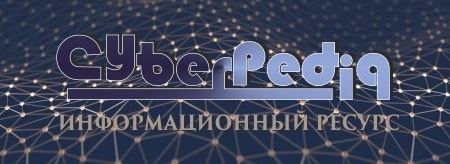
Адаптации растений и животных к жизни в горах: Большое значение для жизни организмов в горах имеют степень расчленения, крутизна и экспозиционные различия склонов...
Кормораздатчик мобильный электрифицированный: схема и процесс работы устройства...
Топ:
Оценка эффективности инструментов коммуникационной политики: Внешние коммуникации - обмен информацией между организацией и её внешней средой...
История развития методов оптимизации: теорема Куна-Таккера, метод Лагранжа, роль выпуклости в оптимизации...
Установка замедленного коксования: Чем выше температура и ниже давление, тем место разрыва углеродной цепи всё больше смещается к её концу и значительно возрастает...
Интересное:
Финансовый рынок и его значение в управлении денежными потоками на современном этапе: любому предприятию для расширения производства и увеличения прибыли нужны...
Наиболее распространенные виды рака: Раковая опухоль — это самостоятельное новообразование, которое может возникнуть и от повышенного давления...
Лечение прогрессирующих форм рака: Одним из наиболее важных достижений экспериментальной химиотерапии опухолей, начатой в 60-х и реализованной в 70-х годах, является...
Дисциплины:
![]() |
![]() |
5.00
из
|
Заказать работу |
|
|
Среднелегированные стали применяют для изготовления конструкций, работающих при низких или высоких температурах, при ударных и знакопеременных нагрузках, в агрессивных средах и других тяжелых условиях. Их разделяют на теплоустойчивые, высокопрочные и др.
Для обеспечения требуемого качества сварных соединений необходимо выполнение ряда технологических приемов.
● В деталях из высокопрочной легированной стали должны быть предусмотрены плавные переходы при соединении элементов и изменении сечений, плавные закругления угловых соединений и другие конструктивные формы, устраняющие концентрацию напряжений.
● Сборку элементов рекомендуется производить в сборочных приспособлениях, обеспечивающих свободную усадку швов и сохранение при этом размеров конструкций.
● Сварные швы выполняют с предварительным и сопутствующим подогревом, если прочность сварного соединения должна быть не ниже прочности основного металла. Листовые конструкции толщиной до 3 мм и менее сваривают без подогрева, при большей толщине используется подогрев. Например, для сталей ЗОХГСА, 25ХГСА температура подогрева составляет 200-300 °С. Для того чтобы избежать перегрева, применяют сварку на малой погонной энергии (пониженное тепловложение). После сварки соединение подвергают термообработке - высокому отпуску.
● Сварные швы выполняют без предварительного и сопутствующего подогрева, если к сварному соединению не предъявляются требования прочности, близкой прочности основного металла. При этом сварку швов ведут электродами, обеспечивающими получение аустенитного металла шва. В этом случае последующую термообработку не производят.
|
При сварке среднелегированных сталей могут образовываться закалочные структуры, холодные трещины, возможен перегрев металла околошовной зоны. Чем выше содержание углерода и легирующих примесей, толще металл, тем хуже свариваемость этих сталей.
Среднелегированные стали сваривают покрытыми электродами с основным покрытием постоянным током обратной полярности.
В зависимости от требований, предъявляемых к металлу шва, используют электроды, обеспечивающие получение среднелегированного металла шва. К ним относятся электроды марок У ОНИ-13/85 (типа Э85), ВИ-10-6 (типа Э100), НИАТ-ЗМ (типа Э125), НИАТ-3 (типа
Э150) и электроды, обеспечивающие получение аустенитного металла шва, например марки НИАТ-5 (типа Э-11Х15Н25М6АГ2).
Швы выполняются многослойными, каскадным или блочным способом, с малыми интервалами времени между наложением слоев. Подогрев металла выше 150 °С снижает вероятность образования закалочных структур и трещин. Электроды перед сваркой прокаливают. Кромки металла следует тщательно защищать от влаги, ржавчины, органических и других загрязнений.
Стали 20ХГСА, 25ХГСА, ЗОХГСА, ЗОХГСНА сваривают электродами марок ЦЛ-18-63, ЦЛ-30-63, НИАТ-ЗМ, ЦЛ-14, УОНИ-13/85 предельно короткой дугой. После сварки соединения подвергают термической обработке - закалке с температуры 880 °С и низкому отпуску с целью обеспечения высокой прочности.
