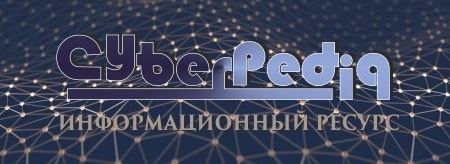
Индивидуальные очистные сооружения: К классу индивидуальных очистных сооружений относят сооружения, пропускная способность которых...
Архитектура электронного правительства: Единая архитектура – это методологический подход при создании системы управления государства, который строится...
Топ:
Выпускная квалификационная работа: Основная часть ВКР, как правило, состоит из двух-трех глав, каждая из которых, в свою очередь...
История развития методов оптимизации: теорема Куна-Таккера, метод Лагранжа, роль выпуклости в оптимизации...
Отражение на счетах бухгалтерского учета процесса приобретения: Процесс заготовления представляет систему экономических событий, включающих приобретение организацией у поставщиков сырья...
Интересное:
Распространение рака на другие отдаленные от желудка органы: Характерных симптомов рака желудка не существует. Выраженные симптомы появляются, когда опухоль...
Принципы управления денежными потоками: одним из методов контроля за состоянием денежной наличности является...
Инженерная защита территорий, зданий и сооружений от опасных геологических процессов: Изучение оползневых явлений, оценка устойчивости склонов и проектирование противооползневых сооружений — актуальнейшие задачи, стоящие перед отечественными...
Дисциплины:
![]() |
![]() |
5.00
из
|
Заказать работу |
|
|
Для проведения НК применяют дефектоскопы. Широко распространен ультразвуковой дефектоскоп УД2 - 70 по ГОСТ 23049 - 84. Он предназначен для:
контроля продукции на наличие дефектов типа нарушения сплошности и однородности материалов готовых изделий, полуфабрикатов и сварных соединений;
измерения глубины и координат залегания дефектов;
измерения отношений амплитуд сигналов, отраженных от дефектов.
Дефектоскоп может применяться для контроля качества продукции при ее изготовлении и эксплуатации в различных отраслях промышленности. Дефектоскоп сохраняет работоспособность при контроле материалов и изделий со скоростями распространения ультразвуковых колебаний в диапазоне 1000 - 8000 м/с. Шероховатость поверхности контролируемого изделия в зоне акустического контакта с преобразователем RZ не более 250 мкм.
Технические характеристики
Значения номинальных частот ультразвуковых колебаний (УЗК) дефектоскопа 1,25; 1,8; 2,5; 5,0; 10,0 МГц. В специальных версиях возможны другие значения номинальных частот.
Номинальные частоты повторения импульсов возбуждения 30; 60; 120; 250; 500; 1000 Гц.
Амплитуда зондирующего импульса генератора дефектоскопа, не менее 185 В при длительности (75±5) нс.
Диапазон изменения коэффициента усиления приемного тракта дефектоскопа от 0 до 100 дБ.
Дискретность изменения коэффициента усиления приемного тракта дефектоскопа составляет 0,5 или 1 дБ. Дискретность скачкообразного изменения клавишей "+dB" составляет 3... 30 дБ.
Динамический диапазон сигналов, наблюдаемых на экране дефектоскопа, не менее 20 дБ.
Диапазон контроля наличия дефектов по стали от 2 до 5000 мм. Диапазон установки диапазона контроля 10... 5000 мм с дискретностью 1 мм.
|
Диапазон измерений глубины залегания дефектов по стали от 2,0 до 5000 мм.
Диапазон установки скорости распространения УЗК 1000-8000 м/с с дискретностью 10м/с.
Диапазон установки угла ввода УЗК ПЭП составляет от 0 до 90° с дискретностью 1°.
Диапазон установки задержки развертки ограничивается следующим соотношением относительно начала импульса возбуждения
Д + 3 = 5000 мм,
где Д - установленный диапазон, мм;
- задержка, мм.
Динамический диапазон ВРЧ не менее 60 дБ.
Количество точек регулировки ВРЧ (в зависимости от диапазона) составляет от 10 до 64.
Количество стробов автоматического сигнализатора дефектов (АСД) - 2.
Диапазон установки длительности стробов АСД составляет от 1 до 5000 мм. Дискретность установки длительности строба АСД и длительности задержки строба АСД составляет 1 мм.
