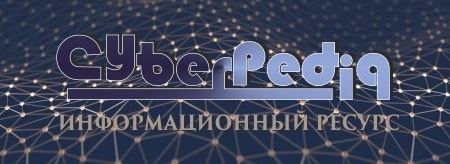
Механическое удерживание земляных масс: Механическое удерживание земляных масс на склоне обеспечивают контрфорсными сооружениями различных конструкций...
Кормораздатчик мобильный электрифицированный: схема и процесс работы устройства...
Топ:
Проблема типологии научных революций: Глобальные научные революции и типы научной рациональности...
Когда производится ограждение поезда, остановившегося на перегоне: Во всех случаях немедленно должно быть ограждено место препятствия для движения поездов на смежном пути двухпутного...
Оценка эффективности инструментов коммуникационной политики: Внешние коммуникации - обмен информацией между организацией и её внешней средой...
Интересное:
Наиболее распространенные виды рака: Раковая опухоль — это самостоятельное новообразование, которое может возникнуть и от повышенного давления...
Влияние предпринимательской среды на эффективное функционирование предприятия: Предпринимательская среда – это совокупность внешних и внутренних факторов, оказывающих влияние на функционирование фирмы...
Аура как энергетическое поле: многослойную ауру человека можно представить себе подобным...
Дисциплины:
![]() |
![]() |
5.00
из
|
Заказать работу |
|
|
25. Переработка мусора. «Безотходная философия Японии». https://flb.ru/7/2032.html?rb_clickid=30732039-1526892254-551219349&utm_campaign=10146277&utm_content=30732039&utm_medium=cpc&utm_source=targetmailru&utm_term=gen_f.age_43
26. Статистический бюллетень «Основные показатели охраны окружающей среды 2017 г. «Национальный доклад о кадастре антропогенных выбросов из источников и абсорбции поглотителями парниковых газов, не регулируемых Монреальским протоколом, за 1990–2015 годы», стр. 23, Росстат.
27. Экология и экономика: сокращение загрязнения атмосферы страны. Бюллетень о текущих тенденциях российской экономики. вып.28. август 2017.
28. http://tass.ru/plus-one/4809920
29.http://bookbk.net/book/119-bezopasnost-avtotransportnyx-sredstv-lomakin-v-v/42-31-vrednye-vybrosy-avtotransporta-v-atmosferu.html
30. Константинов, А. П. Экология и здоровье: опасности мифические и реальные. Экология и жизнь. 2012. № 12. С. 86.
31. https://www.syl.ru/article/288869/new_parnikovyiy-gaz-istochniki-vyibrosov-parnikovyih-gazov
32. bp statistical review of world energy 2018. https://go.mail.ru/search?q=bp+statistical+review+of+world+energy+2018+
33. План по снижению сбросов загрязняющих веществ с 2019 года. https://normativ.org/lib/ekologiya/plan-po-snizheniyu-sbrosov-zagryaznyayushhih-veshhestv-s-2019-goda-normativyi-sostava-stochnyih-vod/
34. Загрязнение и охрана окружающей среды: понятия и пути решения проблемы. http://medsu/ru.
ГЛАВА 2
МЕТОДЫ ОЧИСТКИ СТОЧНЫХ ВОД И ШЛАМОВ
ФИЗИЧЕСКИЕ МЕТОДЫ
Как правило, на первой ступени очистки жидких токсичных отходов используют гравитационные методы для удаления крупных примесей, «забивающих» аппараты и оборудование, применяемые на следующих стадиях.
Шламы после очистки сточных вод содержат огромное количество воды (более 90%), которая вызывает проблемы в их переработке. Обезвоживание представляет собой один из наиболее важных процессов, направленных на сокращение объема и облегчение утилизации шламов.
|
Обычно используемыми методами обезвоживания осадков являются механические (фильтрация, центрифугирование), термические (сушка), физико-химические (электроосмос, обратный осмос, флотация). Практически в любой технологии обезвоживания существует предварительная стадия разделения жидкой и твердой фаз с помощью коагулянтов и флокулянтов. Выбор того или иного способа обезвоживания зависит от свойств обрабатываемой суспензии, требуемой остаточной влажности осадка и чистоты фильтрата, а также возможностей и предпочтений предприятия.
Методы сушки, не считаются подходящими для дегидратации шламов с большим содержанием воды, ввиду неудобства и больших энергетических затрат. Поэтому эти методы рассматриваться не будут. Очевидно, что для обезвоживания шламов, содержащих более 90% воды и представляющих собой коллоидную систему, наиболее подходящими являются технологии фильтрации.
