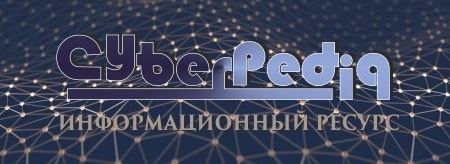
Кормораздатчик мобильный электрифицированный: схема и процесс работы устройства...
Индивидуальные и групповые автопоилки: для животных. Схемы и конструкции...
Топ:
Комплексной системы оценки состояния охраны труда на производственном объекте (КСОТ-П): Цели и задачи Комплексной системы оценки состояния охраны труда и определению факторов рисков по охране труда...
Характеристика АТП и сварочно-жестяницкого участка: Транспорт в настоящее время является одной из важнейших отраслей народного хозяйства...
Особенности труда и отдыха в условиях низких температур: К работам при низких температурах на открытом воздухе и в не отапливаемых помещениях допускаются лица не моложе 18 лет, прошедшие...
Интересное:
Искусственное повышение поверхности территории: Варианты искусственного повышения поверхности территории необходимо выбирать на основе анализа следующих характеристик защищаемой территории...
Влияние предпринимательской среды на эффективное функционирование предприятия: Предпринимательская среда – это совокупность внешних и внутренних факторов, оказывающих влияние на функционирование фирмы...
Как мы говорим и как мы слушаем: общение можно сравнить с огромным зонтиком, под которым скрыто все...
Дисциплины:
![]() |
![]() |
5.00
из
|
Заказать работу |
|
|
Сортамент швеллерных и угловых гнутых профилей включает большое количество различных профилеразмеров. При необходимости использовать тот или иной профилеразмер перед разработкой технологии его производства следует выявить возможность его изготовления методом профилирования с учетом требований существующих стандартов, а затем оценить возможность изготовления профиля на имеющемся оборудовании.
Толщина и ширина заготовок, а также высота формовки профиля должны соответствовать технической характеристике стана. Вначале определяют разме-ры прямолинейных участков поперечного сечения и сравнивают ширину каждого из них с толщиной. Если эти участки имеют ширину меньше пяти-кратной толщины для швеллеров и восьмикратной толщины для угловых профилей, изготовление их профилированием нецелесообразно ввиду невоз-можности получения профилей без поперечного изгиба по стенкам и полкам.
При выборе стана для холодной формовки необходимо сравнить раз-меры профиля, заготовки, механические свойства материала, из которого должен изготавливаться профиль с техническими возможностями профиле-гибочного агрегата, предполагаемого для его производства. Например, швеллер 80×80×4 мм из стали марки Ст3 можно изготовить на профи-легибочном стане 2÷7×80 ÷ 500, а профиль с такими же размерами из стали марки 35ХГСА не может быть изготовлен на нём, так как эта сталь имеет высокие прочностные свойства: σв > 70 кгс/мм2. Стан же допускает изготовление профилей из стали у которой σв ≤ 60 кгс/мм2 .
Угловой профиль 200×200×5 мм можно изготовить на стане 2÷7×80÷500, а швеллер с такой же шириной полок нельзя, так как максимальная высота формовки на этом стане составляет всего 160 мм и подогнуть полки шириной 200 мм на угол 90° в стане невозможно. Профили с шириной исходных заготовок более 500 мм и менее 80 мм не могут быть изготовлены на стане 2÷7×80÷500, так как широкая заготовка не размещается на валках, а рулоны узкой полосы не удерживаются в вертикальном положении центрирующими устройствами разматывателя.
|
Перед расчётом калибровки необходимо определить размеры профиля с учётом допускаемых отклонений. Учёт допусков позволит правильно выбрать начальные размеры валков и возможные пределы их изменения при переточке. Кроме того, правильно выбранные размеры позволяют полностью использовать, все поле допуска. Например, швеллер 160×100×6 мм по ГОСТ 8278 – имеет допуск по высоте стенки ±2,0 мм . Если валки будут рассчитаны на номинальный размер 160 мм , то минусовый допуск не будет использован. Кроме того, диапазон возможной регулировки валков сокращается в два раза и в связи сэтим значительно усложняется настройка стана.
Величину радиусов мест закруглений выбирают минимально возможной. Ширину полок обычно принимают равной номинальному размеру. Режим профилирования определяется исходя из размеров заготовки, формы и размеров готового профиля, а также учитывается технологический процесс формовки: непрерывный или поштучный. Примерные режимы профилирования для изготовления швеллеров и уголков приведены на рисунке 15.20.
