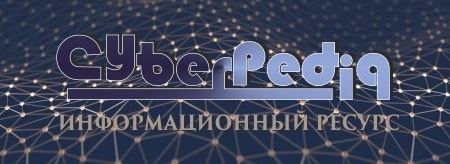
Автоматическое растормаживание колес: Тормозные устройства колес предназначены для уменьшения длины пробега и улучшения маневрирования ВС при...
Наброски и зарисовки растений, плодов, цветов: Освоить конструктивное построение структуры дерева через зарисовки отдельных деревьев, группы деревьев...
Топ:
Теоретическая значимость работы: Описание теоретической значимости (ценности) результатов исследования должно присутствовать во введении...
Устройство и оснащение процедурного кабинета: Решающая роль в обеспечении правильного лечения пациентов отводится процедурной медсестре...
Комплексной системы оценки состояния охраны труда на производственном объекте (КСОТ-П): Цели и задачи Комплексной системы оценки состояния охраны труда и определению факторов рисков по охране труда...
Интересное:
Распространение рака на другие отдаленные от желудка органы: Характерных симптомов рака желудка не существует. Выраженные симптомы появляются, когда опухоль...
Принципы управления денежными потоками: одним из методов контроля за состоянием денежной наличности является...
Уполаживание и террасирование склонов: Если глубина оврага более 5 м необходимо устройство берм. Варианты использования оврагов для градостроительных целей...
Дисциплины:
![]() |
![]() |
5.00
из
|
Заказать работу |
|
|
ОБЩИЕ ПОЛОЖЕНИЯ
1.1 Настоящая инструкция устанавливает технологию разливки стали на МНЛЗ, требования к разливаемому металлу, последовательность операций при разливке стали, последовательность и периодичность контроля процесса, метрологическое обеспечение и безопасные методы проведения работ.
1.2. Инструкция является руководством для технологического персонала цеха. Ответственность за выполнение инструкции возлагается на разливщиков стали, операторов МНЛЗ, сменных мастеров разливки, старших сменных мастеров ДСП, АКР, АКОС, МНЛЗ.
1.3. Контроль за соблюдением технологии разливки возлагается на контролеров, сменных мастеров УТК. Контроль за соблюдением и предупреждением нарушений данной инструкции возлагается на старшего мастера МНЛЗ, старшего мастера разливки, начальника цеха и его заместителей.
1.4. Технологические операции, изложенные в настоящей инструкции, учитывают требования безопасности труда обслуживающего персонала цеха.
КРАТКАЯ ТЕХНОЛОГИЧЕСКАЯ ХАРАКТЕРИСТИКА МНЛЗ
2.1. В цехе установлены две одноручьевые МНЛЗ с вертикальным кристаллизатором с плавным загибом и разгибом непрерывного слитка, без защитного покрытия медных стенок.
2.2. Металлургическая длина (от мениска металла в кристаллизаторе до последнего ролика), мм - 16945,4
в том числе:
- вертикального участка - 2485,О
- участка загиба - 16О4,8
- дугового участка - 6563,6
- участка разгиба - 3536,О
|
2.3. Базовый радиус дугового участка, мм - 6ООО,О
2.4. Размеры отливаемых слябов, мм
- толщина -17О (возможна разливка слябов 150мм)
- ширина - 1О3О ÷ 155О
- длина -32ОО ÷ 12ООО
2.5. Диапозон скоростей разливки, м/мин - 0,2 - 1,3
2.6. Рабочая скорость разливки, м/мин - 0,5 - 1,1
2.6.1. Скорость разливки, обеспечиваемая механизмами, м/мин - 0,2 - 2,0
2.7. Параметры качания кристаллизатора:
- амплитуда качания, мм +3; + 4,5; + 6,О
- частота качания, кач/мин - 4О...2ОО
2.8. Длина кристаллизатора, мм - 12ОО
2.9. Масса металла в стальковше, т:
- максимальная - 140,0
- оптимальная - 120 - 125
2.10. Масса металла в промковше, т:
- максимальная - 18,4
- оптимальная - 13,0 – 14,0
2.11. Высота подъема стальковша на поворотно-передаточном стенде (ППС), мм - 900
2.12. Высота подъема промковша на тележке, мм - 51О
2.13. Отметка разливочной площадки, мм + 1О13О
2.14. Отметка полотна рольгангов, мм + 8ОО
2.15. Шаг роликов транспортных рольгангов, мм 1ООО
2.16. Транспортная скорость рольгангов, м/с О,5
2.17. Усилие резания ножниц, т 37ОО
2.18. Порезка слябов на МНЛЗ 2 – механизм газовой резки (МГР) фирмы «ГЕГА»
2.19. Характеристика МГР:
- Длина отрезаемых слябов, мм – 3200...12000.
