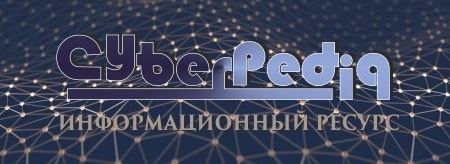
Наброски и зарисовки растений, плодов, цветов: Освоить конструктивное построение структуры дерева через зарисовки отдельных деревьев, группы деревьев...
Состав сооружений: решетки и песколовки: Решетки – это первое устройство в схеме очистных сооружений. Они представляют...
Топ:
Характеристика АТП и сварочно-жестяницкого участка: Транспорт в настоящее время является одной из важнейших отраслей народного хозяйства...
Проблема типологии научных революций: Глобальные научные революции и типы научной рациональности...
Интересное:
Искусственное повышение поверхности территории: Варианты искусственного повышения поверхности территории необходимо выбирать на основе анализа следующих характеристик защищаемой территории...
Отражение на счетах бухгалтерского учета процесса приобретения: Процесс заготовления представляет систему экономических событий, включающих приобретение организацией у поставщиков сырья...
Как мы говорим и как мы слушаем: общение можно сравнить с огромным зонтиком, под которым скрыто все...
Дисциплины:
![]() |
![]() |
5.00
из
|
Заказать работу |
|
|
Ряды | Модуль, мм |
1-й | 1; 1,25; 1,5; 2; 2,5; 3; 4; 5; 6; 8; 10; 12 |
2-й | 1,125; 1,375; 1,75; 2,25; 2,75; 3,5; 4,5; 5,5; 7; 9; 11; 14 |
Примечание. При назначении модулей 1-й ряд следует предпочитать 2-му. |
Значение модулей m < 2 мм в приводе главного движения использовать не рекомендуется из-за возможности большого понижения несущей способности в результате износа, повышенного влияния неоднородности материала, опасности разрушения при перегрузках.
Основные геометрические соотношения для некорригированных передач внешнего зацепления приведены в табл. 2.31.
Таблица 2.31
Геометрические параметры цилиндрических передач внешнего зацепления
без смещения, мм
Шаг зубьев, мм | p = πm |
Диаметр делительной окружности, мм | d = mz /cosβ |
Диаметр окружности вершин, мм | da = d + 2 m |
Диаметр окружности впадин, мм | df = d – 2,5 m |
Межосевое расстояние, мм | a = m (z 1 + z 2)/(2cosβ) |
Передаточное число | u = z 2/ z 1 |
Коэффициент торцового перекрытия | εα = [1,88 – 3,2(1/ z 1 + 1/ z 2)]cosβ |
Коэффициент осевого перекрытия | εβ = b sinβ/(π m) |
Примечание. Передаточное число u по ГОСТ 16532-70 определяется как отношение большего числа зубьев к меньшему независимо от того, как передается вращение: от z 1 к z 2 или от z 2 к z 1. |
Ширина зубчатых колес выбирается в соответствии с установленными эмпирическими соотношениями. В приводах главного движения для уменьшения концентрации нагрузки при высокой твердости зубьев и высоких окружных скоростях рекомендуется применять относительно неширокие колеса и придавать зубьям бочкообразную форму. Для прямозубых колес ширина зубчатого венца b = (6…10) m, для косозубых колес – b = (8…16) m. Коэффициент ширины колес ψ ba = b 2/ a рекомендуется принимать равным 0,1 – 0,2. Численные значения ψ ba регламентированы ГОСТом: 0,100; 0,125; 0,160; 0,200; 0,250 и т.д.
|
Учитывая возможное осевое смещение зубчатых колес при сборке передачи, ширину венца шестерни принимают на несколько миллиметров большей, чем ширину венца колеса:
b 1 = 1,12 b 2.
Межосевое расстояние a по возможности рекомендуется округлять по ряду Ra 40:…80; 85; 90; 95; 100; 105; 110; 120; 125; 130, далее через 10 до 260 и через 20 до 420.
