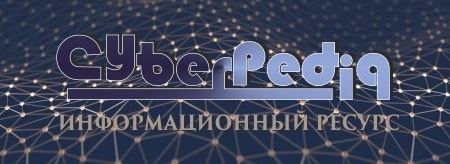
Кормораздатчик мобильный электрифицированный: схема и процесс работы устройства...
Историки об Елизавете Петровне: Елизавета попала между двумя встречными культурными течениями, воспитывалась среди новых европейских веяний и преданий...
Топ:
Комплексной системы оценки состояния охраны труда на производственном объекте (КСОТ-П): Цели и задачи Комплексной системы оценки состояния охраны труда и определению факторов рисков по охране труда...
Генеалогическое древо Султанов Османской империи: Османские правители, вначале, будучи еще бейлербеями Анатолии, женились на дочерях византийских императоров...
Особенности труда и отдыха в условиях низких температур: К работам при низких температурах на открытом воздухе и в не отапливаемых помещениях допускаются лица не моложе 18 лет, прошедшие...
Интересное:
Лечение прогрессирующих форм рака: Одним из наиболее важных достижений экспериментальной химиотерапии опухолей, начатой в 60-х и реализованной в 70-х годах, является...
Отражение на счетах бухгалтерского учета процесса приобретения: Процесс заготовления представляет систему экономических событий, включающих приобретение организацией у поставщиков сырья...
Мероприятия для защиты от морозного пучения грунтов: Инженерная защита от морозного (криогенного) пучения грунтов необходима для легких малоэтажных зданий и других сооружений...
Дисциплины:
![]() |
![]() |
5.00
из
|
Заказать работу |
УТВЕРЖДАЮ
Генеральный директор
ООО «Петросервис-Гео»
_______________Кондрашин В.А.
«____» ______________ 2008 г.
РУКОВОДСТВО
оператора-технолога станции ГТИ
Г. Саратов
Г.
Содержание
Введение. 4
Описание конфигурации станции. 4
1. Установка станции и оборудования на буровой. 5
1.1. Установка станции на буровой. 5
1.2. Установка УСО.. 5
1.3. Установка датчиков технологических параметров. 6
1.4. Установка дегазатора и оборудования для транспортировки газовоздушной смеси. 7
2. Подключение устройств внутри станции. 9
2.1. Установка платы, реализующей 485 интерфейс и настройка драйверов. 9
2.2. Подключение УСО, хроматографа и СГА-02. 9
3. Установка ПО DTCIS и дополнительных программ. 10
3.1. Установка ПО на компьютере «SERVER». 10
3.2. Установка ПО на компьютерах «TECHNOLOG» и «GEOLOG». 11
4. Настройка соединения с устройствами. 12
4.1. Прием данных от УСО.. 12
4.2. Настройка приема данных от хроматографа. 15
4.3. Настройка приема данных от СГА-02. 17
5. Настройка DTCIS. 20
5.1. Настройка списка параметров (датчиков) 20
5.2. Калибровка датчиков. 20
5.3. Настройка списка параметров для записи. 23
5.4. Настройка базы данных. 23
5.5. Настройка критериев. 23
6. Создание новой скважины. 24
6.1. Создание новой скважины.. 24
6.2. Данные по скважине. 24
6.3. Расчеты. 25
6.4. Начало регистрации. 26
7. Сбор и обработка реальновременной информации. 27
7.1. Порядок работы. 27
7.1.1. ПЗР. 28
7.1.2. СПО (Спуск инструмента). 28
7.1.3. Промывка, проработка. 29
7.1.4. Бурение. 32
7.1.5. Газовый каротаж в процессе бурения. 36
7.1.6. СПО (Подъем инструмента). 41
7.2. Действия при сбоях в работе оборудования и ПО. 42
8. Оформление и подготовка материала к сдаче в КИП. 43
Приложения. 444
Введение
Данная инструкция регламентирует последовательность действий оператора при установке на буровой, подключении и эксплуатации компьютеризированной станции ГТИ в составе: с выносной системой сбора и ПО DTCIS, а также содержит указания по методике проведения ГТИ.
