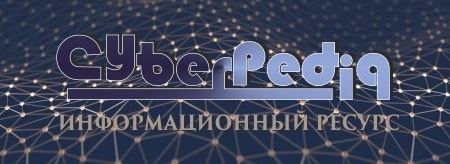
Типы оградительных сооружений в морском порту: По расположению оградительных сооружений в плане различают волноломы, обе оконечности...
Типы сооружений для обработки осадков: Септиками называются сооружения, в которых одновременно происходят осветление сточной жидкости...
Топ:
Организация стока поверхностных вод: Наибольшее количество влаги на земном шаре испаряется с поверхности морей и океанов...
Процедура выполнения команд. Рабочий цикл процессора: Функционирование процессора в основном состоит из повторяющихся рабочих циклов, каждый из которых соответствует...
Основы обеспечения единства измерений: Обеспечение единства измерений - деятельность метрологических служб, направленная на достижение...
Интересное:
Средства для ингаляционного наркоза: Наркоз наступает в результате вдыхания (ингаляции) средств, которое осуществляют или с помощью маски...
Что нужно делать при лейкемии: Прежде всего, необходимо выяснить, не страдаете ли вы каким-либо душевным недугом...
Берегоукрепление оползневых склонов: На прибрежных склонах основной причиной развития оползневых процессов является подмыв водами рек естественных склонов...
Дисциплины:
![]() |
![]() |
5.00
из
|
Заказать работу |
|
|
ОСКОЛЬСКИЙ ПОЛИТЕХНИЧЕСКИЙ КОЛЛЕДЖ
УТВЕРЖДАЮ
ПРЕДСЕДАТЕЛЬ НМС ОПК
________ О.В. Масалытина
Протокол № 01
от «_ 01 _» _ сентября _ 2019 г.
УЧЕБНАЯ ПРАКТИКА
УП.02.01
Методические указания
для студентов очной формы обучения
По выполнению практических работ (заданий)
По специальности: 15.02.14 Оснащение средствами автоматизации технологических процессов и производств (по отраслям)
Квалификация выпускника: Техник
Старый Оскол, 2019 г.
Рассмотрены на заседании П(Ц)К специальности 15.02.14 Протокол № __ 1 _ от __01__ сентября 2019 г. Председатель П(Ц)К _______________ Ю.А. Ушакова | Методические указания составлены в соответствии с рабочей программой по Учебной практике УП.02.01 для специальности среднего профессионального образования 15.02.14 Оснащение средствами автоматизации технологических процессов и производств (по отраслям) |
Составитель:
|
В.В. Горшков, преподаватель ОПК СТИ НИТУ «МИСиС»
СОДЕРЖАНИЕ
Введение ………………………………………………………………...4 Практическое занятие №1
Вводное занятие и инструктаж по охране труда.
Виды слесарных работ. Оснащение…………………………............7
Практическое занятие №2
Разметка заготовок. Плоскостная разметка.
Измерительный инструмент………………………………………...14
Практическое занятие №3
Правка и гибка металла……………………………………………...23
Практическое занятие №4
Рубка и резка металла…………………………………………..........35
Практическое занятие №5
Обработка отверстий - сверление, рассверливание,
зенкерование и развёртывание.……………………………………..49
Практическое занятие №6
Нарезание резьбы – метчиками и плашками………………….........57
Практическое занятие №7
Опиливание металла……………………………………………........69
Практическое занятие №8
Шабрение, доводка, притирка……………………………………….76
Практическое занятие №9
Сборка разъемных соединений
Сборка неразъемных соединений (клепка) ………………………...83
Практическое занятие №10
Основные виды механической обработки - точение,
фрезерование, строгание, шлифование.……………………….........96
Практическое занятие №11
Обработка заготовок на станках с ЧПУ……………………………104
Список использованных источников ……………………………...131
Введение
Учебная практика является частью программы подготовки специалистов среднего звена в соответствии с ФГОС СПО специальности среднего профессионального образования специальности среднего профессионального образования 15.02.14 Оснащение средствами автоматизации технологических процессов и производств (по отраслям).
Учебная практика УП.02.01 является дисциплиной профессионального модуля ПМ 02 Осуществление сборки и апробации, моделей элементов систем автоматизации с учетом специфики технологических процессов.
|
В методических указаниях рассматриваются операции слесарной обработки, виды инструмента, используемого при выполнении слесарных работ, требования к организации рабочего места слесаря и безопасность труда при выполнении операций слесарной обработки.
