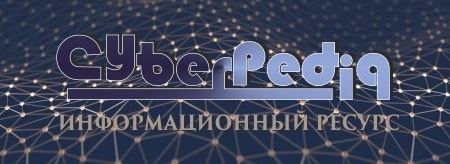
Архитектура электронного правительства: Единая архитектура – это методологический подход при создании системы управления государства, который строится...
Индивидуальные и групповые автопоилки: для животных. Схемы и конструкции...
Топ:
История развития методов оптимизации: теорема Куна-Таккера, метод Лагранжа, роль выпуклости в оптимизации...
Генеалогическое древо Султанов Османской империи: Османские правители, вначале, будучи еще бейлербеями Анатолии, женились на дочерях византийских императоров...
Техника безопасности при работе на пароконвектомате: К обслуживанию пароконвектомата допускаются лица, прошедшие технический минимум по эксплуатации оборудования...
Интересное:
Подходы к решению темы фильма: Существует три основных типа исторического фильма, имеющих между собой много общего...
Как мы говорим и как мы слушаем: общение можно сравнить с огромным зонтиком, под которым скрыто все...
Искусственное повышение поверхности территории: Варианты искусственного повышения поверхности территории необходимо выбирать на основе анализа следующих характеристик защищаемой территории...
Дисциплины:
![]() |
![]() |
5.00
из
|
Заказать работу |
Технология переработки сырья на ДОФ-1
Дробление
Подача сырья производится в приемный бункер емкостью 1000 т. Для предохранения пластинчатого питателя в бункере постоянно поддерживается подушка высотой 1000 мм. В зимнее время бункер обогревается. Для устранения зависания сырья в бункере, используется кран-балка.
Пластинчатым питателем 1-24-120 сырье из приемного бункера подается на I стадию дробления в щековую дробилку СМД-117, где материал дробится до крупности 0-300 мм, после чего ленточным конвейером подается на колосниковый грохот, надрешетный продукт направляется на II стадию дробления в конусную дробилку КСД-2200Гр, где материал дробится до крупности 0-150 мм, подрешетный продукт направляется на III стадию дробления. После II стадии материал рассеивается на тяжелом грохоте ГИТ-51Н, надрешетный продукт направляется на III стадию дробления в конусную дробилку КМД-2200Гр, где дробится до крупности 0-80 мм. Подрешетный продукт с грохота ГИТ-51Н смешивается с продуктом III стадии дробления и ленточными конвейерами подается в промежуточные бункера сепарации.
Технические характеристики пластинчатого питателя 1-24-120
№ пп | Основные данные | Ед. измерения | Величина |
1 | Длина | мм | 12000 |
2 | Ширина | мм | 2400 |
3 | Масса | кг | 88872 |
4 | Производительность | м3/ч | 200-600 |
5 | Скорость | м/с | 0,02-0,06 |
6 | Мощность двигателя | кВт | 75 |
7 | Число оборотов | об/мин | 500-1500 |
Технические характеристики дробилок ДОФ-1
№ пп | Основные данные | Ед. измерения | СМД-117 | КСД-2200Гр | КМД-2200Гр |
1 | Размер наибольшего куска в питании | мм | 1300 | 300 | 110 |
2 | Размер разгрузочной щели | мм | 135-225 | 30-60 | 10-20 |
3 | Ход щеки | мм | 28 | - | - |
4 | Производительность | м3/ч | 550 | 360-610 | 220-260 |
5 | Число оборотов электродвигателя | об/мин | 495 | 495 | 495 |
6 | Мощность электродвигателя | кВт | 250 | 250 | 250 |
7 | Частота вращения главного вала (конуса) | мин-1 | 125 | 242 | 242 |
8 | Масса дробилки без электрооборудования | кг | 164 000 | 77 800 | 77 700 |
Технические характеристики грохотов
№ пп | Показатели | Ед. измерения | Типы грохотов | |
ГИТ-51Н | Колосниковый | |||
1 | Номер грохота | 11 | К1 | |
2 | Размеры просеивающей поверхности | мм | 1750х3500 | 1300х2200 |
3 | Число сит (колосниковых решеток) | шт. | 1 | 1 |
4 | Угол наклона короба (колосниковой решетки) | град. | 25 | 25 |
5 | Частота колебаний короба | мин-1 | 735 | - |
6 | Амплитуда колебаний (полуразмах) | мм | 7 | - |
7 | Мощность электродвигателя | кВт | 18,5 | - |
8 | Масса грохота | кг | 6890 | 1000 |
9 | Производительность максимальная | т/час | 1000 | 520 |
Сухая магнитная сепарация
Основной задачей при сепарации материала является получение качественного концентрата крупностью 0-50 мм со средним содержанием железа – 32%. На сепарации ДОФ-1 обогащаются вкрапленные руды крупностью 0-70 мм, шлировые руды на ДОФ-1, как правило, не перерабатываются.
