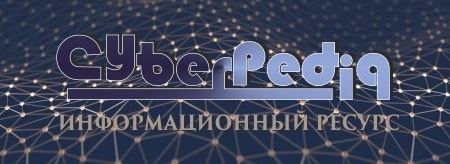
Опора деревянной одностоечной и способы укрепление угловых опор: Опоры ВЛ - конструкции, предназначенные для поддерживания проводов на необходимой высоте над землей, водой...
История развития пистолетов-пулеметов: Предпосылкой для возникновения пистолетов-пулеметов послужила давняя тенденция тяготения винтовок...
Топ:
Процедура выполнения команд. Рабочий цикл процессора: Функционирование процессора в основном состоит из повторяющихся рабочих циклов, каждый из которых соответствует...
Характеристика АТП и сварочно-жестяницкого участка: Транспорт в настоящее время является одной из важнейших отраслей народного...
Особенности труда и отдыха в условиях низких температур: К работам при низких температурах на открытом воздухе и в не отапливаемых помещениях допускаются лица не моложе 18 лет, прошедшие...
Интересное:
Национальное богатство страны и его составляющие: для оценки элементов национального богатства используются...
Отражение на счетах бухгалтерского учета процесса приобретения: Процесс заготовления представляет систему экономических событий, включающих приобретение организацией у поставщиков сырья...
Аура как энергетическое поле: многослойную ауру человека можно представить себе подобным...
Дисциплины:
![]() |
![]() |
5.00
из
|
Заказать работу |
|
|
Введение
Высокопроизводительная работа современного предприятия невозможна без правильно организованных и надежно работающих средств промышленного транспорта. Промышленный транспорт по территориальному признаку разделяют на внешний и внутренний (внутризаводской). Выбор средства межцехового транспортирования определяется главным образом масштабом и типом производства. На современных предприятиях с массовым и крупносерийным производством межцеховое транспортирование осуществляется в основном конвейерами. Для таких предприятий характерна организация сквозного транспортирования, объединяющего межцеховые и внутрицеховые функции, т. е. ввод межцехового конвейера непосредственно в цех, исключая промежуточные перегрузки.
На современном предприятии транспортные и технологические линии взаимосвязаны и представляют собой единую производственную систему. Правильная организация и бесперебойная работа межцехового и внутрицехового транспорта являются таким же обязательным условием успешной работы предприятия, как и рациональная организация производственных процессов.
ПАО «Уралкалий» - одна из крупнейших химических компаний России, является ведущим мировым производителем минеральных удобрений.
Основной специализацией компании является производство калийных удобрений (хлорида калия).
Компания была основана в 1930 году как государственное предприятие и акционирована в 1992 году. Компания «Уралкалий» была зарегистрирована 14 октября 1992 года как открытое акционерное общество в Российской Федерации.
В 2007 году «Уралкалий» стал первой российской публичной компанией химического сектора, акции которой торгуются на биржах РТС, ММВБ и Ь8Е. По результатам рейтингов крупнейших российских предприятий за 2015 год, проведенных ведущими изданиями России, «Уралкалий» входит в ТОП-30 компаний по капитализации.
|
17 мая 2011 года состоялась реорганизация ОАО «Сильвинит» в форме присоединения к ОАО «Уралкалий». ОАО «Уралкалий» стал универсальным правопреемником ОАО «Сильвинит».
Доля «Уралкалия» на мировом рынке хлорида калия составляет порядка 26%. Более 90% продукции «Уралкалия» направляется на экспорт, преимущественно в Китай, Бразилию, Юго-Восточную Азию и Индию - наиболее перспективные и активно развивающиеся калийные рынки, где компания имеет лидирующие позиции. Продукция «Уралкалия» также реализуется в России, странах Европы, на Ближнем Востоке, в США.
ПАО «Уралкалий» – вертикально интегрированный производитель калия, который контролирует всю производственную цепочку – от добычи руды до поставок калийных удобрений покупателям. Такой подход минимизирует риски для поставщиков, позволяя оптимизировать работу на каждом уровне производства и логистики.
