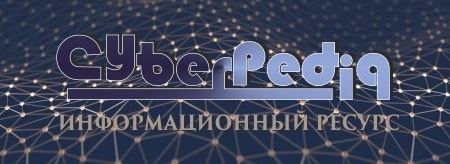
История развития пистолетов-пулеметов: Предпосылкой для возникновения пистолетов-пулеметов послужила давняя тенденция тяготения винтовок...
Таксономические единицы (категории) растений: Каждая система классификации состоит из определённых соподчиненных друг другу...
Топ:
Установка замедленного коксования: Чем выше температура и ниже давление, тем место разрыва углеродной цепи всё больше смещается к её концу и значительно возрастает...
Процедура выполнения команд. Рабочий цикл процессора: Функционирование процессора в основном состоит из повторяющихся рабочих циклов, каждый из которых соответствует...
Марксистская теория происхождения государства: По мнению Маркса и Энгельса, в основе развития общества, происходящих в нем изменений лежит...
Интересное:
Наиболее распространенные виды рака: Раковая опухоль — это самостоятельное новообразование, которое может возникнуть и от повышенного давления...
Инженерная защита территорий, зданий и сооружений от опасных геологических процессов: Изучение оползневых явлений, оценка устойчивости склонов и проектирование противооползневых сооружений — актуальнейшие задачи, стоящие перед отечественными...
Финансовый рынок и его значение в управлении денежными потоками на современном этапе: любому предприятию для расширения производства и увеличения прибыли нужны...
Дисциплины:
![]() |
![]() |
5.00
из
|
Заказать работу |
|
|
Все этапы проектирования, каждый шаг конструктора сопровождается расчётами. Это естественно, т.к. грамотно выполненный расчёт намного проще и в сотни раз дешевле экспериментальных испытаний.
Чаще всего конструктор имеет дело с расчётами на прочность. Оценка прочности элементов конструкции начинается с выбора модели (расчетной схемы). Моделью называют совокупность представлений, условий и зависимостей, описывающих объект расчета. При выборе модели учитывают наиболее значимые и отбрасывают несущественные факторы, которые не оказывают достаточно заметного влияния на условия функционирования элемента конструкции.
Для одной и той же детали может быть предложено несколько моделей расчета, которые будут отличаться глубиной описания реального объекта и условий его работы.
Обязательным является уточнение расчетных режимов на основе тщательного изучения возможных в эксплуатации случаев перегрузок.
Обычные методы расчета позволяют определить напряжения с удовлетворительной степенью точности лишь для сравнительно немногих простейших случаев нагружения. Иногда величина и распределение напряжений в теле деталей не поддаются расчету. Нередко сечения деталей определяются не столько прочностью, сколько технологией изготовления. К нерасчетным деталям относятся многие корпусные и базовые детали. Эффективность метода уточнения напряжения и уменьшения запасов прочности как средства снижения общей массы машин зависит от соотношения массы расчетных и нерасчетных деталей. Необходимо указать, что расчеты деталей основаны на упрощениях, которые не всегда выдерживаются в реальных условиях.
Главные факторы, обусловливающие отклонение истинных напряжений и запасов прочности от значений, определяемых расчетом, следующие:
|
рассеивание характеристик прочности материала по сравнению с номинальными значениями, представляющими собой среднее статистическое из ряда испытаний образцов;
неоднородность материала; рассеивание характеристик прочности в различных участках и точках сечений детали;
изменение прочности материала в зависимости от характера нагрузки (скорость и продолжительность нагружения);
отклонение расчетной схемы от действующих условий нагружения;
отклонение фактически действующих сил от номинальных значений;
отклонение фактических напряжений от номинальных, обусловленных влиянием упругости системы;
игнорирование в расчете прочности и жесткости деталей, сопряженных с рассчитываемой деталью;
местные напряжения на участках заделки деталей и приложения сил;
дополнительные силы и напряжения вследствие неточности изготовления, монтажа и установки (например, повышенные кромочные давления из-за несоосности или. перекосов опор);
перегрузки вследствие превышения расчетных режимов в эксплуатации;
масса и металлоемкость конструкций
внутренние напряжения, возникающие при изготовлении детали, а также обусловленные макро- и микронеоднородностью материала;
изменение характеристик прочности в связи с повышением температуры при работе детали.
Прочность - свойство конструкции выполнять назначение, не разрушаясь в течение заданного времени.
Показатели прочности материалов характеризуются удельной величиной — напряжением, равным отношению нагрузки в характерных точках диаграммы растяжения к площади поперечного сечения образца.
Выгодность материалов по массе можно оценить с помощью удельных показателей, характерных для каждого типа нагружения.
