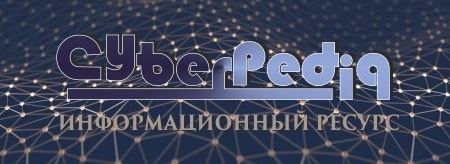
Организация стока поверхностных вод: Наибольшее количество влаги на земном шаре испаряется с поверхности морей и океанов (88‰)...
Эмиссия газов от очистных сооружений канализации: В последние годы внимание мирового сообщества сосредоточено на экологических проблемах...
Топ:
Теоретическая значимость работы: Описание теоретической значимости (ценности) результатов исследования должно присутствовать во введении...
Отражение на счетах бухгалтерского учета процесса приобретения: Процесс заготовления представляет систему экономических событий, включающих приобретение организацией у поставщиков сырья...
История развития методов оптимизации: теорема Куна-Таккера, метод Лагранжа, роль выпуклости в оптимизации...
Интересное:
Искусственное повышение поверхности территории: Варианты искусственного повышения поверхности территории необходимо выбирать на основе анализа следующих характеристик защищаемой территории...
Аура как энергетическое поле: многослойную ауру человека можно представить себе подобным...
Национальное богатство страны и его составляющие: для оценки элементов национального богатства используются...
Дисциплины:
![]() |
![]() |
5.00
из
|
Заказать работу |
|
|
Предмет и задачи курса «Процессы и аппараты химической технологии»
Химическая промышленность начала создаваться на рубеж 18 – 19 в.в. и за исторически короткий период (120 – 150 лет) превратилась в технически развитых странах в одну из основных отраслей народного хозяйства. С развитием химической промышленности возникла потребность в химической науке, обобщающей закономерности основных производственных процессов и разрабатывающей методы расчетов аппаратов на основе их рациональной классификации.
В нашей стране идея по общности ряда основных процессов и аппаратов, применяемых в различных химических производствах, была высказана профессором Денисовым в 1828 году. Позднее аналогичные принципы развивались Д. Менделеевым, предположившим основные процессы химических технологий. Эти идеи легли в основу новой учебной дисциплины по расчету и проектированию основных процессов и аппаратов, которая была введена профессором Крупским в конце 1890 – х годов в Петербургском техническом институте. И в 1912 году профессор Тищенко ввел в Московском техническом институте «Процессы и аппараты» в качестве самостоятельной науки.
Большой вклад в разработки отдельной науки ПАХТ внесли: Тищенко (автор теории расчетов выпарных аппаратов), Коновалов (заложил основы теории перегонки жидкости), Фокин и Павлов (создали уникальную теорию по созданию монографий по ПАХТ). Из зарубежной литературы, посвященной принципам основных расчетов процессов и аппаратов можно отметить книгу В. Бэджера и В. Мак – Кэба, вышедшую в 1932 году и на русском языке в 1933 году под названием «Основные процессы и аппараты химической технологии».
Инженерный курс основных процессов и аппаратов химической технологии построен на химии и физике и при расчетах позволяет определить выход веществ.
|
Материальный баланс.
МБ составляется на основе закона сохранения массы: масса поступающих веществ равна массам всех получающихся в результате проведения процесса веществ, т.е. без учета потерь: ∑Gн = ∑Gк. Однако, в практических условиях неизбежны необратимые потери веществ: ∑Gн = ∑Gк + ∑Gп.
МБ составляется для процесса в целом или для отдельных его стадий. Он может быть составлен для системы в целом или по одному из входящих в нее компонентов. Так, МБ процесса сушки составляют как по всему влажному материалу, поступающему на сушку, так и по одному из его компонентов – массе абсолютно сухого вещества или массе влаги, содержащейся в высушиваемом веществе.
МБ составляется либо за единицу времени (за один час), либо в расчете на единицу массы исходных или конечных продуктов. На основе МБ определяется выход продукта, под которым понимают выраженное в % - ном отношении количество продукта к максимальному. Практический расход материалов обычно превышает теоретический в следствие того, что химические реакции не протекают до конца, происходят потери реагирующих веществ.
Энергетический баланс.
ЭБ составляется на основе закона сохранения энергии, согласно которому количество энергии, введенной в процесс, равно количеству выделяющейся энергии, т.е. приход равен расходу энергии.