28) Особенности сварки чугунов. Температурный режим сварки. Виды технологий. Сварочные материалы.
Чугун имеет ряд специфических свойств и особенностей, которые требуются принимать во внимание перед его сваркой и требуют применения специальных технологий
· Высокая скорость охлаждения, что приводит к отбелеванию, образование слоя белого хрупкого чугуна, который является необрабатываемым.
· Низкие пластические свойства чугуна. Делает чугун способным к перенапряжениям и в результате сварки могут образовываться трещины
· Выгорание углерода при сварке. В результате выгорания образуется окись СО, которая способствует образованию пор при сварке
|
Технологии сварки чугуна
Перед сваркой и ремонтом литья из чугуна необходимо обработать поверхность, чтобы она была гладкой и чистой. Чистая поверхность обеспечивает очень хорошее качество сварки, а также защищает чугун от растрескивания. Сварка чугуна может осуществляться в двух направлениях:
· С подогревом – горячая сварка чугуна
· Без подогрева – холодная сварка
Сварка с предварительным подогревом – горячая или полугорячая
Технология сварки чугуна с подогревом, как правило, используется в тяжелой промышленности. Концепция применения подогрева делает процесс сложнее, так как для него требуется специальное оборудование для прогрева.
В большинстве случаев изделие под сварку нагревается до температуры от 250 до 650 градусов. Следует избегать нагрева более 750 градусов, когда металл переходит в стадию расплавления.
После того, как металл достигает требуемой температуры, начинают его сварку на малых токах, чтобы минимизировать перемешивание и остаточные напряжения.
Большое внесение тепла при сварке также может привести к растрескиванию. После сварки изделие должно охлаждаться постепенно. Для постепенного охлаждения изделие следует поместить в песок или накрыть при помощи специальных изоляционных материалов.
Холодная сварка чугуна без предварительного прогрева
При технологии холодной сварки (без подогрева) очень важно иметь хороший контроль над сварочной дугой и делать как можно короткие сварочные швы. Самый лучший вариант, чтобы швы были длиной не больше 25 мм. Также очень важно, чтобы они остывали постепенно.
Процессы электродуговой сварки чугуна
· Ручная дуговая сварка электродами
· Аргонодуговая сварка
· Полуавтоматическая сварка
Ручная дуговая сварка чугуна покрытыми электродами
Существует четыре типа электродов, которые могут быть использованы для ручной дуговой сварки чугуна: чугунные электроды, электроды с медной основой, электроды с никелевой основой и стальные электроды. Для использования каждого из этих типов электродов есть свои причины и особенности: обрабатываемость, прочность и пластичность шва после сварки.
При сварке чугунными электродами, необходим разогрев детали до температуры в диапазоне от 120 °C до 425 °C, в зависимости от размера детали. Обычно чугунные электроды бывают диаметром от 6 до 15 мм, и сварочный ток для них требуется от 200 до 600 Ампер. Лучше использовать электроды малого диаметра и относительно низкие токи сварки.
|
Существует два типа электродов с медной основой: электроды из сплава олова (ECuSn) и электроды из сплава алюминия (ECuAl). Электродами из сплава олова производят пайку с получением швов с хорошей пластичностью. Алюминиевые электроды применяют для получения более прочного сварного шва.
Существует три типа электродов с никелевой основой. Первый тип (ENiFe-CI) содержит около 50% никеля, второй (ENiCI) содержит около 85% никеля и тип (ENiCu) содержит никель и медь. Применение этих электродов дает примерно одинаковые результаты. Эти электроды могут быть использованы для сварки без подогрева, но рекомендуется нагрев до 40 °C.
Стальные электроды (E-St) не рекомендуются для сварки чугуна, если сварочный шов будет впоследствии механически обрабатываться. Этот тип электродов должен использоваться только для мелкого ремонта.
Технология полуавтоматической сварки
Для сварки чугуна при использовании защитных газов таких как гелий, аргон, азот, углекислый газ и т.д. При этом процессе может быть использовано несколько типов сварочной проволоки, в том числе:
- Стальная проволока (E70S-3) с использованием смеси газов 80% Ar + 20% CO2.
- Никелевая проволока (ENiCu-B) с использованием 100% аргона для защиты.
- Кремний бронзовая проволока (ECuZn-C) с использованием 100% аргона (50% аргона +50% гелия).
