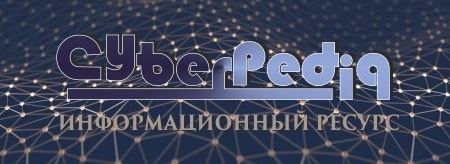
Архитектура электронного правительства: Единая архитектура – это методологический подход при создании системы управления государства, который строится...
Своеобразие русской архитектуры: Основной материал – дерево – быстрота постройки, но недолговечность и необходимость деления...
Топ:
Организация стока поверхностных вод: Наибольшее количество влаги на земном шаре испаряется с поверхности морей и океанов...
Марксистская теория происхождения государства: По мнению Маркса и Энгельса, в основе развития общества, происходящих в нем изменений лежит...
Характеристика АТП и сварочно-жестяницкого участка: Транспорт в настоящее время является одной из важнейших отраслей народного хозяйства...
Интересное:
Наиболее распространенные виды рака: Раковая опухоль — это самостоятельное новообразование, которое может возникнуть и от повышенного давления...
Уполаживание и террасирование склонов: Если глубина оврага более 5 м необходимо устройство берм. Варианты использования оврагов для градостроительных целей...
Принципы управления денежными потоками: одним из методов контроля за состоянием денежной наличности является...
Дисциплины:
![]() |
![]() |
5.00
из
|
Заказать работу |
|
|
ОБЩИЕ СВЕДЕНИЯ О МЕХАНИЗМАХ И МАШИНАХ
1.1. Основные понятия
Основное назначение машин — увеличение производительности и облегчение физического и умственного труда человека. Созданные человеком машины позволяют в некоторых случаях заменять отдельные органы человека, например конечности (манипуляторы роботов). Механизмы отдельных видов машин помогают управлять производственными и другими процессами по определенным программам.
Машина — механическое устройство, выполняющее движения для преобразования энергии, материалов и информации с целью замены или облегчения труда человека.
Основными типами машин являются
- энергетические машины
- рабочие (технологические, транспортные) машины.
Энергетические машины предназначены для преобразования энергии любого вида в механическую, и наоборот.
Рабочие машины осуществляют изменение формы, свойств, состояния и положение предмета труда.
Составными частями машины являются механизмы, служащие для преобразования видов движения. Механизмы, входящие в состав машины, разнообразны. Они представляют собой сочетание твердых тел, а также пневматические, гидравлические, электромагнитные устройства и их сочетания.
В зависимости от функционального назначения механизмы подразделяют на следующие виды:
• механизмы двигателей и преобразователей;
• передаточные механизмы;
• исполнительные механизмы;
• механизмы управления, контроля и регулирования;
• механизмы подачи, транспортирования, питания и сортировки
ШПОНОЧНЫЕ СОЕДИНЕНИЯ
Шпонки предназначены для передачи вращения между двумя деталями, сидящими одна в другой, или для движения деталей вдоль оси.
|
Для установки шпонок на деталях делают углубления— шпоночные канавки по формам и размерам шпонок. При неподвижных соединениях шпонку устанавливают в паз вала плотно или даже с натягом, а в пазу втулки создается более свободная посадка.
![]() | ![]() |
Клиповые шпонки (рис. 80, а) представляют собой клин с уклоном 1: 100,который запрессовывается между валом и ступицей
Призматические шпонки (рис. 80, 6) обеспечивают лучшее центрирование вала с сопрягаемой деталью и образуют неподвижные, так и скользящие соединения. Призматические шпонки закладывают в шпоночные канавки так, чтобы между верхней гранью шпонки и дном канавки верхней детали был зазор. Крутящий момент передается боковыми гранями шпонки, поэтому призматические шпонки должны иметь гарантированным натяг по боковым сторонам в шпоночной канавке.
Направляющие шпонки (рис. 80, в) применяют в тех случаях, когда детали должны свободно перемещаться вдоль вала. Направляющие шпонки крепят на валу винтами.