Методические указания по выполнению практических работ учебной практики способствуют формированию у обучающихся системы умений, практического опыта, элементов общих и профессиональных компетенций.
Образовательный результат |
Уметь: |
У1 пользоваться измерительным инструментом; У2 читать рабочие чертежи и эскизы; У3 пользоваться слесарным инструментом; У4 производить основные виды слесарных работ (правка, рубка, резка, опиливание, сверление, зенкерование и развертывание); У5 производить несложные слесарно-сборочные работы (клепка, паяние, склеивание); У6 производить несложные работы на токарно-винторезном, горизонтально-фрезерном, вертикально-сверлильном, поперечно-строгальном, заточном станках, электрических ножницах, механической пиле; У7 правильно разработать технологический процесс изготовления несложной детали (в виде технологической карты); У8 соблюдать правила ОТ: при слесарных работах, при работе на металлорежущих станках. |
Иметь практический опыт: |
О1 осознанного и углубленного изучения общепрофессиональных и специальных дисциплин; О2 работы со слесарным инструментом; О3 принципа действия и возможностей металлорежущего оборудования. |
Формируемые общие компетенции: |
ОК 1. Выбирать способы решения задач профессиональной деятельности, применительно к различным контекстам. ОК 2. Осуществлять поиск, анализ и интерпретацию информации, необходимой для выполнения задач профессиональной деятельности. ОК 3. Планировать и реализовывать собственное профессиональное и личностное развитие. ОК 4. Работать в коллективе и команде, эффективно взаимодействовать с коллегами, руководством, клиентами. ОК 5. Осуществлять устную и письменную коммуникацию на государственном языке Российской Федерации с учетом особенностей социального и культурного контекста. ОК 6. Проявлять гражданско-патриотическую позицию, демонстрировать осознанное поведение на основе традиционных общечеловеческих ценностей. ОК 7. Содействовать сохранению окружающей среды, ресурсосбережению, эффективно действовать в чрезвычайных ситуациях. ОК 8. Использовать средства физической культуры для сохранения и укрепления здоровья в процессе профессиональной деятельности и поддержания необходимого уровня физической подготовленности. ОК 9. Использовать информационные технологии в профессиональной деятельности. ОК 10. Пользоваться профессиональной документацией на государственном и иностранном языках. ОК 11. Использовать знания по финансовой грамотности, планировать предпринимательскую деятельность в профессиональной сфере. |
Формируемы е профессиональные компетенции |
ПК 2.1. Осуществлять выбор оборудования и элементной базы систем автоматизации в соответствии с заданием и требованием разработанной технической документации на модель элементов систем автоматизации. ПК 2.2. Осуществлять монтаж и наладку модели элементов систем автоматизации на основе разработанной технической документации. ПК 2.3. Проводить испытания модели элементов систем автоматизации в реальных условиях с целью подтверждения работоспособности и возможной оптимизации. |
Виды выполняемых работ |
1. Подготовка поверхности заготовки к разметке, нанесение разметки, кернение. 2. Правка листового материала, прутков, труб. 3. Гибка полосового материала и металла круглого сечения. 4. Рубка полосового металла в тисках. 5. Резание слесарными ножницами и слесарной ножовкой. 6. Сверление сквозных и глухих отверстий по предварительной разметке. 7. Нарезание резьбы плашками и метчиками. 8. Опиливание плоских и криволинейных поверхностей. 9. Шабрение и доводка плоскостей. 10. Сборка разъемных соединений. 11. Сборка неразъемных соединений (клепка). 12. Установка заготовок на металлорежущих станках. 13. Обработка заготовок на станках с ЧПУ. |
|
Практическое занятие №1
Вводное занятие и инструктаж по охране труда.
Виды слесарных работ
Слесарные работы применяются в различных видах производства. К основным видам слесарных работ относятся следующие:
– сборка машин и механизмов;
|
– техническое обслуживание и ремонт машин и механизмов;
– обеспечение производства инструментами и приспособлениями;
– монтаж приборов;
– подвод различных видов энергии.
Слесарные работы различных видов объединяет единая технология выполнения операций. К основным видам слесарных операций относится разметка, рубка, правка и гибка, резка, сверление, опиливание, зенкование и зенкерование, развёртывание отверстий, нарезание резьбы, клёпка, шабрение, распиливание и припасовка, притирка и доводка, пайка, лужение, склеивание.
