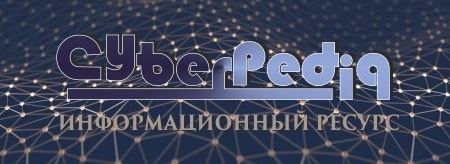
Механическое удерживание земляных масс: Механическое удерживание земляных масс на склоне обеспечивают контрфорсными сооружениями различных конструкций...
Индивидуальные и групповые автопоилки: для животных. Схемы и конструкции...
Топ:
Организация стока поверхностных вод: Наибольшее количество влаги на земном шаре испаряется с поверхности морей и океанов...
Теоретическая значимость работы: Описание теоретической значимости (ценности) результатов исследования должно присутствовать во введении...
Определение места расположения распределительного центра: Фирма реализует продукцию на рынках сбыта и имеет постоянных поставщиков в разных регионах. Увеличение объема продаж...
Интересное:
Мероприятия для защиты от морозного пучения грунтов: Инженерная защита от морозного (криогенного) пучения грунтов необходима для легких малоэтажных зданий и других сооружений...
Берегоукрепление оползневых склонов: На прибрежных склонах основной причиной развития оползневых процессов является подмыв водами рек естественных склонов...
Что нужно делать при лейкемии: Прежде всего, необходимо выяснить, не страдаете ли вы каким-либо душевным недугом...
Дисциплины:
![]() |
![]() |
5.00
из
|
Заказать работу |
|
|
Цель работы
Изучение влияния на срок службы станка характеристик обрабатываемого материала и применяемого инструмента. Расчёт длительности ремонтного цикла металлорежущих станков.
Общие положения
Исходя из основных принципов Единой системы управления качеством продукции, жизненный цикл технологического оборудования машиностроительных предприятий состоит из следующих основных стадий:
1) исследование;
2) проектирование;
3) изготовление;
4) реализация;
5) эксплуатация;
6) утилизация;
При долгосрочном планировании производственной деятельности машиностроительных предприятий необходимо знание о возможности бесперебойной работы металлорежущего оборудования предприятия. Для обеспечения максимальной вероятности безостановочной работы оборудования, станки должны проходить техническое обслуживание и ремонт после их установки и сдачи в эксплуатацию. Таким образом, стадия «эксплуатация» жизненного цикла металлорежущих станков состоит из следующих основных этапов (обозначения использовать при построении структурной модели стадии «эксплуатация» станков):
ПН – пусконаладочные и монтажные работы;
И – период использования станка по назначению;
О – осмотр;
Т – текущий ремонт;
СР – средний ремонт;
КР – капитальный ремонт;
РЦ – ремонтный цикл, объединяющий промежуток времени от ПН до КР.
Определение этапов стадии «эксплуатация»:
Ремонтный цикл – повторяющаяся совокупность различных видов ремонта, выполняемые через равные промежутки оперативного времени работы оборудования.
Структура ремонтного цикла – перечень ремонтов, расположенных в последовательности их выполнения.
|
Продолжительность ремонтного цикла – время между двумя капитальными ремонтами.
Осмотр – операция технического обслуживания, выполняемая с целью проверки всех узлов оборудования и накопления информации об износе деталей, необходимой для подготовки предстоящих ремонтов.
Текущий ремонт – операция, выполняемая для обеспечения или восстановления работоспособности оборудования, состоящая в замене или восстановлении отдельных частей.
Средний ремонт – операция, выполняемая для восстановления исправности и частичного восстановления ресурса оборудования с заменой или восстановлением составных частей ограниченной номенклатуры.
Капитальный ремонт – операция, выполняемая для восстановления исправности и полного либо близкого к полному восстановлению ресурса оборудования.
Эмпирическая формула расчёта продолжительности оперативного времени ремонтного цикла (часы, отработанные оборудованием):
ТРЦ = 16 800∙КОМКМИКТСККСКВКД,
где значения коэффициентов даны в таблицах 1, 2, 3, 4.
Формулы расчёта продолжительности оперативного времени межремонтного периода (часы, отработанные оборудованием):
а) для класса точности Н:
ТМР = ТРЦ : 6;
б) для классов точности П, В, А, С:
ТМР = ТРЦ : 9,
где N = 6 (N = 9) – количество межремонтных периодов в ремонтном цикле.
Структура части стадии «эксплуатация», равной ТРЦ, дана на рисунке 1. Эту часть разбивают на равные промежутки с периодом, равным ТМР. Затем по полученным интервалам размещают интервалы И – О (см. таблицу 1). После этого построение указанной части структуры считают законченным.
