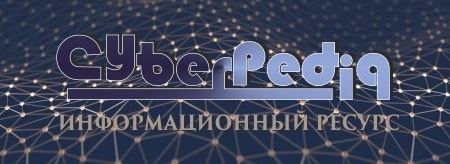
История создания датчика движения: Первый прибор для обнаружения движения был изобретен немецким физиком Генрихом Герцем...
Адаптации растений и животных к жизни в горах: Большое значение для жизни организмов в горах имеют степень расчленения, крутизна и экспозиционные различия склонов...
Топ:
Методика измерений сопротивления растеканию тока анодного заземления: Анодный заземлитель (анод) – проводник, погруженный в электролитическую среду (грунт, раствор электролита) и подключенный к положительному...
Определение места расположения распределительного центра: Фирма реализует продукцию на рынках сбыта и имеет постоянных поставщиков в разных регионах. Увеличение объема продаж...
Особенности труда и отдыха в условиях низких температур: К работам при низких температурах на открытом воздухе и в не отапливаемых помещениях допускаются лица не моложе 18 лет, прошедшие...
Интересное:
Уполаживание и террасирование склонов: Если глубина оврага более 5 м необходимо устройство берм. Варианты использования оврагов для градостроительных целей...
Подходы к решению темы фильма: Существует три основных типа исторического фильма, имеющих между собой много общего...
Аура как энергетическое поле: многослойную ауру человека можно представить себе подобным...
Дисциплины:
![]() |
![]() |
5.00
из
|
Заказать работу |
КУРСОВОЙ ПРОЕКТ
|
По дисциплине __________________________________________________________
________________________________________________________________________
(наименование учебной дисциплины согласно учебному плану)
ПОЯСНИТЕЛЬНАЯ ЗАПИСКА
|
|
_____________________________________________________________________________
Автор: студент гр. ММ-03 ____________________ / Бойцова А.А. /
(подпись) (Ф.И.О.)
ОЦЕНКА: _____________
Дата: ___________________
ПРОВЕРИЛ
Руководитель проекта профессор. ________________ /Теляков Н. М. /
(должность) (подпись) (Ф.И.О.)
Санкт- Петербург
2006
Федеральное агентство по образованию
Государственное образовательное учреждение высшего профессионального образования
Российской Федерации
Санкт-Петербургский государственный горный институт им. Г.В. Плеханова
(технический университет)
УТВЕРЖДАЮ
Декан МФ
_________/Теляков Н.М/
“20”февраля 2006 г.
КУРСОВОЙ ПРОЕКТ (РАБОТА)
|
По дисциплине___________________________________________________________
________________________________________________________________________
(наименование учебной дисциплины согласно учебному плану)
ЗАДАНИЕ
Студент гр. ММ-03 /Бойцова А.А./
(Ф.И.О.)
1. Тема проекта: Рассчитать обжиг цинкового концентрата в кипящем слое производительностью 100 тыс. тонн в год
__________________________________________________________________________
2. Исходные данные к проекту: вариант № 4 Zn=52,1 кг, Pb=1,62кг, Cu=1,2кг, Cd=0,22кг, MgO=0,1кг, Co=0,006кг, S=32,1кг, As=0,3кг, Sb=0,08кг, CaO=0,72кг, Fe=8,2кг, SiO2=2,08кг, Al2 O3=0,27кг,Прочие= 1,0 кг:
3. Содержание пояснительной записки: Приведены расчеты и необходимые обоснования к обжигу цинкового концентрата _
4. Срок сдачи законченного проекта: “30” мая 2006 г.
Руководитель проекта: профессор ____________ /Теляков Н. М./
(должность) (подпись) (Ф.И.О.)
Дата выдачи задания: “20” февраля 2006 г.
Аннотация
В курсовом проектировании выполнен расчёт минералогического состава концентрата, расчёт обжига и его тепловой баланс с определением расхода и прихода тепла. Так же сделан выбор и расчёт основного и вспомогательного оборудования склада концентратов.
Страниц 50, рисунков 5, таблиц 9
The summary
In course designing the dynamic research of movement of the mechanism of moving of a cutter of the machine with definition of the law of movement of an initial link is executed, the diagram of angular speed initial in the established mode of operations is received.