Оснащение
В слесарных мастерских и на участках располагается оборудование индивидуального и общего пользования. К оборудованию индивидуального пользования относятся верстаки с тисками. К оборудованию общего пользования относятся: сверлильные и простые заточные станки (точильно-шлифовальные); опиловочно-зачистные станки; поверочные и разметочные плиты; винтовой пресс; ножовочный станок; рычажные ножницы; плиты для правки и др.
Слесарный верстак является одним из основных видов оборудования рабочего места для выполнения ручных работ и представляет собой специальный стол, на котором выполняют слесарные работы. Слесарные верстаки бывают одно- и многоместными. Одноместные верстаки имеют длину 1000...1200 мм, ширину 700...800 мм, высоту 800...900 мм, а многоместные – длину в зависимости от числа работающих, а ширину и высоту – те же, что и одноместные верстаки. Наиболее широко применяются одноместные верстаки. Многоместные слесарные верстаки имеют существенный недостаток: когда один рабочий выполняет точные работы (разметку, опиливание и т.д.), а другой в это время производит рубку или клёпку, то в результате вибрации верстака нарушается точность работ, выполняемых первым рабочим.
Слесарные тиски представляют собой зажимные приспособления для удерживания обрабатываемой детали в нужном положении. В зависимости от характера работы применяют стуловые, с параллельными губками и ручные тиски. Стуловые тиски получили своё название от способа крепления их на деревянном основании в виде стула, в дальнейшем они были приспособлены для закрепления на верстаках. Стуловые тиски применяют редко и только для выполнения грубых тяжёлых работ, связанных с применением ударной нагрузки, – при рубке, клёпке, гибке и пр. Тиски с параллельными губками и ручным приводом выпускают трёх типов: поворотные, неповоротные, инструментальные со свободным ходом передней губки. Поворотные тиски с параллельными губками могут поворачиваться на угол не менее 60 градусов. Корпус тисков с параллельными губками изготавливают из серого чугуна. Для увеличения срока службы тисков к рабочим частям губок прикрепляют винтами стальные (из инструментальной стали У8) пластины с сетчатой насечкой. Поэтому для зажима обработанной чистой поверхности детали (изделия) рабочие части губок тисков закрывают накладными пластинами («нагубниками»), изготовленными из мягкой стали, латуни, меди, алюминия, кожи и др. Размеры слесарных тисков определяются шириной их губок, которая для поворотных тисков составляет 80 и 140 мм с наибольшим раскрытием губок 95 и 180 мм. Неповоротные тиски с параллельными губками имеют основание, с помощью которого они крепятся болтами к крышке верстака, неподвижную
|
губку и подвижную. Для увеличения срока службы рабочие части губок делают сменными в виде призматических пластинок с сетчатой насечкой из инструментальной стали У8 и прикрепляют к губкам винтами. Ширина губок неповоротных тисков – 80 и 140 мм с наибольшим раскрытием губок 95 и 180 мм. Тиски с дополнительными губками для труб, кроме общего назначения, могут быть использованы для закрепления труб благодаря дополнительному призматическому вырезу. Наибольшие диаметры зажимаемых труб составляют 60, 70 и 140 мм. Ручные слесарные тиски применяются для закрепления деталей (заготовок) небольших размеров при опиливании либо сверлении, так как их неудобно или опасно держать руками. Ручные тиски различают трёх типов – шарнирные, с коническим креплением и пружинные. Их изготавливают с шириной губок 36, 40, 50 и 56 мм и раскрытием губок 28, 30, 40, 50 и 55 мм, а для мелких работ – с шириной губок 6, 10 и16 мм и раскрытием губок 5,5 и 6,5 мм.
При работе на тисках нужно соблюдать следующие правила:
– перед началом работы осматривать тиски, обращая особое внимание на прочность их крепления
к верстаку;
– не выполнять на тисках грубых работ (рубки, правки или гибки) тяжелыми молотками, так как
это приводит к быстрому разрушению тисков;
– при креплении деталей в тисках не допускать ударов по рычагу, это может привести к срыву
резьбы ходового винта или гайки;
– по окончании работ очищать тиски волосяной щёткой от стружки, грязи и пыли, а
направляющие и резьбовые соединения смазывать маслом;
– разводить губки тисков, так как в сжатом состоянии возникают излишние напряжения в
соединении винта и гайки.
