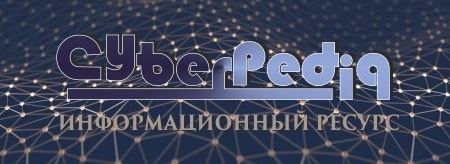
Поперечные профили набережных и береговой полосы: На городских территориях берегоукрепление проектируют с учетом технических и экономических требований, но особое значение придают эстетическим...
Автоматическое растормаживание колес: Тормозные устройства колес предназначены для уменьшения длины пробега и улучшения маневрирования ВС при...
Топ:
Установка замедленного коксования: Чем выше температура и ниже давление, тем место разрыва углеродной цепи всё больше смещается к её концу и значительно возрастает...
Генеалогическое древо Султанов Османской империи: Османские правители, вначале, будучи еще бейлербеями Анатолии, женились на дочерях византийских императоров...
Интересное:
Национальное богатство страны и его составляющие: для оценки элементов национального богатства используются...
Финансовый рынок и его значение в управлении денежными потоками на современном этапе: любому предприятию для расширения производства и увеличения прибыли нужны...
Распространение рака на другие отдаленные от желудка органы: Характерных симптомов рака желудка не существует. Выраженные симптомы появляются, когда опухоль...
Дисциплины:
![]() |
![]() |
5.00
из
|
Заказать работу |
|
|
Прием электроэнергии производится после:
а) окончания ремонтных работ электросистемы установки и оформления документов;
б) получения разрешения энергосбыта на прием электроэнергии;
в) согласования с электроцехом.
Прием электроэнергии производит персонал высоковольтной службы электроцеха совместно с персоналом установки по договоренности с предприятием, снабжающим электроэнергией (ТЭЦ), управление высоковольтных сетей.
Перед приемом необходимо убедиться в отсутствии каких-либо работ на электросхеме и электроагрегатах, а также необходимо оповестить всех работающих на установке о приеме электроэнергии.
6.4 Прием на установку моноэтаноламина (триэтаноламина)
На установку МЭА (ТЭА) привозится в автоцистернах. Из цистерны МЭА (ТЭА) насосом Н-28 перекачивается в емкость Е-12.
Для приготовления раствора МЭА (ТЭА) концентрации не более 15% в емкость Е-12 насосом Н-55(56) подается паровой конденсат.
Раствор МЭА (ТЭА) из емкости Е-12 насосом Н-28 перекачивается в емкость Е-8, откуда насосами Н-26,27 и Н-32,33 подается в колонны К-8,9,11,12.
Система МЭА (ТЭА) перед закачкой в нее приготовленного раствора, промывается паровым конденсатом для удаления грязи, окалины и других отложений.
Пуск установки
Пуск установки производится в следующей последовательности:
1. Подготовка к пуску.
2. Сушка, восстановление и сульфидирование катализатора.
3. Пуск блоков установки.
4. Пуск котла-утилизатора согласно инструкции № 9565.
6.5.1 Подготовка к пуску
6.5.1.1 Загрузка катализатора.
6.5.1.2 Испытание на герметичность.
6.5.1.3 Продувка и испытание на герметичность блоков подготовки, стабилизации и ректификации, очистки газов.
|
6.5.1.1 Загрузка катализатора
Перед загрузкой катализатора вся система (аппаратура, трубопроводы) должна быть тщательно очищена от всякого рода загрязнений, промыта, продута, высушена.
Продувку реакторного блока от загрязнений рекомендуется производить инертным газом.
Перед загрузкой в реакторы рекомендуется производить отсев мелочи от свежего катализатора. Отсев мелочи от катализатора, бывшего ранее в употреблении, обязателен. Рассев катализатора должен производиться на специальном оборудовании, предусматривающем улавливание катализаторной пыли.
Недопустимо попадание дождя или снега на катализатор во время загрузки, рассева, т.к. при этом резко снижается прочность катализатора.
Загрузка катализатора в реакторы должна производиться способом, предотвращающим его истирание или дробление.
Бочки с катализатором должны перемещаться с помощью механических приспособлений, катализатор из бочек пересыпается в загрузочные бункеры, которые поднимаются к горловине реактора.
При засыпке катализатора в реакторы используются тканевые рукава, погружаемые в реактор до уровня насыпаемого слоя.
Чтобы уменьшить давление на нижний слой катализатора и тем самым сохранить его прочность, а также для предотвращения износа катализатора должна предшествовать загрузка фарфоровых шаров Æ 20мм слоем 240мм.
Нежелательные термические реакции удается свести до минимума, заполняя катализатором максимальную часть объема реактора, насколько это совместимо с прочими проектными показателями.
Перед засыпкой из каждой бочки отбирается проба катализатора для составления средней пробы всей партии. Поверх катализатора засыпаются фарфоровые шары слоем 300мм. После окончания загрузки катализатора, монтажа верхних распределительных тарелок, закрыть люка, катализатор продуть в течение 30-40 минут путем подачи азота в трубопровод на входе в реактор с выходом в дымовую трубу по линии сброса газов регенерации.
|
Инертный газ должен быть достаточно сухим, чтобы не допустить образование на катализаторе капельной влаги. После продувки штуцер сброса газов регенерации отглушить и производить опрессовку реактора на рабочее давление совместно со всей системой блока.