Рассчитана на операторов, прошедших обучение на курсах по программе подготовки операторов-технологов, а также имеющих навык работы с ПК и операционной системой WINDOWS XP.
Описание конфигурации станции.
Состав оборудования и программного обеспечения:
- Выносная система сбора ВСС,
- типовой комплект датчиков технологических параметров с соединительными кабелями,
- дегазатор промывочной жидкости (желобной),
- табло (монитор) бурильщика.
- хроматограф «Геопласт 04М»,
- суммарный газоанализатор «СГА 02»,
- система транспортировки газовоздушной смеси.
- автоматизированное рабочее место оператора-технолога – далее по тексту – «SERVER», на котором устанавливается ПО DTCIS,
- автоматизированные рабочие места оператора-технолога («TECHNOLOG») и оператора-геолога («GEOLOG») для обработки и интерпретации данных, на которых устанавливается следующее ПО: GraphPad, ViewData, PlayBack, CGA105, GasSum, WinCrony, TEditor, «Оперирование интервалами данных» Microsoft Office 2003, архиватор 7ZIP.
- Соединительные кабели и сетевое оборудование
На компьютерах станции не должно быть никакого постороннего программного обеспечения (см. «Регламент работы на компьютерах станции ГТИ»).
Установка станции и оборудования на буровой.
Установка УСО
УСО (Выносная система сбора) устанавливается на буровой в месте, которое удовлетворяет его условиям эксплуатации. Cиcтема сбора и соединительные кабели должны иметь удобный доступ для обслуживания, и не должны создавать помех буровой бригаде. При чистке желоба помощник бурильщика должен предупреждать операторов станции ГТИ о необходимости временного демонтажа датчиков, установленных в желобе.
Кабель, протянутый от станции ГТИ до буровой, не должен создавать помех транспорту.
Подключение устройств внутри станции.
Установка ПО DTCIS и дополнительных программ.
В данном диалоге «Монитор бурильщика» устанавливает программу для Табло Бурильщика. Если станция укомплектована Монитором Бурильщика то данная программа не нужна,в таком случае используется расширенный рабочий стол, вторым экраном которого и является Монитор Бурильщика. На этом экране запускается клиентская программа RemoteView.exe (ярлык «Просмотр реальновременных данных по TCP») с необходимым бурильщику экраном.
После установки в меню ПУСК появится пункт “ PetroServices”, в котором будут присутствовать все установленные программы.
· В случае использования УСО «ИМС20-4B» запустить программу «Devices v1-70(325)R.exe» и выбрать к установке «ИМС Выносная система сбора»
После установки в пункте меню «Станция ГТИ» появится пункт «Устройства», где будут перечислены установленные программы.
Каталог программы DTCIS располагается на одном из выбранных Вами логических дисках в каталоге PetroServices. По умолчанию обычно предлагается диск D.
Структура каталога программы подробно описана в «Руководстве пользователя DTCIS». Можно лишь отметить, что База Данных станции ГТИ пишется в формате.dep (как и в программе CDT200) и состоит из следующих файлов:
store.dep store.lst | Данные в масштабе глубины (шаг записи задается в программе). Автоматически сохраняются все параметры. | |
time.dep time.lst | Данные в масштабе времени (шаг записи и сохраняемые параметры задаются в программе) | |
shrt.dep shrt.lst | Данные в масштабе времени (шаг записи 1с). Сохраняемые параметры задаются в программе. |
Прием данных от УСО
Для правильной работы устройства Выносное УСО «ТВР 20-4В» необходима правильная работа драйвера «ИМС Выносная система сбора».
§ скорость – 57600
§ биты данных - 8
§ четность – нет
§ стоповые биты – 1
§ управление потоком – нет
2. Выбираем в главном меню опцию «Настройка» → «Настройка устройства».
Каналы с 1 по 20 – зеленые стрелочки, указывающие, что канал включен в работу. Опция выбирается левой клавишей мыши.
Каналы с 21 по 26 – красные крестики. Эти каналы отсутствуют на измерительной плате Выносного УСО «ТВР 20-4В».
Каналы с 27 по 31 зеленые стрелочки.
Канал 32 – красный крестик.
