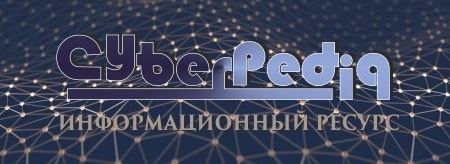
Историки об Елизавете Петровне: Елизавета попала между двумя встречными культурными течениями, воспитывалась среди новых европейских веяний и преданий...
Таксономические единицы (категории) растений: Каждая система классификации состоит из определённых соподчиненных друг другу...
Топ:
Оснащения врачебно-сестринской бригады.
История развития методов оптимизации: теорема Куна-Таккера, метод Лагранжа, роль выпуклости в оптимизации...
Особенности труда и отдыха в условиях низких температур: К работам при низких температурах на открытом воздухе и в не отапливаемых помещениях допускаются лица не моложе 18 лет, прошедшие...
Интересное:
Лечение прогрессирующих форм рака: Одним из наиболее важных достижений экспериментальной химиотерапии опухолей, начатой в 60-х и реализованной в 70-х годах, является...
Берегоукрепление оползневых склонов: На прибрежных склонах основной причиной развития оползневых процессов является подмыв водами рек естественных склонов...
Инженерная защита территорий, зданий и сооружений от опасных геологических процессов: Изучение оползневых явлений, оценка устойчивости склонов и проектирование противооползневых сооружений — актуальнейшие задачи, стоящие перед отечественными...
Дисциплины:
![]() |
![]() |
5.00
из
|
Заказать работу |
|
|
Этот метод состоит в том, что на рабочую поверхность деталей наносят углубления строго определенной геометрической формы (конус, пирамида, сфера и др.). При изнашивании поверхностного слоя детали происходит уменьшение глубины и других размеров углубления, по которым судят о величине линейного износа данного участка поверхности.
Метод предназначен для оценки местного или локального линейного износа деталей. Система углублений позволяет оценивать характер распределения износа на рабочей поверхности детали. Углубление наносят на поверхность детали методом отпечатков и методом вырезанных лунок (рис. 3.1).
Таблица 3.1
Характерные виды повреждений трущихся пар при различных режимах трения
Жидкостный режим трения | Смешанный или граничный режимы трения | Трение без подачи смазочного материала |
Усталостные повреждения (трещины, выкрашивание, отслоение). Износ за счет абразивного воздействия частиц, попадаемых с маслом. Кавитационные повреждения вкладышей (местные и общие по всей и большей части поверхности). Общие коррозионные повреждения или повреждения отдельных структурных составляющих. | Усталостные повреждения (трещины, выкрашивание, отслоение). Износ за счет абразивного воздействия частиц и схватывания на отдельных участках трущихся поверхностей. Образование глубоких и широких борозд, приводящих к задиру трущихся поверхностей. | Износ за счет схватывания, сопровождаемый вырывами и переносом металла с одной поверхности на другую. Образование глубоких и широких борозд, приводящих к задиру трущихся поверхностей. Износ за счет смятия (пластической деформации) трущихся поверхностей |
|
Рисунок 3.1 - Измерение износа методом искусственных баз:
а – метод отпечатков; б – метод лунок; в – метод слепков
Отпечатки обычно наносят четырехгранной алмазной пирамидой с квадратным основанием, углом при вершине между противоположными гранями 136° (такие пирамиды используют в твердомерах Виккерса и для измерения микротвердости). Глубину отпечатка h вычисляют по формуле:
, (3.1)
где d – длина диагонали отпечатка;
α – угол при вершине пирамиды между противоположными гранями.
При α = 136° величина h = 0,143d.
Линейный износ определяют как разность глубины отпечатков до и после испытаний. При α = 136°:
Δh = h1 – h2 = 0,143(d1 – d2), (3.2)
где h1, h2 – глубина отпечатка до и после испытания.
Длину диагонали отпечатка измеряют при помощи оптического измерительного устройства через микроскоп.
Использование отпечатков, наносимых с помощью прибора ПМТ-3, позволяет оценить интенсивность изнашивания отдельных структурных составляющих материала, если размер частиц позволяет наносить на них отпечатки микротвердости. Точность измерения линейного износа по отпечаткам микротвердости составляет доли микрометров (~0,3 мкм). Размеры диагоналей наносимых отпечатков обычно составляют 1 - 10 мкм.
В производственных условиях при измерении линейного износа в труднодоступных местах деталей больших размеров отпечатки наносятся коническими кернами из твердого сплава или закаленной стали или высверливают отверстия конической формы. В этом случае линейный износ определяют по формуле:
, (3.3)
где Δd = d1 – d2 (d1 и d2 – диаметры отпечатков до и после испытаний);
α – угол при вершине конуса.
При α = 120о величина Δh = 0,288Δd.
Диаметры отпечатков измеряют с помощью микроскопа МПГ-2, применяемого при определении твердости на приборе Бриннеля.
