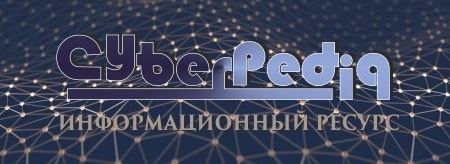
История развития пистолетов-пулеметов: Предпосылкой для возникновения пистолетов-пулеметов послужила давняя тенденция тяготения винтовок...
Типы оградительных сооружений в морском порту: По расположению оградительных сооружений в плане различают волноломы, обе оконечности...
Топ:
Процедура выполнения команд. Рабочий цикл процессора: Функционирование процессора в основном состоит из повторяющихся рабочих циклов, каждый из которых соответствует...
Проблема типологии научных революций: Глобальные научные революции и типы научной рациональности...
Комплексной системы оценки состояния охраны труда на производственном объекте (КСОТ-П): Цели и задачи Комплексной системы оценки состояния охраны труда и определению факторов рисков по охране труда...
Интересное:
Уполаживание и террасирование склонов: Если глубина оврага более 5 м необходимо устройство берм. Варианты использования оврагов для градостроительных целей...
Искусственное повышение поверхности территории: Варианты искусственного повышения поверхности территории необходимо выбирать на основе анализа следующих характеристик защищаемой территории...
Наиболее распространенные виды рака: Раковая опухоль — это самостоятельное новообразование, которое может возникнуть и от повышенного давления...
Дисциплины:
![]() |
![]() |
5.00
из
|
Заказать работу |
|
|
Конвейерная лента ленточных конвейеров является тяговым и грузонесущим органом, а также основным, наиболее дорогим и наименее долговечным, элементом ленточного конвейера.
В зависимости от условий эксплуатации конвейера лента должна отвечать ряду специфических требований:
- достаточной прочностью при растяжении и изгибе;
- малым упругим и остаточным удлинением при рабочей нагрузке;
- антистатичностью и огнестойкостью;
- высокой сопротивляемостью усталостному и абразивному износу, расслоению и пробою;
- продольной гибкостью во избежание необходимости чрезмерного увеличения диаметров барабанов;
- достаточной поперечной гибкостью для вписывания в роликоопоры и образования жёлоба;
- устойчивостью против гниения;
- возможно малой степенью старения и ослабления вследствие механических и атмосферных воздействий.
Резинотросовые ленты находят широкое применение на магистральных подземных конвейерах, особенно большой длины и мощности.
Резинотросовые ленты обладают рядом достоинств:
- высокой прочностью;
- продольной и поперечной гибкостью;
- незначительным удлинением (0,1-0,5%) существенно сокращающем ход натяжного устройства, что имеет особенное значение для конвейеров большой протяжённости;
- высокой скоростью передачи тягового усилия;
- удобством контроля целостности каркаса (тросов) ленты без остановки конвейера различными методами дефектоскопии;
- возможностью улавливания оборвавшейся ленты не только механическими, но и магнитными улавливающими устройствами;
- большим сроком службы (7-8 лет и более).
Резинотросовым лентам свойственны и недостатки:
- трудоёмкость процессов сращивания и ремонта;
|
- больший (в 1,5-2 раза), чем у тканевых лент, вес;
- подверженность тросов коррозии при повреждении обкладок.
Для увеличения поперечной прочности резинотросовых лент в них поверх тросового сердечника укладываются тканевые прокладки (Рис.1б, 1в).
Такие ленты имеют сопротивление пробою в 1,5-2 раза выше, чем ленты с тканевыми прокладками.
Резинотросовые ленты изготовляют с тросами диаметром от 2,1 до 11,5мм с пределами прочности на разрыв ленты 500, 630, 800, 1000, 1250, 1600, 2000, 2500, 3150 (3500), 4000, 5000, 6000 (6300) кгс/см ширины ленты согласно принятым Международным стандартам. В выпускаемых резинотросовых лентах используются тросы с цинковым или латунным покрытием. Тросы с латунным покрытием, как в статических, так и в динамических режимах нагружения обладают большей прочностью связи с резиной, чем тросы с цинковым покрытием. Для обеспечения требуемой прочности связи тросов с резиной рекомендуются конструкции лент с отношением шага тросов к диаметру троса 1,5-3,5. Расстояние крайних тросов от бортов ленты принимается равным 20-40 мм.