Pages 50, figes 5, tables 9
Содержание
ЗАДАНИЕ.. 2
Аннотация. 3
Содержание. 4
Характеристика рудного цинкового сырья. 6
Основные способы извлечения цинка из сырья. 6
Обжиг цинковых концентратов. 8
Цели и типы обжига. 8
Способы обжига. 8
Принцип обжига в КС и его достоинства. 9
Общая схема цепи аппаратов. 9
Приготовление шихты.. 10
Конструкция печи КС.. 11
Практика обжига в печи КС.. 12
Теория процесса. 13
Температура воспламенения сульфидов и кинетика окисления. 13
Основные реакции окисления. 15
Процессы реакционной диффузии при обжиге. 16
Термодинамика реакций обжига. 16
Влияние скорости дутья на выход пыли. 17
Технологическая часть. 19
Минералогический состав концентрата. 22
Расчёт обжига. 23
Расчёт рационального состава огарка в смеси с пылью.. 23
Содержание серы в продуктах обжига. 23
Распределение составляющих шихты в твёрдых продуктах обжига. 25
Распределение состава огарка в смеси с пылями. 26
Расчёт рационального состава огарка. 29
Расчёт рационального состава смеси циклонной пыли и пыли электрофильтров. 31
Расчёт газов. 32
Расчёт обжигов газообразных продуктов. 32
Расчёт количества и состава обжиговых газов, при применении дутья, обогащенного О2 33
Состав обжиговых газов при дутье, обогащённым О2 34
Тепловой баланс обжига. 34
Приход тепла. 34
Расход тепла. 36
Тепловой баланс обжига. 39
Выбор и расчёт основного и вспомогательного оборудования. 40
Расчёт печи кипящего слоя. 40
Оптимальное количество дутья. 40
Удельная производительность печи. 41
Площадь пода печи. 42
Минимальный объём кипящего слоя. 42
Высота кипящего слоя. 42
Общая высота печи. 43
Гидравлическое сопротивление кипящего слоя. 43
Параметры воздуходувки. 43
Размеры и число дутьевых сопел. 43
Расчёт газовой системы.. 44
Участок печь-котёл. 45
Участок котёл-циклон. 45
Участок циклон-дымосос. 46
Участок дымосос-электрофильтр. 46
Классификационное отделение. 47
Процесс классификации. 47
Оборудование склада концентратов. 47
Склад сырья цинкового концентрата. 47
Шихтовый бункер. 48
Дисковая дробилка. 49
Библиографический список. 50
Характеристика рудного цинкового сырья
В природе цинк встречается главным образом в виде сульфида и в меньшей степени- в виде кислородных соединений. В соответствии с преобладающими минералами цинковые руды делят на сульфидные и окисленные.Сульфидные руды содержат цинк главным образом в форме сфалерита (низкотемпературная модификация ZnS), а иногда в форме вюрцита (высокотемпературная модификация ZnS). Железистые разновидности ZnS называют марматитом. В окисленных цинковых рудах цинк представлен главным образом в форме карбонатов (смитсонит ZnCO3 и гидроцинкит ZnCO3* Zn(OH)2) и силикатов (виллемит Zn2SiO4).
В России крупные месторождения цинкосодержащих руд расположены в районах Алтая, Урала,Красноярского края и на Дальнем Востоке. За рубежом крупные месторождения расположены в Канаде, США, Австралии, Швеции, Японии, Перу.
Извлечение цинка в цинковый концентрат обычно составляет 70-85 % от содержания в сульфидных свинцово-цинковых рудах. Содержание технологических важных компонентов в цинковых концентратах обычно укладываются в следующие пределы, %:Zn 40-60; Pb 0,2-3,5; Cu 0,15-2,3; Fe 2,5-13; S 30-35; Cd 0,1-0,5; As 0,03-0,3; Sb 0,01-0,07; Co 0,001-0,013; In 0,001-0,07.Другими технологически важными свойствами концентратов являются плотность 3,4-4,3 г/см3, насыпная масса 1,9-2,9 г/см3, влажность 10-16 % или после подсушки 6-8%.
