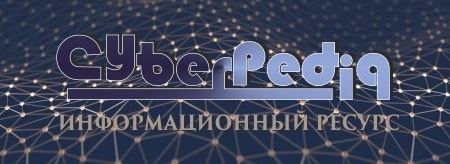
Общие условия выбора системы дренажа: Система дренажа выбирается в зависимости от характера защищаемого...
Индивидуальные очистные сооружения: К классу индивидуальных очистных сооружений относят сооружения, пропускная способность которых...
Топ:
Эволюция кровеносной системы позвоночных животных: Биологическая эволюция – необратимый процесс исторического развития живой природы...
Марксистская теория происхождения государства: По мнению Маркса и Энгельса, в основе развития общества, происходящих в нем изменений лежит...
Техника безопасности при работе на пароконвектомате: К обслуживанию пароконвектомата допускаются лица, прошедшие технический минимум по эксплуатации оборудования...
Интересное:
Подходы к решению темы фильма: Существует три основных типа исторического фильма, имеющих между собой много общего...
Искусственное повышение поверхности территории: Варианты искусственного повышения поверхности территории необходимо выбирать на основе анализа следующих характеристик защищаемой территории...
Мероприятия для защиты от морозного пучения грунтов: Инженерная защита от морозного (криогенного) пучения грунтов необходима для легких малоэтажных зданий и других сооружений...
Дисциплины:
![]() |
![]() |
5.00
из
|
Заказать работу |
|
|
Номер проверки | Что проверяется | Метод проверки | Ширина стола, мм | Прилагаемая сила Р, кГс | Допуск, мм | |
допускаемый | фактический | |||||
Н | Н | |||||
Выдвижную гильзу 1 шпинделя или фрезерную головку в станках с вертикальным шпинделем устанавливают в верхнее положение, поворотную головку – в нулевое положение. В отверстие шпинделя плотно вставляют оправку 2 (конусная часть образующей диска оправки наклонена к ее оси под углом γ) и жестко закрепляют шомполом. На столе жестко закрепляют устройство для создания нагружающей силы F. Перед каждым испытанием консоли, салазкам, столу и выдвижной гильзе шпинделя сообщают перемещения с последующей их установкой в заданное положение, а шпинделю – поворот. При этом консоль подводят в положение проверки перемещением снизу вверх, салазки – перемещением к зеркалу станины, а стол устанавливают в среднее положение перемещением справа налево. | 320 400 | 1250 1000 2000 1600 | 0,60 – 0,75 – |
Окончание табл.16
12 | Относительное перемещение под нагрузкой стола и оправки, закрепленной в шпинделе | При испытании поворотный стол и выдвижную гильзу шпинделя закрепляют. Консоль закрепляют на станине.
Индикаторы 3 укрепляют на устройстве для нагружения и непосредственно на столе так, чтобы их измерительные наконечники касались диска оправки.
Между столом и оправкой создают плавно возрастающую до заданного предела силу F, направление которой определяют углами.
Нагружающую силу прилагают к конусной части диска оправки и направляют через ось оправки. Ее величина устанавливается по индикатору 7 динамометра с помощью тарировочного графика. Нагружение до наибольшего значения силы производится ступенчато через равные интервалы. Затем производится разгрузка до нуля, также ступенчато. Одновременно индикаторами измеряют перемещение оправки относительно стола в трех направлениях. Результаты измерений заносятся в протокол.
Величину отжатий подсчитывают по формуле
![]() ![]() |
|
Графическое построение зависимости между нагрузкой и перемещением дает так называемые кривые жесткости. Нагружая и разгружая узел станка, можно получить точки на графике, которые, будучи соединены между собою, дают кривую, напоминающую петлю гистерезиса (рис. 44). Площадь, ограниченная кривой, представляет собой работу, затраченную на преодоление трения в стыках. Тангенс угла касательной, проведенной к кривой жесткости, представляет собой жесткость нагружаемого узла:
.
Величина z характеризует зазор в стыках между деталями нагружаемого узла при смене направления действия силы па противоположное.