В подземных условиях рудников и угольных шахт применяются ленты с повышенной огнестойкостью (негорючие). Ленту считают огнестойкой, если суммарное время горения шести образцов после удаления их из пламени горелки не превышает 45 секунд, причём длительность горения одного образца должна быть не более 15 секунд. Для изготовления таких лент применяется огнестойкая резина на основе стирольного каучука с антипиренами, а на открытых разработках-морозостойкая резина на основе каучука СКИЗ.
В зависимости от условий эксплуатации резинотросовые ленты изготавливаются следующих видов:
- общего назначения РТЛ;
- трудно воспламеняющиеся РТЛ ТВ;
- трудно сгораемые (трудно горючие) РТЛ ШТС (ТГ);
- пониженной горючести угольные РТЛ ПГУ;
- морозостойкие РТЛМ.
Ленты всех типов изготавливаются длиной: максимально – 320 м; минимально – 120 м.
Для транспортирования скальных пород рекомендуется применять ленты с увеличенным шагом расположения тросов и с увеличенным их диаметром (например, ленты с тросами диаметром 10 мм, шагом 16 мм, толщиной верхней обкладки 30 мм, а нижней 10 мм).
|
Выпускаются и специальные резинотросовые ленты для транспортирования крупнокусковых грузов. Особенность их конструкции состоит в том, что в ленте укладываются в два слоя поперечные тросы. Ленты с поперечными тросами обладают высоким сопротивлением пробою.
Подготовка к стыковке и технология стыковки
Резинотросовых лент.
Стыковка резинотросовых конвейерных лент осуществляется методом горячей вулканизации. При этом последовательно выполняется ряд операций: подготовка рабочего места и стыковочных материалов, оборудования и инструментов, разделка стыкуемых концов лент, сборка и вулканизация стыка.
Для выполнения работ по стыковке и вулканизации резинотросовых лент выбирается место в наиболее удобном участке выработки вблизи возможных пунктов подключения к электросети – это может быть участок става конвейера в районе натяжной или выносной станций, а также в сбойках, где есть возможность работы с автотракторной техникой.
2.1 Подготовка рабочего места.
На участке става, выбранном под рабочее место, демонтируются роликоопоры верхней ветви и устанавливаются столы для разделки ленты или на став укладывается сплошной деревянный настил из досок толщиной 40мм и устанавливается вулканизационный пресс. Настил или столы устанавливаются по обе стороны пресса так, чтобы образовалась рабочая площадка, ширина которой должна быть на 200-300 мм больше ширины ленты, а длина на 1,5-2,0 м больше длины стыка. Для предотвращения попадания влаги на стыкуемые поверхности, если в выработке с кровли идёт «капёж», над рабочим местом устанавливается навес. Рабочее место должно устраиваться на том участке става, где исключён сбор стекающего по ленте конденсата и образования луж. Для обеспечения подгонки стыков к рабочему месту и возможности работы без демонтажа настилов (или столов) и вулканизатора необходимо устанавливать специально изготовленные роликоопоры, позволяющие верхней ветви ленты проходить над настилами (или столами) и над вулканизатором (нижними жёсткостями) с гарантированным зазором.
В подготовку рабочего места также входит:
|
- уборка площадки от посторонних предметов;
- очистка участка длиной 10-15 м от грязи и пыли;
- доставка и расстановка оборудования и материалов;
- подключение оборудования к сети электроснабжения;
- крепление лебёдок, бурение шпуров под конусы и монтаж блочков;
- доставка, подвеска и раскатка ленты;
- обеспечение необходимыми инструментами и приспособлениями в нужном количестве, стыковочными материалами, рекомендованными заводом-изготовителем конвейерных лент, с гарантированным качеством и не истёкшим сроком хранения.
2.2 Подготовка концов лент и схемы их соединений.
