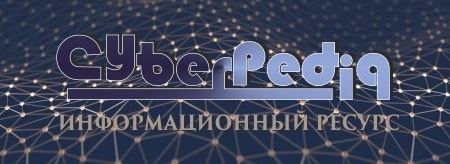
Индивидуальные очистные сооружения: К классу индивидуальных очистных сооружений относят сооружения, пропускная способность которых...
Общие условия выбора системы дренажа: Система дренажа выбирается в зависимости от характера защищаемого...
Топ:
Отражение на счетах бухгалтерского учета процесса приобретения: Процесс заготовления представляет систему экономических событий, включающих приобретение организацией у поставщиков сырья...
Характеристика АТП и сварочно-жестяницкого участка: Транспорт в настоящее время является одной из важнейших отраслей народного хозяйства...
Выпускная квалификационная работа: Основная часть ВКР, как правило, состоит из двух-трех глав, каждая из которых, в свою очередь...
Интересное:
Аура как энергетическое поле: многослойную ауру человека можно представить себе подобным...
Берегоукрепление оползневых склонов: На прибрежных склонах основной причиной развития оползневых процессов является подмыв водами рек естественных склонов...
Принципы управления денежными потоками: одним из методов контроля за состоянием денежной наличности является...
Дисциплины:
![]() |
![]() |
5.00
из
|
Заказать работу |
|
|
Наиболее часто в практике очистки сточных вод используются адсорберы с неподвижным слоем поглотителя (сорбция в динамических условиях), аппараты с псевдоожиженным слоем адсорбента, а также аппараты, в которых обеспечивается интенсивное перемешивание обрабатываемой воды с порошкообразным или пылевидным сорбентом (сорбция в статических условиях). Процесс целесообразно проводить при таких гидродинамических режимах, чтобы он лимитировался во внутридиффузионной области, сопротивление которой можно снизить, изменяя структуру адсорбента и уменьшая размеры зерна.
В зависимости от области применения метода сорбционной очистки, места расположения адсорберов в общем комплексе очистных сооружений, состава сточных вод и крупности сорбента и др. назначают схему сорбционной очистки и тип адсорбера. Так, например, перед сооружениями биологической очистки применяют насыпные фильтры с диаметром зерен сорбента 3 − 5 мм или адсорберы с псевдоожиженным слоем сорбента с диаметром зерен 0,5 − 1 мм. При глубокой очистке производственных сточных вод и возврате их в систему оборотного водоснабжения применяют аппараты с мешалкой и намывные фильтры с крупностью зерен до 0,1 мм[15].
Насыпной фильтр. Наиболее простым является насыпной фильтр, представляющий колонну с рядом слоев сорбента, помещенных между фиксирующими решетками, через которые фильтруется сточная вода. Скорость фильтрования в зависимости от концентрации загрязняющих веществ 1 − 6 м/ч, направление фильтрования жидкости снизу вверх. Фильтры с неподвижным слоем сорбента применяют при регенеративной очистке сточных вод с целью утилизации выделенных относительно чистых продуктов. Обычно сорбционная установка представляет собой несколько параллельно работающих секций, состоящих из 3 − 5 последовательно расположенных фильтров.
|
Статическая адсорбция. Статическая одноступенчатая адсорбция нашла применение в тех случаях, когда адсорбент очень дешев или является отходом производства. Более эффективно (при меньшем расходе адсорбента) процесс протекает при использовании многоступенчатой установки. При этом после окончания процесса в первой ступени адсорбент отделяют отстаиванием или фильтрованием, а сточную воду направляют на вторую ступень, куда вводят свежий адсорбент.
Адсорбент с псевдосжиженным слоем. При относительно высоком содержании в сточной воде мелкодисперсных взвешенных частиц, заиливающих сорбенты, а также в случае, если равновесие устанавливается медленно, рационально применять процесс с псевдоожиженным слоем сорбента (периодического или непрерывного действия). При этом высокие скорости потока сточной воды, проходящей снизу вверх, вызывают интенсивное перемещение гранул адсорбента в объеме слоя, сохраняющего постоянную для данной скорости высоту. Наибольшее применение нашли цилиндрические одноярусные адсорберы [15].
