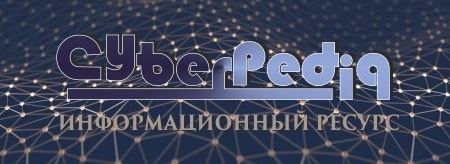
Общие условия выбора системы дренажа: Система дренажа выбирается в зависимости от характера защищаемого...
Семя – орган полового размножения и расселения растений: наружи у семян имеется плотный покров – кожура...
Топ:
Марксистская теория происхождения государства: По мнению Маркса и Энгельса, в основе развития общества, происходящих в нем изменений лежит...
История развития методов оптимизации: теорема Куна-Таккера, метод Лагранжа, роль выпуклости в оптимизации...
Выпускная квалификационная работа: Основная часть ВКР, как правило, состоит из двух-трех глав, каждая из которых, в свою очередь...
Интересное:
Наиболее распространенные виды рака: Раковая опухоль — это самостоятельное новообразование, которое может возникнуть и от повышенного давления...
Берегоукрепление оползневых склонов: На прибрежных склонах основной причиной развития оползневых процессов является подмыв водами рек естественных склонов...
Лечение прогрессирующих форм рака: Одним из наиболее важных достижений экспериментальной химиотерапии опухолей, начатой в 60-х и реализованной в 70-х годах, является...
Дисциплины:
![]() |
![]() |
5.00
из
|
Заказать работу |
|
|
Симплификация – форма стандартизации, заключающаяся в уменьшении количества типов или других разновидностей изделий до числа, достаточных для удовлетворения существующих в данное время потребностей. В объекты симплификации не вносят каких-либо технических усовершенствований.
Упорядочение как управление многообразием связано, прежде всего, с сокращением этого многообразия. В него входят систематизация и классификация.
Систематизация предметов, явлений или понятий преследует цель расположить их в определенном порядке и последовательности, образующей четкую систему, удобную для использования. Наиболее простой формой систематизации является алфавитная система расположения объектов (энциклопедические и политехнические справочники, библиографии и т.п.). Применяют порядковую нумерацию систематизируемых объектов, например, при регистрации ГОСТов в Госстандарте, или расположение их в хронологической последовательности. Для систематизации параметров и размеров машин, их частей и деталей рекомендуются ряды предпочтительных чисел.
Классификация является разновидностью систематизации. Она преследует цель расположить предметы, явления или понятия по классам, подклассам и разрядам в зависимости от их общих признаков. Чаще всего классификация проводят по десятичной системе. На ее основе действует единая десятичная система классификации продукции (ЕДСКП). Все множество продукции делят на 100 классов в соответствии с отраслями производства и конкретизируют ее по свойствам и назначению. Затем каждый класс делят на 10 подклассов, каждый подкласс на 10 групп, каждую группу на 10 подгрупп и каждую подгруппу на 10 видов. Каждый вид может включать 9999 конкретных наименований продукции.
|
Параметрическая стандартизация
Данный метод применяется для установления рациональной номенклатуры изготавливаемых изделий с целью унификации, повышения серийности и развития специализации их производства. Для этого разрабатывают стандарты на параметрические ряды этих изделий.
Параметрический ряд – закономерно построенная в определенном диапазоне совокупность числовых значений главного параметра изделий одного функционального назначения и аналогичных по кинематике или рабочему процессу.
Главный параметр изделия определяет важнейший эксплуатационный показатель изделия, например, грузоподъемность для грузового автомобиля, максимальные габаритные размеры обрабатываемых заготовок для токарного станка, этот параметр не зависит от технических усовершенствований изделия и технологии изготовления.
Главный параметр служит базой для определения числовых значений основных параметров. Основные параметры определяют качество изделий, например, в случае металлорежущего оборудования это точность обработки, мощность, пределы скоростей резания, производительность.
Разновидностью параметрического ряда является типоразмерный (или просто размерный) ряд, его главный параметр – размеры изделий.
