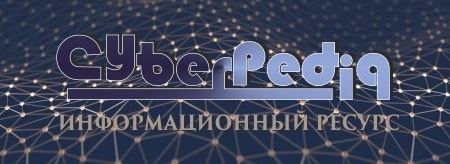
Таксономические единицы (категории) растений: Каждая система классификации состоит из определённых соподчиненных друг другу...
Историки об Елизавете Петровне: Елизавета попала между двумя встречными культурными течениями, воспитывалась среди новых европейских веяний и преданий...
Топ:
Теоретическая значимость работы: Описание теоретической значимости (ценности) результатов исследования должно присутствовать во введении...
Особенности труда и отдыха в условиях низких температур: К работам при низких температурах на открытом воздухе и в не отапливаемых помещениях допускаются лица не моложе 18 лет, прошедшие...
Интересное:
Аура как энергетическое поле: многослойную ауру человека можно представить себе подобным...
Подходы к решению темы фильма: Существует три основных типа исторического фильма, имеющих между собой много общего...
Наиболее распространенные виды рака: Раковая опухоль — это самостоятельное новообразование, которое может возникнуть и от повышенного давления...
Дисциплины:
![]() |
![]() |
5.00
из
|
Заказать работу |
|
|
Техническое обслуживание — это тот перечень работ, выполняемых в промежутках между плановыми и неплановыми ремонтами оборудования, который позволяет обеспечить необходимый уровень надежности работы оборудования.
Текущее техническое обслуживание (ежечасный, ежесменный осмотр и контроль, смазка и другая подобная работа) должно выполняться производственным персоналом цеха или участка.
Текущее или нерегламентированное техническое обслуживание включает в себя:
· четкое выполнение требований эксплуатации оборудования, указанных в технической эксплуатационной документации завода-изготовителя;
· отслеживание режима работы оборудования с предотвращением перегрузок;
· контроль температурного режима;
· контроль периодичности смазки во всех точках;
· моментальное отключение и обесточивание оборудования, вышедшего из строя;
· визуальный контроль изношенности узлов и механизмов;
Плановое техническое обслуживание и ремонт (по необходимости) выполняется персоналом ремонтной службы. В состав плановых традиционно включают работы, требующие разборки какого-либо узла оборудования. Конечно же, такую работу должен выполнять обученный рем. персонал.
Плановое или регламентированное техническое обслуживание выполняемое ремонтным персоналом, включают в себя:
· диагностику и контроль рабочих характеристик оборудования;
· наладку и регулировку;
· чистку рабочих органов и других мест, подверженных засорению;
· долив и замена масла, замена фильтров;
· определение нарушений в эксплуатации оборудования;
Техническое обслуживание должно по возможности выполнятся во время технических простоев оборудования. Как видно из перечисленного объема работ, техническое обслуживание предусматривает тщательную ревизию оборудования - проверку положения всех фиксированных и подвижных соединений, регулировку зазоров, контроль количества и качества топлива, масла, воды, а такие проверку работоспособности отдельных приборов, агрегатов и установки в целом. Для бурового оборудования техническое обслуживание необходимо выполнять также после завершения бурения очередной скважины для выявления возможности последующего использования оборудования. Тщательная ревизия оборудования должна быть завершающим этапом и монтажных работ на новом месте бурения.
|
Операции технического обслуживания выполняются, как правило, персоналом машины или установки (мотористом, механиком, оператором). Все выполненные работы, а также замеченные износы и прочие дефекты, заносятся в специальный журнал. Таким образом, накапливается материал для последующих ремонтов с учетом фактического состояния машины.
16. Система планово-предупредительного ремонта.
Детали, узлы и машина в целом по мере эксплуатации постепенно снижают уровень работоспособности от возникновения в них неполадок и износа. Неполадки (загрязнения, нарушение надежности и плотности соединений и регулировки) устраняются техническим обслуживанием машин, а износ их - только ремонтом.
Основой правильной эксплуатации машин является плановое обеспечение их обслуживанием и ремонтом, исключающее или сводящее к минимуму возможность внезапных отказов.
Широко применяется система планово-предупредительного обслуживания и ремонта машин (система ППР).
Система ППР - комплекс мероприятий по обслуживанию и ремонту машин, выполняемых профилактически по заранее составленному плану для поддержания машин в исправном и работоспособном состоянии.