Различные типы оборудования для механического обезвоживания обеспечивают получение осадка с влажностью в среднем 70-80%, в отдельных случаях <60%. Еще на 25-35% снизить содержание воды в шламе можно с помощью некоторых мембранных технологий [1].
Анализ зависимости насыпного объема осадка сточных вод от его массы, плотности и влажности показывает, что только снижение влажности с 75 до 50% приводит к сокращению объема утилизируемого осадка в 2 раза. Дальнейшее снижение содержания воды механическими методами уже не приводит к существенному уменьшению объема. Таким образом, влажность в пределах 50% является оптимальной для минимизации объема осадка и энергетических затрат. Кроме того, такая степень обезвоживания считается достаточной для последующей термической утилизации шлама. Более глубокая дегидратация осадка (влажность< 40%) возможна только с использованием термических методов [1].
В течение многих лет в практике механического обезвоживания осадков доминируют несколько вариантов оборудования. Большинство установок, построенных в начале 1970-х годов, были громоздкими вакуум-фильтрами, которые затем уступили место центрифугам и ленточным фильтр-прессам раннего поколения. На протяжении большей части 1980-х и 1990-х годов ленточные фильтр-прессы были наиболее распространенными системами обезвоживания. За последние несколько лет произошли многочисленные усовершенствования и инновации в оборудовании обезвоживания осадков.
|
Центрифугирование
Центрифугирование используется для обезвоживания осадков на протяжении многих лет, и новое поколение оборудования значительно превосходит ранние модели. Центрифуги, обычно работающие в режиме 3000 оборотов в минуту, требуют регулярных мероприятий по техническому обслуживанию. Несмотря на это, такие системы являются чрезвычайно гибкими в отношении качества шлама, надежными и легкими в управлении. Кроме того они являются автономными системами, что облегчает контроль запаха.
Есть несколько крупных производителей оборудования для центрифугирования. В частности, компания Wright Pierce [2] недавно разработала ряд новых центрифуг различной производительности, предназначенных для обработки отходов как крупных, так и относительно мелких производств.
Фильтрация
Современные технологии обезвоживания шламов сточных вод - фильтрование под вакуумом - предлагают вакуум-фильтры дискового и барабанного типов нового поколения, а также устройства на основе оригинального конструктивного решения метода - мешочные вакуум-фильтры.
Фильтры
Дисковые вакуум-фильтры. Дисковый вакуум-фильтр состоит из отдельных дисков, покрытых фильтровальным материалом. Каждый диск имеет несколько секторов, сообщающихся с полым валом, на который насажены диски; внутри последних при помощи вакуум-насосов создается разрежение. Вращаясь, диски погружаются в шлам, из которого через фильтрующую ткань отсасывается вода, отводимая затем через полый вал фильтра. Частично обезвоженный шлам налипает на поверхность фильтрующей ткани и отпадает на нее, когда разрежение периодически сменяется небольшим давлением.
Mеждународный концерн «Andritz AG» (Финляндия), один из ведущих разработчиков и изготовителей систем обезвоживания и фильтрации [3], предлагает вакуумные дисковые фильтры типа VF. Полезный перепад давления до 0,75 бар в фильтрах этого типа позволяет наиболее эффективно извлекать жидкость из суспензий.
|
Вакуумные фильтры фирмы Andritz имеют ряд конструктивных особенностей: фильтровальные диски с 20 сегментами на каждом, ванна фильтра с большой глубиной погружения дисков до 45 %;; эффективная система сброса кека резким толчком (snap-blow) и др.
Барабанные вакуум-фильтры. Барабанный вакуум-фильтр по принципу действия не отличается от дискового, однако имеет меньшую производительность из-за меньшей при равных диаметрах фильтрующей поверхности барабана.
Мешочные вакуум фильтры. Новое конструктивное решение метода вакуумной фильтрации осуществлено в установках с мешочным вакуум-фильтром. Эта технология обезвоживания шламов сточных вод отличается простотой и универсальностью использования, низкими капитальными и эксплуатационными затратами.
Примером может служить разработка Российской компании ЗАО «Баромембранная Технология», организованной на базе Владимирского ОАО «Полимерсинтез»[4].
Предлагаемая установка наиболее удобна для обработки небольших объёмов осадков – до 2 м3/сут., с концентрацией твёрдого вещества 0,5–2%. Оборудование работает в периодическом режиме, диапазон отделяемых частиц от 200 до 3 мкм. Хотя разность давлений на фильтрующей перегородке не превышает 90 кПа, установка способна работать, в том числе, и с непрерывной подачей исходной смеси, последующим концентрированием и отжимом осадка. В течение 2-часового рабочего цикла установка позволяет получить осадок влажностью 65–80%. Удельная производительность зависит от свойств осадка и составляет до 30 л/м2.ч.
