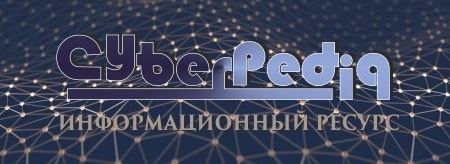
Поперечные профили набережных и береговой полосы: На городских территориях берегоукрепление проектируют с учетом технических и экономических требований, но особое значение придают эстетическим...
Индивидуальные и групповые автопоилки: для животных. Схемы и конструкции...
Топ:
Марксистская теория происхождения государства: По мнению Маркса и Энгельса, в основе развития общества, происходящих в нем изменений лежит...
Характеристика АТП и сварочно-жестяницкого участка: Транспорт в настоящее время является одной из важнейших отраслей народного...
Выпускная квалификационная работа: Основная часть ВКР, как правило, состоит из двух-трех глав, каждая из которых, в свою очередь...
Интересное:
Мероприятия для защиты от морозного пучения грунтов: Инженерная защита от морозного (криогенного) пучения грунтов необходима для легких малоэтажных зданий и других сооружений...
Как мы говорим и как мы слушаем: общение можно сравнить с огромным зонтиком, под которым скрыто все...
Что нужно делать при лейкемии: Прежде всего, необходимо выяснить, не страдаете ли вы каким-либо душевным недугом...
Дисциплины:
![]() |
![]() |
5.00
из
|
Заказать работу |
|
|
Для получения качественного гнутого профиля важное значение имеет определение точной ширины заготовки. Рассчитанную ширину проверяют по развёртке готового профиля вдоль его нейтрального слоя. Расположение нейтрального слоя определяют с помощью следующих формул:
а) если радиус внутреннего угла загиба r больше толщины заготовки
h - по средней линии:
Rразг = r + h / 2 (рис. 15.12);
Рис.15.12 - К определению ширины заготовки
б) если радиус внутреннего угла меньше толщины металла:
Rразг = r + h / 3;
в) при абсолютной величине радиуса внутреннего угла менее 0,5 мм
Rразг = (0,15 - 0,3) h (меньшее значение принимают для большей толщины и меньшего радиуса).
При изгибах в открытых калибрах необходимо учитывать развальцовку заготовки, которая может достигать 2% ширины. В закрытых калибрах развальцовку можно не учитывать. Изгиб с маленьким внутренним углом (при r < 0,5 мм) невозможно выполнить без предварительной подготовки, которую выполняют или развальцовкой места изгиба (рис.15.13, а) или выдавливанием канавки (рис.15.13, б).
а) б)
Рис. 15.13 – Развальцовка заготовки в местах изгибов
Профилирование в непрерывных станах (рис.15.14) заключается в постепен-
ном пластическом изгибе полосы от клети к клети с изменением формы поперечного сечения заготовок и, практически без изменения их площади. Этот процесс
Рис.15.14 – Схема профилирования в непрерывном профилегибочном стане
подобен валковой формовке полосы в трубную заготовку, отличаясь лишь формой конечных профилей. Конструкции профилегибочных станов аналогичны непрерывным трубоформовочным. Они содержат ряд клетей с горизонтальными приводными валками, калибровка которых обеспечивает получение заданного профиля. Не приводные вертикальные ролики, установленные между горизонтальными валками, препятствуют упругому пружинению наклонных участков профиля, а при больших углах наклона этих участков производят дополнительный пластический изгиб.
|
Калибровки валков для производства гнутых профилей можно разделить на четыре основные схемы:
- одновременную, при которой сразу формуются элементы профиля;
- последовательную, при которой вначале формуются крайние участки, а затем – средние или наоборот;
- комбинированную, при которой вначале последовательно формуются крайние участки профиля, а затем - средние или наоборот;
- специальную, при которой для достижения требуемых качественных показателей применяются специальные приёмы.
Применение той или иной схемы для изготовления конкретного профиля обусловлено рядом факторов. Помимо основного требования - производства продукции высокого качества в соответствии с требованиями нормативно-технической документации, принятая схема калибровки должна обеспечивать соотношение технологических параметров с точки зрения их экономичности, а именно: количество и конструкция клетей; профилировка и стойкость валков; удобства настройки и перевалки валков; производительность и качество продукции и.т.д.
По одновременной системе калибровки валков формуются все профили с одним местом изгиба - уголки (рис.15.15, а). По этой системе, как при поштучном, так и при непрерывном способе производства формуются также все симметричные профили открытой формы с двумя местами изгиба - швеллеры (рис.15.15, б), тремя местами изгиба (рис. 15.15, в, г), четырьмя местами изгиба — корытные профили (рис15.15, д).