Система ППР предусматривает следующие основные положения:
1) ремонт оборудования выполняется через планируемые промежутки времени, называемые межремонтными периодами;
|
2) после планового капитального ремонта характеристика оборудования приближается к паспортным данным нового оборудования;
3) в течение ремонтного цикла оборудование в строгой очередности проходит все плановые ремонты, предусмотренные системой;
4) кроме плановых ремонтов выполняется техническое обслуживание оборудования;
5) чередование, периодичность и объем обслуживания и ремонтов определяются назначением, конструкцией и условиями эксплуатации оборудования.
Техническое обслуживание - это комплекс операций по поддержанию работоспособности оборудования и обеспечению его технических параметров в процессе эксплуатации.
Техническое обслуживание, строго регламентируемое по времени и объему, выполняется по перечню обязательных операций, а ремонт планируется по времени и объему и выполняется в установленные планом сроки в объеме, который зависит от фактического состояния машины. Принципиальная схема системы планово-предупредительного обслуживания и ремонта машин представлена на рис. 3.1.
как видно из схемы, техническое обслуживание состоит из ежедневно выполняемых работ (ЕО) - очистка от грязи, осмотр и подтяжка ослабленных резьбовых соединений, проверка и наладка смазочных устройств, проверка действия контрольных, защитных и тормозных устройств, - и периодического технического обслуживания (ПО) - все операции ежедневного технического обслуживания, плюс смазка машины и смена масла в соответствии с картой смазки, мойка снаружи, проверка и регулировка отдельных частей и деталей, проверка и наладка всех систем управления и контроля.
Техническое обслуживание должно по возможности выполнятся во время технических простоев оборудования. Как видно из перечисленного объема работ, техническое обслуживание предусматривает тщательную ревизию оборудования - проверку положения всех фиксированных и подвижных соединений, регулировку зазоров, контроль количества и качества топлива, масла, воды, а такие проверку работоспособности отдельных приборов, агрегатов и установки в целом. Для бурового оборудования техническое обслуживание необходимо выполнять также после завершения бурения очередной скважины для выявления возможности последующего использования оборудования. Тщательная ревизия оборудования должна быть завершающим этапом и монтажных работ на новом месте бурения.
|
Операции технического обслуживания выполняются, как правило, персоналом машины или установки (мотористом, механиком, оператором). Все выполненные работы, а также замеченные износы и прочие дефекты, заносятся в специальный журнал. Таким образом, накапливается материал для последующих ремонтов с учетом фактического состояния машины. Ремонтные работы в зависимости от объема и сложности делятся па три категории.
Текущий ремонт (ТР) ставит задачей поддерживать работоспособность отдельных частей в целом исправной машины.
Объем и сложность операции ТР сравнительно невелики - проверка состояния оборудования, замела быстроизнашивающихся деталей, замен а при необходимости смазки, устранение всех дефектов, не требующее разборки сложных частей оборудования. Оборудование после ремонтных работ проверяют и регулируют. Текущий ремонт выполняется непосредственно па месте установки и эксплуатации оборудования.
Средний ремонт (СР) называют ремонт, при котором восстанавливается работоспособность важных частей машины, утраченная в результате естественного износа дета лей. Этот ремонт связан с значительным объемом сборочно-разборочных работ на основных агрегатах машины.
Средний ремонт стационарного тяжелого и громоздкого оборудования выполняется непосредственно на месте эксплуатации; для ускорения и облегчения работ максимально используются ранее отремонтированные на базе сменные детали и узлы (принцип узлового ремонта). Все ремонтные и монтажные работы выполняются разъездными ремонтными бригадами. используются передвижные ремонтные мастерские.
Капитальным (КР) называют ремонт, осуществляемый с целью восстановления исправности и полного, или близкого к полному, восстановления ресурса изделия с заменой или ремонтом любых его частей, включая базовые, и их регулировкой.