Обжиг цинковых концентратов
Цели и типы обжига
Главная цель обжига концентрата- быстрей, полней и с наименьшими затратами превратить сульфидный цинк в оксидный, из которого цинк рациональней восстанавливать. При этом огарок надо получить в таком состоянии, чтобы он наиболее благоприятен для осуществления последующих стадий технологии и в конечном счёте обеспечил высокие технико-экономические показатели производства в целом. Кроме тог, желательно полнее утилизировать образующийся при обжиге SO2 и выделяющееся тепло.
Обжиг концентратов ведут с получением огарка-порошка и огарка-агломерата для последующей переработки соответственно гидро- или пирометаллургическим способом.
В современной практике огарок-порошок для выщелачивания получают в печах кипящего слоя (КС) при 900-1000 0 С.
В практике пирометаллургического производства цинка обжиг концентратов проводят в две стадии. На первой стадии концентрат обжигают на порошок с частичной или полной десульфуризацией в печах КС при 1050-1150 0 С. На второй стадии этот огарок подвергают агломерационному обжигу на агломашинах (максимальная температура 1300-1400 0 С).
Способы обжига
До 50-х годов обжиг цинковых концентратов на порошок вели в печах с перегребанием шихты на поду (в начальный период вручную, а затем в многоподовых печах механически). Низкие технико-экономические показатели такого обжига заставили искать лучшие способы обжига. В 30-50-е годы на ряде зарубежных предприятий применяли обжиг во взвешенном состоянии: сухой концентрат тангенциально вдувался воздухом в цилиндрическую печь и горел в газовом потоке, большая его часть оседала и выгружалась из нижней части печи в виде огарка, а часть материала (до 40 %) уносилась из печи в виде пыли и улавливалась в пылеулавливающейся системе, включающей и котёл-утилизатор для утилизации технологического тепла. Этот тип обжига более производительный, не требует затрат топлива и даже позволяет утилизировать технологическое тепло, даёт огарок лучшего качества.
В конце 40-х годов в СССР и в Канаде был впервые предложен обжиг в кипящем слое. Этот способ обжига благодаря большим преимуществам перед ранее применявшимися быстро распространился.
Общая схема цепи аппаратов
Технология обжига цинковых концентратов для выщелачивания на разных заводах не имеет принципиальных различий: обжиг ведётся в печах КС в одну стадию. Различия касаются следующего:
· Способов подготовки и исходного состояния шихты для обжига;
· Конструкции печей КС;
· Подготовки и транспорта огарка для выщелачивания;
· Температурных и концентрационных условий обжига;
· Способов утилизации тепла печей КС
На рис. 3 показана схема аппаратов обжигового цеха.
Схема включает узел подготовки шихты к обжигу в сухом виде, печь КС, узел теплоотъема тепла из газа в стояке и из КС кессонами испарительного охлаждения, узел пылеулавливания циклоном и электрофильтрами, узел подготовки огарка к выщелачиванию в сухом виде, узел гидродинамического обеспечения технологического тракта (воздуходувка и дымосос).
Приготовление шихты
Шихту в печь КС подают обычно в сухом виде или в виде пульпы. Подачу на обжиг сухой шихты применяют для шихт, образованных из привозных и довольно близких по составу концентратов. Шихта в виде пульпы предпочтительна, когда цинковый завод находится рядом с обогатительной фабрикой, снабжающей завод концентратом.
Для получения сухой шихты концентраты грейферным краном смешивают для однородности материала. Далее шихту подсушивают в сушильном барабане до остаточной влажности 6-8 %. Если концентраты достаточно сухие, то подсушка не требуется. Подсушенную шихту измельчают на дисковых истирателях или на дезынтеграторах и отсеивают крупные комки на грохотах.
Шихту в виде пульпы готовят репультацией смеси концентратов водой (в пульпе 75-80 % твёрдого) и дополнительно перемешивают в баках с мешалками.
Конструкция печи КС
Конструктивно печи КС разнообразны и различаются профилем поперечного сечения (круглые и прямоугольные), величиной отношения надслоевого объёма печи к площади пода, способом загрузки шихты в печь (через фотокамеру и в слой или через загрузочные окна в стенах печи и по всей поверхности кипящего слоя), конструкцией воздухораспределительной падины.
На рис. 4 схематически показана цилиндрическая печь КС наиболее распространённая на отечественных заводах
Площадь пода печи 34 м2, площадь фотокамеры 1,5 м2, высота печи 10 м, высота сливного порога 1,0-1,2. Фотокамера служит для загрузки шихты в КС, а сливной порог- для выгрузки огарка.