Особенности аргонодуговой сварки
Сварка чугуна в аргоне возможна, но этот процесс очень сложный. Чугун содержит большое количество углерода, от 2% до 6%. Это содержание углерода, как говорилось выше, делает чугун очень хрупким и очень сложно свариваемым. При сварке чугуна требуется соблюдение технологии и тщательный контроль температуры для обеспечения качества сварного шва и предотвращения образования трещин.
При сварке аргоном используются никелевые присадочные прутки. Они являются наиболее предпочтительными и популярными для сварки не плавящимся электродом в среде защитного газа аргона. Так же применяются в качестве присадки алюминиево бронзовые прутки, которые намного дешевле. Но их использование не рекомендуется, если деталь впоследствии будет подвергаться тепловому воздействию.
|
Как и при любом другом процессе, при сварке аргоном необходимо соблюдать ряд требований:
· поверхность места сварки должно быть тщательно очищено от пыли и ржавчины
· деталь перед сваркой аргоном должна быть предварительно нагрета, чтобы предотвратить возможность трещин
· сварка должны вестись на низких токах короткими участками сварочного шва, чтобы контролировать температуру и препятствовать образованию трещин
· - каждый сварочный шов требуется простукивать молотком для снятия остаточных напряжений
· - после окончания сварки необходимо, чтобы изделие остывало медленно и постепенно
29) Способы наплавки металлических слоев с особыми свойствами.
Сущность наплавки состоит в нанесении сваркой плавлением на поверхность детали слоя металла, обладающего требуемым комплексом свойств. Непременным условием наплавки является получение надежного сплавления наносимого слоя с основным металлом и отсутствие или в отдельных случаях наличие минимального количества пор и трещин. Наплавку применяют как при изготовлении новых, так и при восстановлении изношенных деталей. В первом случае технический и экономический эффект достигается в результате получения биметаллических изделий с оптимальным сочетанием свойств металлов наплавленного и основного. Путем наплавки получают изделия с износостойкими, кислотоупорными, жаростойкими, антифрикционными и тому подобными свойствами.
Способы и технология наплавки
Дуговая наплавка под флюсом. Нагрев и расплавление металла, так же как при сварке, осуществляются теплом дуги, горящей между плавящимся электродом и основным металлом под слоем флюса. Наплавка под флюсом является одним из основных видов механизированной наплавки. Основными преимуществами являются непрерывность и высокая производительность процесса, незначительные потери электродного металла, отсутствие открытого излучения дуги. Отличительной особенностью наплавки под флюсом является хороший внешний вид наплавленного слоя (гладкая поверхность и плавный переход от одного наплавленного валика к другому). В процессе наплавки возможны четыре основных способа легирования наплавленного металла.
1. Применение легированной проволоки или ленты и обычных плавленых флюсов. Для наплавки используют легированные сварочные проволоки, специальные наплавочные проволоки и легированные ленты, в том числе спеченные. Наплавка производится под флюсами АН-20, АН-26 и др., которые выбирают в зависимости от состава электродного металла.
|
2. Применение порошковой проволоки или порошковой ленты и обычных плавленых флюсов. Порошковая проволока или лента расплавляется в дуге и образует однородный жидкий расплав. Этот способ позволяет получить наплавленный металл с общим содержанием легирующих примесей до 40 - 50%. Марка порошковой проволоки или ленты выбирается в зависимости от необходимого типа наплавленного металла и его требуемой твердости.
3. Применение обычной низкоуглеродистой проволоки или ленты и легирующих наплавленных флюсов (керамических). Этот способ позволяет ввести в наплавленный металл до 35% легирующих примесей. При наплавке наибольшее применение получили керамические флюсы АНК-18 и АНК-19, обеспечивающие хорошее формирование наплавленного металла, легкую отделимость шлаковой корки, высокую стойкость наплавленного металла против образования пор и трещин.
4. Применение обычной низкоуглеродистой проволоки или ленты и обычных плавленых флюсов с предварительной укладкой легирующих материалов на поверхность наплавляемого изделия.
Здесь возможна предварительная засыпка или дозированная подача легирующих порошков, а также предварительная укладка прутков или полосок легированной стали, намазывание специальных паст на место наплавки и др. Во всех случаях нанесенный легирующий
материал расплавляется дугой и переходит в наплавленный металл.
