый перлит | пластинчатый перлит | феррит в виде строчек или крупных зерен | мелкозернистый перлит при относительно большом содержании феррита | сорбитообразный перлит | карбиды в виде скоплений или сетки | сорбит с невысокой твердостью | сорбит с высокой твердостью | |
Период стойкости быстрорежущих и твердосплавных инструментов при черновой обработке | Самый высокий | Удовлетворительный | Удовлетворительный | Удовлетворительный | Пониженный | Низкий | Низкий | Очень низкий |
Период стойкости быстрорежущих инструментов при протягивании, развертывании и зубонарезании | Низкий | Высокий | Низкий | Низкий | Удовлетворительный | Низкий | Низкий | Очень низкий |
Шероховатость поверхности при протягивании, развертывании, зубонарезании с низкими скоростями резания | Плохая | Хорошая | Плохая | Плохая | Хорошая | Удовлетворительная | Плохая | Очень хорошая |
Зависимость VТ от НВ для серого чугуна более достоверна, чем для стали, а nV = 1,7.
Вследствие малых пластичности и склонности чугуна к упрочнению силы при его резании меньше, чем при обработке литых сталей на ферритной основе. Уменьшаются ширина площадки контакта на передней поверхности, размеры нароста, а заторможенный слой становится неустойчивым. Из-за малой ширины площадки контакта нормальные напряжения достаточно велики и концентрируются вблизи главной режущей кромки инструмента, способствуя ее
сколам. Температура резания при обработке чугунов с пластинчатым графитом ниже, чем при обработке ферритных сталей той же твердости. Однако скорость VT при обработке чугунов ниже
(см. табл. 20).
Очевидно, в этом случае сказывается преобладающее влияние истирающей способности материала и слабое защитное действие нароста и заторможенного слоя на передней поверхности инструмента.
В машиностроении широко используются легированные чугуны различного назначения. Рассмотрим влияние на обрабатываемость основных легирующих элементов.
При небольшом содержании марганца в чугуне период стойкости инструмента не изменяется, а при его увеличении свыше 1,5 % – уменьшается.
Содержание кремния в чугуне до 2,75 % улучшает его обрабатываемость благодаря своему графитизирующему действию, повышение его свыше 3 % приводит к упрочнению феррита, образованию силикатных соединений и снижению VT.
Наличие никеля до 2 % и меди также способствует графитизации чугуна и улучшает его обрабатываемость. Цирконий и титан при добавке их до 0,4 % активно раскисляют металл и повышают VТ.
Молибден, особенно при содержании его свыше 0,5 %, упрочняет основу чугуна и ухудшает его обрабатываемость. Так же действуют добавки хрома и ванадия, кроме того, они заметно активизируют образование карбидов. Чугуны с такими добавками отличаются высокой твердостью и прочностью. Обрабатываемость чугуна ухудшается в зависимости от формы карбидной фазы: мелкоигольчатые карбиды ® длинноигольчатые карбиды ® столбчатые карбиды ® разорванная сетка карбидов ® сплошная сетка карбидов.
Обрабатываемость алюминиевых сплавов. Алюминиевые сплавы с точки зрения обрабатываемости можно разделить на три группы. К первой относятся сплавы низкой твердости, имеющие склонность к налипанию на инструмент, например дюралюминий
в отожженном состоянии. Сплавы второй группы имеют более высокую твердость, не налипают на инструмент. К этой группе относятся термически упрочненный дюралюминий, а также кованые сплавы АК6, АК8 и др.
В третью группу входят широко распространенные литые сплавы, содержащие кремний, в частности силумины различных марок. Для первых двух групп наиболее характерно образование сливной стружки в виде длинных лент или спиралей, для третьей – стружка легко дробится на короткие элементы.
По сравнению со сталью алюминиевые сплавы обладают меньшей твердостью, более низким временным сопротивлением и лучшей теплопроводностью, что позволяет значительно повышать скорость резания и подачу. Однако выбор оптимальных условий обработки затруднен из-за совместного действия целого ряда факторов. Высокая вязкость ряда алюминиевых сплавов интенсифицирует налипание частиц на рабочие поверхности режущего инструмента. Это затрудняет стружкоотвод, может вызвать пакетирование стружки в канавках инструмента и образование задиров на обработанной поверхности. При нагревании алюминий сильно расширяется (в 2 раза больше, чем сталь). Это препятствует достижению высокой точности обработки, например, при развертывании.