Следует отметить, что испытания на жесткость проводят на том участке кривой Гука, где имеет место упругая деформация. Иначе, нагружая узел в области пластической деформации, можно необратимо сдеформировать детали проверяемого узла.
Рис. 44. График зависимости относительной суммарной податливости станка от нагрузки
КОНТРОЛЬ ЗНАНИЙ
1. Классификация металлорежущих станков.
2. Технико-экономические показатели станков.
3. Применение автоматизированного оборудования в зависимости от типа производства.
4. Методы формообразования на металлорежущих станках.
5. Обозначение моделей станков.
6. Приводы движений в металлорежущих станках.
7. Кинематические связи в металлорежущих станках.
8. Соединения кинематических цепей в металлорежущих станках.
9. Типы кинематических цепей в станках и их настройка.
10. Классификация станков токарной группы и развитие их автоматизации.
|
11. Кинематическая структура токарно-винторезных станков.
12. Токарно-лобовые и токарно-карусельные станки для обработки крупногабаритных тел вращения.
13. Особенности многорезцовых токарных станков.
14. Особенности токарно-револьверных станков.
15. Классификация и особенности конструкций токарных автоматов.
16. Одношпиндельные токарные автоматы.
17. Многошпиндельные токарные автоматы и полуавтоматы.
18. Станки сверлильно-расточной группы.
19. Компоновка и состав движений в горизонтально-расточных станках.
20. Особенности координатно-расточных станков.
21. Разновидности станков фрезерной группы.
22. Фрезерные станки для непрерывного фрезерования.
23. Специализированные фрезерные станки.
24. Формализация компоновок металлорежущих станков.
25. Агрегатные станки.
26. Схемы компоновок агрегатных станков.
27. Разновидности станков шлифовальной группы.
28. Бесцентрово-шлифовальные станки.
29. Особенности конструкции станков шлифовальной группы.
30. Классификация зубообрабатывающих станков и применяемые в них методы формообразования.
31. Кинематика зубодолбежного станка, вывод формулы настройки коробки скоростей зубодолбежного станка модели 514.
32. Кинематика зубодолбежного станка, вывод формулы настройки гитары обкатки (деления) зубодолбежного станка модели 514.
33. Кинематика зубодолбежного станка, вывод формулы настройки гитары радиальных подач зубодолбежного станка модели 514.
34. Кинематика зубодолбежного станка, вывод формулы настройки гитары круговых подач зубодолбежного станка модели 514.
35. Компоновка и состав рабочих движений в зубофрезерных станках.
36. Вывод формулы настройки гитары главного движения зубофрезерного станка модели 5Д32.
37. Вывод формулы настройки гитары подачи зубофрезерного станка модели 5Д32.
38. Вывод формулы настройки гитары деления зубофрезерного станка модели 5Д32.
39. Вывод формулы настройки гитары дифференциала зубофрезерного станка модели 5Д32.
40. Станки с ЧПУ.
41. Классификация систем ЧПУ.
42. Датчики обратной связи в станках с ЧПУ.
43. Точность систем ЧПУ в станках.
44. Конструктивные особенности механических передач станков с ЧПУ.
45. Многооперационные станки (обрабатывающие центры).
46. Разновидности устройств автоматической смены инструментов на многооперационных станках.
|
47. Технико-экономические преимущества многооперационных станков с ЧПУ.
48. Исполнительные приводы металлорежущих систем с ЧПУ.
49. Обоснование технической характеристики станков.
50. Основные требования, предъявляемые к металлорежущим станкам.
51. Порядок выполнения кинематических расчетов металлорежущих станков.
52. Множительные структуры коробок передач и их графическое изображение.
53. Понятие о структурных сетках.
54. Построение графиков частот вращения.
55. Построение кинематических схем приводов металлорежущих станков.
56. Приводы с бесступенчатым регулированием скорости.
57. Особые множительные структуры приводов станков.
58. Основные требования, предъявляемые к шпиндельным узлам станков.
59. Особенности конструкций шпиндельных узлов станков.
60. Проектирование шпиндельных узлов.
61. Подшипники качения и скольжения, применяемые в металлорежущих станках.
62. Классификация автоматических линий.
63. Назначение и классификация промышленных роботов.