Минимальное число зубьев у меньшего зубчатого колеса обычно ограничивается условием неподрезания зубьев у основания, для некорригированных передач z min = 17. В станкостроении минимальное число зубьев рекомендуется принимать z min = 21…24, а при работе передачи на высоких оборотах для уменьшения шума целесообразно брать z min≥ 25. Общие рекомендации по выбору числа зубьев шестерни некорригированной передачи представлены в табл. 2.32.
Таблица 2. 32
Число зубьев шестерни
Угол наклона линии зуба,β | Число зубьев шестерни |
β = 0º | z 1 ≥ 21 |
0º < β ≤ 12º | z 1 ≥ 19 |
12º < β ≤ 17º | z 1 ≥ 18 |
17º < β ≤ 21º | z 1 ≥ 17 |
Примечание. Ограничение по условию неподрезания для косозубых колес. |
В коробках скоростей металлорежущих станков числа зубьев колес подвижных зубчатых блоков выбираются по кинематическим условиям. По графику частот вращения для каждой передачи находят передаточное отношение и по табл. П22, исходя из условия равенства суммы зубьев Σ z ведущего и ведомого колес каждой группы передач при одинаковом модуле (сумма зубьев всех колес, находящихся между соседними валами, должна быть одинаковой) и в зависимости от передаточного числа u, определяются числа зубьев. В таблице приведены числа зубьев меньшего колеса передачи.
Таблица 2.33
Формулы для расчета сил в зацеплении
Сила, Н | Передачи | ||
прямозубые | косозубые | ||
Окружная, Ft | 2000 M / d | ||
Радиальная, Fr | Ft tgα | Ft tgα/cosβ | |
Осевая, Fa | отсутствует | Ft tgβ | |
Нормальная, Fn | Ft /cosα | Ft /(cosαcosβ) | |
Примечание. α – угол зацепления. Для некорригированных передач α = 20°.
|
На зубчатые колеса при передаче крутящего момента действует нормальная сила Fn, приложенная в полюсе зацепления. Для удобства расчета валов и подшипников силу Fn раскладывают на три взаимно перпендикулярные составляющие: окружную силу Ft, радиальную Fr и осевую Fa. Формулы для определения данных сил по заданным значениям момента M (Нм) и диаметра d (мм) представлены в табл. 2.33.
Расчет зубчатых передач
При передаче крутящего момента под действием нормальной силы Fn и сил трения зуб находится в сложном напряженном состоянии. Решающее влияние на его работоспособность оказывают два основных напряжения: контактные напряжения σ Н и напряжения изгиба σ F. Для каждого зуба σ Н и σ F не являются постоянно действующими. Переменные напряжения являются причиной усталостного разрушения зубьев: поломка зубьев от напряжений изгиба и выкрашивание поверхности от контактных напряжений. С контактными напряжениями и трением в зацеплении связаны также износ, заедание и другие виды повреждения поверхностей зубьев.
Поскольку в коробке скоростей привода главного движения зубчатые колеса закалены до высокой твердости, основным критерием их работоспособности является прочность на изгиб. С учетом того, что числа зубьев передачи выявляются на стадии кинематического расчета, расчет на прочность сводится к определению модуля по заданным числам зубьев с последующей проверкой на контактную и изгибную прочность (проверочный расчет).
Расчет модулей зубчатых передач
по критерию изгибной прочности
Модуль передачи по условию обеспечения изгибной прочности должен удовлетворять условию:
,
где YFS 1 - коэффициент формы зуба, рассчитываемый в зависимости от эквивалентного числа зубьев:
YFS = 3,47 + 13,2/ zE – 29,7 x / zE + 0,092 x 2;
где zE = z 1 – для прямозубых колес; zE = z 1/cosβ3 – для косозубых передач;
х – коэффициент смещения (для некорригированных колес х = 0);
YF β = 1 – для прямозубых колес, YF β = 0,8 – для косозубых колес;
KF = 1,3…1,5 – коэффициент расчетной нагрузки для шестерни. Меньшее значение принимается при расположении шестерни в середине вала между опорами. Большее значение – при нахождении шестерни рядом с опорой. Этот коэффициент при проверочном расчете подлежит уточнению;
|
М 1 – максимальный крутящий момент на шестерне, Нм. Рассчитывается по кинематической схеме привода;
z 1 – число зубьев шестерни;
ψ m = b / m = 6…10 – для прямозубых колес в подвижных зубчатых блоках;
σ FP 1 – допускаемое изгибное напряжение для материала шестерни, МПа.