Уровень сил резания при обработке алюминиевых сплавов
в 2…4 раза ниже, чем при обработке конструкционных сталей. Характер влияния элементов режима резания и переднего угла на силу резания такой же, как при обработке сталей. Алюминиевые сплавы склонны к наростообразованию. Этот процесс протекает чрезвычайно активно в связи с повышенной адгезионной активностью алюминия к материалам, используемым в качестве инструментальных. Поэтому максимальная высота нароста и его исчезновение отмечаются для алюминиевых сплавов при относительно более низких скоростях резания, чем для сталей.
Между уровнем сил резания и механическими свойствами алюминиевых сплавов нет отчетливой зависимости. Очевидно, последние оказывают сложное совокупное влияние на сопротивление металла пластическому деформированию при образовании стружки
и на ее трение о переднюю поверхность инструмента. В целом при повышении прочности сплавов уровень сил резания увеличивается. Связь между силами резания и характером микроструктуры алюминиевых сплавов следующая: сила резания выше при обработке сплавов с равномерной структурой, когда содержание твердого раствора кремния в алюминии преобладает над содержанием эвтектики; если частицы эвтектики имеют более грубую пластинчатую форму, силы резания меньше.
Уровень допустимых скоростей резания, обеспечивающих низкую шероховатость обработанной поверхности и нормативные периоды стойкости, при обработке алюминиевых сплавов в несколько раз выше, чем при обработке сталей.
Обрабатываемость алюминиевых сплавов можно значительно улучшить за счет применения оптимальных геометрических и конструктивных параметров инструментов, тщательной доводки их режущих кромок и правильного выбора технологической среды. Необходимо конструктивно обеспечивать свободное размещение стружки
в канавках инструмента. Они должны иметь гладкие поверхности
с плавными переходами, что уменьшает возможность налипания на них стружки. Передние углы инструмента рекомендуются для сплавов первой группы 25...40°; для второй – 10...25°; для третьей – 10…15°.
Использование технологических сред наиболее эффективно при чистовой обработке, когда лимитирующим показателем обрабатываемости является шероховатость обработанной поверхности. Выше отмечалось, что резание алюминиевых сплавов сопровождается интенсивным наростообразованием. Поэтому для снижения шероховатости необходимо работать вне зоны нароста либо применять эффективные СОТС. Однако многие операции на современном оборудовании невозможно выполнять на режимах, исключающих наростообразование. Используемые на производстве СОТС на базе керосина или присадок с хлором, фосфором и другими элементами не всегда удовлетворяют санитарно-гигиеническим и противопожарным нормам.
При использовании эмульсий высокие требования к качеству обработанной поверхности не обеспечиваются. При ужесточении таких требований рекомендуется применять масляные СОЖ. В них можно добавлять специальные присадки, способствующие уменьшению трения и массопереноса за счет создания алюминийорганических и высокомолекулярных соединений на площадках контакта.
Обрабатываемость медных сплавов. Медь и ее сплавы находят широкое применение в современном машиностроении в качестве конструкционных, антифрикционных, электротехнических и других материалов.
С точки зрения обрабатываемости медные сплавы можно разбить на три группы: 1) сплавы с гомогенной структурой: латуни Л60, Л63, бронзы БрО4Ц3, БрКН1-3, БрА7 и др. К этой группе относится также медь; 2) сплавы с гетерогенной структурой типа ЛМц52-2, ЛЦ16К4, ЛЦ30А3, ЛЦ23А6Ж3Мц2, БрO10Ф1, БрА9Мц2Л,
БрАЮЖ3Мц2 и др.; 3) сплавы, содержащие свинец, – ЛС63-3, ЛЦ40С, БрО4Ц4С17, БрО5Ц5С5, БрС30 и др.
При обработке сплавов первой группы и красной меди образуется сливная вязкая и трудноломающаяся стружка. Это ухудшает условия работы при использовании автоматизированного оборудования и обработке отверстий (из-за пакетирования стружки в канавках инструмента). Сплавы второй группы также образуют сливную стружку, однако она менее прочная и значительно легче ломается. При резании свинцовистых сплавов образуется короткая хрупкая стружка, а в случае высокого содержания свинца – стружка надлома почти в виде пыли.