ПАО «Уралкалий» уделяет большое внимание поддержанию низкой себестоимости продукции, отсутствию несчастных случаев и аварий, минимизации негативного воздействия на окружающую среду и высокое качество производимой продукции. «Уралкалий» вкладывает средства в развитие персонала и предлагает широкие возможности для профессионального роста.
ПАО «Уралкалий» - ведущий мировой производитель калия, одного из важнейших элементов, необходимых для развития всех живых организмов. На долю Компании приходится около 20% мирового производства калийных удобрений. Компания контролирует всю производственную цепочку от добычи калийной руды до поставок хлористого калия покупателям.
Активы Компании включают пять рудников, шесть калийных и одну карналлитовую фабрику, которые расположены в городах Березники и Соликамск Пермского края. Компании также принадлежат лицензии на разработку двух новых участков. ПАО «Уралкалий» разрабатывает одно из крупнейших в мире Верхнекамское месторождение калийно-магниевых солей, которое по величине является вторым в мире, после Соскачеванского месторождения, которое находится в Канаде. Запасы сильвинита (сырья для производства хлористого калия), принадлежащие ПАО «Уралкалий», составляют в относительном выражении 22 % от общемировых. В абсолютном выражении запасы залегающих солей равны около 8,8 млрд. тонн, что при текущих уровнях добычи может обеспечить компанию сырьем на 200 лет.
|
Значительная часть природных калийных солей перерабатывают в технический продукт хлористый калий, который используется как удобрение, вносимое либо напрямую в почву, либо в составе сложных, комплексных, удобрений. Помимо этого хлористый калий используется и в других отраслях промышленности: химической, нефтехимической, пищевой, фармацевтической.
Обогащенный карналлит (магниевые соли) и продукция каменной соли (поваренная соль пищевая, техническая, для животноводства, рыбной промышленности и т.д.) реализуются отечественным потребителям для производства продукции, в том числе поставляемой на экспорт.
В настоящее время в Березниках добыча ведётся на втором и четвёртом калийных комбинатах. Моя практика проходила на БКРУ-2.
Проектирование Второго Березниковского калийного комбината выполнялось на основании планового задания от 11 апреля 1960 года, согласно которому комбинат должен развить производственную мощность по хлористому калию 3 млн. тонн в год.
Геологической основой для проектирования послужил «Отчет о разведке Дурыманского участка Верхнекамского месторождения калийных солей», составленный Уральским геологическим Управлением в 1957 году и протокол по утверждению запасов калийных солей Дурыманского участка.
В 1963 году начато строительство рудника Второго Березниковского калийного комбината, который был введен в эксплуатацию в 1970 году мощностью 7 млн. тонн сильвинитовой руды в год.
1964 год - начало проходки ствола № 3, начало забивки свай под главный корпус флотационной фабрики. 1965 год - начало проходки стволов № 1 и № 2.
28 ноября 1969 года - вступила в строй первая очередь предприятия.
25 декабря 1970 года - вступила в строй вторая очередь предприятия мощностью 1,5 млн. тонн удобрений в год.
|
Размеры шахтного поля рудника составляют: в меридиональном направлении - 7950 м, в широтном — 7700 м.
Цель работы – изучить технологию стыковки резинотросовых лент при монтаже конвейеров в конвейерных выработках калийных рудников.
Подготовка к стыковке и технология стыковки
Резинотросовых лент.
Стыковка резинотросовых конвейерных лент осуществляется методом горячей вулканизации. При этом последовательно выполняется ряд операций: подготовка рабочего места и стыковочных материалов, оборудования и инструментов, разделка стыкуемых концов лент, сборка и вулканизация стыка.
Для выполнения работ по стыковке и вулканизации резинотросовых лент выбирается место в наиболее удобном участке выработки вблизи возможных пунктов подключения к электросети – это может быть участок става конвейера в районе натяжной или выносной станций, а также в сбойках, где есть возможность работы с автотракторной техникой.
2.1 Подготовка рабочего места.
