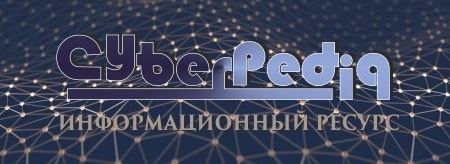
Эмиссия газов от очистных сооружений канализации: В последние годы внимание мирового сообщества сосредоточено на экологических проблемах...
Наброски и зарисовки растений, плодов, цветов: Освоить конструктивное построение структуры дерева через зарисовки отдельных деревьев, группы деревьев...
Топ:
Оценка эффективности инструментов коммуникационной политики: Внешние коммуникации - обмен информацией между организацией и её внешней средой...
Генеалогическое древо Султанов Османской империи: Османские правители, вначале, будучи еще бейлербеями Анатолии, женились на дочерях византийских императоров...
Интересное:
Аура как энергетическое поле: многослойную ауру человека можно представить себе подобным...
Как мы говорим и как мы слушаем: общение можно сравнить с огромным зонтиком, под которым скрыто все...
Подходы к решению темы фильма: Существует три основных типа исторического фильма, имеющих между собой много общего...
Дисциплины:
![]() |
![]() |
5.00
из
|
Заказать работу |
|
|
Лопастные насосы отличаются по коэффициенту быстроходности
или удельной величиной частоты вращения
Это критерии подобия лопастных насосов.
Конструктивно насосы делятся:
- одноступенчатые;
- многоступенчатые;
- с колесами двустороннего входа.
В насосах двухстороннего входа преимущества: нет осевых усилий на подшипник.
Основные причины выхода из с троя насадочного оборудования и методы профилактики:
1) Интенсивный износ уплотнений в коррозионно –активных средах, в средах с твёрдыми включениями и абразивными частями.
Методы профилактики:
а) замена сальников торцовыми уплотнениями;
б) использование запирающих жидкостей для предотвращения утечек перекачиваемой среды.
2) Кавитационный и эрозионный износ лопастей под действием твёрдых включений в жидкости.
Методы профилактики:
а) для эрозионного износа:
- футеровка колёс;
- изготовление колёс из твёрдых металлов
б) для кавитационного износа:
- минимум сократить потери энергии на входе в насос: уменьшение длины трубопроводов; минимальное количество местных гидравлических сопротивлений на всасывающем патрубке, максимально большой диаметр всасывающего трубопровода.
3) Выход из строя подшипников качения из-за возникновения осевой силы и наличия циклических нагрузок, пульсаций, дисбаланса.
Методы профилактики: применение гидропяты или разгрузочного барабана.
4) Выход из строя муфт из-за несоосности двигателя и насоса, осевого усилия и гидравлического удара.
Запуск лопастных насосов происходит при закрытой задвижке, при этом насос должен быть залит жидкостью. Чтобы жидкость не сливалась с насоса на входе ставят обратный клапан.
|
ЭКСПЛУАТАЦИОННЫЙ ХАРАКТЕРИСТИКИ ЛОПАСТНЫХ НАСОСОВ
Эти характеристики необходимы для выбора насоса с целью наиболее рациональной эксплуатации.
1) Объёмная подача - Q, .
Весовая подача - G, .
Подача насоса определяется экспериментальным путём на воде.
2) Напор - м. вод. столба.
3) Мощность ,
,
,
.
4) КПД насоса
4.1 Объемный КПД
5) Кавитационный запас- превышение полного напора жидкости на всасывающем патрубке над давлением насыщенных паров.
6) Геометрическая высота всасывания(для самовсасывающих насосов).
Оптимальный режим эксплуатации насоса при
РАБОТА НАСОСА В ГИДРАВЛИЧЕСКОЙ СЕТИ
Если насосы не обеспечивают потребной подачи тогда прибегают к их совместной работе:
Параллельное включение оправдывается лишь тогда когда характеристики насосов являются пологими кривыми. Когда насос не обеспечивает необходимый напор прибегают к последовательной работе насосов.