На стыкуемых концах посередине ленты трассировочным шнуром наносят осевую линию, длина которой должна быть 3–5 м. От конца ленты на расстоянии, равном длине стыка плюс 0,5-1,5 м, проводят с помощью угольника линию, перпендикулярную осевой линии отрезка ленты. При отсутствии угольника перпендикулярная линия может быть проведена при помощи геометрических построений (Рис.2, Рис.3) следующим образом. На оси отмечается точка а, от которой откладывается отрезок ав = 400 мм и ас = 800 мм. Из точек а и с радиусом R = 500 мм делают засечки. Через точки d и е проводят прямую. Отрезок АВ будет перпендикулярен оси, если проходит через точку в, а отрезок в d = в e = 300 мм. Все последующие измерения при разметке стыкового соединения производят от базовых перпендикулярных линий АВ или А'В', которые закрываются прозрачной плёнкой, приклеиваемой к ленте. При разметке «косого» стыка длина отрезка АО, откладываемого от базовой линии АВ, превышает длину отрезка ВМ на 1/3 ширины ленты. В случае разметки прямого стыка, откладываемые от базовой линии отрезки ВМ и АО имеют одинаковую длину. Зажимы стяжного приспособления устанавливают по перпендикулярным линиям и стягивают концы ленты с таким расчётом, чтобы они были совмещены внахлёстку на длину стыка. Натяжной барабан должен быть отведён в положение с учётом возможности выполнения последующих стыковок. После наложения друг на друга концов лент внахлёстку проверяют параллельность кромок и средней линии. Оси обоих концов ленты будут лежать на одной прямой, если АА'=ВВ'. Отклонения не должны превышать двух миллиметров. Схемы соединения концов резинотросовых лент методом горячей вулканизации с расположением торцевых кромок и границ ступеней под углом 71° 30' к продольной оси ленты приведены на Рис.4 и Рис.5. Допускается изготовление «прямого» стыка с расположением торцовых кромок и границ ступеней перпендикулярно продольной оси ленты. Длина стыка, минимальная длина ступени и рекомендуемая схема соединения в зависимости от типа ленты приведены в таблице 1.
|
Для всех типов лент допускается одноступенчатая конструкция стыкового соединения с частичной вырубкой тросов. Разрывная прочность таких одноступенчатых стыков будет ниже, но вероятность раздвижки тросов и перекоса в месте стыка при его вулканизации снижается и, кроме этого, одноступенчатые стыки короче, чем многоступенчатые, что немаловажно при выполнении срочных стыковочных работ. Это стыковое соединение разработано ВостНИИ и получило название «Ступень-1». Стыки «Ступень-1» прошли испытания на шахтах «Ленинскуголь» на лентах 2РТЛО-3150.
2.3 Разделка концов лент и сборка стыковых соединений.
Концы лент перед разделкой должны быть очищены от грязи, промыты и просушены. На обоих концах лент размечается длина стыка и по крайней границе с обеих сторон подрезаются обкладки. Наружные обкладки удаляются с концов ленты. Для удобства их снятия лента в пределах стыкового соединения разрезается на полосы шириной 150 – 200 мм, затем подрезают обкладки для удаления их воротом. Оставшуюся между тросами резину вырезают ножом, не допуская оголения тросов, так как это приводит к снижению прочности стыкового соединения (Рис.6). Нож должен передвигаться вдоль тросов перпендикулярно плоскости ленты. Оставшиеся торцевые поверхности верхних и нижних обкладок обрезают под углом на ширину 25 мм и тщательно зачищают полученные фаски. Тросы в «резиновых чулках» промывают бензином, просушивают, промазывают со всех сторон клеем (Рис.7) и вновь просушивают.
Сборка стыка начинается с укладки слоя ткани (или целлофановой пленки) на нижнюю плиту пресса. Нагревательные плиты пресса в продольном направлении, с каждой стороны, должны выходить за пределы стыкового соединения как минимум на 100 мм, а в поперечном, с каждой стороны, шире, чем конвейерная лента как минимум на 50 мм.