Сырая руда, поступающая на сепарацию, усредняется в промежуточных бункерах. Материал поступает на обогащение на четыре сепаратора ПБС-90/150. Загрузка сепараторов осуществляется равномерно с помощью ленточных питателей. Сепарация осуществляется в одну стадию.
Качество концентрата при обогащении вкрапленных руд регулируется с помощью отбойников. В начале смены мастер с сепараторщиком устанавливают режим обогащения (положение отбойника) путем отбора экспресс-анализов и визуального осмотра концентрата.
Шлировые руды перерабатываются на ДОФ-1 в исключительных случаях, при этом отбойники отжимаются полностью, и устанавливается минимальный слой при подаче материала на обогащение.
Технические характеристики сепаратора ПБС-90/150
№ пп | Основные данные | Ед. измерения | Величина |
1 | Диаметр барабана | мм | 900 |
2 | Ширина барабана | мм | 1500 |
3 | Число барабанов | шт. | 1 |
4 | Магнитная индукция в рабочей зоне | Тл | 0,132 |
5 | Мощность электродвигателя | кВт | 2 |
6 | Производительность | т/час | 200 |
7 | Частота вращения барабана | мин-1 | 25 |
Общий концентрат ленточными конвейерами подается в бункер. Отходы обогащения поступают на грохочение.
Получение строительного щебня из отходов обогащения
После обогащения хвосты ленточным конвейером подаются на сортировку №1 ДОФ-1 – четыре грохота (два ГИС-52, два ГИЛ-43), где разделяются на фракции крупностью 0-10 мм, 5-40 мм, 40-(70)80 мм.
Фракция 0-10 ленточными конвейерами подается на сортировку №1 ДОФ-1, 2 – два грохота ГИЛ-42, где разделяется на две – 0-5 мм и 3-10 мм.
Фракция 40-80 ленточными конвейерами подается на грохот ГУП – IК, где разделяется на две – 40-80(70) мм и +80 мм.
Фракция 5-40 мм ленточными конвейерами подается на сортировку №2 ДОФ-1 – два грохота ГИЛ-42, где разделяется на три фракции – 0-5 мм, 5-20 мм, 20-40 мм.
Полученный строительный щебень крупностью 3-10 мм, 5-20 мм, 20-40 мм, 40-80(70) мм,+80 мм и песчано-щебеночная смесь крупностью 0-5 и 0-10 мм ленточными конвейерами подаются на склад.
Полученная продукция должна соответствовать ГОСТ 8267-93 и ГОСТ 25607-94.
Технология переработки сырья на ДОФ-2
Дробление
Подача сырья производится в приемный бункер емкостью 500 т. Для предохранения пластинчатого питателя в бункере постоянно поддерживается подушка высотой 1000 мм. В зимнее время бункер обогревается. Для устранения зависания сырья в бункере, используется кран-балка.