На участке става, выбранном под рабочее место, демонтируются роликоопоры верхней ветви и устанавливаются столы для разделки ленты или на став укладывается сплошной деревянный настил из досок толщиной 40мм и устанавливается вулканизационный пресс. Настил или столы устанавливаются по обе стороны пресса так, чтобы образовалась рабочая площадка, ширина которой должна быть на 200-300 мм больше ширины ленты, а длина на 1,5-2,0 м больше длины стыка. Для предотвращения попадания влаги на стыкуемые поверхности, если в выработке с кровли идёт «капёж», над рабочим местом устанавливается навес. Рабочее место должно устраиваться на том участке става, где исключён сбор стекающего по ленте конденсата и образования луж. Для обеспечения подгонки стыков к рабочему месту и возможности работы без демонтажа настилов (или столов) и вулканизатора необходимо устанавливать специально изготовленные роликоопоры, позволяющие верхней ветви ленты проходить над настилами (или столами) и над вулканизатором (нижними жёсткостями) с гарантированным зазором.
В подготовку рабочего места также входит:
|
- уборка площадки от посторонних предметов;
- очистка участка длиной 10-15 м от грязи и пыли;
- доставка и расстановка оборудования и материалов;
- подключение оборудования к сети электроснабжения;
- крепление лебёдок, бурение шпуров под конусы и монтаж блочков;
- доставка, подвеска и раскатка ленты;
- обеспечение необходимыми инструментами и приспособлениями в нужном количестве, стыковочными материалами, рекомендованными заводом-изготовителем конвейерных лент, с гарантированным качеством и не истёкшим сроком хранения.
2.2 Подготовка концов лент и схемы их соединений.
На стыкуемых концах посередине ленты трассировочным шнуром наносят осевую линию, длина которой должна быть 3–5 м. От конца ленты на расстоянии, равном длине стыка плюс 0,5-1,5 м, проводят с помощью угольника линию, перпендикулярную осевой линии отрезка ленты. При отсутствии угольника перпендикулярная линия может быть проведена при помощи геометрических построений (Рис.2, Рис.3) следующим образом. На оси отмечается точка а, от которой откладывается отрезок ав = 400 мм и ас = 800 мм. Из точек а и с радиусом R = 500 мм делают засечки. Через точки d и е проводят прямую. Отрезок АВ будет перпендикулярен оси, если проходит через точку в, а отрезок в d = в e = 300 мм. Все последующие измерения при разметке стыкового соединения производят от базовых перпендикулярных линий АВ или А'В', которые закрываются прозрачной плёнкой, приклеиваемой к ленте. При разметке «косого» стыка длина отрезка АО, откладываемого от базовой линии АВ, превышает длину отрезка ВМ на 1/3 ширины ленты. В случае разметки прямого стыка, откладываемые от базовой линии отрезки ВМ и АО имеют одинаковую длину. Зажимы стяжного приспособления устанавливают по перпендикулярным линиям и стягивают концы ленты с таким расчётом, чтобы они были совмещены внахлёстку на длину стыка. Натяжной барабан должен быть отведён в положение с учётом возможности выполнения последующих стыковок. После наложения друг на друга концов лент внахлёстку проверяют параллельность кромок и средней линии. Оси обоих концов ленты будут лежать на одной прямой, если АА'=ВВ'. Отклонения не должны превышать двух миллиметров. Схемы соединения концов резинотросовых лент методом горячей вулканизации с расположением торцевых кромок и границ ступеней под углом 71° 30' к продольной оси ленты приведены на Рис.4 и Рис.5. Допускается изготовление «прямого» стыка с расположением торцовых кромок и границ ступеней перпендикулярно продольной оси ленты. Длина стыка, минимальная длина ступени и рекомендуемая схема соединения в зависимости от типа ленты приведены в таблице 1.
Для всех типов лент допускается одноступенчатая конструкция стыкового соединения с частичной вырубкой тросов. Разрывная прочность таких одноступенчатых стыков будет ниже, но вероятность раздвижки тросов и перекоса в месте стыка при его вулканизации снижается и, кроме этого, одноступенчатые стыки короче, чем многоступенчатые, что немаловажно при выполнении срочных стыковочных работ. Это стыковое соединение разработано ВостНИИ и получило название «Ступень-1». Стыки «Ступень-1» прошли испытания на шахтах «Ленинскуголь» на лентах 2РТЛО-3150.
|
2.3 Разделка концов лент и сборка стыковых соединений.