Диапазон установки порога АСД (высоты строба АСД) составляет от 0 до 100% высоты экрана.
Диапазон установки линейной компенсированной отсечки составляет от 0 до 100% высоты экрана с дискретностью 1%.
Количество запоминаемых программ настройки дефектоскопа не менее 100.
Количество запоминаемых изображений развертки (А-Скан изображений) не менее 100.
Количество запоминаемых измеренных значений глубины (координат) не менее 2800.
Конструкция дефектоскопа обеспечивает следующие потребительские функции:
режим увеличенного экрана;
режим "электронная лупа";
режим "заморозка" изображения экрана;
режим "замок";
встроенные часы и календарь;
режим связи с ПЭВМ для ввода в ПЭВМ информации из памяти дефектоскопа и возможности распечатки этой информации на принтере; ввода программ настроек из ПЭВМ в память прибора.
Масса дефектоскопа с аккумуляторной батареей (без комплекта ПЭП, кабелей и футляра), не более З кг.
Габаритные размеры дефектоскопа (без ручки для переноса), не более 245х 145х 75 мм.
Размер рабочей части экрана дефектоскопа, не менее 114x86 мм.
Электрическое питание дефектоскопа осуществляется от следующих источников питания:
|
сеть переменного тока напряжением от 187 до 242В, частотой 50±1 Гц;
автономный источник питания - аккумуляторная батарея номинальным напряжением 12В.
Максимальная мощность, потребляемая дефектоскопом от сети переменного тока, не более 20В·А.
Время непрерывной работы дефектоскопа от аккумуляторной батареи, не менее 7 часов.
Время установления рабочего режима дефектоскопа, не более 10 минут.
В основу работы дефектоскопа положена способность ультразвуковых колебаний (УЗК) распространяться в контролируемом изделии и отражаться от внутренних дефектов и границ материалов.
Возбуждение УЗК в контролируемом изделии осуществляется с использованием пьезоэлектрического эффекта преобразователями электрических колебаний в механические ПЭП. Отраженные от дефектов УЗК принимаются ПЭП. Полученные электрические колебания подлежат усилению, преобразованию в цифровую форму, обработке и выдаче на дисплей. Отображение отраженных сигналов на дисплее осуществляется в виде развертки типа А (А - Скан).
Анализируя А - Скан, оператор-дефектоскопист принимает решение о наличии в изделии дефекта и его местоположении. При определении глубины залегания используется формула
, (4.1)
где Н - расстояние от точки ввода УЗК до дефекта, м;
С - скорость распространения УЗК в исследуемом материале, м/с;- время прохождения УЗК от точки ввода до дефекта и обратно, с.
Дефектоскоп реализует эхо-импульсный, теневой и зеркально-теневой методы акустического контроля.
Принцип действия дефектоскопа следующий. По сигналу центрального процессора сигналов (ЦПС) схема генератора зондирующих импульсов вырабатывает возбуждающий импульс, который поступает через разъем генератора на ПЭП и излучается в контролируемое изделие. Отраженный сигнал преобразуется в ПЭП в электрический импульс и через разъем приемника поступает на вход усилителя.
Коэффициент усиления усилителя задается ЦПС через схему цифро-аналогового преобразователя (ЦАП) временной регулировки усиления. Усиленный электрический импульс фильтруется частотным фильтром и поступает на вход аналого-цифрового преобразователя (АЦП). С выхода АЦП цифровой сигнал поступает на ЦПС для дальнейшей обработки и отображения на дисплее.
При НК элеваторов выявляются поверхностные и надповерхностные дефекты типа трещин, надрывов, раковин и другие нарушения сплошности металла зоны элеватора, подвергаемые НК, перечислены в таблице 4.1.
|
Для контроля деталей элеватора ультразвуковым методом применяют прямые (нормальные) и наклонные (призматические) преобразователи с углом призмы 40°, 50° и рабочей частотой 1,8 МГц и 2,5 МГц. Настройку чувствительности ультразвукового дефектоскопа при контроле деталей элеватора производят по испытательным образцам, изготовленным из бездефектных частей списанных деталей элеватора с предварительно нанесенными искусственными дефектами. Для контроля деталей элеватора призматическим преобразователем применяются образца с искусственным дефектом в виде зарубки (рисунок 4.2).
