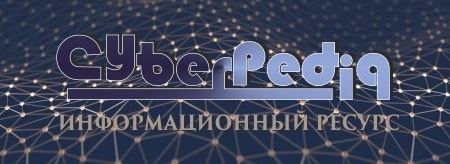
Типы оградительных сооружений в морском порту: По расположению оградительных сооружений в плане различают волноломы, обе оконечности...
Поперечные профили набережных и береговой полосы: На городских территориях берегоукрепление проектируют с учетом технических и экономических требований, но особое значение придают эстетическим...
Топ:
Особенности труда и отдыха в условиях низких температур: К работам при низких температурах на открытом воздухе и в не отапливаемых помещениях допускаются лица не моложе 18 лет, прошедшие...
Когда производится ограждение поезда, остановившегося на перегоне: Во всех случаях немедленно должно быть ограждено место препятствия для движения поездов на смежном пути двухпутного...
Комплексной системы оценки состояния охраны труда на производственном объекте (КСОТ-П): Цели и задачи Комплексной системы оценки состояния охраны труда и определению факторов рисков по охране труда...
Интересное:
Средства для ингаляционного наркоза: Наркоз наступает в результате вдыхания (ингаляции) средств, которое осуществляют или с помощью маски...
Берегоукрепление оползневых склонов: На прибрежных склонах основной причиной развития оползневых процессов является подмыв водами рек естественных склонов...
Мероприятия для защиты от морозного пучения грунтов: Инженерная защита от морозного (криогенного) пучения грунтов необходима для легких малоэтажных зданий и других сооружений...
Дисциплины:
![]() |
![]() |
5.00
из
|
Заказать работу |
|
|
Кафедра ДВС
Конспект лекций по курсу ДВС (СДВС)
Николаев – 2014
Содержание
Тема 1.Сравнение ДВС с другими типами тепловых двигателей. Классификация ДВС. Область их применения, перспективы и направления дальнейшего развития. Соотношение в ДВС и их маркировка.
|
Двигатель внутреннего сгорания – это такой тепловой двигатель, в котором тепловая энергия, выделяющаяся при сгорании топлива в рабочем цилиндре, преобразуется в механическую работу. Преобразование тепловой энергии в механическую осуществляется посредством передачи энергии расширения продуктов сгорания на поршень, возвратно-поступательное движение которого, в свою очередь, через кривошипно-шатунный механизм преобразуется во вращательное движение коленчатого вала, приводящего в движение гребной винт, электрический генератор, насос или другой потребитель энергии.
ДВС можно классифицировать по следующим основным признакам:
– по роду рабочего цикла – с подводом теплоты к рабочему телу при постоянном объеме, с подводом теплоты при постоянном давлении газов и со смешанным подводом теплоты, т. е. вначале при постоянном объеме, а потом при постоянном давлении газов;
– по способу осуществления рабочего цикла – четырехтактные у которых цикл совершается за четыре последовательных хода поршня (за два оборота коленчатого вала), и двухтактные, у которых цикл осуществляется за два последовательных хода поршня (за один оборот коленчатого вала);
– по способу воздухоснабжения – с наддувом и без наддува. В четырехтактных ДВС без наддува цилиндр наполняется свежим зарядом (воздухом или горючей смесью) всасывающим ходом поршня, а в двухтактных ДВС – продувочным компрессором с механическим приводом от двигателя. Во всех ДВС с наддувом наполнение цилиндра осуществляется специальным компрессором. Двигатели с наддувом нередко называют комбинированными, так как помимо поршневого двигателя они имеют и компрессор, подающий воздух в двигатель при повышенном давлении;
|
– по способу воспламенения топлива – с воспламенением от сжатия (дизели) н с искровым зажиганием (карбюраторные к газовые);
– по роду применяемого топлива – жидкого топлива и газовые. К ДВС жидкого топлива относятся и многотопливные двигатели, которые без конструктивных изменений могут работать на различных топливах. К газовым ДВС относятся и двигатели с воспламенением от сжатия, в которых основное топливо газообразное, а жидкое топливо в небольшом количестве используется как запальное, т. е. для воспламенения;
– по способу смесеобразования – с внутренним смесеобразованием, когда топливовоздушная смесь образуется внутри цилиндра (дизели), и с внешним смесеобразованием, когда эта смесь приготовляется до ее подачи в рабочий цилиндр (карбюраторные и газовые двигатели с искровым зажиганием). Основные способы внутреннего смесеобразования – объемное, объемно-пленочное и пленочное;