Очень ответственным элементом конструкции печи является воздухораспределительная подина. Подину печи выполняют из жароупорного бетона на стальном перфорированном листе с вставленными в отверстия соплами для распределения дутья равномерно по площади.
Тонкие (пылевидные) фракции выносятся с дутьём из КС и обжигаются во взвешенном состоянии. Пылевая часть огарка улавливается в пылеуловителях и выгружается из них для выщелачивания. Грубодисперсная часть огарка выгружается из печи через сливной порог и тоже направляется на выщелачивание.
Для стационарного теплового режима обжига необходим тепловой баланс в КС, который обеспечивается отводом тепла из слоя. Отъём тепла из обжиговых газов осуществляется с помощью котлов-утилизаторов или вертикальных стояков, охлаждаемых кессонами испарительного охлаждения.
Узел пылеулавливания состоит из котла-утилизатора, одной или двух ступеней циклонов для грубого пылеулавливания и электрофильтров для тонкого пылеулавливания. Обеспыленный газ направляют в сернокислотное производство.
Дутьё воздуха в печь подают от турбовоздуховки по воздуховодам в воздушную коробку, расположенную под воздухораспределительной подиной. А далее воздух через сопла в подине под определённым давлением поступает в КС.
Транспортировку огарка от печей КС осуществляют или в виде пульпы, или в сухом виде. Транспортировка пульпы аппаратурно проще, чем сухого огарка.
Совершенствование обжигового передела по технико-экономическим показателям достигают также изменением конструкции печей КС. Эти изменения направлены на увеличение единичной мощности печей за счёт увеличения пода.
Увеличение площади пода печей потребовало изменить способ загрузки шихты в печь КС для лучшего её использования: вместо загрузки шихты через фотокамеру в слой применяют загрузку скоростными забрасывателями через загрузочное окно в стенке печи для равномерного распределения шихты по поверхности КС.
Практика обжига в печи КС
Для поддержания нормального режима обжига в печи КС необходимы следующие условия:
· Постоянство минералогического и дисперсного состава шихты и скорость загрузки её в слой;
· Равномерное распределение дутья по площади подины;
· Постоянство заданного давления в воздушной коробке под подиной;
· Постоянство тягового режима в пылегазовом тракте для отвода технологических газов;
Теория процесса
Основные реакции окисления
Окисление сульфида может происходить по следующим реакциям:
MeS + 202 = MeSO4
MeS + О2 = Me + SO2
Основная реакция окисления сульфида Zn, протекающая с выделением тепла, достаточного для самопроизвольного течения процесса окисления имеет вид:
ZnS + 1,5О2 = ZnO + SO2
ZnS + О2 = ZnO + SO2
Технологическая часть
Состав концентратов
Таблица1
Наим. | Zn | Pb | Cu | Cd | MgO | Co | S | As | Sb | CaO | Fe | SiO2 | Al2O3 | Прочие |
состав | 52,1 | 1,62 | 1,2 | 0,22 | 0,1 | 0,006 | 32,1 | 0,3 | 0,08 | 0,72 | 8,2 | 2,08 | 0,27 | 1,0 |
Расчёт минерального состава
Согласно минералогическому составу исследованию концентрат содержит следующие минералы: ZnS, PbS, GuFeS2, CdS, MgCO3, Sb2S3, As2S3, CaCO3, SiO2, Al2O3, Fe2S8,FeS2.
Расчёт производим на 100 кг сухого концентрата:
1. Определим количество S в ZnS
2. Определим количество S в PbS
3. Определим количество S в CuFeS2
4. Определим количество Fe в CuFeS2
5. Определим количество S в CdS
6. Определим количество S в As2S3
7. Определим количество S в Sb2S3
8. Определим количество S в CoS
9. Определим количество CO2 в CaCO3
10. Определим количество CO2 в MgCO3
Для образования ZnS, PbS, CdS, GuFeS2,As2S3, Sb2S3 требуется серы 27,182(25,45+0,25+1,2+0,06+0,192+0,03+0,003) кг. Остальная сера в количестве 4,9 (32,1-27,182) кг свяжется с железом в виде Fe2S8, FeS2.