Рис.15.20- Режимы профилирования швеллеров (1) и уголков (2) стан 2-7×80÷500
Как показал опыт поштучного процесса формовки, гнутые профили, изготовленные указанным способом, имеют нестабильные размеры поперечного сечения по длине. На переднем конце, как правило, полки завалены внутрь профиля, а на заднем развалены наружу. Для устранения указанных дефектов и получения профилей со стабильными геометрическими размерами по всей длине, в калибровках валков применяют метод «двойного перегиба», сущность которого заключается в том, что, при профилировании, после подгибки полок профиля до угла, меньшего на 2–3° окончательного угла на профиле, производят разгибку на 8–10° в сторону, обратную подгибке. После этого производят догибку полок до необходимого угла профиля. Такой метод позволяет значительно уменьшить отклонения размеров как на концевых участках, так и в средней части профиля. Одной из причин получения гнутых профилей с неточными геометрическими размерами поперечного сечения является предельное относительно оси валков смещение заготовки в процессе формовки и неправильный захват ее валками в момент входа в калибр при поштучном профилировании.
|
Часто смещение полосы по ширине калибра происходит при профилирова-
нии серповидных заготовок и несимметричных профилей. Опыт производства гнутых профилей показал, что отклонения размеров подгибаемых элементов от номинальных получаются в первых клетях до суммарного угла подгибки 30–40°. После деформации на этот угол полоса приобретает достаточную поперечную жёсткость, уменьшается возможность её отклонения от прямолинейности. Большой суммарный угол подгибки элементов профиля обеспечивает фиксацию переднего конца полосы при заходе в калибр. В этом случае до начала формовки полоса под действием верхнего валка принимает правильное положение относительно оси профилирования. Для надёжного удержания полосы от поперечного смещения, в валках первых формующих клетей применяют закрытые калибры (рис.15.21).
Рис.15.21 - Закрытые калибры для профилирования швеллеров
Ширина калибров определяется по формулам:
для первой клети
Вк1 = Взаг + 1 мм; (1)
для последующих клетей
Вкп=0,5(Вn+Вп-1), (2)
где Взаг – ширина исходной заготовки;
Вп-1 Вп – ширина проекции сечения формуемой полосы в осевой плоскости валков соответственно (п–1) - й и п-й клетей.
Ширину калибров, закрытых цилиндрическими буртами нижних валков, нельзя принимать равной ширине полосы в осевом сечении валков. Для уменьшения зазора между буртами калибра и полосой и удержания полосы от поперечного смещения при углах подгибки более 30° применяют закрытые калибры с наклонными буртами. В калибрах такого типа угол закрытия калибра равен углу подгибки (рис.15.22).
|
Калибры с наклонными буртами надёжно удерживают полосу в осевом на-правлении валков, но при заходе в калибр её положение не фиксируется, что приводит к неправильному захвату и, вследствие этого, к переформовке мест из-
Рис.15.22 - Калибровка валков для производства уголков (25÷50)×(25÷50)×2,5 мм
гиба или развальцовке кромок полосы. Этот недостаток можно устранить применением калибров, закрытых буртами верхних валков, имеющими криволинейную поверхность. Такие калибры обеспечивают постоянные зазоры между кромкой
полосы и поверхностью буртов и надёжно фиксируют полосу при её заходе в калибр и выходе из него. Недостатком такой конструкции калибров является сложность их изготовления, поэтому на практике применяют калибры, закрытые буртами конической формы (клети № 5 и 6).
Уголки и швеллеры целесообразно изготовлять на станах с соотношением основных диаметров валков Dов / Dон >1. Врез калибра осуществляется в тело верхнего валка, подгибка полок – вверх. Для создания оптимального скоростного режима в калибрах, обеспечивающего минимальное проскальзывание заготовки по поверхности валков, на наиболее нагруженных участках, формующих места изгиба, следует так располагать профиль в валках, чтобы формовка мест изгиба осуществлялась участками валков, лежащими на окружностях основных диаметров или близкими к ним.
Перед расчётом калибровки валков необходимо определить величины радиусов мест изгиба по проходам, исходя из ширины криволинейных участков по формуле:
(3)
где b - ширина дуги места изгиба;
α – суммарный угол подгибки в данном проходе;
d - толщина полосы;
х - коэффициент, зависящий от соотношения радиуса изгиба к толщине.
