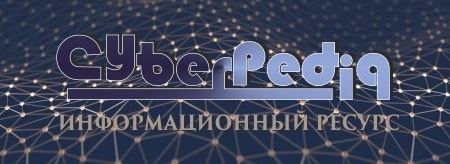
Общие условия выбора системы дренажа: Система дренажа выбирается в зависимости от характера защищаемого...
Кормораздатчик мобильный электрифицированный: схема и процесс работы устройства...
Топ:
Характеристика АТП и сварочно-жестяницкого участка: Транспорт в настоящее время является одной из важнейших отраслей народного хозяйства...
Комплексной системы оценки состояния охраны труда на производственном объекте (КСОТ-П): Цели и задачи Комплексной системы оценки состояния охраны труда и определению факторов рисков по охране труда...
Отражение на счетах бухгалтерского учета процесса приобретения: Процесс заготовления представляет систему экономических событий, включающих приобретение организацией у поставщиков сырья...
Интересное:
Лечение прогрессирующих форм рака: Одним из наиболее важных достижений экспериментальной химиотерапии опухолей, начатой в 60-х и реализованной в 70-х годах, является...
Финансовый рынок и его значение в управлении денежными потоками на современном этапе: любому предприятию для расширения производства и увеличения прибыли нужны...
Наиболее распространенные виды рака: Раковая опухоль — это самостоятельное новообразование, которое может возникнуть и от повышенного давления...
Дисциплины:
![]() |
![]() |
5.00
из
|
Заказать работу |
Все реакции, рассмотренные в предыдущей главе, представляют окончательный результат окисления сульфида и совершенно не дают никаких указаний о механизме процесса. Конечный результат окисления сульфида определяется величиной изменения стандартного изобарно - изотермического потенциала реакций. Сравнение этих величин для однотипных реакций предпочтительно реализуется на реакцию, для которой изменение стандартного изобарно - изотермического потенциала представляет наиболее отрицательную величину. Убыль стандартного изобарно - изотермического потенциала реакции окисления сульфидов при данных условиях зависит от соотношения давлений диссоциации сульфида, сульфата и окисла данного материала и давления диссоциации сернистого ангидрида.
Сульфаты тяжелых цветных металлов в зависимости от температуры могут окисляться, при температуре 700 - 800°С, окисление сульфидов в основном идет до состояния окислов. Образование окисла или сульфата при обжиге происходит по следующим конечным реакциям:
MeS +1,5O2=MeO+SO2
SO2+O2=2SO3
MeO+SO3=MeSO4
Первая реакция практически необратима, для второй реакции константа равновесия равна:
для третьей реакции:
Когда порциональное давление серного ангидрида в печных газах меньше диссоциации сульфата, т. е. когда:
идет образование окисла. Из приведённого неравенства вытекают следующие условия обжига:
1.С повышением температуры давление диссоциации сульфата увеличивается и происходит разрушение с образованием окисла.
2.Большой избыток воздуха необходим для интенсификации процесса и обеспечивается повышенной тягой в печи.
3 В процессе обжига громадное значение имеет хороший контакт печных газов с обжигаемым материалом, который в известковой степени обеспечивается более длительным пребыванием шихтовых материалов в печи.
Влияние скорости дутья на выход пыли
Одним из важнейших показателей обжига в кипящем слое является количество унесённой в газоходную систему пыли. Процессы, осуществляющиеся в кипящем слое, обычно сопровождаются большим пылевыносом 24 - 40%. В общем случае на степень пылевыноса влияют следующие факторы:
1. Грануметрический состав;
2. Физические и химические свойства концентрата и оборотной пыли;
1200 1400 1600 1700 1800
Рис.5
На графике приведены фактические данные, полученные при различных режимах обжига на печах кипящего слоя, характеризующие влияние удельного расхода воздуха на содержание серы в получаемой закиси. Из графика видно, что для получения закиси с содержанием серы менее 0,5%, расход на 1т концентрата должен составлять: при расходе оборотной пыли 25 - 40% от веса концентрата - 1730 м3; при расходе оборотной пыли 10 -20% от веса концентрата - 1700 м3.
Технологическая часть
Состав концентратов
Таблица1
Наим. | Zn | Pb | Cu | Cd | MgO | Co | S | As | Sb | CaO | Fe | SiO2 | Al2O3 | Прочие |
состав | 52,1 | 1,62 | 1,2 | 0,22 | 0,1 | 0,006 | 32,1 | 0,3 | 0,08 | 0,72 | 8,2 | 2,08 | 0,27 | 1,0 |
Расчёт минерального состава
Согласно минералогическому составу исследованию концентрат содержит следующие минералы: ZnS, PbS, GuFeS2, CdS, MgCO3, Sb2S3, As2S3, CaCO3, SiO2, Al2O3, Fe2S8,FeS2.
Расчёт производим на 100 кг сухого концентрата:
1. Определим количество S в ZnS
2. Определим количество S в PbS
3. Определим количество S в CuFeS2
4. Определим количество Fe в CuFeS2
5. Определим количество S в CdS
6. Определим количество S в As2S3
7. Определим количество S в Sb2S3
8. Определим количество S в CoS
9. Определим количество CO2 в CaCO3
10. Определим количество CO2 в MgCO3
Для образования ZnS, PbS, CdS, GuFeS2,As2S3, Sb2S3 требуется серы 27,182(25,45+0,25+1,2+0,06+0,192+0,03+0,003) кг. Остальная сера в количестве 4,9 (32,1-27,182) кг свяжется с железом в виде Fe2S8, FeS2.
Количество оставшегося Fe для соединений с серой составляет 7,15(8,2-1,05) кг.
Разложим количество Fe2S8, FeS2. Обозначим количество Fe в пирите через Х, тогда количество Fe в Fe7S8 будет (7,15-Х) кг.
11. Определим количество S в FeS2
12. Определим количество S в Fe7S8
4,65-0,65X+1,14X= 4,9
X=0,1 кг
Количество S в FeS2 1,14X= 0,114 кг
Количество S в Fe7S8 4,65- 0,114=4,536 кг
Количество Fe в FeS2 0,1 кг
Количество Fe в Fe7S8 7,15- 0,1= 7,05 кг
FeS2= Fe+ S2=0,1+ 0,114=0,214 кг
Fe7S8= Fe7+ S8=7,05+4,536=11,586 кг
Считаем, что SiO2 и Al2O3 остаются без изменения. На основании расчётов составляем таблицу минералогического состава цинкового концентрата.
Состав сооружений: решетки и песколовки: Решетки – это первое устройство в схеме очистных сооружений. Они представляют...
Наброски и зарисовки растений, плодов, цветов: Освоить конструктивное построение структуры дерева через зарисовки отдельных деревьев, группы деревьев...
Автоматическое растормаживание колес: Тормозные устройства колес предназначены для уменьшения длины пробега и улучшения маневрирования ВС при...
Индивидуальные и групповые автопоилки: для животных. Схемы и конструкции...
© cyberpedia.su 2017-2024 - Не является автором материалов. Исключительное право сохранено за автором текста.
Если вы не хотите, чтобы данный материал был у нас на сайте, перейдите по ссылке: Нарушение авторских прав. Мы поможем в написании вашей работы!