Фильтр-элемент из синтетической ткани, характеризуется низкой адгезией. К основным достоинствам установки можно отнести: большую удельную поверхность фильтрования (до 12 м2); относительно низкий износ тканевого фильтр-элемента, возможность его многократной регенерации и лёгкой замены; возможность исключения из системы ресивера между насосом и фильтром (как это принято в установках с нутч-фильтром), так как удалённая жидкость поступает непосредственно в циркуляционный контур насоса; простоту эксплуатации и широкий диапазон использования; сравнительно низкую стоимость по сравнению с аппаратами, выполняющими аналогичные функции.
|
Положительные результаты опытно-промышленных испытаний установок с мешочным вакуум-фильтром позволили разработать технологические решения процесса механического обезвоживания осадков в составе очистных комплексов, проектируемых и выпускаемых ЗАО «БМТ».
Гравитационные фильтры. Еще одна из инновационных технологий последних лет - дегидратация осадков методом статического обезвоживания с применением так называемых "геотруб".. Ее предлагают, в частности, компания Geotech® (Германия) [5].
Технологическая схема изображена на рис. 2.1. Суть технологии состоит в том, что осадки любого вида перекачиваются в огромный текстильный мешок SoilTain® фирмы Huesker из специального материала Geolon®, произведенного из нитей полипропилена высокой плотности, соединенных в прочную ткань с устойчивым положением нитей относительно друг друга. Материал имеет уникальную тонкую структуру пор, обеспечивающую удержание шламовых частиц малого размера и отвод воды. Жидкость удаляется методом гравиметрического дренажа и давления, что приводит к обезвоживанию осадка и соответствующему уменьшению его объема. Процесс обезвоживания повторяется до тех пор, пока мешок не будет полностью заполнен обезвоженным шламом. По окончании процесса оставшаяся внутри мешка обезвоженная масса может быть утилизирована, либо рекультивирована с использованием существующих технологий.
Эффективность обезвоживания может быть существенно повышена с использованием полимеров-флокулянтов. Технология может применяться для обезвоживания осадка сточных вод как муниципальных, так и промышленных предприятий, когда требуется разделение твердых и жидких фракций в больших объемах.
Рис.2.1. Технологическая схема статического обезвоживания [5].
Мобильный технологический комплекс по обезвоживанию сырого осадка сточных вод на базе установки EcoTrain® состоит из 4 модулей: подачи осадка; приготовления и подачи растворов флокулянтов; смешивания осадка с раствором флокулянта; дозирования вспомогательных веществ (дезинфектант, дезодорат, реагент для удаления тяжелых металлов, стабилизатор) и управления.
Важным элементом предлагаемого оборудования является патентованная система TWIN MIX® смешивания осадка с раствором флокулянта, осуществляющая кавитационную гомогенизацию осадка с последующим высокоэффективным контактным взаимодействием с раствором флокулянта. Это дает возможность значительной экономии флокулянта и позволяет добиться высокой степени обезвоживания осадка.
Мобильный комплекс может быть снабжен автономным питанием и использоваться на удаленных территориях. В настоящее время выпускаются технологические линии производительностью до 200 м3 осадка/час.
|
Преимуществом такой технологии является отсутствие капитального строительства; непрерывный технологический процесс; получение фильтрата, соответствующего требованиям сброса на очистные сооружения; низкая энергоёмкость; низкие эксплуатационные затраты. Данная технология в настоящее время реализуется на ряде российских полигонов.
Гипербар-фильтры. Фильтрацию под давлением впервые начали применять только с середины 80-х годов XX века. Это метод фильтрации, при котором дисковый фильтр устанавливается внутри напорного резервуара. Данная система улучшает процесс фильтрации за счет использования большей разницы давления по всей поверхности фильтруемого материала. Концерн Andritz [3] выпускает напорные фильтры типа HBF (гипербарфильтры), позволяющие при давлении фильтрации до 6 бар обезвоживать большие объемы мелкодисперсных суспензий с высоким сопротивлением фильтрации, получая минимальную остаточную влажность (15-18%). Самая высокая удельная производительность этих фильтров позволяет максимально сократить требуемую площадь фильтрации. К преимуществам напорных фильтров Andritz следует также отнестинебольшую площадь размещения и полностью автоматизированный режим эксплуатации установки.