Пластинчатым питателем 1-18-120 сырье из приемного бункера подается на I стадию дробления в щековую дробилку СМД-118, где материал дробится до крупности 0-300 мм, после чего ленточным конвейером подается на колосниковый грохот, надрешетный продукт направляется на II стадию дробления в конусную дробилку КСД-2200Гр, где материал дробится до крупности 0-150 мм, подрешетный продукт направляется на III стадию дробления. После II стадии материал рассеивается на тяжелом грохоте ГИТ-51Н, подрешетный продукт ленточными конвейерами подается на сортировку №1 ДОФ-2, надрешетный продукт направляется на III стадию дробления в конусную дробилку КМД-2200Гр, где дробится до крупности 0-60 мм. После III стадии материал рассеивается на тяжелом грохоте ГИТ-42, подрешетный продукт ленточными конвейерами подается на сортировку №1 ДОФ-2, надрешетный продукт вторично направляется на III стадию дробления (замкнутый цикл).
Сухая магнитная сепарация
После грохочения фракции 0-10 и +10 мм ленточными конвейерами подаются в промежуточные бункера. Заполнение бункеров производится с помощью загрузочных тележек. Бункер для фракции 0-10 мм имеет три секции, бункер для фракции +10 мм – пять секций. Разгрузка бункеров производится ленточными питателями (фракция +10 мм) и вибропитателями (фракция 0-10 мм).
Основная задача сепарации – получение качественного концентрата с содержанием железа 33-35% в крупном продукте и 27-30% в мелком продукте и получение объединенного концентрата с содержанием железа в среднем не менее 32%.
Для настройки режима сепарации, мастером и сепараторщиком устанавливается режим обогащения в зависимости от вида руды (вкрапленная, шлировая).
Вкрапленные руды обогащаются при силе тока 8-20 ампер. Отбойник находится в прижатом положении. Качество концентрата регулируется силой тока.
Шлировые руды обогащаются при максимальной силе тока 15-20 ампер. Отбойник находится в отжатом положении. Качество концентрата регулируется положением отбойника.
После настройки режима сепарации производится отбор проб на экспресс-анализ концентрата.
Обогащение крупного и мелкого материала производится раздельно. После обогащения концентрат объединяется.
Горнблендит
Показатели | Щебень фракции, мм | ПЩС (отсев) | ||||||
5(3)-10 | 5(3)-20 | 20-40 | 40-80(70) | 60-150 | 25-60 | 0-5 | 0-10 | |
Содержание зерен пластинчатой и лещадной формы | 13 - 25 19,2 | 9,7 - 22,4 17,1 | 13 – 31,3 22,6 | 12,1- 29,2 21,2 | 16 – 24,5 20,1 | 13,4 –22,0 16,7 | 19,2 | 19,2 |
Марка щебня: | ||||||||
– по дробимости | 1000-1200 | 1200-1400 | 1200-1400 | 1200-1400 | 1200-1400 | 1200-1400 | 1000-1200 | 1000-1200 |
– по истираемости | И1-И2 | И1-И2 | И1 | И1 | И1 | И20м-И40м | И2 | И2 |
– по сопротивлению удару на копре | – | – | – | – | – | У75-У50 | – | – |
Содержание слабых пород | До 5% | До 5% | До 5% | До 5% | До 5% | До 5% | – | – |
Содержание пылевидных и глинистых частиц | До 2% | До 2% | До 2% | До 2% | До 2% | – | <10% | <10% |
Содержание глины в комках | нет | нет | нет | нет | нет | нет | нет | нет |
Насыпная плотность т/м3 | 1,6 | 1,55 | 1,55 | 1,55 | 1,55 | 1,55 | 1,64 | 1,64 |
Морозостойкость | 200 | 300 | 300 | 300 | 300 | 300 | 200 | 200 |
Содержание частиц размером менее 0,16 мм | – | – | – | – | – | <1,5 | – | – |
Удельная электропроводность, см/м | – | – | – | – | – | 0,03 0,18 | – | – |
– в насыщенном растворе | – | – | – | – | – | <0,06 | – | – |
– в выпаренном растворе | – | – | – | – | – | <0,35 | – | – |
ГОСТ | 8267-93 | 8267-93 | 8267-93 | 8267-93 | ТУ | 7392-2002 | 25607-94 | 25607-94 |
Концентрат железорудный
Концентрат железорудный, выпускаемый на ДОФ, должен соответствовать требованиям ТУ-14-187-01 (срок введения 1.05.99г. – постоянный)
Содержание железа: среднее 32%, допустимое – не менее 30%.