Проведение химико-технологических процессов обычно связано с затратами различных видов энергии: механической, электрической и др. Эти процессы часто сопровождаются изменением энтальпии системы вследствие изменения агрегатного состояния вещества. В химических процессах большое значение может иметь тепловой эффект протекания реакции. Частью ЭБ является тепловой баланс, который в общем виде выражается уравнением ∑Qн = ∑Qк + Qп. При этом вводимое тепло ∑Qн = Q1 + Q2 + Q3, где Q1 – тепло, вводимое с исходным веществом, Q2 – тепло, вводимое извне, Q3 – тепло, вводимое физическими или химическими превращениями (это 1-3 % от прихода тепла). Отводимое тепло складывается из тепла, удаляющегося с конечными продуктами и отводимого с теплоносителем. В ЭБ кроме тепла учитывается приход и расход всех видов энергий. Например, затраты механической энергии на перемещение жидкости или сжатие и перемещение газов. На основании теплового баланса находят расход водяного пара воды и др. теплоносителей, а по данным ЭБ – общий расход энергии на осуществление процесса.
|
Система единиц измерения
При расчетах технических процессов и оборудования приходится пользоваться химическими и физическими данными, которые имеют свои единицы измерения. Приходится пользоваться: М (1*106), к (1*103), д (1*10-1), с (1*10-2), м (1*10-3), мк (1*10-6). ГОСТ 6887-61 по СИ (м, кг, с); МКГСС (м, кгс, с); СГС (см, г, с).
Основные теории подобия
Изучение технологических процессов с целью получения уравнений, описывающих данный процесс, необходимых для их анализа и расчета, проводят чисто теоретически. Дифференциальные уравнения описывают целый класс однородных явлений. И для выявления конкретного явления необходимо дифференцированное уравнение ограничивать дополнительными условиями однозначности. Условия однозначности включают в себя геометрическую форму и размеры системы, физические константы участвующих в нем веществ, начальные условия, граничные условия. Для опытного изучения процесса необходима определенная теория – теория подобия процессов. Она позволяет при экспериментируемых опытах применять наименьшее количество физических величин, участвующих в процессе. Найти область применения производственных опытов. Подобие однозначности включает в себя:
1. геометрическое подобие
2. временное подобие
3. подобие физических величин
4. подобие начальных условий
5. подобие граничных условий.
1.Геометрическое подобие соблюдается, если сходственные стороны аппаратов являются пропорциональными величинами.
ℓ″1/ℓ′1 = ℓ″2/ℓ′2 = ℓ″3/ℓ′3 =…= Kℓ
Kℓ - множитель геометрического преобразования
ℓ″1= Kℓ*ℓ′1, ℓ″2 = Kℓ * ℓ′2, ℓ″3 = Kℓ * ℓ′3
ℓ″1, ℓ″2, ℓ″3 – характеризующие размеры второго аппарата, подобные первому аппарату.
|
2. Временное подобие соблюдается, если отношение интервалов времени двух подобных процессов является величинами постоянными.
τ″1/τ′1 = τ″2/τ′2 = τ″3/τ′3 =…= Kτ
Kτ - множитель временного преобразования
τ″1= Kτ * τ′1, τ″2 = Kτ * τ′2, τ″3 = Kτ* τ′3
3. Подобие физических величин соблюдается, если отношение этих величин для двух подобных процессов остается постоянным.
γ″1/γ′1 = γ″2/γ′2 = γ″3/γ′3 =…= Kγ
Kγ - множитель физического преобразования.
4. Подобие граничных условий соблюдается, если отношение величин, характеризующих данное условие на границе для двух подобных процессов, находится в постоянных соотношениях.
5. Подобие начальных условий соблюдается, если отношение величин для двух подобных процессов находится в постоянных соотношениях.
Подобие процессов однозначности распространяется на весь объем только начальный момент времени, в дальнейшем показывает подобие процесса на границе. Процессы подобны, если они описываются одним и тем же уравнением и системой дифференцированных уравнений при одних и тех же условиях однозначности.
Второй закон механики:
f = m(dW/dτ)
f′dτ′ / m′dW′ = 1 (1)
f′′dτ′′ / m′′dW′′ = 1 (2) выразим переменные в Ур.2 через переменные Ур.1 путем умножения на преобразователь кf
f′dτ′ Kτ / Kmm′dW′ Kw = 1
кf Kτ / Km Kw * f′dτ′ / m′dW′ = 1 (3)
Уравнение 1 и 3 отличаются комплексом физических величин. Когда кf Kτ / Km Kw = 1 уравнения 1 и 3 одинаковы.
f′τ′ / m′W′ = f′′τ′′ / m′′W′′ = idem
полученный комплекс физических величин называется критерием подобия; в данном случае критерий называется критерием Ньютона
Nℓ = fτ / mW.