Последовательное включение насосных установок менее экономично чем использование одного насоса.
ОСНОВНЫЕ МЕТОДЫ РЕГУЛИРОВАНИЯ ЛОПАСТНЫХ НАСОСОВ
В следствии изменения технологических параметров химических и нефтеперерабатывающих производств, таких как температура, давление, расход часто возникает необходимость изменения эксплуатационных характеристик насосного оборудования для обеспечения требуемых параметров технологического цикла
Изменение характеристик насосного оборудования может быть достигнуто неопытными способами:
1) Изменение характеристик насосной установки.
Под понятием насосная установка подразумевают: насосный агрегат(насос и электродвигатель), система трубопроводов по обсасывающей и нагнетательной линии, система вентиляцией задвижек, поворотов потока, клапаны и система резервуаров.
Изменением характеристик насосной установки мы не изменяем характеристику насоса.
|
1. Изменит характеристику насосной установки можно дросселированим трубопровода, изменением диаметра трубопровода, изменить количество местных сопротивлений. Дросселирование – самый неэкономичный способ т.к. при дросселировании теряется часть энергии.
2. Перепуск жидкости с напорной лини во всасывающую.
Способ неэкономичный т.к. часть энергии тратится на циркуляцию жидкости.
3. Изменение напорной характеристики насоса.
Он наиболее экономичный, но требует длительного оборудования или модернизации самого агрегата.
Изменить характеристику можно двумя путями:
1) Изменением числа оборотов.
Из теории подобия следует: ;
а) изменением частоты тока;
б) применение редуктора, мультипликатора; и т. д.
2) Изменением геометрии рабочего колеса насоса(подрезкой рабочего колеса)
Существуют рекомендации по обточке рабочего колеса, так слишком большая обточка приводит к снижению КПД насоса
![]() | 60 | 120 | 200 | 300 | 350 | >350 |
![]() | 0,2 | 0,15 | 0,11 | 0,09 | 0,07 | 0 |
Для повышения напорной характеристики насоса существует метод изменения геометрии рабочего колеса – «затыловка» рабочей кромки на выходе из насоса.
ПОДБОР НАСОСА ПО ЗАДАННЫМ ПАРАМЕТРАМ
При эксплуатации часто возникает необходимость замены насосного оборудования в связи с изменением технологического регламента.
При подборе насосов исходят из следующих требований:
1) Насос должен работать в наиболее экономичном режиме.
При подборе насоса необходимо производить расчёт характеристик с воды на рабочую среду.
Подбор насоса:
1.Определить коэффициент удельной быстроходности
2. По коэффициенту определяем тип насоса.
3. По сводным графикам Q-H отыскивают марку насоса в каталогах и ГОСТах.
Верхняя часть полей характеристик соответствует нормальному диаметру , а нижняя минимальной обточке.
Боковые пределы соответствуют зоне максимального КПД. Если рабочая точка не попадает на поле насоса то выбирают между ближайшими полями или обращаются к сводным графикам других насосов.
Окончательная проверка правильности выбора производится по сводным таблицам технических данных насоса.
МАШИНЫ ДЛЯ ТРАНСПОРТИРОВКИ И СЖАТИЯ ГАЗА
|
Компрессоры бывают:
- объёмного типа(поршневые, ротационные, диафрагменные);
- лопастного типа(центробежные, осевые);
- струйные.
В компрессорах объёмного типа сжатие газа осуществляется в замкнутой лопасти, объём которой изменяется. В лопастных- газу сообщается большая скорость.
В зависимости от давления компрессоры делят:
- вакуум компрессоры(от 2 атм.- газодувки);
- компрессоры низкого давления (2 атм.-10 атм.);
- компрессоры среднего давления (10-100 атм.;
- компрессоры высокого давления(от 100 атм).