Здесь важно подчеркнуть, что система ППР предполагает использование при ремонте машин частично изношенных деталей. Следовательно, капитальный ремонт не всегда может обеспечить полное восстановление ресурса машины, что необходимо учитывать при разработке технических условий на ремонт.
|
Капитальный ремонт выполняется на ремонтных заводах или хорошо оснащенных крупных ремонтных базах. Иногда капитальный ремонт совмещается с работами по модернизации оборудования, например, меняется целиком или частично аппаратура централизованной смазки или запуска машины, при восстановлении отдельных ответственных деталей или узлов частично меняется конструкция, применяются более современные материалы и методы обработки, чтобы повысить долговечность деталей или узлов и перевести их в более высокую по износостойкости группу деталей.
17. Виды обслуживания машин и оборудования.
Длительная эксплуатация машины без поломок и аварий может быть достигнута при хорошем знании их устройства и соблюдении правил технического обслуживания и управления машиной.
Техническое обслуживание и ремонт машин, а также двигателей проводят по системе планово-предупредительного ремонта (ППР), при которой машины поступают в ремонт по плану, отработав установленное количество машино-часов.
Система ППР представляет собой комплекс организационно-технических мероприятий профилактического характера, проводимых периодически в плановом порядке и направленных на содержание машин в работоспособном состоянии.
Система ППР предусматривает выполнение всех видов технического обслуживания и ремонта — текущего, среднего и капитального.
Техническое обслуживание машин —это комплекс профилактических мероприятий, проводимых периодически с целыо предотвращения преждевременного износа или поломки деталей и узлов машин. Своевременное и высококачественное техническое обслуживание обеспечивает максимальную продолжительность межремонтного периода машин.
К операциям по техническому обслуживанию относятся очистка, мойка, смазка, осмотр машины; контроль технического состояния узлов, агрегатов, механизмов, приборов; основного и сменного рабочего оборудования и машин в целом; крепление деталей и частей, регулирование узлов и агрегатов; заправка, опробование отдельных узлов и всей машины.
В соответствии с объемом выполняемых работ техническое обслуживание разделяется на: – ежесменное, выполняемое регулярно перед началом смены, в течение и по окончании смены;
– периодическое техническое обслуживание ТО-1 и ТО-2, выполняемое после определенного числа часов работы машин.
Ежесменное обслуживание выполняют перед началом работы машины, в течение рабочего дня, между сменами и после окончания работы машины.
Перед началом работы необходимо:
1) проверить и долить систему питания смазки и охлаждения;
|
2) осмотреть крепления механизмов, подтянуть гайки и устранить обнаруженные дефекты;
3) тщательно проверить исправность рулевого управления и тормозов;
4) проверить состояние шин и давление воздуха;
5) проверить наличие и исправность инструмента;
6) пустить двигатель и проверить его работу на малых, средних и после прогрева на высоких оборотах коленчатого вала на холостом ходу, проверить манометр, термометры масла и воды, сигнал, стоп-сигнал и фары;
7) на ходу проверить действие муфты сцепления, коробки передач, тормозов и механизмов управления рабочими органами;
8) на ходу проверить работу рулевого управления.
В течение рабочего дня необходимо:
1) не менее двух раз внимательно осмотреть машину, затянуть ослабленные болты, проверить давление в шинах и устранить мелкие дефекты; 4
2) следить за состоянием машины и особенно узлов, подверженных износу и поломкам или требующих тщательного ухода и регулирования, не допускать работы механизмов с ненормальным шумом и стуком;
3) периодически проверять трущиеся поверхности и степень их нагревания;
4) следить за действием смазочных приборов, маслопроводов системы охлаждения, уплотнений и контрольных приборов;
5) следить за состоянием подшипников, не допуская их перегрева;
6) не допускать перегрева или переохлаждения двигателя, поддерживать необходимый уровень воды в радиаторе и масла в картере двигателя;
7) не допускать работы машины при неисправном топливном насосе или карбюраторе;
8)проверять работу фрикционных и тормозных лент, не допуская пробуксовывания;
9) при обнаружении дефекта, грозящего аварией, немедленно остановить машину и сообщить об этом механику или другому лицу, ответственному за эксплуатацию машин.
