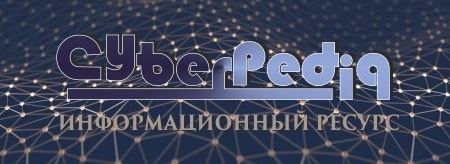
История развития хранилищ для нефти: Первые склады нефти появились в XVII веке. Они представляли собой землянные ямы-амбара глубиной 4…5 м...
Организация стока поверхностных вод: Наибольшее количество влаги на земном шаре испаряется с поверхности морей и океанов (88‰)...
Топ:
Эволюция кровеносной системы позвоночных животных: Биологическая эволюция – необратимый процесс исторического развития живой природы...
Характеристика АТП и сварочно-жестяницкого участка: Транспорт в настоящее время является одной из важнейших отраслей народного...
Отражение на счетах бухгалтерского учета процесса приобретения: Процесс заготовления представляет систему экономических событий, включающих приобретение организацией у поставщиков сырья...
Интересное:
Лечение прогрессирующих форм рака: Одним из наиболее важных достижений экспериментальной химиотерапии опухолей, начатой в 60-х и реализованной в 70-х годах, является...
Что нужно делать при лейкемии: Прежде всего, необходимо выяснить, не страдаете ли вы каким-либо душевным недугом...
Инженерная защита территорий, зданий и сооружений от опасных геологических процессов: Изучение оползневых явлений, оценка устойчивости склонов и проектирование противооползневых сооружений — актуальнейшие задачи, стоящие перед отечественными...
Дисциплины:
![]() |
![]() |
5.00
из
|
Заказать работу |
|
|
Подготовка МНЛЗ к разливке металла производится в соответствии раздела 3.
Подготовка промковша производится в соответствии раздела 4.
Подготовка металла к разливке производится в соответствии раздела 5.
Температура стали в стальковше после обработки на АКОС и промковше должна соответствовать таблице 10.
7.1. Установить на промковш (температура футеровки промковша от 1100 до 12000С) предварительно разогретый от 900 до 1000 ºС погружной стакан (для кремнемарганцовистых марок стали – п.3.3.9, для углеродистых марок стали – п.3.3.10). Отцентрировать погружной стакан в кристаллизаторе и произвести выверку стакана по вертикали (визуально).
Допустимые отклонения вертикально установленного стакана в сторону широких граней ± 5 мм, узких ± 10 мм.
Таблица 10
Марка стали | Температура металла в стальковше | Средняя температура металла в пром. ковше | Время выдержки в стопе до отправления на продольную резку из цеха | |
на первую плавку в серии, оС | на вторую и последующие плавки серии, оС | |||
SAE 1006 | 1605 + 5 | 1595 + 5 | 1555 ±5 | 3 часа |
SAE 1008 | 1605 + 5 | 1595 + 5 | 1555 ±5 | 3 часа |
SAE 1010 | 1605 + 5 | 1595 + 5 | 1555 ±5 | 3 часа |
SAE 1018 | 1600 + 5 | 1590 + 5 | 1550 ±5 | 3 часа |
RST 36-2 | 1605 + 5 | 1595 + 5 | 1555 ±5 | 3 часа |
С45R+H+A | 1575 + 5 | 1565 + 5 | 1525 ±5 | 2 часа |
Ст.1сп | 1605 + 5 | 1595 + 5 | 1555 ±5 | 3 часа |