Основные конструкции компрессоров:
1) Центробежные компрессора:
Преимущества:
- высокая производительность;
- компактность;
- возможность непосредственного соединения с приводом.
2) Поршневые:
Преимущества:
- большое давление.
Недостатки:
- небольшая производительность.
Используют для дозировки
3) Винтовые:
Преимущества:
- бесшумны;
- компактны.
Используют для высоковязких газов.
Основные отличия компрессоров от насосов следующие:
1) Компрессора имеют распределительные органы- клапаны(пластинчатые, золотниковые, с пружинами и др.).
2) Элементы компрессоров не смазываются перекачиваемой жидкостью, поэтому компрессора имеют смазочные устройства работающие в двух направлениях:
- смазка цилиндра;
- смазка кривошипно–шатунного механизма.
Способы смазки:
1) разбрызгивание;
2) ввод масла в газовый поток;
3) подвод смазки к каждой смазываемой точке в строгом определённом количестве. Это обеспечивается многоплунжерным насосом.
Уплотнения компрессоров:
Сальники имеют металлическую набивку (мягкая набивка используется до 8 атм). Уплотнения смазываются маслом. Для пожаро- и взрывоопастных газовых смесей используют сложные конструкции торцовых уплотнений.
Компрессорные станции имеют фильтры, маслогазоотделители, газосборники. Конструкция зависит от производительности компрессоров. Компрессорные установки имеют холодильники расположенные между ступенями сжатия газа и на выходе. Наиболее распространены батарейные или кожухотрубные.
В связи с тем, что давление в компрессорах большие, что может привести к разрушению трубопровода используют предохранительные клапаны:
|
закрытые и открытые, с пружинами, грузовые, и т.д.
ОСНОВНЫЕ ЭКСПЛУАТАЦИОННЫЕ ХАРАКТЕРИСТИКИ МАШИН ДЛЯ ТРАНСПОТИРОВКИ И СЖАТИЯ ГАЗОВ.
Степень сжатия
Вентиляторы предназначены для перемещения газа при малом сопротивлении гидравлической сети.
Газодувки – для перемещения больших количеств газа при высоком сопротивлении гидравлической сети.
Компрессора – для сжатия газа и перемещение его на большие расстояния.
Вакуум-насосы – для отсасывания газа при давлениях ниже атмосферного.
Вентиляторы и газодувки для больших расходов газа создающие разряжение не всасывании называются эксгаустерами.
Основные характеристики:
P – давление;
Q – подача;
N - потребляемая мощность;
n – число оборотов.
При эксплуатации компрессорного оборудования необходимо соблюдать ряд правил:
1) Перед пуском компрессора необходимо убедится о наличии достаточного количества масла в системе смазки.
2) Открыть продувочные вентили холодильников(вода может быть увлечена в следующую ступень компрессора за холодильником и вызывать разрушение компрессора.
3) Проверить ограничители крышек;
4) Запустить охлаждающую воду.
5) Проверять включен ли компрессор в холостую линию.
После пуска:
1) Проверяют работу системы смазка.
2) Закрывают продувочные вентили холодильников убедившись, что из них вышел сухой воздух.
3) Переключают компрессор на рабочую линию(предварительно убедившись о распределении давления по ступеням.
Контроль за работой компрессора осуществляется по приборам.
Остановка компрессора:
1) Стравливают давление газа.
2) Открывают продувочные вентили.
3) Останавливают двигатель.
4) Отключают охлаждающую воду.
5) Убедится, что подшипники не греются.
При работе:
1) Добавлять масло в систему смазку.
2) Наблюдать за ростом температуры охлаждающей воды.
3) Очищать холодильники от скопившейся влаги и масла.
4) Очистка масляных фильтров.
5) Проверка работы предохранительных клапанов.
6) Проверка работы уплотнений.
7) Проверка состояния фундаментов.
