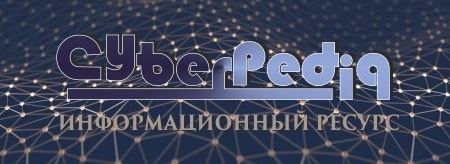
Механическое удерживание земляных масс: Механическое удерживание земляных масс на склоне обеспечивают контрфорсными сооружениями различных конструкций...
Таксономические единицы (категории) растений: Каждая система классификации состоит из определённых соподчиненных друг другу...
Топ:
Отражение на счетах бухгалтерского учета процесса приобретения: Процесс заготовления представляет систему экономических событий, включающих приобретение организацией у поставщиков сырья...
Оценка эффективности инструментов коммуникационной политики: Внешние коммуникации - обмен информацией между организацией и её внешней средой...
Особенности труда и отдыха в условиях низких температур: К работам при низких температурах на открытом воздухе и в не отапливаемых помещениях допускаются лица не моложе 18 лет, прошедшие...
Интересное:
Как мы говорим и как мы слушаем: общение можно сравнить с огромным зонтиком, под которым скрыто все...
Отражение на счетах бухгалтерского учета процесса приобретения: Процесс заготовления представляет систему экономических событий, включающих приобретение организацией у поставщиков сырья...
Берегоукрепление оползневых склонов: На прибрежных склонах основной причиной развития оползневых процессов является подмыв водами рек естественных склонов...
Дисциплины:
![]() |
![]() |
5.00
из
|
Заказать работу |
|
|
Дебутанизатор К-2 выводится на режим после вывода установки на нормальный технологический режим.
Для вывода К-2 на режим собирается схема циркуляции К-2: Фракция С3-С5 с Е-4 ® насосы Н-36,37 ® межтрубное пространство Т-4® трубное Т-22®К-2® трубное пространство Т-4®Х-6® прием Н-29® трубопровод подачи фракции С3-С5.
Избыток фракции с низа К-2 (пентан-изопентановой) должен быть выведен на СЖГ.
Набирается уровень в К-2 до 70% шкалы вторичного прибора, включается теплообменник Т-5(1) по пару и поднимается температура в К-2 в соответствии с нормами технологического режима.
При появлении уровня в Е-3 подать орошение на верх К-2.
При достижении качества отвечающего требованиям СТП фракция С3-С4 с верха колонны К-2 откачивается на СЖГ, АГФУ-2 или ТСЦ, а низ колонны К-2 пентан-изопентановая фракция выводится на СЖГ.
Остановка установки
Нормальная остановка установки производится по письменному распоряжению начальника цеха или его заместителя под непосредственным руководством начальника установки в следующих случаях:
а) при регенерации катализатора;
б) при остановке на ремонт;
в) при заранее известном прекращении подачи сырья, водорода, оборотной воды и т.д.
Для остановки установки необходимо предупредить:
а) диспетчера НПЗ, НХЗ и объединения.
б) работников товарной группы площадки «Д».
в) цеха № 32,33,9,51 о прекращении приема водорода.
г) работников установок Л-35/6, Л-35/11-1000, гидроочистки дизтоплива, Л-16-1 о прекращении приема водородсодержащего газа и прекращении сдувок отработанного, работников 35/6, СЖГ, ТК-2, 35-11-1000, парк АВТ, Л-16-1, ЭЛОУ-АВТ-4, ГО-2,3.
д) установку элементарной серы о прекращении подачи сероводорода
|
е) факельное хозяйство об. 645 и НХЗ о возможных сбросах.
ж) цех КИП и электроцех.
з) цех водоснабжения и работников оперативной службы по теплоснабжению.
и) лабораторию.
1. Отключить технологические блокировки.
2. Снизить загрузку по Оренбургскому конденсату со скоростью 15-20 м3/ч до 40% производительности с одновременным снижением загрузки на гидроочистку.
3. Продолжать циркуляцию по змеевикам печей П-1,5,6, с плавным снижением температуры в кубах колонн К-1,3,4.