Временные параметры:
Задержка ожидания ответа канала – 20 мсек
Задержка между опросом каналов – 10 мсек
Задержка между полным опросом устройств – 50…100 мсек
В таблице могут быть типичные значения или калибровочные данные, прилагаемые к системе сбора.
Типичные данные:
Точка 1 |
Точка 2 | Коэффициенты | ||||
мкВ/мкА | код | мкВ/мкА | код | А | В | |
Аналоговые каналы напряжения | 0 | 32768 | 10000000 | 65535 | 305.185095 | -10000305.18 |
Аналоговые каналы тока | 0 | 32768 | 20833 | 65535 | 0.635792 | -20833.63 |
Цифровые каналы измерения частоты | 0 | 32768 | 256000 | 65535 | 3.90631 | 0 |
Цифровой канал глубиномер | 0 | 0 | 0 | 0 | 1 | 0 |
Выбор единиц отображения продиктован тем, что в DTCIS должны поступать только целочисленные значения (т.е. цифры после запятой отбрасываются).
Примечание: Для того, чтобы введенные калибровки устройства заработали необходимо нажать клавишу «Расчёт коэффициентов». Расчет коэффициентов может производиться только после любого изменения значений в поле «Точка 1» или «Точка 2». В случае несоответствия коэффициентов приведенным в таблице – ввести вручную!
№ | тип канала | Коэффициент усиления | код | результат |
аналоговый напряжение | 1 | ХХХХ-код шестнадцатиричный | число в микровольтах | |
аналоговый ток | 1 | ХХХХ-код шестнадцатиричный | число в микроамперах | |
Цифровой частотный | 1 | ХХХХ-код шестнадцатиричный | число в милиГерцах | |
Цифровой глубиномер | 128 | ХХХХ-код шестнадцатиричный | пересчитанный десятичный код |
Примечание:
а) для аналоговых каналов и для цифровых частотных должны быть установлены (двойной щелчок левой клавишей мыши на канале):
§ коэффициент усиления - 1
§ функция обработки кода – Прямой код
б) для канала глубиномера соответственно:
§ коэффициент усиления - 128
§ функция обработки кода – Глубиномер
Канал глубиномера подсвечивается голубым цветом. Коэффициент усиления 128 для канала глубиномера служит для обнаружения отключения питания Выносной системы сбора.
Для аналоговых каналов изменение коэффициента усиления ведет к изменению диапазона измерения входных сигналов. (Коэффициент 2 приводит к измерению от 0В до +5В при том же диапазоне кодов)
Настройка DTCIS
5.1. Настройка списка параметров (датчиков)
· войти с уровнем доступа Администратор (Меню Помощь-Установка уровня доступа – выбрать «Администратор», пароль «1»).
· вызвать пункт меню «База данных»-«Состояние параметров…» и выбрать для просмотра полный список. (в правом нижнем углу).
· пройти по списку параметров для установки в поле «статус» признаков: нет, ручной, расчетный, датчик.
Те параметры, которые назначаются датчиками, появятся в списке датчиков и им должны быть присвоены соответствующие номера каналов УСО или др. устройств.
После этого все каналы должны быть откалиброваны.
Калибровка датчиков.
· вызвать пункт меню «Расчеты»-«Калибровка входных данных от системы сбора»
· пройти по списку параметров - датчиков, вызывая кнопку «Калибровать»
· в появившемся окне выполнить следующее:
o выбрать номер канала
o заполнить таблицу «базовые точки калибровки»
o выбрать функцию калибровки и фильтрацию при необходимости
Процедура калибровки подробно описана в “DTCIS руководство пользователя”.
Выбор функции калибровки:
Для параметров Хроматограф канал1, 2 и Время анализа хроматографа – Прямой код.
Для газов – выбрать функцию калибровки - «линейная». Нажать кнопку «таблица». В таблице задать коэффициент А 0,0001. Нажать ОК. Расчет не нажимать! Нажать ОК.
Для параметров с линейной характеристикой – Линейная.
Для всех остальных параметров – Кусочно-линейная.
Для сильно “шумящих” параметров применяется фильтрация
(коэффициент более 5 использовать не рекомендуется, т. к. при этом теряется информативность параметра).
Особенности калибровки различных датчиков:
Þ Вес на крюке Wкр.