Сегментные шпонки (рис. 80, г) работают так же, как и призматические, но применяют их только для неподвижных соединений. Крутящий момент передается через боковые стороны шпонок и пазов. Основным преимуществом соединения сегментными шпонками является простота и дешевизна изготовления шпонок и шпоночных пазов.
Тангенциальные шпонки (рис. 80, д), как и клиновые, состоят из двух клиньев с уклоном 1:100. Широкая грань тангенциальной шпонки направлена по касательной к цилиндрической поверхности вала. Затягивание осуществляется ударами молотка по торцу широкой части одного из клиньев. Такие шпонки ставят при диаметрах вала более 100 мм.
ШЛИЦЕВЫЕ СОЕДИНЕНИЯ
Шлицевые соединения образуются выступами и впадинами вала и ступицами по всей окружности сопряжения, направленными вдоль оси.
Они предназначены для передачи больших крутящих моментов. По сравнению со шпоночными такие соединения имеют следующие преимущества:
|
1. Более точное центрирование детали по валу.
2. Вал почти не ослаблен, особенно при большом количестве шлицев, когда
впадины можно сделать неглубокими.
3. При сборке шлицевых соединений не требуется никаких пригоночных операций, так как после механической обработки деталей таких соединений получается полная их взаимозаменяемость.
На рис. 81, а, 6, в показаны прямобочные, эвольвентные и треугольные профили шлицев.
![]() | |
![]() |
ТРУБНЫЕ СОЕДИНЕНИЯ
Жидкости и газы обычно перекачивают насосами или компрессорами по трубопроводам. Трубы бывают чугунные, стальные, медные, латунные, алюминиевые. Наиболее распространены стальные трубы. Чугунные трубы применяют для отвода в канализационную сеть загрязненнойводы, а медные, латунные и алюминиевые — для подачи горючих и смазочных материалов.
По способу изготовления стальные трубы делятся на две группы; сварные и бесшовные (цельнотянутые).
Если трубопровод не требует разборки, то трубы сваривают. Если соединение труб разъемное, применяют фланцы или фитинги.
Соединение труб на фланцах.
Фланцевое соединение труб как более надежное используют в ответственных трубопроводах.
По характеру присоединений фланцев к трубам различаютчетыре типа соединений:
1. приварка встык (рис. 83, а):
2. соединение на резьбе (рис. 83, б);
3. соединение развальцовкой (рис. 83,в, г);
4. соединение разбортовкой труб (рис. 83, д).
Чтобы создать герметичность, между фланцами укладывают прокладки из мягкого упругого материала. После укладки прокладок устанавливают болты или шпильки.
![]() | Рис. 83. Соединение труб на фланцах: а- приварка встык, б- на резьбе, в- развальцовкой, г- схема работы вальцовки; 1- труба, 2-фланец, 3- ролик, 4-конус вальцовки, д- разбортовкой. |
НЕРАЗЪЕМНЫЕ СОЕДИНЕНИЯ
Неразъемными называются такие соединения, которые могут быть разобраны лишь путем разрушения или недопустимых остаточных деформаций одного из элементов конструкции.
Неразъемные неподвижные соединения осуществляются
- механическим путем (запрессовкой, склепыванием),
- с помощью сил физико-химического сцепления (сваркой, пайкой и склеиванием)
СОЕДИНЕНИЕ ДЕТАЛЕЙ СВАРКОЙ
|
Сварка — процесс получения неразъемных соединений посредством установления межатомных связей между свариваемыми частями при их местном или общем нагреве, или пластическом деформировании, или совместном действии того и другого.
Неразъемные соединения, выполненные с помощью сварки, называют сварными соединениями. Посредством сварки соединяют преимущественно детали из металлов. Однако сварные соединения применяют и для деталей из неметаллов — пластмассы и керамики или их сочетаний.
СОЕДИНЕНИЕ ДЕТАЛЕЙ ПАЯНИЕМ
Паянием называют процесс образования неразъемного соединения материалов при помощи расплавленного металла или сплава, называемого припоем. От сварки паяние отличается тем, что кромки соединяемых материалов не расплавляются, а только нагреваются до температуры плавления припоя. Припои имеют более низкую температуру плавления, чем соединяемые материалы. Припой расплавляется и затвердевает в зазоре между поверхностями соединяемых деталей.
