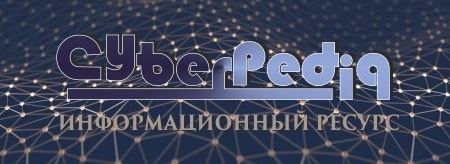
Адаптации растений и животных к жизни в горах: Большое значение для жизни организмов в горах имеют степень расчленения, крутизна и экспозиционные различия склонов...
Организация стока поверхностных вод: Наибольшее количество влаги на земном шаре испаряется с поверхности морей и океанов (88‰)...
Топ:
Определение места расположения распределительного центра: Фирма реализует продукцию на рынках сбыта и имеет постоянных поставщиков в разных регионах. Увеличение объема продаж...
Оценка эффективности инструментов коммуникационной политики: Внешние коммуникации - обмен информацией между организацией и её внешней средой...
Марксистская теория происхождения государства: По мнению Маркса и Энгельса, в основе развития общества, происходящих в нем изменений лежит...
Интересное:
Распространение рака на другие отдаленные от желудка органы: Характерных симптомов рака желудка не существует. Выраженные симптомы появляются, когда опухоль...
Что нужно делать при лейкемии: Прежде всего, необходимо выяснить, не страдаете ли вы каким-либо душевным недугом...
Искусственное повышение поверхности территории: Варианты искусственного повышения поверхности территории необходимо выбирать на основе анализа следующих характеристик защищаемой территории...
Дисциплины:
![]() |
![]() |
5.00
из
|
Заказать работу |
|
|
Прием машин или агрегата в ремонт.
Разборочные работы.
Мойка, обезжиривание деталей и удаление отложений.
Удаление нагара.
Дефектоскопия деталей.
Сортировка деталей.
Восстановление деталей ремонтными размерами.
Восстановление деталей постановкой дополнительных ремонтных деталей.
Прием машин в ремонт.
В ремонт машины принимаются в соответствии с существующими Едиными техническими условиями на сдачу в капитальный ремонт и выдачу из капитального ремонта машин, агрегатов и узлов. При сдаче машин в капремонт необходимо иметь наряд на ремонт, справу о техническом состоянии машин, паспорт для машин и двигателей ранее подвергавшихся капремонту. По результатам приема составляют приемо-сдаточный акт.
Разборочные работы.
Перед разборкой машины моют горячей водой под давлением до 1,5…2,0 МПа. Это обеспечивает надлежащие условия последующих работ по демонтажу агрегатов и узлов. После этого выполняют очистительные операции. Так, разборку агрегатов производят после наружной очистки и обезжиривания с выпариванием острым паром емкостей для масла двигателя, коробки передач и т.д. Подразборка агрегатов производится на тупиковых постах, полная разборка производится как на тупиковых постах, так и на поточных линиях в зависимости от сложности агрегата.
Мойка, обезжиривание деталей и удаление отложений.
Для обезжиривания деталей применяют различные растворы. После обезжиривания детали ополаскивают горячей водой, что предохраняет их от коррозии. Имеются в широком ассортименте синтетические поверхностные моющие средства, которые не вызывают коррозии черных и цветных металлов, не оказывают вредного воздействия на кожу и одежду, поэтому детали после их обезжиривания не нуждаются в ополаскивании. Процесс обезжиривания ведется при невысоких температурах. Для обезжиривания используют такие вещества как сульфонол, керосин и бензин с последующей промывкой жидким маслом (веретенным).
|
Для мойки и обезжиривания деталей применяют различные моечные установки и машины.
Удаление нагара.
Нагар откладывается на ряде деталей двигателя: на стенках камер сгорания, на тарелках клапанов, во впускном и выпускном трубопроводе и др. Нагар образуется вследствие неполного сгорания топлива и масла.
Для удаления нагара применяют щелочные растворы. Детали, имеющие нагар, погружают в ванну с температурой раствора 80 – 90° С на 40 – 60 мин. Часто для очистки деталей от нагара применяют косточковую крошку. Установка, используемая для этой цели, по принципу действия аналогична пескоструйной. Жировые загрязнения превращаются в эмульсию, уносимую моющим раствором.
Дефектоскопия деталей.