Концы лент перед разделкой должны быть очищены от грязи, промыты и просушены. На обоих концах лент размечается длина стыка и по крайней границе с обеих сторон подрезаются обкладки. Наружные обкладки удаляются с концов ленты. Для удобства их снятия лента в пределах стыкового соединения разрезается на полосы шириной 150 – 200 мм, затем подрезают обкладки для удаления их воротом. Оставшуюся между тросами резину вырезают ножом, не допуская оголения тросов, так как это приводит к снижению прочности стыкового соединения (Рис.6). Нож должен передвигаться вдоль тросов перпендикулярно плоскости ленты. Оставшиеся торцевые поверхности верхних и нижних обкладок обрезают под углом на ширину 25 мм и тщательно зачищают полученные фаски. Тросы в «резиновых чулках» промывают бензином, просушивают, промазывают со всех сторон клеем (Рис.7) и вновь просушивают.
Сборка стыка начинается с укладки слоя ткани (или целлофановой пленки) на нижнюю плиту пресса. Нагревательные плиты пресса в продольном направлении, с каждой стороны, должны выходить за пределы стыкового соединения как минимум на 100 мм, а в поперечном, с каждой стороны, шире, чем конвейерная лента как минимум на 50 мм.
Затем на ткань укладывают сдублированную резиновую заготовку, состояющую из нескольких слоёв обкладочной резины суммарной толщиной, равной толщине обкладок и площадью, соответствующей площади стыка. Поверх уложенной заготовки укладывается слой прослоечной резины (Рис.8). Все склеиваемые поверхности резиновых слоёв заготовок должны быть предварительно освежены бензином, просушены, промазаны клеем и вновь высушены до слегка липкого состояния, а после совмещения слоёв их необходимо тщательно прикатать роликом. Прикатка осуществляется от середины к краям. Протерев поверхность заготовки бензином, промазав её клеем и просушив до слегка липкого состояния, начинают укладку тросов. Перед укладкой обрезиненные тросы вторично покрывают клеем и просушивают. Раскладка тросов согласно схеме соединения начинается от краёв стыка и производится строго параллельно оси. Обрезка тросов осуществляется специальными ножницами в соответствии со схемами на (Рис.4, Рис.5). К каждому уложенному тросу приклеивают полоску прослоечной резины толщиной, равной зазору между тросами. Крайние тросы должны располагаться по направлению движения ленты. Тросы должны укладываться плотно, без воздушных пузырей между ними. Зазоры между концами тросов заполняются прослоечной резиной. Укладка слоёв прослоечной и обкладочной резины верхнего пакета заготовки на поверхность уложенных тросов производится таким же образом, как и нижнего пакета.
Стык прикатывается роликом и простукивается молотком для удаления воздуха. Собранный стык покрывается тканью.
Для получения качественного соединения ленты необходимо соблюдать чистоту и аккуратность при работе. Загрязнение стыка попадание штыба, крошек резины, недостаточная просушка растворителя и клея приводят к образованию пор в резине и снижению прочности стыка.
Технология изготовления стыков «Ступень – 1» несколько отличается от технологии изготовления других стыков. У этих стыков вырубают лишние тросы у границ стыка. В лентах 2РТЛО-1500 и 2РТЛО-2150 вырубают каждый четвёртый трос, а в лентах 2РТЛО-3150 вырубают каждый третий. Вырубку начинают со второго, третьего или четвёртого от кромки ленты троса. Крайние тросы всегда оставляют целыми. При изготовлении заготовок обкладок и в процессе сборки стыка клей не применяют.
2.4 Вулканизация стыка.
На нижней плите пресса устанавливают ограничительные линейки, толщина которых меньше толщины целой части ленты на 1,0 -1,5 мм. Устанавливают верхнюю плиту пресса и создают давление. Удельное давление плит на участке соединения должно быть не менее 1,5 Мпа (15 кгс/см²). Вулканизация осуществляется в соответствии с режимом, указанным в технологической карте ППР. Время вулканизации при температуре 145°±5°С составляет от 40 до 52 минут, в зависимости от толщины заготовки стыка перед вулканизацией и толщины готовой ленты. Отсчёт времени вулканизации начинается с момента достижения температуры в плитах пресса 140°С. Снятие давления и разъём плит пресса производится при остывании плит до температуры 70°С.