Удельная прочность — отношение предела прочности к плотности, характеризует прочность при одинаковом весе конструкции — чем выше, тем конструкция легче при одинаковой прочности.
|
Жесткость материала — свойство материала, отражающее способность материала сопротивляться нагрузке и не деформироваться (изгибаться, растягиваться). Чем больше деформация при приложении одинаковой нагрузки — тем жесткость ниже. При этом речь идет о восстановимой (упругой) деформации — то есть, при устранении нагрузки образец принимает первоначальную форму.
Жесткость определяет работоспособность конструкции в такой же (а иногда и в большей) мере, как и прочность. Повышенные деформации могут нарушить нормальную работу конструкции задолго до возникновения опасных для прочности напряжений. Нарушая равномерное распределение нагрузки, они вызывают сосредоточенные силы на отдельных участках деталей, в результате чего появляются местные высокие напряжения, иногда значительно превосходящие номинальные напряжения.
Нежесткость корпусов расстраивает взаимодействие расположенных в них механизмов, вызывая повышенное трение и износ подвижных соединений; нежесткость валов и опор зубчатых передач нарушает правильное зацепление колес и приводит к быстрому износу зубьев; нежесткость цапф и подшипников скольжения вызывает повышенные кромочные давления, появление очагов полужидкостного и полусухого трения, перегрев, заедание или снижение срока службы подшипников; нежесткость неподвижных соединений, подверженных действию динамических нагрузок, вызывает фрикционную коррозию, наклеп и сваривание поверхностей.
У машин-орудий жесткость рабочих органов определяет точность размеров обрабатываемых изделий. В металлорежущих станках точность обработки зависит от жесткости станин и рабочих органов, в прокатных станах точность проката - от жесткости клетей и валков.
Жесткость имеет большое значение для машин облегченного класса (транспортные машины, авиационная, ракетная техника). Стремясь облегчить конструкцию и максимально использовать прочностные ресурсы материалов, конструктор в данно,м случае повышает уровень напряжения, что сопровождается увеличением деформаций. Широкое применение равнопрочных, наиболее выгодных по массе конструкций, в свою очередь, вызывает увеличение деформаций, так как равнопрочные конструкции наименее жесткие.
|
Особую остроту приобретают вопросы жесткости в связи с появлением высокопрочных и сверхпрочных материалов, применив которых обусловливает резкое увеличение деформативности конструкций.
Нередки случаи недооценки сил, действующих на конструкцию. Очень часто при расчете получают ничтожные рабочие силы, а фактически же неожиданно возникают нагрузки, приводящие к поломкам и выходу из строя деталей. Эти нагрузки могут быть вызваны неточностями монтажа, деформаций недостаточно жестких элементов конструкции, остаточными деформациями, перетяжкой крепежных деталей, повышенным трением и перекосами трущихся частей узла, силами, возникающими при транспортировке и установке машины, и другими факторами, не учитываемыми расчетом.
Деформации можно рассчитать лишь в простейших случаях методами сопротивления материалов и теории упругости. В большинстве случаев приходится иметь дело с нерасчетными деталями, сечения которых определяются условиями изготовления (например, технологией литья) или имеющими сложную конфигурацию, затрудняющую определение напряжений и перемещений.
Здесь приходится прибегать к моделированию, эксперименту, опыту имеющихся аналогичных конструкций, а нередко полагаться только на интуицию, вырабатывающуюся с течением времени у конструктора. Опытный конструктор, зная действующие силы, определяет более или менее правильно деформации, выявляет слабые места и, пользуясь различными приемами, увеличивает жесткость, компонуя рациональную конструкцию. Напротив, конструкции, спроектированные начинающими конструкторами, обычно страдают недостатком жесткости.
Одинаковой жесткости конструкции (то есть способности противостоять нагрузке, не деформируясь), можно добиться двумя путями:
1. Применением более жесткого материала.
2. Увеличением сечения элемента конструкции.
Очевидно, что увеличение диаметра труб при том же материале вызовет увеличение количества материала — и соответственно веса.
Таким образом, из одного и того же материала получаются конструкции различной прочности и жесткости, и наоборот — одинаковой прочности и жесткости конструкции можно добиться при использовании различных материалов. Основное различие здесь — в весе.
|
Как уже неоднократно отмечалось в различных статьях, сталь — материал самый жесткий, самый прочный, но и самый тяжелый. Именно поэтому труба для стальной рамы будет небольшого диаметра (жесткость и так высока, прочность позволяет делать трубы тонкостенными, а большая плотность не дает увеличить диаметр трубы). В результате при нужной прочности и весе жесткость конструкции оказывается ниже, чем у столь же прочной алюминиевой конструкции подобного веса, особенно при равных размерах конструкций.