Осуществление ступенчатой адсорбционной очистки в системе последовательно расположенных адсорберов-фильтров (гранулированный или зерненый адсорбент) или аэраторов-отстойников (порошкообразный адсорбент) позволяет существенно снизить (в 5–10) раз расход адсорбентов. [21].
Принципиальная технологическая схема адсорбционной очистки сточных вод включает следующие стадии: 1) первичную очистку сточных вод от взвешенных веществ в работающих поочередно накопительных емкостях; 2) собственно стадию адсорбционной очистки от поллютантов в системе, состоящей из последовательно работающих адсорберов и аэраторов-отстойников, 3) стадию отделения (при использовании порошкообразного адсорбента) и утилизации отработанного адсорбента. По мере отработки адсорбционной емкости углеродного адсорбента в первом адсорбере его разгружают, заполняют новой порцией углеродного адсорбента и включают в качестве последней ступени в технологической схеме адсорбционной очистки.
|
В фильтровальных сооружениях используются как тяжелые, так и плавающие загрузки.
Адсорбция на плавающих сорбентах. Технология адсорбционной очистки водоемов с помощью плавающих сорбентов достаточно проста: сорбент равномерно распределяют по поверхности загрязненной воды, а затем по истечении определенного времени собирают специальными приспособлениями. Регенерации сорбенты, обычно, не подлежат.
Особенность такого адсорбционного метода состоит в том, что распределенные на поверхности воды сорбенты практически не проникают в толщу загрязнения, и коэффициент их использования не высок. Частично устранить эти недостатки можно путем подачи тонкодисперсного сорбента в зону очистки из-под воды. Под действием выталкивающей силы сорбент всплывает на поверхность, проходя сквозь слой загрязнения, и поглощает растворенные в воде гидрофобные органические вещества. Обработку загрязненной воды сорбентом из-под воды целесообразно осуществлять напорным водным потоком с помощью эжекторного устройства [52].
Для обработки суспензий плавающими адсорбентами в адсорберах можно использовать обычное оборудование, например статические адсорберы, а также различные аппараты с циркулирующей жидкостью.
Регенерация адсорбентов. Важнейшей стадией процесса адсорбционной очистки сточных вод является регенерация адсорбента. Из угля адсорбированные вещества извлекают десорбцией насыщенным или перегретым водяным паром (0,3-0,6 МПа равна 200-300 °С) либо нагретым инертным газом (120-140 °С). После десорбции пары конденсируют и вещество извлекают из конденсата. Для регенерации углей может быть использована и экстракция органическими низкокипящими и легко перегоняющимися с водяным паром растворителями: метанолом, бензолом, толуолом, дихлорэтаном и др. По окончании десорбции остатки растворителей из угля удаляют острым паром или инертным газом. Для десорбции слабых органических электролитов их переводят в диссоциированную форму и вымывают из пор адсорбента горячей водой, раствором кислот (для удаления органических оснований) или раствором щелочей (для удаления кислот). Например, фенол десорбируют растворами гидроксида или карбоната натрия; В некоторых случаях проводят деструктивную окислительную или термическую регенерацию. Термическую регенерацию проводят в печах различной конструкции при температуре 700-800°С в бескислородной среде. Разрабатываются биологические методы регенерации углей, при которых адсорбированные вещества биохимически окисляются [15].
|
Ионный обмен
Ионообменный метод используется для удаления ионов металлов, прочих примесей, обессоливания. Его суть состоит в способности ионообменных материалов убирать из растворов электролита ионы, а давать эквивалентное количество ионов ионита. Для очистки используются синтетические ионообменные смолы в виде гранул – иониты. Они состоят из полимерных веществ, нерастворимых в воде, имеют на поверхности подвижные ионы, которые при соблюдении определенных условий вступают в реакции обмена с ионами аналогичного знака, которые есть в воде. Существуют слабо- и сильнокислые катиониты с анионитами, в отдельную категорию выделяются иониты смешанного действия. Избирательное поглощение молекул загрязняющих веществ поверхностью твердого адсорбента происходит в результате воздействия на них поверхностных неуравновешенных сил адсорбента.