4. Дальнейшее уменьшение загрузки на реакторный блок производить с переводом сырья помимо Е-9 в Е-25.
5. При достижении загрузки на реакторном блоке 20 м3/ч остановить насосы Н-13¸18, сырье из К-1 перевести помимо Е-9 в Е-25 полностью, перевести откачку фракции НК-62, 62-85, 85-180 в К-3, 180-КК в Е-25, прекратив прием Оренбургского конденсата.
6. Продолжить циркуляцию продукта по блоку подготовки сырья и ректификации с одновременным снижением температур низа и верха колонн.
7. Циркуляцию водородсодержащего газа по системе реакторного блока продолжить в течение 5-8 часов для удаления адсорбированного продукта с поверхности катализатора при рабочих условиях процесса.
8. Снизить подпитку свежего водорода в систему и сдув отработанного водорода из системы.
9. Уменьшить подачу фракции С3-С5 в К-2, снизить температуру К-2 уменьшением количества подачи пара в подогреватели Т-5(1,2) и Т-22. Откачку фракции С3-С5 полностью перевести в колонну К-3 на орошение, вывод фракции С5 с установки закрыть.
Для дальнейшего охлаждения колонны К-2 включить в работу схему циркуляции колонны К-2: Х-6 ®Н-29® Т-4®Т-22® К-2®Т-4®Х-6.
10. Откачать оставшийся продукт из Е-3 в К-11, остановить насосы Н-11,12.
11. Перепустить насыщенный раствор МЭА из К-11 в К-10 на регенерацию и отключить колонну К-11 задвижками.
12. Прекратить вывод бокового погона из колонны К-1, остановить насосы Н-9,10.
13. Отключить теплообменники Т-1а, Т-2 по межтрубному пространству, направляя фракцию 180-КК по байпасам, остановить закачку конденсата в Е-25 и загрузку колонны К-1, включив насосы Н-1,2.
|
14. Снизить температуру в низу колонны К-1 до 70¸90°С со скоростью 20-25°С/ч, потушить форсунки печи П-1, циркуляцию горячей струи по змеевикам П-1 продолжать до полного охлаждения колонны, а затем откачать продукт из К-1 в емкость Е-25 или с установки и остановить насосы Н-7,8.
15. Откачать остатки продукта из емкости Е-1 мимо Е-9 и остановить насосы Н-5,6.
16. Освободить от бензина полностью сепаратор С-1 в С-3, а из С-3 в К-3 и отключить их по бензину от блока ректификации.
17. Прекратить подачу МЭА (ТЭА) в К-9, перепустить МЭА (ТЭА) с глухой тарелки в К-10 на регенерацию и отключить колонну по подаче МЭА (ТЭА) и его выходу.
18. Снизить температуру в низу колонны уменьшением подачи топлива к форсункам печей П-5,6, а при достижении температуры 70-90°С со скоростью 20-25°С/ч, потушить форсунки печей, продолжая циркуляцию горячих струй по змеевикам печей.
19. Снизить температуру в низу колонны К-5 до 70-80°С со скоростью 20-25°С/ч путем снижения расхода пара в подогреватель Т-10.
20. Откачать продукт из емкости Е-4 в колонну К-2 и остановить насосы Н-36,37.
21. Прекратить подачу МЭА (ТЭА) в колонну К-12, остановить насосы Н-32,33, перепустить МЭА (ТЭА) до бензина из К-1 в К-10 через С-6 на регенерацию и отключить колонну по МЭА (ТЭА) и бензину.
22. После снижения температуры в низу колонны К-3 прекратить циркуляцию горячей струи через П-5 и остановить насосы Н-38,39, а продукт передавить в колонну К-4 остаточным давлением.
23. Перекачать продукт из емкости Е-5 в колонну К-5 и закрыть паровое питание из К-4 в К-5.
24. Прекратить циркуляцию горячей струи через змеевики печи П-6, откачать продукт с низа колонны К-4 в емкость Е-25 или с установки и остановить насосы Н-34,35.
25. Откачать продукт из Е-6 в Е-25 или с установки и остановить насосы Н-46,47.