Ст.2сп | 1605 + 5 | 1595 + 5 | 1555 ±5 | 3 часа |
Ст.3сп | 1595 + 5 | 1585 + 5 | 1540 ±5 | 3 часа |
10 | 1605 + 5 | 1595 + 5 | 1550 ±5 | 3 часа |
20 | 1595 + 5 | 1585 + 5 | 1540 ±5 | 3 часа |
35 | 1585 + 5 | 1575 + 5 | 1535 ±5 | 2 часа |
Д | 1580 + 5 | 1570 + 5 | 1530 ±5 | 2 часа |
S45C | 1580 + 5 | 1570 + 5 | 1530 ±5 | 2 часа |
S35R+H+A | 1585 + 5 | 1575 + 5 | 1535 ±5 | 2 часа |
09Г2С | 1590 + 5 | 1580 + 5 | 1540 ±5 | 3 часа |
Ст.1пс | 1605 + 5 | 1595 + 5 | 1555 ±5 | 3 часа |
Ст.2пс | 1605 + 5 | 1595 + 5 | 1555 ±5 | 3 часа |
Ст.3пс | 1595 + 5 | 1585 + 5 | 1545 ±5 | 3 часа |
Ст.5сп | 1585 + 5 | 1575 + 5 | 1535 ±5 | 2 часа |
Ст.5пс | 1595 + 5 | 1585 + 5 | 1540 ±5 | 2 часа |
Ст.6сп | 1585 + 5 | 1575 + 5 | 1525 ±5 | 2 часа |
50 | 1575 + 5 | 1565 + 5 | 1525 ±5 | 2 часа |
С45R | 1585 + 5 | 1575 + 5 | 1535 ±5 | 2 часа |
S35R | 1585 + 5 | 1575 + 5 | 1535 ±5 | 2 часа |
CR45 | 1585 + 5 | 1575 + 5 | 1535 ±5 | 2 часа |
S25C | 1590 + 5 | 1580 + 5 | 1540 ±5 | 2 часа |
1-057 | 1590 + 5 | 1580 + 5 | 1540 ±5 | 2 часа |
S355JR | 1600±5 | 1590±5 | 1540 ±5 | 3 часа |
S275JR | 1605 ±5 | 1595 ±5 | 1545 ±5 | 3 часа |
S235JRG2 | 1595 ±5 | 1585 ±5 | 1545 ±5 | 3 часа |
S355J2G3 | 1585 + 5 | 1575 + 5 | 1535 ±5 | 3 часа |
A36-1 | 1600 + 5 | 1590 + 5 | 1550 ±5 | 3 часа |
A36-2 | 1595 + 5 | 1585 + 5 | 1545 ±5 | 3 часа |
St44-2 | 1595 + 5 | 1585 + 5 | 1545 ±5 | 3 часа |
A36 | 1600 + 5 | 1590 + 5 | 1550 ±5 | 3 часа |
S235JR | 1595 ±5 | 1585 ±5 | 1545 ±5 | 3 часа |
S355J2 | 1590 + 5 | 1580 + 5 | 1540 ±5 | 2 часа |
S235JR+N | 1595 ±5 | 1585 ±5 | 1545 ±5 | 3 часа |
SS 400 | 1595 ±5 | 1585 ±5 | 1545 + 5 | 3 часа |
S355J2G3+N | 1595 + 5 | 1585 + 5 | 1545 ±5 | 3 часа |
S275JR+AR | 1595 ±5 | 1585 ±5 | 1545 ±5 | 3 часа |
S355JR+AR | 1595 ±5 | 1585 ±5 | 1545 ±5 | 3 часа |
АМ1 | 1615 + 5 | 1610 + 5 | 1555 ±5 | 3 часа |
10(15)ХСНД | 1605 + 5 | 1600 + 5 | 1540 ±5 | 24 часа |
St1sp | 1605 + 5 | 1595 + 5 | 1555 ±5 | 3 часа |
St 52-3 | 1590 ±5 | 1585 ±5 | 1545 ±5 | 3 часа |
08 пс | 1610 + 5 | 1605 + 5 | 1555 ±5 | 3 часа |
Rst 37-2N | 1605 + 5 | 1595 + 5 | 1555 ±5 | 3 часа |
7. 2. Для защиты металла в промковш отдают ШОС51, в кристаллизатор – ШОС 50К. (п.3.3.11 – 3.3.13).
|
7.3. Химический состав стали должен удовлетворять ГОСТ, ТУ и МС с рекомендуемым содержанием S не более 0,015 масс% и со следующими рекомендуемыми соотношениями химических элементов:
[Mn] / [Si] ³ 2,3; [Mn] / [S]=23 ¸ 25;
7.4. По команде мастера разливки открыть шиберный затвор, в стык защитной трубы с коллектором одновременно подать аргон 20 - 25 м3/ч при давлении от 0,2 до 0,4 МПа (2,0 - 4,0 кгс/см2) и на струю отдать от 10 до 20 кг силикокальция марки СК15, СК25, СК30. Допускается вместо подачи аргона стык стакана-коллектора и защитной трубы защищать плавкой вставкой.