Если вулканизационным прессом невозможно осуществить вулканизацию всего стыка за один приём из-за недостаточной площади плит, то стыковка производится в несколько приёмов. При перестановке пресса перекрывают завулканизированный участок на 100 мм. Вулканизацию стыка в несколько приёмов начинают только со средней части. Это даёт возможность закрепить все элементы соединения, равномерно распределить резину в обе стороны и удалить оставшийся воздух в стыке. При вулканизации стыка одновременно несколькими прессами соединение перекрывается металлическим листом толщиной 1-3 мм.
Каждое стыковое соединение нумеруется в виде рельефного оттиска (или гравировки) на верхней обкладке (Рис.9). Для нанесения номера используется набор жестяных пластинок с выштампованными выпуклыми цифрами. Пластинки закладываются между плитой пресса и резиновой обкладкой ленты выпуклыми цифрами в сторону обкладки.
И способы их устранения
Надежная работа конвейерных лент зависит от правильного выбора ее типа, конструкции и исполнения, качества монтажа и способа соединения, хранения до начала эксплуатации, а также правильности ее эксплуатации на конвейере. Срок службы может быть значительно увеличен, если в процессе эксплуатации лента подвергается профилактическому и техническому ремонтам.
В табл.1 представлены возможные неполадки в ленте при ее эксплуатации и рекомендуемые мероприятия по их устранению.
Таблица 1.
Неполадки | Причины | Способы устранения |
1 | 2 | 3 |
1. Лента буксует на приводном барабане | Недостаточное натяжение ленты | Увеличить натяжение ленты |
Заклинивание ленты | Обнаружить место заклинивания и устранить причину, вызывающие его | |
Попадание на ленту и на поверхность барабана масляных продуктов, штыба, влаги и т.п. | Удалить масло, штыб и влагу. Насухо протереть барабан. Установить очистное устройство для очистки поверхности ленты | |
Заштыбовка большого числа нижних роликов | Расштыбовать ролики | |
Отсутствие или сильный износ футеровки барабана. | Заменить барабан на футерованный или произвести футерование поверхности барабана соответствующим материалом | |
Перегрузка конвейера | Уменьшить нагрузку до расчетной | |
Недостаточный угол обхвата лентой барабана | Увеличить угол обхвата лентой барабана | |
Лента сильно перетянута | Ослабить натяжение ленты посредством натяжного устройства до расчетной величины |
Продолжение таблицы 1.
1 | 2 | 3 |
2. Лента сбивается в сторону на барабанах | Перекошены барабаны | Устранить перекос барабанов |
Попадание смазки на поверхность барабанов | Удалить смазку, протереть насухо поверхность барабана и устранить причину ее попадания | |
Одностороннее налипание штыба на барабан | Устранить налипание штыба | |
Концы ленты перекошены при стыковке | Перестыковать ленту | |
Односторонняя загрузка материала на ленту | Отцентрировать загрузочное устройство | |
Стационарные и регулируемые ролики не установлены соответственно движению ленты | Отцентрировать ленту с помощью стационарных и регулируемых роликов | |
3. Лента сбивается в сторону нижних и верхних роликов средней части става | Перекос одного или нескольких роликов перед участком сбегания | Переместить в направлении движения ленты тот конец ролика, в направлении которого сбегает лента |
Искривленность става | Произвести рихтовку става | |
Не вращается часть роликов | Проверить состояние роликов, невращающиеся ролики заменить | |
Поверхности части роликов облеплены материалом | Очистить поверхность ролика | |
Роликоопоры расположены не горизонтально | Установить роликовые опоры горизонтально | |
Перекос концевых и отклоняющих барабанов | Отрегулировать положение барабанов | |
Односторонняя загрузка конвейера | Устранить одностороннюю загрузку ленты | |
Отдельные куски ленты непрямолинейны | Перестыковать ленту или заменить отрезок ленты | |
4.Повышен - ный износ рабочей обкладки | Загрязнились или заклинились опорные ролики нижней ветви конвейера | Очистить и заменить неисправленные ролики. Улучшить очистку ленты. |
Большая разность между скоростью ленты и скоростью падающего груза в месте загрузки | Установить загрузочный лоток, придающий грузу скорость, близкую к скорости ленты |
Продолжение таблицы 1.