Общие требования к организации рабочего места слесаря
Одним из основных элементов организации рабочего места является его планировка, при выполнении которой учитывают требования научной организации труда к расположению рабочего места по отношению к другим рабочим местам в мастерской, расположению оборудования, местоположению рабочего и оснастки, размещению инструментов, приспособлений (порядок на рабочем месте). Расстояния между тарой с заготовками и готовой продукцией и оборудованием (верстаком) должны быть такими, чтобы рабочий мог использовать преимущественно движение рук. При планировке рабочих мест должны учитываться зоны досягаемости рук в горизонтальной и вертикальной плоскостях. Наиболее удобная, оптимальная зона определяется полудугой радиусом примерно 300 мм для каждой руки. Максимальная зона досягаемости – 430 мм без наклона корпуса и 650 мм – с наклоном корпуса не более чем на 30 градусов для учащегося среднего роста.
Основные требования по соблюдению указанного порядка на рабочих местах состоят в следующем:
– всё необходимое для работы должно находиться под рукой, чтобы можно было сразу найти нужный предмет;
– инструменты и материалы, которые во время работы требуются чаще, размещают ближе к себе, а применяемые реже – дальше;
– все используемые предметы располагают примерно на высоте пояса;
– инструменты и приспособления размещают так, чтобы их удобно было брать соответствующей
рукой: что берут правой рукой – держат справа, что берут левой – слева;
– нельзя класть один предмет на другой или на отделанную поверхность детали;
– документацию (чертежи, технологические или инструкционные карты, наряды и др.) держат в удобном для пользования и защищенном от загрязнения месте;
– заготовки и готовые детали хранят так, чтобы они не загромождали проходы, и чтобы рабочему не приходилось часто нагибаться, если надо взять или положить заготовку или изделие;
– лёгкие предметы кладут выше тяжёлых.
Практическое занятие №2
Измерительный инструмент
Цель занятия
1. Изучить назначение и сущность разметки, инструменты и приспособления для разметки, контрольно-измерительные инструменты, методы измерения, технику безопасности при разметке.
2. Научиться выполнять разметку, используя приспособления для разметки и контрольно-измерительные инструменты.
В результате освоения данной темы обучающийся должен приобрести следующие умения У1-У4, У8
получить практический опыт О1, О2
Разметкой называется операция нанесения на обрабатываемую заготовку разметочных линий, определяющих контуры будущей детали или места, подлежащего обработке.
Точность, достигаемая при обычных методах разметки, составляет примерно 0,5 мм. При точной разметке её можно повысить до сотых долей миллиметра.
Различают несколько видов разметок:
– плоскостная разметка,выполняемая обычно на поверхности плоских деталей, на полосовом и листовом материале. Заключается в нанесении на заготовку контурных параллельных и перпендикулярных линий (рисок), окружностей, дуг, углов, осевых линий, разнообразных геометрических фигур по заданным размерам или контуров различных отверстий по шаблонам;
– пространственная разметка наиболее широко распространена в машиностроении, по приёмам она существенно отличается от плоскостной.
Подготовка к разметке
Перед разметкой необходимо выполнить следующее:
– очистить заготовку от пыли, грязи, окалины, следов коррозии стальной щёткой и др.;
– тщательно осмотреть заготовку; при обнаружении раковин, пузырей, трещин и т. п., точно измерить их и, составляя план разметки, принять меры к удалению этих дефектов в процессе дальнейшей обработки (если это возможно);
– все размеры заготовки должны быть тщательно рассчитаны, чтобы после обработки на поверхности не осталось дефектов;
– изучить чертеж размечаемой детали, выяснить её особенности и назначение; уточнить размеры; определить базовые поверхности заготовки, от которых следует откладывать размеры в процессе разметки; при плоскостной разметке базами могут служить обработанные кромки заготовки или осевые линии, которые наносятся в первую очередь; за базы удобно также принимать приливы, бобышки, платики.
Способы разметки
Разметка по шаблону обычно применяется при изготовлении больших партий одинаковых по форме и размерам деталей, но иногда этим способом размечают даже малые партии, если изделия сложной формы.
Разметка по образцу отличается тем, что не требуется изготовление шаблона. При этом учитывают износ.