7.5. При достижении в промковше 25-30% рабочего уровня металла (260-300 мм) закрыть зеркало металла ШОС 51 (БШС) или другими ШОС для промковша, согласно рекомендациям ИТЦ.
7.6. Время между последним измерением температуры металла на АКОС и открытием шиберного затвора должно составлять не более 20 мин, от момента поднятия горелок разогрева до поступления металла в промковш – не более 5 мин. Открытие шиберного затвора сталеразливочного ковша считается началом разливки.
|
7.7. После наполнения металлом промковша на 1/3 высоты разливщик проверяет работу шиберного затвора на открытие и закрытие. И при удовлетворительной его работе отдает команду открыть стопор промковша и дать металл в кристаллизатор. Время наполнения промковша до открытия стопора от 18 до 20 сек при полном открытии шиберного затвора и диаметре стакана 70 мм. Одновременно в кристаллизатор в процессе его заполнения до уровня от 400 до 450 мм равномерно дать от 6 до 7 кг подготовленных холодильников. (Расход холодильников определяется в зависимости от ширины кристаллизатора).
7.8. Оператор главного пульта управления объявляет: «Металл» в кристаллизаторе" и начинает отсчет времени. Одновременно подать воду и воздух на ЗВО. Контролер УТК фиксирует время заполнения кристаллизатора до момента начала пуска качания и вытягивания заготовки. Время заполнения кристаллизатора фиксируется в журнале разливки.
При заполнении промковша необходимо постоянное присутствие на участке слесаря по ремонту гидравлики для принятия срочных мер в случае некрытия шиберного затвора.
7.9. После перекрытия выходных отверстий погружного стакана подать на мениск шлакообразующую смесь. Во время наполнения кристаллизатора разливщик проверяет работу стопора путем периодического перекрытия струи металла. В случае некрытия стопора необходимо приработать его. Заплески стенок кристаллизатора во время наполнения не допускаются.
7.10. Поверхность смеси, покрывающей мениск металла в кристаллизаторе, должна быть серого цвета. Оголение мениска не допускается. При появлении красных пятен ШОС равномерно подсыпается по всей поверхности. Запрещается перемешивание расплавленного ШОС с нерасплавленной.
7.11. При подходе уровня металла к номинальному (60 – 100 мм от верхнего среза медных стенок), но не ранее, чем через 40 секунд после начала наполнения кристаллизатора, по команде мастера включить привод качания кристаллизатора.
Частота качания соответствует таблице 11 в зависимости от принятой амплитуды качания.
Таблица 11 ЗАВИСИМОСТЬ ЧАСТОТЫ КАЧАНИЯ КРИСТАЛЛИЗАТОРА ОТ СКОРОСТИ РАЗЛИВКИ И АМПЛИТУДЫ
Амплитуда ± 3,0мм
V разл м/мин | 0,20 | 0,25 | 0,30 | 0,35 | 0,40 | 0,45 | 0,50 | 0,55 | 0,65 | 0,70 | 0,75 |
Част. кач., 1/мин | 40 33 30 | 44 37 34 | 48 41 37 | 52 44 41 | 56 47 43 | 60 50 46 | 63 53 49 | 66 56 51 | 69 58 54 | 71 60 56 | 75 63 58 |
|