Основным достоинством паянии является то, что соединяемые материалы не нагревают до высоких температур, что сохраняет их физические и механические свойства,
Различают два вида паяния:
4. легкоплавкими припоями - имеют температуру плавления до 500° С и незначительную механическую прочность (5- 7 кГ/мм2).
5. тугоплавкими припоями - имеют температуру плавления выше 500° С. Такими припоями можно получить прочность паяного соединения, близкую к прочности основного металла соединяемых деталей.
СОЕДИНЕНИЕ ДЕТАЛЕЙ КЛЕПКОЙ
Клепкой называется процесс получения неразъемных соединений при помощи заклепок. Соединение деталей осуществляется деформированием (расклепыванием) выступающего стержня заклепки, из которого образуется другая головка (замыкающая).
Клепку мелкими заклепками с диаметром стержня до 8—10 мм выполняют в холодном состоянии, а заклепками с диаметром стержня более 10 мм — в нагретом состоянии (горячая клёпка) Клепка может быть ручная и механизированная.
ВИДЫ ЗАКЛЕПОЧНЫХ СОЕДИНЕНИЙ
Заклепочный шов - один или несколько рядов заклепок, расположенных в определенном порядке для получения неразъемного соединения
|
I. По назначению клепаные швы делятся на три вида:
1. прочные- применяемые для соединения ферм, мостов, колонн, и т. п.;
2. плотные- используемые при изготовлении баков, сосудов, резервуаров и других изделий (такие швы должны обладать высокой герметичностью; для повышения герметичности между склепываемыми листами ставят различные прокладки или шов чеканят);
3. прочно-плотные, применяемые при склепывании резервуаров с высоким внутренним давлением (наряду с прочностью такой шов должен обладать хорошей герметичностью; герметичность прочно-плотных швов достигается чеканкой).
II. По характеру расположения соединяемых деталей различают:
1. соединения внахлестку (рис. 86, а), когда один лист накладывают на другой;
2. соединения встык, когда листы подводят встык и соединяют наложенной на них одной накладкой (рис. 86, б) или двумя (рис. 86, в).
III. По расположению заклепок швы делятся на:
1. однорядные,
2. двухрядные,
3. многорядные,
4. параллельные
5. шахматные. (рис. 86 г)
|
СОЕДИНЕНИЕ ДЕТАЛЕЙ СКЛЕИВАНИЕМ
Склеивание деталей — это вид сборки неподвижных неразъемных соединений, при котором между поверхностями деталей сборочного узла вводится слой специального вещества, способного неподвижно скреплять их — клея. Склеивание как метод сборки неподвижных соединений находит в последнее время все большее распространение, так как можно получить клеевые швы, по прочности не уступающие основному материалу.
Механическая прочность склеенного соединения зависит:
• от вида и качества клея,
• от качества склеиваемых поверхностей,
• от толщины слоя клея и равномерности его распределения,
• от соблюдения температурных и других режимов.
Важнейшее свойство любого клея — это адгезия, т. е. способность сцепляться с поверхностью материала. Адгезия может быть различна в зависимости от вида клея и характера склеиваемых поверхностей.
Наиболее распространенные клеевые соединения:
• внахлестку
• врезные (шунтовые)
• со вставными элементами
СОЕДИНЕНИЕ ДЕТАЛЕЙ С ГАРАНТИРОВАННЫМ НАТЯГОМ
ВАЛЫ
Деталь машины, передающим круговой момент и поддерживающая вращающиеся детали, называется – в а л о м
Вращающаяся или неподвижная летала машины, служащая для поддержания вращающихся деталей, но не передающая крутящего момента называется - о с ь ю.