Сопротивление усталости. Повышение сопротивления усталости при кратковременных перегрузках объясняется деформационным упрочнением, происходящим при пластических деформациях микрообъемов материала, сходным с упрочнением при наклепе. Установлено, что под действием пластических деформаций происходят упрочняющие процессы: разупорядочение кристаллических решеток; увеличение плотности дислокаций; измельчение кристаллических блоков и увеличение степени их разориентировки; зубчатая деформация поверхностей спайности в результате выхода пластических сдвигов на поверхность зерна и, как следствие, увеличение связи между зернами.
Возрастание прочности, наблюдаемое при повышении уровня перегрузок до известного предела, можно объяснить прогрессивным увеличением числа микрообъемов, подвергающихся пластической деформации, и увеличением интенсивности дисперсионного упрочнения. На определенной стадии процесс упрочнения прекращается. Это наступает при таком уровне и частоте перемен напряжения, когда в материале возникают необратимые внутренние межкристаллитные повреждения, нарушающие сплошность материала.
Изучение сопротивления усталости при нестационарных режимах имеет большое принципиальное и прикладное значение, так как позволяет глубже узнать природу усталости, рациональнее использовать материал и точнее определять долговечность конструкций в эксплуатационных условиях. Однако расчет усложняется. Необходим огромный экспериментальный материал для того, чтобы выяснить закономерности изменения пределов выносливости при различных спектрах нагружения. Должны быть учтены факторы концентрации напряжений, состояния поверхности и т. д., влияние которых на вид кривых усталости при нестационарных режимах может быть иным, чем при стационарном нагружении, и очень значительным.
Наибольшее значение на современном этапе развития теории циклической прочности (в частности, прочности при нестационарных режимах) имеет изучение природы усталости с позиций металловедения и физики металлов. Без создания стройной металлофизической теории циклической прочности эмпирическое изучение последней будет только накоплением статистического материала, пригодного для использования в частных случаях инженерных расчетов.
|
Возникает также задача целесообразного использования наблюдаемых закономерностей упрочнения для повышения сопротивления усталости и долговечности конструкций, состоящая в разработке рациональных режимов «тренировки» деталей повышенными циклическими нагрузками, чередующимися с периодами отдыха. Наряду с этим необходима разработка методов деформационного упрочнения деталей дозированной пластической деформацией статическими и циклическими нагрузками.
Установлено, что предел выносливости образцов, нагружаемых циклическими растягивающими напряжениями, существенно увеличивается при предварительной деформации образца в результате происходящего при этом объемного наклепа материала. Особенно значителен эффект пластического деформирования при нагрузке того же знака, что и рабочая.
Деформирование создает в поверхностных слоях остаточные напряжения, противоположные по знаку рабочим напряжениям. Это явление, используемое в процессе заневоливания.
Повышение циклической прочности пружин можно применить для упрочнения других деталей, например валов, работающих на кручение, круговой или плоский изгиб.
Еще больший эффект дает совмещение зональной упругой или упругопластической деформации с внешним наклепом напряженных зон (наклеп в напряженном состоянии).
Контактная прочность. При контактном нагружении сила действует на малом участке поверхности, вследствие чего в поверхностном слое металла возникают высокие местные (локальные) напряжения. Этот вид нагружения встречается при соприкосновении сферических и цилиндрических тел с плоскими, сферическими или цилиндрическими поверхностями.
При теоретическом решении задачи о напряженном состоянии в зоне контакта упругих тел (Герц, Динник, Беляев, Фэппль) предполагают, что нагрузка статическая, материалы тел изотропны, площадка контакта мала по сравнению с поверхностями и действующие силы направлены нормально к этой плошадке.
В машиностроительных конструкциях нагрузка, как правило, бывает циющческр, вследствие периодического изменения действующей силы, а также вследствие относительного движения соприкасающихся тел.
В схемах нагружение имеет циклический характер, даже если действующая сила статическая, так как нагружению подвергаются последовательно различные точки поверхностей. Относительное перемещение соприкасающихся тел нарушает теоретическое (по Г. Герцу) распределение напряжений в зоне контакта. Поверхностный слой в зоне контакта подвергается сжатию и растяжению в тангенциальном направлении. Расположение зон сжатия и растяжения зависит от характера движения. При чистом качении зоны сжатия на обеих сопрягающихся поверхностях (зачерненные участки) расположены по одну сторону от центра контакта (встречно движению), по другую сторону материал подвергается растяжению.