Сушка катализатора производится азотом или водородсодержащим газом.
6.5.1.2 Испытание на герметичность реакторного блока
Перед включением в работу периодически действующих систем продувок и испытаний на плотность обеспечить тщательную проверку исправности трубопроводов, арматуры, аппаратов, приборов КИП и А и предохранительных устройств.
Испытание систем высокого давления гидроочистки производится путем опрессовки азотом на максимальное рабочее давление.
1. Е-9 воздушник до отсекающей задвижки.
прием насосов Н-13¸18®выкид Н-13¸18®межтр.пр-воТ-6(1).
2. Азот на выкид ЦК-1 ® межтр. пр-во Т-6(1) ® Т-7(1,2,3) ® Т-6® П-2®
Х-14
Р-1®Т-6® Т-18® Т-7(3шт) ®Т-6(1) ®ВХК-3® ®С-1®К-8®
Х-14а
® С-5а® С-5® свеча (воздушник)
3. С-1® Т-8(1) ®С-3® Х-15® К-9
4. Опрессовать систему гидроочистки на рабочее давление, включив воздушный компрессор на азоте по схеме: азот от ПК-5 ® Р-1.
Опрессовку системы высокого давления производить следующим образом: после заполнения аппаратов и трубопроводов инертным газом, равномерно, в течение часа, поднять давление до 0,5 МПа (5 кгс/см2) и прекратить подъем давления, произвести обмыливание фланцевых соединений.
В случае наличия дефектов, пропусков, давление в системе сбросить и устранить дефекты. После этого поднять давление до 0,5 МПа (5 кгс/см2).
При удовлетворительных результатах опрессовки продолжить плавный подъем давления со скоростью 0,5 МПа (5 кгс/см2) в час с остановками, обмыливанием и выявлением дефектов при давлении 1 МПа (10 кгс/см2), 2 МПа (20 кгс/см2), 3 МПа (30 кгс/см2), 4 МПа (40 кгс/см2) и далее до рабочего.
После опрессовки и устранения всех дефектов реактор готов к сушке катализатора.
Скорость подъема давления в системе производится со скоростью не более 5 кгс/см2 в час.
Выполнение всех операций по испытанию системы на герметичность производится согласно ПБ 09-540-03.
|
6.5.1.3 Продувка на проходимость и испытание на герметичность блоков установки
Опрессовка системы осуществляется инертным газом на максимальное рабочее давление из системы высокого давления.
Продувка аппаратов и трубопроводов всех блоков азотом до содержания кислорода не более 0,5% объемных.
А) Блок подготовки сырья.
1. Азот на прием насоса Н-1,2 ® прием Е-25 ® свеча.
2. Азот на прием насоса Н-1,2 ® трубное пространство Т-1® Т-1А® Т-2® К-1®ВХК-1® Е-1 ® свечи (воздушник)
Н-5,6 ® воздушник на клапане регулятора расхода
орошения К-1 (поз.210д).
Ф-1,2® Е-9® свеча (воздушник).
3. Азот на прием Н-7,8 ® обратным ходом ® К-1
® межтр. пр-во Т-2 ® П-1 ®К-1
® межтр. пр-во Т-1А ® ВХ-1 ® свеча на КРУ К-1
(поз.304е)
4. Азот с К-1®боковой погон®Н-9,10® Ф-1,2 ® Е-9® свеча (воздушник).
Опрессовать колонну и связанные с ней аппараты на 0,25 МПа (2,5кгс/см2).
Б) Блок ректификации.
Для продувки системы ректификации, а также для опрессовки используется азот из системы гидроочистки.
1. С-1® Т-8(1) ®С-3® Т-8(2) ® Т-3 ® Т-9 ® Т-11 ® К-3 ® Т-8(1,2) ® ВХК-5 ® ХК-5 ® Е-4 ® свеча.
2. Азот на прием Н-36,37®Т-4 ®Т-22® К-2® Т-4® Х-6®воздушник.
К-3
3. Азот на прием Н-36,37® К-2® К-12® свеча (воздушник)
4. Азот на прием Н-11,12 ® К-2®ВХК-2 ® ХК-1®свеча® Е-3®свеча
К-11®свеча
5. Азот на прием насосов Н-38,39 ® Т-18® П-5® К-3®Е-4® Х-15®К-9
ВХК-6® Е-5®свеча
6. К-3 ® К-4 ® К-5 ® ВХК-7® Е-6®свеча
7. Азот на прием Н-34,35 ® П-6® К-4
Т-9®Т-3® ВХК-8® Х-5 ® воздушник.
К-5
8. Азот на прием Н-46,47 ® Х-3® воздушник.
Азот на прием Н-48,49 ® ВХ-3 ® Х-4 ® воздушник.
К-5
10. Опрессовать колонну К-3 и связанные с ней аппараты азотом из С-1 на 1,25 МПа (12,5 кгс/см2).