0,80 | 0,85 | 0,90 | 0,95 | 1,0 | 1,05 | 1,10 | 1,15 | 1,20 | 1,25 | 1,30 |
81 68 62 | 83 70 65 | 86 73 67 | 88 75 69 | 91 77 72 | 91 80 74 | 96 82 76 | 98 84 78 | 101 86 80 | 103 88 82 | 105 90 84 |
Амплитуда ± 4,5мм
V разл м/мин | 0,20 | 0,25 | 0,30 | 0,35 | 0.40 | 0,45 | 0,50 | 0,55 | 0,60 | 0,65 | 0,70 |
Част. кач., 1/мин | 32 27 24 | 36 30 27 | 40 33 30 | 43 36 32 | 46 36 35 | 48 41 37 | 39 42 51 | 54 55 41 | 56 47 43 | 58 49 45 | 61 51 47 |
0,75 | 0,80 | 0,85 | 0,90 | 0,95 | 1,0 | 1,05 | 1,10 | 1,15 | 1,20 | 1,25 | 1,30 |
63 53 49 | 65 55 51 | 67 57 52 | 69 58 54 | 71 60 55 | 73 62 57 | 75 64 58 | 77 65 60 | 79 67 62 | 81 68 63 | 82 70 65 | 84 72 66 |
Амплитуда ± 6,0мм
V разл м/мин | 0,20 | 0,25 | 0,30 | 0,35 | 0,40 | 0,45 | 0,50 | 0,55 | 0,60 | 0,65 | 0,70 |
Част. кач., 1/мин | 27 23 21 | 31 26 23 | 34 29 26 | 37 32 28 | 29 33 30 | 42 35 32 | 44 37 34 | 46 39 35 | 48 41 37 | 50 42 39 | 52 44 40 |
0,75 | 0,80 | 0,85 | 0,90 | 0,95 | 1,0 | 1,05 | 1,10 | 1,15 | 1,20 | 1,25 | 1,30 |
54 46 42 | 56 47 43 | 58 49 45 | 60 50 46 | 61 52 47 | 63 53 49 | 65 54 50 | 66 56 51 | 68 57 52 | 69 58 54 | 71 59 55 | 72 61 56 |
Амплитуда качания должна быть А = ± 6 мм. При повышении усилия вытягивания заготовки из кристаллизатора более 5 тс пользоваться меньшими значениями частот качания.
При средних значениях температуры металла в промковше пользоваться средними значениями частот качания.
При низких значениях температуры металла в промковше и малых усилиях вытягивания заготовки (менее 1,0 тс) пользоваться высокими значениями частот качания.
7.12. При отсутствии «зависания» металла в кристаллизаторе, по команде мастера включить приводы вращения роликовых секций со скоростью 0,2 м/мин. Оператор главного пульта объявляет: «машина пушена».
7.13. Скорость разливки увеличивают по схеме:
- скорость 0,2 м/мин в течение 30 с до 0,3 м/мин L = 0,1 м
- скорость 0,3 м/мин в течение 20 с до 0,4 м/мин L = 0,2 м
- скорость 0,4 м/мин в течение 15 с до 0,5 м/мин L = 0,3 м
- скорость 0,5 м/мин в течение 12 с до 0,6 м/мин L = 0,4 м
- скорость 0,6 м/мин в течение 10 с до 0,7 м/мин L = 0,5 м
- скорость 0,7 м/мин в течение 8 с до 0,8 м/мин L = 0,6 м
Скорость разливки 0,8 м/мин поддерживают до первого измерения температуры (после отливки 3 м слитка). Разливщик и мастер разливки должны контролировать работу ШОС в кристаллизаторе и «подвисание» слитка до выхода на рабочую скорость.
|
7.13.1. В процессе разливки производят измерения температуры металла в промковше: после отливки 3 м слитка, после 10 м и в последующем через 10 м до конца разливки. Затем в зависимости от температуры металла в промковше выходят на требуемую скорость разливки табл.12 и частоту качания кристаллизатора согласно табл.11.
Таблица 12 Температурно-скоростные режимы разливки углеродистых марок стали в зависимости от сечения заготовки
Температура разливки 1555±5ºС