– по типу камеры сгорания (КС) – с неразделенными однополостными КС, с полуразделенными КС (КС в поршне) и разделенными КС (предкамерные, вихрекамерные и воздушно-камерные КС);
– по частоте вращения коленчатого вала n – малооборотные (МОД) с n до 240 мин-1, среднеоборотные (СОД) с 240 < n < 750 мин-1, повышенной оборотности (ПОД) с 750 <n< 1500 мин-1 и высокооборотные (ВОД) с n > 1500 мин-1;
– по назначению – главные, предназначенные для привода судовых движителей (гребных винтов), и вспомогательные, приводящие в движение электрические генераторы судовых электростанций или судовые механизмы;
– по принципу действия – простого действия (рабочий цикл совершается только в одной полости цилиндра), двойного действия (рабочий цикл совершается в двух полостях цилиндра над и под поршнем) и с противоположно движущимися поршнями (в каждом цилиндре двигателя имеется два механически связанных поршня, движущихся в противоположных направлениях, с помещенным между ними рабочим телом);
– по конструктивному исполнению кривошипно-шатунного механизма (КШМ) – тронковые и крейцкопфные. В тронковом двигателе силы нормального давления, возникающие при наклоне шатуна, передаются направляющей частью поршня – тронком, скользящим во втулке цилиндра; у крейцкопфного двигателя поршень не создает сил нормального давления, возникающих при наклоне шатуна, нормальное усилие создается в крейцкопфном соединении и передается ползунами на параллели, которые закреплены вне цилиндра на станине двигателя;
|
– по расположению цилиндров – вертикальные, горизонтальные, однорядные, двухрядные, У-образные, звездообразные и т. п.
Основными определениями, которые относятся ко всем ДВС, являются:
– верхняя и нижняя мертвые точки (ВМТ и НМТ), соответствующие верхнему и нижнему крайнему положению поршня в цилиндре (в вертикальном двигателе);
– ход поршня,т. е. расстояние при перемещении поршня из одного крайнего положения в другое;
– объем камеры сгорания (или сжатия), соответствующий объему полости цилиндра при нахождении поршня в ВМТ;
– рабочий объем цилиндра, который описан поршнем при его ходе между мертвыми точками.
Марка дизеля дает представление о его типе и основных размерах. Маркировку отечественных дизелей осуществляют в соответствии с ГОСТ 4393-82 «Дизели стационарные, судовые, тепловозные и промышленные. Типы и основные параметры». Для маркировки приняты условные обозначения, состоящие из букв и цифр:
Ч – четырехтактный;
Д – двухтактный;
ДД – двухтактный двойного действия;
Р – реверсивный;
С – с реверсивной муфтой;
П – с редукторной передачей;
К – крейцкопфный;
Г – газовый;
Н – с наддувом;
1А, 2А, ЗА, 4А – степень автоматизации по ГОСТ 14228-80.
Отсутствие в условном обозначении буквы К означает, что дизель тронковый, буквы Р – дизель нереверсивный, а буквы Н – дизель без наддува. Цифры в марке перед буквами указывают число цилиндров, а после букв: число в числителе – диаметр цилиндра в сантиметрах, в знаменателе – ход поршня в сантиметрах.
В марке дизеля с противоположно движущимися поршнями указывают оба хода поршня, соединенных знаком «плюс», если ходы разные, или произведение «2 на ход одного поршня» при равенстве ходов.
В марке судовых дизелей производственного объединения «Брянский машиностроительный завод» (ПО БМЗ) дополнительно указывается и номер модификации, начиная со второй. Этот номер приводится в конце маркировки по ГОСТ 4393-82. Ниже приведены примеры маркировки некоторых двигателей.
|
12ЧНСП1А 18/20 – дизель двенадцатнцилиндровый, четырехтактный, с наддувом, с реверсивной муфтой, с редукторной передачей, автоматизированный по 1-й степени автоматизации, с диаметром цилиндра 18 см и ходом поршня 20 см.
16ДПН 23/2 X 30 – дизель шестнадцатицилиндровый, двухтактный, с редукторной передачей, с наддувом, с диаметром цилиндра 23 см и с двумя противоположно движущимися поршнями, имеющими каждый ход 30 см,
9ДКРН 80/160-4 – дизель девятицилиндровый, двухтактный, крейцкопфный, реверсивный, с наддувом, с диаметром цилиндра 80 см, ходом поршня 160 см, четвертой модификации.
