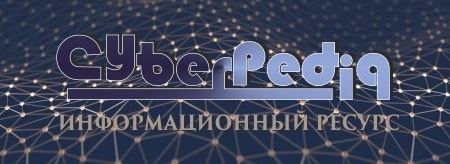
История развития пистолетов-пулеметов: Предпосылкой для возникновения пистолетов-пулеметов послужила давняя тенденция тяготения винтовок...
Индивидуальные и групповые автопоилки: для животных. Схемы и конструкции...
Топ:
Особенности труда и отдыха в условиях низких температур: К работам при низких температурах на открытом воздухе и в не отапливаемых помещениях допускаются лица не моложе 18 лет, прошедшие...
Теоретическая значимость работы: Описание теоретической значимости (ценности) результатов исследования должно присутствовать во введении...
Генеалогическое древо Султанов Османской империи: Османские правители, вначале, будучи еще бейлербеями Анатолии, женились на дочерях византийских императоров...
Интересное:
Подходы к решению темы фильма: Существует три основных типа исторического фильма, имеющих между собой много общего...
Отражение на счетах бухгалтерского учета процесса приобретения: Процесс заготовления представляет систему экономических событий, включающих приобретение организацией у поставщиков сырья...
Аура как энергетическое поле: многослойную ауру человека можно представить себе подобным...
Дисциплины:
![]() |
![]() |
5.00
из
|
Заказать работу |
|
|
Позволяет повысить надёжность технологических линий.
Есть резервирование:
1) резервное;
2) смешанное;
3) основное.
Основное резервирование – выход машины или аппаратов нарушает систему основной линии и приводит в выходу её из строя.
Резервное резервирование – отказ технологической системы и наступает когда выйдет из строя основное подключение и когда выйдет первый резервный ряд системы.
Существует два вида резервирования:
1) общее (основное);
а) общее резервирование с постоянно включённым резервом;
б) общее резервирование способом замещения.
2) раздельное резервирование.
Раздельное подключение - есть постоянно включенный резерв, если вышел 1 аппарат основного включения то включается 1 аппарат резервного включения
Раздельное подключение методом замещения – при раздельном резервировании обеспечивается большой выигрыш надёжности чем при большом числе оборудования.
Существует резерв:
а) горячий (постоянно включенный резерв);
б) теплый (облегченный). Параметры отличаются от рабочих параметров;
в) холодный (ненадёжный) – аппарат отключён от технологической линии и находится в ремонте.
Диагностика и дефектоскопия в машиностроении
Техническая диагностика заключается в определении технического состояния объекта, его составных частей путём измерения количественных и качественных измерений параметров с помощью специальных средств.
Диагностические параметры – признаки характеризующие техническое состояние машины, её основных частей и имеющих количественное выражение.
В качественных параметрах используется:
1) структурные параметры(зазоры, натяги, несоосность);
2) функциональные (мощность, удельный расход).
|
Задача технического диагностирования машин:
1) процесс эксплуатации - проверка работоспособности машины в целом или её сборочной единицы
2) при техническом обслуживании - определяется действительная потребность той или иной операции технического обслуживания;
3) при ремонте – поиск дефектов с установлением их места, вида, причины возникновения, контроль качества;
4) при прогнозировании остаточного ресурса – сбор информации о техническом состоянии машины, сборочной единицы; обработка и анализ этой информации, принятие решений о возможности дальнейшей эксплуатации машин и необходимом объеме технического обслуживания или ремонта.
Виды диагностики:
1) по техническому состоянию:
а) общее;
б) углублённое диагностирование.
При общем диагностировании проверяется работоспособность машин и правильность функционирования общих параметров.
Устанавливается дальнейшая возможность работы машины или аппарата без необходимых регулировочных ремонтных работ:
1) регулирование отдельных сборочных единиц;
2) возможность технического обслуживания и ремонта.
При углублённом диагностировании проводят углублённый диагноз состояния сборочной единицы и поиск дефектов в выявлением возможным местом их возникновения, причины и характера, устанавливается объём регулирования и ообъем ремонтных работ. При этом используются локальные параметры, характер неисправность сборочных единиц.