Гидродинамические подобия.
Преобразуем уравнение Навье – Стокса, получим функциональную зависимость между критериями, характеризующими силы, действующие при движении в вязкой жидкости. Запишем уравнение Навье – Стокса для капельной жидкости в развернутой форме для вертикальной оси z:
|
Для подобного преобразования этого уравнения воспользуемся правилом - критерий подобия можно получить путем деления одной части уравнения на другую и последующим отбрасыванием знаков математического преобразования.
Если движение жидкости установившееся, то ее скорость не зависит от времени, т.е. dωz/dτ = 0, при этом заменяя в левой части уравнения характеризующие силы инерции, дифференциалы конечной силы инерции
где ℓ - определяющий линейный размер.
В правой части уравнения (1) отражающей действие силы тяжести равен ρg, а член dP/dz отражает влияние давления, его можно заменить на Р/ℓ, преобразуем все остальное отражает действие силы трения:
Разделим члены одной части на члены другой его части и найдем таким образом выражение, характеризующее соотношение между соответствующими силами и силами инерции, или иначе говоря, выразим эти силы в относительных единицах. Приняв за масштаб силы инерции, получим безразмерное соотношение величин, которое называют критерием подобия. Выражение, характеризующее отношение силы тяжести к силе инерции имеет вид:
ρg / ρω2/ℓ = gℓ / ρω2 = Fr – критерий Фруда. Чтобы избежать отрицательных чисел, пользуются обратными выражениями: Fr = ω2 / ρℓ. Fr отражает влияние сил тяжести или собственного веса на движение жидкости. Соотношение между силами может быть охарактеризовано выражением: Р/ℓ/ ρω2/ℓ = Р / ρω2, которое называется критерием Эйлера. Обычно ему дают несколько другой вид, вводя вместо абсолютного давления разность давлений между двумя точками жидкости.
Еu = ΔР / ρω2 – критерий Эйлера отражает влияние перепада гидростатического давления на движение жидкости, он характеризует отношение изменения силы гидростатического давления к силе инерции подобных потоку.
Найдем выражение, являющееся мерой силы трения к силе инерции, приняв за критерий подобия (для избежания чисел меньше 1) обратное отношение
ρω2/ℓ / μω/ℓ2 = ωℓρ / μ = Re – критерий Рейнольдса – отражает влияние силы трения на движение жидкости. Он характеризует отношение инерционных сил к силам трения потока. При неустановившемся движении жидкости в уравнении Навье – Стокса
член dωz /dτ ≠ 0, заменив член нестационарностью двигателя ρω / τ, и охарактеризуем соотношение этой величиной:
ρω2/ℓ / ρω/τ = Но – критерий гомохронности, учитывает характер движения в подобных условиях. Уравнение Навье – Стокса можно представить в виде функциональной зависимости между полученными критериями подобия: φ(Ho, Fr, Eu, Re) = 0.
Метод анализа размерности
|
Теорию подобия можно применять в том случае, если есть возможность составить дифференциальное уравнение, описывающее данный процесс, и задаться начальными условиями. Если нет такой возможности, то воспользуемся методом анализа размерности. Для этого проводят предварительные опыты и выявляют параметры, влияющие на проведение процесса, т.е. движущие силы.
ПРИМЕР: по трубе движется жидкость, движение описывается данным уравнением
ΔР = ƒ(d,ℓ, ρ, μ, ω) (1)
Пусть функция общего вида (1) приближенно может быть представлена в виде степенной зависимости ΔР,d,ℓ,ρ,μ,ω, т.е.
ΔР = А [d]a [ℓ]b [ρ]c [μ]b [ω]k (2)
Единицы измерения:
[ΔР] = [кгс/м2] = [F/L2]
[d] = [м] = [L]
[ℓ] = [м] = [L]
[ρ] = [кгс*с2/м2] = [F*T2 / L4]
[μ] = [кгс*с/м2] = [F*T / L2]
[ω] = [м/с] = [L / T ]
В основу положена П – теория Бэкингема, согласно которой общая функциональная зависимость, связывающая между собой n переменных величин при m – основной единице измерения, можно представить в виде зависимости между безразмерной зависимостью этих величин (n – m), а при наличии подобия – в виде связи между крит. подобия, т.е. если рассматриваемое явление вписывается в общем виде в соотношение (1), связывающее 6 физических величин, и эти величины выражаются посредством трех основных единиц измерения, т.е. n = 6, m = 3, n – m = 3.