Дуговая наплавка в защитных газах. Наплавку в защитных газах применяют в тех случаях, когда невозможны или затруднены подача флюса и удаление шлаковой корки. Преимуществами данного вида наплавки являются визуальное наблюдение за процессом и возможность его широкой механизации и автоматизации с использованием серийного сварочного оборудования. Ее применяют при наплавке деталей в различных пространственных положениях, внутренних поверхностей, глубоких отверстий, мелких деталей и сложных форм и т.п. Технология выполнения наплавки в защитных газах во многом сходна с технологией наплавки под флюсом, отличие лишь в том, что вместо флюсовой применяют газовую защиту зоны сварки. Помимо перечисленных преимуществ это освобождает сварщика от необходимости засыпки флюса и удаления шлака. С целью уменьшения разбрызгивания металла наплавка в защитном газе производится самой короткой дугой. Наплавку плоских поверхностей во избежание коробления деталей производят отдельными участками «вразброс». Цилиндрические детали можно наплавлять по винтовой линии как непрерывным валиком, так и с поперечными колебаниями электрода: Короткие участки могут наплавляться продольными валиками вдоль оси цилиндрической детали, но здесь возможно возникновение деформаций, которые в процессе наплавки следует уравновешивать. Для этого наплавка каждого последующего валика должна производиться с противоположной стороны по отношению к уже наплавленному. При наплавке внутренних цилиндрических и конических поверхностей применяют специальные удлиненные мундштуки.
Наплавка может производиться в углекислом газе, аргоне, гелии и азоте. Высоколегированные стали, а также сплавы на алюминиевой и магниевой основе наплавляются в аргоне или гелии. Наплавка меди и некоторых ее сплавов может производиться в азоте, который ведет себя по отношению к ней нейтрально. При наплавке углеродистых и легированных сталей используют более дешевый углекислый газ. Наплавка может производиться как плавящимся, так и неплавящимся электродами. Неплавящийся вольфрамовый электрод обычно применяют при наплавке в аргоне и гелии. Наибольшее распространение получила наплавка в углекислом газе плавящимся электродом на постоянном токе обратной полярности. Учитывая, что углекислый газ окисляет расплавленный металл, в наплавочную проволоку обязательно вводят раскислители (марганец, кремний и др.). При наплавке применяют как проволоку сплошного сечения, так и-порошковую. Для наплавки деталей из углеродистых и низколегированных сталей с целью восстановления их размеров применяют сварочные проволоки сплошного сечения Св-08ГС, Св-08Г2С, Св-12ГС, а также наплавочные Нп-40, Нп-50, Нп-30ХГСА и др. При необходимости получения наплавленного слоя с особыми свойствами применяют порошковые проволоки.
Недостатком способа является то, что в процессе наплавки в углекислом газе наблюдается сильное разбрызгивание жидкого металла, приводящее к налипанию брызг на мундштук и засорению сопла горелки. Кроме того, возможность сдувания газовой струи ветром затрудняет наплавку на открытом воздухе.
Дуговая наплавка порошковыми проволоками. Наплавка порошковой проволокой с внутренней защитой основана на введении в сердечник проволоки кроме легирующих компонентов также шлакообразующих и газообразующих материалов. Применение флюсовой и газовой защиты при наплавке такой проволокой не требуется. Легирующие элементы порошковой проволоки переходят в шов, а газо- и шлакообразующие материалы создают защиту металла от азота и кислорода воздуха. В дуге тонкая пленка расплавленного шлака покрывает капли жидкого металла и изолирует их от воздуха. Разложение газообразующих материалов создает поток защитного газа. После затвердевания на поверхности наплавленного валика образуется тонкая шлаковая корка, которая может не удаляться при наложении последующих слоев. При наплавке используют различные самозащитные порошковые проволоки. Для наплавки низкоуглеродистых слоев используют сварочные проволоки типа ПП-АН3 и др. Для получения слоев с особыми свойствами применяют специальные проволоки. Так, для наплавки деталей, работающих при больших давлениях и повышенных температурах, применяют порошковую проволоку ПП-3ХВ3Ф-О, наплавку деталей, подвергающихся интенсивному абразивному износу, производят самозащитной порошковой проволокой ПП-У15Х12М-О (буква О в обозначении марки порошковой проволоки указывает, что данная порошковая проволока предназначена для наплавки открытой дугой).