Содержание влаги 1,5%, допустимое – не более 2%.
Содержание класса крупностью более 50 мм – не более 10%.
Конусная дробилка КМД-2200
В конусных дробилках материал дробится в кольцевом пространстве см. рис 2.1, образованном наружной неподвижной броней 6 и расположенным внутри этой брони подвижным дробящим конусом 21, насажанным на вал 16. Приближение дробящего конуса 21 к неподвижной броне 6 сопровождается дроблением кусков материала, поступающих в пространство между ними, а удаление - разгрузкой дробленного продукта, выходящего вниз под дробилку. Основное дробящее действие конусных дробилок - раздавливание, но имеет место и разлом кусков при изгибе, возникающим когда кусок зажат между вогнутой поверхностью чаши и выпуклой поверхностью дробящего конуса.
Станина 1 дробилки представляет собой цилиндрическую отливку. Нижним фланцем станина устанавливается на фундаменте. На верхнем фланце лежит опорное кольцо 2, представляющее собой также цилиндрическую отливку, на внутренней поверхности которой сделана винтовая нарезка. Кольцо своим фланцем скрепляется с фланцем станины длинными болтами 3 и пружинами 4. Пружины 4 служат для защиты дробилок от поломок. При попадании в камеру дробления недробимых предметов, пружины под действием усилий, значительно превышающих нормальное, сжимаются, наружная чаша вместе с установочным кольцом приподнимается и недробимый предмет проходит через дробилку. Еслинедробимый предмет настолько велик, что не выходит из камеры дробления, то конус заклинивается и дробилка останавливается; срабатывает электрическая система защиты. Для удаления застрявшего предмета современные дробилки снабжаются гидравлическими домкратами 27, позволяющие дополнительно поднять опорное кольцо с неподвижной чашей и освободить застрявший предмет.
Регулирующее кольцо представляет собой отливку с нарезкой на внешней цилиндрической поверхности, которой регулирующее кольцо ввинчивается в нарезку на опорном кольце. Внутренняя поверхность регулирующего кольца сделана конической, более широкой в нижней части. Она покрывается футеровкой 6 из марганцовистой стали. Неподвижная броня крепится с наружной стороны регулирующего кольца болтами 7, зацепляющимися с крючьями 9, отлитой заодно с неподвижной броней, которое пропускается через отверстие в регулирующем кольце. В нижней части регулирующего кольца броня ложится на обработанный бурт, а на всей остальной поверхности плотность прилегания неподвижной брони обеспечивается цинковой заливкой 8. Проемы, в которых размещены крепящие неподвижную броню болты, закрыты сверху кольцевым кожухом 10, соединенным с регулирующим кольцом стержнями 11с клиновым креплением. На кольцевом кожухе 10 укреплена приемная воронка 12. В нижней части станины имеется цилиндрическая втулка 13, отлитая с ребрами жесткости и станиной как одно целое. Вертикальные оси станины и втулки совпадают. Во втулку вставляется и жестко к ней крепится сменная бронзовая цилиндрическая втулка 14, выполняющая роль подшипника для эксцентрикового стакана 17. В верхней части эксцентрикового стакана закреплена большая коническая шестерня 34.В самом стакане сделана коническая расточка, расположенная эксцентрично относительно вертикальной оси стакана. Между хвостовиком вала 16 подвижного конуса и эксцентриковым стаканом 15 установлена промежуточная втулка 17. Хвостовик вала подвижного конуса имеет в нижней части сферическую поверхность, которая с центральной расточной промежуточной втулкой 17 образует шарнирное соединение. Это соединение фиксирует положение горизонтальной составляющей усилия дробления, передающееся на эксцентрик. Положение этой нагрузки эксцентрикового узла такое, что втулки 15,17 нагружаются центральной силой, в результате чего исклю исключается перекос и неравномерное нагружение рабочих поверхностей подшипников скольжения. Шарнирное соединение оказывается нагруженным элементом. Для повышения надежности его уменьшены скорости проскальзывания рабочих поверхностей: хвостовик 16 вала оканчивается прямоугольным выступом, который входит в прямоугольный паз вкладыша 18, запрессованный в промежуточную втулку 17.