1 | 2 | 3 |
| Большой провес ленты между опорными роликами нижней ветви. Лента касается почвы | Увеличить натяжение ленты, если оно меньше расчетного. Уменьшить расстояние между роликоопорами |
Уплотнения загрузочных лотков не обрезинены | Установить обрезиненные борта загрузочных лотков | |
Концевой барабан завален штыбом | Расчистить концевой барабан | |
Нижняя часть става заштыбована и лента движется по слою штыба | Расштыбовать став конвейера | |
5. Повышенный износ нерабочей обкладки ленты | Лента на приводном барабане пробуксовывает | Увеличить натяжение ленты до расчетного значения |
Ролики верхней ветви не вращаются | Очистить ролики, заменить неисправные | |
Материал просыпается на нижнюю ветвь ленты и затягивается под барабан | Установить сбрасыватель между ветвями ленты. Отрегулировать загрузку ленты | |
6. Пробой резиновой обкладки и небольшие порывы прокладок каркаса | Отсутствие загрузочного лотка и большая высота падения материала на ленту | Установить загрузочный лоток Установить амортизирующие ролики Отрегулировать загрузку материала на конвейер, чтобы он падал на ленту в пролете между роликоопорами. Уменьшить высоту свободного падения транспортируемого материала на ленту |
7. Разрыв стыкового соединения | Некачественное соединение ленты | Перестыковать ленту в соответствии с инструкцией. Использовать свежий ремонтный материал при вулканизации стыка. Использовать рекомендуемые резины и клея завода-изготовителя ленты |
Несоответствующий (значительно меньший) диаметр приводного барабана) | Применять данный тип стыковки на лентах, работающих с приводными барабанами большего диаметра | |
Транспортируемый материал попадает между лентой и барабаном | Установить очистное устройство (сбрасыватель) на нижней ветви конвейера перед барабаном. |
Продолжение таблицы 1.
1 | 2 | 3 |
Неправильно выбрана переходная зона между желобчатостью и разгрузочным барабаном | Увеличить длину переходной зоны или приподнять ее относительно днища лотка (желобчатости) | |
8. Износ кромок ленты | Кромки лент трутся о неподвижные части рам става конвейера вследствии смещения ленты в сторону | Отцентрировать движение ленты |
9. Продольные порезы рабочей обкладки | Отсутствуют поддержи-вающие ролики, лента задевает за кромки кронштейна | Не допускать работу конвейера без поддерживающих роликов |
Уплотнения загрузочных лотков очень плотно прижимаются к ленте и они очень жесткие | Установить более эластичные резиновые уплотнения (полосы). Выдерживать определенное расстояние между поверхностью ленты и уплотнениями. Применять специальные резиновые полосы, а не куски старых резинотканевых лент | |
Лента трется о металли-ческие части загрузочного лотка | Отрегулировать зазор между лентой и металлическими элементами лотка. | |
10. Поперечные порывы у края ленты | Загибание ленты вверх на барабане или вблизи него | Улучшить центрирование ленты. Установить концевые выключатели, срабатывающие при сходе ленты в сторону. |
Последняя роликоопора рабочей ветви расположена слишком близко к разгрузочному барабану | Отодвинуть или снять последнюю роликоопору. Установить переходные роликоопоры. | |
Лента имеет повышенную серповидность | Перестыковать участок серповидной ленты (заменив на новый). Проверить условия складирования лент и их транспортировку в соответствии с заводскими рекомендациями. |
Продолжение таблицы 1.