Количество оставшегося Fe для соединений с серой составляет 7,15(8,2-1,05) кг.
Разложим количество Fe2S8, FeS2. Обозначим количество Fe в пирите через Х, тогда количество Fe в Fe7S8 будет (7,15-Х) кг.
11. Определим количество S в FeS2
12. Определим количество S в Fe7S8
4,65-0,65X+1,14X= 4,9
X=0,1 кг
Количество S в FeS2 1,14X= 0,114 кг
Количество S в Fe7S8 4,65- 0,114=4,536 кг
Количество Fe в FeS2 0,1 кг
Количество Fe в Fe7S8 7,15- 0,1= 7,05 кг
FeS2= Fe+ S2=0,1+ 0,114=0,214 кг
Fe7S8= Fe7+ S8=7,05+4,536=11,586 кг
Считаем, что SiO2 и Al2O3 остаются без изменения. На основании расчётов составляем таблицу минералогического состава цинкового концентрата.
Расчёт обжига
Принимаем, что в продуктах обжига (огарок, цинковая пыль, пыль электрофильтров) вся сера связана с цинком в ZnS; 50% Pb, Mg, Cd связаны в PbO, CdO, Mg; а 50% в PbSO4, CaSO4, MgSO4. Все карбонаты диссоциируют на МеО и CO2; Cu, Cd, Co, Fe, As, Sb, и часть Zn окисляется до окиси, часть Zn окисляется до сульфата; Al2O3 остаётся без изменения; 40% SiO2 связывается в силикат цинка ZnO SiO2.
Содержание серы в продуктах обжига
Таблица 3
Сера | Огарок | Пыль |
SОБЩ | 23,59 | 8,51 |
SS | 18,7 | 6,75 |
SSO | 4,89 | 1,76 |
Расчёты для других составляющих шихты ведутся таким же образом. После проведения расчётов заполняем таблицу “Распределение составляющих шихты в твёрдых продуктах обжига”.
Составляющие
Переходит в огарок
Переходит в пыль
Всего
Соединения
Всего
SiO2
0,83
1,25
2,08
2,1
Соединения
Составляющие огарка
Всего
SiO2
0,61
0,92
1,53
2,2
Соединения
Составляющие пыли
Всего
SiO2
0,22
0,33
0,55
2,1
Расчёт газов
Сырой концентрат содержит 32,1 кг серы из которого выгорает 94% серы, то есть 30,18 кг.
Условно принимаем, что 95% серы окисляется до SO2, а 5% до SO3.
Количество S в SO2
Количество S в SO3
Количество О2 необходимое для окисления S до SO2
Количество О2 необходимое для окисления S до SO3
Теоретическое количество О2 для процесса обжига складывается из О2, необходимого для окисления материалов и для окисления S до SO2 и SO3.
O2=6,8+28,6+2,25=37,65 кг
В концентрате содержится 6% влаги, то есть 2,3 кг воды
Тепловой баланс обжига
Расчёт теплового баланса производим на 102, 3 кг концентрата (на 100 кг сухого концентрата)
Приход тепла
1. Физическое тепло концентрата
2. Физическое тепло воздуха
3. Тепло экзотермических реакций
Для расчётов пользуемся таблицей “Рациональный состав огарка в смеси с пылями”.
·
·
·
·
·
·
·
·
·
·
((__lxGc__=window.__lxGc__||{'s':{},'b':0})['s']['_228268']=__lxGc__['s']['_228268']||{'b':{}})['b']['_697691']={'i':__lxGc__.b++};
Организация стока поверхностных вод: Наибольшее количество влаги на земном шаре испаряется с поверхности морей и океанов (88‰)...
История развития пистолетов-пулеметов: Предпосылкой для возникновения пистолетов-пулеметов послужила давняя тенденция тяготения винтовок...
Общие условия выбора системы дренажа: Система дренажа выбирается в зависимости от характера защищаемого...
Типы оградительных сооружений в морском порту: По расположению оградительных сооружений в плане различают волноломы, обе оконечности...
© cyberpedia.su 2017-2024 - Не является автором материалов. Исключительное право сохранено за автором текста.
Если вы не хотите, чтобы данный материал был у нас на сайте, перейдите по ссылке: Нарушение авторских прав. Мы поможем в написании вашей работы!