При скольжении и качении со скольжением участок сжатия на опережающей поверхности расположен перед центром контакта (встречно движению), а на отстающей поверхности - наоборот; на противоположных участках материал подвергается растяжению.
В зоне сжатия опережающей поверхности происходит сближение и сдвиг волокон материала в направлении, указанном стрелками. В зоне растяжения волокна, упруго расправляясь, перемещаются в том же направлении. На отстающей поверхности волокна перемешаются в обратном направлении. В результате на поверхности контакта возникают силы трения, отклоняющие действующие силы от нормали к площадке контакта.
Из предыдущего ясно, что действительные условия в зоне контакта гораздо сложнее, чем при статическом нагружении, вследствие чего формулы, выведенные для случая статического нагружения, применимы только как первое приближение.
Долговечность циклически нагруженных соединений определяется сопротивлением усталости материала. Кривые сопротивления усталости при контактном нагружении в общем близки к кривым усталости для случаев одноосного напряженного состояния (растяжения, сжатия) с тем различием, что численные значения разрушающих напряжений гораздо выше и кривые не имеют отчетливо выраженного горизонтального участка предела выносливости.
Тепловые взаимодействия. В узлах, состоящих из деталей, имеющих различную рабочую температуру или изготовленных из материалов с разными коэффициентами линейного расширения, тепловые деформации могут существенно влиять на взаимное расположение деталей.
Осевые зазоры. При нагреве в соединениях возникают термические зазоры или натяги, которые необходимо учитывать при назначении сборочных (холодных) зазоров.
Примером может служить конструкция фиксирующего подшипника скольжения. Пусть вал изготовлен из стали с коэффициентом линейного расширения а, корпус подшипника - из сплава. Таким образом, в соединении возникает натяг 0,1 мм; вал будет защемлен в подшипнике. Если в рабочем состоянии должен быть обеспечен минимальный зазор, допустим 0,05 мм, то первоначальный холодный зазор должен быть равен 0,05 + 0,15 = 0,2 мм.
Выбор правильных торцовых зазоров имеет особое значение для многоопорных валов с подшипниками, находящимися на большом расстоянии один от другого.
Пусть передний подшипник А является фиксирующим. При нагреве картер удлиняется в направлении, указанном стрелкой. При назначении конструктивных зазоров к этим значениям следует прибавить первоначальные холодные зазоры, которые устанавливают с помощью размерного анализа по допускам на изготовление.
Расположение фиксирующих баз. Фиксирующие базы следует выбирать с таким расчетом, чтобы при всех возможных температурных изменениях размеров системы точность расположения деталей не нарушалась или нарушалась бы в наименьшей мере.
В узле конической передачи, установленной в корпусе из легкого сплава, фиксирующий подшипник расположен на значительном расстоянии от центра зацепления зубчатых колес. Удлинение корпуса при нагреве вызывает смещение малого колеса передачи в направлении, указанном стрелкой. Большое колесо перемещается в том же направлении, но на меньшую величину (вследствие меньшего значения коэффициента линейного расширения стального вала). В результате зазор в зацеплении уменьшается. При известных соотношениях зубчатые колеса могут начать работать враспор.
В правильной конструкции фиксирующим является задний подшипник, расположенный на сравнительно малом расстоянии от центра зацепления. Смещения колес относительно друг друга при нагреве здесь гораздо меньше; кроме того, зазор в зацеплении с нагревом увеличивается, а не уменьшается, как в предыдущем случае.
Обеспечение свободы температурным перемещениям. Следует избегать осевой фиксации деталей в двух точках. При наличии температурных деформаций в случае такой фиксации могут появиться термические напряжения, вызванные торможением смежности.
Примером ошибочной установки является фиксация вала в двух подшипниках качения одновременно. Если корпус подшипников выполнен из материала с иным коэффициентом линейного расширения, чем вал, а также если вал и корпус имеют различные рабочие температуры, то в узле возникает зазор или натяг. Последний может привести к защемлению подшипников. Неизбежные погрешности выполнения осевых размеров соединения, в свою очередь, могут вызвать появление зазоров или натягов.
Вал следует фиксировать в одном подшипнике. Второй подшипник должен быть плавающим, т. е. иметь свободу перемещения в осевом направлении.
Фиксация гильзы в двух точках - верхним буртиком и уплотняющим буртиком ошибочна. При нагреве гильзы возникают термические силы, сжимающие гильзу и растягивающие рубашку. В правильной конструкции гильза зафиксирована только верхним буртиком. Уплотнение выполнено скользящим; гильза имеет возможность свободно перемещаться относительно рубашки.