Рис.15.15 – Схемы калибровки валков для производства гнутых профилей
В некоторых случаях при изготовлении швеллеров с малой степенью не симметричности, зетовых равнополочных и несимметричных профилей с четырьмя и пятью местами изгиба (рис.15.15, е) при непрерывном процессе профилирования также применяется одновременная система калибровки валков. Использование одновременной системы при непрерывном профилировании несимметричных профилей обеспечивает стабильность процесса и четкое выполнение элементов поперечного сечения; затруднения вызываются необходимостью устранения продольного скручивания и боковой кривизны на готовых профилях.
|
Одновременная система калибровки валков меняется в ряде случаев для изготовления гофрированных гнутых профилей (рис.15.15, ж) из материалов с легко нарушаемой поверхностью - сплавов на базе алюминия, сталей с цинковым и лакокрасочным защитным покрытием, нержавеющих сталей и т. п., обеспечивая высокие качественные показатели готовых изделий.
Поверхность гофрированных профилей, изготовленных по этой системе, получается без вмятин, царапин и надрывов. Такие нарушения поверхности фор-муемого металла часто наблюдаются при использовании других систем калибровки. Однако комплект валков для изготовления гофрированного профиля по одновременной системе весит на 35 - 45% больше, чем по другим системам.
Зетовые профили в большинстве случаев формуются по последовательной системе калибровки валков (рис.15.15, з). Преимуществом этой системы являются стабильность процесса профилирования и возможность устранения продольного скручивания в процессе формовки.
Последовательная система калибровки валков может применяться при изготовлении полузакрытых и замкнутых профилей с тремя и четырьмя местами изгиба (рис.15.15, и) при непрерывном процессе формовки. По этой системе вначале формуются полки, а затем боковые стенки профиля. Так же такая система может применяться также при изготовлении гнутых профилей с шестью и более местами изгиба. Наибольшее распространение такая система получила при изготовлении гофрированных гнутых профилей. Для их производства, как при непрерывном, так и при поштучном профилировании применяется последовательная система калибровки валков с формовкой вначале центрального гофра, а затем соседних гофров (рис.15.15, к), или центрального гофра и элементов соседних гофров (рис.15.15, л). Последовательная система используется при изготовлении курированных профилей из рядовых, конструкционных и низколегированных сталей и обеспечивает высокие качественные показатели продукции при наименьшей (по сравнению с другими системами) массе комплекта валков. Комбинированная система калибровки валков широко применяется для изготовления несимметричных профилей с двумя - пятью местами изгиба, а также полузакрытых и замкнутых профилей.
|
У несимметричных швеллеров (рис.15.15, м) как при штучном, так и при непрерывном процессе вначале формуются оба места изгиба (с различными углами подгибки) до окончательной формовки меньшей полки, а в последних проходах -только место изгиба у большей полки. Такая система позволяет устранять продольное скручивание профиля в процессе формовки. Недостатком сисиемы является неустойчивость процесса профилирования в последних клетях, когда формуется только одно место изгиба.
Комбинированная система калибровки валков даёт наилучшие результаты при изготовлении замкнутых и полузакрытых профилей с тремя (рис.15.15, н) и четырьмя (рис.15.15, о) местами изгиба. По этой системе вначале последовательно формуются полки до определенного угла α, а затем боковые стенки до угла подгибки β; в последних переходах все места изгиба формуются одновременно. Применение такой системы обеспечивает высокое качество профилей и устойчивость процессов профилирования. Для изготовления гофрированных профилей комбинированные системы калибровок валков не используются.
Специальная система калибровки валков используется для изготовления гофрированных гнутых профилей высокого качества (рис.15.15, п). По этой системе в первых клетях предусматривается формовка волнистой заготовки, из которой в последних клетях осадкой изготавливают профили типа ребристых плит. Использование в качестве промежуточной заготовки волнистого профиля обеспечивает минимальное утонение металла в местах изгиба и повышенные механических свойств изделий.
Сортовые гнутые профили могут быть изготовлены осадкой волнистой заготовки. При этом в первых проходах формуется волнистый профиль (рис.15.15, д) из криволинейных элементов которого в последних клетях осадкой формуются прямолинейные участки и места закруглений. Процес формировании профиля непрерывный, так как заготовка одновре-менно взаимодействует со всеми парами валков. На современных агрегатах процес формования заготовки може производиться в бесконечном режиме путём сваривания отдельных рулонов и порезкой бесконечного профиля на требуемые размеры летучими ножницами или пилами.
|
Суть процесса профилирования заключается в последовательном приближении листовой или полосовой заготовки до заданой формы профиля, путём последовательных подгибов без изменения размеров поперечного сечения. Последовательное приближение осуществляется образованием промежуточных форм в каждой паре формующих валков (рис.15.16).