Основные параметры насоса.
1. Производительность (Q, [м3/с]) – это объем жидкости, подаваемый насосом в нагнетательный трубопровод в единицу времени.
2. Напор (Н, [м]) – характеризует удельную энергию, сообщаемую насосом единице веса перекачиваемой жидкости, т.е. на какую высоту может быть поднята перекачиваемая жидкость.
3. Полезная мощность Nп = γQH = ρgQH – энергия, затрачиваемая на сообщение жидкости энергии.
4. Мощность на валу Nℓ > Nп, т.к. происходит потеря мощности в насосе. Nℓ = Nп / ηн.
5. КПД характеризует мощности в насосе. Номинальная мощность в насосе Nдв > Nℓ, т.к. происходит потеря энергии при передаче от электродвигателя к насосу.
КПД насосной установки:
η = ηv *ηг *ηмех *ηпер *ηдв, где
ηv - объемный, учитывающий потери при утечке через сальниковые уплотнения, неоднородные закрытия клапанов, выделения воздуха при всасывании;
ηг – гидравлический – учитывающий потери при движении жидкости через насос;
ηмех – это потери на механическое трение насоса;
ηпередачи – это потери от электродвигателя к валу насоса;
ηдвигателя – это потери в двигателе.
6. Установочная мощность двигателя (Nуст) – рассчитывается по величине номинальной мощности двигателя с учетом возможных перегрузок в момент пуска. Nуст = βNдв
7. Коэффициент запаса мощности β = 1,1 – 2 чем меньше Nдв , тем больше β.
Центробежные насосы.
Всасывание жидкости происходит равномерно и непрерывно под действием центробежной силы, возникающей при вращении рабочего колеса с лопатками, заключенного в спиралеобразном корпусе. 1 – всасывающий трубопровод
2 – рабочее колесо
3 – корпус
4 – рабочая лопатка
5 – нагнетательный трубопровод
Жидкость проходит через всасывающий трубопровод и отбрасывается к стенке корпуса под действием центробежной силы, возникшей под вращением рабочего колеса. Частицы жидкости попадают в канал переменного сечения, вследствие чего по уравнению Бернулли происходит преобразование кинетической энергии потока в статистический напор, т.е. увеличение давления. Напор центробежных насосов ограничен с одним центр.колесом. Для достижения высокого напора применяют многоступенчатые насосы.
Характеристики центробежных насосов.
- это графическая зависимость напора мощности на валу и кпд насоса от его производительности при постоянном числе оборотов. Эти характеристики получают при испытании центробежных насосов, изменяя степень задвижки на нагнетательной линии. При малой производительности максимальный будет напор.
Nℓ = ρgQH / ηн → ηн = ρgQH / Nℓ
Напор ↓ т.к. при уменьшении расхода ↑ стоимость, следовательно ↑ скоростной напор и по уравнению Бернулли должно ↓ пьезометрический напор, т.е. ↓ давление (Q → max;H → 0). Мощность на валу ↑ с ↑ расхода увеличиваются потери, т.е. требуется большая мощность на вал.
Характеристика сети.
- это зависимость между напором и расходом жидкости, необходимом для перемещения жидкости по сети.
Hr – геометрическая (потери) высота подачи;
h – потери напора;
H = Hr + hп
hп = ∑ξ * ω2/2g
Q = ω *S
ω =Q /S
hп = ∑ξ (Q2 /S22g) = k Q2
H = Hr + kQ
k – коэффициент пропорциональности.
Совмещая характеристику насоса и сети получаем рабочую точку А, т.е. точку, отвечающую наибольшей производительности насоса, работающего на данную сеть. Если она не совпадает с μн max, то либо заменяют насос, либо уменьшают гидравлическое сопротивление трубопровода.
Поршневые насосы
В поршневых насосах всасывание и нагнетание жидкости происходит при возвратно – поступательном движении поршня. 1 – всасывающий клапан,
2 – нагнетательный клапан,
3 – поршень,
4 – цилиндр,
5 – кривошипно – шатунный механизм.