Разметка по месту чаще применяется при сборке больших деталей. Одну деталь размечают по другой в таком положении, в каком они должны быть соединены.
Разметка карандашом производится по линейке на заготовках из алюминия и дюралюминия. Размечать последние с помощью чертилки не разрешается, так как при нанесении рисок разрушается защитный слой, и создаются условия для появления коррозии.
Точную разметку выполняют по тем же правилам, что и обычную, но применяют более точные измерительные и разметочные инструменты.
Правка металла
Кривизну деталей проверяют на глаз или по зазору между плитой и деталью.
Во время правки важно правильно выбирать места, по которым следует наносить удары. Правку выполняют на наковальне, правильной плите или надёжных подкладках, исключая возможность соскальзывания с них детали при ударе.
Правка полосового металла осуществляется в следующем порядке. Полосу располагают на правильной плите так, чтобы она лежала выпуклостью вверх, соприкасаясь с плитой в двух точках. По выпуклым частям наносят удары, регулируя их силу в зависимости от толщины полосы и величины кривизны: чем больше искривление и толще полоса, тем сильнее должны быть удары. Результат правки (прямолинейность заготовки) проверяют на глаз, а более точно – на разметочной плите по просвету или наложением линейки на полосу.
Правка прутка осуществляется следующим образом:после проверки на глаз на выпуклой стороне мелом отмечают границы изгибов, затем пруток укладывают на плиту или наковальню так, чтобы изогнутая часть находилась выпуклостью вверх, и наносят удары молотком.
Правка листового металла (рисунок 7) более сложна, чем предыдущие операции. При правке заготовок с выпучинами выявляют покоробленные участки, устанавливают, где больше выпучен металл. Правку начинают с ближайшего к выпучине края (рисунок 7 а), по которому наносят один ряд ударов молотком в пределах, указанных зачернёнными кружками. Затем наносят удары по второму краю. После этого по первому краю наносят второй ряд ударов и переходят опять ко второму краю и так до тех пор, пока постепенно не приблизятся к выпучине.
Рисунок 7 – Приемы правки листового материала
Если лист имеет волнистость по краям, но ровную середину, то удары молотком наносят от середины листа к краям (рисунок 7 б).
Тонкие листы правят лёгкими деревянными молотками – киянками, медными, латунными или свинцовыми молотками, а очень тонкие листы кладут на ровную плиту и выглаживают металлическими или деревянными брусками (рисунок 7 в, г).
Правка (рихтовка) закаленных деталей. После закалки стальные детали иногда коробятся. Правка искривленных после закалки деталей называется рихтовкой. Точность рихтовки может составлять 0,01...0,05 мм.
В зависимости от характера рихтовки применяют молотки с закалённым бойком или специальные рихтовальные молотки с закруглённой стороной бойка.
Изделия толщиной более 5 мм, если они закалены не насквозь, а только на глубину 1...2 мм, имеют вязкую сердцевину, поэтому рихтуются сравнительно легко; их нужно рихтовать, нанося удары по выпуклым местам. В случае коробления изделия по плоскости и по узкому ребру рихтовку выполняют отдельно – сначала по плоскости, а потом по ребру.
Правку короткого пруткового материала выполняют на призмах, правильных плитах или простых подкладках. Прямолинейность проверяют на глаз или по просвету между прутком и плитой.
Правку валов (диаметром до 30 мм) выполняют на ручных прессах с применением призмы.
Правку наклёпом производят после укладки изогнутого вала на ровную плиту выпуклостью вниз, нанося небольшим молотком частые и лёгкие удары по поверхности вала. После возникновения на поверхности наклёпанного слоя просвет между валом и плитой исчезает, и правку прекращают.
Оборудование для правки
В основном, на предприятиях применяют машинную правку на правильных вальцах, прессах и специальных приспособлениях.
Гибочные вальцы бывают ручными и приводными. На ручных и приводных трёхвалковых гибочных вальцах правят заготовки прямые и изогнутые по радиусу, имеющие на поверхности выпучины и вмятины.
Листогибочная трёхвалковая машина имеет расположенные один над другим валки, которые регулируются в зависимости от толщины заготовки, удаляясь друг от друга или сближаясь. Заготовку устанавливают между двумя передними валками и, вращая рукоятку по часовой стрелке, пропускают между валками до полного устранения выпучин и вмятин.