На базе параметрических (типоразмерных) рядов создают конструктивные ряды конкретных типов (моделей) изделий одинаковой конструкции и одного функционального назначения. В большинстве случаев числовые значения параметров выбирают из рядов предпочтительных чисел, в машиностроении наиболее часто используют ряд R 10 (рисунок 2.1). По этому ряду установлены номинальные мощности электрических машин, приняты диаметры дисковых фрез (50, 63, 80, 100 мм).
Рисунок 2.1 – Параметрический ряд кривошипных прессов, построенный
по развиваемому усилию на ползуне
Унификация
Унификация (от лат. unio – единство и facare – делать, т. е. приведение чего – либо к единообразию, к единой форме или системе) – это приведение объектов одинакового функционального назначения к единообразию (например, к оптимальной конструкции) по установленному признаку и рациональное сокращение числа этих объектов на основе данных об их эффективной применяемости.
|
В основе унификации рядов деталей, узлов, агрегатов, машин и приборов лежит их конструктивное подобие, которое определяется общностью рабочего процесса, условий работы изделий, т. е. общностью эксплуатационных требований. Унифицированные изделия, их составные части и детали должны обладать полной взаимозаменяемостью по показателям качества (или совместимостью) и по присоединительным размерам.
Унификации подлежат также другие виды продукции, в том числе марки материалов и их размеры, инструмент, технологическая оснастка, а также методы испытания и контроля, документация, процессы, нормы, требования, обозначения и т. д.
Различают следующие виды унификации: типоразмерную, внутриразмерную и межтиповую.
Типоразмерная унификация применяется в изделиях одинакового функционального назначения, отличающихся друг от друга числовым значением главного параметра (так, унифицированы токарно-винторезные станки для обработки заготовок диаметром 250 – 1250 мм, рисунок 2.2).
Рисунок 2.2 – Единый конструктивно-унифицированный ряд токарно-винторезных станков для обработки деталей диаметром 250 – 1250 мм
Внутритиповая унификация осуществляется в изделиях одного и того же функционального назначения, имеющих одинаковое числовое значение главного параметра, но отличающихся конструктивным исполнением составных частей (так, степень унификации двигателей ЯМЗ составляет 80 – 95%).
Межтиповая унификация проводится в изделиях различного типа и различного конструктивного исполнения. Например, унификация продольно-фрезерных, строгальных, шлифовальных станков между собой на основе стандартной ширины обрабатываемых заготовок, установленных по ряду R 10 (800, 1000, 1250 и 1600 мм). Это позволяет для всех указанных станков применять 45% унифицированных узлов (стойки, станины, поперечины и др.).
Работы по унификации могут проводиться на следующих уровнях: заводском, отраслевом, межотраслевом и международном.
Уровень унификации изделий или их составных частей определяется с помощью системы показателей, из которых обязательным является коэффициент применяемости на уровне типоразмеров, рассчитываемый в процентах:
|
%,
где n – общее количество типоразмеров изделий; n о – количество оригинальных типоразмеров.
Применение унификации позволяет заметно уменьшить объем конструкторских работ и сократить сроки проектирования; уменьшить время на подготовку производства и освоения выпуска новой продукции; повысить объем выпуска продукции за счет специализации, а также качество выпускаемой продукции.
Агрегатирование
Агрегатирование – метод создания машин, приборов и оборудования из отдельных стандартных, унифицированных узлов, многократно используемых на основе геометрической и функциональной взаимозаменяемости.
Агрегатирование обеспечивает расширение области применения машин, приборов, оборудования разного функционального назначения путем их компоновки из отдельных узлов, изготовленных на специализированных предприятиях. Эти агрегаты должны обладать полной взаимозаменяемостью по всем эксплуатационным показателям и присоединительным размерам.
Большое распространение получили агрегатные станки, состоящие из унифицированных элементов. На рисунке 2.3 показана типовая компоновка агрегатного металлорежущего станка модели 11А234, предназначенного для сверления отверстий, снятия фасок и нарезания резьбы в тормозном барабане автомобиля. При смене объекта производства такие станки легко разобрать и из тех же агрегатов собрать новые станки для обработки других деталей.