Подача жидкости осуществляется импульсивно. По устранению этого недостатка используют импульсы двойного и тройного действия. Поршневые насосы различают: поршневые и плунжерные.
Рабочий орган – это поршень с поршневыми кольцами.
Плунжерные – без уплотнительных колец и имеет большое соотношение длины к диаметру. Производительность поршневых насосов простого действия зависит от объема цилиндра.
Q = Vц *n
Производительность зависит только от числа оборотов.
Конструкции насосов
1. Насос «Импеллер»
1 – рабочее колесо,
3– направляющий аппарат,
2 – корпус.
2. «Вихревой насос»
1 – корпус,
2 – рабочее колесо,
3 – входное окно,
4 – уплотняющий участок,
5 – кольцевой канал,
6 – нагнетательный клапан.
3. «Шестеренчатый» насос
Перемещение и сжатие газа
Машины, предназначенные для перемещения и сжатия газов, называются компрессорными машинами. Отношение конечного давления, создаваемого компрессорной машиной, к начальному давлению, при котором происходит всасывание газа, называют степенью газа.
В зависимости от степени сжатия компрессорные машины делятся на:
- вентиляторы (Р2/Р1 < 1), предназначенные для перемещения большого количества газов;
- газодувки 1,1 < P2/P1 < 3,0 – для перемещения газов при высоких сопротивлениях в газопроводах.
- компрессоры P2/P1 > 3,0 - для высоких давлений;
- вакуум – насосы, для отстаивания газов при давлении ниже атмосферного (Р2/Р1 < 8÷10).
По принципу действия компрессорные машины делятся на:
- поршневые – сжатие газа происходит за счет уменьшения объемов при движении поршня,
- ротационные – сжатие газов происходит за счет уменьшения объема эксцентрично расположенного ротора,
- центробежные – сжатие осуществляется за счет придания дополнительной энергии газу от вращающихся лопаток,
- осевые – газ сжимается вдоль оси рабочего колеса.
Поршневые компрессоры делятся по числу всасываний и нагнетаний за один двойной ход поршня на компрессор простого и двойного действия. По числу степени сжатия – на одноступенчатые и многоступенчатые.
Ступень сжатия – это часть компрессорной машины, где газ сжимается до конечного или промежуточного давления.
Рассмотрим одноступенчатый компрессор простого действия:
1 – поршень,
2 – кривошипно – шатунный механизм,
3 – цилиндр,
4 – клапан всасывающий,
5 – нагнетательный клапан,
6 – маховое колесо.
Одноступенчатые компрессоры могут быть одно- и многоцилиндровые. Для контроля за работой поршневых компрессоров снимается индикаторная диаграмма, представляющая собой зависимость между давлением и объемом газа, всасываемым и нагнетаемым поршнем за один двойной ход поршня или за один оборот коленвала.
Рассмотрим индикаторную диаграмму идеального компрессора. В нем всасывание начинается сразу же после начала движения поршня, вплотную подходящего к стенкам цилиндра. Горизонтальная прямая АВ соответствует процессу всасывания газа. Линия ВС – процессу сжатия газа в цилиндре от давления р0 до р1. Горизонтальная линия СД – процессу нагнетания газа. ДА – процессу стравливания газа. Заштрихованная площадь диаграммы соответствует работе, затрачиваемой на сжатие газа.
Ротационный компрессор.
В корпусе компрессора вращается ротор, расположенный эксцентрично относительно его внутренней поверхности. Пластины (зачерненные) в пазах свободно перемещаются в пазах ротора. И при его вращении выбрасывается центробежно из пазов. Эта же сила плотно прижимает пластины и внутренние поверхности корпуса. Таким образом, серповидное рабочее пространство между ротором и корпусом разделяется с помощью пластин, на ряд не равных по объему камер. Газ поступает из всасывающего патрубка и заполняет полости камеры. В камере, находящейся в положении В, всасывание прекращается и начинается сжатие. При вращении камеры вправо объем уменьшается и газ, находящийся в ней, сжимается. Сжатие заканчивается когда камера достигает положение С, в этом положении полость камеры сообщается с нагнетательным трубопроводом, после чего начинается нагнетание газа. В положении Д газ полностью вытесняется из рабочей камеры. Зазор между ротором и цилиндром в нижней части образует мертвое пространство Е, в положениях от Д до А происходит расширение газа в мертвом пространстве. В точке А начинается всасывание газов. Затем цикл повторяется.