8) Поддержание машины в чистоте.
ПОДБОР КОМПРЕССОРОВ ПО ИХ ХАРАКТЕРИСТИКАМ
Подбор компрессора осуществляется аналогично насосному оборудованию
1) Определяют характеристику сети
При расчёте характеристики сети необходимо учитывать сжимаемость газа.
2) Определяем рабочую точку.
3) Определяем по полям характеристик тип компрессора с учётом степени сжатия.
МАШИНЫ ДЛЯ ТРАНСПОРТИРОВАНИЯ ТВЁРДЫХ И СЫПУЧИХ МАТЕРИАЛОВ. ИХ ЭКСПЛУАТАЦИЯ.
Транспортёры применяются для механизированных работ, то обеспечения такого технологического процесса, который бы обеспечивал переработку твёрдых и сыпучих материалов без применения ручного труда.
|
Переработка твёрдых и сыпучих материалов включает этапы:
1. доставка материалов в цех;
2. перегрузка материалов;
3. размещение материалов в складах.
4. подготовка материала для использования в технологических процессах и перемещение вдоль технологических линий.
Способы транспортировки зависят от
- размера частиц перемещаемого материала(крупные гранулы, кусковый материал, порошки, пасты);
- тары в которой находится материал(контейнеры, ящики, мешки, насыпной материал);
- типа и размеров складов(открытые площадки, навесы, одно - и многоэтажные здания и т.д.
- расстояния между агрегатами технологической линии;
- высоты по которую подается материал и др. требований технологического процесса.
Бестарные куски со склада расположенного не более 40-60 м можно доставлять при помощи ленточного или скребного конвеера.
Если расстояние превышает 60 м целесообразно применять пневмотранспорт для сыпучих веществ.
Для транспортировки сыпучих материалов применяются следующие типы транспортёров:
1) ленточный конвейер.
Недостатки - провисание ленты
2) поршневой транспортёр(элеватор) для вертикального перемещения материалов;
3) вибрационно – винтовой транспортёр
Пневматический транспортёр передаёт сыпучий материал по трубам в взвешенном состоянии в потоке сжатого воздуха.
ОСНОВЫЕ КОНСТРУКЦИИ ТЕПЛООБМЕННОГО ОБОРУДОВАНИЯ
Теплообменный аппарат - технологическое оборудование для процессов нагрева, охлаждения среды, изменения её агрегатного состояния или утилизации тепла.
В общем объёме химического оборудования теплообменники занимают 15-18 %, а в нефтепереработке до 50%.
По конструкции теплообменники делят на:
Теплообменники из труб:
- кожухотрубчатые (до 80% от всех конструкций);
- труба в трубе;
- погружные змеевиковые;
- пластинчатые и т.д.
По назначению:
- холодильники;
- подогреватели;
- испарители;
- конденсаторы.
По направлению движения потоков:
- прямоточные;
- противоточные:
- перекрёстного тока.
В химической, нефтеперерабатывающей и нефтехимической промышленности существуют особенности эксплуатации теплообменников, которые необходимо учитывать при выборе конструкций, материалов, направления потоков, элементов в которые необходимо подавать контактируемые теплоносители.
Если одна из сред имеет высокое давление то если теплообменник трубчатый то в трубное пространство направляется теплоноситель с большим давлением (трубы малого диаметра выдерживают большие давления).
Если один из теплоносителей коррозионно активен то его направляют по трубам, так как в процессе работы в случае выхода из строя отдельных трубок их заваривают. Но для коррозионных сред рекомендуют использовать полимеры. Грязный теплоноситель пускают в то пространство которое более доступно для промывки и очистки.
ТЕПЛООБМЕННЫЕ АППАРАТЫ И ОБЛАСТИ ИХ ПРИМЕНЕНИЯ
Основные конструкции:
Теплообменники могут изготавливаться с поперечными или продольными перегородками. С подвижными или не подвижными трубными решётками. Используются как подогреватели, холодильники, испарители, конденсаторы.