Между сменами необходимо:
1) тщательно очистить машину от пыли и грязи;
2) осмотреть машину и выявить повреждения или неисправности, а также устранить мелкие дефекты, записанные в журнале приема и сдачи смены;
3) проверить состояние доступных для осмотра крепежных деталей, шпоночных соединений и упорных колец;
4) устранить течь в маслопроводах гидросистемы, масло-топливопроводах;
5) отрегулировать фрикционы, тормоза и механизмы управления;
6) устранить все другие дефекты, обнаруженные при работе машины;
7) заправить машину горючим, маслом и водой (при необходимости);
8) проверить степень натяжения и определить состояние канатов, цепей, ременных передач и др.;
9) осмотреть состояние ходовой части;
10) осмотреть и проверить соединительные муфты и, при необходимости заменить негодные детали;
11) устранить неисправности защитных ограждений;
12) проверить и отрегулировать отдельные детали и узлы;
13) записать в журнале приема и сдачи смен дефекты, подлежащие устранению при очередном ремонте.
В конце смены следует:
1) очистить автогрейдер от пыли и грязи;
2) очистить -сетку радиатора и воздухоочиститель;
3) при работе в запыленном воздухе сменить масло в поддоне воздухоочистителя;
4) заправить дизельным топливом, предварительно промыв фильтр заливной горловины, прочистить отверстия в пробках;
5) проверить затяжку всех пробок для слива масла и контроля уровня масла.
При техническом обслуживании (ТО-1) следует:
1) выполнить все работы, предусмотренные ежесменным обслуживанием;
2) сменить масло в картере двигателя, промыв систему дизельным топливом;
3) промыть реактивную масляную центрифугу и проверить, как она вращается;
4) промыть масляный фильтр грубой очистки;
5) из фильтра-отстойника фильтра тонкой очистки топлива слить отстой и заполнить систему топливом;
6) бачок-компенсатор топливого манометра освободить от топлива, отсоединить трубку от дна бачка; при установке трубки на.место обратить внимание на герметичность соединения;
7) муфту сцепления проверить и при необходимости отрегулировать;
8), проверить и при необходимости отрегулирозать натяжение ремня вентилятора;
9) проверить и при необходимости отрегулировать зазоры клапанов двигателя;
10) сапун снять, промыть и установить на место, набивку сапуна разрыхлить и смазать маслом;
11) проверить щетки коллекторов электростартера и генераторов;
12) смазать подшипники генератора и электростартера;
13) смазать машину по таблице смазки.
При техническом обслуживании (ТО-2) следует:
1) выполнить все работы, предусмотренные ТО-1;
2) промыть закрепленные сетки воздухоочистителя дизельным топливом или керосином, для чего снять поддон, съемные кассеты и корпус воздухоочистителя;
3) слить отстой из корпуса фильтра тонкой очистки топлива и промыть фильтр;
4) промыть фильтр-отстойник;
5) в топливном насосе и его регуляторе заменить масло;
6) промыть систему охлаждения;
7) проверить осевой зазор в конических подшипниках заднего моста, балансиров и ходовых колес и при необходимости отрегулировать его;
8) отрегулировать рулевой механизм;
9) отрегулировать тормоза;
10) смазать машину по таблице смазки.
Таким образом, можно сделать вывод, что техническое состояние машины зависит от следующих факторов.
В начале работы машины трущиеся детали прирабатываются и нуждаются в особенно тщательной и более частой смазке, регулировании и внимательном уходе. Затем длительное время детали работают с оптимальными зазорами, однако также нуждаются в строгом выполнении всех мероприятий по уходу для поддержания рабочего состояния, предусмотренных инструкций. В предремонтный период зазоры увеличиваются, из-под трущихся поверхностей легко выжимается масло, появляется стук в сочленениях. Все это может привести к поломкам важных и дорогостоящих агрегатов. К этому времени смазывающие устройства, насосы, сальники работают хуже.
Техническое состояние машины зависит от условий работы, от прочности разрабатываемых грунтов и нагрузки на рабочий орган, от интенсивности загрузки машины в течение рабочего времени, от погоды и многих других факторов.
18. Классификация способов восстановления деталей.
Ремонт детали предусматривает восстановление ее работоспособности, первоначальной посадки, размеров, геометрической формы и взаиморасположения осей, прочности, твердости, герметичности и др.
Устранить одни и те же дефекты возможно различными способами, например изношенные места могут быть отремонтированы хромированием, металлизацией, наплавкой, механической обработкой и другими способами, и наоборот, — один и тот же способ ремонта может быть применен для устранения разных дефектов. Например, сварка применима для восстановления изношенных участков детали, заварки трещин, наплавки резьбы и др.