На некоторых отечественных заводах кроме обязательной по ГОСТу марки выпускаемым дизелям присваивают и марку заводскую. Например, заводской марке Г -74 (завод «Двигатель революции») соответствует марка 6ЧН 36/45.
В большинстве зарубежных стран маркировка двигателей не регламентируется стандартами, а фирмы-строители используют собственные системы условных обозначений. Но даже одна и таже фирма нередко меняет принятые обозначения. Все же необходимо отметить, что многие фирмы в условных обозначениях указывают основные размеры двигателя: диаметр цилиндра и ход поршня.
Четырехтактный ДВС.
Четырехтактный ДВС На рис. 2.1 показана схема работы четырехтактного тронкового дизеля без наддува (четырехтактные двигатели крейцкопфного типа вообще не строят).
Рис. 2.1. Принцип работы четырехтактного ДВС
1-й такт – впуск или наполнение. Поршень 1 движется от ВМТ к НМТ. При нисходящем ходе поршня через впускной патрубок 3 и расположенный в крышке впускной клапан 2 в цилиндр поступает воздух, так как давление в цилиндре из-за увеличения объема цилиндра становится ниже давления воздуха (или рабочей смеси в карбюраторном двигателе) перед впускным патрубком ро. Впускной клапан открывается несколько раньше ВМТ (точка r), т. е, с углом опережения 20…50° до ВМТ, что создает более благоприятные условия для поступления воздуха в начале наполнения. Впускной клапан закрывается после НМТ (точка а'), так как в момент прихода поршня в НМТ (точка а) давление газа в цилиндре еще ниже, чем в впускном патрубке. Поступлению воздуха в рабочий цилиндр в этот период способствует и инерционный подпор воздуха, поступающего в цилиндр- Поэтому впускной клапан закрывается с углом запаздывания 20...45° после НМТ.
Углы опережения и запаздывания определяют опытным путем. Угол поворота коленчатого вала (ПКВ), соответствующий всему процессу наполнения, составляет примерно 220...275° ПКВ.
|
Отличительная особенность дизеля с наддувом заключается в том, что за время 1-го такта свежий заряд воздуха засасывается не из окружающей среды, а поступает во впускной патрубок при повышенном давлении из специального компрессора. В современных судовых дизелях компрессор приводится в движение газовой турбиной, работающей на отработавших газах двигателя. Агрегат, состоящий из газовой турбины и компрессора, называют турбокомпрессором. В дизелях с наддувом линия наполнения обычно идет выше линии выпуска (4-го такта).
2-й такт – сжатие. При обратном ходе поршня к ВМТ с момента закрытия впускного клапана поступающий в цилиндр свежий заряд воздуха сжимается, в результате чего повышается его температура до уровня, необходимого для самовоспламенения топлива. Топливо в цилиндр впрыскивается форсункой 4 с некоторым опережением до ВМТ (точка n) при высоком давлении, обеспечивающей качественное распыливание топлива. Опережение вспрыскивания топлива до ВМТ необходимо для подготовки его к самовоспламенению в момент прихода поршня в район ВМТ. В этом случае создаются наиболее благоприятные условия для работы дизеля с высокой экономичностью. Угол впрыска на номинальном режиме в МОД обычно равен 1...9°, а в СОД – 8...16° до ВМТ. Момент воспламенения (точка с) на рисунке показан в ВМТ, однако он может быть и несколько смещен относительно ВМТ, т. е, воспламенение топлива может начаться раньше или позднее ВМТ.
3-й такт – сгорание и расширение (рабочий ход). Поршень движется от ВМТ к НМТ. Распыленное топливо, смешанное с горячим воздухом, воспламеняется и сгорает, в результате чего резко повышается давление газов (точка z), а затем начинается их расширение. Газы, действуя на поршень во время рабочего хода, совершают полезную работу, которая через кривошнпно-шатунный механизм передается потребителю энергии. Процесс расширения заканчивается в момент начала открытия выпускного клапана 5 (точка b ’), которое происходит с опережением 20...40°. Некоторое уменьшение полезной работы расширения газа по сравнению с тем, когда клапан стал бы открываться в НМТ, компенсируется снижением затрачиваемой работы на следующем такте.