Испарители имеют вертикальную конструкцию для свободного движения пара вверх и для предотвращения образования застойных зон.
Теплообменники с неподвижными трубными решётками используют при перепаде температур менее 50 , линейное расширение трубок и кожуха достигают значений при которых возможны разрывы из-за неравенства расширений. Для предотвращения этого применяют различные компенсирующие устройства.
Основные виды компенсирующих устройств:
- с плавающей головкой;
- с U-образные трубами;
Также применяются сальниковые компенсаторы.
Способы крепления труб:
- развальцовка;
- сварка;
- сальниковое.
Интенсификация процессов теплообмена достигается выравниванием термического сопротивления на противоположных сторонах поверхности теплопередачи. С той стороны где коэффициент теплопередачи меньше подбирают рациональный гидродинамический режим потоков(ликвидация застойных зон при помощи установки распределительных устройств у штуцеров, увеличение скорости движения теплоносителя, установка турбулизирующих вставок, оребрение поверхности и т.д.
МАССООБМЕННОЕ ОБОРУДОВАНИЕ
Массообменное оборудование предназначено для проведения процессов при которых вещество переходит из одной фазы в другую путём диффузии.
К массообменным процессам относятся:
- абсорбция;
- адсорбция;
- экстракция;
- сушка;
- ректификация;
- кристаллизация.
Основной вид оборудования:
- колонны(полые, распылительные, тарельчатые, насадочные).
Насадочные колонны используют при диаметре до 4 метров так как при больших диаметрах ухудшается распределение жидкости по сечению.
В тарельчатых колонах тарелки монтируют на расстоянии более 300-400 мм. Это обусловлено необходимостью предотвращения уноса жидкости с тарелки на тарелку. Через 5-10 тарелок необходимы люки диаметром 500 мм для технического обслуживания. В местах установки люка расстояние между тарелками увеличивается до 800-1000 мм.
Для обеспечения равномерного распределения жидкости по тарелке колонну устанавливают строго вертикально, а тарелки горизонтально по уровню.
ОСНОВНЫЕ ЭКСПЛУАТАЦИОННЫЕ ПАРАМЕТРЫ МАССООБМЕННОГО ОБОРУДОВАНИЯ
Основные параметры зависят от технологического процесса и условий эксплуатации. В общем случае эксплуатационными параметрами является:
- расход газа;
- расход жидкости;
- соотношение нагрузок по фазам ;
- давление на входе и на выходе;
- перепад давления на каждом элементе;
- КПД тарелки или эффективность по Мерфи:
,
- диапазон устойчивости работы колоны:
;
где и
- расходы газа при котором колонна работает эффективно.
СПОСОБЫ УСТРАНЕНИЯ АВАРИЙНЫХ СИТУАЦИЙ ПРИ РАБОТЕ КОЛОННОГО ОБОРУДОВАНИЯ
Наиболее опасным является прекращение подачи воды в дефлегматор. При этом давление в колонне растёт, что может привести к аварии. Для предотвращения этого на линии подачи пара устанавливают предохранительные клапаны или гидрозатворы.
В случае остановки колонны её выводят на рабочий режим очень медленно повышая температуру на 1-2 в течении 1-2 часов тем самым предотвращая гидроудары.
МАШИНЫ ДЛЯ ИЗМЕЛЬЧЕНИЯ ТВЕРДЫХ МАТЕРИАЛОВ
Измельчение - процесс механического разрушения твёрдых тел под действием внешних сил.
Разделяют машины по способу воздействия на твёрдое тело:
- по степени измельчения делят на дробилки и мельницы.
Дробилки:
- валковые;
- щековые;
- конусные;
- молотковые;
Мельницы:
- шаровые барабанные;
- вибрационные;
- трубные трехканальные.