Измеряется сила натяжения неподвижной ветви талевого каната пропорциональная весу бурильной колонны в буровом растворе. Кроме того, на датчик действует сила пропорциональная весу крюкоблока (Wк), талевого каната (Wт), квадрата (Wкв) при бурении.
Калибровка осуществляется следующим образом:
Тензодатчик калибруется по двум точкам; 1).Код, снятый при пустом крюке - значение 0; 2). Код, снятый по показаниям датчика при полном весе бурильной колонны на крюке – значение веса, соответствующее расчётному весу бурильной колонны с учетом облегчения за счет выталкивающей силы раствора =Wк* (1-Yp/Yж), где:
Wк – вес колонны, рассчитанный по компоновке.
Yp – удельный вес раствора
Yж – удельный вес металла
Полученная прямая в программе автоматически продолжается до максимального кода.
ГИВ с датчиком МД-10 калибруется аналогично.
Внимание! ГИВ на первые 10 делений не калибруется.
Þ Глубина долота.
Калибровка датчика глубин производится установкой точек калибровки на каждый метр длины квадрата, плюс последняя точка на длину свечи.
Þ Давление на входе Рвх.
Измеряются суммарные потери давления при прокачке раствора через бурильные трубы (Рт), долото (Рд), кольцевое пространство скважины (Рк.п.) датчиком типа МД200, МД300 или тензометрическим. При работе с вращающимся превентором, ликвидации выброса, опрессовке колонны, необходимо измерять давление на выходе скважины. Датчик МД200 врезается в выкидную линию. Калибруется по двум точкам: 1).Код х (при подключенном, но не врезанном в гидравлическую систему МД200) - значение 0; 2). Код х - значение Рвх с манометра буровой.
Þ Обороты ротора N рот.
Датчик нелинейный, калибруется на максимальное число точек, находящихся в рабочем интервале (50-100 об/мин).
Применяется “фильтрация с автосбросом” для фиксирования одиночных импульсов при подклинках (см. “DTCIS руководство пользователя” раздел “Калибровка датчика”).
Þ Момент на роторе Мрот.
Измеряется сила, пропорциональная силе сопротивления вращению бурильного инструмента, датчиками усилий разного типа. Примерную калибровку можно выполнить по удельному моменту разрушения горных пород или просто в условных единицах. Момент холостого хода ставиться равным 40-50 у.е., с тем чтобы при увеличении нагрузки на долото на 10 т момент увеличился на 4-5 у.е.. Фильтрация применяется аналогично параметру “Обороты ротора”.
Þ Расход на входе Q вх.
Измеряется объёмный расход бурового раствора расходомерами типа РГР (тарируется заводом изготовителем) или ультразвуковым. В случае отсутствия датчика расход рассчитывается по ходам насосов. Для этого необходимо параметр “Расход на входе” отметить как расчетный.
Þ Поток на выходе Q вых.
Измеряется поток бурового раствора на выходе. Датчик устанавливается так, чтобы реагировал на малейший поток, возникающий при доливе или при вытеснении раствора из скважины. Используется как индикатор расхода, для использования в
качестве расходомера необходима установка участка специального желоба (щелевой расходомер).
Þ Ходы насосов Хн1, Хн2, Хн3.
Измеряются число двойных ходов поршней насосов. Датчик нелинейный, калибруется на максимальное число точек, находящихся в рабочем интервале (50-100 ход/мин).
Þ Температура раствора на выходе Твых.
Измеряется температура раствора, выходящего из скважины. Датчик устанавливается на поплавке в открытом желобе или в трубке, залитой маслом, в закрытом желобе как можно ближе к устью скважины. Калибруется при помощи термометра по максимальному числу точек в рабочей области (20-80°С). По изменению температуры должны выделятся: забойная пачка, газированная пачка раствора, изменение температуры при промыве инструмента, износе долот.
Þ Объёмы раствора в емкостях V 1, V 2, V 3, V 4, V 5, V дол.