4-й такт – выпуск. Поршень движется от НМТ к ВМТ, выталкивая отработавшие газы из цилиндра. Давление газов в цилиндре в данный момент несколько выше давления после выпускного клапана. Чтобы полностью удалить отработавшие газы из цилиндра, выпускной клапан закрывается после прохода поршнем ВМТ, при этом угол запаздывания закрытия составляет 10...60° ПКВ. Поэтому в течение времени, соответствующего углу 30...110° ПКВ, одновременно открыты впускной и выпускной клапаны. Это улучшает процесс очистки камеры сгорания от отработавших газов, особенно в дизелях с наддувом, так как давление наддувочного воздуха в данный период выше давления отработавших газов.
Таким образом, выпускной клапан открыт в период, соответствующий 210...280° ПКВ.
Принцип работы четырехтактного карбюраторного двигателя отличается от дизеля тем, что рабочая смесь – топливо и воздух – приготовляется вне цилиндра (в карбюраторе) и поступает в цилиндр в период 1-го такта; смесь воспламеняется в районе ВМТ от электрической искры.
Полезная работа, полученная за периоды 2-го и 3-го тактов, определяется площадью a с zba (площадь с наклонной штриховкой, см, 4-й такт). Но во время 1-го такта двигатель затрачивает работу (с учетом атмосферного давления ро под поршнем), равную площади над кривой r ' ma до горизонтальной линии, соответствующей давлению ро. За время 4-го такта двигатель затрачивает работу на выталкивание отработавших газов, равную площади под кривой brr' до горизонтальной линии ро. Следовательно, в четырехтактном двигателе без наддува работа так называемых «насосных» ходов, т. е. 1-го и 4-го тактов, когда двигатель выполняет роль насоса, является отрицательной (эта работа на индикаторной диаграмме показана площадью с вертикальной штриховкой) и должна быть вычтена из полезной работы, равной разности работ в период 3-го и 2-го тактов, В реальных условиях работа насосных ходов очень мала, в связи с чем эту работу условно относят к механическим потерям, В дизелях с наддувом, если давление наддувочного воздуха, поступающего в цилиндр, выше среднего давления газов в цилиндре в период выталкивания их поршнем, работа насосных ходов становится положительной.
Двухтактный ДВС.
В двухтактных двигателях очистка рабочего цилиндра от продуктов сгорания и наполнение его свежим зарядом, т. е, процессы газообмена, происходят только в тот период, когда поршень находится в районе НМТ при открытых органах газообмена. Очистка цилиндра от отработавших газов при этом осуществляется не поршнем, а предварительно сжатым воздухом (в дизелях) или горючей смесью (в карбюраторных и газовых двигателях). Предварительное сжатие воздуха или смеси происходит в специальном продувочном или наддувочном компрессоре. В процессе газообмена в двухтактных двигателях некоторая часть свежего заряда неизбежно удаляется из цилиндра вместе с отработавшими газами через выпускные органы. В связи с этим подача продувочного или наддувочного компрессора должна быть достаточной, чтобы компенсировать эту утечку заряда.
Выпуск газов из цилиндра происходит через окна или через клапан (количество клапанов может быть от 1 до 4). Впуск (продувка) свежего заряда в цилиндр в современных двигателях осуществляется только через окна. Выпускные и продувочные окна размещены в нижней части втулки рабочего цилиндра, а выпускные клапаны – в крышке цилиндра.
Схема работы двухтактного дизеля с контурной продувкой, т. е. когда выпуск и продувка происходят через окна, показана на рис. 2.2. Рабочий цикл имеет два такта.
1-й такт – ход поршня от НМТ (точка m) до ВМТ. Вначале поршень 6 перекрывает продувочные окна 1 (точка d'), прекращая тем самым поступление свежего заряда в рабочий цилиндр, а затем поршень перекрывает и выпускные окна 5 (точка b '), после чего начинается процесс сжатия воздуха в цилиндре, который заканчивается, когда поршень придет в ВМТ (точка с). Точка n соответствует моменту начала впрыскивания топлива форсункой 3 в цилиндр. Следовательно, в течение 1-го такта в цилиндре заканчиваются выпуск, продувка и наполнение цилиндра, после чего происходит сжатие свежего заряда и начинается впрыскивание топлива.