Мембранные фильтры. Технологии мембранной фильтрации появились около 50 лет назад. Они основаны на использование в качестве фильтра различных полимерных (ацетатцеллюлозы, полисульфон, полиэфирсульфон, полиамид и др.) и неорганических керамических пористых материалов, обладающих свойством селективной проницаемости к компонентам растворов. Мембранные технологии дают возможность проводить хорошее разделение фаз и контролировать размер фильтруемых частиц, осуществлять концентрирование и извлечение из сточных вод ценных растворенных веществ. Однако такие недостатки как высокая стоимость, быстрая загрязняемость фильтров и небольшая мощность в прошлом делали эти методы не привлекательными и позволяли использовать лишь в малозагрязненных (например, простая вода), или в дорогостоящих средах (например, фармацевтическая индустрия). В настоящее время процесс усовершенствован и широко используется.
VSEP –технология (vibratory shear enhanced processing или вибрационные мембранные фильтры). Опираясь на достоинства мембранных технологий, американская компания New Logic Research [6] в 1987 г. изобрела, так называемую VSEP-систему («Vibratory Shear Enhanced Process» –вибрационный поперечный улучшенный процесс). В настоящее время это единственная технология, предлагающая высокую фильтрующую мощность для обработки самых загрязненных систем, в том числе промышленных шламов.
Принцип VSEP –технологии показан на рис. 2.2. Для минимизации наслоений на поверхности фильтра, используется метод, названный «перекрёстно - напорной фильтрацией». Он основан на проходе жидкости под высоким напором вдоль поверхности мембраны. Мембраны находятся в трубчатом или спиральном резервуаре, через который непрерывно подается жидкость для фильтрации. Колебательные вибрации создают высокие скорости сдвига на поверхности мембранного фильтра, что предотвращает загрязнение и износ мембраны, делая возможной фильтрование даже частиц высокой твёрдости.
2 |
1 |
Рис.2.2. Принцип VSEP-технологии: вибрационный сдвиг(1) и поперечный поток (2) [6].
Технология позволяет увеличить скорость фильтрации в 10 раз. Не происходит потери продукта (по сравнению с центрифугой или прессом), к системе не нужно добавлять реагенты-хлопьеобразователи, не требуется больших затрат энергии. Кроме того VSEP ситемы компактны. На сегодняшний день VSEP-технология широко используется во всем мире [6].
Фильтр-прессы
Камерные фильтр-прессы. Камерный фильтр-пресс представляет собой набор фильтровальных плит, размещенный между передней стойкой фильтр-пресса и его нажимной плитой. Механизм зажима плит монтируется в задней стойке фильтр-пресса. Как правило, фильтр-прессы оснащаются гидроцилиндром для создания рабочего усилия сжатия плит, но в некоторых случаях возможно использование электромеханического зажима плит. В зависимости от типа крепления плит различают фильтр-прессы с верхней и боковой подвеской. В зависимости от свойств отфильтрованного осадка возможны различные варианты выполнения механизма выгрузки отфильтрованного осадка. Разделяемая суспензия поступает внутрь сжатого пакета плит по коллектору. После заполнения камер фильтрования, за счет возникающего в них избыточного давления, жидкая фаза проходит через фильтрующие перегородки и отводится за пределы фильтр-пресса. Твердая фаза задерживается на фильтрующей перегородке в виде осадка. Стандартный материал для камерных плит – полипропилен. Возможное рабочее давление: 6, 15 и 30 бар.
Мембранные фильтр-прессы. Процесс «заполнения и фильтрации» для мембранных фильтр-прессов такой же, как для камерных фильтр-прессов. После достижения определенного давления, как правило, 4˗10 бар, в зависимости от характеристик шлама, подача шлама прекращается, и мембрана медленно расширяется, используя либо воду, либо воздух для сжатия. Кек тем самым сжимается и еще больше обезвоживается. Этот процесс продолжается, пока поток фильтрата не достигнет установленного минимального предела. Потом среда сжатия отводится и производится разгрузка кека. Материалы для мембран включают полипропилен или синтетический каучук (например, акринитрилбутадиеновый каучук, этилен-пропилен-диен-метиленовый каучук или TPE термопластический эластомер) [3].
Вследствие множественных запросов для промышленного и коммунального применения, фирмы-изготовители производят модульные конструкции фильтр-прессов. В дополнение к базовому оборудованию, возможно добавление различных модульных компонентов. Такие фильтр-прессы могут быть интегрированы в различные технологические процессы [3, 7].