Рисунок 4.2 - Испытательный образец для настройки чувствительности дефектоскопа
Для контроля деталей элеватора прямым преобразователем применяются образцы с искусственным дефектом в виде плоскодонного сверления (рисунок 4.2).
Глубина прозвучивания «Н» принимается равной толщине контролируемой детали или участка.
Подготовка к контролю
Элеватор подвергается НК в разнообразном виде, к комплекту деталей должен быть приложен паспорт на элеватор. Детали элеватора перед контролем должны быть очищены от грязи, масел, ржавчины, отслаивающейся окалины и краски любыми способами (механическим, промывкой в керосине, в растворе каустической соды с последующим ополаскиванием). В случае, когда краска или окалина имеет хорошее сцепление с металлом и представляет собой плотную (без рыхлостей и пор) пленку или слой на поверхности или окалину. Острые выступы и неровности на поверхности, подвергаемой НК, удаляют с помощью ручной шлифовальной машинки с мелким наждачным камнем, напильником или наждачной бумагой. При зачистке контролируемых поверхностей следить за тем, чтобы размеры ее не вышли за пределы допусков размеров деталей.
Рисунок 4.3 - Образец для настройки чувствительности дефектоскопа нормальным преобразователем
элеватор диагностика дефектоскопия безопасность
Ультразвуковой контроль можно проводить при температуре окружающего воздуха от +5 до +40°С, температура деталей элеватора должна быть такой же, при несоблюдении этих условий снижается чувствительность метода. Для обеспечения акустического контакта между искателем и изделием подготовленную поверхность перед контролем тщательно протирают ветошью, а затем на нее наносят слой контактной смазки. Для получения надежного акустического контакта преобразователь - контролируемое изделие следует применять различные по вязкости масла. Выбор масла по вязкости зависит от чистоты контролируемой поверхности и температуры окружающей среды. Чем грубее поверхность и выше температура, тем более вязкие масла следует применять в качестве контактной жидкости. Наиболее подходящей контактной жидкостью для контроля деталей элеватора являются масла типа МС-20 ГОСТ 21743-76. Увеличение вязкости контактной жидкости снижает чувствительность к выявлению дефектов. Поэтому в каждом случае следует выбирать контактную жидкость с минимальной вязкостью, обеспечивающей надежный акустический контакт преобразователь-контролируемая деталь.
|
Порядок контроля
После очистки поверхности детали элеватора подвергают визуальному контролю невооруженным глазом и с помощью оптических средств. При этом выявляют крупные трещины, задиры, остаточную деформацию, подрезы, следы наклепа. При обнаружении трещин и следов заварки трещин деталь бракуется.
Контроль размеров деталей производится в соответствии с технической документацией на ремонт элеватора. Измерительный инструмент для контроля размеров и критерии оценки годности деталей элеватора приводятся в картах контроля на ремонт.
Ультразвуковой контроль деталей элеватора осуществляется прямыми и призматическими преобразователями в соответствии с линиями сканирования, показанными на рисунках контролируемых деталей.Рабочую настройку, ультразвукового дефектоскопа проводят по испытательным образцам (рисунки 4.1, 4.2). Для настройки дефектоскопа ультразвуковой преобразователь с углом призмы 40°, 50° и рабочей частотой 1,8МГц или прямой преобразователь с рабочей частотой 2,5 МГц устанавливают на поверхность образца, на которую предварительно нанесена контактная смазка. Настройка скорости развертки должна соответствовать толщине прозвучиваемой детали элеватора или зоне прозвучивания. Чувствительность при контроле призматическим преобразователем настраивают по угловому отражателю (зарубке), выполненному на поверхности образца, противоположной той, на которой находится преобразователь. Чувствительность при контроле прямым преобразователем настраивают по плоскодонному сверлению диаметром 3 мм (см. рисунок 4.2).Добиваются на экране дефектоскопа максимальной амплитуды импульса от контрольного отражателя (дефекта) в виде "зарубки" или плоскодонного сверления, затем ручками "Чувствительность" и "Ослабление" доводят амплитуду импульса до 2/3 высоты экрана дефектоскопа. Мешающие сигналы при этом убрать с помощью ручки "Отсечка шумов".
|
Зону АСД устанавливают таким образом, чтобы ее начало находилось рядом с зондирующим импульсом, а конец - рядом с импульсом от контрольного отражателя. Зондирующий импульс должен быть вне зоны действия АСД. Настраивают чувствительность АСД так, чтобы он срабатывал при величине эхо-сигнала от контрольного дефекта, равной 2/3 высоты экрана дефектоскопа. Таким образом устанавливают чувствительность оценки при контроле деталей элеватора. Проводят повторный поиск контрольного отражателя на испытательном образце и при надежном его выявлении переходят к контролю деталей элеватора.