Ионообменные материалы по химическому составу можно разделить на две группы: минеральные и органические.
Природные минеральные иониты являются, как правило, кристаллическими силикатами, жесткая решетка которых несет избыточный заряд. Наиболее важными представителями этой группы ионитов являются цеолиты, способные к обмену катионами. Катионы и нейтральные молекулы больших размеров не могут проникать в решетку цеолитов, вследствие чего цеолиты обладают ситовым эффектом и применяются в качестве ионных или молекулярных сит. Их применение в качестве ионнообменников ограничено из-за малой емкости поглощения и способности к разложению в кислой среде с выделением кремниевой кислоты.
На практике используются иониты на основе синтетических смол. Группы, придающие ионитам свойства катионитов: -SO3H (сульфогруппа), -СООН (карбоксильная) и -ОН (фенольная). Функциональными группами, придающими материалу смолы анионообменные свойства, являются различные аминогруппы (N, =NH, –NH2) и группы четырехзамещенного аммония (– NR3OH).
|
По способности извлекать из воды ионы различных металлов катиониты делятся на сильно-, средне- и слабокислотные. Сильнокислотные способны извлекать из воды ионы как сильных (Na+, K+, NH4+ и др.), так и слабых оснований (Pb2+, Hg2+ и др.). Слабокислотные катиониты способны извлекать из воды только катионы сильных оснований. Сильнокислотные катиониты позволяют осуществлять процесс ионного обмена при любых значениях рН, а слабокислотные – при рН ≥ 7.
Аниониты также делятся на сильно-, средне- и слабоосновные. Сильноосновные аниониты могут извлекать анионы сильных и слабых кислот (SO42-, Cl-, NO3-, Br-, SiO32- и т. д.), слабоосновные – только сильных кислот. Сильноосновные аниониты применяются при любых значениях рН, слабоосновные – при рН ≤ 9.
Ионный обмен считается самым эффективным способом водоподготовки и умягчения воды. Жесткость воде придают растворенные в ней соли магния и кальция, а ионный обмен регулирует их содержание и нормализует состав.
С помощью ионного обмена можно удалить из сточных вод большинство катионов тяжелых металлов (Cd, Сu, Zn, Нg, Сr, Pb) и токсичные анионы. Если концентрация металла мала, ионный обмен объединяют с методом осаждения [61].
Аниониты применяют для удаления из сточных вод токсичных анионов, например, цианидов. Регенерация сильноосновного анионита, насыщенного цианид-ионами, производится 5-10% раствором NaOH или NaCl. Десорбция цианидов проходит не полностью (простые цианиды десорбируются на 80 - 90, комплексные на 42- 78%). Достижение большей полноты регенерации требует значительного расхода регенерирующих растворов. Элюаты содержат до 10—15 г/л цианидов и могут быть утилизированы или обезврежены электрохимическим или реагентными методами [62].
Для очистки стоков от анионовсильных кислот применяется технологическая схема одноступенчатого Н-катионирования и ОН-анионирования с применением сильнокислотного катионита, слабоосновного анионита. Для глубокой очистки сточных вод применяется одно- или двухступенчатое Н-катионирование с последующим двухступенчатым ОН-анионированием. Если в стоках много диоксида углерода и его солей, то емкость сильноосновного анионита быстро истощается. Для уменьшения истощения стоки после катионитового фильтра дегазируют в специальных приборах.
Ионообменная очистка воды может осуществляться в аппаратах с плотным и псевдоожиженным слоем, пульсационных колоннах и т. д. Наибольшее распространение в практике получили ионообменные фильтры с плотным слоем, которые отличаются относительно простой конструкцией и надежность и отработанного технологического процесса.
|
Ионообменные смолы регенерируют, с помощью насыщенных растворов.
Коагуляция/флокуляция
Необходимым этапом подготовки шлама к фильтрации или центрифугированию (а также флотации и седиментации) является его смешивание с коагулянтами и флокулянтами. Такая обработка приводит к изменению структуры твердой фазы осадка и увеличивает водоотдачу.
Коагуляция Коагуляция - это первый этап удаления коллоидных частиц. Ее суть состоит в дестабилизации коллоидов, главным образом, путем нейтрализации поверхностного электрического заряда, следствием чего является слипание частиц. Известны два основных типа коагулянтов – минеральные и органические.