Эксцентриковый стакан внизу опирается на подпятник 19, состоящий из нескольких скользящих друг по другу шайб. Подпятник лежит в гнезде на донной плите 20, которая прикреплена болтами к втулке 13. В верхней части на рабочем валу 16 жестко закреплен дробящий конус 21 и тарелка 22, равномерно подающая дробимый материал в камеру дробления дробилки.
Дробящий конус представляет собой отливку с пологой боковой поверхностью. Высота конуса примерно в 3 раза меньше диаметра его основания. Боковая поверхность конуса, которой он нажимает на куски материала, заполняющей камеру дробления, футерована кольцевой броней 23. Для плотного прилегания брони к поверхности конуса пространство между ними заполнено цинковой заливкой 24. Нижняя поверхность дробящего конуса тщательно обработана по сфере радиуса R. Этой сферической нижней поверхностью дробящий конус лежит на сферической опоре (подпятник) 25, служащей для него подпятником и связанной с втулкой станины. Сферический подпятник воспринимает вес дробящего конуса, вес рабочего вала и вертикальную составляющую усилия дробления. Таким образом вал 16 через посредство дробящего конуса как бы подвешен на сферическом подпятнике 25. При вращении эксцентрикового стакана ось рабочего вала описывает коническую поверхность с вершиной в точке, являющейся центром соприкасающихся сферических поверхностей конуса 21 и подпятника 25. При этом дробящий конус скользит по поверхности подпятника. Последний покрыт сменным бронзовым вкладышем 27, по которому скользит сферическая поверхность дробящего конуса. Для предотвращения проникновения пыли к сферическому подпятнику и приводному механизму в дробилке имеется гидравлический затвор 28. Подпятник 25 имеет кольцевую канавку, заполненную водой, которая подается под напором по трубопроводу через кольцевую камеру. Избыток воды переливается через порог канавки и по спускной кольцевой выточке и трубопроводу отводится из дробилки. К внутренней поверхности дробящего конуса прикреплен воротник 26, свободный обрез которого при работе дробилки все время погружен вводу, заполняющую канавку.
На распределительную тарелку 22 через загрузочную воронку 29 поступает дробимый материал. Тарелка вместе с дробящим конусом совершает круговые качания, оставаясь все время в наклонном положении. Материал, сползая по тарелке, падает в рабочее пространство дробилки по всей окружности приемного отверстия. Дробленый продукт разгружается из рабочего пространства вниз через кольцевую щель между дробящим конусом и наружной чашей; далее он выходит под дробилку на ленточный конвейер.
Привод у конусных дробилок мелкого дробления осуществлен непосредственно от электродвигателя, вал которого муфтой 30 соединяется с приводным валом 31. Приводной вал 31 с подшипниками 32 смонтирован в установочной обойме 33, закрепленной фланцем на станине дробилки. Жидкая смазка подается в дробилку от специального насоса к подпятнику, на который опирается эксцентриковый стакан. Заполнив гнездо подпятника, масло поднимается вверх по зазорам во втулках 14, 17 смазывает трущиеся поверхности эксцентрикового стакана и рабочего вала. Одновременно масло по осевому каналу, высверленному в теле рабочего вала, поднимается до дробящего конуса и по радиальному каналу на валу и в дробящем конусе подается на трущиеся поверхности сферического подпятника. После смазки и охлаждения всех этих поверхностей масло сливается на конические шестерни 34, смазывает их и по сливной трубе удаляется в бак - отстойник. установочная обойма приводного вала имеет самостоятельный подвод и слив масла.