Рис. 15.16 - Схема формирования корытного профиля
Рассмотрим процесс профилирования в двух смежных парах валков. В первуй паре заготовка подгибается на j, в другой – на угол a, а угол b - суммарний угол подгибки (рис.15.17, а). Изменение угла j на величину a происходит пос-
а) б)
Рис. 15.17 – Схема профилирования полосы
а) в двух смежных парах валков; б) однократной подгибки
тепенно на участке АВ. Участок АВ, который влияет на схеми напряжено - деформированого состояния при профилировании называют участком плавного перехода.В отличие от процесса прокатки, при профилировании линейная скорость всех точек поперечного сечения постоянка. В процессе подгибки точка В, расположенная на кромке заготовки перемещается на угол a (положение точки В1, но при наличии жёсткого конца, точка В останется в плоскости, перпендикулярной поперчному сечению заготовки. Поэтому кромка АВ увеличится до раз мера АВ1 (рис.15.16, б), а относительное удлинение кромки составит:
=
. (15.2)
Величина относительного удлинения находиться в пределах упругой деформации, то есть:
(15.3)
где s – растягивающие напряжения; Е – модуль жёсткости.
Величина растягивающих напряжений и относительного удлинения кромок увеличивается при увеличении ширины отгибаемого участка а и угла отгибки a и уменьшается при увеличении длины участка при увеличении длины участка плавного перехода L. Для обеспечения движения формируемой полосы по стану, каждая пара валков, кроме сил, затраченных на деформацию должна осуществлять втягивающую силу. В этом случае полная величина растягивающих напряжений составит:
. (15.4)
Если величина растягивающих напряжений превыысит проедел прочности, возникнет пластическое растяжение кромки, что приведёт к браку.
|
1.4. Выбор режима формообразования
Режим формовки, характеризуемый углами подгибки и радиусами кривизны мест изгиба профилируемой заготовки, имеет решающее значение для обеспечения требуемого качества профиля при минимальных затратах.
Суммарным углом подгибки αс считается центральный угол, опирающийся на криволинейный участок сечения профиля.
Угол подгибки в данном проходе Δα п характеризуется разностью суммарных углов подгибки в рассматриваемом α п и предшествующем αп-1переходах Δαп= α п – (α п -1). Подгибка может быть двусторонней (а) и односторонней (б) (рис.15.18). При двусторонней подгибке, когда криволинейный участок профиля
а) б)
Рис.15.18. Схемы подгибки
расположен по обе стороны от основной оси профиля, угол подгибки считается не суммарный угол 2 Δα п , а только половина его Δα п. С увеличением угла подгибки за проход параметры напряженно-деформированного состояния металла профиля возрастают и, при достижении определенных значений в местах изгиба металл значительно утоняется, а вдоль кромок профиля возникают гофры.
В связи с этим назначать оптимальный режим формовки следует с учетом параметров напряженно-деформированного состояния и механических свойств металла, размеров заготовки и элементов профиля, системы калибровки валков и, технологического процесса профилирования (непрерывного или поштучного).
При непрерывном процессе профилирования можно применять более жёсткие режимы, чем при поштучном, и, следовательно, меньшее число рабочих клетей.
При непрерывном профилировании вход полосы в валки происходит только в начале профилирования при настройке стана. Дефекты, возникающие при больших углах подгибки, возникают только на переднем конце профиля, которой впоследствии отрезается. Подгибаемый элемент профиля (полка) на участке плавного перехода подвержен продольной знакопеременной деформации (растяжению - сжатию и изгибу), в результате чего происходит поворот материальных точек на нормалях к серединной поверхности. Наибольшая продольная деформация происходит в поверхностных слоях полосы, а минимальная — во внутренних.
Металл серединных слоев на большей части ширины подгибаемого элемента со стороны места изгиба продольно сжат. Затем по мере приближения к кромкам деформация сжатия металла уменьшается до нуля и переходит в деформацию растяжения у кромок. На участке плавного перехода подгибаемые элементы практически не удлиняются, а даже укорачиваются. В процессе профилирования возникает волнистость (гофрированность) вдоль кромок вследствие уменьшения длины подгибаемого элемента вблизи мест изгиба по сравнению с его длиной вдоль кромок.
Вследствие неравномерной по ширине элемента продольной деформации и даже при отсутствии продольного растяжения — сжатия, возможно появление волнистости вдоль кромок или продольного изгиба профиля.
Если на готовом профиле после формовки в валках длина вдоль кромок окажется большей, чем вдоль участка изгиба, даже при уменьшении длины всех элементов профиля по сравнению с длиной исходной заготовки, то в зависимости от геометрических характеристик элементов профиля возможно коробление (гофрированность) на плоских участках.