Минеральные коагулянты – обычно гидролизуемые соли железа (FeCl3, Fe(SO4)2) или алюминия (Al2(SO4)3, квасцы). С целью интенсификации процесса в последнее время начинают использовать модифицированные (предгидролизованные) коагулянты, например, полиоксихлорид алюминия (ОХА или по международной номенклатуре непатентованное название РАС) и композиционные коагулянты, представляющие собой смеси солей алюминия, железа, кальция, титана. Коагулянты нового поколения устраняют проблему снижения щелочности шлама и выделения в качестве побочного продукта СО2. Главными достоинствами минеральных коагулянтов являются универсальность их применения и низкая стоимость.
Коагуляция соединениями алюминия и кальция является одним из методов удаления фосфатов. При этом протекают следующие реакции:
Аl(ОН)3 + РО43- + 3Н+ + 4NаОН = NаАlО2 + Nа3РО4 + 5Н2О,
2Na3PO4 + 3СаСl2 = Са3(РО4)2 + 6NaCl
Выпадающий фосфат кальция удаляют фильтрованием.
Органические коагулянты - длинноцепочечные полимеры с положительно заряженными функциональными группами (обычно четвертичным аммонием). Сейчас на рынке представлены четыре основных семейства органических коагулянтов: полиамины, полидадмак (полидиаллилдиметиламмония хлорид), дициандиамидные смолы, меламиноформальдегидные смолы. Основными преимуществами таких коагулянтов являются небольшие дозы и небольшой объем образующегося ила (нет гидроокиси). Кроме того, эти коагулянты не влияют на рН осадка.
На практике часто используются смеси из минеральных и органических коагулянтов, которые позволяют объединить преимущества как органических, так и минеральных коагулянтов. В таких смесях в качестве минерального коагулянта чаще всего используется РАС [63, 64].
В настоящее время полимеры применяются как основные коагулянты, полностью или частично заменяя неорганические. Полимерные коагулянты оказались более экономичными в широком диапазоне процессов, включая осаждение, флотацию и фильтрацию. Для данных процессов полимерные коагулянты доказали свою способность стабильно обеспечивать качество очищенной воды, соответствующее установленным стандартам, при оптимальной надежности, эффективности и экономичности [63].
Флокуляция Флокуляция– следующий за коагуляцией этап образования агрегатов из дестабилизированных коллоидных частиц. Флокулянты с их зарядом и очень высоким молекулярным весом фиксируют дестабилизированные частицы за счет ионных и водородных связей вдоль полимерной цепи. В результате происходит увеличение размера частиц, находящихся в водной фазе образуются хлопья.
Флокулянты разделяют на катионные, анионные и неионные. Наиболее часто используются полиакриламиды (Мr ~105-106). Их выпускают в виде геля с содержанием полимера от 7 до 11% или гранул, например, отечественные препараты ПАА-1 и ПАА-ГС соответственно. Применяют также полиоксиэтилен, полиакрилат, полиэтиленимин и др., а также флокулянты на основе природных веществ (крахмал, эфиры целлюлозы, гуаровые смолы, хитозан и др.) [63-65].
Оптимальный выбор коагулянта/флокулянта для конкретной системы возможен только на основе результатов лабораторного анализа и испытаний и основан больше на эмпирическом, чем на теоретическом подходе.
Для обработки стоков, содержащих сульфатный лигнин, российскими учеными разработан новый композиционный коагулянт на основе титанилсульфата и сульфата алюминия. Обычно для осаждения сульфатного лигнина применяется сульфат алюминия, но его эффективность недостаточно высока (<80%). Коагулянты на основе солей Ti (IV) обладают значительно более высокой коагулирующей способностью, однако диапазон рН их эффективного действия достаточно узкий (рН 2 – 4). Применение смешанного коагулянта на основе титанилсульфата и сульфата алюминия значительно расширяет диапазон рН (рН 2 – 8), в котором может быть получено эффективное (до 90%) выделение сульфатного лигнина из его водных растворов [66].