Камерные фильтр-прессы используются на ряде предприятий для обезвоживания шлам-лигнина в процессе его подготовки к сжиганию. С их помощью влажность шлама можно понизить до 52 - 56%. Подходящим оборудованием являются, например, автоматические фильтр-прессы башенного типа ФПАКМ. [8]. Они предназначены для разделения на жидкую и твердую фазы суспензий, содержащих от 10 до 1500 кг/м3 взвешенных частиц и образующих осадки с большим гидравлическим сопротивлением. В зависимости от особенностей конструкции установлены различные типоразмеры по величине площади поверхности фильтрования: от 2,5 до 25 м2. Данный ряд содержит фильтры, предназначенные как для работы с трудно-фильтруемыми суспензиями, в которых размер частиц не должен превышать 3 мм, так и для легко фильтруемых сред с размером частиц до 8 мм. Тип материала деталей, соприкасающихся с обрабатываемой средой, варьируется в зависимости от агрессивности среды. Система автоматики выполнена на базе программируемого контролера.
Ленточные фильтр-прессы. Для дегидратации трудно обезвоживаемых щламов, используют ленточные пресс-фильтры непрерывного действия. Благодаря своей модульной конструкции, эти устройства обеспечивают оптимальную длительность фильтрации и постепенное возрастание давления отжима, позволяя достигать максимальной степени отделения жидкой фазы из шлама.
Рис. 2.3. Технологическая схема обезвоживания с применением ленточного пресс-фильтра [3].
Технологическая схема обезвоживания с применением ленточного пресс-фильтра приведена на рис. 2.3.
Обработанный раствором флокулянта осадок поступает в зону предварительного сгущения на ленте фильтр-пресса. Там происходит гравитационное сгущение. Затем осадок зажимается между двумя перфорированными лентами и проходит через несколько (8-14) валов уменьшающегося диаметра, что обеспечивает постепенное повышение давления на осадок. Обезвоженный осадок с помощью скребка снимается с ленты и сбрасывается в устройство выгрузки. Фильтрат собирается в нижней части пресса в специальный лоток. Для промывки лент предусмотрены линии промывки, которые с помощью форсунок непрерывно очищают ленты перед поступлением новой порции осадка.
Производительность и качественные показатели работы линии зависят от физических свойств шлама, типа применяемого флокулянта, сита. Предлагаемый способ позволяет прессовать неоднородный шлам с низким исходным содержанием сухого вещества (меньше чем 1 %). Пропускная способность таких прессов в среднем составляет 25-100 м3/ч шлама, обезвоживание за один цикл - с 99,2- 95 % (на входе) до 80 % (выходе) влажности, снижение объема осадка более чем на 82% от начального [9].
На разработке ленточных прессов и дополнительных компонентов линий для обработки шлама специализируются фирмы Vanex (Словакия) [10], Huber BS (Германия) [9] и Andritz [3] и многие другие.
Ленточные фильтр-прессы были отраслевым стандартом в течение многих лет и продолжают оставаться подходящей альтернативой для многих технологических схем.
Преимущества фильтр-прессов, по сравнению с другими типами фильтровального оборудования, заключаются в их хорошей адаптации к фильтруемой среде, высокой степени обезвоживания (благодаря удлиненной зоне мощного предварительного обезвоживания), низком энергопотреблении, низком расходе вспомогательных реагентов (коагулянтов, флокулянтов, промывной воды).
Поворотные дисковые фильт-прессы. Поворотный дисковый пресс (Rotary Disc Press - RDP) является относительно новой технологией, внедренной несколько лет назад канадской фирмой Fournier Industries [11]. Технология была видоизменена другими производителями и введена на рынок.
Она использует метод медленного вращения шлама. Принцип работы поворотного дискового пресса состоит в том, что шлам в смеси с флокулянтом подается в прямоугольный канал, расположенный между двумя параллельными дисками из хромированной нержавеющей стали, которые медленно вращаются на одном валу (обычно от 1 до 3 оборотов в минуту). Устройство содержит от 1 до 6 пар дисков. Фильтрат проходит через экраны, шлам продолжает обезвоживаться, перемещаясь в канале. Сила трения медленно движущихся экранов в сочетании с контролируемым ограничением выхода, приводит к получению твердого остатка высокой степени обезвоженности.
Горизонтальные и наклонные винтовые фильтр- прессы. Технологии отжимных винтовых прессов представлены на рынке очистных сооружений в Европе более десяти лет назад компанией Huber [9]. Устройство винтового пресса схематически изображено на рис. 2.4.
Рис.2.4. Технологическая схема обезвоживания с применением винтового пресса. Huber Technology ROTAMAT® RoS 3Q Inclined Screw Press [9]: полимер (1), насос для полимера (2), полимерный порошок (3), кондиционер для полимера (4), частотно-регулируемый насос подачи раствора полимера (5), вода (6), статический смеситель (7), дозирование раствора (8), шлам из резервуара (9), частотно-регулируемый насос подачи шлама (10), смеситель (11), стабилизационный реактор (12), контрольная панель управления (13),скрин-пресс (14), насос возврата фильтрата (15), обезвоженный шлам (16).