Технология выполнения наплавки самозащитной порошковой проволокой в основном ничем не отличается от технологии наплавки в углекислом газе. Открытая дуга дает возможность точно направлять электрод, наблюдать за процессом формирования наплавляемого слоя, что имеет большое значение при наплавке деталей сложной формы. Одним из преимуществ этого способа является применение менее сложной аппаратуры по сравнению с аппаратурой, применяемой при наплавке под флюсом и защитном газе, а также возможность выполнять наплавочные работы на открытом воздухе; увеличивается производительность по сравнению с наплавкой под флюсом и в защитных газах, снижается себестоимость наплавляемого металла.
30) Напыление — технологический процесс образования покрытий.
Напыление — технологический процесс образования покрытий. Процесс образования покрытия очень сложен и охватывает целый ряд одновременно протекающих физических и химических явлений, причем продолжительность этих явлений находится в интервале от наносекунд до минут.
Существует несколько способов напыления покрытий:
1) Газопламенное напыление проволокой, порошком или прутком. Напыляемый материал расплавляется в пламени газовой горелки при сжигании горючего газа (обычно ацетилено-кислородная смесь в пропорции 1:1) и переносится на поверхность струей сжатого воздуха. Температура плавления напыляемого материала должна быть ниже температуры пламени горючей смеси.
Преимуществами данного способа являются низкие затраты на оборудование и его эксплуатацию.
2) Детонационное напыление производится несколькими циклами в секунду, за каждый цикл толщина напыленного слоя составляет около 6 мкм. Диспергированные частицы имеют высокую температуру (более 4000 град.) и скорость (более 800 м/с). При этом температура основного металла невелика, что исключает его тепловое деформирование. Однако деформация может произойти от действия детонационной волны, это и является ограничением применения данного метода. Стоимость детонационного оборудования также велика, требуется наличие специальной камеры.
3) Электродуговая металлизация. В сопло электрометаллизатора подаются две проволоки, одна из которых служит анодом, а другая — катодом. Между ними возникает электрическая дуга и проволока плавится. Распыление происходит при помощи подачи сжатого воздуха. Процесс протекает на постоянном токе. Данный метод обладает следующими преимуществами:
· а) высокая производительность (до 40 кг/ч напыляемого металла),
· б) более прочные покрытия с высокой адгезией по сравнению с газопламенным способом,
· в) возможность использования проволок из разных металлов позволяет получить покрытие-«псевдосплав»,
· г) невысокие эксплуатационные затраты.
Недостатками электродуговой металлизации являются:
· а) возможность перегрева и окисления напыляемых материалов при малой скорости их подачи,
· б) выгорание легирующих элементов напыляемых материалов.
4) Плазменное напыление. В плазмотронах анодом служит сопло, охлаждаемое водой, а катодом — вольфрамовый стержень. В качестве плазмообразующего газа обычно используют аргон и азот, иногда с добавлением водорода. Температура на выходе из сопла может составлять несколько десятков тысяч градусов, в результате резкого расширения газа плазменная струя приобретает высокую кинетическую энергию.
Высокотемпературный процесс плазменного напыления позволяет наносить тугоплавкие покрытия. Изменение режима напыления дает возможность использования самых различных материалов — от металла до органики. Плотность и адгезия таких покрытий также высоки. Недостатками метода являются: относительно невысокая производительность и интенсивное ультрафиолетовое излучение.
5) Электроимпульсное напыление. Метод основан на взрывном плавлении проволоки при прохождении через нее электрического разряда конденсатора. При этом около 60% проволоки расплавляется, а остальные 40% переходят в газообразное состояние. Расплав представляет собой очень мелкие частицы от нескольких сотых долей до нескольких миллиметров. При чрезмерном уровне разряда металл проволоки полностью превращается в газ. Перемещение частиц к напыляемой поверхности происходит за счет расширения газа при взрыве.
Преимуществами метода являются отсутствие окисления в результате вытеснения воздуха, высокая плотность и прочность сцепления покрытия. К недостаткам относятся ограничение в выборе материалов (они должны быть электропроводными), а также невозможность получения покрытий большой толщины.
6) Лазерное напыление. При лазерном напылении порошок подается на лазерный луч через подводящее сопло. В пучке лазера порошок расплавляется и наносится на деталь. Защитный газ служит для предохранения от окисления. Областью применения лазерного напыления является покрытие штамповочных, гибочных и режущих инструментов.