Запатентован метод удаления сульфатного лигнина из сточных вод от отбелки целлюлозы, основанный на добавлении в сточные воды (рН 4,5-7) соединений кальция (оксид, гидроксид или неорганические соли) с последующим осаждением лигнина соединениями алюминия (сульфат, полимерный гидроксид, формиат) [67].
В работе [68] сообщается, что обработка черного щелока с помощью СaSO4*2H2O в присутствии СО2 приводит к 63%-ному удалению суспендированных твердых веществ.
Существует мнение, что полиэлектролиты лучше осветляют сточные воды целлюлозно-бумажных производств, чем неорганические коагулянты [69].
Авторами [70, 71] проведено сравнительное изучение ряда традиционных коагулянтов, таких как Al2(SO4)3, гексаметилен-диамин-эпихлорогидрин-поликонденсат (НЕ), полиэтиленимин (РЕI), и природного аминополисахарида хитозана с иммобилизованной на нем пероксидазой. Наиболее эффективным реагентом для снижения ТОС, АОХ и цветности сточных вод оказался модифицированный хитозан.
Запатентована разработка ученых Иркутского ГТУ, в которой предложен метод обработки шлам-лигнина флокулянтом, и гидрофобизатором. Метод отличается тем, что в качестве гидрофобизатора используют аммониевую соль октилбетатиопропионовой кислоты. Такой гидрофобизатор, содержащий в своем составе длинноцепочечный алкильный радикал C8H17-, с одной стороны будет способствовать улучшению процесса гидрофобизации поверхности частиц осадка, а с другой, благодаря наличию атома S, группы COONH4 лучшей адсорбции реагента на поверхности осадка с образованием прочного гидрофобного слоя. Положительный эффект заключается в увеличении водоотдачи шлама и сокращении времени пребывания осадка на стадии обезвоживания. Это, в свою очередь, позволяет увеличить производительность вакуум-фильтров, фильтр-прессов, флотомашин [72].
Отдельное место занимают методы обезвоживания с использованием полимерных флокулянтов, цель которых - перевод шламовых осадков в твердый плотный материал, который легко поддается погрузке и транспортировке с последующей утилизацией (например, сжиганием).
Запатентованный в РФ метод переработки шламов, содержащих более 80% воды, включает введение в шлам гидрофильного высокомолекулярного полимера с последующим перемешиванием, формованием, например, с помощью грохота и сушкой на воздухе. В качестве полимера используют порошкообразную натриевую соль карбоксиметилцеллюлозы (КМЦ) в количестве 3-15 мас.% от общей массы шлама.
Перевод гидратированной суспензии в твердое состояние происходит за счет растворения полимера во влаге шлама, и интенсивного испарения воды сквозь полимерную сетку. Na-КМЦ способна образовывать гидратные комплексы и за счет этого вытягивать значительное количество воды из внутренних слоев шлама и испарять ее в воздух. В результате получают сухой плотный продукт, состоящий, в основном, из связанных твердых фаз шлама и потерявший до 70-80% в объеме и массе (за счет потери гидратированной влаги и свободной воды) [73].
Флотация
Для улучшения разделения твердой и жидкой фаз может быть использована дополнительная стадия обработки – флотация. Ее цель – выделение из воды взвешенных веществ, а также части веществ, находящихся в коллоидном состоянии.
Метод основан на реализации различной смачиваемости частиц в системах «твердая фаза – жидкость – газ». На практике его осуществляют, либо путем барботажа газа через суспензию, либо насыщения жидкости газом под давлением, с последующим его сбросом. В том и в другом случае реализуется принцип всплывания твердых частиц под действием выталкивающей силы прикрепленных к ним пузырьков воздуха. Этот метод намного эффективнее и производительнее метода седиментации. Обычно продолжительность флотации составляет 3 – 10 минут, отстаивания – 90 – 360 мин [74].
Выбор конкретного способа флотации определяют специфические требования. Наиболее эффективным и распространенным является метод напорной флотации, основанный на растворении воздуха в воде при повышении давления до 5 – 6 атмосфер и образовании огромного количества мельчайших пузырьков при сбросе давления до атмосферного. Во многих случаях гораздо более рационально вместо огромных и неэффективных отстойников использовать компактные флотаторы. Флотационная обработка высококонцентрированных сточных вод позволяет до 70 -80 % снизить показатели ХПК и БПК [74].