64. Основные технические характеристики и компоновки промышленных роботов.
65. Правила эксплуатации производственного оборудования.
66. Транспортировка и установка станков.
67. Фундаменты для установки станков и их расчет.
68. Смазка механизмов, узлов и деталей в металлорежущих станках.
69. Испытания металлорежущих станков.
70. Организация ремонта металлорежущих станков.
ГЛОССАРИЙ
Автоматизация – применение технических средств с целью полной или частичной замены участия человека в процессах получения, преобразования, передачи и использования энергии, материалов или информации.
Адаптация – способность системы перестраивать свою структуру и(или) поведение в ответ на изменение внешних воздействий среды, сохраняя при этом значение некоторого показателя ее функционирования.
Адаптивная система – класс технических систем, обладающих способностью приспосабливаться как к изменяющимся условиям окружающей среды, так и к различным отклонениям от нормы в них самих. В основе адаптивных систем лежат обратные связи, поддержание которых осуществляется посредством специальных технических устройств – сенсорных, диагностических, контрольных.
|
Автоматизированное оборудование – совокупность устройств, механизмов, приборов, посредством которых осуществляется какой-либо производственный процесс, в результате которого от человека не требуется сознательного, постоянного регулирования этого процесса.
Автоматизированный привод – самодействующий привод, выполняющий работу с частичным участием человека.
Автоматический привод – самодействующий привод, выполняющий работу без участия человека.
Амортизация – процесс перенесения определенной части стоимости основных фондов по мере их износа на производственный продукт и использование для восстановления средств труда.
Безотказность – свойство товара (оборудования), характеризующее способность сохранять работоспособность в течение требуемого периода времени.
Гидропривод – устройство, предназначенное для приведения в действие оборудования и содержащее в себе источники энергии (насосы, аккумуляторы) и потребители энергии (гидравлические двигатели), а также аппаратуру, гидравлические линии (трубопроводы) и рабочую среду (рабочую жидкость).
Гибкое автоматизированное производство (ГАП) – автоматизированная производственная система, в которой на основе соответствующих технических средств и организационных решений обеспечивается возможность оперативной переналадки на выпуск новой продукции в достаточно широких пределах ее номенклатуры и параметров.
Долговечность – свойство объекта сохранять работоспособное состояние до наступления предельного состояния при установленной системе технического обслуживания и ремонта.
Качество продукции – совокупность технических, эксплуатационных, экономических и других свойств, обусловливающих ее пригодность для удовлетворения определенных потребностей.
Контроль – аналитическая функция управления, состоящая в наблюдении за ходом определенных процессов, сравнении величины контролируемого параметра с заданной программой, выявлении отклонений от программы.
Машина – техническое устройство, работа которого основывается на использовании механизмов и механического движения.
Материалоемкость – показатель расхода материала, вещества на единицу производимого изделия.
Механизация – замена ручных средств труда машинами и механизмами.
Методы управления – методы воздействия субъекта управления на объект по практическому осуществлению стратегических и тактических целей системы управления.
Надежность техники – свойство техники в течение заданного времени сохранять свою работоспособность, исправность и выполнять установленные функции.
|
Отказ – событие, заключающееся в нарушении исправного состояния объекта при сохранении его работоспособности.
Обратная связь – одно из основных понятий кибернетики, первоначально в теории регулирования – принцип подачи выходного сигнала на управляющий элемент схемы для его последующей корректировки.
Привод – совокупность источника движения (двигателя) и передач до рабочего органа машины.
Программирование – вид деятельности, необходимый для организации решения различных задач на ЭВМ.
Производство серийное и массовое – типы промышленного производства, отличающиеся узкой номенклатурой выпускаемых изделий, большим объемом и регулярностью изготовления однородной продукции.
Ремонт техники – восстановление работоспособности неисправной, т.е. отказавшей, поврежденной, изношенной или выработавшей установленный ресурс техники.
Робототехника, роботы – область науки и техники, связанная с изучением, созданием и использованием принципиального нового технического средства комплексной автоматизации производственных процессов – робототехнических систем.
Роторная линия – автоматическая линия машин, принцип действия которых основан на совместном движении по окружности инструмента и обрабатываемого им предмета.