26. Откачать продукт с низа колонны К-5 в емкость Е-25 или с установки и остановить насосы Н-48,49.
27. Остановить все воздушные вентиляторы холодильников воздушного охлаждения по блокам подготовки сырья и ректификации и закрыть задвижки на откачке продуктов с установки.
28. После десорбции углеводородов с поверхности катализатора приступить к снижению температуры в слое катализатора до 150°С со скоростью 10-20°С в час. Закрыть свежий водород на установку.
29. При температуре 150°С в слое катализатора потушить форсунки печи П-2 и приступить к снижению давления в системе, открыв сдув водорода в топливную сеть со скоростью 0,3-0,5 МПа (3-5 кгс/cм2) в час.
|
30. Прекратить подачу МЭА (ТЭА) в К-8, остановить насосы Н-26,27, перепустить МЭА (ТЭА) с глухой тарелки через сепаратор С-6 в колонну К-10 на регенерацию и отключить задвижками колонну К-8 по МЭА (ТЭА). Регенерацию МЭА (ТЭА) продолжать пока не восстановится раствор, т.е. не прекратится выход сероводорода из сепаратора С-7. Содержание сульфидов должно быть не более 0,7% мас. в регенерированном растворе МЭА (ТЭА) из Е-8.
31. Выдавить остаток МЭА из С-6 топливным газом через Т-1 в К-10, провести регенерацию, снизить температуру в низу колонны уменьшением подачи пара в подогреватель Т-13, перепустить МЭА (ТЭА) из колонны К-10 через Т-12, ВХ-4, Х-7 в Е-8, остановить насосы орошения К-10, Н-24,25, закрыть сброс сероводорода с установки и отключить воздушные холодильники ВХ-4, ВХК-9, воду в ХК-9 закрыть.
32. Сбросить давление с аппаратов блока подготовки сырья, ректификации и очистки газов, кроме К-8, на факел через Е-21, Е-24, и приступить к освобождению змеевиков печи П-1,5,6 и всех аппаратов от бензина в емкость Е-10 с последующей откачкой в парк площадки «Д» или на другие установки, перерабатывающие Оренбургский конденсат по линии некондиции, которая врезается в линию сырья установки до отсекающей задвижки в емкость Е-25, а по МЭА (ТЭА) в емкость Е-11.
33. При давлении 0,6-0,8 МПа (6-8 кгс/cм2) в системе остановить компрессор ЦК-1, сбросить давление водорода на факел до 0,2 МПа (2 кгс/cм2) и приступить к подготовительным работам по регенерации катализатора.
6.14 Выжиг кокса из змеевиков печи П-2
Паровоздушный метод удаления кокса из труб печи наиболее приемлем для печей, змеевики которых состоят из легированных хромомолибденовых или хромовольфрамовых и аустенитных труб, которые достаточно теплоустойчивы, при нагреве до высокой температуры не делают заметного появления окалины и имеют большую толщину стенок.
Очистка труб от кокса обусловлена следующим:
При разложении углеводородов в радиантных трубах образуется кокс, который частично выносится из печи и частично оседает.
|
Отложенный кокс внутри труб уменьшает сечение труб, в связи, с чем понижается производительность печей и ухудшается теплопроводность, возрастает перепад температур между наружной поверхностью труб и потоком, что приводит к перегреву труб и в конечном итоге - прогару.
Удаление кокса, выжиг его производится паровоздушным методом с выбросом продуктов горения в дымовую трубу.
Удаление кокса из змеевиков печей является ответственной операцией и должна выполняться квалифицированным персоналом.
Подготовка к выжигу кокса
После продувки реакционной системы азотом и удаления из нее углеводородов и водорода на факел, установить паспортные заглушки на выходе из Т-6/1 в печь и на входе в реактор, после чего соединить линию выхода газов регенерации из печи в дымовую трубу.
Снять заглушку на линии подачи пара к змеевику печи, на входе пара и воздуха в змеевик печи.