В настоящее время на российских целлюлозно-бумажных предприятиях действует большое количество различных типов флотаторов. Наиболее распространены напорные флотаторы конструкции В.А.Копылова, установленные еще в 1970–1980 гг., но до сих пор не потерявшие своей актуальности.
Среди компаний, поставляющих на рынок флотаторы собственных конструкций, можно назвать такие фирмы как «Metso» (Финляндия) - флотаторы «Raisio» [75], «KWI inc.»(Австрия) [76] и др. Компания «KWI inc.» занимает значительную часть рынка флотационной техники. Специально для целлюлозно-бумажной промышленности разработана установка Megacell, сочетающая достоинства флотаторов Supercell и полочных отстойников. Скорость флотации при заметном улучшении качества очистки увеличена в этих установках за счет применения U-образных наклонных ламелей. Установка является новейшей разработкой компании, и проектировалась специально в качестве установки локальной очистки оборотных вод макулатурных производств. Однако она хорошо зарекомендовала себя и на других технологических линиях. Установка имеет два исполнения – горизонтальное и вертикальное. В вертикальных установках возможно получение флотшлама концентрацией до 100 г/л [77]. Исключительную эффективность показали установки напорной флотации KWI SediDAF. Данные установки предназначены для быстрого сгущения (продолжительность пребывания в установке 20 минут) активного ила до концентрации 60 – 90 г/л. Монтаж этих установок параллельно с существующими вторичными отстойниками позволяет получить «живой» активный ил с высокой концентрацией, тем самым существенно увеличить окислительную мощность аэротенков. При этом в качестве основного корпуса флотатора могут быть использованы существующие отстойники или илоуплотнители, что существенно снижает капитальные затраты [77].
Рис.2.5. Технологическая схема флотационного уплотнения шлама [78]:
1-центробежный насос; 2- инжектор; 3- напорный; 4- флотатор; 5- регулятор уровня жидкости; 6- аэратор; 7- транспортер; 8- бункер для осадка; 9- шнековый дозатор флокулянта; 10- растворный бак; 11- плунжерный насос
Метод флотационной обработки может быть включен в схему поэтапной рекуперации осадка карт-накопителей БЦБК и использован для извлечения как мелко, так и грубодисперсных примесей из надшламовых вод.
В Иркутском ГТУ предложен модернизированный вариант технологии тонкослойной напорной флотации, учитывающий конкретные особенности фильтрационных характеристик шлам-лигнина [78]. Установлено, что время полного осветления надшламовых вод меньше при одновременном проведении пенной и напорной флотации. Выбраны оптимальные технологические параметры и даны практические рекомендации по внедрению наиболее эффективных реагентных режимов для обработки осадка карт шламонакопителей в процессе обезвоживания. Сточные воды, образующиеся после флотационного уплотнения и обезвоживания флото-шлама, и содержащие, в основном, легко окисляемую органику и остаточные химические реагенты, направляются на очистные сооружения комбината [78]. Предлагаемая технологическая схема флотационного уплотнения шлам-лигнина показана на рис. 2.5. Основные технологические процессы предлагаемого метода прошли успешные промышленные испытания.
Электроосмос
Электроосмос – одна из относительно новых мембранных технологий очистки сточных вод и обезвоживания осадков. В основе метода лежат явления электрофореза (направленное движение заряженных частиц коллоидных систем в жидкой среде под действием внешнего электрического поля) и электроосмоса (движение влаги через капилляры или поры под влиянием постоянного электрического тока в сторону падения электрического потенциала).
Процесс электроосмотического обезвоживания проходит несколько характерных этапов, показанных на рис. 2.6: 1 – отрицательно заряженные частицы осадков передвигаются к аноду; 2 – вода, выделенная электроосмосом, фильтруется через сетку со стороны катода; 3 – связанная вода осадков перемещается к катоду под действием капиллярного давления;4 – разрушение клеточных мембран осадков позволяет выпустить связанную воду. При проведении процесса электроосмотического обезвоживания температура осадка повышается до 60–80оС, в результате чего происходит разрушение клеточных оболочек живых организмов и, как следствие, обеззараживание осадка [79].