- Длина отрезаемого темплета, мм – 70
- Ход сдвижного стола, мм – 580
- Диаметр ролика, мм – 350
- Количество газокислородных резаков, шт - 2 (основные)
|
- 2 (пробоотборные)
- Скорость рабочего реза, мм/мин - 290 - 300
2.20. Система охлаждения:
2.20.1. Кристаллизатор - вода с петлевым охлаждением рабочих стенок через сверленные каналы
- расход воды на кристаллизатор, м3/ч - 290…360
- температура воды на входе в кристаллизатор, ºС - до 35
2.20.2. Система вторичного охлаждения (ЗВО) - вода+воздух, вода
2.20.2.1. Расход воды, м3/ч:
- минимальный - 24,12
- максимальный - 85,4
2.20.2.1. Рабочее давление, МПа - 0,9
2.20.2.2. Температура воды, ºС - до 35
2.20.2.3. Рабочее давление воздуха, МПа - 0,4
2.20.3. Система охлаждения оборудования - вода
2.20.3.1. Рабочее давление воды, МПа - 0,6
2.20.3.2. Рабочая температура воды, ºС - до 35
2.20.3.3. Расход воды, м3/ч - 240
из них:
- ролики ЗВО - 133
- ролики рольгангов - 20
- резаки МГР - 3,5
- корпуса подшипников средних опор - 80
- короб МГР - 2,0
2.20.4. Аварийное водоснабжение – 60% от общего рабочего расхода воды на систему.
2.20.4.1. Продолжительность расходования воды, мин:
- на охлаждение кристаллизатора - 30
- на охлаждения слитка - 30
- на охлаждение оборудования - 90
- рабочее давление, МПа - 0,4
2.20.5. Длина зоны вторичного охлаждения, мм:
- 1 зона - 1О35
- 2 зона - 2О7О
- 3 зона - 232О
- "подбой" - 12О
2.20.6. Среднее время подготовки МНЛЗ к работе, мин 6О
ПОДГОТОВКА МНЛЗ К РАЗЛИВКЕ МЕТАЛЛА
3.1.Выверка и настройка технологической оси МНЛЗ.
3.1.1. Выверка и настройка технологической оси МНЛЗ производится согласно данной инструкции под руководством мастера МНЛЗ силами дневного технологического персонала участка МНЛЗ и механиков участка МНЛЗ.
|
3.1.2. Перед началом проверки снимается плитный настил, кристаллизатор, очищаются от мусора скрапа роликовые секции и бункер вторичного охлаждения.
3.1.3. Проводится измерение отклонения технологической оси МНЛЗ от требуемого значения, её настройка.
3.1.4. Результаты настройки технологической оси МНЛЗ посекционно заносятся в агрегатный журнал МНЛЗ мастером МНЛЗ.
3.2. Производится контроль состояния оборудования, используемого для настройки технологической оси МНЛЗ и сменного оборудования.
3.2.1. В комплект элементов для настройки технологической оси МНЛЗ и подготовки сменного оборудования входят:
- эталон кристаллизатора (черт.5636.87.9ОО);
- стенд для настройки кристаллизатора (черт.5636.65.6ОО);
- ключ для вращения червячных редукторов кристаллизатора при настройке его узких стенок (черт.5629.87.15О);
- измеритель конусности и износа стенок кристаллизатора (черт.5613.34.25О), состоящий из линейки с уровнем и микрометрическим винтом;
- стенд для опрессовки кристаллизатора (черт.5636.65.7ОО);
- подставка для хранения и транспортировки эталона кристаллизатора (черт.5636.87.92О);
- стенды для настройки роликовых блоков (черт.5636.66.ОО и 5636.66.3ОО) для секций №3 и №4 и для секций №5 и №6 cоответственно;
- стенды для настройки роликовой секции №1 (черт.5636.65.18О) и роликовой секции №2 (черт.5636.65.3ОО);
- стенд для настройки роликовых секций №3 и №4 (черт.5636.66.100), опорных поверхностей рам указанных секций под 4-х роликовые блоки;
- стенд для настройки съемного блока (черт.5636.65.ОО);
- эталон роликовой секции №1 (черт.5636.65.15О) для выверки опорных баз под секцию №1 на съемном блоке и контроля технологической оси МНЛЗ после монтажной выверки оборудования,
- подставка (черт.5636.65.17О) предназначена для хранения эталона роликовой секции №1,
- шаблоны зоны УРС (спецификация С-5636.65.755) и шаблоны зоны вторичного охлаждения (спецификация С-5636.66.44О) предназначены для контроля полотна роликов на стыках секций при монтаже и после ремонтов (см. техописание 5636.98.6ОО ТО).