сечение 170х1550…1460
Температура металла в п/ковше, 0С | 1535 | 1540 | 1545 | 1550 | 1555 | 1560 | 1565 | 1570 |
Скорость разливки, м/мин | 0,90 | 0,85 | 0,80 | 0,75 | 0,70 | 0,65 | 0,60 | 0,60 |
* | * | раб. | рабоч. | рабоч. | рабоч. | * | * |
сечение 170х1420…1380
Температура металла в п/ковше, 0С | 1535 | 1540 | 1545 | 1550 | 1555 | 1560 | 1565 | 1570 |
Скорость разливки, м/мин | 0,95 | 0,90 | 0,85 | 0,80 | 0,75 | 0,70 | 0,65 | 0,60 |
* | * | раб. | рабоч. | рабоч. | рабоч. | * | * |
сечение 170х1250…1350
Температура металла в п/ковше, 0С | 1535 | 1540 | 1545 | 1550 | 1555 | 1560 | 1565 | 1570 |
Скорость разливки, м/мин | 1,0 | 0,95 | 0,90 | 0,85 | 0,80 | 0,75 | 0,65 | 0,60 |
* | * | раб. | рабоч. | рабоч. | рабоч. | * | * |
сечение 170х1100…1030
Температура металла в п/ковше, 0С | 1535 | 1540 | 1545 | 1550 | 1555 | 1560 | 1565 | 1570 |
Скорость разливки, м/мин | 1,05 | 1,0 | 0,95 | 0,90 | 0,85 | 0,80 | 0,75 | 0,70 |
* | * | раб. | рабоч. | рабоч. | рабоч. | * | * |
Температура разливки 1550±5ºС
сечение 170х1550…1460
Температура металла в п/ковше, 0С | 1535 | 1540 | 1545 | 1550 | 1555 | 1560 | 1565 |
Скорость разливки, м/мин | 0,85 | 0,80 | 0,75 | 0,70 | 0,65 | 0,60 | 0,60 |
* | раб. | рабоч. | рабоч. | рабоч. | * | * |
сечение 170х1420…1380
Температура металла в п/ковше, 0С | 1535 | 1540 | 1545 | 1550 | 1555 | 1560 | 1565 |
Скорость разливки, м/мин | 0,90 | 0,85 | 0,80 | 0,75 | 0,70 | 0,65 | 0,65 |
* | раб. | рабоч. | рабоч. | рабоч. | * | * |
сечение 170х1250…1350
Температура металла в п/ковше, 0С | 1535 | 1540 | 1545 | 1550 | 1555 | 1560 | 1565 | 1570 | 1575 |
Скорость разливки, м/мин | 0,95 | 0,90 | 0,85 | 0,80 | 0,75 | 0,70 | 0,65 | 0,60 | 0,60 |
* | раб. | раб. | рабоч. | рабоч. | * | * | * | * |
сечение 170х1100…1030
Температура металла в п/ковше, 0С | 1535 | 1540 | 1545 | 1550 | 1555 | 1560 | 1565 |
Скорость разливки, м/мин | 1,0 | 0,95 | 0,90 | 0,85 | 0,80 | 0,75 | 0,65 |
* | раб. | рабоч. | рабоч. | рабоч. | * | * |
Температура разливки 1545±5ºС
сечение 170х1550…1460 мм
Температура металла в п/ковше, 0С | 1530 | 1535 | 1540 | 1545 | 1550 | 1555 | 1560 |
Скорость разливки, м/мин | 0,85 | 0,80 | 0,75 | 0,70 | 0,65 | 0,60 | 0,60 |
* | раб. | рабоч. | рабоч. | рабоч. | * | * |
сечение 170х1420…1380 мм
Температура металла в п/ковше, 0С | 1530 | 1535 | 1540 | 1545 | 1550 | 1555 | 1560 |
Скорость разливки, м/мин | 0,90 | 0,85 | 0,80 | 0,75 | 0,70 | 0,65 | 0,60 |
* | раб. | рабоч. | рабоч. | рабоч. | * | * |
сечение 170х1250…1350 мм
Температура металла в п/ковше, 0С | 1530 | 1535 | 1540 | 1545 | 1550 | 1555 | 1560 | 1565 |
Скорость разливки, м/мин | 0,95 | 0,90 | 0,85 | 0,85 | 0,80 | 0,70 | 0,65 | 0,60 |
* | раб. | рабоч. | рабоч. | рабоч. | * | * | * |
сечение 170х1030…1100
|
Температура металла в п/ковше, 0С | 1530 | 1535 | 1540 | 1545 | 1550 | 1555 | 1560 | 1565 |