Водокольцевые компрессоры
1 – корпус,
2 – ротор,
3 – всасывающее отверстие,
4 – нагнетающее отверстие.
В корпусе один компрессор расположен эксцентрично. Ротор – 2 с лопатками плоской формы. Перед пуском компрессор заполняется водой примерно на половину, которая при вращении ротора отбрасывается к периферии и образует водяное кольцо, соосное с корпусом компрессора и эксцентричное по отношению к ротору. Количество жидкости, заливаемое в компрессор, должно быть таким, чтоб концы всех лопаток были погружены в водяное кольцо. Между лопатками ротора и водяным кольцом образуются ячейки, объем которых за время первой половины оборота увеличивается, а за время второй – уменьшается. Газ рассасывается в ячейки, объем которых возрастает через отверстие 3 в торцевой крышке компрессора. При дальнейшем вращении ротора газ сжимается вследствие уменьшения объема ячеек и в конце оборота выталкивается в нагнетательное отверстие 4 крышки компрессора. В компрессорах такого типа жидкое кольцо играет по существу роль поршня. С помощью кольца изменяется объем рабочей камеры. Эти компрессоры называются также компрессорами с жидкостным поршнем.
Механические процессы.
Крупное дробление.
Рассмотрим щековые дробилки.
1,2 – неподвижная и подвижная щеки,
3 – эксцентриковый интервал,
4 – шатун,
5,6 – распорные плиты.
В щековой дробилке материал измельчается путем раздавливания в сочетании с раскалыванием между неподвижной и подвижной щеками. Подвижная щека приближается при рабочем ходе или отходит при холостом ходе от неподвижной щеки при вращении эксцентрикового вала. Во время рабочего хода происходит дробление, а во время холостого – выгрузка дробленого материала под действием собственного материала.
Различают щековые дробилки с нижним и верхним подвесом щеки. Преимущества: простота и надежность, широкое применение, компактность и легкость обслуживания. Недостатки: периодический характер дробящего усилия, отсюда возникает вибрация и возможность сбивания рабочего пространства.
Конусные дробилки.
1 – подвижный конус,
2 – неподвижный конус,
3 – эксцентриковый вал.
Крупное дробление в конусных дробилках осуществляется в эксцентриковых дробилках, где конус вращается вокруг неподвижной оси с валом, расположенной на конической шестерне (ее нет). Среднее и мелкое дробление в конусных дробилках с верхним подвесом. Преимущества: большая производительность, уравновешенная работа, высокая степень измельчения. Недостатки: очень сложная конструкция, дороговизна, большая высота, сложность обслуживания.
Среднее и мелкое дробление.
1. Волоковая дробилка
1 – неподвижный волок
2 – подвижный волок
Измельчение производится путем раздавливания между двумя волоками. Привод осуществляется на каждый волок. Дробилки могут различаться по количеству, форме и скорости волоков. Также могут быть зубчатые волоки. При различной скорости волоков усиливаются стирающие действия.
2. Ударно – центробежные дробилки
Молотковая дробилка
1 – корпус
2 – отбойная плита
3 – диск
4 – молотки
5 – колосниковая решетка
Преимущества: высокая степень измельчения. Недостатки: значительный износ плит и молотков, сложность балансировки ротора.
3. Отражательная дробилка
1 – колосниковая решетка
2 – ротор
3 – лопатки
4 – щитки
Материал, проходя через решетку, поступает на ротор, обращающийся с окружной скоростью. С помощью лопаток куски отбрасываются на щитки, и измельчение происходит при ударе лопаток и кусков о щитки. Преимущества: высокая степень измельчения, высокая однородность продукта. Недостатки: износ лопаток и щитков.
Тонкое измельчение.
Барабанные мельницы
Измельчение происходит внутри измельчающего барабана под действием мелющих тел. Мелющие тела – шары или стержни – не применяют. Мелющие тела под воздействием центробежных сил и сил трения увлекаются вместе с движущейся стенкой на определенную высоту, а затем падают и измельчают материал ударами, истиранием, раздавливанием. Измельчение проводят как мокрым, так и сухим методом. Преимущества: универсальность, постоянство скорости вращения, надежность и простота обслуживания. Недостатки: износ мелющих тел, загрязнение продуктов, шум.