3.2.2. Эталон кристаллизатора предназначен для выставки базовых поверхностей и шаблонов на стенде настройки кристаллизатора, а также для выставки базовых поверхностей на съемном блоке. Эталон представляет собой сварную конструкцию, имитирующую базовую стенку кристаллизатора, с реперными и базовыми платиками.
|
3.2.3. Контроль базовых размеров эталонов производится через каждые шесть месяцев и заносится в специальный журнал механиком (ст. мастером) ОПТО. Эталоны являются измерительным инструментом, поэтому необходимо предохранять их от механических повреждений и тепловых деформаций. Хранение эталона необходимо производить на специальной подставке.
3.2.4. Стенд для настройки кристаллизатора должен быть настроен в соответствии с инструкцией по монтажу и эксплуатации завода-изготовителя. Периодичность проверки стенда: один раз в 6 месяцев. Данные проверки заносятся механиком (ст. мастером) в специальный журнал.
3.2.5. Стенды для настройки роликовых секций №1-№6 предназначены для обезличенной настройки опорных базовых поверхностей секций, выверки полотна роликов и настройки раствора роликов по толщине отливаемого сляба. Периодичность проверки стенда: один раз в 6 месяцев. Данные проверки заносятся механиком (ст. мастером) ОПТО в специальный журнал.
3.2.6. Шаблоны для проверки технологической оси МНЛЗ являются измерительным инструментом, поэтому их необходимо предохранять от механических повреждений и тепловых деформаций.
Контроль рабочей поверхности шаблонов производится не реже одного раза в месяц. Данные контроля заносятся механиком (ст. мастером) ОПТО в специальный журнал.
3.2.7. Измеритель для контроля и настройки узких стенок кристаллизатора проверяется дневным персоналом участка МНЛЗ один раз в сутки. Данные проверки заносятся в специальный журнал дневным оператором МНЛЗ (мастером МНЛЗ).
3.3. Подготовка оборудования к разливке.
3.3.1. После окончания разливки плавки (или серии плавок) отключается подача аргона в стык «защитная труба - стакан коллектор», в стопор – моноблок, в стык «погружной стакан – стакан дозатор». Снимаются все подводящие устройства.
Удаляются настыли с крышки и стенок промежуточного ковша подрезкой с помощью кислорода и кислородной трубки.
Остатки шлака и металла удаляются из ковша на стенде кантовки. При нормальных условиях разливки, остаток металла не должен превышать 4 - 5 т при остаточном уровне металла в промковше 200 – 300 мм. После этих операций ковш передается на участок ремонта. Время остаточного затвердевания металла в промковше 24 часа.
3.3.2. Проверка и подготовка кристаллизатора.
3.3.2.1. Устанавливаемые на МНЛЗ кристаллизаторы должны быть отремонтированы, настроены в ОПТО согласно технологической инструкции ТИ ЭС6р–9-2006 и приняты дневным оператором МНЛЗ, мастером МНЛЗ или старшим оператором МНЛЗ.
|
Результаты измерений при настройке кристаллизатора заносятся в паспорт, находящийся в месте эксплуатации кристаллизатора (ПУ – 10, ОПТО).
3.3.2.2. После окончания разливки плавки с плиты кристаллизатора удаляются остатки шлака, металла, теплоизолирующей смеси, титановой корочки «коржей» (при наличии). Запрещается сбрасывать указанный шлам в полость кристаллизатора.
3.3.2.3. При подготовке кристаллизатора к разливке производится контроль и настройка конусности узких стенок, установка базовой стенки относительно первой секции и проверка состояния рабочей полости.
3.3.2.4. Уклон узких стенок кристаллизатора проверяют измерителем конусности (черт.5613.34.25О), который устанавливают на верхний торец узкой стенки перед каждой серией плавок. Цена деления уровня измерителя конусности 0,05 мм/м.
Конусность кристаллизатора (для конусомера с расстоянием между щупами 1000мм) рассчитывается по формуле:
К(мм) = Lв - Lн , где
2,4
Lв - ширина кристаллизатора по верху, мм
Lн - ширина кристаллизатора по низу, мм
По центру широкой стенки кристаллизатора по большому радиусу и малому радиусу должна быть выполнена насечка внизу и вверху (по углу со стороны рабочей полости). От данных насечек измеряется расстояние до узких стенок вверху и внизу.
Отклонение между половинами широких граней внизу и вверху не должно быть более 0,2 мм.
Внутренние размеры кристаллизатора и наружные размеры головки затравки в зависимости от марки стали приведены таблице Приложения 1.
3.3.2.5. Установка кристаллизатора относительно базовой стенки МНЛЗ контролируется с помощью шаблона 0-1 перед каждой плавкой. Шаблон устанавливается на чистый верхний торец широкой стенки кристаллизатора на расстоянии 100-200 мм от узких стенок. Неприлегание шаблона не допускается. Шаблон должен касаться двух верхних роликов секции, зазор между роликами и шаблоном не допускается.