Таблица 2.34
Пределы выносливости σ Flimb, σ Н limb и коэффициенты безопасности SF, SH при расчете на контактную и изгибную прочность
Вид термообработки | Марка стали | Твердость зубьев HRC | Модуль колеса m, мм | σ Hlimb, МПа | SH | σ Flimb, МПа | SF | |
на поверхности | в сердцевине | |||||||
Объемная закалка | 50ХНМ; 40Х; АЦ40Х и др. | 45…55 | 4…6 | 17 HRC +200 | 1,1 | 550 | 1,85 | |
1…4 | 500 | 1,85 | ||||||
Закалка ТВЧ по всему контуру | 55ПП; У6; 35ХМ; | 56…63 | 25…28 | 3…12 | 1050 | 1,2 | 900 | 1,75 |
40Х; 40ХН и др. | 45…55 | 600 | ||||||
Закалка ТВЧ сквозная с охватом впадины | 35ХМ; 40Х; 40ХН и др. | 45…55 | 45…55 | 1…3 | 500 | |||
Закалка ТВЧ сквозная до переходной поверхности | 400 | |||||||
Азотирование | 35ХЮА; | 55…67 | 24…40 | 1…6 | 650 | |||
38ХМЮА; 40Х; 40ХФА; 40ХНМА | 50…59 | |||||||
Цементация с автоматическим регулированием процесса, закалка с повторного нагрева | 12ХН3А; 20ХН3А; 20ХН2М и др. | 58…62 | 30…40 | 1,5…6 | 1380 | 950 | 1,55 | |
32…45 | 6…10 | |||||||
Цементация, закалка с повторного нагрева | 12ХН3А; 20ХН3А; 20ХН2М | 56…60 | 32…45 | 1,5…6 | 1300 | 800 | 1,65 | |
4…10 | ||||||||
20Х | 27…32 | 1,5…4 | 750 | |||||
Цементация, закалка с непосредственного нагрева | 18ХГТ | 56…60 | 30…43 | 1,5…6 | ||||
Нитроцементация с автоматическим регулированием процесса, закалка с непосредственного нагрева | 25ХГМ | 58…60 | 32…45 | 1,5…2 | 1350 | 1,2 | 1000 | 1,55 |
25ХГТ | 750 | |||||||
25ХГМ | 56…60 | 32…45 | 1,5…4 | 750 | 1,65 | |||
25ХГТ | 27…35 | 680 | ||||||
Нитроцементация, закалка с непосредственного нагрева | 25ХГМ | 32…45 | 750 | |||||
25ХГТ | 27…35 | 680 |
Допускаемое изгибное напряжение определяется приближенно по выражению:
σ FP = 0,4σ FlimbYN,
где σ Flimb – предел выносливости зубьев по напряжениям изгиба, табл. 2.34.
YN – коэффициент долговечности при изгибе:
,
где qF – показатель степени кривой усталости по изгибным напряжениям. Значение qF определяется по табл. 2. 35, при этом коэффициент YN не должен превышать максимального значения YN max;
NFE – эквивалентное число циклов перемены напряжений:
|
NFE = μ FN Σ,
где μ F – коэффициент приведения, табл. 2.35; N Σ – суммарное число циклов изменения напряжений за весь срок службы. Значение N Σ определяется приближенно для частоты вращения шестерни n 1 (мин-1) при максимальном крутящем моменте М 1:
N Σ = (55200…64400) n 1.
Меньшее значение N Σ принимается для универсального станка, большее – для специального. При NFE ≥ 4·106 коэффициент YN = 1.