Скорость разливки, м/мин | 1,0 | 0,95 | 0,90 | 0,85 | 0,80 | 0,75 | 0,70 | 0,65 |
* | раб. | рабоч. | рабоч. | рабоч. | * | * | * |
Температура разливки 1540±5ºС
сечение 170х1550…1460 мм
Температура металла в п/ковше, 0С | 1525 | 1530 | 1535 | 1540 | 1545 | 1550 |
Скорость разливки, м/мин | 0,85 | 0,80 | 0,75 | 0,70 | 0,65 | 0,60 |
* | раб. | рабоч. | рабоч. | рабоч. | * |
сечение 170х1420…1380 мм
Температура металла в п/ковше, 0С | 1525 | 1530 | 1535 | 1540 | 1545 | 1550 | 1555 |
Скорость разливки, м/мин | 0,90 | 0,85 | 0,80 | 0,75 | 0,70 | 0,65 | 0,60 |
* | раб. | рабоч. | рабоч. | рабоч. | * | * |
сечение 170х1250…1350 мм
Температура металла в п/ковше, 0С | 1525 | 1530 | 1535 | 1540 | 1545 | 1550 | 1555 | 1560 |
Скорость разливки, м/мин | 0,95 | 0,90 | 0,85 | 0,80 | 0,75 | 0,70 | 0,65 | 0,60 |
* | раб. | рабоч. | рабоч. | раб. | * | * | * |
сечение 170х1030…1100 мм
Температура металла в п/ковше, 0С | 1525 | 1530 | 1535 | 1540 | 1545 | 1550 | 1555 | 1560 |
Скорость разливки, м/мин | 1,00 | 0,95 | 0,90 | 0,85 | 0,80 | 0,75 | 0,70 | 0,65 |
* | раб. | рабоч | рабоч. | рабоч. | * | * | * |
Температура разливки 1535±5ºС
сечение 170х1550
Температура металла в п/ковше, 0С | 1520 | 1525 | 1530 | 1535 | 1540 | 1545 | 1550 |
Скорость разливки, м/мин | 0,85 | 0,8 | 0,75 | 0,70 | 0,65 | 0,60 | 0,60 |
* | раб. | рабоч. | рабоч. | раб. | * | * |
сечение 170х1420…1380
Температура металла в п/ковше, 0С | 1520 | 1525 | 1530 | 1535 | 1540 | 1545 | 1550 | 1555 |
Скорость разливки, м/мин | 0,90 | 0,85 | 0,80 | 0,75 | 0,70 | 0,65 | 0,60 | 0,60 |
* | раб. | рабоч. | рабоч. | раб. | * | * | * |
сечение 170х1250…1350
Температура металла в п/ковше, 0С | 1520 | 1525 | 1530 | 1535 | 1540 | 1545 | 1550 | 1555 |
Скорость разливки, м/мин | 0,95 | 0,90 | 0,85 | 0,80 | 0,75 | 0,70 | 0,65 | 0,60 |
* | раб. | рабоч. | рабоч. | раб. | * | * | * |
сечение 170х1030…1100
Температура металла в п/ковше, 0С | 1520 | 1525 | 1530 | 1535 | 1540 | 1545 | 1550 | 1555 | 1560 |
Скорость разливки, м/мин | 1,0 | 0,95 | 0,90 | 0,85 | 0,80 | 0,75 | 0,70 | 0,65 | 0,60 |
* | раб. | раб. | рабоч. | раб. | * | * | * | * |
Температура разливки 1530±5ºС
сечение 170х1550
Температура металла в п/ковше, 0С | 1515 | 1520 | 1525 | 1530 | 1535 | 1540 | 1545 | 1550 |
Скорость разливки, м/мин | 0,85 | 0,80 | 0,75 | 0,70 | 0,65 | 0,60 | 0,60 | 0,55 |
* | раб. | рабоч. | рабоч. | раб. | * | * | * |
сечение 170х1420…1380
Температура металла в п/ковше, 0С | 1515 | 1520 | 1525 | 1530 | 1535 | 1540 | 1545 | 1550 |
Скорость разливки, м/мин | 0,90 | 0,85 | 0,80 | 0,75 | 0,70 | 0,65 | 0,60 | 0,60 |
* | раб. | рабоч. | рабоч. | раб. | * | * | * |
сечение 170х1250…1350
Температура металла в п/ковше, 0С | 1515 | 1520 | 1525 | 1530 | 1535 | 1540 | 1545 | 1550 |
Скорость разливки, м/мин | 0,95 | 0,90 | 0,85 | 0,80 | 0,75 | 0,70 | 0,65 | 0,60 |
