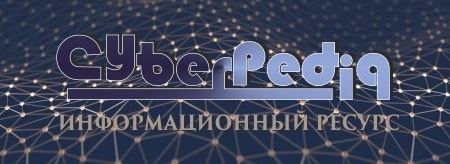
Биохимия спиртового брожения: Основу технологии получения пива составляет спиртовое брожение, - при котором сахар превращается...
Адаптации растений и животных к жизни в горах: Большое значение для жизни организмов в горах имеют степень расчленения, крутизна и экспозиционные различия склонов...
Топ:
Характеристика АТП и сварочно-жестяницкого участка: Транспорт в настоящее время является одной из важнейших отраслей народного хозяйства...
Установка замедленного коксования: Чем выше температура и ниже давление, тем место разрыва углеродной цепи всё больше смещается к её концу и значительно возрастает...
Характеристика АТП и сварочно-жестяницкого участка: Транспорт в настоящее время является одной из важнейших отраслей народного...
Интересное:
Мероприятия для защиты от морозного пучения грунтов: Инженерная защита от морозного (криогенного) пучения грунтов необходима для легких малоэтажных зданий и других сооружений...
Уполаживание и террасирование склонов: Если глубина оврага более 5 м необходимо устройство берм. Варианты использования оврагов для градостроительных целей...
Как мы говорим и как мы слушаем: общение можно сравнить с огромным зонтиком, под которым скрыто все...
Дисциплины:
![]() |
![]() |
5.00
из
|
Заказать работу |
|
|
Таблица 1
Сварочный ток, А, в зависимости от пространственного положения при сварке электродами основного типа
Диаметр электрода, мм
Пространственное положение
Нижнее
Вертикальное
Потолочное
3; 3,25
100-130
100-130
90-110
4
170-220
160-180
150-180
5
210-250
180-200
Сварку не ведут
При использовании электродов газозащитного типа сварку корня шва выполняют сверху вниз без колебательных движений, опираясь концом электрода на кромки свариваемых труб. Сварку выполняют постоянным током обратной или прямой полярности при напряжении холостого хода источника питания не менее 75В. Значения сварочного тока при сварке электродами диаметром 3,25 мм не должны превышать 100-110А; при сварке электродами диаметром 4 мм в нижнем и полувертикальном положении 120-160А, в остальных положениях 100-140А. Скорость сварки следует поддерживать в диапазоне 16-22 м/ч. Изменяя в процессе сварки угол наклона электрода от 40 до 90°, сварщик сохраняет образующееся при сквозном проплавлении кромок технологическое окно, через которое он наблюдает за оплавлением кромок.
Для снижения уровня остаточных сварочных напряжений в сварном соединении периметр неповоротного стыка разбивается на симметричные, диаметрально противоположные участки и многослойная сварка выполняется в последовательности, приведенной на рис. 2. Больший эффект снижения сварочных напряжений и деформации дает применение обратноступенчатого метода сварки и одновременное заполнение разделки двумя или четырьмя сварщиками.
Рис.2. Рекомендуемый порядок выполнения многослойного шва при сварке электродами с основным покрытием: а - Ø < 200 мм, б - Ø 300 мм.
|
При сварке трубопроводов небольшого диаметра (до 530 мм) с целью уменьшения объема монтажных работ в траншее часто практикуется укрупнение в секции труб сваркой с поворотом стыков на 90 или 180°. Трубу делят по окружности на четыре примерно одинаковых по длине участка. Заварив участки 1 и 2 стык поворачивают на 90° для сварки участков 3 и 4 (рис. 3). Затем, выполняя очередной поворот на 90°, производят последовательно сварку участков 5 и 6, 7 и 8.
Рис.3. Сварка с поворотом труб на 90°: а - первого слоя, б - второго,
Последовательность выполнения участков слоя.
В другом случае, после сварки участков 1 и 2 (рис. 4) выполняют поворот стыкуемых труб на 180° для сварки участков 3 и 4. Затем поворот на 90° и 180° для сварки участков 5 и 6, 7 и 8 соответственно.
Рис.4. Сварка с поворотом труб на 180°: а - первого слоя, б - второго,
Последовательность выполнения участков слоя.
Подготовка кромок труб под сварку
Перед началом сварочно-монтажных работ необходимо убедиться в том, что используемые трубы и детали трубопроводов имеют сертификаты качества и соответствуют проекту, техническим условиям на их поставку. Трубы и детали должны пройти входной контроль в соответствии с требованиями соответствующих стандартов и технических условий на трубы.