Таблица 2.35
Показатели степени кривой усталости qF, qН
и коэффициенты приведения μ F, μ Н
Термообработка | qF | qH | μ F | μ Н | YN max | ZN max |
Зубчатые колеса с однородной структурой материала, включая закаленные при нагреве ТВЧ со сквозной закалкой, и зубчатые колеса со шлифованной переходной поверхностью, независимо от твердости и термообработки их зубьев | 6 | 6 | 0,038 | 0,125 | 4 | 2,6 |
Азотированные, цементированные и нитроцементированные зубчатые колеса с нешлифованной переходной поверхностью | 9 | 6 | 0,016 | 0,125 | 2,5 | 1,8 |
Примечание. Коэффициенты приведения μ F и μ Н приведены для режима нагружения, характерного для металлорежущих станков. |
В проверочном расчете σ FP уточняется.
Если зубчатая передача входит в подвижный зубчатый блок, то модуль m, определяется для каждой передачи, затем из полученных значений выбирается наибольшее и округляется в большую сторону по ГОСТ 9563-80.
После вычисления модуля определяется межосевое расстояние a (табл. 2.31), рассчитываются основные геометрические параметры передачи (табл. 2.31), выявляется окружная скорость колес и назначается степень точности передачи.
Если передача косозубая, то после выявления модуля m, выбирается угол β из условия коэффициента осевого перекрытия εβ ≥ 1,1:
β ≥ arcsin(4 m / b 2).
Рис. 2.31. Косозубые передачи с заданным межосевым расстоянием
Рекомендуемое значение β = 8…18°. Затем уточняется межосевое расстояние а (см. табл. 2.31). Если межосевое расстояние уже задано (например, конструкция на рис. 2.31), уточняется суммарное число зубьев: Σ z = (2 a cosβ)/ m с последующим округлением до целого числа в меньшую сторону и уточнением фактического значения угла β до шестого знака после запятой:
β = arcos(Σ zm /(2 a)).
Коэффициенты расчетной нагрузки
По ГОСТ 21354 – 87 коэффициенты расчетной нагрузки определяются как произведение коэффициентов:
K F = K FA K F αK F βK FV,
K H = K HA K H αK H βK HV,
где K A - коэффициент, учитывающий внешнюю динамическую нагрузку; Kα - коэффициент распределения нагрузки между зубьями, Kβ - коэффициент концентрации нагрузки; K V - коэффициент, учитывающий внутреннюю динамическую нагрузку.
|
Концентрация нагрузки и динамические нагрузки различно влияют на прочность по контактным и изгибным напряжениям. Соответственно различают:
· K H = K HA K H αK H βK HV - в расчетах по контактным напряжениям;
· K F = K FA K F αK F βK FV - в расчетах по напряжениям изгиба.
Коэффициент внешней динамической нагрузки K A в приводах главного движения металлорежущих станков следует принимать K HA = K FA = 1,25.
Таблица 2.36
Коэффициенты K F β и K Н β
| Угол наклона зубьев | Расположение передач | ||||||||||||||
симметричное | вблизи опоры | консольное | ||||||||||||||
Жесткость вала | ||||||||||||||||
любая | высокая | средняя | высокая | средняя | ||||||||||||