Эффективность и качество восстановления деталей существенно зависят от того, каким способом будет производиться работа по обеспечению необходимого уровня их потребительских свойств. Способы восстановления деталей подразделяются в зависимости от видов дефектов (рис. 1).
Механическую обработку применяют как самостоятельный способ восстановления деталей, а также в качестве операции при подготовке или окончательной обработке деталей, восстановленных другими способами. В качестве самостоятельных способов восстановления деталей механической обработкой используют обработку под ремонтный размер и постановку дополнительных ремонтных деталей (ДРД). Обработкой под ремонтный размер восстанавливают геометрическую форму, шероховатость и параметры точности изношенных поверхностей деталей. ДРД применяют в целях
Рис. 1. Классификация способов восстановления деталей
износа рабочих поверхностей деталей, а также при замене изношенных или поврежденных частей сложных деталей.
Пластическое деформирование применяют при восстановлении размеров деталей, их формы и физико-механических свойств.
Сварка предназначена для устранения механических повреждений деталей (трещин, отколов и др.), а наплавка — для нанесения металлических покрытий на поверхности деталей в целях компенсации их износа.
Напыление используют для нанесения металлических покрытий на изношенные поверхности восстанавливаемых деталей.
Гальванические и химические способы обработки предназначены для восстановления изношенных поверхностей деталей (хромирование, железнение, никелирование); для защиты деталей от коррозии (цинкование, бронзирование, оксидирование); для защитно-декоративных целей (хромирование, никелирование, цинкование, оксидирование); для придания поверхностям деталей специальных свойств, обеспечивающих хорошую прира-батываемость (меднение, лужение, свинцование, фосфатирова- ние), защиту от науглероживания при цементации (меднение), повышение электрической проводимости (меднение, серебрение), повышение отражательной способности (хромирование, никелирование), подслоя под другое покрытие (медь, никель) или грунта под окраску.
Электрофизические способы применяют в основном при обработке деталей, восстановленных нанесением покрытий с высокой твердостью, когда применение механической обработки нецелесообразно.
Представленные способы восстановления обеспечивают заданный уровень качества деталей, который достигают за счет правильного выбора способа, управления процессами нанесения покрытий и последующей обработки деталей. Основными управляющими факторами являются свойства исходных материалов, применяемых при нанесении покрытий, и режимы обработки.
19. Ремонт деталей методом механической обработки.
К механическим видам обработки относятся главным образом такие, которые связаны с применением лезвийного инструмента (в том числе и абразивного), а к электрическим — электрохимический, электроабразивный, электроконтактный, электроэрозионный и др.
Механическая обработка при ремонте и восстановлении деталей имеет много общего с обработкой, применяемой при изготовлении новых деталей. Например, цилиндрические наружные поверхности можно получить обтачиванием, шлифованием, притиранием, полированием и деформированием, а внутренние — сверлением, развертыванием, растачиванием, притиранием, хонингованием, шлифованием, прошивкой и др. Плоские поверхности получают строганием, фрезерованием, опиливанием, шабрением, шлифованием и полированием.
Однако при ремонте и восстановлении деталей машин эти процессы имеют и некоторые особенности: у деталей приходится снимать обработкой неравномерный по толщине слой металла, так как изношенные детали обычно имеют неправильную геометрическую форму, а после наращивания — разный по толщине припуск на обработку. Кроме того, после некоторых способов наращивания (например, электроимпульсный, гальванический, некоторые виды наплавки и др.) поверхностный слой детали обычно имеет высокую твердость, что требует использования особых режимов резания и инструмента.
Выбор установочных баз. Установочные базы (поверхности), определяющие положение обрабатываемой детали относительно инструмента, подразделяют на основные и вспомогательные. Основные базы — это поверхности, определяющие положение детали в комплектной группе. Вспомогательные базы — специально созданные поверхности, определяющие положение детали при обработке. Эти базы могут быть в виде поверхностей центровых отверстий, специальных поверхностей, поясков у отверстий и т. д. Например, у коленчатого вала основными базами являются коренные шейки и посадочные места под маховик и шестерню, вспомогательными базами — центровые отверстия или пояски у краев отверстий.