Измеряются уровни в емкостях, число которых зависит от принятой системы циркуляции. Должны измерятся с достаточной точностью, оговоренной с Заказчиком, объёмы долива, вытеснения, изменения объёмов в рабочих емкостях. Установка датчиков производится в месте, где нет сильного осаждения шлама и колебаний поплавков от работающих мешалок. Масштабы регистрации, в зависимости от зеркала емкости, устанавливаются следующим образом
Изменению уровня 0.5м в процессе калибровки присваивается соответствующее изменение объема; далее измеряется фактический объем (мерной линейкой),который устанавливается изменением коэффициента В в калибровочном графике.
Пример калибровки аналогового датчика смотрите в Приложении 1
Настройка базы данных.
· вызвать пункт меню «База данных»-«Настройка Базы Данных»
· установить интервалы сохранения данных в соответствии с требованиями Заказчика и КИПа.
Если требования не определены – рекомендуется установить следующие значения
для интервалов сохранения данных:
Временной интервал сохранения данных – 10 сек.
Глубинный интервал сохранения данных – 0,2 м.
Интервал аварийного сохранения данных – 5 мин (это интервал времени, через который сохраняются промежуточные данные расчетов и массивов по отставанию). Сохранение идет в файлы:
Realtime.db
Compute.ini
Настройка критериев
· Выполнить пункт (см. пункт меню «Расчеты»-«Критерии определения технологического режима работ». В пункте “Над забоем” должно стоять значение не менее 1,5 длины свечи. По достижении этого значения программа переходит в режим СПО. При переходе от режима бурения к режиму СПО и обратно автоматически переключаются наборы экранов, которые Вы выбрали для работы в этих режимах. Для пункта “Глубина инструмента” рекомендуется устанавливать значение от 50 до 100м,
· Выполнить пункт «Расчеты»-«Критерии определения технологического этапа работ» ориентируясь на модель определения технологического этапа работ из пункта меню “Менеджер”.
Саму модель этапов изменять не рекомендуется.
На этом этапе сделаны самые необходимые настройки для начала регистрации.
Создание новой скважины.
Создание новой скважины
· Закрыть все программы из комплекса DTCIS.
· вызвать пункт меню «пуск»-«PetroServices»-«Инструменты»-«Создание новой скважины»
· назначить каталог для сохранения текущих данных
· выбрать необходимую операцию (создание новой скважины, создание нового ствола, восстановление скважины из архива)
· нажать “Выполнение”.
Далее необходимо запустить «Реальновременная обработка данных» и внести в программу данные по скважине и буровому инструменту.
Данные по скважине
· выполнить пункт меню «Скважина»-«Данные по скважине…»
· выполнить пункт меню «Скважина»-«Данные по насосам»
Если нет датчиков ходов насосов, необходимо периодически вводить требуемое значение ходов в этом диалоге. Это значение будет писаться в базу данных и участвовать в расчете производительности (Расход на входе). При этом параметры “Ходы насосов 1, 2, 3 ” надо сделать расчетными в настройке списка параметров.
· выполнить пункт меню «Скважина»-«Параметры газокаротажного оборудования».
Рекомендуются следующие установки:
Параметры хроматографа:
Период анализа хроматографа – 3мин.
Время очистки хроматографа – 1мин.
В пункте Параметры ГВЛ – Время прохождения пробы - нужно указать время задержки по газо-воздушной линии.
Это время проверяется экспериментально:
Со стороны дегазатора в ГВЛ с помощью шприца подается большая концентрация газа и засекается время его выхода по показаниям суммарного газоанализатора.
В списках для привязки параметров по времени отставания должны присутствовать следующие параметры:
На устье:
Температура раствора на выходе из устья.
Плотность раствора на выходе из устья
После ГВЛ:
Общий газ
После хроматографа:
H2 - Водород C1 - Метан C2 - Этан C3 - Пропан C4 - Бутан C5 - Пентан Сумма газов С1+...+С6 | С1 - Относительное содержание метана. С2 - Относительное содержание этана. С3 - Относительное содержание пропана. С4 - Относительное содержание бутана. С5 - Относительное содержание пентана. |
· выполнить пункт меню «Скважина»-«Данные по буровому раствору»
Параметры раствора. Данные (Yг / см3, PV, мПа*сек, YР Дпа) берутся у инженера по растворам. Обратить внимание – пластическая вязкость вводится в Па*сек=0.01мПа*сек, динамическое напряжение сдвига в Па=0.1 ДПа.