Степень точности по нормам плавности | ||||||||||||||||
4,5,6 | 7 | 8 | 4,5,6 | 7 | 8 | 4,5,6 | 7 | 8 | 4,5,6 | 7 | 8 | 4,5,6 | 7 | 8 | ||
K F β, K Н β | ||||||||||||||||
0,2 | β = 0º | 1 | 1,05 | 1,07 | 1,05 | 1,07 | 1,1 | 1,1 | 1,12 | 1,13 | 1,1 | 1,1 | 1,15 | 1,2 | 1,2 | 1,25 |
β > 0º | 1 | 1,07 | 1,1 | 1,07 | 1,1 | 1,14 | 1,14 | 1,17 | 1,18 | 1,14 | 1,14 | 1,21 | 1,28 | 1,28 | 1,35 | |
0,3 | β = 0º | 1,05 | 1,07 | 1,1 | 1,08 | 1,1 | 1,15 | 1,18 | 1,2 | 1,2 | 1,15 | 1,2 | 1,25 | 1,2 | 1,3 | 1,35 |
β > 0º | 1,07 | 1,1 | 1,14 | 1,11 | 1,14 | 1,21 | 1,25 | 1,28 | 1,28 | 1,21 | 1,28 | 1,35 | 1,28 | 1,42 | 1,49 | |
0,4 | β = 0º | 1,05 | 1,1 | 1,15 | 1,1 | 1,15 | 1,2 | 1,2 | 1,25 | 1,3 | 1,2 | 1,25 | 1,3 | 1,3 | 1,4 | 1,45 |
β > 0º | 1,07 | 1,14 | 1,21 | 1,14 | 1,21 | 1,28 | 1,28 | 1,35 | 1,42 | 1,28 | 1,35 | 1,42 | 1,42 | 1,56 | 1,63 | |
0,6 | β = 0º | 1,1 | 1,15 | 1,2 | 1,15 | 1,2 | 1,3 | 1,3 | 1,35 | 1,45 | 1,3 | 1,35 | 1,45 | 1,45 | 1,6 | 1,65 |
β > 0º | 1,14 | 1,21 | 1,28 | 1,21 | 1,28 | 1,42 | 1,42 | 1,49 | 1,63 | 1,42 | 1,49 | 1,63 | 1,63 | 1,84 | 1,91 | |
0,8 | β = 0º | 1,1 | 1,2 | 1,3 | 1,2 | 1,3 | 1,4 | 1,4 | 1,5 | 1,6 | 1,4 | 1,5 | 1,6 | 1,6 | 1,8 | 1,9 |
β > 0º | 1,14 | 1,28 | 1,42 | 1,28 | 1,42 | 1,56 | 1,56 | 1,7 | 1,84 | 1,56 | 1,7 | 1,84 | 1,84 | 2,12 | 2,26 | |
1 | β = 0º | 1,15 | 1,25 | 1,35 | 1,25 | 1,35 | 1,5 | 1,5 | 1,6 | 1,75 | – | – | – | – | – | – |
β > 0º | 1,21 | 1,35 | 1,49 | 1,35 | 1,49 | 1,7 | 1,7 | 1,84 | 2,05 | – | – | – | – | – | – | |
Примечание. Коэффициенты K F β и K Н β приведены для зубчатых колес, используемых в коробках скоростей и редукторах станков. |
Коэффициент распределения нагрузки между зубьями Kα определяется в зависимости от степени точности (n СТ) изготовления зубчатых колес по нормам плавности. Для прямозубых передач:
K H α = 1 + 0,06(n СТ – 5), при 1 ≤ K H α ≤ 1,25.
Для косозубых передач при твердости поверхностей зубьев шестерни H1 > 350HB и колеса H2 > 35HB:
K H α = 1 + 0,15(n СТ – 5), при 1 ≤ K H α ≤ 1,6.
В расчетах на прочность по напряжениям изгиба полагают K F α = K H α, для прямозубых колес K F α =1. Отметим, что для точно изготовленных передач K H α = 1.
Коэффициенты K F β и K Н β, учитывающие концентрацию нагрузки по ширине зубчатого венца, зависят от расположения колес относительно опор, материала передачи, ширины венца и степени точности передачи. При конструировании передачи необходимо учитывать все факторы, влияющие на концентрацию нагрузки, и в первую очередь учитывать жесткость валов, опор и корпусов. Приближенные значения K F β и K Н β определяются по табл. 2.36.
Коэффициенты K FV и K Н V выбирают по табл. 2.37 в зависимости от степени точности передачи по нормам плавности, твердости зубьев, наклона зуба и окружной скорости. Коэффициент K FV = K Н V при условии, что оба колеса передачи закалены до высокой твердости H > 350HB.