Этот метод также имеет ряд недостатков. На результат измерения размеров отпечатков влияет вспучивание металла по краям отпечатка. Поэтому перед измерением вспучивание удаляют шлифованием или полированием или проводят первое измерение после приработки деталей. Кроме того, форма отпечатков после снятия нагрузки заметно изменяется у материалов с высокими пределами текучести в результате упругого восстановления материала. Применение метода отпечатков затруднено, когда износ сопровождается пластической деформацией поверхностного слоя, приводящей к искажению формы и заплыванию отпечатков. При использовании метода микротвердости отпечатки довольно трудно обнаружить после испытания деталей.
|
Широкое распространение получил метод вырезанных лунок предложенный М.М. Хрущовым и Е.С. Берковичем. На поверхности детали с помощью вращающегося алмазного резца (резец имеет вид трехгранной призмы) вырезают углубление в форме остроугольной лунки (рис. 3.1, б). Глубину лунки определяют по формуле:
, (3.4)
где l –длина лунки;
r – радиус, описываемый вершиной резца;
R – радиус цилиндрической поверхности, на которой наносится лунка ("-" – для вогнутой поверхности; "+" – для выпуклой поверхности; R = ¥ - для плоскости).
Для плоской поверхности трения:
h = l2/8r. (3.5)
Линейный износ (D h) определяют по уменьшению глубины лунки. Для плоской поверхности трения линейный износ определяется по формуле:
, (3.6)
где l1 и l2 – длина лунки до и после испытаний.
Для цилиндрической поверхности трения износ вычисляются с учетом ее радиуса кривизны (R):
. (3.7)
Преимущества методов вырезанных лунок перед методом отпечатков – отсутствие выдавливания металла по краям лунки, изменения формы лунки, а также большая точность метода. Здесь вдавливание заменено резанием и явления вспучивания и упругого восстановления сведены к минимуму. Кроме того, имеется выгодное соотношение между глубиной лунки и ее длиной, составляющее 1:50 – 1:80 против 1:7 при методе отпечатков. Рекомендуется наносить лунки следующих размеров: l = 1 - 2 мм, h = 20,8 - 83,0 мкм. Поэтому уменьшение длины лунки легко измерить даже при незначительном износе. Точность метода лунок находится в пределах ± (1 - 2) мкм, а в отдельных случаях может достигать ± 0,5 мкм. Важно то, что усилия, необходимые для вырезания лунки, невелики, что позволяет создавать малогабаритные приборы.
|
Недостатки метода вырезанных лунок – невозможность применения его для измерения износа грубо отработанных поверхностей, а также для определения очень малого износа (порядка 1 мкм).
В ряде случаев более удобно наносить лунки абразивным (карборундовым или алмазным) диском.
При затруднении измерения износа непосредственно на детали применяют метод негативных отпечатков (рис. 3.1, в). С поверхности в том месте, где нанесено углубление (обычный отпечаток или специальная риска), снимают слепок при помощи самотвердеющей массы (например, стиракрила) или оттиск на пластичном металле или пластмассе. Высоту отпечатка измеряют обычными средствами и сравнивают с размером, снятым при вторичном оттиске изношенной поверхности.
Метод искусственных баз может быть использован для измерения износа только тех деталей, на поверхности которых допускается нанесение углублений. На базе метода лунок создан ряд приборов для измерения износа плоских, цилиндрических наружных и внутренних фасонных поверхностей в производственных и лабораторных условиях. Выпускается ряд приборов моделей T3.II для определения износа применительно к деталям разного назначения и геометрической формы согласно ГОСТ 23.301-78: модель 965 – для определения износа цилиндров гильз и поршневых колец двигателей внутреннего сгорания; модель 967 – для определения износа валов, в том числе шеек коленчатых валов; модель 966 – для определения износа плоских направляющих станин станков. Характеристики приборов представлены в таблице 3.2.
Таблица 3.2
Характеристики приборов моделей T3.II
Линейное увеличение объектива микроскопа | не менее 3,7 |
Числовая апертура объектива микроскопа | не менее 0,11 |
Цена наименьшего деления шкалы окуляра микроскопа, мм | 0,03 |
Радиус траектории вершины резца, мм | 11±0,1 |
Форма рабочей части алмазного резца РАИ-1 приведена на рисунке 3.2, а характеристики в таблице 3.3.
|
Рисунок 3.2 Форма рабочей части алмазного резца РАИ-1
Таблица 3.3
Характеристики резца РАИ-1
Угол a между осью и гранью | 65° ± 1° |
Угол между ребрами в плоскости грани | 115° |
Отклонение вершины алмазной пирамиды от оси оправки, мм | не более 0,23 |
Для точного определения износа зубьев шестерен используют метод искусственных баз, осуществляемый путем механического нанесения на рабочую поверхность зуба продольных и поперечных канавок с помощью алмазного резца. Канавки наносятся как вдоль длины зуба, так и по его высоте.
При измерении износа по нескольким лункам можно получить точную картину распределения износа или эпюру износа по поверхности трения деталей. На рисунке 3.3 показаны эпюры износа для цилиндрических поверхностей в радиальном направлении (по четырем поясам четырех цилиндров тракторного двигателя).
ПРИБОРЫ И МАТЕРИАЛЫ
|
|
Своеобразие русской архитектуры: Основной материал – дерево – быстрота постройки, но недолговечность и необходимость деления...
Состав сооружений: решетки и песколовки: Решетки – это первое устройство в схеме очистных сооружений. Они представляют...
История развития пистолетов-пулеметов: Предпосылкой для возникновения пистолетов-пулеметов послужила давняя тенденция тяготения винтовок...
Кормораздатчик мобильный электрифицированный: схема и процесс работы устройства...
© cyberpedia.su 2017-2024 - Не является автором материалов. Исключительное право сохранено за автором текста.
Если вы не хотите, чтобы данный материал был у нас на сайте, перейдите по ссылке: Нарушение авторских прав. Мы поможем в написании вашей работы!