Концы труб и соединительных деталей должны иметь форму и размеры скоса кромок, соответствующие применяемым процессам сварки. При их несоответствии допускается механическая обработка кромок в трассовых условиях. Для труб небольшого диаметра (до 520 мм) возможно применение торцевателей, фаскоснимателей, труборезов и шлифмашинок. Для больших диаметров применяются орбитальные фрезерные машины, гидроабразивная резка и шлифмашинки. В отдельных случаях, при врезке катушек или выполнении захлестов, допускается применение термических способов подготовки кромок, таких как:
· газокислородная резка с последующей механической зачисткой кромок абразивным кругом на глубину 0,1...0,2 мм;
|
· воздушно-плазменная резка с последующей механической обработкой на глубину до 1 мм - вследствие насыщения кромки азотом (при использовании аргона в качестве плазмообразующего газа механическая обработка не требуется); в) воздушно-дуговая резка с последующей зашлифовкой на глубину до 0,5 мм (науглераживание кромок);
· строжка и резка специальными электродами типа АНР-2М, АНР-3 или ОК.21.03, после которых не требуется механическая обработка.
Перед сборкой труб необходимо очистить внутреннюю полость труб от попавших туда грунта, грязи, снега, а также зачистить до металлического блеска кромки и прилегающие к ним внутреннюю и наружную поверхность труб и соединительных деталей на ширину не менее 10 мм
Все трубы поступают на трассу с заводов с разделкой кромок, предназначенной для ручной дуговой сварки покрытыми электродами. Эта разделка (рис. 5, а) имеет для труб любого диаметра при толщине стенки более 4 мм угол скоса кромок 25-30° и притупление 1-2,6 мм. При толщине стенки 16 мм и более трубы большого диаметра могут поставляться с комбинированной разделкой кромок в соответствии с рис. 5, б.
Размер В зависит от толщины стенки и составляет:
· 7 мм - при толщине стенки трубы 15... 19 мм
· 8 мм - при толщине стенки трубы 19...21,5 мм
· 10 мм - при толщине стенки трубы 21,5... 26 мм.
Рис. 5. Типы разделки кромок труб для ручной дуговой сварки (а, б), автоматической сварки в среде защитных газов (в), автоматической сварки под флюсом (г, д, е, ж) и порошковой проволокой с принудительным формированием (а,б).
Для трубопроводов Ø1000 мм и свыше, когда предусмотрено выполнение подварочного корневого шва изнутри, рекомендуется разделка представленная на рис.5, в. При строительстве распределительных трубопроводов допускается ручная дуговая сварка труб без разделки кромок с толщиной стенки до 4 мм. Кроме того, для трубопроводов диаметром до 152 мм возможно применение газовой сварки (без разделки кромок - до 3 мм, и односторонним скосом кромок - до 5 мм).
Соединение разностенных труб на трассе допускается без дополнительной обработки кромок:
· для толщин стенок не более 12,5 мм, если разность толщины не превышает 2 мм;
· для толщин стенок свыше 12,5 мм, если разность толщины не превышает 3 мм. В этом случае смещение стыкуемых кромок не допускается.
|
Соединение труб или труб с запорной и распределительной арматурой с большей разностью толщин стенок осуществляют посредством вварки между стыкуемыми элементами переходников заводского изготовления или вставок из труб промежуточной толщины длиной не менее 250 мм.
Допускается выполнять непосредственную сборку и сварку труб или труб с деталями трубопроводов при разностенности до 1,5 толщин при специальной обработке, прилегающей к торцу поверхности более толстой трубы или детали (рис.6, а). Сварка нахлесточных стыков разностенных труб не допускается.
Непосредственное соединение труб с запорной и распределительной арматурой разрешается при условии, если толщина стыкуемого торца арматуры не превышает 1,5 толщины стенки трубы с подготовкой патрубка арматуры согласно (рис. 6, б). Указанная подготовка должна быть осуществлена заводом-поставщиком.
Рис. 6. Подготовка для сварки торцов труб и деталей с разной толщиной стенки.
Аргонодуговая сварка труб
Дуговую сварку с защитой дуги инертным газом (аргоном или гелием) применяют для производства тонкостенных труб (с прямым швом) диаметром 15—426 мм и толщиной стенки 0,2—5 мм из высоколегированных сталей аустенитного класса, а также из никеля и его сплавов, магния, циркония и др. Наибольшее распространение такая сварка получила для выпуска труб диаметром от 6 до 71 мм с толщиной стенки от 0,4 до 3,0 мм.
Существенным преимуществом метода аргонодуговой сварки является возможность сварки труб из высоколегированных сталей, а недостатком — сравнительно низкие скорости сварки: 0,5—1,5 м/мин.
В качестве исходной заготовки при этом методе сварки труб применяют ленту в рулонах. Оборудование для подготовки и формовки заготовки принципиально не отличается от описанного выше для сварки труб сопротивлением и радиочастотной.