*. Сверхтонкое измельчение
При сверхтонком измельчении материала разрушение происходит не по поверхности трещин, пересекающих всю толщу частиц, а главным образом путем «отшелушивания» (усталостного разрушения) вследствие поверхностной трещиноватости измельчаемых частиц. Наиболее эффективно и с наименьшими затратами энергии сверхтонкое измельчение осуществляется при высокочастотном воздействии на материал посредством сравнительно слабых ударов. Часто повторяющиеся, но относительно слабые воздействия на материал могут быть получены в мельницах с минимальной массой мелющих тел или без них.
Сверхтонкое измельчение производят в вибрационных, струйных и коллоидных мельницах, в которых частицы материала измельчаются ≈ от 10 – 0,1 мм до 75*10-5 – 1*10-4 мм.
Вибрационная мельница
представляет собой цилиндрический или корытообразный корпус – 1, примерно на 80 % своего объема загруженный шарами (иногда стержнями) – 2. Корпус приводится в колебательные движения валом – 3, снабженным дебалансом (в мельницах инерционного типа) или эксцентриковым валом (в гравитационных мельницах). При вращении неуравновешенной массы вала (вибратора) – 3 со скоростью от 1000 до 3000 мин-1 корпус – 1 с шарами в нем и измельчаемым материалом совершает качательное движение по элептической траектории в плоскости, перпендикулярной оси вибратора. Мелющие тела при этом вращаются вокруг собственной оси, а все содержимое корпуса приводится в планетарное движение в сторону обратную направлению вибратора. Материал интенсивно измельчается под действием частых соударений мелющих тел и истиранием. Корпус установлен на пружинящие опоры – 4 и деревянные подкладки, предотвращающие передачу вибраций основанию мельницы. Вибрационные мельницы используют для сухого и мокрого измельчения периодического и непрерывного действия.
Схема струйной мельницы с трубчатой камерой:
1 – трубчатый контур, в нижнюю часть которого через систему сопел – 2 поступает энергоноситель. Материал на измельчение подается таким образом, чтобы каждая пара струй пересекалась в вертикальной плоскости на некотором расстоянии от противоположной стенки трубы. Материал измельчается при многократных соударениях частиц в точках пересечения струй и в общем вихревом потоке. Разделение измельченного материала по крупности частиц происходит в поле центробежных сил при поворотах потока в коленах 4 и 5 трубы. Крупные части отбрасываются к внешней стенке и вновь попадают в зону измельчения. Мелкие движутся у внутренней стенки трубы, выходят вместе с энергоносителем через жалюзи – 6 инерционного пылеразделителя в трубу -7 и далее во внешнюю систему улавливания (циклоны и матерчатый фильтр).
Достоинства струйных мельниц: высокая энергонапряженность и эффективность измельчения, отсутствие вращающихся деталей и мелющих тел, возможность сочетания помола и классификации с сушкой, окислением, восстановлением и т.д.
Недостатки: большой расход энергоносителя, высокая энергоемкость.
Коллоидные мельницы. В коллоидных мельницах, применяемых в основном для мокрого сверхтонкого измельчения, материал измельчается в весьма малом (до 0,05 мм) зазоре между быстро вращающимися (ω до 100 м/сек) дисковым ротором и неподвижным корпусом (статором). В вихревом потоке, образующемся в этом зазоре, частицы материала вращаются вокруг собственных осей с такими скоростями, что центробежные силы разрывают их.
Нагревание водяным паром
- широко применяется в химической промышленности для ускорения многих массообменных, диффузионных процессов. Преимущества: в результате конденсации пара получают большее количество тепла при относительно небольшом расходе пара, т.е. теплота конденсации его составляет приблизительно r = 2,26*106Дж/кг при р = 1 атм.
Важным достоинством насыщенного пара является постоянство температуры его конденсации при данном давлении, что дает возможность точно поддерживать температуру его нагрева, а также в случае необходимости регулировать ее, изменяя давление греющего пара. Имеет постоянство вдоль всей поверхности стенки, что дает возможность легко автоматизировать процесс.
Основной недостаток водяного пара – значительное возрастание давления с повышением температуры => температуры, до которых можно производить нагревание насыщенным водяным паром, обычно не превышают 180 - 160˚С, что соответствует
рпара ~ 10-12 атм. При больших давлениях требуется слишком дорогая толстостенная т/о аппаратура, а также велики расходы на коммуникации и арматуру.