Рассверливание изношенных отверстий может осуществляться индивидуально, координатно или совместно в зависимости от технических требований.
Индивидуально отверстия рассверливают в том случае, когда несущественна точность их расположения относительно друг друга. У некоторых деталей оси всех отверстий как основной, так и сопрягаемой детали взаимосвязаны, смещение осей недопустимо и нельзя нарушить взаимозаменяемость. Такие отверстия рассверливают координатно с помощью кондукторов, сохраняя у них расстояния как между осями, так и от базовых поверхностей.
Совместное рассверливание применяют для деталей, скрепляемых болтами и имеющих установочные штифты. При износе отверстий под штифты (в задней балке, в кожухе муфты сцепления и др.) детали совмещают штифтами, скрепляют болтами, убирают штифты и совместно рассверливают или развертывают изношенные отверстия.
Развертывание изношенных отверстий применяют как конечную операцию после рассверливания или растачивания и как самостоятельную операцию при малых величинах припуска на обработку. На ремонтных предприятиях используют как нерегулируемые — для работы на станках, так и регулируемые развертки — для работы вручную.
Шлифование является наиболее распространенным способом чистовой обработки восстанавливаемых деталей, когда требуется получить точность 6, 7 и 8 квалитетов и шероховатость поверхности порядка 0,2...0,6 мкм.
После шлифования наружные цилиндрические поверхности можно обрабатывать (полировать) абразивными и алмазными бесконечными лентами на том же станке с помощью специального приспособления.
Полирование абразивными и алмазными бесконечными лентами дает возможность получить шероховатость поверхности выше исходной, обрабатывать не только основную цилиндрическую поверхность, но и радиусы перехода у галтелей.
Притирка пастами обеспечивает шероховатость поверхности от 0,08 мкм до 0,025 мкм и точность в пределах 1...3 мкм. Эту операцию применяют для удаления небольших износов с поверхности особо точных деталей (плунжерных пар), а также для точной подгонки одной детали к другой.
Процесс ведется притирами из перлитного чугуна с использованием паст Государственного оптического института (ГОИ), содержащих зерна окиси хрома.
Хонингование и суперфиниширование применяют для получения поверхности с малой шероховатостью. При хонинговании абразивные бруски закрепляют в головке, которая совершает вращательное и возвратно-поступательное движение. Хонингование используют для обработки внутренних поверхностей, например для обработки поверхности гильз и цилиндров, нижней головки шатуна и т. д. Шероховатость поверхности после хонингования подходящая. Наружные поверхности обрабатывают колеблющимися и одновременно движущимися вдоль вращающейся детали брусками (суперфиниширование). В процессе хонингования и суперфиниширования деталь обильно поливают охлаждающей жидкостью.
Алмазное хонингование применяют при обработке поверхностей стальных, чугунных деталей и чистовой обработке хромовых и железных покрытий. Алмазное хонингование улучшает чистоту поверхности на два класса и точность обработки в 1,5...2 раза по сравнению с абразивным.
Перспективными операциями для получения высокого класса чистоты и упрочнения при обработке поверхностей после наращивания являются также методы поверхностного пластического деформирования раскатками (шариковыми и роликовыми) или выглаживанием с помощью приспособлений.
При выглаживании упрочняется поверхностный слой и на 2...4 класса снижается шероховатость поверхности по сравнению с исходной. При выглаживании и упрочнении в качестве смазочно-охлаждающей жидкости используют масло. При алмазном выглаживании алмаз впаивается в оправу.
Восстановление и ремонт резьбовых поверхностей. Изношенные резьбовые поверхности на валах восстанавливают электродуговой или газовой наплавкой вручную с последующим нарезанием резьбы номинального размера. На валах с резьбой более можно применять вибродуговую наплавку по впадинам резьбы в среде пара без предварительной проточки. При ручной наплавке старую резьбу следует удалить проточкой для улучшения качества наплавленного слоя.
Изношенную резьбу в отверстиях деталей восстанавливают постановкой резьбовых спиральных вставок. Технология состоит из рассверливания резьбового отверстия на больший диаметр, нарезания резьбы в отверстии под резьбовую вставку, ввертывания спиральной вставки в отверстие детали монтажным ключом, удаления технологического поводка у вставки специальным бородком, контроля восстановленной резьбы.