3.3.2.6. Кристаллизатор не допускается к эксплуатации и подлежит отправке на ремонт в следующих случаях:
- наличие выбоин, царапин, задиров, вмятин глубиной более 1,5 мм, и поджогах на медных стенках (продольные следы поджога медных стенок говорят о засорении охлаждающих каналов)
- при выработке низа узких стенок более, чем на 1,5 мм на сторону или широких стенок более, чем на 1,0 мм на сторону.
- зазоры в стыках широких и узких стенок превышают 0,2 мм (при зазорах не более 0,2 мм может производится подчеканка зазора) зазор проверяется щупом
- течь воды в рабочую полость кристаллизатора
- коробление рабочих плит более, чем на 0,3 мм на расстоянии 400 мм от верха
- на расстоянии 400 мм от верха задиры и раковины на рабочей поверхности кристаллизатора не должны превышать 0,5 мм
- при появлении угловых продольных трещин на заготовках предыдущей плавки
- при снижении расхода воды на охлаждение кристаллизатора до 240 м3/ч при давлении в сети 0,6 – 0,75 МПа (6,0 – 7,5 кг/см2)
- если перепад температуры воды в процессе разливки на выходе превышает 120С
- выход из строя редукторов перемещения торцевых стенок
3.3.2.7. Со стенок кристаллизатора убираются остатки металла, шлака. Мелкие дефекты зачищаются.
3.3.2.8. Решение о замене кристаллизатора принимает мастер разливки МНЛЗ.
3.3.2.9. Выставку кристаллизатора относительно первой секции проверяют после каждой плавки (или окончании серии плавок).
3.3.2.10. Воздух из каналов охлаждения кристаллизатора должен быть спущен. Течь воды в полость кристаллизатора из-под пробок не допускается. Проверка производится при рабочем давлении и расходе воды.
3.3.2.11. С помощью контрольного груза проверяется правильность показаний датчика измерения усилия вытягивания.
3.3.3. Проверка системы вторичного охлаждения.
3.3.3.1. Проверить визуально установку коллекторов и форсунок относительно роликовых секций. Распыляемые факелы водовоздушной (водяной) смеси должны лежать в плоскости, перпендикулярной оси МНЛЗ.
3.3.3.2. Оператор проверяет работу форсунок «подбоя» и системы вторичного охлаждения. Работа форсунок каждой секции и на каждую грань слитка проверяется отдельно при заданных режимах охлаждения.
Расходы воды приведены в Приложении 2.
Форсунки должны стоять перпендикулярно к граням слитка. Факел распыления должен равномерно распределяться по граням и не перекрываться роликами секций или защитными листами, уложенными на роликовые секции. Работа форсунок «подбоя» и первого ряда между кристаллизатором и роликовой секцией должна быть проверена. Факел форсунок «подбоя» должен быть параллелен роликам, и подавать воду строго посередине между роликами и нижним срезом стенок кристаллизатора. Форсунки считаются вышедшими из строя, если нельзя организовать факел (контролируется визуально).
Проверяется исправное состояние форсунок после обнаружения неравномерности температуры поверхности слитка по сторонам.
3.3.3.3. Во всех 1-3 зонах и «подбое» применяется водовоздушная смесь (или "подбое" и 1 зоне применяется вода) согласно заданному режиму в зависимости от марки стали и скорости разливки.
3.3.3.4. Проверить правильность установок в АСУ "ЗВО" в зависимости от скорости разливки.
3.3.4. Проверка состояния затравки.
3.3.4.1. Головка затравки должна быть очищена от остатков металла, не иметь трещин и заусенцев.
3.3.4.2. Надувные элементы затравки проверяются при давлении воздуха не менее
О,4 МПа (4 кгс/см.2). Падение давления при этом не должно превышать О,О2 МПа
(О,2 кг/см2) в течение 3О минут после прекращения подачи воздуха.
3.3.4.3. Проверить правильность положения оси крепления головки затравки. Лыска на оси должна быть расположена со стороны большого радиуса.
3.3.4.4. Проверить установку накладок со стороны малого радиуса затравки.
3.3.5. Перед заведением затравки в кристаллизатор необходимо произвести комплексное опробование МНЛЗ в присутствии дежурного персонала (механики, гидравлики, электрики, энергетики, КИП, АСУТП).
3.3.5.1. В процессе опробования проверить состояние поддерживающей системы МНЛЗ:
- соответствие показаний скорости разливки реальной скорости движения затравки
- состояние поверхности роликов (отсутствие вмятин и выбоин);
- отсутствие скрапин и других сторонних предметов между роликами;
- вращение роликов по секциям (ролики должны легко вращаться и не
иметь люфтов);
- наличие протоков воды на охлаждение роликов.
В случае обнаружения заклинивания роликов, появления люфтов, расфиксации осей и невозможности ликвидации этого на месте, секции подлежат замене.
3.3.5.2. Проверить плавность движения и отсутствие стука при качании кристаллизатора, убедиться в правильности измерения частоты качания.