ЭСПЛУАТАЦИОННЫЕ ХАРАКТЕРИСТИКИ ДРОБИЛОК И МЕЛЬНИЦ
- Массовая производительность G;
- потребляемая мощность;
- плотность материала и его прочностные свойства;
- КПД дробилки;
- степень измельчения I (отношение между размером среднего куска материала на входе и на выходе.
Дробилки и мельницы работают в очень тяжёлых условиях:
- высокие ударные нагрузки;
- запылённость;
Это производит к тому, что между исполнительными механическими дробилками во избежание заклинивания устанавливают предохранительные устройства(ременные передачи, муфты специальных конструкций). Подшипником воспринимают большие ударные нагрузки. Для фильтрации масла от загрязнений устанавливают различные фильтрующие элементы(фильтры, гидроциклоны…)
Из-за ударных нагрузок часто ослабляют фундаментальный крепёж. Необходима проверка фундаментных болтов.
ВСПОМОГАТЕЛЬНОЕ ОБОРУДОВАНИЕ ХИМИЧЕСКИХ ПРОИЗВОДСТВ. ТРУБОПРОВОДЫ
Колонная аппаратура, компрессоры, насосы, фильтры, сушилки, кристаллизаторы, резервуары и др. устройства связаны между собой большим количеством коммуникаций называемых вспомогательное оборудование химических производств.
К этому оборудованию относят:
1) трубопроводы:
- обычные;
- обвязочные;
- специальные;
- неметаллические;
2) арматура.
- регулирование;
- изменение движения направления;
- отключение отдельных участков токов;
- предохранение оборудования и труб от разрушения в следствии опасно-
го повышения давления.
В химической промышленности транспортирование продуктов сырья имеют особенности:
- температура (-200 1200
);
- перепады давлений( мм. рт. ст. до 18000 атм.).
Поэтому вспомогательное оборудование изготавливается со специального материала по специальным правилам. Существует правила эксплуатации для различных типов трубопроводов.
На каждый вид оборудования завод – изготовитель дает документацию на обвязку технологическим трубопроводом. На каждые 10 метров трубопровода обвязочного в среднем комплектуется 33 наименования типоразмеров труб, 61 наименование арматуры, 50 наименования фланцев, 23 отводов, 133 шпилек, болтов, гаек и прокладок. На заводах изготавливаются только прямые участки труб, а все повороты, отводы изготавливают и устанавливают по месту во время монтажа. Это на 40 % снижает трудоемкость заводского изготовителя, и снижается вероятность ошибок(нестыковок труб, фланцев, отверстий, арматуры и т.д.), снижает расход материалов, повышается качество и надёжность обвязочных трубопроводов.
Под трубопроводами специального назначения подразумевают трубопроводы под давлением более 100 атм. и называются трубопроводы высокого давления. На них распространяются специальные правила на эксплуатацию и обслуживание;
Под давлением меньше атмосферного(вакуум) трубы по которым транспортируют токсичные и агрессивные продукты.
Основное требование к трубопроводам специального назначения – их герметичность. На трубопроводах высокого давления ставят специальные фланцевые соединения, болтовые соединения усиленные, устанавливают металлические прокладки, их часто проверяют на наличие утечек, а сварные соединения контролируют специальными методами. Для вакуумных трубопроводов герметичность проверять визуально очень сложно так как утечка происходит во внутрь. Поэтому эти трубопроводы стараются изготавливать цельными с минимальным количеством фланцевых соединений.
Для трубопроводов для агрессивных, химически активных сред применяют по возможности неметаллические материалы.
Из хрупких материалов - фарфор.
Из футерованных материалов – гумирование, покрытие полиэтиленом, винипластом, стеклом.
Не металлические материалы имеют ограниченное применение:
Стеклянные –для особо чистых продуктов.
Винипластовые – только в помещениях(так как не выдерживают долгое время минусовых температур)
Полиэтилен – выдерживает многократное оттаивание и замерзание.