Синхронизация – процесс согласования длительности операции с тактом поточной линии.
Станок металлорежущий – рабочая машина, предназначенная для формообразования изделий путем обработки металлов резанием.
Техника – совокупность механизмов и машин, а также систем и средств управления, добычи, хранения, переработки вещества, энергии и информации, создаваемых в целях производства и обслуживания непроизводственных потребностей общества.
Технологичность изделия – совокупность его свойств, обеспечивающих минимальные затраты ресурсов в производстве и эксплуатации.
Техническое обслуживание – комплекс работ, выполняемых в ходе эксплуатации техники с целью подготовки ее к использованию, а также для поддержания надежности и обеспечения эффективного применения.
Числовое программное управление (ЧПУ) – устройство для выработки сигналов управления оборудованием на основе программ, задаваемых человеком или вычислительными машинами (ЭВМ).
Эксплуатация техники – использование техники по назначению пеосле ее изготовления.
Эффективность – обобщающая характеристика качества экономического роста, соотношение между результатами и затратами или ресурсами.
СПИСОК ЛИТЕРАТУРЫ
1. Металлорежущие станки / под ред. В.Э.Пуша. – М.: Машиностроение, 1986.
2. Гондин, Ю.Н. Расчеты деталей фрезерных станков на прочность и жесткость: учеб. пособие / Ю.Н.Гондин [и др.]. – Горький: ГГУ им. Н.И.Лобачевского, 1978.
3. Лизогуб, В.А. Научные основы конструирования и технологии шпиндельных узлов металлорежущих станков / В.А.Лизогуб. – М.: Издательство «Научтехлитиздат», 2002.
4. Металлорежущие станки / под ред. В.К.Тепинкичиева. – М.: Машиностроение, 1973.
5. Устинов, Б.В. Обоснование основных технических характеристик и разработка кинематической схемы при проектировании металлорежущих станков: метод. указания / Сост.: Б.В.Устинов. – Горький: ГПИ им. А.А.Жданова, 1981.
6. Металлорежущие системы машиностроительных производств / под ред. Г.Г.Земскова и О.В.Таратынова. – М.: Высш. шк., 1988.
7. Моторин, Б.М. Эксплуатация металлорежущих станков: учеб. пособие / Б.М.Моторин. – Горький: ГПИ им. А.А.Жданова, 1973.
8. Устинов, Б.В. Токарный патронный полуавтомат модели 1П717Ф3 с устройством числового программного управления: метод. указания. Часть 1 / Сост.: Б.В.Устинов, Н.М.Чернышов. – Горький: ГПИ им. А.А.Жданова, 1987.
9. Гондин, Ю.Н. Многоцелевые станки с ЧПУ: метод. указания / Сост.: Ю.Н.Гондин, Б.В.Устинов, Н.М.Чернышов. – Горький: ГПИ им. А.А.Жданова, 1989.
10. Гондин, Ю.Н. Методические указания к лабораторным работам по курсу «Металлорежущие станки» для студентов специальности 0501. Часть V / Сост.: Ю.Н.Гондин. – Горький: ГПИ им. А.А.Жданова, 1979.
11. Научно-технический прогресс: словарь / под ред. В.Г.Горохов, В.Ф.Халипов. – М.: Политическая литература, 1987.
|
|
Наброски и зарисовки растений, плодов, цветов: Освоить конструктивное построение структуры дерева через зарисовки отдельных деревьев, группы деревьев...
Индивидуальные очистные сооружения: К классу индивидуальных очистных сооружений относят сооружения, пропускная способность которых...
Механическое удерживание земляных масс: Механическое удерживание земляных масс на склоне обеспечивают контрфорсными сооружениями различных конструкций...
История развития пистолетов-пулеметов: Предпосылкой для возникновения пистолетов-пулеметов послужила давняя тенденция тяготения винтовок...
© cyberpedia.su 2017-2024 - Не является автором материалов. Исключительное право сохранено за автором текста.
Если вы не хотите, чтобы данный материал был у нас на сайте, перейдите по ссылке: Нарушение авторских прав. Мы поможем в написании вашей работы!