Принцип агрегатирования широко используется при создании стандартной, переналаживаемой оснастки, изготавливаемой из стандартных узлов, деталей и заготовок.
Примером могут служить универсально-сборные приспособления (УСП). Такие приспособления компонуют из окончательно и точно обработанных взаимозаменяемых элементов: угольников, стоек, призм, опор, прихватов, зажимов, крепежных деталей и др.
На рисунке 2.4 показан поворотный кондуктор для сверления равномерно расположенных по окружности отверстий в заготовке 5, которая базируется плоскостью и отверстием на плиту 4 и палец 2 и закрепляется с помощью быстросменной шайбы 6. Плита 4 размещена на диске поворотно-делительного механизма, состоящего из поворотной головки 1, делительного диска 3 и фиксатора.
|
Поворотная головка установлена в поворотных кронштейнах 13. Кондукторная планка 8 с втулкой 7 с помощью опор 9, 11, 12 и планки 10 прикреплена к кронштейнам 13 на опорах 14.
Внедрение унификации и агрегатирования позволяет перейти от конструирования и производства необоснованного оригинального и дорогого оборудования и машин к созданию и выпуску на их основе проверенных оптимальных унифицированных агрегатов. При этом в создаваемых компоновках обеспечиваются оптимальные эксплуатационные показатели, а сроки проектирования и освоения новой техники сокращаются с 4 – 6 до 1,5 – 2 лет. Затраты на проектирование и освоение серийного производства снижаются в 1,5 – 2 раза, себестоимость изготовления машин уменьшается на 25 – 30%. Агрегатирование упрощает эксплуатацию изделий, сокращает их металлоемкость и расходы на ремонт.
Типизация
Типизация – метод стандартизации, заключающийся в установлении типовых объектов для данной совокупности, применяемых за основу (базу) при создании других объектов, близких по функциональному назначению.
Типизация развивается в трех основных направлениях: стандартизация типовых технологических процессов; стандартизация типовых конструкций изделий общего назначения; создание нормативно-технических документов, устанавливающих порядок проведения каких-либо работ, расчетов, испытаний и т.п.
Типизация конструкции изделий – разработка и установление типовых конструкций, содержащих общие для ряда изделий, их составных частей и деталей конструктивные параметры. На основе анализа уже существующие типов и типоразмеров изделий, их составных частей и деталей, сопровождающего процесс типизации, также могут быть разработаны новые перспективные типы и типоразмеры изделий, их составные части и детали.
Типизация технологических процессов – разработка технологического процесса для производства однотипных деталей или сборки однотипных составных частей или изделий той или иной классификационной группы. Типизации технологических процессов предшествует установление типовых представителей обрабатываемых деталей или собираемых объектов, обладающих наибольшим числом признаков данной классификационной группы.
Типовой технологический процесс должен быть общим для группы деталей, иметь единый план обработки по основным операциям, однотипное оборудование и оснастку. При разработке типового технологического процесса за основу может быть взят наиболее совершенный действующий технологический процесс или спроектирован новый.
|
|
|
Особенности сооружения опор в сложных условиях: Сооружение ВЛ в районах с суровыми климатическими и тяжелыми геологическими условиями...
Типы оградительных сооружений в морском порту: По расположению оградительных сооружений в плане различают волноломы, обе оконечности...
История развития хранилищ для нефти: Первые склады нефти появились в XVII веке. Они представляли собой землянные ямы-амбара глубиной 4…5 м...
Состав сооружений: решетки и песколовки: Решетки – это первое устройство в схеме очистных сооружений. Они представляют...
© cyberpedia.su 2017-2024 - Не является автором материалов. Исключительное право сохранено за автором текста.
Если вы не хотите, чтобы данный материал был у нас на сайте, перейдите по ссылке: Нарушение авторских прав. Мы поможем в написании вашей работы!