Аргонодуговая сварка труб может производиться на тех же трубоэлектросварочных агрегатах, что и радиочастотная сварка, и сварка сопротивлением. Заменяют лишь радиочастотный ламповый генератор или сварочный трансформатор на соответствующее устройство для дуговой сварки. При этом соответственно снижается и скорость привода установкой специальных редукторов.
|
Р ис. 7. Схема аргонодуговой сварки прямошовных труб:
1 — смотровое окно; 2 — вольфрамовый электрод; 3 — сварочная горелка;
4 — уплотняющая прокладка;
5 — свариваемая труба;
6 — уплотнительное кольцо;
7 — полугерметичная камера;
8 — приспособление для поддува газа;
9 — опорно-сварочные валки;
10 — верхняя крышка камеры;
Баллон с газом
Схема аргонодуговой сварки прямошовных труб показана на рис. 7. Трубная заготовка из формовочного стана поступает к сварочному стану. Между кромками трубной заготовки и не плавящимся электродом из вольфрама возбуждается электрическая дуга. Происходит расплавление кромок заготовки. Обжимаясь в опорно-сварочных валках, кромки свариваются. Применяемый внутренний поддув зоны сварки позволяет значительно уменьшить величину внутреннего грата. Небольшая толщина стенки (1,5—3,0 мм) и необходимое сварочное давление дают возможность вести процесс без применения присадочного материала.
Схема аргонодуговой сварки прямошовных труб показана на рис. 7. Трубная заготовка из формовочного стана поступает к сварочному стану. Между кромками трубной заготовки и не плавящимся электродом из вольфрама возбуждается электрическая дуга. Происходит расплавление кромок заготовки. Обжимаясь в опорно-сварочных валках, кромки свариваются. Применяемый внутренний поддув зоны сварки позволяет значительно уменьшить величину внутреннего грата. Небольшая толщина стенки (1,5—3,0 мм) и необходимое сварочное давление дают возможность вести процесс без применения присадочного материала.
Применение аргона в качестве защитного газа обеспечивает более устойчивое горение сварочной дуги, лучшую защиту сварного соединения и меньшее провисание металла шва по сравнению с гелием, так как потенциал ионизации гелия выше, а плотность меньше, чем у аргона. Поэтому применение аргона для сварки труб из нержавеющей стали, титана и др. более целесообразно. Аргон подается в камеру через сопло сварочной головки под избыточным давлением 19,6—49 кн/м² (0,2—0,5 am). Внутрь трубы аргон подается под избыточным давлением 29,2—98,1 кн/м² (0,3—1,0 ат).
При производстве труб диаметром до 100 мм применяют вольфрамовый электрод одного диаметра, равный 4 мм. При аргонодуговой сварке используют постоянный ток напряжением 12—15 в и силой 150—200 а (это зависит от размера свариваемых труб). Для получения постоянного тока применяют сварочный трансформатор и преобразователь постоянного тока. Расход аргона при сварке со скоростью до 1 м/мин составляет 15—30 л/мин. На стане предусмотрена регулировка электрода как по высоте, так и поперек оси сварки.
|
Особое внимание при аргонодуговой сварке труб уделяют чистоте кромок. Кроме этого, при производстве труб из цветных металлов (титан, ниобий и т. д.), а также из высоколегированных сталей особенно следят за хорошей чистотой поверхности трубы. В связи с этим для уменьшения налипания металла валки последних клетей формовочного стана иногда выполняют составными. Участки валка, где имеется наибольшая вероятность налипания, изготовляют из текстолита или пластмассы. Наружный грат на трубе, образовавшийся после сварки, зачищают в потоке иглофрезой. После зачистки грата и охлаждения трубу калибруют на калибровочном стане и разрезают на мерные длины резцовым отрезным устройством.
При аргонодуговой сварке предел прочности металла шва обычно на 10—20% выше, чем основного металла, а относительное удлинение ниже на 10—30%.
Трубы, сваренные этим способом, в основном предназначены для химической промышленности. Поэтому после сварки их подвергают холодной прокатке и волочению, последующей термической обработке для полного выравнивания свойств шва и основного металла. Это повышает коррозионную стойкость шва.
Аргонодугсвая сварка в сравнении с другими известными способами сварки труб из легированных сталей имеет следующие преимущества:
· полная защита металла и электрода от окисляющего воздействия кислорода воздуха;
· возможность работы без специальных электродных покрытий, флюсов и последующей очистки шва от флюсов и шлаков;
· устойчивость горения дуги, что облегчает осуществление непрерывного процесса сварки;
· высокие механические свойства и коррозийная стойкость сварного шва, а также хороший внешний вид;
· безопасность напряжения сварочного тока как при холостом ходе, так и при горении дуги.
|
|
Состав сооружений: решетки и песколовки: Решетки – это первое устройство в схеме очистных сооружений. Они представляют...
Своеобразие русской архитектуры: Основной материал – дерево – быстрота постройки, но недолговечность и необходимость деления...
Механическое удерживание земляных масс: Механическое удерживание земляных масс на склоне обеспечивают контрфорсными сооружениями различных конструкций...
Индивидуальные и групповые автопоилки: для животных. Схемы и конструкции...
© cyberpedia.su 2017-2024 - Не является автором материалов. Исключительное право сохранено за автором текста.
Если вы не хотите, чтобы данный материал был у нас на сайте, перейдите по ссылке: Нарушение авторских прав. Мы поможем в написании вашей работы!