Затем на ткань укладывают сдублированную резиновую заготовку, состояющую из нескольких слоёв обкладочной резины суммарной толщиной, равной толщине обкладок и площадью, соответствующей площади стыка. Поверх уложенной заготовки укладывается слой прослоечной резины (Рис.8). Все склеиваемые поверхности резиновых слоёв заготовок должны быть предварительно освежены бензином, просушены, промазаны клеем и вновь высушены до слегка липкого состояния, а после совмещения слоёв их необходимо тщательно прикатать роликом. Прикатка осуществляется от середины к краям. Протерев поверхность заготовки бензином, промазав её клеем и просушив до слегка липкого состояния, начинают укладку тросов. Перед укладкой обрезиненные тросы вторично покрывают клеем и просушивают. Раскладка тросов согласно схеме соединения начинается от краёв стыка и производится строго параллельно оси. Обрезка тросов осуществляется специальными ножницами в соответствии со схемами на (Рис.4, Рис.5). К каждому уложенному тросу приклеивают полоску прослоечной резины толщиной, равной зазору между тросами. Крайние тросы должны располагаться по направлению движения ленты. Тросы должны укладываться плотно, без воздушных пузырей между ними. Зазоры между концами тросов заполняются прослоечной резиной. Укладка слоёв прослоечной и обкладочной резины верхнего пакета заготовки на поверхность уложенных тросов производится таким же образом, как и нижнего пакета.
|
Стык прикатывается роликом и простукивается молотком для удаления воздуха. Собранный стык покрывается тканью.
Для получения качественного соединения ленты необходимо соблюдать чистоту и аккуратность при работе. Загрязнение стыка попадание штыба, крошек резины, недостаточная просушка растворителя и клея приводят к образованию пор в резине и снижению прочности стыка.
Технология изготовления стыков «Ступень – 1» несколько отличается от технологии изготовления других стыков. У этих стыков вырубают лишние тросы у границ стыка. В лентах 2РТЛО-1500 и 2РТЛО-2150 вырубают каждый четвёртый трос, а в лентах 2РТЛО-3150 вырубают каждый третий. Вырубку начинают со второго, третьего или четвёртого от кромки ленты троса. Крайние тросы всегда оставляют целыми. При изготовлении заготовок обкладок и в процессе сборки стыка клей не применяют.
2.4 Вулканизация стыка.
На нижней плите пресса устанавливают ограничительные линейки, толщина которых меньше толщины целой части ленты на 1,0 -1,5 мм. Устанавливают верхнюю плиту пресса и создают давление. Удельное давление плит на участке соединения должно быть не менее 1,5 Мпа (15 кгс/см²). Вулканизация осуществляется в соответствии с режимом, указанным в технологической карте ППР. Время вулканизации при температуре 145°±5°С составляет от 40 до 52 минут, в зависимости от толщины заготовки стыка перед вулканизацией и толщины готовой ленты. Отсчёт времени вулканизации начинается с момента достижения температуры в плитах пресса 140°С. Снятие давления и разъём плит пресса производится при остывании плит до температуры 70°С.
Если вулканизационным прессом невозможно осуществить вулканизацию всего стыка за один приём из-за недостаточной площади плит, то стыковка производится в несколько приёмов. При перестановке пресса перекрывают завулканизированный участок на 100 мм. Вулканизацию стыка в несколько приёмов начинают только со средней части. Это даёт возможность закрепить все элементы соединения, равномерно распределить резину в обе стороны и удалить оставшийся воздух в стыке. При вулканизации стыка одновременно несколькими прессами соединение перекрывается металлическим листом толщиной 1-3 мм.
Каждое стыковое соединение нумеруется в виде рельефного оттиска (или гравировки) на верхней обкладке (Рис.9). Для нанесения номера используется набор жестяных пластинок с выштампованными выпуклыми цифрами. Пластинки закладываются между плитой пресса и резиновой обкладкой ленты выпуклыми цифрами в сторону обкладки.
|
|
Наброски и зарисовки растений, плодов, цветов: Освоить конструктивное построение структуры дерева через зарисовки отдельных деревьев, группы деревьев...
История создания датчика движения: Первый прибор для обнаружения движения был изобретен немецким физиком Генрихом Герцем...
Биохимия спиртового брожения: Основу технологии получения пива составляет спиртовое брожение, - при котором сахар превращается...
Архитектура электронного правительства: Единая архитектура – это методологический подход при создании системы управления государства, который строится...
© cyberpedia.su 2017-2024 - Не является автором материалов. Исключительное право сохранено за автором текста.
Если вы не хотите, чтобы данный материал был у нас на сайте, перейдите по ссылке: Нарушение авторских прав. Мы поможем в написании вашей работы!