Ультразвуковой преобразователь устанавливают на контролируемую поверхность детали элеватора с предварительно нанесенной контактной смазкой и ведут контроль детали по линиям сканирования, показанным на рисунках контролируемых деталей, при этом с помощью переключателя "Ослабление" повышают чувствительность дефектоскопа на 3 - 5 дБ по сравнению с чувствительностью оценки и ведут поиск дефектов, следя за срабатыванием АСД.
При срабатывании АСД дефектоскоп из режима поисковой чувствительности переводят в режим чувствительности оценки (п.п.4.7 - 4.9) и определяют:
) местонахождение дефекта;
) максимальную амплитуду эхо-сигнала;
) условную протяженность дефекта.
При контроле необходимо отличать на экране ЭЛТ дефектоскопа ложные эхо-сигналы, появляющиеся вследствие особенностей конструкции деталей элеваторов. Эти сигналы следует фиксировать на экране ЭЛТ. Все эхо-сигналы, не совпадающие с ложными, следует считать сигналами от дефекта. Оценка характера дефектов производится по косвенным признакам:
интенсивное отражение от трещин наблюдается при направлении прозвучивания, перпендикулярном плоскости дефекта (при этом на экране ЭЛТ виден четкий импульс);
интенсивное отражение от дефекта круглой формы наблюдается при различных направлениях прозвучивания (при этом на экране ЭЛТ импульс более размытый).
Окончательное заключение о наличии дефекта или его отсутствии оператор-дефектоскопист дает после того, как предполагаемый дефект будет прозвучен во всех возможных направлениях и исследован в соответствии с п. 4.12. Через 0,5 ч после начала контроля, а затем через каждые 1,5 - 2 ч работы проверяют настройку дефектоскопа по испытательному образцу, согласно п.п. 4.5-4.9.
Контроль корпуса элеватора
Ультразвуковой дефектоскопией проверяют проушины корпуса, место перехода проушин в корпус на наличие трещин, раковин, внутренних пор. Для контроля применяется прямой преобразователь с рабочей частотой 2,5 МГц. Прозвучивание проводят с обеих торцевых поверхностей корпуса элеватора. Чувствительность дефектоскопа настраивают по испытательному образцу с плоскодонным сверлением. Сканируя корпус элеватора следят за срабатыванием АСД дефектоскопа.
При срабатывании АСД дефектоскоп из режима поисковой чувствительности переводят в режим чувствительности оценки и определяют:
) местонахождение дефекта;
) максимальную амплитуду эхо-сигнала;
) длину пути, пройденного преобразователем при включенном АСД (условную протяженность дефекта).
Контроль серьги
Контролируют серьгу ультразвуковым методом. Проверяются проушины, прямолинейная часть ее и зона закругления. Контроль серьги ведут преобразователем с учетом призмы 40° на частоте 1,8 МГц прямым лучом.
Проушины проверяют поочередным прозвучиванием всех плоских поверхностей. Преобразователь перемещают вокруг отверстия проушины. Направление прозвучивания совпадает с ходом движения преобразователя. Контроль ведется при прямом и обратном ходе. При настройке скорости развертки преобразователь располагают на внутренней плоскости поверхности проушины. Скорость развертки настраивают по прямому двугранному углу, одной из сторон которого является плоскость противоположная плоскости ввода УЗК. Глубина прозвучивания принимается равной толщине проушины. Чувствительность дефектоскопа настраивается по зарубке с эквивалентной площадью 5,1 мм² (3 мм ×1,7 мм).