КЛАССИФИКАЦИЯ ВАЛОВ
I. По конструкции
Прямые
Гладкие
Ступенчатые
II. По типу сечения.
1. Сплошные (цельные)
2. Полые (для уменьшения веса валов, для размещения внутри вала других деталей)
Ш. По расположению в пространстве;
Горизонтальные
2. Вертикальные
Наклонные
Крутящий момент на валы передается при помощи шпоночных или шлицевых соединений.
|
Для надежного крепления вала в механизме предусмотрены опоры. Поэтому участки вала лежащие в опорах качения пли скольжения называются –
Ц а п ф а м и
В свою очередь в зависимости от расположения на валу цапфы делятся на:
1. Шипы - расположенные на концах вала и воспринимающие радиальные нагрузки:
2. Шейки - располагаются в центре нала;
3. Пята - торцевая часть вала воспринимающая только осевую
нагрузку.
Валы наготавливают из углеродистой стали марок 30. 40, 45, Ст3. Ст4. Ст5 и легированных сталей.
Подшипники.
Неподвижные опоры вращающихся в них валов и осей, предназначенные для восприятия радиальных и осевых нагрузок, называются- п о д ш ип н и ка м и.
Нагрузка действующая перпендикулярно оси вала называется - радиальной. Нагрузка действующая вдоль оси вала называется - о с е в о й.
Сила препятствующая передвижению поверхности одного твердого тела по поверхности другого называется – с и л о й т р е н и я.
Трение бывает:
1. Скольжения - поверхность касания одной детали. перемещаясь по другой, остается все время неизменной.
2. Качения - детали перекатываются одна по другой и точка или линия поверхности их соприкосновения постоянно меняется.
В зависимости от сил трения возникающих в подшипниках они подразделяются на:
1. ПОДШИПНИКИ СКОЛЬЖЕНИЯ.
ПОДШИПНИКИ КАЧЕНИЯ.
Основными элементами подшипников качения являются: 1) тела качения - шарики или ролики, установленные между 2) кольцами и удерживающиеся друг от друга на определенном расстоянии при помощи
3) сепаратора.
Подшипники качения более стойки, по сравнению с подшипниками скольжения, кроме того, они способны работать при разных частотах вращения вала без дополнительной регулировки, не нуждаются в большом количестве смазки и сложном уходе.
Промышленностью выпускаются следующие диапазоны размеров подшипников качения: D = 1 - 260 мм с dшариков от 0,35 до 203 мм и массой от 0,5 грамм до 3.5 тонн.
МУФТОВЫЕ СОЕДИНЕНИЯ.
Устройства, предназначенные для соединения валов и передачи крутящего момента без изменения его направления называются - муфтами.
Функции выполняемые муфтами:
1. Обеспечивают работу соединяемых валов при небольших смещениях осей,
2. Смягчают при работе толчки и удары;
3. Предохраняют части машин от воздействия перегрузок;
4. Быстрое соединение или разъединение деталей на ходу или в неподвижном состоянии;
5. Регулирование передаваемого крутящего момента в зависимости от угловой скорости;
6. Передача крутящего момента только в одном направлении;
7. Облегчение пуска машины; и т.д,
КЛАССИФИКАЦИЯ МУФТ.
САЛЬНИКОВЫЕ УСТРОЙСТВА
Сальниковые устройства служат для уплотнения мест выхода валов, штуцеров, штоков, шпинделей и др.
В зависимости от назначения сальниковые устройства подразделяются:
Тип сальниковой набивки | Предел использования |
Среда работы | |
Давление (МПа) | Температура (° С) | ||
1. Хлопчатобумажная | 3,0 | 100 | Воздух, вода |
2. Пеньковая просаленная | 16,0 | 100 | Воздух, вода |
3. Асбестовая сухая | 2,5 | 400 | Вода, нефть, воздух, масло |
4. Хлопчатобумажная просаленная | 3,0 | 100 | Воздух, вода, масло |
5.Асбестовая пропитанная (АП) | 2,5 | 300 | Пар, минеральные кислоты, аммиак, растворы солей |
6. Асбестопроволочная | 4,5 | 400 | Пар, вода, бензин, органические растворители |
7. Асбестовая масло-бензостойкая (АМБ) | 2,0 | 300 | Органические растворители |
8. Фторопласт – 4 | 10,0 | От -195 до +250 | Кислоты, щелочи, растворители любых концентраций |
МЕХАНИЧЕСКИЕ ПЕРЕДАЧИ
Механической передачей называют устройство для передачи механического движения от двигателя к исполнительным органам машины. Может осуществляться с изменением значения и направления скорости движения, с преобразованием вида движения.