Таблица 2.37
Коэффициенты K FV и K Н V динамической нагрузки
Степень точности |
| Угол наклона зубьев | Окружная скорость V, м/с | ||||||
1…3 | 3…6 | 6…9 | 9…12 | 12…15 | 15…18 | 18…24 | |||
5 | 10…100 | β = 0º | 1 | 1,05 | 1,05 | 1,1 | 1,1 | 1,15 | 1,15 |
β > 0º | 1 | 1,025 | 1,025 | 1,05 | 1,05 | 1,075 | 1,075 | ||
100…200 | β = 0º | 1 | 1,05 | 1,1 | 1,15 | 1,15 | 1,2 | 1,3 | |
β > 0º | 1 | 1,025 | 1,05 | 1,075 | 1,075 | 1,1 | 1,15 | ||
6 | 10…100 | β = 0º | 1 | 1,05 | 1,1 | 1,1 | 1,15 | 1,2 | 1,25 |
β > 0º | 1 | 1,025 | 1,05 | 1,05 | 1,075 | 1,1 | 1,125 | ||
100…200 | β = 0º | 1,05 | 1,1 | 1,15 | 1,2 | 1,2 | 1,3 | 1,35 | |
β > 0º | 1,025 | 1,05 | 1,075 | 1,1 | 1,1 | 1,15 | 1,175 | ||
7 | 10…100 | β = 0º | 1 | 1,05 | 1,1 | 1,15 | – | – | – |
β > 0º | 1 | 1,025 | 1,05 | 1,075 | – | – | – | ||
100…200 | β = 0º | 1,05 | 1,1 | 1,15 | 1,25 | – | – | – | |
β > 0º | 1,025 | 1,05 | 1,075 | 1,125 | – | – | – | ||
8 | 10…100 | β = 0º | 1 | 1,1 | 1,15 | – | – | – | – |
β > 0º | 1 | 1,05 | 1,075 | – | – | – | – | ||
100…200 | β = 0º | 1,05 | 1,15 | 1,2 | – | – | – | – | |
β > 0º | 1,025 | 1,075 | 1,1 | – | – | – | – | ||
Примечания: 1. Коэффициенты K FV и K Н V приведены для нормально и тяжело нагруженных зубчатых передач. 2. Коэффициенты K FV и K Н V приведены для зубчатых передач при H1 > 350HB и H2 > 350HB. |
Проверочный расчет цилиндрических зубчатых передач
на выносливость при изгибе
Расчетное местное напряжение от изгиба рассчитывается в опасном сечении на переходной поверхности ножки зуба, МПа:
σ F = Ft K FYFSYF β Y ε/(bm) ≤ σ FP,
где Ft – расчетная окружная сила, Н (см. табл. 2.33); K F – коэффициент расчетной нагрузки при изгибе; YFS - коэффициент формы зуба; YF β = 1 – εββº/120 ≥ 0,7 – коэффициент, учитывающий наклон зуба; b – ширина зубчатого венца; Y ε – коэффициент, учитывающий перекрытие зубьев:
· для прямозубых передач Y ε =1;
· для косозубых передач при εβ < 1: Y ε = 0,2 + 0,8/εα;
· для косозубых передач при εβ ≥ 1: Y ε = 1/εα,
где εβ - коэффициент осевого перекрытия, табл. 2.31; εα - коэффициент торцового перекрытия, табл. 2.31.
Допускаемое напряжение изгиба σ FP, МПа:
σ FP = σ Flimb YNY δ YRYX / SF,
где σ Flimb - предел выносливости зубьев по напряжениям изгиба, табл. 2.34.
YN - коэффициент долговечности при изгибе по формуле.
SF - коэффициент безопасности при расчете на изгиб, табл. 2.34.
Y δ - опорный коэффициент, отражающий чувствительность материала зубьев к концентрации напряжений:
Y δ = 1,082 – 0,172lg m,
где m – модуль зуба, мм.
YR – коэффициент, учитывающий шероховатость переходной поверхности:
· при зубофрезеровании и шлифовании YR = 1;
· при полировании YR = 1,05…1,2:
a) цементация, нитроцементация, азотирование YR = 1,05;
б) нормализация и улучшение YR = 1,2;
в) при закалке ТВЧ, когда закаленный слой повторяет очертание впадины между зубьями YR = 1,05;
г) при сквозной закалке ТВЧ по всему сечению зуба YR = 1,2.
YX - коэффициент, учитывающий размеры зубчатого колеса:
· при d ≤ 400мм, YX = 1;
· при d > 400мм, YX = 1,05 – 0,000125 d.
Допускаемое напряжение σ FP определяется раздельно для шестерни и колеса. Если хотя бы в одном случае расчетное напряжение σ F превысит допускаемое σ FP, необходимо либо изменять термообработку и материал колес, либо выбирать больший модуль m, с последующим пересчетом всех геометрических параметров передачи и проверкой контактной и изгибной прочности.
