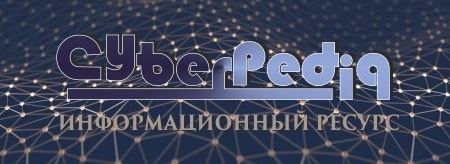
Кормораздатчик мобильный электрифицированный: схема и процесс работы устройства...
Общие условия выбора системы дренажа: Система дренажа выбирается в зависимости от характера защищаемого...
Топ:
Генеалогическое древо Султанов Османской империи: Османские правители, вначале, будучи еще бейлербеями Анатолии, женились на дочерях византийских императоров...
Марксистская теория происхождения государства: По мнению Маркса и Энгельса, в основе развития общества, происходящих в нем изменений лежит...
Выпускная квалификационная работа: Основная часть ВКР, как правило, состоит из двух-трех глав, каждая из которых, в свою очередь...
Интересное:
Отражение на счетах бухгалтерского учета процесса приобретения: Процесс заготовления представляет систему экономических событий, включающих приобретение организацией у поставщиков сырья...
Лечение прогрессирующих форм рака: Одним из наиболее важных достижений экспериментальной химиотерапии опухолей, начатой в 60-х и реализованной в 70-х годах, является...
Средства для ингаляционного наркоза: Наркоз наступает в результате вдыхания (ингаляции) средств, которое осуществляют или с помощью маски...
Дисциплины:
![]() |
![]() |
5.00
из
|
Заказать работу |
№ этапа | № параметра | Наименование контролируемого параметра CM | Виды СМ | ||||||
Эп | Эн | Пс | Пп | Гз | Гг | Ф | |||
1 | 1 | Наличие сертификата и ТУ | + | + | + | + | + | + | + |
2 | Наличие этикетки на каждой упаковке | + | + | + | + | + | + | + | |
3 | Срок годности | + | - | - | + | + | + | + | |
2 | 1 | Сохранность упаковки | + | + | + | + | + | + | + |
2 | Геометрия и состояние поверхности | + | + | + | + | - | - | + | |
3 | Прочность покрытия | + | - | - | - | - | - | - | |
4 | Прочность проволоки | - | - | + | - | - | - | - | |
5 | Химический состав | - | - | + | - | + | + | + | |
6 | Влажность | + | - | - | + | - | - | + |
В п. 1.3 для Гг и Гз проверяют срок годности заполненных баллонов.
В п. 2.2. для Ф проверяют однородность строения, размеры зерен и цвет.
В п. 2.3. для Пс с омедненной поверхностью проверяют прочность и толщину покрытия.
4.2. Первый этап общих испытаний состоит в проверке представленной заказчиком сопроводительной документации.
4.2.1. Аттестации подлежат СМ, срок годности которых истекает не менее, чем через 6 месяцев после подачи заявки на аттестацию. СМ с истекшим сроком годности аттестации не подлежат.
4.2.2. Все СМ должны быть упакованы в герметичную тару, предохраняющую от механических повреждений в соответствии с требованиями нормативных документов, утвержденных в установленном порядке.
В случае нарушения упаковки СМ подлежат проверке на сварочно-технологические свойства и контролю состояния материалов согласно ТУ на СМ.
4.3. Второй этап общих испытаний состоит в проверке качества изготовления СМ. Геометрические размеры и состояние поверхности проверяется только для Эп, Эн, Пс, Пп и Ф.
4.3.1. Для проверки соответствия электродов (Эп) по качеству покрытия от каждого упаковочного места из разных пачек отбирают 0,1%, но не менее 10 и не более 200 электродов от каждой партии.
На контактный торец электрода должен быть нанесен слой ионизирующего покрытия, облегчающего зажигание дуги, Маркировка электрода на покрытии (или стержне) должна включать полное наименование марки. Маркировка должна визуально определяться после трехкратной прокалки в печи перед использованием. Покрытие электрода на торце должно быть снято под углом 30-45°. Показатели оцениваются визуально-измерительным контролем.
4.3.1.1. Отобранные электроды (Эп) подвергают внешнему осмотру. Измеряют следующие обнаруженные дефекты: протяженность вмятин, волосных трещин, участков сетчатого растрескивания на поверхности покрытия и оголенные участки стержня с погрешностью не более 1 мм (с помощью линейки), а также фиксируют наличие оголенных участков стержня, глубину рисок, вмятин, задиров, размеры пор по поверхности покрытия;
При визуальном контроле стержня электрода под покрытием в случае обнаружения ржавчины или окалины на его поверхности аттестация электродов данной партии запрещается.
4.3.1.2. На поверхности покрытия электродов допускаются:
- поры с максимальным наружным размером не более 1,5 толщины покрытия (но не более 2 мм) и глубиной не более 50% толщины покрытия при условии, если на 100 мм длины электрода количество пор не превышает двух;
- поверхностные продольные волосные трещины и местные сетчатые растрескивания в суммарном количестве не более двух на электрод при протяженности каждой волосной трещины или участка растрескивания не более 10 мм.
- отдельные продольные риски глубиной не более 25% толщины покрытия, а также местные вмятины глубиной не более 50% толщины покрытия в количестве не более четырех при суммарной протяженности до 25 мм на одном электроде.
- местные задиры на поверхности покрытия, если их глубина не превышает 25% толщины покрытия, а их количество на одном электроде составляет не более двух.
4.3.1.3. Разность толщины покрытия при контроле микрометром определяют в трех произвольно выбранных местах электрода, смещенных одно относительно другого на 50 - 100 мм по длине и на 120° по окружности.
Места замеров следует выбирать таким образом, чтобы они приходились на центральную часть электрода, т.е. отступив с каждой стороны электрода (от контактной части и его торца) не менее чем на 50 мм.