При контроле прямолинейной части серьги преобразователь зигзагообразно перемещают вокруг ее цилиндрической поверхности. Направление прозвучивания при этом совпадает с ходом движения преобразователя. Контроль проводят при прямом и обратном ходе преобразователя. Величина продольного перемещения преобразователя определяется длинной прямолинейного участка серьги. При настройке скорости развертки преобразователь располагают на цилиндрической поверхности серьги. Скорость развертки настраивают по углу, образованному участком цилиндрической поверхности, противоположном участку ввода УЗК, и закруглением между плоской поверхностью проушины и цилиндрической поверхностью серьги. Глубины прозвучивания принимается равной диаметру серьги по цилиндрической части. Чувствительность настраивается по зарубке с эквивалентной площадью 6 мм² (3 мм × 2 мм). Шаг сканирования должен быть не более 1/2 ширины преобразователя. Настройка дефектоскопа, созданная при контроле цилиндрической части серьги полностью сохраняется и используется при контроле закругления серьги.
При контроле закругления серьги преобразователь перемещают по поверхности вдоль оси серьги. Направление прозвучивания совпадает с ходом движения преобразователя. Контроль ведут при прямом и обратном ходе. В процессе перемещения преобразователь слегка поворачивают на 10 - 15° в обе стороны. Закругление серьги проверяют поочередным прозвучиванием обоих плоских участков закругления.
Сканируя серьгу, следят за срабатыванием АСД дефектоскопа. При срабатывании АСД дефектоскоп из режима поисковой чувствительности переводят в режим чувствительности оценки и определяют:
местонахождение дефекта;
максимальную амплитуду эхо-сигнала;
условную протяженность дефекта.
Контроль челюстей
Челюсти контролируют ультразвуком при помощи преобразователя с углом призмы 40° на частоте 1,8 МГц прямым лучом. Проверка проводится с обеих плоских поверхностей челюсти последовательно. При контроле преобразователь зигзагообразно перемещают по плоской поверхности челюсти. Район отверстия под палец контролируют круговым движением преобразователя. Для надежности контроль ведут сначала при прямом ходе движения, затем при обратном. При контроле челюсти скорость развертки настраивают по нижнему ее углу (нижнему при таком положении челюсти, когда поверхность ввода УЗК верхняя). При этом преобразователь расположен на черновой поверхности челюсти. При контроле челюсти в районе отверстия под палец скорость развертки настраивается также по нижнему ее углу.
Глубина прозвучивания принимается равной толщине проушины челюсти. Чувствительность дефектоскопа в обоих случаях настраивается по зарубке с эквивалентной площадью 3,6 мм² (3 мм × 1,2 мм). Сканируя челюсть следят за срабатыванием АСД дефектоскопа. При срабатывании АСД дефектоскоп из режима поисковой чувствительности переводят на режим чувствительности оценки и определяют:
) местонахождение дефекта;
) максимальную амплитуду эхо-сигнала;
) условную протяженность дефекта.
Оценка результатов контроля
По результатам исследования дефектов определяют пригодность деталей элеватора к дальнейшей эксплуатации. Детали элеваторов отбраковывают в следующих случаях:
если амплитуда эхоимпульса обнаруженного дефекта равна по высоте амплитуде эхоимпульса от искусственного дефекта или превышает ее;
если обнаруженный на поисковой чувствительности дефект является протяженным, то есть если расстояние перемещения преобразователя по контролируемой поверхности между точками, соответствующими моментам исчезновения сигнала от дефекта составляет более 10 мм.
По результатам НК составляется акт (приложение А) в двух экземплярах, один из которых прилагается к паспортам элеваторов. В паспорте записывается номер акта и дата проведения контроля. Второй экземпляр хранится в службе неразрушающего контроля.
|
|
Архитектура электронного правительства: Единая архитектура – это методологический подход при создании системы управления государства, который строится...
Адаптации растений и животных к жизни в горах: Большое значение для жизни организмов в горах имеют степень расчленения, крутизна и экспозиционные различия склонов...
Автоматическое растормаживание колес: Тормозные устройства колес предназначены для уменьшения длины пробега и улучшения маневрирования ВС при...
Семя – орган полового размножения и расселения растений: наружи у семян имеется плотный покров – кожура...
© cyberpedia.su 2017-2024 - Не является автором материалов. Исключительное право сохранено за автором текста.
Если вы не хотите, чтобы данный материал был у нас на сайте, перейдите по ссылке: Нарушение авторских прав. Мы поможем в написании вашей работы!