3.3.5.3. Проверить функционирование устройства отделения затравки в автоматическом режиме путем прогона затравки через роликовые секции МНЛЗ или перекрытия светового луча перед фотодатчиком. После проверки необходимо вновь включить устройство отделения затравки в режим автоматического функционирования.
3.3.5.4. Проверить на МНЛЗ 1 работу гидравлических ножниц и АСУ "РЕЗ":
- обратить внимание на отсутствие "зависания" и "самохода" нижнего суппорта;
- зазор между упорами верхнего и нижнего суппортов в верхнем положении последнего должен быть не менее 3О-4О мм;
- гайки крепления ножей должны быть обтянуты;
- на режущих кромках не допускается наличие трещин и выбоин;
- перекрытие ножей должно составлять 1О-2О мм;
- проверить функционирование системы охлаждения ножей.
3.3.5.5. Проверить на МНЛЗ 2 работу машины газовой резки (МГР) фирмы «ГЕГА»:
После окончания разливки:
- закрыть запорные вентили газовых сред и воды.
- нажать кнопку «MASHINE OFF» (машина выключена) на ПУ МГР. При этом прерываются все рабочие функции МГР и закрываются все клапаны. Управляющее напряжение можно отключить нажатием кнопки аварийного выключения «EMERGECY OFF».
- изъять ключ-бирку на ПУ МГР.
- после окончания разливки на МНЛЗ и автоматической (ручной) порезки слитка последней плавки серии на мерные заготовки оператор МГР должен остановить работу МНЛЗ и передать управление на ПУ-10 и известить оператора ПУ-10 об окончании порезки и начале профилактических работ. Оператор ПУ-10 ключом-биркой полностью отключает работу МНЛЗ.
- оператору резки МГР осмотреть ролики 6-ой секции, транспортного рольганга, сдвижного стола, измерительного ролика. Все ролики должны вращаться свободно. При обнаружении невращающихся роликов, имеющих поломку: трещины, перекосы, большой износ (более 6 мм на диаметр проверяется визуально), вращающиеся бандажи, задиры, приглашается мастер (старший мастер МНЛЗ) и ставится в известность для дальнейшего принятия мер по устранению неисправности.
- скардовины с поверхности роликов очищаются.
- из-под рольганга сдвижного стола на тележке рольганга (при включенной системе уборки шлама) убирается короб со шламом, скардовиной, мелкой обрезью, Уборка короба со шлаком с тележки и установка пустого короба производится с помощью крана №22. Тележка с пустым коробом закатывается под сдвижной стол МГР.
- проверяется состояние шлангов и трубопроводов, подводящих газ и кислород к резакам.
3.3.5.6. Подготовка МГР к работе и работа производится согласно технологической инструкции ТИ ЭС6р – 8 – 06.
3.3.5.7. Перед проверкой агрегатов МНЛЗ оператор ПУ – 10 устанавливает ключ-бирку в рабочее положение.
3.3.5.8. По мере проверки агрегатов МНЛЗ дежурные соответствующих ремонтных служб делают запись в журналах на постах о готовности к разливке с росписью и указанием номера бригады, ФИО.
3.3.5.9. После проверки поставить ключи управления в нулевое положение,
ключ-бирки извлечь.
3.3.6. Заведение затравки.
Осуществляется после полной готовности оборудования, систем КИПиА, АСУТП с записью в технологических журналах дежурного персонала с росписью.
3.3.6.1. Установить на кристаллизатор защитный экран.
3.3.6.2. Проверенную и подготовленную затравку завести в полость кристаллизатора с помощью машины для заведения затравки. Высота головки, выступающей над срезом кристаллизатора, должна составлять не менее 1ООО мм.
3.3.6.3. С помощью устройства для наддува затравки довести давление воздуха в камерах до О,5 МПа (5кгс/см.2), после чего отвести машину для заведения затравки. Рабочее давление затравки 0,45-0,60 МПа (4,5-6,0 кгс/см2).
3.3.6.4. Не извлекая устройства для наддува, с помощью вращения роликовых секций, отпустить затравку на расстояние 8ОО мм от среза кристаллизатора до верхней площадки торца головки затравки для кристаллизатора Н = 1200 мм и на 650 мм - для кристаллизатора Н = 950 мм. Затравку на наддуве оставить до установки стальковша с плавкой на стенд. Извлекать устройство для наддува при нахождении стальковша в резервной позиции.
3.3.6.5. После установки затравки в исходное положение выполнить следующие операции:
- убрать защитный экран;
- зачеканить зазор между затравкой и стенками кристаллизатора асбестовым шнуром общего назначения марки ШАОН, ШАМ (ГОСТ 1779), при этом разрешается для этого применять асбестовые шнуры марок ШАП (шнур асбестовый пуховый), ШАМ (шнур асбестовый магнезиальный - ГОСТ 1779). Диаметр асбестовых шнуров марок ШАОН и ШАМ должен быть в пределах 20-25 мм. Шнур асбестовый пуховый марки ШАП применяется в состоянии поставки (ГОСТ 1779 диаметр шнура не оговаривает). При зачеканивании выступание или заглубление асбестового материала в зазоре не должны быть более 3 мм. Асбестовый материал используется сухим после естественной сушки.
