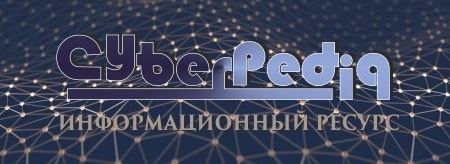
Автоматическое растормаживание колес: Тормозные устройства колес предназначены для уменьшения длины пробега и улучшения маневрирования ВС при...
Археология об основании Рима: Новые раскопки проясняют и такой острый дискуссионный вопрос, как дата самого возникновения Рима...
Топ:
Отражение на счетах бухгалтерского учета процесса приобретения: Процесс заготовления представляет систему экономических событий, включающих приобретение организацией у поставщиков сырья...
Особенности труда и отдыха в условиях низких температур: К работам при низких температурах на открытом воздухе и в не отапливаемых помещениях допускаются лица не моложе 18 лет, прошедшие...
Когда производится ограждение поезда, остановившегося на перегоне: Во всех случаях немедленно должно быть ограждено место препятствия для движения поездов на смежном пути двухпутного...
Интересное:
Средства для ингаляционного наркоза: Наркоз наступает в результате вдыхания (ингаляции) средств, которое осуществляют или с помощью маски...
Лечение прогрессирующих форм рака: Одним из наиболее важных достижений экспериментальной химиотерапии опухолей, начатой в 60-х и реализованной в 70-х годах, является...
Распространение рака на другие отдаленные от желудка органы: Характерных симптомов рака желудка не существует. Выраженные симптомы появляются, когда опухоль...
Дисциплины:
![]() |
![]() |
5.00
из
|
Заказать работу |
|
|
Системы программного управления в сварочной технике в основном работают по жесткой программе. Это в первую очередь устройства управлением сварочным циклом при механизированной сварке под флюсом и в среде защитных газов. Для управления последовательностью прохождения команд цикла в сварочном оборудовании имеются специальный блок или дополнительные устройства, если цикл короткий. Для сварки под флюсом цикл содержит: включение источника – подъем сварочной проволоки для зажигания дуги – подача электрода вниз с заданной скоростью и одновременное движение по линии шва – отключение движения – отключение подачи проволоки для заварки кратера – выключение источника. Сюда могут быть добавлены включение-выключение флюсоотсоса и других вспомогательных устройств. Более сложными являются циклы механизированной сварки в среде защитных газов. Для сварочного полуавтомата блок цикла реализует три варианта программного управления: сварка длинных швов, сварка коротких швов и сварка точками, рис. 50.
Рис. 50. Временные диаграммы (циклограммы) работы блока цикла сварочным полуавтоматом в режимах: сварка длинных швов (а); сварка коротких швов (б); сварка точками (в)
Сварка длинных швов начинается после однократного нажатия и отпускания кнопки «пуск» на горелке, рис. 50, а. При этом срабатывает клапан газа и через время продувки (на временной диаграмме не показано) включается источник питания и двигатель подачи проволоки. При замыкании электрода на свариваемый металл возбуждается дуга и начинается сварка, которая продолжается до повторного нажатия кнопки «пуск». После этого останавливается двигатель подачи проволоки и после её обгорания с погашением дуги с выдержкой tи отключается источник питания, потом через время tг отключается клапаном защитный газ. При сварке коротких швов (рис. 50, б) кнопку необходимо держать до окончания сварки. При сварке точками (рис. 50, в) двигатель подачи проволоки включается на заданное сварщиком время (регулируется на пульте управления). Подача электродной проволоки производится в течение заданных интервалов времени t1, t2, t3. Эти интервалы не зависят от длительности нажатия кнопки «пуск». Программа завершения сварки происходит автоматически с отпусканием кнопки после прохождения цикла.
|
При сварке неплавящимся электродом (рис. 51) нажатием «пуск» включается газовый клапан для предварительной продувки аргона и после выдержки времени tпг включаются источник питания и сварочный осциллятор. Возбуждается дуга и производится нарастание сварочного тока в течение времени tн с начального значения (5…15 А) до заданного. Через время tз.пр включается подача присадочной проволоки, а через время tз.к – движение каретки (движение сварочного трактора или головки). На рис. 51 время tн.п., tр.п. и tк.п. означает время начала, работы и окончания программы соответственно. После нажатия кнопки «стоп» происходит снижение тока, затем через время tпд начинается спад скорости подачи проволоки с последующим реверсом и через время tсд остановка движения. Процесс сварки прекращен, но защитный газ продолжает подаваться и отключается через время tз.о. Все выдержки времени регулируются от нуля до десятков секунд.