1 | 2 | 3 |
11. Разбухание резины обкладок, вспучивание и образование пузырей на обкладке | Обильное попадание масла на обкладку | Проверить уплотнение подшипниковых узлов опорных роликов. Установить причину попадания масла на ленту и исключить таковое в дальнейшем. |
Попадание влаги и пыли через мелкие пробои верхней обкладки | Периодически осматривать ленту и ремонтировать мелкие повреждения. | |
12. Обкладки ленты твердеют или растрескиваются | Химическое или термическое повреждение | Поставить ленту соответствующего исполнения для данных конкретных условий эксплуатации. |
Неправильное складирование и транспортирование | Хранить и транспортировать ленту в соответствии с рекомендациями завода-изготовителя лент. | |
13. Механические соединительные элементы выдергиваются из соединенных концов лент (стык) | Длина соединительных элементов не соответствует диаметру приводного барабана | Заново состыковать ленту, используя меньшую длину соединительных элементов. Заменить механическое соединение в соответствии с рекомендуемым диаметром приводного барабана. |
Неправильно выбран типоразмер соединитель-ных элементов | Применить механические соединительные элементы, соответствующие прочности ленты и ее толщине. | |
14. Точечный износ (в виде воронок) рабочей обкладки новой ленты | Нерациональное соотношение толщины обкладок к толщине тканевого сердечника | Заменить ленту с меньшей толщиной рабочей обкладки или на ленту с большей толщиной тканевого сердечника |
15. Точечный износ (в виде воронок) рабочей окладки работающей ленты | Попадание масла или смазки на обкладку ленты | Проверить уплотнение подшипниковых узлов роликов. Исключить попадание масел на ленту путем проведения соответствующих мероприятий. |
Эксплуатация шахтных (трудно воспламеняющихся, трудно сгораемых, трудно горючих) конвейерных лент должна осуществляться в соответствии с «Руководством по эксплуатации подземных ленточных конвейеров в угольных и сланцевых шахтах».
Введение
Высокопроизводительная работа современного предприятия невозможна без правильно организованных и надежно работающих средств промышленного транспорта. Промышленный транспорт по территориальному признаку разделяют на внешний и внутренний (внутризаводской). Выбор средства межцехового транспортирования определяется главным образом масштабом и типом производства. На современных предприятиях с массовым и крупносерийным производством межцеховое транспортирование осуществляется в основном конвейерами. Для таких предприятий характерна организация сквозного транспортирования, объединяющего межцеховые и внутрицеховые функции, т. е. ввод межцехового конвейера непосредственно в цех, исключая промежуточные перегрузки.
На современном предприятии транспортные и технологические линии взаимосвязаны и представляют собой единую производственную систему. Правильная организация и бесперебойная работа межцехового и внутрицехового транспорта являются таким же обязательным условием успешной работы предприятия, как и рациональная организация производственных процессов.
ПАО «Уралкалий» - одна из крупнейших химических компаний России, является ведущим мировым производителем минеральных удобрений.
Основной специализацией компании является производство калийных удобрений (хлорида калия).
Компания была основана в 1930 году как государственное предприятие и акционирована в 1992 году. Компания «Уралкалий» была зарегистрирована 14 октября 1992 года как открытое акционерное общество в Российской Федерации.
В 2007 году «Уралкалий» стал первой российской публичной компанией химического сектора, акции которой торгуются на биржах РТС, ММВБ и Ь8Е. По результатам рейтингов крупнейших российских предприятий за 2015 год, проведенных ведущими изданиями России, «Уралкалий» входит в ТОП-30 компаний по капитализации.
17 мая 2011 года состоялась реорганизация ОАО «Сильвинит» в форме присоединения к ОАО «Уралкалий». ОАО «Уралкалий» стал универсальным правопреемником ОАО «Сильвинит».
Доля «Уралкалия» на мировом рынке хлорида калия составляет порядка 26%. Более 90% продукции «Уралкалия» направляется на экспорт, преимущественно в Китай, Бразилию, Юго-Восточную Азию и Индию - наиболее перспективные и активно развивающиеся калийные рынки, где компания имеет лидирующие позиции. Продукция «Уралкалия» также реализуется в России, странах Европы, на Ближнем Востоке, в США.
ПАО «Уралкалий» – вертикально интегрированный производитель калия, который контролирует всю производственную цепочку – от добычи руды до поставок калийных удобрений покупателям. Такой подход минимизирует риски для поставщиков, позволяя оптимизировать работу на каждом уровне производства и логистики.