Процесс образования стружки при резании медных сплавов
в ряде случаев сопровождается ее интенсивными пластическими деформациями. В частности, толщина стружки может превысить толщину среза в 10 и более раз. Коэффициенты kа, kl зависят главным образом от структуры сплава. Наибольшие их значения характерны для гомогенных структур, наименьшие – для высокосвинцовистых
и гетерогенных сплавов высокой твердости.
При обработке медных сплавов в практически используемом диапазоне скоростей отсутствует нарост. Поэтому зависимости
kl = f (V), Рz = f (V) имеют монотонный характер, характерный для материалов, не склонных к наростообразованию. Уровень сил резания зависит от структуры и механических характеристик сплава. Так, при точении гомогенных сплавов и меди сила Рz может быть выше, чем при обработке конструкционных сталей, а для высокосвинцовистых гетерогенных сплавов – уменьшится примерно в 10 раз.
Обрабатываемость медных сплавов определяется температурой в зоне резания и истирающей способностью сплава:
1) присадка к меди любого элемента, образующего с ней твердый раствор (олова, алюминия, кремния), уменьшает VT в 3…4 раза вследствие резкого снижения теплопроводности материала и увеличения температуры резания в 1,6…2 раза;
2) присадка к медному сплаву никеля, который полностью растворяется в меди и не создает новой фазы, слабо влияет на VT;
3) переход от гомогенных структур к гетерогенным приводит
к понижению VT почти вдвое за счет истирающего действия твердых частиц эвтектоида; температура резания при этом изменяется незначительно;
4) создание новых фаз в гетерогенных сплавах практически не влияет на обрабатываемость; исключение составляют добавки свинца, которые за счет снижения истирающей способности материала
и снижения температур резания в 1,4…2 раза способствуют значительному возрастанию VT.
Приведенные закономерности позволяют определенным образом расположить медные сплавы по их обрабатываемости (табл. 22). При обработке медных сплавов с K м = 1 VT в 2…3 раза выше, чем при обработке чугунов и сталей. Обрабатываемость медных сплавов резко ухудшается при наличии в них шлаковых включений, а также микротрещин и других дефектов отливки.
Таблица 22
Коэффициенты обрабатываемости медных сплавов
№ п/п | Группа сплавов | k м |
Гетерогенные высокой твердости (НВ 150…200) | 0,7 | |
Гетерогенные средней твердости (НВ 100…140) | 1,0 | |
Гетерогенные свинцовистые | 1,7 | |
Гомогенные | 2,0 | |
Гомогенные с содержанием свинца: свыше 15 % менее 10 % | 4,0 12,0 | |
Красная медь | 8,0 |
Шероховатость поверхности при обработке медных сплавов
не зависит от скорости резания. Причиной является тот факт, что физические факторы резания (нарост, температура, процесс стружкообразования) влияют на формирование поверхностного слоя значительно меньше, чем подача и геометрические факторы (углы в плане, радиус вершины и т.д.).
В качестве технологических сред при обработке меди и ее сплавов рекомендуется использовать жидкости на водной основе
Аквол-12 (1,5...3%-ю), Укринол-1 (3... 10%-ю), НГЛ-205(5%-ю) или масла В-31, МР-2у, МР-8, индустриальное ИС-12. Хорошо зарекомендовали себя среды с присадками на базе серы, хлора, фосфора, являющиеся сильными окислителями.
Обрабатываемость жаропрочных, нержавеющих сталей
и сплавов. По своим физико-механическим свойствам жаропрочные, жаростойкие и нержавеющие стали и сплавы имеют много общего, что обусловливает их технологические качества. В зависимости от химического состава и с целью обеспечения удовлетворительной обрабатываемости резанием труднообрабатываемые стали и сплавы имеют различную структуру: ферритную, мартенситно-ферритную, аустенитную и аустенитно-мартенситную. В связи с этим стали подразделяются на классы (табл. 23). Например, жаропрочные и жаростойкие стали чаще всего относятся к аустенитному классу. Структура таких сталей представляет собой твердый раствор аустенита
с гранецентрированной кристаллической решеткой. Кроме того, большая часть деформируемых жаропрочных сплавов относится
к типу дисперсионно-твердеющих. Высокая дисперсность структуры повышает сопротивление ползучести сплавов и препятствует возникновению и развитию процессов скольжения.