Таблица 1 - Структурные модели стадии «эксплуатация» жизненного цикла
металлорежущего оборудования
|
Класс точности | Категория массы (тонна) | Структура стадии «эксплуатация» |
Н
| 10 | ПН-И-О-И-Т-И-О-И-Т-И-О-И-СР-И- -О-И-Т-И-О-И-Т-И-О-И-КР |
Св. 10 до 100 | ПН-И-О-И-Т-И-О-И-Т-И-О-И-Т-И- -О-И-Т-И-О-И-Т-И-О-И-КР | |
Св. 100 | ПН-И-О-И-Т-И-О-И-Т-И-О-И-Т-И-О-И- -Т-И-О-И-Т-И-О-И-Т-И-О-И-КР | |
П, В, А, С
| 10 | ПН-И-О-И-Т-И-О-И-Т-И-О-И-СР-И-О-И- -Т-И-О-И-Т-И-О-И-СР-И-О-И-Т-И-О-И-Т- -И-О-И-КР |
Св. 10 до 100 | ПН-И-О-И-Т-И-О-И-Т-И-О-И-Т-И-О-И- -Т-И-О-И-Т-И-О-И-Т-И-О-И-Т-И-О-И-Т- -И-О-И-КР | |
Св. 100 | ПН-И-О-И-Т-И-О-И-Т-И-О-И-Т-И-О-И- -Т-И-О-И-Т-И-О-И-Т-И-О-И-Т-И-О-И-Т- -И-О-И-Т-И-О-И-КР |
Таблица 2 - Коэффициент КД
Год выпуска оборудования | Значение коэффициента |
До 1975 С 1976 по 1980 С 1981 по 1998 С 1998 | 0,8 0,9 1,0 1,2 |
Таблица 3 - Значения коэффициентов, входящих в эмпирические
формулы для определения продолжительности ремонтного цикла и
межремонтных периодов
Коэффициент | Определяемый параметр | Значения коэффициента |
КОМ КМИ КТС ККС | Обрабатываемый материал Сталь конструкционная Прочие материалы Материал применяемого инструмента Металл Абразив Класс точности Н П В,А,С Категория массы До 10 т Св. 10 до 100 т Св. 100 т | 1,0 0,75 1,0 0,8 1,0 1,5 2,0 1,0 1,35 1,7 |
Таблица 4 - Коэффициент КВ
Возраст станка | Класс точности станка | Порядковый номер планируемого ремонтного цикла | Значение коэффициента |
До 10 лет | Н, П В, А, С | 1-й и 2-й 1-й | 1,0 |
Св. 10 лет
| Н П, В, А, С | 2-й и 3-й 2-й | 0,9 |
Н П, В, А, С | 4-й 3-й | 0,8 | |
Н П, В, А, С | 5-й и более 4-й и более | 0,7 |
Цикл: ПН -…-КР – периодическая величина стадии «эксплуатация» с периодом ТРЦ.
Рисунок 1 - Схема разделения ремонтного цикла на межремонтные периоды
Таблица 5 - Значения стабильной ремонтосложности RМ наиболее
распространённого металлорежущего оборудования
№ модели |
Модель
| Класс точности |
Масса, кг
| Наибольший диаметр обрабатываемой детали, мм | Расстояние между центрами |
Ремонтосложность
| ||
Механики RММ | Электрич. RМЭ | |||||||
1 | 1К62 | Н | 2 160 2 200 2 400 | 400 | 710 1000 1400 | 10,5 | 9,0 | |
2 | 16К20 | Н | 2 740 2 910 3 130 | 400 | 710 1000 1400 | 12,0 | 9,0 | |
3 | 1М63Б | Н | 5 490 | 630 | 2800 | 14,0 | 11,0 | |
4 | 1М64 | Н | 11 390 | 800 | 2800 | 16,0 | 12,0 | |
5 | 1М65 | Н | 12 480 15 630 | 1000 | 2800 5000 | 16,5 17,0 | 13,0 | |
6 | 3А151 | П В | 3 800 | 200 | - | 12,0 14,5 | 25 | |
7 | 3Б722 | П В | 6 950 | 320Х1000* | - | 21,5 26 | 18 | |
8 | 3А227 | П В | 2 700 | 100 | - | 15 17,5 | 16 | |
9 | 53А50Н | Н | 9 650 | 500 | - | 23 | 32 | |
10 | 6Р12 | Н | 3 065 | 320Х1250* | - | 11,0 | 11,0 | |
11 | 6Р81 | Н | 2 280 | 250Х1000* | - | 9,0 | 7,5 | |
12 | 2А135 | Н | 1 300 | 35** | - | 4,5 | 5,5 | |
13 | 2М55 | Н | 4 370 | 50** | - | 20 | 16 | |
* Обозначение размера стола станка.