Заключение
При прохождении практики на ОАО «Первоуральское рудоуправление» я узнала историю создания завода и разработки карьера. Так же я ознакомилась с процессом добычи и производства щебня и руды. Увидела работу конусной дробилки.
Данная практика была очень познавательна, так как моя специальность на прямую связана с работой этого завода.
Общие сведения о Первоуральском рудоуправлении
Титаномагнетитовые, малотитанистые, ванадийсодержащие руды Первоуральского месторождения располагаются в горнблендитовом теле, залегающим среди роговообманкового габбро в части Ревдинского массива. Полоса горнблендитов имеет меридианальное простирание, длиной 8-9 км и ширину в пределах месторождения 450-600 м. Месторождение состоит из трёх частей II, III, IV Магниток.
Первоуральское месторождение титаномагнетитовых разрабатывается открытым способом в настоящее время ОАО “Первоуральское рудоуправление”. Месторождение отрабатывалось комплексно. Продукцией рудоуправления является железо-ванадиевый концентрат и горнблендитовый щебень.
Титаномагнетитовые руды гор Магниток открыты в 1702 году крестьянином Уткинской слободы Фёдором Росовым. Титаномагнетитовые руды Первоуральского месторождения подразделяются на два типа руд: вкрапленные и сплошные (массивные).
В 1905-1907 годах район изучался Н.Н. Смирновым. Им отмечено, что руда залегает в виде густо расположенных отдельных шлиров различной мощности, разделённых пустой породой. Переходы к вмещающим породам постепенные.
Основной этап изучения месторождения начат с 1929 года.
В 1929-1931 годах работы проводились партией УОМПИ (П.Г. Пантелеев). Установлена магнитная аномалия, проходящая через вершины гор Магниток.
Смена положительных и отрицательных напряжений объяснялась густой сетью шлиров титаномагнетита. Выделены основные формы рудных тел: 1.) шлировые прожилки мощностью от нескольких мм до 0.5 м; 2.) штокверковые залежи до 1.5 м; 3.) отдельные стяжения 5-15см; 4.) сгустки штокообразной формы 10*20 мм; 5.) вкрапленные с размером зёрен от микроскопических до 2-3 см. Максимальные запасы руд определялись в 65 млн. тонн.
В 1933-1934 годах трестом “Востокруда” на II и III Магитках пройдено 12 скважин (1177 пог. м). Произведён полный расчёт запасов, запасы в количестве 86.6 млн. тонн по категориям В+С1, утверждённые ЦКЗ 19.2.1936, явились основанием для разведки месторождения.
В 1936 году разведку месторождения ведёт Уральский геологоразведочный трест, а в 1937-1339 годы продолжает Первоуральское рудоуправление. В этот период на II и северной части III Магниток пройдено 46 буровых скважин общим метражом 4223 пог м.
В 1943 году П.С.Могилевской были подсчитаны запасы месторождения в количестве 84.3млн тонн по категориям В+С1, но небыли утверждены в виду недоработанности материалов.
С 1943 по 1955 годы разведку месторождения производила Первоуральская геологоразведочная партия треста “Уралгерметразведка”. Участки II и III Магниток были разведаны по сетке 50*50м и 50*25 м на глубину 100 м, участок IV Магнитки в северной и южной частях по сетке 100*50 м в центральной части 20050 м, на глубину 150 м скважинами ударно-канатного и колонкового бурения. Всего было пройдено 71 скважина общим метражом 9968 пог м.
В 1951 году был проведён промежуточный подсчёт по состоянию
1.01.1951 в количестве 142.1 млн. тонн по сумме категории А+В+С1 и 26.8 млн. тонн по категории С2.
В 1955 году А.Е. Галкина считала, что месторождение полностью разведано, оруденение оконтурено достоверно и никаких комментарий по дальнейшему направлению работ не даёт. Средняя глубина разведки месторождения соответствовала горизонту абсолютной отметки+250м.С увеличения запасов титаномагнетитовых руд в 1969 году разведочные работы на месторождении были возобновлены и продолжены до 1972 года.