раб. | рабоч. | рабоч. | раб. | * | * | * | * |
сечение 170х1030…1100
Температура металла в п/ковше, 0С | 1515 | 1520 | 1525 | 1530 | 1535 | 1540 | 1545 | 1550 |
Скорость разливки, м/мин | 1,0 | 0,95 | 0,90 | 0,85 | 0,80 | 0,75 | 0,70 | 0,60 |
раб. | рабоч. | рабоч. | раб. | * | * | * | * |
температура разливки 1525±5ºС
сечение 170х1550…
Температура металла в п/ковше, 0С | 1510 | 1515 | 1520 | 1525 | 1530 | 1535 | 1540 | 1545 |
Скорость разливки, м/мин | 0,85 | 0,80 | 0,75 | 0,70 | 0,65 | 0,60 | 0,60 | 0,55 |
* | раб. | рабоч. | рабоч. | раб. | * | * | * |
сечение 170х1380…1420 мм
Температура металла в п/ковше, 0С | 1510 | 1515 | 1520 | 1525 | 1530 | 1535 | 1540 | 1545 |
Скорость разливки, м/мин | 0,90 | 0,85 | 0,80 | 0,75 | 0,70 | 0,65 | 0,60 | 0,60 |
* | раб. | рабоч. | рабоч. | раб. | * | * | * |
сечение 170х1250…1350 мм
Температура металла в п/ковше, 0С | 1510 | 1515 | 1520 | 1525 | 1530 | 1535 | 1540 | 1545 |
Скорость разливки, м/мин | 0,95 | 0,90 | 0,85 | 0,80 | 0,75 | 0,70 | 0,65 | 0,60 |
* | раб. | рабоч. | рабоч. | раб. | * | * | * |
сечение 170х1030…1100 мм
Температура металла в п/ковше, 0С | 1510 | 1515 | 1520 | 1525 | 1530 | 1535 | 1540 | 1545 | 1550 |
Скорость разливки, м/мин | 1,0 | 0,95 | 0,90 | 0,85 | 0,80 | 0,75 | 0,70 | 0,65 | 0,60 |
* | раб. | раб. | раб. | раб. | * | * | * | * |
Примечание:
* - рекомендуемые значения исходя из условий разливки
7.14. Выбранный уровень металла поддерживать в пределах от 60 до 100 мм от верхнего среза медных стенок кристаллизатора. Для уменьшения выработки поверхности погружного стакана по шлаковому поясу поменять 1 раз уровень погружения стакана в пределах ± 20 – 40 мм на плавке.
7.14. Во время наполнения кристаллизатора на струю отдать 200 - 300 г гранулированного алюминия (один стакан емкостью 250 мл).
7.15. Предельно допустимое значение усилия вытягивания заготовки из кристаллизатора 10 тс. При повышении усилия вытягивания заготовки до предельных значений 10 тс необходимо снизить скорость вытягивания заготовки до 0,60-0,65 м/мин. При сохранении усилия более 10 тс или дальнейшем повышении его остановить разливку.
7.16. После наполнения металлом промковша засыпать шлакообразующую смесь ШОС (БШС или другую ШОС согласно рекомендациям ИТЦ) 51, массой 60 кг, а затем через каждые 20 т разлитого металла засыпать в промковш по 10 -15 кг ШОС 51 (БШС или другую ШОС согласно рекомендациям ИТЦ). Общий расход ШОС в промковш 0,8-1,0 кг/т стали.
7.17. Расход шлакообразующей смеси ШОС 50К или другую ШОС согласно рекомендациям ИТЦ в кристаллизатор от 0,8 до 1,0 кг на тонну.
7.18. Расход воды на вторичное охлаждение в зависимости от сечения кристаллизаторов и скорости разливки поддерживать в соответствии табл.4.
7.19.Раскрой непрерывнолитой заготовки производить согласно табл.13 на МГР «GEGA» или гидравлическими ножницами.