Таблица 23
Классификация труднообрабатываемых сталей и сплавов
по их обрабатываемости резанием
Номер группы | Марка стали (сплава) | Термическая обработка | Временное сопротивление, Мпа | Краткая характеристика | Коэффициент обрабатываемости K м* |
I | 34ХН3М | Отжиг | Теплостойкие хромистые, хромоникелевые и хромомолибденовые стали перлитного и мартенситного классов | 0,8 | |
34ХН3МФ | Закалка и отпуск | ||||
20Х3МВФ (Эи415) | То же | ||||
Х6СМ | Отжиг |
Продолжение табл. 23
II | 12Х13 | Закалка и отпуск | Коррозионно-стойкие нержавеющие хромистые и сложнолегированные стали ферритного, мартенситно-ферритного и мартенситного классов | 0,65 | |
25Х13Н2 (ЭИ474) | Отжиг | 700… 1000 | |||
1Х12Н2ВМФ (ЭИ961) | Закалка и отпуск | ||||
20Х13 | То же | ||||
30Х13 | – «– | ||||
40Х13 | Нормализация и отпуск | ||||
14Х17Н2 (ЭИ268) | Закалка и отпуск | ||||
09Х16Н4Б | То же | ||||
07Х16Н6 | Нормализация и отпуск | ||||
23Х13НВМФЛ | Закалка и отпуск | ||||
ЭП311 | То же | ||||
III | 12Х18Н10Т | Закалка | Коррозионно-стойкие, кислотостойкие, жаростойкие хромоникелевые стали аустенитного и аустенитно-мартенситного классов | 0,5…0,4 | |
20Х23Н18 (ЭИ417) | То же | ||||
Х15Н5Д2Т | – «– | ||||
Х15Н9Ю (ЭИ904) | – «– | 850… 1100 | |||
12Х21Н5Т (ЭИ811) | – «– | ||||
Х17Н5М3 (ЭИ925) | Нормализация |
Продолжение табл. 23
IV | 45Х14Н14В2М (ЭИ96) | Закалка и старение | Жаропрочные, жаростойкие, кислотостойкие хромоникелемарганцовистые сложнолегированные стали аустенитного класса | 0,3 | |
08Х15Н24В4ТР | Старение | ||||
12Х25Н16Г7АР (ЭИ835) | Закалка и старение | ||||
37Х12Н8Г8МФБ (ЭИ481) | То же | ||||
10Х11Н20Т3Р (ЭИ696) | – «– | ||||
15Х18Н13С4ТЮ (ЭИ654) | Закалка | 700… 750 | |||
V | 36НХТЮ (ЭИ702) | Закалка и старение | Жаропрочные деформируемые сплавы на железоникелевой и никелевой основах | 0,16…0,075 | |
ХНЮВ (ЭИ868) | Закалка | ||||
ХН77ТЮ (ЭИ437А) | Закалка и старение | ||||
ХН35ВТЮ (ЭИ787) | То же | ||||
ХН56ВМТЮ | Закалка | ||||
ХН75МВЮ (ЭИ827) | Закалка и старение | ||||
ХН60МВТЮ | То же | ||||
ХН82ТЮМБ | – «– |
Окончание табл. 23
VI | ВЖ36-Л2 | Закалка и старение | Окалиностойкие и жаропрочные литейные сплавы на никелевой основе | 0,04 | |
АНВ-300 | То же | ||||
ЖС6К | – «– | ||||
ЖС3ДК | – «– | ||||
ХН67ВМТЮЛ | – «– |
* По сравнению со сталью 45. Если за эталон принять сталь Х18Н9Т (III группа), k м следует увеличить вдвое.
Худшая обрабатываемость жаропрочных и нержавеющих сталей и сплавов по сравнению со сталью 45 определяется их физико-механическими характеристиками, химическими свойствами, структурой, теплофизическими показателями. Рассмотрим некоторые свойства жаропрочных и нержавеющих материалов, затрудняющие их механическую обработку.
К таким свойствам относятся следующие.