Правка валов и угловой стали на винтовых прессах применяется в тех случаях, когда правка молотком не обеспечивает должного результата.
Некоторые особенности имеет правка угловой стали. Деформированный уголок устанавливают в призме на столе пресса, между полками уголка устанавливают закалённый стальной валик. При нажиме винтом пресса валик придаёт уголку соответствующую форму. Листы, полосы и ленты правят на листоправочных станках, горизонтальных правильнорастяжных машинах и пневматических молотах.
Сварные соединения, имеющие коробления, подвергаются холодной правке вручную с помощью деревянных и стальных молотков на плитах, наковальнях и т. д. Холодную правку выполняют особенно осторожно.
Механизация гибочных работ
Профили (полосовой, сортовой металл) с разными радиусами кривизны гнут на трёх- и четырёхроликовых станках. Предварительно налаживают станок установкой верхнего ролика относительно двух нижних вращением рукоятки. При гибке заготовка должна быть прижата верхним роликом к двум нижним.
Профили с большим радиусом гибки получают на трёхроликовых станках (рисунок 10 а) в несколько переходов. При гибке заготовка 3 должна быть прижата верхним роликом 5 к двум нижним 1 и 6.
Четырёхроликовый станок (рисунок 10 б) состоит из станины 1, двух ведущих роликов 3 и 5, подающих заготовку, и двух нажимных роликов 4 и 8, изгибающих заготовку 7. Такие станки применяются для гибки профильного проката по дуге окружности или по спирали.
Рисунок 10 – Гибка кривых профилей
Гибка труб
Трубы гнут ручным и механизированным способами, в горячем и холодном состоянии, с наполнителями и без них. Способ гибки зависит от диаметра и материала трубы, значения угла изгиба.
Гибка труб в горячем состоянии применяется при диаметре более 100 мм. При горячей гибке с наполнителем трубу отжигают, размечают, один конец закрывают деревянной или металлической пробкой.
Диаметры пробок (заглушек) зависят от внутреннего диаметра трубы. Для труб малых диаметров заглушки делают из глины, резины или твёрдой древесины; выполняют их в виде конусной пробки длиной, равной 1,5...2 диаметрам трубы, с конусностью 1:10. Для труб больших диаметров заглушки изготовляют из металла.
Для каждой трубы в зависимости от ее диаметра и материала должен быть установлен минимально допустимый радиус гибки. При гибке труб этот радиус должен быть не меньше трех диаметров трубы, а длина нагреваемой части зависит от угла изгиба и диаметра трубы. Если трубу изгибают под углом 90º, то нагревают участок, равный шести диаметрам трубы, если под углом 60º, – равный четырем диаметрам, если под углом 45º, – трем диаметрам и т.д.
Длина L (мм) нагреваемого участка трубы определяется по формуле:
L = α · d/15,
где α – угол изгиба трубы, град; d – наружный диаметр трубы, мм;
15 – постоянный коэффициент
(90: 6 = 15; 60: 4 = 15; 45: 3 = 15).
При гибке труб в горячем состоянии работают в рукавицах. Трубы нагревают паяльными лампами в горнах или пламенем газовых горелок до вишнёво-красного цвета. Трубы рекомендуется изгибать с одного нагрева, так как повторный нагрев ухудшает качество металла.
Гибка труб в холодном состоянии выполняется с помощью различных приспособлений. Простейшим приспособлением для гибки труб диаметром 10...15 мм является плита с отверстиями, в которой в соответствующих местах устанавливают штыри, служащие упорами при гибке.
Трубы небольших диаметров (до 40 мм) с большими радиусами кривизны гнут в холодном состоянии, применяя простые ручные приспособления с неподвижной оправой. Трубы диаметром до 20 мм изгибают в приспособлении, которое крепится к верстаку с помощью ступицы и плиты.
Подлежащие гибке в холодном состоянии медные или латунные трубы заполняют расплавленной канифолью, расплавленным стеарином (парафином) или свинцом в расплавленном состоянии.
Медные трубы, подлежащие гибке в холодном состоянии, отжигают при температуре 600...700 градусов и охлаждают в воде. Наполнитель при гибке медных труб в холодном состоянии – канифоль, а в нагретом – песок.
Латунные трубы, подлежащие гибке в холодном состоянии, предварительно отжигают при температуре 600...700 градусов и охлаждают на воздухе. Наполнители те же, что и при гибке медных труб.