· выполнить пункт меню «Скважина»-«Данные по долоту»
· выполнить пункт меню «Скважина»-«Компоновка бурового инструмента»-
Сначала вводят КНБК, затем инструмент, спускаемый в скважину.
· выполнить пункт меню «Скважина»-«Компоновка ствола скважины»-
заносятся диаметры и интервалы постоянных сечений, начиная с устья. Данные по открытой части ствола уточняются по кавернометрии.
· выполнить пункт меню «Скважина»-«Дополнительное оборудование»
Для наклонной скважины:
· выполнить пункт меню «Скважина»-«Проектные данные проложения ствола скважины»
· выполнить пункт меню «Скважина»-«Фактические данные проложения ствола скважины»
Расчеты.
· настроить модули расчетов в соответствии с требованиями заказчика.
· отметить емкости, участвующие в расчете общего объема раствора.
· выполнить пункт меню “Расчет оборотов долота”
· выполнить пункт меню “Расчет расходов раствора”
· выполнить пункт меню ”Расчет веса бурового инструмента в скважине”.
Рекомендуется пользоваться 3-м методом “ Ввод веса бурового инструмента (взвешивание) ”, как наиболее простым и надежным. Этот метод также предпочтителен при наклонном бурении.
· выполнить пункт меню “ Скорости проходки, инструмента…”
· выполнить пункт меню “ Расчет притока/потерь бурового раствора”
· выполнить пункт меню “Расчет времени отставания выхода параметров с забоя”.
Если введена конструкция скважины и компоновка инструмента, выбирается метод (1) По данным компоновки скважины и инструмента.
Объем размыва ствола скважины устанавливается исходя из длины открытого ствола и кавернозности. При отсутствии данных – установить 1-2м3.
При отсутствии данных по компоновке выбирается метод (2) Добавление задержки за шаг глубины. Значение задержки периодически корректируется.
(см. “Проверка расчета времени отставания” в п. 7.1.3)
6.4. Начало регистрации.
· В пункте ”Данные” выбрать ”Изменить номер рейса”.
· Ввести номер рейса и номер файла.
· В пункте меню “Выполнение” выбрать “Старт обработки данных с позиции“, выбрать текущую позицию.
При этом, все данные, накопленные в кольцевом файле во время манипуляций по настройке программы, будут пропущены и регистрация начнется “с чистого листа”.
Для ускоренного запуска программ на компьютере – сборщике (при включении или в случае перезагрузки компьютера) рекомендуется пользоваться программой “менеджер запуска”.
Порядок работы.
Требования к проведению работ изложены в “Технической инструкции по проведению геолого-технологических исследований нефтяных и газовых скважин”
(РД 153-39.0-069-01)
Основной задачей оператора-технолога является получение достоверной информации о процессе бурения с целью предупреждения аварий и осложнений. К аварийным ситуациям относятся: выбросы пластового флюида, катастрофическое поглощение бурового раствора и гидроразрывы пласта, прихваты, сломы, обрывы бурильного инструмента. К нежелательным ситуациям относятся всевозможные нарушения технологического процесса бурения и нерациональная отработка долот.
Работа оператора заключается в измерении и регистрации параметров, выделении аномалий параметров – выдаче предупреждений бурильщику, оценке ситуации – выдаче рекомендаций и соответствующем оформлении материалов (см. Рис. 7.1).
![]() |
Для решения этих задач в распоряжении оператора оборудование станции и программное обеспечение реальновременного сбора данных и последующей обработки.
Далее описана последовательность действий оператора с начала нового рейса.
(см. Приложение 3). Последовательность работы привязана к этапам строительства скважины.
ПЗР
Во время ПЗР:
· проверить данные по долоту;
· проверить и, если необходимо, скорректировать данные по раствору;
· проверить список инструмента;
· включить Хроматограф и Суммарный газоанализатор;
· проверить наличие сигналов с датчиков и калибровки;
· профилактика оборудования и датчиков:
- очистка дегазатора, ГВЛ;
- осмотр датчиков, УСО, смазка и сушка разъемов.