Нагревание глухим паром
- это когда теплоноситель и хладагент разделены стенкой. Пар, соприкасаясь с холодной стенкой, конденсируется и пленка конденсата стекает с поверхности, температура ее приблизительно равна температуре пара. При расчете температуры пленки берут равной температуре пара. Пар подводят в аппарат обычно сверху, а конденсат отводят снизу. Расход глухого пара при непрерывном нагревании определяется из уравнения теплового баланса: D = G*c(t2 – t1) + Qп / (Iп - Iк), где
D – расход глухого пара;
G – расход нагревательной среды;
с – удельная теплоемкость вещества (теплоносителя);
t2 – температура нагретой среды;
t1 – начальная температура нагреваемой среды;
Qп – потери тепла в окружающую среду;
Iп – энтальпия или теплосодержание греющего пара;
Iк – энтальпия конденсации.
Если пар не будет полностью конденсироваться на поверхности т/о и его часть будет уходить с конденсатом, то это вызовет непроизвольный расход пара. Пар, который не сконденсировался – пролетный пар.
Нагревание острым паром
- применяют в тех случаях, если имеется возможность смешивания нагреваемой среды с конденсатом, т.е. пар непосредственно введен в эту среду. Это более экологичный метод нагрева, т.к. температура парового конденсата с нагреваемой средой выравнивается. Если одновременно с нагреванием жидкость нужно перемешивать, то ввод острого пара осуществляют через барбатер (трубы с отверстиями и закрытые с одного торца). Расход острого пара определяют, учитывая равенство конечных температур конденсата и нагревателя. Тогда находят уравнение теплового баланса
D = G*c(t2 – t1) + Qп / (Iп - с *t2), где
ск – удельная теплоемкость конденсата.
Нагревание горячей водой
Горячая вода в качестве нагревающего агента обладает определенными недостатками по сравнению с насыщенным водяным паром. Коэффициент теплоотдачи у воды как и у любой другой жидкости ниже коэффициента теплоотдачи у конденсирующего пара. Кроме того, температура горячей воды снижается вдоль поверхности теплообмена, что ухудшает процесс теплообмена и снижает его регулирование. Горячую воду получают в котлах и паровых водонагревателях (бойлерах). Вода применяется обычно для нагрева до температур не более 100˚С, для температуры больше 100 ˚С используют в качестве теплоносителя воду, находящуюся под избыточным давлением ризб = 22,5 МПа.
Нагревание топочными газами
Дымовые или топочные газы относятся к числу наиболее давно применяемых нагревательных агентов. Топочные газы позволяют осуществлять нагревание до высоких температур (1000 - 1100˚С) при незначительных избыточных давлениях. Наиболее часто топочные газы используются для нагревания других газов через стенку других нагревательных агентов. При нагревании до 420˚С для изготовления т/о аппаратуры применяются обычные углеродистые стали. Расход топлива при нагреве топочными газами определяется из уравнения теплового баланса:
В = G*c(t2 – t1) + Qп / (I1 - I2), где
В – расход газообразного топлива,
I1 – энтальпия топочных газов на входе в т/о,
I2 - энтальпия топочных газов на выходе из т/о.
Конденсация паров
- может быть осуществлена путем охлаждения пара, либо посредством охлаждения и сжатия одновременно. Конденсацию пара в основном используют в ХТП, например, при выпаривании, в вакуум - сушке, и в других процессах для создания разряжения. Пары, подлежащие конденсации, обычно отводятся из аппарата, где они образуются, отдельный закрытый аппарат, служащий для конденсации паров, называемых конденсаторами. Объем получаемого конденсата в 1000 и 100 раз меньше объема пара, из которого он образуется. В результате в конденсаторе создается разряженное пространство, причем пространство уменьшается с уме
|
|
Автоматическое растормаживание колес: Тормозные устройства колес предназначены для уменьшения длины пробега и улучшения маневрирования ВС при...
Поперечные профили набережных и береговой полосы: На городских территориях берегоукрепление проектируют с учетом технических и экономических требований, но особое значение придают эстетическим...
Своеобразие русской архитектуры: Основной материал – дерево – быстрота постройки, но недолговечность и необходимость деления...
История развития хранилищ для нефти: Первые склады нефти появились в XVII веке. Они представляли собой землянные ямы-амбара глубиной 4…5 м...
© cyberpedia.su 2017-2024 - Не является автором материалов. Исключительное право сохранено за автором текста.
Если вы не хотите, чтобы данный материал был у нас на сайте, перейдите по ссылке: Нарушение авторских прав. Мы поможем в написании вашей работы!