Рис. 2.6. Схема электроосмотического обезвоживания [79].
С помощью электроосмоса влажность прошедшего предварительно механическое обезвоживание осадка может быть снижена еще на 25–35% без применения реагентов, т.е. до величины 50-45%, достаточной для последующей термической утилизации шлама [79].
Серийный выпуск оборудования для непрерывного электроосмотического обезвоживания осадков сточных вод ELODE® (Electro Osmosis Dehydrator) первой в мире освоила южнокорейская компания Samwoo Intech Co. Ltd. (2004 г.) [80]. В настоящее время имеется положительный опыт эксплуатации целого ряда установок ELODE® в различных отраслях промышленности в Южной Корее и Японии. Принципиальная схема установки ELODE® приведена на рис. 2.7.
Рис. 2.7. Схема установки электроосмотического обезвоживания ELODE® [79]:
1 – подача исходного осадка на транспортер; 2 – анод (барабан); 3 – промывка ленты; 4 – отвод фильтрата и промывных вод; 5 – катод («гусеница»); 6 – фильтровальная лента с дополнительно обезвоженным осадком.
Основными элементами установок ELODE® являются анод (барабан) и катод (гусеничного типа). Исходный, предварительно обезвоженный осадок направляется транспортером на фильтровальную ткань между анодом и катодом. На электроды подается регулируемое напряжение, что позволяет подобрать режим обработки, наиболее подходящий для данного типа осадка. В межэлектродном пространстве осадок разогревается до температуры 60–80 оС. Испарения от установки отводятся через воздухозаборный зонт и направляются на очистку. Фильтрат собирается в поддон и отводится от установки. Обезвоженный осадок снимается с сетки скребком и поступает на транспортер. Сетка промывается водой, подаваемой насосом высокого давления через форсунки. Процесс электроосмотического обезвоживания происходит непрерывно и регулируется с помощью автоматической системы.
Установки ELODE® имеют ширину полотна от 500 до 3000 мм. Для осадков с исходной влажностью не более 80% (в зависимости от структуры и свойств осадка) удельная производительность установок составляет до 0,4 т/ч по сухому веществу на один метр ширины полотна. Удельные затраты электроэнергии составляют 250–300 кВт·ч/т по сухому веществу, или 180 кВт·ч/т удаляемой влаги. По сравнению с методом термической сушки осадка энергетические затраты при электроосмотическом обезвоживании ниже в 5–6 раз.
Установки ELODE® производятся в двух основных вариантах: отдельное устройство, размещаемое после оборудования механического обезвоживания (ленточных фильтр-прессов, вакуум-фильтров,центрифуг и т. п.); или модуль ленточного фильтр-пресса. Установки ELODE® сертифицированы в Евросоюзе и Российской Федерации [80].
Следует отметить, что работы по изучению этого метода проводились в конце прошлого века ведущими научно-техническими центрами СССР. Были разработаны и испытаны пилотные установки, в том числе и для обработки осадков целлюлозно-бумажного производства. Так, например, еще в 1982 г Иркутским институтом органической химии Сибирского отделения АН СССР внедрена опытная установка непрерывного обезвоживания шлам-лигнина.[81].
|
|
Адаптации растений и животных к жизни в горах: Большое значение для жизни организмов в горах имеют степень расчленения, крутизна и экспозиционные различия склонов...
История создания датчика движения: Первый прибор для обнаружения движения был изобретен немецким физиком Генрихом Герцем...
Поперечные профили набережных и береговой полосы: На городских территориях берегоукрепление проектируют с учетом технических и экономических требований, но особое значение придают эстетическим...
Механическое удерживание земляных масс: Механическое удерживание земляных масс на склоне обеспечивают контрфорсными сооружениями различных конструкций...
© cyberpedia.su 2017-2024 - Не является автором материалов. Исключительное право сохранено за автором текста.
Если вы не хотите, чтобы данный материал был у нас на сайте, перейдите по ссылке: Нарушение авторских прав. Мы поможем в написании вашей работы!