Значения коэффициента смещения нейтральной оси х в зависимости от соотношения радиуса изгиба к толщине полосы составляет:
R/d 0,65–1,0 1,1–1,5 1,6–2,0 2,5—3,5 4 и более
|
х 0,3 0,35 0,4 0,45 0,5
Расстояние между центрами дуг мест закруглений во всех проходах принимается постоянным:
Bст =H–2(R1+d), (4)
где H – высота профиля.
Учёт пружинения металла калибровкой валка при формовке швеллеров производится в предпоследней клети. Эта клеть изготавливается с выпуклой средней частью нижнего валка и вогнутой верхнего валка. Расчёт величины выпуклости и её радиуса производится из условия, что угол между стенкой и полками в валках предпоследней клети равен 90°. Последняя формующая клеть имеет валки без выпуклости и вогнутости и поэтому регулировкой зазора между ними можно регулировать перегиб полок профиля и величину угла между полками и стенкой.
Величина стрелы прогиба может быть определена в соответствии со схемой (рис.4) по формуле:
(5)
где Δh – стрела прогиба;
а - длина хорды;
α – центральный угол, соответствующий дуге.
Радиус закругления выпуклой части валка определяется по формуле:
(6)
Рис.15.23 - Схема для определения стрелы прогиба валков
Такой способ учёта пружинения металла позволяет регулировать размеры профиля в зависимости от марки стали, из которой он изготавливается. Учёт пружинения металла при формовке уголков производится за счёт угла освобождения полок в калибре валков последней формующей клети, который принимается равным 10 – 15'. Изменением зазора между валками, калибр которых имеет углы освобождения, можно регулировать величину угла между полками уголка в пределах ±2°.
Расчёт основных размеров валков для изготовления швеллеров и уголков производится в соответствии с размерами профиля по проходам и режимом профилирования. Размеры валков для формовки швеллеров определяются в соответствии с рисунком 15.24, а угловых профилей – 15.25.
Рис.15.24 - К определению размеров валков при профилировании
швеллерных профилей
Рис.15.25 - К определению размеров валков профилирования угловых профилей.
Ширина цилиндрического участка нижнего валка:
B=bст+2c, (7)
где: с=(R+d)tgα/2; bст – ширина стенки в данном переходе;
R -внутренний радиус в месте изгиба;
d – толщина профиля;
α – угол подгибки в данном переходе.
Ширина конусного участка нижнего валка:
В1= b+ b1 +b2, (8)
|
где: B = (c+bn+bдоп)cosα=[(R+d)tgα/2+bn+(5÷10)] cosα;
b1=R1sinα; b2=10÷20 мм (выбирается конструктивно).
Формующий диаметр нижнего валка:
Dо.н. =kD¢о.н., (9)
где k = 1,0 ÷ 1,004 – коэфф., учитывающий натяжение полосы между клетями.
D'о.н. – диаметр цилиндрического элемента нижнего валка предыдущей клети.
В случае профилирования без натяжения (k=1) катающие диаметры всех нижних валков принимаются одинаковыми.
Диаметр конусного участка нижнего валка:
Dб.н =Dо.н +2h=Dо.н +2(h1+h2), (10)
где: h1=[(R+d)tgα/2+bn+(5÷10)]sinα; h2=R1(1–cosα).
Формующий диаметр верхнего валка:
Dо.в =i Dо.н , (11)
где: i – передаточное отношение цилиндрической пары шестеренной клети.
Диаметр конусного элемента верхнего валка:
Dб.в = Dо.н+ Dо.в– Dо.н+2(d–δ), (12)
где: δ – зазор между валками по буртам.
Ширина конусного элемента:
B3=B1+c+B5 (13)
Ширина цилиндрического элемента верхнего валка:
B4=B+2B1–2B3 (14)
Размер В3– выбирается из условий термической обработки и составляет 25–30 мм для валков с диметром не более 350–400 мм и 35–40 мм для валков с диаметром более 400 мм.
Расчёт калибровки валков для изготовления угловых профилей имеет некоторые особенности. Основной диаметр верхнего валка проходит по вершине гребня, а на нижнем он находится в точке пересечения образующей нижнего конусного участка и радиуса закругления мест изгиба, проведенного через точку сопряжения образующей конусной части с закруглением верхнего валка.
Верхний валок изготовляется цельным, а нижний составным из двух частей. Углы освобождения на верхних валках не применяют, за исключением последней клети, где этот угол использован для учета пружинения полосы.
Размеры валков для изготовления угловых профилей определяют в соответствии со схемой (рис.15.25)следующим образом.