Таблица 13 Раскрой непрерывнолитой заготовки на мерные длины (слябы)
в горячем состоянии с учетом линейной усадки
№ п/п | Длина сляба в холодном состоянии для стана 2300 / 1700 СТП 134-39-97 | Длина непрерывнолитой заготовки | ||
Среднее значение длины сляба, мм | Минимальное значение, мм | Максимальное значение, мм | ||
1 | 3200 ±5030 | 3244 | 3214 | 3294 |
2 | 3250 ±5030 | 3294 | 3264 | 3344 |
3 | 3300 ±5030 | 3345 | 3315 | 3395 |
4 | 3350 ±5030 | 3396 | 3366 | 3446 |
5 | 3400 ±5030 | 3446 | 3416 | 3496 |
6 | 3450 ±5030 | 3497 | 3467 | 3547 |
7 | 3500 ±5030 | 3548 | 3518 | 3598 |
8 | 3550 ±5030 | 3598 | 3568 | 3648 |
9 | 3600 ±5030 | 3649 | 3619 | 3699 |
10 | 3650 ±5030 | 3700 | 3670 | 3750 |
11 | 3700 ±5030 | 3750 | 3720 | 3800 |
12 | 3750 ±5030 | 3801 | 3771 | 3851 |
13 | 3800 ±5030 | 3852 | 3822 | 3902 |
14 | 3850 ±5030 | 3903 | 3873 | 3953 |
15 | 3900 ±5030 | 3953 | 3923 | 4003 |
16 | 3950 ±5030 | 4004 | 3974 | 4054 |
17 | 4000 ±5030 | 4055 | 4025 | 4105 |
18 | 4050 ±5030 | 4105 | 4075 | 4155 |
19 | 4100 ±5030 | 4156 | 4126 | 4206 |
20 | 4150 ±5030 | 4207 | 4177 | 4257 |
От одной или последней серии отливается один короткий сляб в пределах размеров 1650-1900 мм (в холодном состоянии) и в пределах 1675-1925 мм в горячем состоянии. Порезка: на гидравлических ножницах, а свыше 3750 мм можно резать на МГР «GEGA».
Таблица 14
№ п/п | Длина сляба в холодном состоянии для стана 2300 СТП 134-33-97 | Длина непрерывнолитой заготовки | ||
Среднее значение длины сляба, мм | Минимальное значение, мм | Максимальное значение, мм | ||
1 | 3200 ±5030 | 3244 | 3214 | 3294 |
2 | 3250 ±5030 | 3294 | 3264 | 3344 |
3 | 3300 ±5030 | 3345 | 3315 | 3395 |
4 | 3350 ±5030 | 3396 | 3366 | 3446 |
5 | 3400 ±5030 | 3446 | 3416 | 3496 |
6 | 3450 ±5030 | 3497 | 3467 | 3547 |
7 | 3500 ±5030 | 3548 | 3518 | 3598 |
8 | 3550 ±5030 | 3598 | 3568 | 3648 |
9 | 3600 ±5030 | 3649 | 3619 | 3699 |
10 | 3650 ±5030 | 3700 | 3670 | 3750 |
11 | 3700 ±5030 | 3750 | 3720 | 3800 |
12 | 3750 ±5030 | 3801 | 3771 | 3851 |
13 | 3800 ±5030 | 3852 | 3822 | 3902 |
14 | 3850 ±5030 | 3903 | 3873 | 3953 |
15 | 3900 ±5030 | 3953 | 3923 | 4003 |
16 | 3950 ±5030 | 4004 | 3974 | 4054 |
17 | 4000 ±5030 | 4055 | 4025 | 4105 |
18 | 4050 ±5030 | 4105 | 4075 | 4155 |
19 | 4100 ±5030 | 4156 | 4126 | 4206 |
20 | 4150 ±5030 | 4207 | 4177 | 4257 |
21 | 9500 ±5030 | 9630 | 9600 | 9680 |
22 | 9550 ±5030 | 9680 | 9650 | 9730 |
23 | 9600 ±5030 | 9731 | 9701 | 9781 |
24 | 9650 ±5030 | 9782 | 9752 | 9832 |
25 | 9700 ±5030 | 9832 | 9802 | 9882 |
26 | 12000 ±5030 | 12164 | 12134 | 12214 |
|
|
История развития хранилищ для нефти: Первые склады нефти появились в XVII веке. Они представляли собой землянные ямы-амбара глубиной 4…5 м...
Наброски и зарисовки растений, плодов, цветов: Освоить конструктивное построение структуры дерева через зарисовки отдельных деревьев, группы деревьев...
Типы оградительных сооружений в морском порту: По расположению оградительных сооружений в плане различают волноломы, обе оконечности...
Своеобразие русской архитектуры: Основной материал – дерево – быстрота постройки, но недолговечность и необходимость деления...
© cyberpedia.su 2017-2024 - Не является автором материалов. Исключительное право сохранено за автором текста.
Если вы не хотите, чтобы данный материал был у нас на сайте, перейдите по ссылке: Нарушение авторских прав. Мы поможем в написании вашей работы!