Дефектоскопия – методика и способы обнаружения дефектов деталей без нарушения их целостности. Дефекты деталей классифицируют в зависимости от причин их появления последующим их признакам: дефекты, вызванные недостатком конструкции детали; дефекты, связанные с нарушением технологии изготовления; дефекты, появляющиеся вследствие недостатков технологического процесса изготовления детали; дефекты в результате естественного изнашивания; дефекты, возникающие из-за нарушений инструкции по эксплуатации машин; дефекты аварийного характера.
Недостатком конструкции могут быть: выбор материала, несоответствующего условиям работы детали, назначение размеров не соответствующих нагрузочным режимам, неправильный выбор сопряжений, термообработки, покрытий, смазки и т.д.
Нарушениями технологии изготовления деталей могут быть: неправильная замена материала, отклонение от предусмотренных посадок сопрягаемых мест, нарушение термообработка и т.д.
|
Недостатком технологии изготовления является операция старения с целью снятия внутренних напряжений при отливке или штамповки, отсутствие операции старения корпусных деталей и т.д.
Дефекты аварийного характера появляются из-за внутренних пороков или усталости материала детали.
Сортировка деталей.
В результате дефектоскопии все детали сортируют на три группы: годные, требующие ремонта и непригодные. Каждую группу маркируют краской определенного цвета. Годные детали направляют на комплектацию агрегатов, требующих ремонта, в соответствующие цехи для ремонта, а негодные детали – в утиль.
На все детали, прошедшие контроль, составляют дефектовочную ведомость, в которой указывают общее количество одноименных деталей, а также количество годных, требующих ремонта и негодных деталей.
Требованием эксплуатации к конструкции агрегата является примерно равная износостойкость его деталей. Желательно, чтобы кривые протекания износов всех деталей главного агрегата укладывались в возможно более узкую зону диаграммы (она заштрихована).
В этом случае после истечения ремонтного цикла все детали данного агрегата будут нуждаться в ремонте одновременно, в период же межремонтного пробега агрегат будет работать надежно.
Детали, подлежащие восстановлению, направляют в соответствующие производственные цехи.
Дефекты деталей делятся на три основные группы:
- естественные износы, при которых происходят изменения геометрической формы и размеров сопрягаемых поверхностей деталей;
- механические повреждения (деформации, трещины, обломы, выкрашивания, надиры, пробоины);
- повреждения антикоррозионных покрытий и коррозия металла деталей.
Ремонт деталей ремонтными размерами. Суть этого способа заключается в следующем. Если номинальный размер изнашивающейся части детали, например шейки вала, больше минимального размера по прочности детали, определенного конструктором расчетным или экспериментальным путем, то такая изношенная часть может быть отремонтирована снятием с нее некоторого минимально необходимого слоя металла в целях устранения нарушений (вследствие износа) правильной геометрической формы. После такой операции изношенная часть детали будет иметь правильную геометрическую форму и она пригодна для дальнейшей работы.
|
Следовательно, ремонтным размером называется такой размер, который будет иметь износившаяся часть детали после снятия с нее механической обработкой слоя металла, необходимого для придания этой части детали правильной геометрической формы с учетом припуска на обработку.
Способ основан на применении механической обработки (точение, шлифование и др.) и имеет ряд преимуществ: обеспечивает взаимозаменяемость сопрягаемых деталей в пределах данного ремонтного размера, позволяет организовать массовый выпуск заменяемой детали на заводах, упрощает технологию восстановления сопрягаемой более сложной детали, снижает стоимость и сокращает время восстановления.
Величину нормализованного ремонтного размера устанавливают в зависимости от величины и характера износа поверхности, а также от припуска на механическую обработку, который должен быть минимальным.
|
|
Общие условия выбора системы дренажа: Система дренажа выбирается в зависимости от характера защищаемого...
Двойное оплодотворение у цветковых растений: Оплодотворение - это процесс слияния мужской и женской половых клеток с образованием зиготы...
Историки об Елизавете Петровне: Елизавета попала между двумя встречными культурными течениями, воспитывалась среди новых европейских веяний и преданий...
Особенности сооружения опор в сложных условиях: Сооружение ВЛ в районах с суровыми климатическими и тяжелыми геологическими условиями...
© cyberpedia.su 2017-2024 - Не является автором материалов. Исключительное право сохранено за автором текста.
Если вы не хотите, чтобы данный материал был у нас на сайте, перейдите по ссылке: Нарушение авторских прав. Мы поможем в написании вашей работы!