Постановка резьбовых вставок увеличивает ресурс и надежность резьбовых соединений, особенно в алюминиевых и чугунных деталях.
Ремонтируют также изношенные резьбы на валах проточкой и нарезанием резьбы уменьшенного ремонтного размера, а в отверстии расточкой (или сверлением) и нарезанием резьбы увеличенного размера. При рассверливании, если допускается смещение оси отверстия, сверло направляют по старому отверстию. Если же ось нельзя смещать, то пользуются кондукторными приспособлениями. После нарезания резьчатая шпилька: ввертыша (пробки) в отверстия увеличенного размера ставят соответствующего размера болты или шпильки.
В ряде случаев, когда отверстие в сопрягаемой детали нельзя увеличить, шпильки изготовляют ступенчатыми. Если резьбу в отверстии на больший размер нарезать нельзя, устанавливают резьбовые пробки, в которых изготовляют резьбу номинального размера.
Изношенные резьбовые отверстия в стальных и алюминиевых деталях можно полностью заварить и обработать под номинальную резьбу. Для восстановления плотности резьбового соединения применяют клеи и составы на основе эпоксидных смол, вводя их в сопряжение при завертывании.
Ремонт трещин в корпусных деталях фигурными вставками. Технология постановки фигурных вставок состоит из подготовки детали под вставку, установки ее и зачистки отремонтированной поверхности.
Фигурные вставки в виде профилированной ленты из малоуглеродистой стали бывают двух видов: уплотняющие и стягивающие.
Электрические методы обработки. Для обработки высокотвердых поверхностей после наращивания (наплавка высокотвердыми электродами, порошковыми электродами, железнение, плазменное напыление, хромирование и др.) все большее распространение начинают получать электрические методы обработки.
Электрохимическая обработка — это процесс анодного растворения металла с поверхности детали. Процесс мало зависит от твердости, прочности и других механических свойств обрабатываемого металла.
20. Ремонт заменой элемента детали.
У значительного количества деталей сложной формы изношенными или поврежденными являются отдельные небольшие элементы детали: гладкие и резьбовые отверстия, шейки валов, места посадки подшипников качения в корпусных деталях, венцы шестерен и т. п. При этом целесообразным является удаление дефектного слоя металла или дефектного элемента детали и восстановление ее постановкой дополнительной ремонтной детали (ДР) — втулки, ввертыша, венца, шестерни — или заменой дефектного элемента детали.
Этот способ имеет несколько характерных случаев применения:
1) ремонт отверстий постановкой ремонтной втулки, гильзы или кольца;
2) ремонт валов напрессовкой втулки, кольца или постановкой полувтулок;
3) ремонт элементов детали разнообразной формы способом удаления дефектного и установки нового элемента детали: заменой зубчатого венца, шлицевой ступицы, шлицевого конца и др.;
4) ремонт плоских поверхностей постановкой планок или накладок.
Ремонт гладких отверстий постановкой ремонтной втулки является наиболее простым и распространенным способом. Примерами такого способа ремонта являются места посадки наружных колец подшипника качения в корпусах коробок передач, раздаточных коробках, ступицах колес, отверстия в сателлитах, чашке дифференциала и в проушинах шкворня моторного катка, отверстие в полумуфте асфальтоукладчика.
Гильзование блоков цилиндров легких и пусковых двигателей применяется тогда, когда диаметр цилиндра больше предельно установленных ремонтных размеров. Для этого цилиндр двигателя растачивают под гильзу с учетом толщины стенок гильзы 3—4 мм.
Заготовку гильзы изготовляют центробежной отливкой из серого или легированного титано-медистого чугуна (НВ 180—230) и подвергают механической обработке. При обработке наружного диаметра учитывается натяг величиной 0,05—0,10 мм. Внутренний диаметр гильзы должен иметь припуск на обработку ее после запрессовки в цилиндр. До запрессовки гильзу подвергают гидравлическому испытанию.
Ремонт валов постановкой втулок колец, полувтулок применяется при больших износах валов и наружных цилиндрических поверхностей деталей в тех случаях, когда другие виды ремонта (наварка, гальванопокрытия и др.) нецелесообразны или неприменимы.