1. Высокое упрочнение материала в процессе его деформирования резанием. Жаропрочные и нержавеющие стали чаще всего относятся к сталям аустенитного класса, имеющим кристаллиты с гранецентрированной кристаллической решеткой. Поэтому сплавы аустенитного класса характеризуются низким пределом текучести при том же временном сопротивлении, т.е. они весьма пластичны. Чем более пластичен материал, тем большие работу и силы резания надо затратить на снятие одного и того же объема такого материала. Исследования микротвердости корней стружки показали, что при точении стали Х18Н10Т она примерно в два раза больше, чем у недеформированного металла; относительное упрочнение для сплавов IV и V групп составляет 50...60 %, что значительно меньше, чем при обработке конструкционных материалов.
2. Жаропрочные и нержавеющие стали и сплавы имеют низкую теплопроводность по сравнению с конструкционными материалами (табл. 24). При их обработке выделяется значительное количество теплоты, резко возрастает уровень температур в зоне резания. Это способствует активизации адгезионных и диффузионных процессов, интенсифицирует изнашивание рабочих поверхностей инструментов, снижает уровень VT. Как следствие, использование твердых сплавов
Таблица 24
Теплопроводность различных материалов
Материал | Теплопроводность, Вт/м, °С | Материал | Теплопроводность, Вт/м, °С |
Медь | 0,0360 | Сплав ХН77ТЮ | 0,0019 |
Сталь 45 | 0,0040 | Сплав ЖС6К | 0,0017 |
Сталь ШХ15 | 0,0033 | Чугун СЧ10 | 0,0039 |
Сталь 2Х13 | 0,0027 | Твердый сплав ВК8 | 0,0055 |
Стал 12Х18Н9Т | 0,0023 | Твердый сплав Т15К6 | 0,0027 |
в качестве инструментального материала не всегда возможно, а применение быстрорежущих инструментов оправдано лишь при малых скоростях резания. При увеличении скорости температура резания превышает предел теплостойкости инструментального материала
и инструмент быстро выходит из строя. Повышению производительности обработки указанных материалов и уровня стойкости инструмента способствует применение соответствующе подобранных СОЖ.
3. Способность рассматриваемых материалов сохранять исходную прочность и твердость при повышенных температурах приводит к тому, что в процессе резания инструмент испытывает высокие удельные нагрузки. Весьма слабое разупрочнение жаропрочных
и нержавеющих материалов при нагреве до высоких температур приводит к тому, что на передней поверхности режущего инструмента действуют высокие удельные нагрузки (до 5000...9000 МПа), соответствующие нагрузкам, возникающим при обработке закаленных конструкционных сталей с 61...65 HRC. Этому обстоятельству способствуют значительно более высокие по сравнению с конструкционными сталями коэффициенты трения на контактных площадках, обусловленные интенсивным адгезионным взаимодействием. Высокое химическое сродство обрабатываемого и инструментального материалов вызывает их схватывание и даже разрушение контактных площадок. Наибольшую способность к адгезии имеют металлы, обладающие повышенной пластичностью, с атомными диаметрами, различающимися не более чем на 15...18 % (например, железо-хром, железо-медь).
4. Большая истирающая способность жаропрочных и нержавеющих сталей и сплавов обусловлена наличием в них, кроме фазы твердого раствора, еще и второй фазы, когда образуются интерметаллидные или карбидные включения. Последние, подобно абразиву, истирают инструмент, вызывая ускоренное изнашивание его кромок. В процессе пластической деформации жаропрочных и нержавеющих материалов происходит выделение карбидов, твердость которых приближается к твердости твердых сплавов гру
|
|
Эмиссия газов от очистных сооружений канализации: В последние годы внимание мирового сообщества сосредоточено на экологических проблемах...
Археология об основании Рима: Новые раскопки проясняют и такой острый дискуссионный вопрос, как дата самого возникновения Рима...
Механическое удерживание земляных масс: Механическое удерживание земляных масс на склоне обеспечивают контрфорсными сооружениями различных конструкций...
Архитектура электронного правительства: Единая архитектура – это методологический подход при создании системы управления государства, который строится...
© cyberpedia.su 2017-2024 - Не является автором материалов. Исключительное право сохранено за автором текста.
Если вы не хотите, чтобы данный материал был у нас на сайте, перейдите по ссылке: Нарушение авторских прав. Мы поможем в написании вашей работы!