Изучение технологических свойств титаномагнетитовых руд и вмещающих пород производили: Ландсберг, В.Д.Бененсон, Г.И. Конторович и др.
В 1962 году на площади месторождения производились гидрогеологические изыскания с целью установления возможностей водоснабжения рудного посёлка питьевой водой. Выявлены благоприятные условия для водоснабжения.
В 1907-1908 годах на северо-западном склоне II Магнитки был заложен карьер с шестью уступами. После двух летней разработки карьер имел размеры 60на 80 м, глубина 15 м. Необходимость механизации работ и сложность металлургического процесса заставили прекратить работу и рудник был заброшен. Сведений о добыче не сохранилось.
В 1936 году Первоуральское рудоуправление возобновило разработку месторождения и продолжает её до сих пор.
Месторождение разрабатывается открытым способом - путем выборочной механизированной добычи руд, системой тупиковых железнодорожных съездов.
В настоящее время работы сосредоточены на II, III, IV Магнитках. Длина карьера охватывающего II, III, IV Магнитку составляет около 3500 м, наибольшая глубина 100 м.
Горные работы по добыче рудной массы и выемке вскрышных пород заключается в обуривании, взрывании и погрузке горной массы в ж/д вагоны типа думпкар и последующей транспортировкой рудной массы на дробильно-сортировочные фабрики ДОФ-1 и ДОФ-2 и вскрышных пород в отвал.
ОАО «Первоуральское рудоуправление» (рудник) является градообразующим предприятием пос. Магнитка г. Первоуральска.
Рудоуправление располагает полным пакетом основных правоустанавливающих и разрешительных документов.
Основными технологическими подразделениями рудника являются карьер и 2 дробильно-обогатительных фабрики (ДОФ). Технологический транспорт – железнодорожный (железнодорожный цех).
Рудоуправление обладает развитой инфраструктурой и вспомогательными службами. Однако основные фонды характеризуются значительным износом и практически не обновляются.
Товарной продукцией рудника в порядке значимости являются:
- щебень в диапазоне фракций 5(3)÷150 мм;
- песчано – щебеночная смесь фракций 0-5 и 0-10 мм;
- товарная руда – железованадиевый концентрат сухой магнитной сепарации с содержанием железа от 32 до 36%;
- взорванная скальная порода (скала).
В современных реалиях рыночной экономики конкурентоспособность продукции низкая из-за ее невысокого качества. Ввиду пониженного спроса на товарную продукцию в настоящее время производственные мощности рудоуправления используются частично, в сравнении с показателями 1990 г. в 2009 г. их использование составило: по карьеру (горная масса) – 53,4%; по дробильно-обогатительным фабрикам (переработка скальных грунтов) – 58,8%.
При сохранении тенденции падения спроса на продукцию, производство Первоуральского рудоуправления будет убыточным.
Функционирование предприятия в ближайшей перспективе с учетом его социальной значимости возможно лишь при весомой региональной поддержке. Без поддержки Первоуральское рудоуправление обанкротится, а на его базе может функционировать малое предприятие с минимальным выпуском щебня для обеспечения нужд близлежащих потребителей.
Папиллярные узоры пальцев рук - маркер спортивных способностей: дерматоглифические признаки формируются на 3-5 месяце беременности, не изменяются в течение жизни...
История создания датчика движения: Первый прибор для обнаружения движения был изобретен немецким физиком Генрихом Герцем...
Автоматическое растормаживание колес: Тормозные устройства колес предназначены для уменьшения длины пробега и улучшения маневрирования ВС при...
История развития пистолетов-пулеметов: Предпосылкой для возникновения пистолетов-пулеметов послужила давняя тенденция тяготения винтовок...
© cyberpedia.su 2017-2024 - Не является автором материалов. Исключительное право сохранено за автором текста.
Если вы не хотите, чтобы данный материал был у нас на сайте, перейдите по ссылке: Нарушение авторских прав. Мы поможем в написании вашей работы!