Дюралюминиевые трубы перед гибкой отжигают при температуре 350…400 градусов и охлаждают на воздухе.
При массовом изготовлении деталей из труб наибольших диаметров применяют ручные трубогибочные приспособления и рычажные трубогибы, а для гибки труб больших диаметров (до 350 мм) – специальные трубогибочные станки и прессы.
Гибку труб в кольцо производят на трёхроликовом гибочном станке.
Широко используют новые способы гибки труб.
Гибка с растяжением заготовки заключается в том, что заготовку подвергают совместному действию растягивающих (превышающих предел текучести металла) и изгибающих усилий. Такой способ применяют при изготовлении труб для самолётов, автомашин, морских судов и др.
При гибке труб с нагревом токами высокой частоты нагрев, гибка и охлаждение происходят непрерывно и последовательно в специальной высокочастотной установке типа трубогибочных станков. Установка допускает гибку труб диаметром от 95 до 300 мм. Она состоит из двух частей – механической и электрической.
Развальцовка (вальцевание) труб заключается в расширении (раскатывании) концов труб изнутри специальным инструментом (вальцовкой).
Процесс развальцовки состоит в том, что на конец трубы надевают фланец с выточенными в его отверстии канавками, затем в трубу вставляют вальцовку с роликами и вращают. Наиболее производительным является вальцевание на специальных вальцовочных машинах и различных механизмах.
При гибке металла дефектами чаще всего являются косые загибы и механические повреждения обработанной поверхности как результат неправильной разметки или закрепления деталей в тисках выше или ниже разметочной линии, а также неправильного нанесения ударов.
При гибке труб следует соблюдать следующие условия:
– тщательно следить за равномерностью вытягивания внешней стенки и посадки внутренней стенки трубы;
– учитывать, что вытягивания внешней стенки трубы происходят легче, чем посадка внутренней стенки;
– трубу гнуть плавно, без рывков;
– во избежание разрыва нельзя гнуть трубу и выправлять складки, если труба охладилась до светло-вишнёвого цвета (800 градусов), поэтому трубы больших диаметров гнут с многократным нагревом.
Практическое занятие №4
Рубка и резка металла.
Цель занятия
1. Изучить назначение и приемы рубки металла, оборудование, инструмент и приспособления, заточка инструмента, контроль качества. Назначение, сущность и способы резки металла. Применяемый режущий инструмент, приспособления, оборудование. Возможные дефекты при резке и рубке металла и меры по их предупреждению. Техника безопасности при рубке и резке металла.
2. Научиться выполнять рубку и резку металла различными способами.
В результате освоения данной темы обучающийся должен приобрести следующие умения У1-У4, У8
получить практический опыт О1, О2
Рубкой называется слесарная операция, при которой с помощью режущего (зубила, крейцмейселя и др.) и ударного (слесарного молотка) инструмента с поверхности заготовки (детали) удаляются лишние слои металла или заготовка разрубается на части.
В зависимости от назначения обрабатываемой детали рубка может быть чистовой и черновой. В первом случае зубилом за один рабочий ход снимают слой металла толщиной от 0,5 до 1 мм, во втором – от 1,5 до 2 мм. Точность обработки, достигаемая при рубке, составляет 0,4...1 мм. При рубке осуществляется резание – процесс удаления режущим инструментом с обрабатываемой заготовки (детали) лишнего слоя металла в виде стружки. Режущая часть (лезвие) представляет собой клин (зубило, резец) или несколько клиньев (ножовочное полотно, метчик, плашка, фреза, напильник).
На заготовке различают обрабатываемую и обработанную поверхности, а также поверхность резания. Обрабатываемой называется поверхность, с которой будет сниматься слой материала, а обработанной – поверхность, с которой стружка снята. Поверхность, по которой сходит стружка при резании, называется передней, а противоположная – задней.
Инструменты для рубки
Режущие инструменты. Зубило (рисунок 11 а) – это простейший режущий инструмент, в котором форма клина выражена особенно чётко.
Чем острее клин, т. е. чем меньше угол, образованный его сторонами, тем меньшее усилие потребуется для его углубления в материал.
Слесарное зубило представляет собой стальной стержень, изготовленный из инструментальной углеродистой или легированной стали (У7А, У8А, 7ХФ, 8ХФ).