Рис. 2.2. Принцип работы двухтактного ДВС
2-й такт – ход поршня от ВМТ до НМТ. В районе ВМТ форсункой впрыскивается топливо, которое воспламеняется и сгорает, при этом давление газов достигает максимального значения (точка z) и начинается их расширение. Процесс расширения газов заканчивается в момент начала открытия поршнем 6 выпускных окон 5 (точка b), после чего начинается выпуск отработавших газов из цилиндра за счет перепада давления газа в цилиндре и выпускном коллекторе 4. Затем поршень открывает продувочные окна 1 (точка d) и происходят продувка и наполнение цилиндра свежим зарядом. Продувка начнется только после того, как давление газов в цилиндре станет ниже давления воздуха рs в продувочном ресивере 2.
Таким образом, в течение 2-го такта в цилиндре происходят впрыскивание топлива, его сгорание, расширение газов, выпуск отработавших газов, продувка и наполнение свежим зарядом. Во время этого такта осуществляется рабочий ход, обеспечивающий полезную работу.
Индикаторная диаграмма, представленная на рис. 2, одинакова как для дизеля без наддува, так и для дизеля с наддувом. Полезная работа цикла определяется площадью диаграммы md ' b 'с zbdm.
Работа газов в цилиндре положительна в период 2-го такта и отрицательна во время 1-го такта.
Остов двигателя
Основные неподвижные детали образуют остов двигателя, являющийся опорой для различных узлов и движущихся деталей. Он состоит из фундаментной рамы, картера, цилиндров и их крышек. Все эти элементы соединены связями в единую конструкцию.
Конструктивное оформление деталей остова определяется назначением и типом двигателя, количеством и расположением цилиндров, схемами КШМ и механизма газораспределения. Силы от давления газов, инерции движущихся масс и предварительной затяжки связей при сборке, действующие на остов, вызывают деформацию его элементов. При достаточной механической прочности элементов для нормальной работы двигателя остов должен обладать необходимой продольной и поперечной жесткостью, при которой сохраняются линия укладки коленчатого вала, перпендикулярность осей цилиндров к оси коленчатого вала, геометрическая форма рабочих цилиндров.
На рис. 3.3 показаны конструктивные схемы остовов судовых рядных двигателей, различающиеся между собой числом разъемов между его деталями и способами укладки коленчатого вала. Эти различия вызваны особенностями требований к габаритам, массе, технологии изготовления, удобству обслуживания и ремонта двигателя. Остовы V-образных двигателей и с ПДП (и подобные им) более сложные и выполняются по схожим между собой схемам.
Остов крейцкопфных двигателей, имеющих обычно большую высоту (рис. 3.3, а), состоит из фундаментной рамы 1, картера 2, цилиндров 3 с установленными в них цилиндровыми втулками 4 и крышек цилиндров 6, закрепленных шпильками 5. Из технологических соображений и удобства монтажа остов выполняют, как минимум, с тремя горизонтальными разъемами и с коленчатым валом, уложенным в подшипники фундаментной рамы. Жесткость его обеспечивается за счет увеличения сечений продольных и поперечных связей рамы, применения картеров коробчатой конструкции, соединения деталей длинными анкерными связями 7.
Рис. 3.3. Конструктивные схемы остовов дизелей
В тронковых двигателях для повышения жесткости остова, снижения его массы отдельные его элементы часто объединяют в одно целое, что технологически вполне приемлемо. Конструктивно это решается объединением цилиндров двигателя с картером в общий блок-картер 1 (рис. 3.3, б), а также применением развитой по высоте фундаментной рамы 1, выполненной как одно целое с картером и отдельным блоком цилиндров 2 (рис. 3.3, в). Соединяют эти элементы сквозными анкерными связями 2 (рис. 3.3, б) или укороченными силовыми шпильками 3 (рис. 3.3, в), ввернутыми в нижнюю часть блока цилиндров.
Остов с подвесным коленчатым валом широко распространен в современных ВОД и СОД в связи с большой жесткостью и меньшей массой конструкции. В однорядных СОД большой мощности применяют блок-картер 1, к которому снизу массивными крышками подшипников 2 подвешивают коленчатый вал (рис. 3.3, г). Часто остовы рядных и V-образных двигателей с подвесным валом выполняют по схеме, где картер 1 и блок цилиндров 2 отлиты раздельно и стянуты силовыми шпильками 3 (рис. 3.3, д). При этой схеме, несмотря на дополнительный разъем, сохраняется жесткость, упрощается изготовление остова, снижается его масса, так как блок цилиндров разгружен от растягивающих усилий. В большинстве двигателей крышки крепят к блоку цилиндров короткими силовыми шпильками, устанавливаемыми в верхней его плите. Общая масса деталей остова во многом определяется схемой их нагружения. При растяжении остова газовыми силами детали его получаются более тяжелыми. В конструкциях, где остов стянут анкерными связями, детали могут быть облегчены, так как чугун на сжатие работает лучше, чем на растяжение.