Порошковые материалы применяются при газопламенном, плазменном, лазерном и детонационном напылении. Проволока или пруток — при газопламенном, электродуговом и электроимпульсном напылении. Чем мельче фракция порошка, тем меньше пористость, лучше адгезия и выше качество покрытия. Напыляемую поверхность при любом способе напыления располагают на расстоянии не менее 100 мм от сопла.
Напыление покрытий применяется:
· в общем машиностроении для упрочнения деталей (подшипники, ролики, шестерни, калибры, в том числе резьбовые, станочные центры, матрицы и пуансоны, и др.);
· в автомобильной промышленности для нанесения покрытий на коленвалы и распредвалы, кулаки тормозов, цилиндры, головки и кольца поршней, диски сцепления, выхлопные клапаны;
· в авиационной промышленности для нанесения покрытий на сопла и другие элементы двигателей, лопатки турбин, для облицовки фюзеляжа;
· в электротехнической промышленности — для покрытий конденсаторов, отражателей антенн;
· в химической и нефтехимической промышленности — для покрытия клапанов и седел клапанов, сопел, плунжеров, валов, крыльчаток, цилиндров насосов, камер сгорания, для защиты от коррозии металлоконструкций, работающих в морской среде;
· в медицине — для напыления электродов озонаторов, зубных протезов;
· в быту — для упрочнения кухонного оборудования (посуда, плиты).
31) Технологии термической резки металлов
Термическая резка металла – основной промышленный метод разделки металла толщиной от 0,5 до 350 мм. В настоящее время наибольшее распространение получили технологии термической резки металла:
· Плазменная резка
· Газокислородная резка
· Лазерная резка
Плазменная резка
Плазмой называют четвертое состояние вещества. Плазменная резка использует свойства ионизированного газа, образующегося в электрической дуге под высоким давлением. Такая электрическая дуга обладает высокой электропроводимостью, что дает возможность сформировать ее в тонкую струю температурой от 5000 до 30000 градусов. Такая струя позволяет резать любые электропроводные металлы и их сплавы.
Плазменная резка – высокопроизводительная технология для обработки листового металла толщиной от 0,5 до 150 мм. Получение максимального полезного эффекта плазменной технологии резки обеспечивается на толщинах стали от 1,5 до 40 мм. В этом диапазоне толщин плазма позволяет получить:
· Высокую скорость резки
· Высокую точность резки
· Наилучшую шероховатость поверхности реза
Газокислородная резка
Газокислородная (автогенная) резка металла заключается в сгорании предварительно разогретого металла в струе химически чистого кислорода, с последующим удалением (выдувкой) этой струей расплавленного металла из зоны резки. Современная газокислородная технология позволяет резать сталь толщиной от 2 до 2000 мм. Диапазон максимально полезной эффективности газокислородной резки составляет 30-300 мм. Главными преимуществами данной технологии являются:
· Простота использования
· Возможность резать большие толщины
· Низкая стоимость оборудования
Лазерная резка
Резка при помощи лазера приводит к местному нагреву металла с последующим выдуванием расплавленного металла из зоны резки. Эту технологию резки металла отличает высокая производительность и точность реза, ширина реза составляет всего 0,5 мм. Применяется лазерная резка для изготовления изделий любой сложности из черных, цветных металлов, сплавов, пластиков, стекла и дерева. Резка металла лазером производится в диапазоне от 0,2 до 35 мм, но высокую эффективность показывает на толщинах до 12 мм. Основные преимущества лазерной резки:
· Высокая скорость резки
· Малая ширина реза и высокая точность деталей
· Возможность резки тонколистового материала
· Высокая производительность и эффективность
|
|
Адаптации растений и животных к жизни в горах: Большое значение для жизни организмов в горах имеют степень расчленения, крутизна и экспозиционные различия склонов...
История развития хранилищ для нефти: Первые склады нефти появились в XVII веке. Они представляли собой землянные ямы-амбара глубиной 4…5 м...
Археология об основании Рима: Новые раскопки проясняют и такой острый дискуссионный вопрос, как дата самого возникновения Рима...
Двойное оплодотворение у цветковых растений: Оплодотворение - это процесс слияния мужской и женской половых клеток с образованием зиготы...
© cyberpedia.su 2017-2024 - Не является автором материалов. Исключительное право сохранено за автором текста.
Если вы не хотите, чтобы данный материал был у нас на сайте, перейдите по ссылке: Нарушение авторских прав. Мы поможем в написании вашей работы!