Механические передачи вращательного движения делятся:
- по способу передачи движения от ведущего звена к ведомому на передачи трением (фрикционные, ременные) и зацеплением (цепные, зубчатые, червячные)
- по соотношению скоростей ведущего и ведомого звеньев на замедляющие (редукторы) и ускоряющие (мультипликаторы);
- по взаимному расположению осей ведущего и ведомого валов на передачи с параллельными, пресекающимися и перекрещивающимися осями валов.
В каждой передаче различают два основных вала: входной и выходной, или ведущий и ведомый. Между этими валами в многоступенчатых передачах располагаются промежуточные валы.
Основные характеристики передач:
1. Мощность Р1 на входе и Р2 на выходе, Вт;
2. Быстроходность, выражающаяся частотой вращения n1 на входе и n2 на выходе, мин–1, или угловыми скоростями ω1 и ω2, с-1;
3. Передаточное отношение – отношение угловой скорости ведущего звена к угловой скорости ведомого звена:
коэффициент полезного действия(КПД)
Одноступенчатые передачи имеют следующие КПД: фрикционные – 0,85…0,9; ременные – 0,90…0,95; зубчатые – 0,95…0,99; червячные – 0,7…0,9; цепные – 0,92…0,95;
Зубчатые передачи
Зубчатая передача состоит из двух колес, посредством которых они сцепляются между собой. Зубчатое колесо с меньшим числом зубьев называют шестерней, с большим числом зубьев – колесом.
В зубчатой передаче вращающий момент передается от шестерни (ведущей элемент) к зубчатому колесу (ведомый элемент) специальными зубьями нарезанными специальными модульными фрезами на цилиндрической поверхности заготовок.
Основными преимуществами зубчатых передач являются:
- постоянство передаточного числа (отсутствие проскальзывания);
- компактность по сравнению с фрикционными и ременными передачами;
- высокий КПД (до 0,97…0,98 в одной ступени);
- большая долговечность и надежность в работе (например, для редукторов общего применения установлен ресурс ~ 30 000 ч);
- возможность применения в широком диапазоне скоростей (до 150 м/с), мощностей (до десятков тысяч кВт).
Недостатки:
- шум при высоких скоростях;
- невозможность бесступенчатого изменения передаточного числа;
- необходимость высокой точности изготовления и монтажа;
- незащищенность от перегрузок;
- наличие вибраций, которые возникают в результате неточного изготовления и неточной сборки передач.
Червячная передача
Червячная передача применяется для передачи вращения от одного вала к другому, когда оси валов перекрещиваются. Угол перекрещивания в большинстве случаев равен 90º. Наиболее распространенная червячная передача (рис. 2.10) состоит из так называемого архимедова червяка, то есть винта, и червячного колеса.
Рис. 2.10. Червячная передача
Червяки различают по следующим признакам:
по форме поверхности, на которой образуется резьба,
– цилиндрические (рис. 2.12, а)
– глобоидные (рис. 2.12, б);
по форме профиля резьбы
– архимедовы цилиндрические червяки
– эвольвентные цилиндрические червяки.
Архимедов червяк имеет трапецеидальный профиль резьбы в осевом сечении, в торцевом сечении витки резьбы очерчены архимедовой спиралью.
Эвольвентный червяк представляет собой косозубое зубчатое колесо с малым числом зубьев и большим углом их наклона. Профиль витка в торцевом сечении очерчен эвольвентой.
Фрикционные передачи
Передачи, работа которых основана на использовании сил трения, возникающих между рабочими поверхностями двух прижатых друг к другу тел вращения, называют ф р и к ц и о н н ы м и п е р е д а ч а м и.