Для проводки анкерных связей в поперечных балках деталей остова выполняют вертикальные каналы (колодцы). Анкерная связь 7 (рис. 3.3, а) представляет собой стержень с резьбой под гайки на обоих его концах. В МОД для удобства при монтаже анкерные связи выполняют из двух частей, соединенных резьбовой муфтой. Для устранения поперечных вибраций длинных анкерных связей используют эластичные стопорные устройства. Затягивают анкерные связи гидравлическим домкратом с усилием, обеспечивающим плотное соединение деталей остова при наибольшем давлении в цилиндре. Анкерные связи изготовляют из углеродистой стали.
Все связи, затягиваемые гидравлическим способом, имеют специальную конструкцию: концы их оборудуют нарезным хвостовиком для крепления гидродомкрата, а гайки к ним имеют цилиндрическую форму с отверстиями на боковой поверхности под вороток. Гидравлический домкрат используют в СОД и МОД также для затяжки силовых связей рамовых подшипников, подшипников нижней (кривошипной) и верхней головки шатуна, крышек цилиндров, штоков поршней, насадки кулачных шайб, выкатывания вкладышей рамовых подшипников и др.
Фундаментная рама.
Фундаментная рама является основанием для деталей остова, предназначена для укладки коленчатого вала и служит емкостью для сбора масла, вытекающего из узлов смазывания двигателя. Рама нагружена массой двигателя, силами давления газов, силами инерции поступательно движущихся и вращающихся масс.
Рама (рис. 3.4, а, б) образована продольными и поперечными балками, которые должны иметь требуемую жесткость. Продольные балки 2 оснащены верхними обработанными полками 3 для установки на них картера и нижними опорными полками (лапами) 1 для крепления двигателя к судовому фундаменту.
Поперечные балки 4 двутаврового или коробчатого сечения расположены между цилиндрами и по торцам рамы. В верхней части поперечных балок выполнены гнезда (постели) 5 для рамовых подшипников коленчатого вала, а в стенках балок – вертикальные каналы (колодцы) а для анкерных связей и отверстия b для перетекания масла вдоль рамы. Для увеличения поперечной жесткости рамы по возможности максимально сближают анкерные связи и располагают разъем рамовых подшипников ниже верхней ее плоскости.
Рис. 3.4. Фундаментные рамы и рамовые подшипники:
а – литая; б – сварно-литая; в, г, д, е – рамовые подшипники соответственно с креплением крышки шпильками, домкратами, подвесной и установочный
В зависимости от типа и мощности двигателя фундаментные рамы выполняют литыми (рис. 3.4, а), сварными или сварно-литыми. Из технологических соображений фундаментные рамы СОД чаще всего выполняют литыми из чугуна СЧ20, СЧ3О, реже из стали 15Л, 30Л. Фундаментные рамы МОД и некоторых СОД для уменьшения массы и стоимости делают сварно-литыми (рис. 3.4, б). В таких конструкциях поперечные балки или часть их, включающая постель подшипника и анкерные каналы, выполняются литыми, а остальные части поперечных балок и продольные балки – сварными из проката стали 20, 25.
Полость рамы и закрывающий ее снизу поддон образуют маслосборник. Для увеличения жесткости рамы поддон часто делают заодно с ней (рис. 3.3, б, в). В СОД с подвесным коленчатым валом (рис. 3.3, г, д) и МОД он съемный сварной конструкции. Поддон выполняют с уклоном к середине или к кормовой части рамы, чтобы обеспечить в условиях плавания надежный слив масла в циркуляционную цистерну или прием из него масла циркуляционным насосом. В маслосборнике между поперечными перегородками рамы часто устанавливают металлическую сетку, уменьшающую пенообразование масла и предотвращающую попадание в него посторонних предметов.
Если двигатель оборудован навешенными насосами (водяными, масляными, топливоподкачивающими), то они монтируются на переднем торце рамы. На кормовом торце, где выходит коленчатый вал, во избежание утечек масла выполняют уплотнение.