Зубило изготавливают длиной 100, 125, 160, 200 мм, ширина рабочей части соответственно равна 5, 10, 16 и 20 мм. Рабочую часть зубила на длине 0,3...0,5 закаливают и отпускают. Степень закаливания зубила можно определить старым напильником, которым проводят по закалённой части.
Крейцмейсель (рисунок 11 б)отличается от зубила более узкой режущей кромкой и предназначен для вырубания узких канавок, шпоночных пазов и т. п. Для вырубания профильных канавок – полукруглых, двугранных и других применяют специальные инструменты для рубки крейцмейсели, называемые канавочниками.
а – зубило, б – крейцмейсель, в - канавочник
Рисунок 11Инструменты для рубки
Канавочники (рисунок 11 в) изготовляют из стали У8А длиной 80, 100, 120, 150, 200, 300 и 350 мм с радиусом закругления 1; 1,5; 2; 2,5 и 3 мм.
Заточка зубил и крейцмейселя производится на заточном станке. Перед заточкой инструмента подручник устанавливают как можно ближе к шлифовальному кругу. Зазор между подручником и заточным кругом должен быть не более 2...3 мм, чтобы затачиваемый инструмент не мог попасть между кругом и подручником.
Канавочники (рисунок 6 в) изготовляют из стали У8А длиной 80, 100, 120, 150, 200, 300 и 350 мм с радиусом закругления 1; 1,5; 2; 2,5 и 3 мм.
Заточка зубил и крейцмейселя производится на заточном станке. Перед заточкой инструмента подручник устанавливают как можно ближе к шлифовальному кругу. Зазор между подручником и заточным кругом должен быть не более 2...3 мм, чтобы затачиваемый инструмент не мог попасть между кругом и подручником.
После заточки зубила или крейцмейселя с режущих кромок снимают заусеницы. Угол заострения проверяют шаблоном, представляющим собой пластинки с угловыми вырезами 70, 60, 45 и 35 градусов.
Слесарный молоток – это инструмент для работы с различными слесарными инструментами.
Слесарные молотки с круглым бойком (рисунок 12 б) изготавливают шести номеров: № 1 (200 г) применяют в разметке и правке; № 2 (400 г), № 3 (500 г) и № 4 (600 г) – для слесарных работ; № 5 (800 г) и № 6 (1000 г) применяют редко.
Слесарные молотки с квадратным бойком (рисунок 12 а)изготовляют восьми номеров: № 1 (50 г), № 2 (100 г) и № 3 (200 г) – для слесарноинструментальных работ; № 4 (400 г), № 5 (500 г) и № 6 (600 г) – для слесарных работ, рубки, гибки, клёпки и др.; № 7 (800 г) и № 8 (1000 г) применяют редко. Для тяжёлых работ применяют молотки массой 4...16 кг, называемые кувалдами.
В некоторых случаях, например, при изготовлении изделий из тонкой листовой стали, применяют деревянные молотки – киянки, которые бывают с круглым или прямоугольным ударником.
а б в
а – молоток с квадратным бойком; б – молоток с круглым бойком;
в – схемы расклинивания рукояток:1 – боек; 2 – клин деревянный; 3 – носок;
4 – рукоятка.
Рисунок 12 – Молотки слесарные
Сущность процесса резки
Резкой называют отделение частей (заготовок) от сортового или листового металла. Резка выполняется как со снятием стружки, так и без снятия. Сущность процесса резки ножницами заключается в отделении частей металла под действием пары режущих ножей. Разрезаемый лист помещают между верхним и нижним ножами. Верхний нож, опускаясь, давит на металл и разрезает его. Н
|
|
Историки об Елизавете Петровне: Елизавета попала между двумя встречными культурными течениями, воспитывалась среди новых европейских веяний и преданий...
Автоматическое растормаживание колес: Тормозные устройства колес предназначены для уменьшения длины пробега и улучшения маневрирования ВС при...
Типы сооружений для обработки осадков: Септиками называются сооружения, в которых одновременно происходят осветление сточной жидкости...
Типы оградительных сооружений в морском порту: По расположению оградительных сооружений в плане различают волноломы, обе оконечности...
© cyberpedia.su 2017-2024 - Не является автором материалов. Исключительное право сохранено за автором текста.
Если вы не хотите, чтобы данный материал был у нас на сайте, перейдите по ссылке: Нарушение авторских прав. Мы поможем в написании вашей работы!