Средства контроля:
- разрушающей;
- неразрушающий.
При неразрушающем контроле:
Контролируют состоянии машины или аппарата без нарушения целостности.
Средства: КИП, проникающие поля, излучения, и средства для получения информации о использовании материалов или объектов.
Неразрушающий контроль:
1) магнитный;
2) электрический;
3) тепловой;
4) радиоволновой;
5) оптический;
6) акустический;
7) проникающими веществами.
Классификация приборов неразрушающего контроля:
|
1) акустические:
а) теневые;
б) эхоимпульсивные;
в) резонансные;
г) свободных колебаний;
2) капиллярные:
а) цветные(хроматические);
б) яркостные (ахроматические);
в) люминесцентные;
г) фильтрующие;
3) магнитные:
а) магнитопорошковые;
б) магнитографические;
в) магнитоферрозондовые;
е) магнитополупроводниковые.
4) оптические:
а) прошедшего излучение;
б) отраженного излучение;
в) собственного излучения.
5) тепловые:
а) прошедшего излучение;
б) отраженного излучение;
в) собственного излучения.
6) радиоволновые:
а) прошедшего излучение;
б) отраженного излучение;
в) собственного излучения.
7) радиационные:
а) ренгеновские;
б) излучение;
в) излучение;
г) позитронные.
8) электромагнитные(вихревых токов):
а) проходные;
б) накладные;
в) экранные;
г) комбинированные.
Методы неразрушающего контроля:
1) цветная дефектоскопия – обнаружение мелких трещин. Готовят раствор, состоящий из керосина, бензина, вазелина и добавляют яркую краску или пигмент. Этот раствор на очищенную обезжиренную поверхность детали наносят пульвилизатором. Выдерживают 5-10 минут, а затем смывают, подготовленный абсорбент(мел или каолин) и наносят на поверхность детали.
2) люминисцентная дефектоскопия – люминисцентный краситель применяется аналогично цветной дефектоскопии, трещины до 0,01 мм, глубиной не менее 0,2 мм, нанесение проявляющего порошка.
3) магнитная дефектоскопия – берут феромагнитный порошок, смачивают и посыпают поверхность детали. Гранулы порошка выстраюются по линии электромагнитного поля, там где есть дефект они огибают его, скатываются, уплотняются. Этот метод не позволяет определить глубину дефекта.
4) Ультразвуковой контроль:
а) проникающая волна;
б) отражающая волна.
ДУК-1; ДУК-2.
Проникающей волной контроль заключается – есть деталь, источник ультразвука с одной стороны и приёмник ультразвука с другой стороны. Поверхность обезжирена, смочена водой.
Отражающей волной – источник и приёмник расположены на одной стороне. Можно проконтролировать сварные швы, двутавровые, угловые, обнаруживать флюсовые включения.
5) радиационный метод: есть помещение где проверяют контроль сварных швов, сварной шов делится на участки и нумеруется, снизу кассета, сверху источник радиационного излучения. На каждой плёнке нумерация кассет высвечивается.
|
Разрушающие виды контроля
Проводят для определения механических свойств детали или заготовок, объем определения при разработке конструкторской документации.
1) определение твердости материала:
а) метод вдавливания шарика(Бринелль);
б) методом алмазного конуса(Роквелл);
в) алмазной пирамиды Викерса.
г) бойок с алмазным наконечником – для неметаллических материалов.
ГОСТ 1497-84 «Металлы. Методы испытания на растяжение»
ГОСТ 10.0.0.6-80 «Трубы металлические. Методы испытаний на растяжение».
ГОСТ 9454-78 «Металлы. Методы испытания на ударный изгиб при повышении комнатных температурах» (от 100 до 1200
).
ГОСТ 8694-75 «Трубы. Испытание труб на раздачу» (оправки с углом конуса 30, 45, 60, 90, 120 . Применяются также оправки с углом конуса 6 и 12).
Признаком успешного испытания является отсутствие трещин или надрывов(определяется наглядно).