Рамовые подшипники являются опорой для шеек коленчатого вала и представляют собой разъемный подшипник скольжения, состоящий из двух цилиндрических полувкладышей, внутренняя поверхность которых залита антифрикционным сплавом. Корпусом для вкладышей являются жесткий прилив (постель) в поперечных перегородках рамы или картера и крышка подшипника, прижимающая вкладыши к постели. Во время работы двигателя элементы подшипника нагружены силами от давления газов и силами инерции КШМ, вызывающими механические напряжения в деталях подшипника и износ трущихся поверхностей. Вкладыши выполняют сменными, не требующими пригонки при установке. Они бывают толстостенными, имеющими толщину стенки более 1/20 его наружного диаметра (до 5 мм), и тонкостенными с толщиной стенки менее 1/30 диаметра (менее 5 мм).
В МОД применяют толстостенные, выполненные из сталей 25 и 30, вкладыши 4 (рис. 3.4, в, г), рабочую поверхность которых заливают баббитом Б89, Б83, БН. Толщина слоя заливки составляет 1,8...2,5 мм. По мере износа слоя баббита масляный зазор в подшипнике регулируют удалением из стыка между вкладышами калиброванных прокладок 3. В СОД и ВОД, имеющих повышенные нагрузки на подшипник, применяют тонкостенные вкладыши 1 (рис. 3.4, д) из малоуглеродистой стали 10, 15 или 20 с заливкой толщиной 0,3...0,8 мм из свинцовистой бронзы БрСЗ0. Для улучшения противозадирных свойств, прирабатываемости, свинцовистую бронзу покрывают тонким слоем свинцово-оловянистого сплава. При износе заливки тонкостенные вкладыши заменяют.
Крышка подшипника 2 крепится болтами или шпильками 1 (рис. 3.4, в), усилие затяжки которых должно обеспечить плотность стыка при действии на крышку в четырехтактных двигателях наибольшей силы инерции КШМ, а в двухтактных двигателях – силы заедания Р = (1,0…1,5) F п MH, где 1,0...1,5 МПа – условное усилие, отнесенное к 1 м2 площади поршня. Иногда в СОД и МОД для уменьшения расстояния между анкерными связями крышку 2 прижимают одним-двумя домкратами 1, упирающимися в подкрепленную ребром поперечную балку картера или блок-картера (рис. 3.4, г). Крышки имеют двутавровое или коробчатое сечение и отливаются из чугуна СЧ20, СЧ25 или стали 30.
Подвесной коленчатый вал в двигателях без фундаментной рамы лежит на жестких крышках (подвесках) 2, изготовленных из стального литья или поковки. Крепится подвеска шпильками 3 с усилием затяжки, превышающим усилие от максимального давления сгорания. В высокофорсироваиных ВОД и СОД, чтобы исключить деформацию подшипникового узла, подвесные крышки 2 соединяют с картером 5 горизонтальными связями 4 (рис. 3.4, д). Надежная фиксация крышек относительно фундаментной рамы или картера обеспечивается применением направляющих пазов и замков.
От проворачивания и осевого смещения в корпусе подшипника толстостенные вкладыши фиксируют закраинами и штифтами, а тонкостенные – штифтами или отогнутыми выступами (усиками), которые входят в углубления у разъема в корпусе подшипника. В судовых условиях нижние вкладыши могут быть удалены без подъема коленчатого вала выкатыванием из постели.
Для фиксации коленчатого вала во время работы двигателя один из рамовых подшипников (чаще кормовой) выполняют установочным. Его вкладыши снабжают опорными 1 и упорными 2 поверхностями, залитыми антифрикционным сплавом. В них упираются обработанные кольцевые поверхности щек 3 и кольцевой гребень (бурт) 4 вала (рис. 3.4, е). Некоторые МОД и СОД имеют встроенные главные упорные подшипники, воспринимающие упор гребного винта. В таких двигателях надобность в установочных подшипниках отпадает.
Масло для смазывания и охлаждения подшипника подводят через его крышку (рис. 3,4 в) или постель (рис. 3.4, г) и далее по сверлениям или кольцевым канавкам к холодильникам в плоскости разъема, способствующим распределению масла по длине шейки вала и образованию масляного клина. Для повышения несущей способности подшипника холодильники не доводят до краев вкладыша, а круговую канавку выполняют только на верхнем вкладыше.
Картер (станина) двигателя.
Картер служит для соединения цилиндров с фундаментной рамой, образует закрытое пространство для КШМ. Он подвергается растяжению от действия максимальной силы давления газов при отсутствии анкерных связей и сжатию усилием предварительной затяжки при наличии их, а также изгибу в крейцкопфных двигателях от действия нормального усилия.