Выжиг кокса
1. Зажечь две форсунки печи и поднять температуру на выходе из печи со скоростью 50°С в час до 250°С, подавая через змеевики печи азот от воздушных компрессоров установки ГО-4.
2. Осторожно, не допуская гидроударов, дать пар в змеевик печи, постепенно повышая его количество до 16 т/ч (по 2 тонны на поток), после чего подачу азота прекратить.
3. Поднять температуру на выходе из печи со скоростью 50°С в час. При температуре на выходе из печи 580°С осторожно дать воздух в змеевик печи, медленно открывая задвижку на линии входа воздуха в линию пара. Не допускать попадания пара обратным ходом в линию воздуха. Давление в печи держать 0,2-0,3МПа (2-3 кгс/cм2). При выжиге кокса температуру паровоздушной смеси на выходе из печи держать не более 650°С.
Температура перевалов должна быть в пределах норм технологического режима.
Контроль температуры должен вестись по приборам с регистрацией показаний.
4. Следить за состоянием и цветом труб змеевика печи. Начало горения кокса в трубах змеевика определяется по посветлению поверхности труб. Не допускать нагрева труб ярче темно-красного цвета для П-2.
5. В том случае, если горение сразу не начинается, приступить к постепенному осторожному добавлению воздуха.
Постоянно следить за цветом труб. При появлении признаков горения кокса отрегулировать подачу пара и воздуха, т.е. стабилизировать процесс горения.
При необходимости: если кокс не загорается, подачу пара сократить до минимума вплоть до полного закрытия, количество подаваемого воздуха увеличить. Если в этом случае кокс загорится, то необходимо дать пар в змеевики для отрегулирования нормального цвета труб.
6. Окончание выжига определяется одинаковым составом воздуха на входе и выходе из печи, т.е. содержание О2 и СО2 постоянно на входе и выходе.
|
7. После полного выжига, приступить к снижению температуры на перевалах со скоростью 50°С в час.
Продуть змеевики печей паром в указанном выше количестве (см. п.2) в течение одного часа.
8. По достижении температуры на выходе из змеевика 100°С закрыть подачу пара и воздуха в змеевик, потушить рабочие форсунки.
9. Отглушить линии подачи пара на выжиг.
10. Приступить к промывке водой змеевиков печи, для чего:
а) собрать схему подачи воды в змеевик печи;
б) заполнить змеевик печи водой и отрегулировать расход воды 0¸30м3/ч.
11. Зажечь рабочие форсунки печи с расчетом равномерного прогрева всех змеевиков и довести температуру на выходе из печи не более 70¸80°С.
12. Промывку вести в течение 2-3 часов до появления чистой воды после змеевиков печей.
13. По окончании промывки потушить форсунки, прекратить подачу воды и отглушить врезки в линии «пар воздух в печь».
14. Произвести опрессовку змеевиков печи с целью выявления возможных дефектов. Давление испытания должно соответствовать паспортным данным.
15. После опрессовки змеевика печи продуть азотом для удаления из них воды. Для полного удаления воды зажечь форсунки и довести температуру перевалов до 150-200°С.
Продувку закончить после того, как на выходе из печи будет идти азот без признаков пара и влаги. После этого потушить форсунки, охладить змеевики печи, прекратить подачу азота.
|
|
Опора деревянной одностоечной и способы укрепление угловых опор: Опоры ВЛ - конструкции, предназначенные для поддерживания проводов на необходимой высоте над землей, водой...
Архитектура электронного правительства: Единая архитектура – это методологический подход при создании системы управления государства, который строится...
Историки об Елизавете Петровне: Елизавета попала между двумя встречными культурными течениями, воспитывалась среди новых европейских веяний и преданий...
Типы сооружений для обработки осадков: Септиками называются сооружения, в которых одновременно происходят осветление сточной жидкости...
© cyberpedia.su 2017-2024 - Не является автором материалов. Исключительное право сохранено за автором текста.
Если вы не хотите, чтобы данный материал был у нас на сайте, перейдите по ссылке: Нарушение авторских прав. Мы поможем в написании вашей работы!