ПАО «Уралкалий» уделяет большое внимание поддержанию низкой себестоимости продукции, отсутствию несчастных случаев и аварий, минимизации негативного воздействия на окружающую среду и высокое качество производимой продукции. «Уралкалий» вкладывает средства в развитие персонала и предлагает широкие возможности для профессионального роста.
ПАО «Уралкалий» - ведущий мировой производитель калия, одного из важнейших элементов, необходимых для развития всех живых организмов. На долю Компании приходится около 20% мирового производства калийных удобрений. Компания контролирует всю производственную цепочку от добычи калийной руды до поставок хлористого калия покупателям.
Активы Компании включают пять рудников, шесть калийных и одну карналлитовую фабрику, которые расположены в городах Березники и Соликамск Пермского края. Компании также принадлежат лицензии на разработку двух новых участков. ПАО «Уралкалий» разрабатывает одно из крупнейших в мире Верхнекамское месторождение калийно-магниевых солей, которое по величине является вторым в мире, после Соскачеванского месторождения, которое находится в Канаде. Запасы сильвинита (сырья для производства хлористого калия), принадлежащие ПАО «Уралкалий», составляют в относительном выражении 22 % от общемировых. В абсолютном выражении запасы залегающих солей равны около 8,8 млрд. тонн, что при текущих уровнях добычи может обеспечить компанию сырьем на 200 лет.
Значительная часть природных калийных солей перерабатывают в технический продукт хлористый калий, который используется как удобрение, вносимое либо напрямую в почву, либо в составе сложных, комплексных, удобрений. Помимо этого хлористый калий используется и в других отраслях промышленности: химической, нефтехимической, пищевой, фармацевтической.
Обогащенный карналлит (магниевые соли) и продукция каменной соли (поваренная соль пищевая, техническая, для животноводства, рыбной промышленности и т.д.) реализуются отечественным потребителям для производства продукции, в том числе поставляемой на экспорт.
В настоящее время в Березниках добыча ведётся на втором и четвёртом калийных комбинатах. Моя практика проходила на БКРУ-2.
Проектирование Второго Березниковского калийного комбината выполнялось на основании планового задания от 11 апреля 1960 года, согласно которому комбинат должен развить производственную мощность по хлористому калию 3 млн. тонн в год.
Геологической основой для проектирования послужил «Отчет о разведке Дурыманского участка Верхнекамского месторождения калийных солей», составленный Уральским геологическим Управлением в 1957 году и протокол по утверждению запасов калийных солей Дурыманского участка.
В 1963 году начато строительство рудника Второго Березниковского калийного комбината, который был введен в эксплуатацию в 1970 году мощностью 7 млн. тонн сильвинитовой руды в год.
1964 год - начало проходки ствола № 3, начало забивки свай под главный корпус флотационной фабрики. 1965 год - начало проходки стволов № 1 и № 2.
28 ноября 1969 года - вступила в строй первая очередь предприятия.
25 декабря 1970 года - вступила в строй вторая очередь предприятия мощностью 1,5 млн. тонн удобрений в год.
Размеры шахтного поля рудника составляют: в меридиональном направлении - 7950 м, в широтном — 7700 м.
Цель работы – изучить технологию стыковки резинотросовых лент при монтаже конвейеров в конвейерных выработках калийных рудников.
Назначение, конструкция, типы и характеристики
|
|
Папиллярные узоры пальцев рук - маркер спортивных способностей: дерматоглифические признаки формируются на 3-5 месяце беременности, не изменяются в течение жизни...
Поперечные профили набережных и береговой полосы: На городских территориях берегоукрепление проектируют с учетом технических и экономических требований, но особое значение придают эстетическим...
Своеобразие русской архитектуры: Основной материал – дерево – быстрота постройки, но недолговечность и необходимость деления...
Типы сооружений для обработки осадков: Септиками называются сооружения, в которых одновременно происходят осветление сточной жидкости...
© cyberpedia.su 2017-2024 - Не является автором материалов. Исключительное право сохранено за автором текста.
Если вы не хотите, чтобы данный материал был у нас на сайте, перейдите по ссылке: Нарушение авторских прав. Мы поможем в написании вашей работы!