ТРУБОПРОВОДНАЯ АРМАТУРА
Существуют следующая классификация арматуры по назначению:
1) Запорная арматура – для герметичных отключений.
2) Распределительная арматура - для распределения потоков.
3) Регулирующая арматура – для регулирования расхода.
4) Предохранительная - предохранение от повышенного давления сверх номинального.
5) Перепускная – поддержание постоянного давления среды посредством перепуска избытка среды при повышении её подачи сверх номинального хода.
6) Арматура обратного действия - предотвращения обратного потока среды.
7) Аварийно отсечная - прекращение подачи при аварийных ситуациях.
8) Конденсатоотводящая – отвод конденсата с одновременным предотвращеним проскока пара.
Вентили:
-запорные;
- регулирующие;
- дроссельные;
Вентили бывают чугунные, стальные и пластиковые из пластмасс. Вентили высокого давления и сопротивления изготавливают диаметром мм.
Особенности эксплуатации:
Недостатки:
- Для загрязненных и легкокристаллизирующихся жидкостей вентили непригодны.
Задвижки.
Устанавливаются на трубопроводы .
Преимущества:
- сравнительно низкое сопротивление;
- малая строительная длина (длина в осёвом направлении);
- простота конструкции позволяет устранять опасность забивки;
Недостатки:
- герметичность ниже чем у вентилей.
Краны .
Краны бывают сальниковые, натяжные.
Краны для легкозастывающих продуктов и при P<10 атм.
Недостатки:
- быстро открываются, что может привести к гидроудару;
- длительное время простойка крана приводит к прилипании пробки крана;
ПРЕДОХРАНИТЕЛЬНЫЕ КЛАПАНЫ
Защищают от повышения давления .
Клапаны бывают:
- пружинные;
- рычажные;
- в виде предохранительных пластин;
В пластинах предохранительных происходит разрыв пластин.
Пружинные используют для горючих и токсичных веществ ввиду их герметичности, но они требуют частой регулировки.
Рычажные – в них используют сальниковые уплотнения, поэтому возможен прорыв газов.
Предохранительные пластины ставят совместно с рычажными или пружинными.
ОБРАТНЫЕ КЛАПАНЫ
Устанавливаются для предотвращения обратного хода жидкости или газа(при внезапной остановки насоса, компрессора и т.д.)
Существует обратные клапаны высокого и сверхвысокого давления устанавливаемые на вертикальных участках трубы.
Эксплуатируются при температурах -60 +600
и давлении 10-160 атм.
Недостатки:
-высокое гидравлическое сопротивление;
- высокая точность монтажа.
РЕДУКЦИОННЫЕ КЛАПАНЫ
Для понижения давления в трубопровод. В основном выполняются подпружиненными и настроены на определенное давление.
Недостатки:
- пружина со временем теряет свои свойства.
КОНДЕНСАТООТВОДЧИКИ
Предотвращают проскок пара в лини сбора конденсата. Устанавливаются за теплообменниками в которых используют водяной пар.
Бывают:
- поплавковые конденсатоотводчики;
- сифонные;
- термодинамические.
УКАЗАТЕЛИ УРОВНЯ
Устанавливаются на аппаратах. Они имеют стеклянную трубку, которая может разрушаться при больших давлениях. Для больших давлений указатели уровня снабжают шаровыми клапанами, которые срабатывают при разрыве трубки и предотвращают вытекание жидкости.
Из условий безопасной работы и прочности стекла обычно длина мерного стекла не превышает 800-900 мм, поэтому на высоких сосудах по высоте устанавливают несколько указателей уровня.
АППАРАТУРА С ДИСТАНЦИОННЫМ УПРАВЛЕНИЕМ
Применяют для
- механических работ,
- управление аппаратурой в труднодоступных и отдалённых местах;
- для управления арматурой в токсичной среде.