Винтовые прессы предназначены для уплотнения, прессования и передачи в накопительную емкость или на транспортер шламов очистных сооружений. Существуют два типа устройств - наклонные (Inclined Screw Press - ISP) и горизонтальные (Horizontal Screw Press – HSP). Как правило, горизонтальные прессы более удобны для больших объемов обрабатываемых шламов.
Приводом транспортного винта (шнека) реверсивный планетарный гидродвигатель осуществляет непрерывную медленную подачу рабочей суспензии в желобе. В шлам добавляется флокулянт, который создает необходимую консистенцию фильтруемой смеси. Секция фильтрования находится в нижней части желоба и представляет собой пластину с отверстиями. Вода проходит через мембрану, а шнек транспортирует продукты фильтрации наверх для последующей утилизации. В верхней части шнека есть зона обезвоживания, где происходит удаление остатка воды. Продвижение шлама сопровождается постепенным повышением давления, что увеличивает скорость фильтрации. Постоянное перемещение шлама предотвращает налипание осадка на фильтр и снижает сопротивление фильтрации. Винтовые прессы позволяют уменьшить объем шламов до сброса их в приемную емкость на 70-75%.
Японская фирма FKC [12] является ведущим производителем отжимных винтовых прессов для использования в целлюлозно-бумажной и других отраслях промышленности, а с недавнего времени, для муниципальных очистных сооружений. Фирма Wright Pierce [2] (CША) в настоящее время разрабатывает новую модель горизонтального винтового пресса для муниципальных очистных сооружений в Нью-Гэмпшир [13]. Винтовые прессы для обезвоживания бытовых и промышленных шламов представлены на Российском рынке [14].
Все перечисленные выше отжимные устройства медленного вращения относятся к новому поколению технологий обезвоживания и отличаются малым расходом флокулянта, низким энергопотреблением, удобной системой модульной сборки.
В заключение, можно привести таблицу 2.1., в которой дана сравнительная оценка различных технологий обезвоживания на примере оборудования нового поколения, производимого фирмой Huber.
Таблица 2.1. Сравнение различных технологий обезвоживания на примере оборудования фирмы Huber [9].
Затраты | Поворотный дисковый пресс | Наклонный винтовой пресс | Ленточный фильтр-пресс | Центрифуга |
Капитальные | 4 | 2 | 1 | 3 |
Ежегодные | 2 | 1 | 3 | 4 |
«Жизненный цикл» | 2 | 1 | 3 | 4 |
* 1 = наилучшая; 4 =наихудшая
ФИЗИКО-ХИМИЧЕСКИЕ МЕТОДЫ
К физико-химическим методам очистки сточных вод относят коагуляцию, флотацию, адсорбцию, ионный обмен, экстракцию, ректификацию, выпаривание, дистилляцию, обратный осмос и ультрафильтрацию, кристаллизацию и др. Эти методы используют для удаления из сточных вод тонкодисперсных взвешенных частиц, растворимых газов, токсичных металлов и их солей, а также токсичных, биохимически неокисляемых органических загрязнений. Выбор конкретного способа определяется свойствами и количеством стоков.
Адсорбция
Адсорбционные технологии в настоящее время широко используются для удаления органических и неорганических загрязнителей из промышленных и бытовых стоков. Адсорбционные технологии основаны на процессе концентрирования растворенного вещества из объема фаз на поверхности твердого адсорбента. Преимущественно их применяют для глубокой очистки сточных вод от растворенных органических веществ после биохимической очистки, а также в локальных установках, если концентрация этих веществ в воде невелика и они биологически не разлагаются или являются сильно токсичными. Верхний предел применения адсорбционных методов составляет 1000 мг/л, нижний - 5 мг/л. Эффективность адсорбционной очистки достигает 80-95% [15].
В качестве сорбентов используют активные угли, синтетические сорбенты и некоторые отходы производства (золу, шлаки, опилки и др.). Минеральные сорбенты - глины, силикагели, алюмогели и гидроксиды металлов для адсорбции различных веществ из сточных вод используют сравнительно редко, так как энергия взаимодействия их с молекулами воды велика.
Коммерческие адсорбенты
Активированные угли. Среди различных адсорбентов наибольшее применение нашел активированный уголь. Его отличает высокое сродство к фенолам, полициклическим соединениям и многим другим органическим поллютантам [16].