- промазать стыки широких и узких граней кристаллизатора алебастром;
- на головку затравки, с целью исключения ее размыва и перегрева, укладывать листовую обрезь толщиной слоя 8-1О мм с перекрытием нижних зазоров, при этом зазор между листовой обрезью и стенкой кристаллизатора должен быть 2-3 мм. Отверстие для наддува забивается асбестом и укрывается холодильником толщиной 8-1О мм;
- забивка зазора между стенкой кристаллизатора и головкой затравки контролируется мастером разливки МНЛЗ или старшим оператором, а выборочно - старшим мастером,
- общая масса подготовленных холодильников составляет 1О-15 кг, в зависимости от сечения кристаллизатора, из них 4...5 кг холодильников укладывается на верхний торец затравки, а 6-9 кг холодильников отдается в процессе заполнения металлом кристаллизатора, при этом 6-.9 кг холодильников состоит из мелкой обезжиренной стальной обрези (сечки) или отходов спектральных проб. Запрещается использовать влажные или окисленные холодильники. Холодильники перед укладкой на головку затравки должны быть просушены в специальной таре на стенде сушки смеси.
3.3.7. На разливочной площадке подготавливают аварийные емкости для слива остатков металла и шлака из промежуточного ковша. Все емкости должны быть сухими и очищенными от шлака и скрапа.
3.3.8. Проверяется наличие на рабочей площадке рабочего инструмента в необходимом количестве (заморозки, ломики, крючки, лопаты), кислородные трубки для промыва стакана, подрезки скардовин, а также кислородные шланги и шланги для подачи аргона к стыкам металлопровода.
3.3.9. Для разливки коррозионностойких, кремнемарганцовистых углеродистых марок стали подготавливаются огнеупорные изделия различных фирм – изготовителей, выполненные в соответствии с базовыми чертежами ИТЦ ОАО «ЧМК». Фирмы изготовители поставляют огнеупорные изделия выполненные по своим чертежам на основании базовых чертежей ИТЦ ОАО «ЧМК» и после прохождения опытно-промышленных испытаний поставляемых изделий.
Таблица 3.3.9
№ п.п. | Наименование изделия | Базовый чертеж изделия | Место установки | Разливаемые группы марок стали |
1. | Стакан–коллектор | 62-07.08.27-1 | Шиберный затвор стальковша | Все |
2. | Труба защитная | 62-07.08.27-2 | Стальковш (в стык со стаканом-коллектором | Все |
3. | Стопор–моноблок | 62-07.08.27-3 | Промковш (в стык со стаканом-дозатором) | Все |
4. | Стержень стопора–моноблока | 62-07.08.27-3.1 | Промковш (для установки в стопор и вилку стопорного механизма) | Все группы марок стали |
5. | Стакан–дозатор | 62-07.08.27-4 | Промковш (в стык со стопором и погружным стаканом) | Все группы марок стали |
6. | Стакан погружной | 62-07.08.27-5 | Кристаллизатор (в стык со стаканом дозатором) | Для разливки коррозионно-стойких марок стали |
7. | Стакан погружной | 62-07.08.27-6 | Кристаллизатор (в стык со стаканом дозатором) | Для разливки кремнемарганцевистых, углеродистых марок стали с Mn более 0,8 % |
8. | Труба защитная ТКСБ – 82.01 | 202.М643.00.СБ ОАО «Динур» | Стальковш(в стык со стаканом-коллектором) | Для разливки углеродистых марок стали с Mn не более 0,8 % |
9. | Стакан №118 (погружной) кварцевая керамика | 202.М641 ОАО «Динур» | Кристаллизатор (в стык к стакану-дозатору) | Для разливки углеродистых марок стали с Mn не более 0,8% |
10. | Уплотнительная вставка ДП47Р–19 ЧМК | Р–047.00 ЗАО «РМК» | Стакан № 118 (в воронку стакана для уплотнения) | Для разливки всех марок стали без продувки Ar |
11. | Стакан погружной №118.01 | 202.М.649.00.СБ с фетром ОАО «Динур» | Кристаллизатор (в стык со стаканом дозатором с уплотнительным фетром) | Для разливки углеродистых марок стали с Mn не более 0,8 % |
12. | Уплотнительная вставка АК52Р–194 ЧМК | Р – 052.00 ЗАО «РМК» | Труба защитная ТКСБ – 82.01 и трубы различных фирм | Для разливки всех марок стали без продувки аргоном |
3.3.9.1. Для системы быстрой смены погружного стакана “на лету” используются следующие огнеупорные изделия и крепежные элементы:
Таблица 3.3.9.1.