ГОСТ 8695-75 «Трубы. Методы испытания на сплющивание диаметра не более 400 мм, температура , s=15% d.
Отрезается труба и затем между двумя паралельными стенками сдавливается. Сварной шов должен находится под 90 под усилие сжатия. Величина сплющивания задаётся. Надрывы, трещины отсуствуют, считаеся, что образец прошёл испытание.
На срез –электрозаклёпки.
Тема: Основые стадии жизненного цикла оборудования
1) НИР- научно иследовательские работы.
2) ОКР- опытно конструкторские работы.
Нир+ОКР= НИОКР(научно иследовательские и опытно-конструкторские работы.
3) изготовление опытного образца;
4) испытание опытно- промышленного образца;
5) изготовление опытно- промышленного образца;
6) испытание опытно- промышленного образца;
7) монтаж оборудования;
8) пуско-наладочные работы;
9) эксплуатация;
10) вывод оборудования из эксплуатации;
11) демонтаж оборудования.
На первой стадии производится литературный обзор, патентный поиск, выбор конструктивной схемы, определение параметров машины, материалы, методика расчёта.
На второй стадии согласно НИИ расчёт всех элементов, расчёт модельного образца, геометрических размеров.
Изготавливается опытный образец и проводится его испытание. При испытании функционально определяется режимы работы(температура и давление).
|
Изготавливается промышленный образец с учётом требований.
Испытание может производится на заводе изготовителе. На заводе- потребителе разрабатуется документации, произведение предварительных испытаний.
Пуско-наладочные работы производятся на заводе-изготовителе, производитя обучение будущего персонала и составляется документация. Есплуатация составляет 80% жизненного цикла оборудования, персонал проводит ремонты, следит за техничечкими параметрами оборудования.
После того как оборудование отработало свой ресурс или оно морально устарело, то его выводят из експлуатации (останавлюется технологическая линия, делается промывка оборудования, отсоединение его от вспомогательного оборудования, обезжиривается), после чего происходит демонтаж.
Содержание разделов технического регламента:
1) общая характеристика производства и технико-економический уровень:
а) полное наименование производства;
б) год ввода в эксплуатацию;
в) мощность производства;
г) количество технологических линий;
д) чертежи;
е) организация- разработка процесса;
2) характеристика продукции:
а) наименование;
б) наименование государственного государственного стандарта технический условий по которым выпускается продукция;
в) свойства продукции, область применения; физико-химические свойства.
3) характеристика исходного сырья, материалов и полуфабрикатов(в виде таблицы).
4) описание технологического процесса и схемы;
5) материальный баланс;
6) ежегодные нормы расхода основных видов сырья, материалов и энергоресурсов;
7) ежегодные нормы образования отходов производства;
8) нормы технологического режима;
9) контроль производства управления технологических процессов;
10) неполадки оборудования и способы их устранения;
11) охрана окружающей среды;
12) основные правила безопасной эксплуатации производства;
13) перечень обязательных инструкций (пусковые инструкции, общепроизводственные, инструкции по технике безопасности, санитарии, а также план ликвидации аварийных ситуаций, инструкции по подготовке оборудования и ремонта оборудования, инструкции по всем рабочим местам в соответствии со штатым расписанием);
14) чертежы технологической схемы;
15) спецификации на основное оборудование.
|
|
Адаптации растений и животных к жизни в горах: Большое значение для жизни организмов в горах имеют степень расчленения, крутизна и экспозиционные различия склонов...
Автоматическое растормаживание колес: Тормозные устройства колес предназначены для уменьшения длины пробега и улучшения маневрирования ВС при...
История развития хранилищ для нефти: Первые склады нефти появились в XVII веке. Они представляли собой землянные ямы-амбара глубиной 4…5 м...
Биохимия спиртового брожения: Основу технологии получения пива составляет спиртовое брожение, - при котором сахар превращается...
© cyberpedia.su 2017-2024 - Не является автором материалов. Исключительное право сохранено за автором текста.
Если вы не хотите, чтобы данный материал был у нас на сайте, перейдите по ссылке: Нарушение авторских прав. Мы поможем в написании вашей работы!