Уголь, используемый для очистки сточных вод, должен обладать большой удельной поверхностью (до нескольких тысяч м2/г), и относительно крупными порами (с эффективным радиусом 0,8-5,0 нм), чтобы его поверхность была доступна для органических молекул, быть прочными, быстро смачиваться водой, иметь определенный гранулометрический состав. В процессе очистки используют как мелкозернистые (0,25-0,5 мм) так и высокодисперсные угли (< 40 мкм) [15].
Установлено, что c помощью адсорбции на активированном угле содержание загрязняющих веществ в сточных водах производства беленой целлюлозы (показатель цветности 2300о, ХПК -21,26 мг/л, AOX - -80,2 мг/л) можно снизить на 90% и довести экологические показатели до уровня, соответствующего международным нормам IPPC(Integrаted Pollution Prevention and Control directive) [17].
Эффективность использования активированного угля для очистки стоков сульфатцеллюлозного производства от хлорфенолов до предельно допустимых значений AOX показана в работе [18]. Установлено, что сорбционная емкость углей по фенолам резко уменьшается с повышением рН среды и при рН=9 не превышает 10-15%.
Коммерческие активированные угли помимо величины удельной площади поверхности и распределения пор по размерам отличаются химией поверхности. Выпускаются окисленные угли с высоким содержанием кислородных групп; угли, прошедшие термальную обработку (700-900оС); угли, предобработанные HNO3, H2SO4, NaOH, TiO2 и др; модифицированные полифункциональные многостенные углеродные нанотрубки [16]. Различные виды предобработки направлены на увеличение адсорбционной емкости угля.
В нашей стране широкое распространение получили активированные угли марок АГ-3, СКТ-3, УАФ и др. Разработкой новых активных углей, перспективных для использования в процессах очистки сточных вод, занимаются ученые РХТУ им. Д.И. Менделеева. За последние годы ими предложено около 30 новых образцов: АГ-95-Р, АДБ, АДБ-В, АК-Ф, «Гидросорб-5», «Гидро-сорб-5-Р», КВ-3, КСВ, КСВ-3, КДС-СС, ПДС, ПДС-5, САУ-В, СКГ-3, СКД, ТПА, ТПА-6, УАФ-Р, ФТГ и др. Разработаны технологии использования этих углей применительно к реальным объектам очистки [19].
В последнее время распространение получают дешевые синтетические активированные угли, прекурсорами которых являются возобновляемые растительные материалы. В основном, используются промышленные и сельскохозяйственные отходы: кукурузные початки, багасса, скорлупа орехов, солома, древесные опилки, бумажный шлам, лигнин, а также торф и бурый уголь.. Производство активированного угля включает карбонизацию сырья при температурах до 700°С с последующей газификацией при более высоких температурах в токе газа-окислителя, либо предварительную пропитку кислотами или солями с последующей термообработкой при умеренных температурах 400-600°С) [16].
В работе [20] изучена адсорбция фенолов и хлорзамещенных фенолов на активированном угле, полученном путем пиролиза педварительно пропитанного фосфорной кислотой лигнина, осажденного из черного щелока сульфатного производства. Определены оптимальные условия синтеза адсорбента: соотношение реагентов - 2 г H3PO4/г лигнина и температура активации 430°С. Адсорбент рекомендован к промышленному использованию.
Росссийскими авторами [21,22] проведено сравнительное изучение экономичных углеродных адсорбентов, полученных из бурого угля, смешанных отходов древесины и гидролизного лигнина. Гидролизный лигнин и древесное сырье подвергали пиролизу (500°С) и последующей парогазовой активации (800°С). Полученные углеродные адсорбенты хорошо извлекают из водных растворов неорганические (медь, хром) и органические (фенол, нефтепродукты, муравьиная и уксусная кислоты) примеси и рекомендованы для использования на очистных сооружениях.
Адсорбенты испытаны для очистки концентрированных фенолсодержащих сточных вод химкомбината «Енисей». Для достижения степени очистки 90-95 % расход адсорбентов составил 25-40 кг/м3 и 70-90 кг/м3 при исходной концентрации фенола в стоках 1,07 г/л и 5,64 г/л соответственно. Согласно литературным данным [23], при очистке концентрированных сточных вод экономически оправданный расход адсорбента, полученного из высококачественного древесного сырья, может составлять 90-100 кг/м3.
Одним из известных недостатков адсорбентов, получаемых из бурых углей и древесного сырья, является их низкая механическая прочность (прочность на истирание – 55-68%), поэтому их регенерация нецелесообразна. Отработанные углеродные адсорбенты рекомендовано утилизировать без какого-либо риска нанесения дополнительного экологического ущерба путем сжигания в энергетических установках в качестве облагороженного топлива (теплота сгорания 5800-7200 кКал/кг) [21,22].