В зависимости от назначения фрикционные передачи можно разделить на две основные группы:
- передачи с нерегулируемым передаточным отношением (рис. 2.15, а); - регулируемые передачи, называемые вариаторами, позволяющими плавно (бесступенчато) изменять передаточное отношение.
а)
б)
Рис. 2.15. Схемы фрикционных передач
По расположению осей
- с параллельными осями валов
- пересекающимися осями валов;
По поверхности катков
- с цилиндрической поверхностью рабочих катков;
- с конической поверхностью рабочих катков;
- с шаровой поверхностью рабочих катков;
- с торовой поверхностью рабочих катков;
По конструктивным особенностям
- с постоянным или автоматически регулируемым прижатием катков,
- с промежуточным фрикционным элементом или без него и т.д.
Ременные передачи
Ременная передача состоит из двух шкивов, закрепленных на валах, и охватывающего их ремня. Ремень надет на шкивы с определенным натяжением, обеспечивающим трение между ремнем и шкивами, достаточное для передачи мощности от ведущего шкива к ведомому.
В зависимости от формы поперечного сечения ремня различают:
- плоскоременную передачу (рис. 2.16, а),
- клиноременную передачу (рис. 2.16, б)
- круглоременную (рис. 2.16, в) передачу.
Рис. 2.16. Ременные передачи
Цепные передачи
Цепная передача состоит из двух колес с зубьями (звездочек) и охватывающей их цепи. Наиболее распространены передачи с втулочно-роликовой цепью (рис. 2.19, а) и зубчатой цепью (рис. 2.19, б). Цепные передачи применяются для передачи средних мощностей (не более 150 кВт) между параллельными валами в случаях, когда межосевые расстояния велики для зубчатых передач.
![]() | По назначению цепи подразделяют - на приводные, используемые в приводах машин; - тяговые, применяемые в качестве тягового органа в конвейерах, и грузовые, используемые в грузоподъемных машинах для подъема грузов. |
ОБЩИЕ СВЕДЕНИЯ О МЕХАНИЗМАХ И МАШИНАХ
1.1. Основные понятия
Основное назначение машин — увеличение производительности и облегчение физического и умственного труда человека. Созданные человеком машины позволяют в некоторых случаях заменять отдельные органы человека, например конечности (манипуляторы роботов). Механизмы отдельных видов машин помогают управлять производственными и другими процессами по определенным программам.
Машина — механическое устройство, выполняющее движения для преобразования энергии, материалов и информации с целью замены или облегчения труда человека.
Основными типами машин являются
- энергетические машины
- рабочие (технологические, транспортные) машины.
Энергетические машины предназначены для преобразования энергии любого вида в механическую, и наоборот.
Рабочие машины осуществляют изменение формы, свойств, состояния и положение предмета труда.
Составными частями машины являются механизмы, служащие для преобразования видов движения. Механизмы, входящие в состав машины, разнообразны. Они представляют собой сочетание твердых тел, а также пневматические, гидравлические, электромагнитные устройства и их сочетания.
В зависимости от функционального назначения механизмы подразделяют на следующие виды:
• механизмы двигателей и преобразователей;
• передаточные механизмы;
• исполнительные механизмы;
• механизмы управления, контроля и регулирования;
• механизмы подачи, транспортирования, питания и сортировки
|
|
Поперечные профили набережных и береговой полосы: На городских территориях берегоукрепление проектируют с учетом технических и экономических требований, но особое значение придают эстетическим...
Общие условия выбора системы дренажа: Система дренажа выбирается в зависимости от характера защищаемого...
Индивидуальные и групповые автопоилки: для животных. Схемы и конструкции...
Эмиссия газов от очистных сооружений канализации: В последние годы внимание мирового сообщества сосредоточено на экологических проблемах...
© cyberpedia.su 2017-2024 - Не является автором материалов. Исключительное право сохранено за автором текста.
Если вы не хотите, чтобы данный материал был у нас на сайте, перейдите по ссылке: Нарушение авторских прав. Мы поможем в написании вашей работы!