11. Опрессовать колонну К-4 и связанные с ней аппараты на 0,45 МПа (4,5 кгс/см2).
|
12. Опрессовать колонну К-5 и связанные с ней аппараты на 0,3 МПа (3 кгс/см2).
В) Блок очистки газов.
® К-9® топливная сеть ®газ к печам П-1,2,5,6 ® Т-15 ®
®коллекторы печей П-1,2,5,6 ® свеча.
Азот на ® К-9®С-6® Т-12 ® К-10
Прием ® К-11 ® трубопровод фракции (С3-С4) с установки®
Н-32,33 ® воздушник
® ® К-11 ® С-6® Т-12 ® К-10
® К-12 ® трубопровод фракции С3-С4 с установки®
® воздушник
® К-12 ® С-6® Т-12 ® К-10
Азот на К-10 ®ВХК-9 ®ХК-9®С-7® трубопровод сероводорода с
прием ® установки ® воздушник.
Н-24,25 К-10 ® Т-12 ®ВХ-4 ®Х-7®Ф-5,6®Е-8® свеча.
1. Опрессовать колонну К-9 азотом на 0,8 МПа (8 кгс/см2) через съемную катушку.
2. Опрессовать колонну К-10 и связанные с ней аппараты на 0,16 МПа (1,6 кгс/см2) азотом из общей линии.
3. Опрессовать колонну К-11 на 2,4 МПа (24 кгс/см2) азотом от компрессора ПК-5 по временному трубопроводу.
4. Опрессовать колонну К-12 на 1,4МПа (14 кгс/см2) азотом от воздушника компрессора по временному трубопроводу.
5. Продуть факельный трубопровод через ручные сбросы от ППК из всех аппаратов с выходом азота через воздушник и опрессовать его на 0,05 МПа (0,5 кгс/см2).
6. Продуть дренажный коллектор нефтепродуктов в Е-10 со всех аппаратов на факел через Е-24 в Е-10, коллектор МЭА в Е-11 из аппаратов связанных с МЭА на свечу из Е-11.
После продувки и опрессовки всех блоков, аппаратов и трубопроводов сбросить давление азота через свечи и воздушники в атмосферу и приступить к приему конденсата и водорода.
Пуск блока подготовки сырья, гидроочистки и ректификации производится одновременно, при необходимости - раздельно.
Прием газообразного топлива
При приеме газообразного топлива на установку необходимо:
1. Продуть линии топлива инертным газом.
2. Опрессовать линии топлива к печам до форсунок инертным газом.
3. При давлении инертного газа в топливной линии не менее 1МПа (10 кгс/см2) проверить герметичность вентилей форсунок.
4. Отглушить все форсунки паспортными заглушками.
5. Проверить работу регулирующих клапанов, приборов КИП и А.
6. Давление инертного газа сбросить до нуля, все воздушники отглушить.
7. Привести в рабочее состояние клапаны-регуляторы давления, температуры.
8. Поставить в известность диспетчера НПЗ о приеме топлива.
9. Сделать направление топливного газа к подогревателю Т-15.
10 Открыть постепенно общую задвижку на линии газа, принять газ к печам.
11. Продуть все участки топливной линии на факел у каждой печи в течение 15-20 мин.
12. Продуть все коллекторы печи П-1,2,5,6 на факел для подогрева коллекторов.
13. Розжиг форсунок печей производится в присутствии ИТР цеха, перед розжигом форсунок необходимо:
|
а) продуть печи паром в течение не менее 15 минут с момента появления пара из дымовой трубы.
б) снять заглушку на подаче топливного газа к форсунке печи, немедленно зажечь форсунку, розжиг остальных форсунок производить идентично, по необходимости.
Подготовка реакторного блока к сушке и прокалке катализатора
Перед сушкой и прокалкой катализатора тщательно продуть систему реакторного блока азотом до содержания кислорода до 0,5% объемных, подаваемого с компрессора ПК-5 на выкид турбокомпрессора ЦК-1.
Систему продуть по схеме: трубопровод азота в трубопровод подачи сырья на РБ ® Т-6(1) ® Т-7(1,2,3) ® Т-6 ® П-2 ® Р-1 ®Т-6 ®Т-18 ®
Х-14
®Т-7(3,2,1)®Т-6(1)®ВХК-3® С-1®К-8®С-5а®С-5® свеча.
Х-14а
При достижении содержания кислорода в продувочном азоте не более 0,5% объемных прекратить выдув.
|
|
Историки об Елизавете Петровне: Елизавета попала между двумя встречными культурными течениями, воспитывалась среди новых европейских веяний и преданий...
Состав сооружений: решетки и песколовки: Решетки – это первое устройство в схеме очистных сооружений. Они представляют...
Биохимия спиртового брожения: Основу технологии получения пива составляет спиртовое брожение, - при котором сахар превращается...
Механическое удерживание земляных масс: Механическое удерживание земляных масс на склоне обеспечивают контрфорсными сооружениями различных конструкций...
© cyberpedia.su 2017-2024 - Не является автором материалов. Исключительное право сохранено за автором текста.
Если вы не хотите, чтобы данный материал был у нас на сайте, перейдите по ссылке: Нарушение авторских прав. Мы поможем в написании вашей работы!