Программирование может производиться и при сварке мнопроходных стыковых швов, обеспечивая нужную последовательность заполнения разделки стыка. В этом случае программой задаются координаты перемещения сварочной горелки Х и У, рис. 52. Блоки программирования представляют собой аналоговые электронные или цифровые микропроцессорные устройства.
Рис. 51. Циклограмма работы блока управления при сварке неплавящимся
|
электродом
Рис. 52. Схемы заполнения разделки стыка (а) и перемещения П сварочной горелки по координатам Х (б) и У (в) при многослойной сварке; 1 – 7 – номера проходов при сварке стыка
Наиболее часто программирование применяется при сварке неплавящимся электродом неповоротных стыков труб различных диаметров (орбитальная сварка). Ранее упоминалась система блоков БАРС, где для этих целей имеется блок программирования, позволяющий четыре раза изменить параметры режима за время сварки неплавящимся электродом неповоротного стыка трубы диаметром до 150 мм. Программа реализуется при помощи электромеханических реле времени и электромагнитных реле. Для этих же целей предназначен комплекс фирмы ESAB, включающий источник питания с системой ЧПУ и специальную сварочную головку для орбитальной сварки. При применении орбитальной сварки окружность трубы разбивается на сектора, в каждом из которых устанавливаются оптимальные значения параметров. Таких секторов может быть до 100. При разбивке на четыре сектора (рис. 53) длина всей окружности трубы представляется равной единицы. Тогда точка 1 имеет координату 0,000 (точка начала сварки 1 выбирается оператором). В этом секторе устанавливаются параметры сварки, исходя из необходимости нагреть холодную трубу до проплавления. Параметры должны обеспечить оптимальное проплавление до следующей точки. Во втором секторе происходит переход шва на потолочное положение и параметры сварки должны соответственно измениться. Третий сектор характеризуется сваркой «на подъем» при нагретой трубе. В этом секторе следует скорректировать ток и скорость сварки. Окончание шва очень часто является проблемным при сварке. Необходимо учитывать автоподогрев и снизить ток. Для окончания шва координата точки конца шва выбирается больше 1,000 произвольно (максимально до 1,500). Кроме тока и скорости сварки могут программироваться поперечные колебания относительно оси шва, напряжение дуги, время задержки в начальной точке.
Рис. 53. Схематичное разбиение окружности трубы на секторы
Пример диаграммы такого рабочего цикла при импульсной сварке неплавящимся электродом показан на рис. 54.
Рис. 54. Временная диаграмма рабочего цикла: 1 – плавное нарастание тока; 2 – предварительный нагрев; 3 – первый сектор; 4 – плавное уменьшение тока при смене сектора; 5 – второй сектор; 6 – плавное нарастание тока; 7 – третий сектор; 8 – четвертый сектор; 9 – пятый сектор, плавное гашение дуги и остановка сварки
|
При импульсной сварке возможно программирование синхронного периодического изменения подачи электродной проволоки и движения сварочной головки в зависимости от тока, рис. 55. Для обеспечения высокого качества сварных соединений применяют системы управления с МП-контроллером и возможностью подключения компьютера (см. рис. 8).
Рис. 55. Временная диаграмма процесса синхронизации скорости сварки и
скорости подачи присадочной проволоки при импульсной сварки
В станках для сварки типовых деталей осуществляют цикловое программное управление. В таких станках после размещения собранного под сварку узла автоматически производится установка сварочной горелки на начало сварки, процесс сварки с перемещением головки или узла, удаление сварочной головки для съема узла и установки следующего. Последовательность операций может выполняться с помощью путевых выключателей. Такие системы называются системами с путевым контролем. Работа системы может быть описана с помощью графа функционирования. По графу функционирования, используя метод карт Карно, производится синтез системы с путевым контролем. Например, станок для сварки кольцевых швов узлов типа «проушина – втулка». Схема перемещения сварочной головки и собранного узла, установленного на планшайбе станка, при сварке показана на рис. 56.