Следует обеспечивать свободу перемещения крепежных лап машины и агрегатов, нагревающихся при работе. Одну из лап (или ряд лап, расположенных в линию) закрепляют жестко; остальным придают свободу перемещения.
Упрочнение конструкции. При упругом упрочнении конструкции заранее придают деформации, противоположные деформациям при рабочем нагружении. Классическим примером этого способа упрочнения являются шпренгельные балки. В систему вводят тензоры стержни из высокопрочного материала. Натягивая стержни, в балке создают предварительные напряжения на стороне, ближайшей к стержням, - напряжения сжатия. Приложение рабочей нагрузки вызывает напряжения обратного знака. Сложение предварительных и рабочих напряжений существенно уменьшает конечные напряжения в балке. Напряжения растяжения в стержнях возрастают.
Освоено производство предварительно напряженных балок. В полку, противоположную действию нагрузки, закатывают стержни из высокопрочной проволоки, предварительно напряженные механически или термически (нагревом). Такие балки можно без нарушения преднатяга резать на куски произвольной длины.
В конструкции к нижней полке прикреплена предварительно напряженная накладка из высокопрочной листовой стали. К стальным балкам накладки приваривают, к балкам из легких сплавов приклепывают.
Другой пример упругого упрочнения - скрепление резервуаров, выполненных из легких сплавов, путем намотки стальной проволоки (или ленты) в один или несколько рядов. При намотке в стенках сосуда создаются напряжения сжатия, которые, вычитаясь из напряжений растяжения, возникающих под действием внутреннего давления, значительно уменьшают конечные напряжения в стенках сосуда. Напряжения растяжения в проволоке при приложении внутреннего давления возрастают.
При известных соотношениях напряжения в стенках сосуда под рабочей нагрузкой могут быть равны нулю или даже сохранять отрицательный знак. Стенки сосуда будут в этом случае испытывать под нагрузкой напряжения сжатия, уменьшенные по сравнению с напряжениями, созданными при скреплении. Подобные системы имеют смысл только в том случае, если материал скрепляющих элементов прочнее материала скрепляемых деталей. Создание предварительного напряжения позволяет разгрузить слабый материал и делает конструкцию в целом более прочной.
В качестве упрочняющих элементов применяют холоднотянутую проволоку и прутки, а также холоднокатаную ленту малых сечении, обладающие значительно более высокой прочностью, чем массивные горячекатаные профили.
Разновидностью упругого упрочнения является скрепление полых толстостенных цилиндрических деталей, подверженных действию высокого внутреннего давления. В данном случае не обязательно, чтобы скрепляющие элементы превосходили по прочности скрепляемые; эффект упрочнения здесь основан на своеобразном распределении напряжений по сечению детали.
В толстостенном сосуде, подвергающемся действию внутреннего давления, напряжения по Ламе максимально на внутренней поверхности стенки и падает к наружной. С целью упрочнения деталь изготовляют из двух труб; внутреннюю запрессовывают в наружную трубу с большим натягом. В наружной трубе возникают напряжения растяжения, а во внутренней - напряжения сжатия. В результате сложения предварительно возбужденных напряжений с рабочими пик растягивающих напряжений у внутренней стенки уменьшается, напряжения по сечению выравниваются, и прочность конструкции возрастает.
При пластическом упрочнении участки материала, наиболее нагруженные в рабочем состоянии, предварительно подвергают пластической деформации, создавая в них остаточные напряжения, противоположные по знаку рабочим.
Упрочнение перегрузкой заключается в воздействии на деталь повышенной силы того же направления, что и рабочая, вызывающей пластические деформации наиболее напряженных участков.
Термопластичное упрочнение основано на том, что при неравномерном нагреве в горячих участках детали возникают напряжения сжатия, а в холодных - напряжения растяжения. Их значение зависит от температурного перепада, коэффициента линейного расширения и модуля упругости материала. При достаточно больших температурных перепадах появляются местные пластические деформации, которые можно использовать для упрочнения.
|
|
Индивидуальные и групповые автопоилки: для животных. Схемы и конструкции...
История развития хранилищ для нефти: Первые склады нефти появились в XVII веке. Они представляли собой землянные ямы-амбара глубиной 4…5 м...
Типы сооружений для обработки осадков: Септиками называются сооружения, в которых одновременно происходят осветление сточной жидкости...
Биохимия спиртового брожения: Основу технологии получения пива составляет спиртовое брожение, - при котором сахар превращается...
© cyberpedia.su 2017-2024 - Не является автором материалов. Исключительное право сохранено за автором текста.
Если вы не хотите, чтобы данный материал был у нас на сайте, перейдите по ссылке: Нарушение авторских прав. Мы поможем в написании вашей работы!