Постановка полувтулок для восстановления размера вала применяется в тех случаях, когда ремонтируемый вал или цапфа недоступны для постановки целой втулки.
Постановка полувтулок является трудоемкой и дорогостоящей операцией, поэтому этот способ ремонта имеет ограниченное применение.
Способ ремонта заменой элемента детали применяется в тех случаях, когда на сложной детали с большим числом рабочих поверхностей одна или несколько поверхностей имеют чрезмерный износ, а остальные изношены незначительно. В этом случае изношенный элемент детали удаляют и заменяют вновь изготовленным. Заменяемый элемент с основной деталью соединяют резьбой или напрессовкой с последующей заваркой (замена венца звездочек компенсационной муфты моторных катков и асфальтоукладчика; замена изношенного венца на блоках шестерен и каретках коробки передач моторных катков, тракторов и других самоходных машин; замена изношенного стержня клапана двигателя приваркой нового стержня встык и др.).
Технологический процесс ремонта заменой части детали состоит из следующих основных этапов:
1. Удаление дефектной части детали и подготовка поверхности соединения. Если заменяется часть детали, термически обработанная (цементированная или закаленная), то перед механической обработкой необходимо произвести местный отпуск детали. Отпуск производится нагревом участка детали пламенем газовой сварочной горелки или т. в. ч.
2. Изготовление заменяемой части детали. Размеры этой части могут быть окончательными, без дальнейшей обработки или с припусками на обработку для тех поверхностей детали, которые требуют соблюдения соосности или точности взаиморасположения. Материал заменяемой части должен быть такой же, как у основной детали, или наиболее отвечающий условиям работы данного участка детали.
3. Соединение и закрепление заменяемой части с основной деталью. Детали могут быть соединены путем запрессовки, свертывания, приварки и т. п. Простым, надежным и экономичным способом соединения частей детали является стыковая сварка, при этом для снятия возникших в процессе сварки внутренних напряжений производят термообработку — нормализацию или отжиг.
Если заменяемая часть детали подлежит термообработке (например, венцы шестерен), то термообработка производится до постановки венца. Если термообработка детали должна быть произведена после установки ремонтной детали на основную, то нагревать детали для термообработки следует так, чтобы не произошло окисления окончательно обработанных поверхностей (нагрев в нейтральной или восстановительной среде, нагрев в соляных ваннах, электролитах и токами высокой частоты). Окончательная механическая обработка детали и контроль качества ремонта.
21. Механизированные способы сварки и наплавки.
Наиболее распространена наплавка под флюсом.
Флюс насыпают слоем толщиной 50—60 мм, и статическое давление слоя флюса на жидкий металл составляет 7—9 гс/см2. Этого незначительного давления достаточно, чтобы устранить нежелательные механические воздействия дуги на ванну жидкого металла, разбрызгивание * жидкого металла и нарушение формирования шва даже при очень больших силах тока.
Для наплавки под флюсом применяют электроды в виде одной или нескольких проволок диаметром 1—6 мм или электродной ленты толщиной 0,4—0,8 мм и шириной 20—100 мм.
Качество наплавленного металла, форма валиков, глубина проплавления металла изделия зависят от режима наплавки. При наплавке под флюсом получается однородный наплавленный металл, свободный от трещин и пор с гладкой поверхностью и плавным переходом от валика к валику.
Процесс наплавки легко контролировать и регулировать.
Наплавка металла под флюсом обеспечивает наиболее высокое качество наплавленного
|
|
Архитектура электронного правительства: Единая архитектура – это методологический подход при создании системы управления государства, который строится...
Историки об Елизавете Петровне: Елизавета попала между двумя встречными культурными течениями, воспитывалась среди новых европейских веяний и преданий...
Эмиссия газов от очистных сооружений канализации: В последние годы внимание мирового сообщества сосредоточено на экологических проблемах...
Автоматическое растормаживание колес: Тормозные устройства колес предназначены для уменьшения длины пробега и улучшения маневрирования ВС при...
© cyberpedia.su 2017-2024 - Не является автором материалов. Исключительное право сохранено за автором текста.
Если вы не хотите, чтобы данный материал был у нас на сайте, перейдите по ссылке: Нарушение авторских прав. Мы поможем в написании вашей работы!