Алгоритм функционирования позиционной автоматической системы такого станка содержит предписание: опустить сварочную головку на начало шва; включить технологическую операцию сварки (ТО) с одновременным вращением узла; по истечению заданного времени достаточного для сварки кольцевого шва с перекрытием (реле времени КТ), отключить вращение; выключить оборудование, обеспечивающее технологическую операцию сварки и поднять сварочную головку.
Рис. 56. Схема станка для сварки кольцевых швов: 1 – изделие; 2 – планшайба станка; 3 – станина станка; Y1 и Y2 электромагниты золотника; S1 и S2 – путевые выключатели; СГ – сварочная головка; ИП – источник питания; К1 – контакты реле; М – электродвигатель планшайбы; Ред – редуктор
|
Граф функционирования системы (без учета кратковременных задержек вращения на продувку газа и на подъем головки после остановки вращения) показан на рис. 57.
Более сложный алгоритм функционирования обеспечивается в станке для сварки двух симметричных половинок узла «вставка» продольными швами, рис. 58,59.
Рис. 57. Граф функционирования механизмов станка рис. 57
Рис. 58. Схема работы станка для сварки двух продольных симметричных швов: 1 – 9 последовательность перемещений при сварке и повороте узла; Q – усилия прижимов (условно – действительное расположение на схеме станка)
Рис. 59. Схема станка для сварки продольного шва: 1 – влагосборник; 2 - предохранительный клапан; 3 – лубрикатор; 4 – кран подачи воздуха в пневмоприжимы; 5 – кран пневмовыталкивателя; 6 – пневмоприжимы; 7 – пневмозолотники; 8 – пневмоцилиндр опускания-подъема горелки; 9 – пневмоцилиндр стопора; 10 – пневмоцилиндры поворота; 11 – пневмоцилиндр выталкивателя; SQ1…SQ8 – путевые выключатели; Y1...Y3 – электромагниты золотников; штрих пунктирной линией обведено расположение пневмоцилиндров прижимов на планшайбе (вверху) и схема их работы при зажиме узла (внизу)
После опускания сварочной головки, сварки и подъема головки – 1, 2, 3 (рис. 58), расстопоривается планшайба станка – 4; производится поворот на 180о – 5; снова стопорится – 6 и далее сварка в обратном направлении – 7, 8, 9. Все перемещения кроме движения сварочной горелки со скоростью сварки осуществляются пневматическими приводами (рис. 59). Последовательность работы пневмоустройств станка и сварки продольных швов (ТО) описывается следующим графом функционирования, рис.60.
Рис. 60. Граф функционирования механизмов станка рис. 58 и рис. 59
Поворот планшайбы на 180о обеспечивается включением электромагнита Y3.1 или Y3.2 в зависимости от того, в каком положении до этого была планшайба, т.е. какой путевой выключатель (SQ7 или SQ8) был включен.
Для более сложных и перестраиваемых перемещений рабочих органов сварочного оборудования применяют устройства с числовым программным управлением, используя опыт разработки металлорежущих станков с ЧПУ и робототехнических комплексов. Примером таких установок могут служить устройства для приварки или наплавки шипов грузового пола самолета (ИЭС им. Патона), машины для плазменной резки «Кристалл» (г. С-т Петербург), разработки известных фирм Швеции, Германии, Австрии и США.
|
|
Адаптации растений и животных к жизни в горах: Большое значение для жизни организмов в горах имеют степень расчленения, крутизна и экспозиционные различия склонов...
Индивидуальные очистные сооружения: К классу индивидуальных очистных сооружений относят сооружения, пропускная способность которых...
История создания датчика движения: Первый прибор для обнаружения движения был изобретен немецким физиком Генрихом Герцем...
Автоматическое растормаживание колес: Тормозные устройства колес предназначены для уменьшения длины пробега и улучшения маневрирования ВС при...
© cyberpedia.su 2017-2024 - Не является автором материалов. Исключительное право сохранено за автором текста.
Если вы не хотите, чтобы данный материал был у нас на сайте, перейдите по ссылке: Нарушение авторских прав. Мы поможем в написании вашей работы!