Допускается проверка разности толщины покрытия другими методами и специальными приборами неразрушающим методом (обычно в центральной части длины электрода), обеспечивающими точность измерения с погрешностью 0,01 мм. В этом случае в акте проверки необходимо приводить конкретную марку прибора или его техническую характеристику.
4.3.1.4. Разность толщины покрытия электродов (Эп) оценивается с учетом требований НД по сварке указанных в заявке групп технических устройств. В том случае, когда допускается применение электродов, изготовленных по стандартам, разность покрытий не должна превышать значений, приведенных в табл. 13. В том случае, когда согласно НД следует применять электроды, изготовленные по ТУ, разность толщины покрытия не должна превышать значений, указанных в табл. 14.
Таблица 13
Допускаемая разность толщины покрытия Эп*
_____________
* Данные табл. 13 и 14 допустимы при отсутствии специальных требований в НД на аттестуемый СМ.
Номинальный диаметр электродов, мм | Максимально допустимая разность толщины покрытия, мм |
2,5 | 0,1 |
3,0 | 0,12 |
4,0 | 0,16 |
Таблица 14
Допустимая разность толщины покрытия Эп*
_____________
* Данные табл. 13 и 14 допустимы при отсутствии специальных требований в НД на аттестуемый СМ.
Шифр СМ | Диаметр электрода, мм | Максимально допустимая разность толщины покрытия, мм |
ЭпВ | 2,5-2,6 | 0,08 |
3,0-3,25 | 0,1 | |
4 | 0,12 | |
ЭпЦ | 3 | 0,08 |
4 | 0,1 | |
5 | 0,12 |
4.3.1.5. Кривизна электродов не должна превышать:
- при длине электрода 300 мм - 0,6 мм;
- при длине электрода 350 мм - 0,7 мм;
- при длине электрода 450 мм - 0,9 мм.
4.3.2. Контроль прутков вольфрама включает:
- проверку диаметра и овальности прутка;
- проверку состояния поверхности.
Проверку диаметра и овальности проводят микрометром или штангенциркулем в четырех местах по длине прутка. Размеры должны соответствовать государственным стандартам, техническим условиям и сопроводительным документам о качестве.
Проверку состояния поверхности прутков выполняют визуально. Поверхность должна быть гладкой, без вмятин и забоин. Электроды ЭнИ должны иметь шлифованную поверхность без рисок.
4.3.3. Геометрические размеры и состояние поверхности для Пс и Пп проверяют в соответствии с государственными стандартами, утвержденными в установленном порядке.
Проволока для проверки выбирается из нескольких партий (не менее трех партий), каждая из которых должна состоять из проволоки одной марки, одной плавки, одного диаметра, одного назначения и одного вида поверхности. Осмотру и обмеру должны подвергаться все мотки (катушки, кассеты) проволоки. Проволока (Пс) в мотках (катушках, кассетах) должна состоять из одного отрезка, свернутого неперепутанными рядами и плотно, чтобы исключить возможность "распушивания" или разматывания мотка. Концы проволоки должны быть легко находимы.
4.3.3.1. Диаметр проволоки измеряют микрометром с точностью до 0,01 мм в двух взаимно перпендикулярных направлениях в каждом сечении не менее чем в двух местах, на расстоянии не менее 5 м одно от другого. Предельные отклонения по диаметру для проволоки диаметром до 4 мм составляют - 0,09 мм, диаметром 4 мм - 0,16 мм. Овальность проволоки не должна превышать половины предельного отклонения по диаметру.
4.3.3.2. Поверхность проволоки должна быть чистой и гладкой, без трещин, расслоений, пленок, закатов, раковин, забоин, окалины, ржавчины, масла и других загрязнений. На поверхности проволоки допускаются риски (в том числе затянутые), царапины, местная рябизна и отдельные вмятины.
4.3.3.3. При поставке проволоки с улучшенной поверхностью за счет шлифования или обточки на поверхности проволоки допускаются мелкие волочильные риски, царапины, следы шлифовки, местная рябизна и отдельные вмятины, при глубине каждого из указанных пороков не более 1/4 предельного отклонения по диаметру. На поверхности низкоуглеродистой и легированной проволоки не допускается наличие технологических смазок, за исключением следов мыльной смазки без графита и серы.
4.3.3.4. Порошковую проволоку (Пп) проверяют дополнительно на коэффициент заполнения взвешиванием образцов длиной 100-150 мм с погрешностью не более 0,01 г, определяя отдельно массу образца и массу оболочки. Величина предельных отклонений коэффициента заполнения от номинальных значений допускается не более ±1,5%. Допуск на равномерность заполнения при взвешивании отрезков проволоки из разных участков бухт не более 5%.
Для бесшовных Пп и Пп со сложной конструкцией поперечного сечения оценку коэффициента заполнения допускается не проводить.
4.3.3.5. При проверке диаметра Пп предельные отклонения не должны превышать указанных в табл. 15.
Таблица 15
Эмиссия газов от очистных сооружений канализации: В последние годы внимание мирового сообщества сосредоточено на экологических проблемах...
Наброски и зарисовки растений, плодов, цветов: Освоить конструктивное построение структуры дерева через зарисовки отдельных деревьев, группы деревьев...
Археология об основании Рима: Новые раскопки проясняют и такой острый дискуссионный вопрос, как дата самого возникновения Рима...
Биохимия спиртового брожения: Основу технологии получения пива составляет спиртовое брожение, - при котором сахар превращается...
© cyberpedia.su 2017-2024 - Не является автором материалов. Исключительное право сохранено за автором текста.
Если вы не хотите, чтобы данный материал был у нас на сайте, перейдите по ссылке: Нарушение авторских прав. Мы поможем в написании вашей работы!