В связи с этим при расчете режима профилирования учитывалось распределение продольной деформации по всей ширине профиля. Углы подгибки участков профиля за один проход принимают в зависимости от ширины подгибаемого участка, толщины профилируемой полосы, способа формовки в рабочих валках, вспомогательных роликах или направляющих линейках, основываясь на имеющемся опыте производства аналогичных профилей.
Величины углов подгибки в зависимости от ширины подгибаемого элемента. принимаемые за один проход при непрерывном процессе профилирования, приведены в табл.1 и. табл.2 ,
При выборе технологических переходов следует руководствоваться данными, приведенными в табл.1-2, и возможностью получения профиля в валках простых форм без использования вспомогательных роликов и направляющих линеек.
Таблица 1 - Углы подгибки для профилей толщиной до 2мм
Ширина подгибаемого элемента | Угол подгибки, град | ||||
α1 | α2 | α3 | α4 | α5 | |
<5 5…15 ≥15 | 45 30 20 | 90 60 55 | 80 75 | 93 93 | 90 90 |
Таблица 2 - Углы подгибки в зависимости от толщины заготовок
Инструмент | Угол подгибки, град, при толщине, мм | ||
0,5…0,8 | 0,8…1,2 | 1,2…1,5 | |
Рабочие валки | 45 | 30 | 22 |
Вспомогательные вертикальные ролики | 30 | 20 | 15 |
Формующие линейки | 20 | 15 | 12 |
Таблица 3 - Углы подгибки за один проход.
Профиль | Клеть | Угол подгибки, град, при профилировании | |
Поштучном | Непрерывном | ||
Дверная коробка | Первые Промежуточные Последние | 8…10 12…14 8…12 | 8…12 15…20 8…12 |
Вторым важным технологическим параметром, определяющим режим профилирования, является радиус закругления переходных форм.
Места изгиба полосы по клетям формировались с переменным и с постоянными радиусами и расстояниями между центрами дуг мест закруглений. При профилировании полос с постоянными радиусами и расстояниями между центрами начало изгибаемого участка лежит в начале закругления готового профиля, ближе к середине полосы, и подгибка ведется от начала участка к периферии.
В той же последовательности осуществляется подгибка при переменных радиусах кривизны, но с постоянным расстоянием между их центрами.
При формовке полос с постоянными или переменными радиусами и переменным расстоянием между их центрами начало изгибаемого участка лежит ближе к периферии профиля, и подгибка ведется от периферии к середине профилируемой полосы. При этом расстояние между центрами радиусов уменьшается.
Переменные радиусы, мм, по проходам определяют по формуле:
(1.4)
При формовке с постоянными радиусами кривизны радиусы закругления на рабочем инструменте для толщин более 1,5 мм принимаются на 1 мм меньше предусмотренных технологией.
Для получения минимально допустимых радиусов кривизны в местах изгиба профиля валки изготавливают без полученных по расчету закруглений, углы на валках только слегка притупляются.
Для лучшего выполнения мест закругления профиля и обеспечения большей стойкости валков без переточек калибровку валков рассчитывают из условия постоянства ширины мест изгиба, а затем уменьшают расчетный радиус до конечного во всех технологических переходах.
Расстояние между центрами дуг мест изгиба по проходам при формовке с постоянными радиусами (рис.4).
Рис.15.19 - Схема для определения расстояния между центрами дуг:
(1.5)
где: Сп — расстояние между центрами дуг места изгиба в данном проходе;
Ск — расстояние между центрами дуг мест изгиба в готовом профиле;
ρ1, ρ2 —радиусы кривизны нейтрального слоя деформации в местах изгиба;
αп1, α п2 — углы подгибки в данном проходе, град.
Применение постоянных радиусов при формовке позволяет получить более точную геометрию готового профиля, но при этом требуется большее усилие при профилировании. Использование для формовки переменных радиусов уменьшает нагрузку на валки, но несколько ухудшает геометрию профиля.
|
|
История создания датчика движения: Первый прибор для обнаружения движения был изобретен немецким физиком Генрихом Герцем...
Общие условия выбора системы дренажа: Система дренажа выбирается в зависимости от характера защищаемого...
Наброски и зарисовки растений, плодов, цветов: Освоить конструктивное построение структуры дерева через зарисовки отдельных деревьев, группы деревьев...
Состав сооружений: решетки и песколовки: Решетки – это первое устройство в схеме очистных сооружений. Они представляют...
© cyberpedia.su 2017-2024 - Не является автором материалов. Исключительное право сохранено за автором текста.
Если вы не хотите, чтобы данный материал был у нас на сайте, перейдите по ссылке: Нарушение авторских прав. Мы поможем в написании вашей работы!