Ширина наклонного участка калибра на нижнем валке:
bк=m+n+bn+k, (15)
где: m=(R+d)tgα;
n =π/180(R+xd)(45–α) – запас металла в полке для формовки места закругления в последующих клетях;
bn = bk – (m + n + k) – ширина прямолинейного участка полки;
k –участок захода полосы в валки, размер которого принимается не менее: k ≥ (m + n +bn)(cosαn – cosαn-1).
Ширина калибра нижнего валка:
2Вк = 2bк cos α. (16)
Ширина калибра верхнего валка:
Bк. в =2(bкcosα-ctgα) (17)
Глубина калибра нижнего валка:
Нк = bк sin α. (18)
Полная ширина валка:
В3=2(В1+В2)+Вкb, (19)
где – В1 – ширина канавки под выход шлифовального камня принимается конструктивно, исходя из имеющегося оборудования для шлифовки валков;
В2 – ширина бурта для настройки, которая принимается равной не менее 15 мм из условия удобства настройки валков.
Минимальный диаметр нижнего валка:
Dн =Dф.н –2x, (20)
где: x=(R+d) .
Диаметр бурта нижнего валка Dбн=Dн+2Hк (21)
Формующий диаметр верхнего валка Dфн =Dфн i, (22)
где i – передаточное число цилиндрической пары шестеренной клети.
Диаметр бурта верхнего валка:
Dб.в =Dф. н –2Hк +2(R+d)(1/cosα–1).
Остальные размеры элементов валков, указанные на рис.5 и 6 выбирают конструктивно или рассчитывают с учётом имеющихся станков, размеров заготовок и условий термической обработки. Материалом для валков служит легированная сталь марок 9ХС, Х12Ф, 9Х, 9ХФ, Х12Н1.
При изготовлении корытных профилей наибольшее применение получила схема формовки с одновременной подгибкой боковых стенок и полок при параллельном горизонтальном их расположении. Во избежание переформовки элементов корытных профилей рабочие валки в первых клетях с суммарными углами подгибки до 30° выполняют с закрытыми калибрами.
При разработке калибровки валков первоначально определяют ширину отдельных элементов профиля и полную ширину его развёртки. Затем в соответствии с принятым режимом формовки определяют размеры калибров валков. Переходные формы профиля по клетям рассчитывают исходя из условия постоянства ширины разверток мест изгиба, т. е. исходя из принципа переменной величины радиусов закруглений. Расчёт остальных размеров переходных форм профиля и элементов валков осуществляют с помощью простых геометрических формул.
Рис.15.26 - Калибровка валков швеллера 130×135×8мм
На рис. 15.27 приведена схема технологических переходов при изготовлении корытного профиля 100×100×55×5 мм. Для компенсации пружинения металла
в предчистовой клети стенку профиля изгибают таким образом, чтобы линия,
перпендикулярная к боковой стенке калибра образовала с горизонталью угол, равный углу пружинения. В последней чистовой клети стенка выправляется и необходимые углы между элементами профиля могут быть получены соответ-
ствующей настройкой валков. Угол пружинения принимается с учётом свойств профилируемого металла и составляет 2–4°.
В настоящее время корытные профили изготовляют на агрегатах с соотношением Dов / Dо.н > 1 осуществляя врез калибра в тело верхнего валка. В результате проведенных исследований [1] установлено, что корытные профили целесообразно изготовлять на агрегатах с соотношением Dо.в / Dо.н = 1. При этом цилиндрические участки верхних валков, осуществляющие подгибку крайних полок, а также цилиндрические участки нижних валков, формующие стенку профиля, следует выполнять свободно вращающимися на подшипниках скольжения или качения
Рис.15.27 - Переходные формы поперечного сечения корытного
профиля 100×100×55×5мм
1.Тришевский И.С., Юрченко А.Б., Марьин В.С, и др. Производство гнутых профилей. Оборудование и технология. М.: Металлургия, 1982.384 с.
|
|
Механическое удерживание земляных масс: Механическое удерживание земляных масс на склоне обеспечивают контрфорсными сооружениями различных конструкций...
История создания датчика движения: Первый прибор для обнаружения движения был изобретен немецким физиком Генрихом Герцем...
Эмиссия газов от очистных сооружений канализации: В последние годы внимание мирового сообщества сосредоточено на экологических проблемах...
Индивидуальные и групповые автопоилки: для животных. Схемы и конструкции...
© cyberpedia.su 2017-2024 - Не является автором материалов. Исключительное право сохранено за автором текста.
Если вы не хотите, чтобы данный материал был у нас на сайте, перейдите по ссылке: Нарушение авторских прав. Мы поможем в написании вашей работы!