№ п.п | Наименование изделия и крепежных элементов | Базовый чертеж изделия | Место установки | Разливаемые группы марок стали |
1 | 2 | 3 | 4 | 5 |
1. | Стопор моноблок | RB-1942-0101RHI | Промковш (в стык со стаканом дозатором) | Все |
2. | Стержень стопора-моноблока | 62-07.08.27-3.1 | Промковш (для установки в стопор и вилку стопорного механизма) | Все |
3. | Стакан дозатор | NC-0048-0101 RHI | Промковш (в стык со стопором моноблоком и погружным стаканом) | Все |
4. | Погружной стакан | МТ-1086-0101 | Кристаллизатор (в стык со стаканом дозатором) | Кремнемарганцевистые, углеродистые марки стали с Mn более 0,8 % |
5. | Погружной стакан | МТ-2562-0101 | Кристаллизатор (в стык со стаканом дозатором) | Коррозионностойкие марки стали |
6. | Погружной стакан | МТ-1087-0101 | Кристаллизатор (в стык со стаканом дозатором) | Кремнемарганцевистые, углеродистых марки стали |
7. | Заглушка | TD-0005-0301 | В качестве шиберной плиты в системе для закрытия ручья | Все |
8. | Кольцо металлическое | 9036668 RING 315/210x25 RHI | В качестве подвижного фланца одевается на стакан дозатор | Все |
9. | Кольцо упорное Dвн.д.б.=52 мм | STW00002 RHI | Одевается на стержень стопора моноблока под вилку | Все |
10. | Кольцо упорное подвижное Dвн.д.б.=52 мм | STW00003 RHI | Одевается на стержень стопора моноблока под вилку | Все |
11. | Кольцо (шайба) | STW00003 RHI | Одевается на стержень на вилку Изменить внутр. диаметр вмято D=42 на D=52 мм | Все |
3.3.9.2. Используемые огнеупорные изделия различных фирм по назначению:
Наимено-вание изделия | Номера чертежей фирм | ||||
ОАО «Динур» | Далмонд | Staverma | Vesuvius | Майертон | |
Коррозионностойкие марки стали | |||||
Труба защитная | 129.GM.CHMK.TUSH.01 | S2809 | BD00001 | ||
Стакан дозатор | 202.И.551СБ | 088.GM.CHMK.NOT.04 | S2804 | BQ04045 | TN0-0305- 02.00 |
Стопор-моноблок | 202.И.547СБ | 085.GM.CHMK.STOM.01 | S2840 | BP00001 | |
Стакан погружной | 202.И.505.00 СБ | 31.GM.CHMK.SUN.01 | S2806Z | SEN-0305-07.00 | |
Стакан коллектор | S2803 | КС14458 | CN-305-01.00 CN-305-01.01 (D=60 и 70) | ||
Кремнемарганцевистые, углеродистые марки стали (Mn более 0,8 %) | |||||
Стакан коллектор | S2803 | KC14458 | CN-305-01.00 CN-305-01.01 | ||
Труба защитная | 129.GM.CHMK.TUSH.01 | S2809 | BD00001 | ||
Стопор-моноблок | 202.И547СБ | 085.GM.CHMK.STOM.01 | S2840 | BP00001 | |
Стакан погружной | 202.И.506.00 СБ | 126.GM.CHMK.SUN.01 | S3228Z | BL02651 | SEN-0305-06.00 |
Стакан дозатор | 202.И.551СБ | 088.GM.CHMK.NOT.04 | S2804 | BQ04045 | TN-0305-02.00 |
Углеродистые марки стали с Mn более 0,8 % | |||||
Стакан коллектор | 1 29.GM.CHMK.TUSH.01 | S2803 | KC14458 | CN-305-01.00 CN-305-01.01 | |
Труба защитная Стопор-моноблок Стакан дозатор Стакан погружной (кварцевы) | ТКСБ-82.01 202.И547СБ 202.И.551СБ №118 202М641 №118.01 202.М.649.00 СБ | 085.GM.CHMK.STOM.01 088.GM.CHMK.NOT.04 | S2809 S2840 S2804 | BD00001 BP00001 BQ04045 | TN-0305-02.00 |
3.3.1О. Для разливки стали готовится шлакообразующая смесь (ШОС) в соответствии с технологической инструкцией ВТИ -134-СТ-ПС5-01-96 с требуемым химическим составом и содержанием влаги не более О,5%.
Марки шлакообразующих смесей подразделяются по назначению:
ШОС 51 – покровная теплоизолирующая ассимилирующая шлаковая ШОС дается в промковш при разливке углеродистых, кремнемарганцевистых и коррозионностойких марок стали.