** Наибольший диаметр сверления. |
Таблица 6 - Трудоёмкость ремонта и осмотров металлорежущего
оборудования (механическая часть)
Вид работ | Капитал. ремонт | Средний ремонт | Текущий ремонт | Плановый осмотр | |
Перед внутрицикловым ремонтом | Перед капитальным ремонтом | ||||
Норма времени, час на 1RММ | |||||
Станочные | 14,0 | 3,0 | 2,0 | 0,1 | 0,1 |
Слесарные | 36,0 | 6,0 | 4,0 | 0,75 | 1,0 |
Итого | 50,0 | 9,0 | 6,0 | 0,85 | 1,1 |
Таблица 7 - Трудоёмкость ремонта и осмотров металлорежущего
оборудования (электрическая часть)
Вид работ | Капитал. ремонт | Средний ремонт | Текущий ремонт | Плановый осмотр | |
Перед внутрицикловым ремонтом | Перед капитальным ремонтом | ||||
Норма времени, час на 1RМЭ | |||||
Станочные | 2,5 | - | 0,3 | - | - |
Электросле-сарные и прочие | 10,0 | - | 1,2 | 0,2 | 0,25 |
Итого | 12,5 | - | 1,5 | 0,2 | 0,25 |
Ремонт механической и электрической частей станка может быть совмещён во времени. |
Трудоёмкость одного из видов ремонта или технического обслуживания:
Тi = (СТЭi + СЛЭi)·RМЭ + (СТМi + СЛМi)·RММ < НП,
где i – наименование этапа (О; Т; СР; КР);
RМЭ; RММ – ремонтосложность электрической (литера Э) или механической (литера М) частей оборудования (см. таблицу 5)
ТЭi … СЛМi – трудоёмкость станочных (литера Т) и слесарных работ (литера Л) при ремонте электрической (Э) или механической (М) частей оборудования (см. таблицы 6 и 7);
НП – норма времени на простой оборудования из-за ремонта (см. таблицу 8).
Таблица 8 - Нормативы простоя оборудования (сутки) на одну
ремонтную единицу (1RМ) из-за ремонта при различной сменности
работы ремонтных бригад
Ремонтные работы и работы по техническому уходу |
Нормативы простоя НП металлорежущего оборудования на одну ремонтную единицу при работе ремонтной бригады
| |||
В одну смену | В две смены | В три смены | ||
Проверка на точность как самостоятельная операция Текущий ремонт Средний ремонт Капитальный ремонт | 0,1 0,25 0,6 1,0 | 0,05 0,14 0,33 0,54 | 0,04 0,1 0,25 0,41 |
Производя вычисление по всем видам ремонта и техобслуживания, находим время, затраченное на ремонт и техническое обслуживание в течение одного ремонтного цикла:
ΣТР = 5ТО + 4ТТ + ТСР + ТОКР + ТКР.
Время, в течение которого оборудование можно использовать по назначению:
ТИ = ТРЦ – ΣТР.
Время, затрачиваемое на пусконаладочные работы, можно определить по приближённой формуле:
ТПН ≈ 0,5ТТ + ТФ,
где ТФ = 0,45m + 3 – время строительства фундамента, сут.;
m – вес станка, т.
В случае установки станка на специальные опоры:
ТПН ≈ 0,5ТТ.
Порядок выполнения работы
Примеры вариантов заданий даны в приложении А.
Вычислить длительность ремонтного цикла. Затем, прибавляя время на пусконаладочные работы, определить продолжительность первого ремонтного цикла стадии «эксплуатация» оборудования.
При нахождении времени ТИ длительности этапа И из ТРЦ исключаем время, найденное исходя из трудоёмкости всех осмотров, текущих ремонтов, среднего и капитального ремонтов.
Построение структуры стадии «эксплуатация» станков. Структура периодичная, с периодом равным ТРЦ. Построить J-й ремонтный цикл (J – номер цикла в соответствии с вариантом задания).
Содержание отчёта
1.4.1 Название работы.
1.4.2 Содержание задания.
1.4.3 Расчет длительности ремонтного цикла станка.
1.4.4 Расчет продолжительности межремонтного периода.
1.4.5 Продолжительность этапа «использование по назначению».
1.4.6 Рисунок структурной модели стадии «эксплуатация» станка по заданию.
1.4.7 Ф.И.О. студента, группа, подпись и дата выполнения работы.
Вопросы для самопроверки
1.5.1 Какое влияние оказывает марка обрабатываемого материала и материал инструмента на продолжительность ремонтного цикла?
1.5.2 Дайте определение «ремонтный цикл» и «межремонтный период».
1.5.3 Назовите этапы стадии «эксплуатация».
1.5.4 Перечислить основные виды ремонта оборудования.
1.5.5 Напишите эмпирическую формулу расчёта продолжительности оперативного времени ремонтного цикла.
|
|
Историки об Елизавете Петровне: Елизавета попала между двумя встречными культурными течениями, воспитывалась среди новых европейских веяний и преданий...
Общие условия выбора системы дренажа: Система дренажа выбирается в зависимости от характера защищаемого...
Кормораздатчик мобильный электрифицированный: схема и процесс работы устройства...
Эмиссия газов от очистных сооружений канализации: В последние годы внимание мирового сообщества сосредоточено на экологических проблемах...
© cyberpedia.su 2017-2024 - Не является автором материалов. Исключительное право сохранено за автором текста.
Если вы не хотите, чтобы данный материал был у нас на сайте, перейдите по ссылке: Нарушение авторских прав. Мы поможем в написании вашей работы!