В процессе работы оператор-технолог должен использовать различные экраны рабочей программы, максимально отражающие особенности ситуации, происходящей в данный момент времени на буровой.
Во время смены режима работ БУРЕНИЕ -> СПО в программе Realtime автоматически меняется набор экранов. Поэтому во время работы в каждом из режимов оператор должен создать для работы определенный набор экранных форм (пункт меню “Экраны”).
Во время бурения (если правильно работает модель этапов) в верхней части рабочего окна программы Realtime.exe отображается технологический режим и этап “БУРЕНИЕ”, во время СПО – режим “СПО” и т.д.
7.1.2. СПО (Спуск инструмента).
Во время СПО необходимо:
· На компьютере «SERVER» в программе Realtime открыть экраны СПО2 и СПО3. Экран СПО3 используется для контроля долива и вытеснения бурового раствора. Экран СПО2 используется для контроля затяжек и посадок инструмента, скорости СПО, а также количества поднятых/опущенных свечей.
· На компьютере «TECHNOLOG» в программе «Графический планшет» открыть форму вывода временных данных и контролировать спуск инструмента, делая при необходимости комментарии на диаграмме.
· В самом начале спуска инструмента необходимо контролировать изменение глубины долота до завершения сборки КНБК, т. к. на малых весах возможны ошибки при расчете глубины. Это связано с неуверенным определением в программе этапа технологических работ при малых значениях параметра “Вес на крюке”. Далее программа автоматически будет рассчитывать глубину долота в соответствии со списком труб бурового инструмента (если он у Вас заполнен).
· В процессе СПО используется «Корректировка глубины СПО по списку инструмента», для расчета которой используется «Компоновка бурового инструмента». Несмотря на это, необходимо визуально по диаграмме контролировать количество спущенных свечей, и, сверяясь с мерой бурильного инструмента, контролировать корректность расчета глубины долота программой.
Цель этих мероприятий – подойти к забою с минимальной ошибкой по глубине. Это особенно важно при наклонно-направленном бурении, т. к. в этих условиях затруднено определение момента постановки на забой по другим параметрам.
· Во время спуска контролируются:
Промывка, проработка.
Во время Промывки и Проработки: необходимо:
· Проверить систему транспортировки газовоздушной смеси. Проверить герметичность ГВЛ.
· С помощью калибровочного газа проверить работу газоаналитических приборов (хроматограф, суммарный газоанализатор). Если есть необходимость – внести изменения в настройки и калибровки.
· Проверить дегазатор и другие датчики, устанавливаемые на желобе.
· На компьютере «SERVER» в программе Realtime открыть экран «Бурение 6» и «Хроматограф 1»
· Поставить параметры на сигнализацию.
· Контролировать технологические параметры промывки / проработки.
· Проверить баланс вытеснения после СПО и зафиксировать на диаграмме.
· На компьютере «TECHNOLOG» в программе «Графический планшет» зафиксировать выход забойной пачки и на диаграмме отметить максимальную концентрацию газа. Выдача рекомендации на дегазацию бурового раствора или отсечение забойной пачки в отстойную емкость.
· Во время остановки циркуляции проверить время задержки по линии (по диаграмме в «Графический планшет - Газовый повременка.pdt»)
· Произвести проверку расчета времени отставания и привязку.
Проверка расчета времени отставания:
Если в программу внесены данные по задержкам в ГВЛ и Хроматографе, то расчет «времени отставания» и привязка данных газового каротажа к глубине производится в программе сбора автоматически. Тем не менее, правильность расчетов и привязки данных необходимо периодически проверять на этапе первоначальных настроек и во время бурения несколько раз за рейс, так как возможно увеличение кавернозности, изменение параметров раствора, поглощения/притока бурового раствора, изменение режима течения (турбулентный/ламинарный) и пр.
Для проверки времени отставания существует несколько методик:
A.) Расчетная методика.
Суть расчетной методики заключается в определении суммарного объема затрубного пространства и времени "отставания" бурового раствора по каналу связи "забой-устье" при известном расходе бурого раствора.
Последовательность расчета:
Ø Рассчитывается объем скважины, как сумма объемов цилиндров с разными диаметрами (интервалы открытого и обсаженного ствола).