Проверочный расчет на контактную выносливость зубьев
Расчетное контактное напряжение в полюсе зацепления, МПа:
,
где Ft - расчетная окружная сила, Н (табл. 2.33); K Н - коэффициент расчетной нагрузки при расчете по контактным напряжениям; b 2 - ширина зубчатого венца колеса, мм; d 1 - диаметр делительной окружности шестерни, мм; u – передаточное число;
ZH - коэффициент, учитывающий форму сопряженных поверхностей зубьев в полюсе зацепления и определяемый по рис. 2.32, в зависимости от угла наклона зубьев β и суммарного коэффициента смещения X Σ: ZH = 1,76 для прямозубых передач при угле зацепления α = 20° и X Σ = 0;
ZЕ - коэффициент, учитывающий механические свойства материалов сопряженных зубчатых колес: для стали при модуле упругости Е = 2,11·105 МПа и коэффициенте Пуассона n = 0,3, ZЕ = 274 МПа;
Z ε - коэффициент, учитывающий суммарную длину контактных линий:
· для прямозубых передач ;
· для косозубых передач ,
где εα - коэффициент торцового перекрытия, табл. 2.31.
Рис. 2.32. Коэффициент ZH
Допускаемое контактное напряжение σ HP, МПа:
σ HP = σ HlimbZNZLZRZXZV / SH,
где σ Hlimb - базовый предел контактной выносливости, табл. 2.34.
SH - коэффициент безопасности, табл. 2.34.
ZL = 1 - коэффициент, учитывающий влияние смазочного материала;
ZR - коэффициент, учитывающий параметр шероховатости поверхностей зубьев колес; ZR = 1 при Ra ≤ 1,25 мкм, ZR = (0,9…0,95) в остальных случаях;
ZX - коэффициент, учитывающий размеры зубчатого колеса:
· при d ≤ 1000 мм: ZX = 1;
· при d > 1000 мм: .
ZV - коэффициент, учитывающий окружную скорость V, м/с: при H > 350HB определяется ZV = 0,925 V 0,05;
ZN - коэффициент долговечности:
· при
;
· при
,
где ZN max - максимальное значение коэффициента долговечности, табл. 2.35;
NHlim - базовое число циклов перемены напряжений; определяется в зависимости от твердости поверхности зубьев по Бринеллю по табл. 2.38.
Таблица 2.38
Базовое число циклов NHlim
H, HB | 200 | 250 | 285 | 450 | 520 | 530 | 550 | 560 и более |
NHlim | 107 | 17·106 | 23,4·106 | 70·106 | 99·106 | 104·106 | 113·106 | 120·106 |
График для пересчета единиц твердости HRC и HV в единицы твердости по Бринеллю HB представлен на рис. 2.33.
NHE - эквивалентное число циклов перемены напряжений:
NHE = μ HN Σ,
где μ H - коэффициент приведения при расчете на контактную выносливость, табл. 2.35; N Σ - суммарное число циклов изменения напряжений за весь срок службы.
Рис. 2.33. Соотношение твердостей HB, HRC, HV
Величины расчетных контактных напряжений одинаковы для шестерни и колеса, поэтому за расчетное допускаемое контактное напряжение принимают:
· для прямозубых передач наименьшее допускаемое контактное напряжение: σ HP = min(σ HP 1; σ HP 2), где σ HP 1 - допускаемое контактное напряжение для шестерни, σ HP 2 - допускаемое контактное напряжение для колеса;
· для косозубых передач: σ HP = 0,45(σ HP 1 + σ HP 2).
Конструкция зубчатых колес
Конструкция зубчатых колес зависит от геометрических размеров, способа получения заготовки, применяемого материала, технологии изготовления и других факторов.