Для МОД с р е до 1,1 МПа картер выполнялся из отдельных А-образных сварных или литых стоек 2 с каналами а под анкерные связи, устанавливаемые в плоскости поперечных балок фундаментной рамы 1 (рис. 3.5, а). Жесткость конструкции обеспечивалась креплением стоек к усиленной фундаментной раме и блоку цилиндров, а также боковыми щитами, закрывающими пространство между стойками. Такая конструкция (с большим количеством разъемов) в современных МОД с высокими р z не может обеспечить требуемую жесткость остова. Поэтому в длинноходовых форсированных МОД перешли на сварные коробчатые конструкции 1 (рис. 3.5, б) которые, несмотря на увеличение бокового усилия, создают достаточную прочность и жесткость остова, упрощают сборку двигателя, повышают его герметичность.
К фланцам на А-образных стойках или к поперечным листам коробчатых станин крепят вертикальные чугунные или стальные направляющие (параллели), которые воспринимают боковое усилие, передаваемое ползунами крейцкопфа. Параллели бывают одно- и двусторонними. Односторонние параллели 4 (рис. 3.5, в) располагают с одной стороны от детален движения в плоскости, проходящей через ось цилиндра. Они имеют съемные обратные щеки 3, воспринимающие боковые усилия при изменении направления их действия. Двусторонние параллели 1 (рис. 3.5, г), имеющие четыре направляющих поверхности и работающие попарно, крепят по обе стороны от деталей КШМ в плоскостях, смещенных от оси цилиндра.
Картеры СОД с D > 200 мм во всех случаях выполняют литыми или сварными коробчатого типа (блок-станины). Особенности их конструкции определяют общей компоновкой остова (рис. 3.3). Для крепления двигателя с подвесным валом к судовому фундаменту в нижней части картера выполняют лапы (рис. 3.3, г, д).
Рис. 3.5. Станины двигателей:
а – из отдельных стоек; б – коробчатая; в, г – параллели
В боковых щитах станин или стенках картеров и блок-картеров выполняют люки с крышками для доступа внутрь картера с целью осмотра, ремонта и замены элементов КШМ. По Правилам Регистра на крышках люков должны быть установлены предохранительные клапаны на случай взрыва паров масла при перегревах или заеданиях. На картерах или блок-картерах СОД и ВОД обычно размещают распределительные валы, элементы механизма газораспределения, ТНВД, воздухораспределители, регуляторы и другие устройства. В МОД А-образные стойки и картеры отливают из чугунов СЧ20, СЧ30 или сваривают из стального проката. Поперечные перегородки сварно-литых картеров с постелями для коренных подшипников подвесных валов отливают из сталей 15Л, 35Л. Картеры и блок-картеры ВОД для уменьшения массы двигателя могут отливаться из сплавов АЛ5 и АЛ9.
Рабочий цилиндр
Рабочим цилиндром называется часть двигателя, где осуществляется рабочий цикл. Цилиндр состоит из рубашки и вставной втулки рабочего цилиндра. Во втулке движется поршень и протекают рабочие процессы. Рубашка является опорой для втулки и образует полости охлаждения для нее. Цилиндры устанавливают на верхнюю обработанную плоскость станины или картера и закрепляют шпильками или чаще всего анкерными связями. В зависимости от способа крепления рубашка растягивается усилием от давления газов или сжимается усилием затяжки анкерных связей. В тронковых двигателях рубашки нагружены также нормальным усилием КШМ.
Для ВОД и СОД рубашки цил
|
|
Археология об основании Рима: Новые раскопки проясняют и такой острый дискуссионный вопрос, как дата самого возникновения Рима...
Типы оградительных сооружений в морском порту: По расположению оградительных сооружений в плане различают волноломы, обе оконечности...
Папиллярные узоры пальцев рук - маркер спортивных способностей: дерматоглифические признаки формируются на 3-5 месяце беременности, не изменяются в течение жизни...
Наброски и зарисовки растений, плодов, цветов: Освоить конструктивное построение структуры дерева через зарисовки отдельных деревьев, группы деревьев...
© cyberpedia.su 2017-2024 - Не является автором материалов. Исключительное право сохранено за автором текста.
Если вы не хотите, чтобы данный материал был у нас на сайте, перейдите по ссылке: Нарушение авторских прав. Мы поможем в написании вашей работы!