Ø Рассчитывается объем бурильной колонны, как сумма объемов цилиндров с разными диаметрами (УБТ, СБТ, ЛБТ).
Ø Рассчитывается объем затрубья скважины, как разность между объемом скважины и объемом бурильной колонны.
Ø Определяется время отставания бурового раствора при данном расходе.
Время отставания бурового раствора определяется по формуле:
t от = 3.14 .10-3(D2 – d2).H / 4. Qвх.
, где D –номинальный диаметр долота или внутренний диаметр обсадной колонны, d – внешний бурильных труб, H – глубина скважины, Qвх. – производительность буровых насосов при промывке. При расчете необходимо учитывать коэффициент кавернозности ствола скважины (берется из ГТН).
B.) Индикаторная методика.
Индикаторная методика определения "отставания" бурового раствора предполагает введение под квадрат какого-либо индикатора (целлофан, резиновая крошка, бензин) с последующим определением времени движения этого индикатора по гидравлической системе скважины oт устья до забоя по бурильным трубам и от забоя до устья по затрубью при работающих насосах.
При этом выход таких индикаторов как целлофан и резиновая крошка фиксируется визуально на устье скважины, а выход бензина - по увеличению показаний газоанализатора.
Бурение.
· Открыть экран Бурение 4_м (Рис.7.5).
· Постановка на забой различна на вертикальных и наклонно-направленных скважинах.
Как правило, началу нового долбления предшествует проработка ранее пробуренного интервала. В конце проработки по нескольким параметрам (мера инструмента, вес, момент на роторе и др.) определяется момент постановки на забой. В зависимости от различных факторов некоторые параметры приобретают большую информативность, другие теряют свою значимость. Это зависит от метода бурения (роторное, турбинное) типа скважины, компоновки инструмента, разбуриваемых пород, состояния призабойной зоны и ствола скважины (степень зашламления, сужение ствола), типа долота, забойного двигателя и др.
Дальнейшие указания предполагают использование 3-го метода (“Ввод веса бурового инструмента (взвешивание)”) в пункте меню РАСЧЕТЫ -> ”Расчет веса бурового инструмента в скважине”.
· На вертикальной скважине постановка на забой производится в следующем порядке:
1. По “мере инструмента” (глубине долота) определяется момент подхода к забою. Если измеряемые технологические параметры не имеют резких колебаний и стали по характеру изменения близкими к режиму бурения – можно перейти к процедуре взвешивания инструмента (определения собственного веса инструмента), необходимой для корректного расчета нагрузки на долото.
2. Взвешивание производится при включенной циркуляции, инструмент установлен на высоте 1 метра от забоя при движении вниз, при вращении в течении 3-5 минут. За полный вес принимается среднемаксимальное значение параметра “Вес на крюке”, которое вводится c помощью кнопки в программе Realtime.exe
Для правильного определения нагрузки на долото желательно, чтобы все бурильщики одинаково проводили взвешивание и с достаточной периодичностью.
Если до момента касания забоя взвешивание не производилось из-за разгрузки инструмента на стенки скважины (во время проработки), то перед бурением необходимо “оторваться” на 1-2 м и выполнить все вышеописанные действия.
|
характеризуется кривой разгрузки
(см.Рис.7.4). Ее переход к верти-
кальному участку можно считать
моментом постановки на забой.
В этой точке происходит вы
Автоматическое растормаживание колес: Тормозные устройства колес предназначены для уменьшения длины пробега и улучшения маневрирования ВС при...
Адаптации растений и животных к жизни в горах: Большое значение для жизни организмов в горах имеют степень расчленения, крутизна и экспозиционные различия склонов...
Наброски и зарисовки растений, плодов, цветов: Освоить конструктивное построение структуры дерева через зарисовки отдельных деревьев, группы деревьев...
История развития хранилищ для нефти: Первые склады нефти появились в XVII веке. Они представляли собой землянные ямы-амбара глубиной 4…5 м...
© cyberpedia.su 2017-2024 - Не является автором материалов. Исключительное право сохранено за автором текста.
Если вы не хотите, чтобы данный материал был у нас на сайте, перейдите по ссылке: Нарушение авторских прав. Мы поможем в написании вашей работы!