При соотношении диаметров колеса и вала менее двух, или если толщина стенки в корпусе колеса между впадиной зуба и шпоночным пазом менее двух модулей, целесообразно давать конструкцию в виде вала-шестерни. В остальных случаях подобные конструкции – сборные с применением шпоночного или шлицевого соединения. Изготавливают зубчатые колеса из прутка при небольших габаритных размерах в условиях мелкосерийного производства (рис. 2.34, а) или ковкой в штампах (рис. 2.34, б) в условиях среднесерийного производства. Соотношения размеров зубчатого колеса следующие:
b = (6…10) m; d СТ = 1,6 d; S = 3 m;
S СТ = 0,5(d СТ – d); f = 0,6 m; C = (0,35…0,4) b;
R ≥ 6 мм; L СТ = (1…1,5) d; D = mz,
где m – модуль зубьев, мм; d – внутренний диаметр ступицы (диаметр вала, на который устанавливается зубчатое колесо), мм; z – число зубьев на колесе. Выточки глубиной 1...2 мм на боковой поверхности зубчатого колеса (рис. 2.34, а) диаметром менее 80 мм допустимо не делать.
В коробках скоростей часто используются зубчатые блоки из двух колес (рис. 2.35) для переключения которых используются специальная вилка 1, соединяемая с подвижным блоком колес через радиальный шариковый подшипник 2. Длину ступицы колеса 3 необходимо согласовывать с расчетной длиной шпонки 4 по передаваемому крутящему моменту. Причем данное условие относится также и к одиночным зубчатым колесам.
Сборные конструкции зубчатых блоков применяются в приводах, если окружная скорость передачи более 6 м/с, поскольку профиль зуба необходимо шлифовать. При скоростях менее 6 м/с допустимо зубчатый блок делать монолитным с расстоянием между колесами в 6…8 мм для выхода долбяка при нарезании зубчатого профиля на колесе.
Располагаться зубчатые колеса на валу должны таким образом, чтобы ступицы колес находились на участке вала, передающим крутящий момент. Например, в схеме привода на рис. 2.12, а у первой пары колес, передающей вращение с первого вал на второй, ступицы у зубчатых колес должны находиться с разных сторон. У ведущего колеса слева, у ведомого – справа, так как именно на этих участках происходит закручивание валов. Ступицы способствуют выравниванию напряжений смятия в шпоночных (или шлицевых соединениях).
![]() | ![]() |
а) | б) |
Рис. 2.34. Варианты формы зубчатого колеса получаемой:
а - точением из прутка; б - штамповкой с последующим точением
Рис. 2.35. Конструкция сборного зубчатого колеса
РЕМЕННЫЕ ПЕРЕДАЧИ
Ременные передачи широко применяются в приводах главного движения токарных, фрезерных и шлифовальных станков для сообщения вращательного движения, как валам коробок скоростей, так и непосредственно шпинделя.
Основные достоинства ременных передач обусловлены способностью смягчать ударную нагрузку при резании, обеспечивать плавную и бесшумную работу и возможностью вращаться с высокими окружными скоростями, что особенно актуально для современных режимов резания. Однако необходимо иметь в виду, что ременные передачи дают дополнительную нагрузку на опоры валов от сил предварительного натяжения ветвей ремня, не гарантируют постоянство передаточного отношения в передачи из-за возможности проскальзывания ремня по рабочей поверхности шкивов (в особенности при попадании масла) и обладают относительно невысокой долговечностью ремня.
В станкостроении в основном используются три разновидности ременных передач: клиноременная, поликлиновая и зубчато-ременная, основные технические характеристики которых приведены в табл. 2.39.
Таблица 2.39
|
|
История развития хранилищ для нефти: Первые склады нефти появились в XVII веке. Они представляли собой землянные ямы-амбара глубиной 4…5 м...
Архитектура электронного правительства: Единая архитектура – это методологический подход при создании системы управления государства, который строится...
Типы сооружений для обработки осадков: Септиками называются сооружения, в которых одновременно происходят осветление сточной жидкости...
Историки об Елизавете Петровне: Елизавета попала между двумя встречными культурными течениями, воспитывалась среди новых европейских веяний и преданий...
© cyberpedia.su 2017-2024 - Не является автором материалов. Исключительное право сохранено за автором текста.
Если вы не хотите, чтобы данный материал был у нас на сайте, перейдите по ссылке: Нарушение авторских прав. Мы поможем в написании вашей работы!