Приводы бывают:
- электрические;
- пневматические;
- гидравлические.
Электропривод самый простой, но он неприменим при перекачке взрывоопасных сред. Пневомо- и гидроприводы дорогие, сложны в эксплуатации, но не взрыво- и огнеопасны.
НАДЕЖНОСТЬ РЕЗЕРВИРОВАННЫХ УЗЛОВ, АППАРАТОВ И ТЕХНОЛОГИЧЕСКИХ ЛИНИЙ
Способы резервирования
Вероятность безотказной работы, эффективность (объем выполненной работы, удельная производительность), среднее время безотказной работы, среднее время ремонта, т. е. надежность аппаратов, машин, технологических линий в химической промышленности могут быть улучшены путем повышения:
- надежности за счет применения более надежных выпускаемых серийно деталей и узлов, контроля их качества, выбора оптимальных режимов, регулировки, подтяжки, разгрузки, увеличения запаса прочности узлов и деталей и т. д.;
- конструктивной надежности за счет совершенствования кинематических схем аппаратов, использования оптимальных конструктивных решений, применения стандартизированных и унифицированных узлов и деталей, надежной сборки, защиты от коррозии и других воздействий, предусмотрения удобства подхода при ремонте оборудования, применения высококачественных, материалов (заметим, что от таланта конструктора, его знаний, кругозора, творческого замысла зависит надежность оборудования);
- эксплуатационной надежности путем разработки рациональных способов и условий хранения оборудования до его эксплуатации, разработки инструкций по монтажу, эксплуатации, ремонту машин и аппаратов химических производств, сохранения во время работы температурных режимов, подготовки мероприятий по обеспечению взрывозащищенности аппаратов, проведения предварительных испытаний и т. д.
Иногда оказывается, что изготовленные машины, аппараты химического машиностроения и их узлы по своим техническим данным не могут обеспечить необходимых показателей надежности той или иной технологической линии или самого аппарата или машины. Тогда применяют резервирование, т. е. вводят избыточные аппараты, узлы или детали, а также резервные технологические линии. Эти резервные аппараты и технологические линии выполняют функции основных аппаратов и линий.
Резервирование узлов в аппаратах, самих аппаратов, технологических линий в химических производствах является способом повышения надежности за счет включения резерва, предусмотренного при конструировании аппаратов или в процессе их эксплуатации. Этот способ повышения надежности позволяет создавать систему аппаратов, надежность которой выше надежности входящих составляющих.
В литературе есть сведения о построении надежных аппаратов из менее надежных узлов. Практика ограничивает возможности применения резервирования, так как оно связано с увеличением веса и производственной площади, повышением стоимости и т. д.
Существуют основное, резервное и смешанное соединения аппаратов (узлов, деталей, блоков).
Основным соединением аппаратов (далее будем употреблять лишь слово «аппарат», имея в виду и узел, и деталь, и блок, и даже технологическую линию) называется такое соединение, при котором отказ хотя бы одного аппарата ведет к отказу всего соединения. Так, например, в технологической схеме производства силикатного кирпича (схема 13) имеется основное соединение аппаратов.
Схема 13
|
|
Наброски и зарисовки растений, плодов, цветов: Освоить конструктивное построение структуры дерева через зарисовки отдельных деревьев, группы деревьев...
Архитектура электронного правительства: Единая архитектура – это методологический подход при создании системы управления государства, который строится...
История создания датчика движения: Первый прибор для обнаружения движения был изобретен немецким физиком Генрихом Герцем...
Историки об Елизавете Петровне: Елизавета попала между двумя встречными культурными течениями, воспитывалась среди новых европейских веяний и преданий...
© cyberpedia.su 2017-2024 - Не является автором материалов. Исключительное право сохранено за автором текста.
Если вы не хотите, чтобы данный материал был у нас на сайте, перейдите по ссылке: Нарушение авторских прав. Мы поможем в написании вашей работы!