ШОС 50К – теплоизолирующая, ассимилирующая, смазывающая ШОС дается в кристаллизатор при разливке углеродистых, кремнемарганцевистых и марок стали.
ШОС 55Д - теплоизолирующая, ассимилирующая, смазывающая ШОС дается в кристаллизатор при разливке коррозионностойких марок стали аустенитного класса и в промковш в район стопора - моноблока (при необходимости разжижения шлака – в промковш до перегородки).
ШОС 56Д - теплоизолирующая, ассимилирующая, смазывающая ШОС с более высокой температурой плавления (чем ШОС 55Д) дается в кристаллизатор при разливке коррозионностойких марок стали ферритного класса, а также дается в промковш стопора - моноблока (при необходимости разжижения шлака – в промковш до перегородки для разжижения шлака).
Подается на участок из ЦПС-5 в специальных крытых контейнерах, а затем для использования в подогретом виде пересыпается на специальном стенде в мульды.
Импортная ШОС используется в состоянии поставки без предварительной сушки.
3.3.11. Шлакообразующая смесь предварительно нагревается в специальной таре (двухзонной мульде) над газовыми горелками до достижения влажности не более О,5%. При нагреве ШОС ее необходимо периодически перемешивать (через 20 - 30 мин) для исключения конденсации влаги в верхних слоях ШОС и выгорания углерода в боковых и донной части. Перед разливкой температура ШОС должна быть 60 – 1000С (не терпит рука), а из мульды в 5-ти точках (углы и середина) под наблюдением контролера УТК отбирается 100-200 г ШОС, усредняется перемешиванием и передается контролеру УТК для отправки в хим. лабораторию на анализ влажности. Для анализа влажности запрещается использовать бумажную тару. Рекомендуется отправлять в стеклянной или целлофановой таре.
3.3.12. Шлаковая смесь в каждой мульде должна иметь маркировку: № партии ШОС, марку и дату изготовления. Эти данные списываются с бирки контейнера из ЦПС-5. Данные по влажности заносятся в паспорт плавки. Категорически запрещается перемешивание ШОС разных марок.
3.3.12.1. ЭСПЦ-6 принимает в работу ШОС только с известным химическим составом, соответствующим требованиям ТИ-134-СТ-ПС5-01-96. Соответствие химическому составу устанавливает УТК ЦПС-5 и передает данные по каждой партии ШОС в УТК ЭСПЦ-6. Пробы на химический анализ от каждой партии ШОС отправляет в химическую лабораторию УТК ЦПС-5.
3.3.13. На главном посту управления проверяется готовность электрооборудования механизма качания кристаллизатора, приводов вращения роликовых секций. После проверки ключи ставятся в нулевое положение.
3.3.14. Проверяется функционирование тележек промежуточных ковшей и устройств для разогрева, а также передаточно-поворотного стенда. Обратить особое внимание на срабатывание сигнализации и блокировок.
3.3.15. На тележку промковша подается подготовленный промежуточный ковш и ставится на стенд для разогрева промежуточных ковшей. Подготовку и разогрев промковшей выполняют в соответствии с технологической инструкцией ТИ ЭС6-11-99. Нагрев рабочей поверхности футеровки промковша осуществляется до температуры 11ОО-12ОО оС.
Для полного прогрева промковша до рабочего режима нагрев промковша после сушки осуществляется на форсированном режиме в течении 2,5-3 часов. Если ковш уже разогрет, а разливка по какой то причине откладывается, то необходимо снизить интенсивность работы горелок до среднего уровня. При длительном разогреве промковша (более 24 часов) промковш на разливку не отдается и меняется на другой.
3.3.16. Готовность ковша к разливке определяется старшим разливщиком совместно с дежурным слесарем КИПиА. Последний производит измерение температуры футеровки промковша, которая фиксируется контролером ОТК в плавильной карте.
3.3.17. Ввести исходные данные в АСУ "Оперативное диспетчерское управление" ("ОДУ"):
- № бригады;
- фамилию сменного мастера разливки, № МНЛЗ;
- марка стали;
- сечение слитка;
- раскрой слитка;
- № стальковша;
- № промковша;
- стойкость кристаллизатора;
- стойкость промковша;
- № плавк
|
|
Биохимия спиртового брожения: Основу технологии получения пива составляет спиртовое брожение, - при котором сахар превращается...
Кормораздатчик мобильный электрифицированный: схема и процесс работы устройства...
Общие условия выбора системы дренажа: Система дренажа выбирается в зависимости от характера защищаемого...
Механическое удерживание земляных масс: Механическое удерживание земляных масс на склоне обеспечивают контрфорсными сооружениями различных конструкций...
© cyberpedia.su 2017-2024 - Не является автором материалов. Исключительное право сохранено за автором текста.
Если вы не хотите, чтобы данный материал был у нас на сайте, перейдите по ссылке: Нарушение авторских прав. Мы поможем в написании вашей работы!