Разработан одностадийный способ получения активных углей из лигнина и других видов растительной биомассы, использующий катализаторы низкотемпературного разложения и порообразующие добавки. [24]. Установлено, что дегидратация и углефикация пропитанной катализаторами биомассы протекают в интервале температур 80–350 °С. Таким образом можно получать универсальные угольные сорбенты, обладающие как высоким сорбционным объемом пор, так и ионообменными свойствами. Адсорбент перспективен для очистки газовых выбросов, сточных вод и технических жидкостей.
Цеолиты. В последнее время особое внимание привлекают дешевые доступные природные алюмосиликатные адсорбенты, такие как цеолиты. Они отличаются большой удельной поверхностью, способностью к ионному обмену, возможностью химического модифицирования поверхности, простотой регенерации, очень низкой ценой. Крупные месторождения природных цеолитов и минеральных глин имеются во многих странах, в том числе в России. Из более чем 40 видов природных цеолитов только семь типов (морденит, клиноптилолит, шабазит, эрионит, ферриерит, филлипсит, и анальцим) существуют в достаточном количестве.
В работах [25,26] проведено сравнительное изучение различных природных цеолитов и активированного угля в процессах удаления фенолов из водной среды и показаны хорошие адсорбционные характеристики цеолитов. Использование в качестве адсорбентов натролита и клиноптилолита дает возможность за короткое время (менее 4 ч) снизить содержание фенольных загрязняющих веществ на 50 - 60% [26].
Высокую эффективность для очистки стоков от ионизированных поллютантов, в том числе замещенных ароматических соединений и фенолов, показали природные цеолиты, модифицированные поверхностно-активными веществами, например бромидом гексадецилтриметиламмония – HDTMAB. Все изотермы адсорбции фенолов оказались линейными и могли быть описаны с помощью коэффициента распределения KН. [27].
Модификация цеолитов циклодекстринами (ЦД), особенно-α-ЦД, также значительно улучшает их адсорбционные свойства. Для модифицированного циклодекстрином клиноптилолита адсорбционная емкость по фенолу и 4-СР возрастает соответственно на 65 и 74% [28].
Полимерные смолы. Широко используются адсорбенты на основе синтетических смол. Компания Purolite International Limited, в сотрудничестве с российскими производителями, разработала серию суперсетчатых полимерных сорбентов для промышленного применения. Большие различия в площади поверхности, пористости и содержании функциональных групп дают возможности их использования для селективного удаления конкретных органических веществ. Установлено, что связывание фенолов на полимерных сорбентах осуществляется двумя способами - путем ионного обмена и молекулярной адсорбции. Так адсорбция фенола на образце Амберлита IRA-420 предпочтительна из кислых растворов, в щелочных же растворах идет как адсорбция, так и ионный обмен [29,30].
В работе [31] показано, что среди коммерческих адсорбентов фимы Purolite лучшим для дезактивации фенолов в промышленных стоках является Amberlite XAD-4. Фенолы хорошо адсорбируются из растворов с низким значением рН, где они присутствуют в молекулярной форме, в щелочных средах связывание фенолов резко уменьшается. Регенерация адсорбента может быть выполнена с помощью его промывания раствором NaOH.
Показано эффективное удаление из воды хлорпроизводных фенола (2-CP, 3 CP, и 4-CP) с помощью смол фирмы Hypersol-Macronet (MN-100, МН-150, МН-200) [32]. Сополимеры на основе винилпиридина и дивинилбензола также хорошо связывают фенолы и отличаются более высоким адсорбционным потенциалом, чем пористые сополимеры дивинилбензола со стиролом, не содержащие ионообменных групп [33]. Регенерируют неионогенные адсорбенты, промывая их органическими растворителями, например ацетоном или метанолом.
|
|
Индивидуальные очистные сооружения: К классу индивидуальных очистных сооружений относят сооружения, пропускная способность которых...
Историки об Елизавете Петровне: Елизавета попала между двумя встречными культурными течениями, воспитывалась среди новых европейских веяний и преданий...
Семя – орган полового размножения и расселения растений: наружи у семян имеется плотный покров – кожура...
Таксономические единицы (категории) растений: Каждая система классификации состоит из определённых соподчиненных друг другу...
© cyberpedia.su 2017-2024 - Не является автором материалов. Исключительное право сохранено за автором текста.
Если вы не хотите, чтобы данный материал был у нас на сайте, перейдите по ссылке: Нарушение авторских прав. Мы поможем в написании вашей работы!