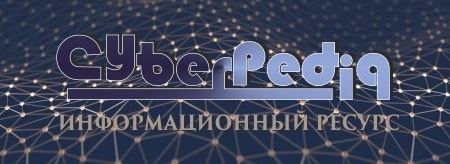
Таксономические единицы (категории) растений: Каждая система классификации состоит из определённых соподчиненных друг другу...
Организация стока поверхностных вод: Наибольшее количество влаги на земном шаре испаряется с поверхности морей и океанов (88‰)...
Топ:
Марксистская теория происхождения государства: По мнению Маркса и Энгельса, в основе развития общества, происходящих в нем изменений лежит...
История развития методов оптимизации: теорема Куна-Таккера, метод Лагранжа, роль выпуклости в оптимизации...
Особенности труда и отдыха в условиях низких температур: К работам при низких температурах на открытом воздухе и в не отапливаемых помещениях допускаются лица не моложе 18 лет, прошедшие...
Интересное:
Мероприятия для защиты от морозного пучения грунтов: Инженерная защита от морозного (криогенного) пучения грунтов необходима для легких малоэтажных зданий и других сооружений...
Распространение рака на другие отдаленные от желудка органы: Характерных симптомов рака желудка не существует. Выраженные симптомы появляются, когда опухоль...
Влияние предпринимательской среды на эффективное функционирование предприятия: Предпринимательская среда – это совокупность внешних и внутренних факторов, оказывающих влияние на функционирование фирмы...
Дисциплины:
![]() |
![]() |
5.00
из
|
Заказать работу |
|
|
Обратные связи в системах управления автоматизированным
Оборудованием и точность обработки
Система управления (СУ) любого автоматизированного оборудования в том или ином объеме включает элементы информационно-измерительной системы (ИИС), которые в совокупности участвуют в создании обратных связей (ОС) для стабилизации или оптимизации процессов обработки.
Источником выходных параметров СУ может служить непосредственно размер обрабатываемой детали (регулируемый размерный параметр)или какой-либо иной, связанный с ним функциональной зависимостью: положение режущей кромки инструмента, положение исполнительных органов станка (бабок, ходовых винтов и т.д.)
С точки зрения обеспечения качества обработки (размер и форма детали, качество поверхности) эти ОС обладают различной способностью к компенсации технологических погрешностей.
Точность ОС зависит от протяженности звеньев различных цепей станка, в состав которых входит регулируемый размерный параметр, и от погрешности размеров этих звеньев.
![]() |
Рис.1. Схема возможного расположения датчиков положения
1 - Обрабатываемая деталь; 2 – Резец; 3 - Исполнительное устройство;
4 - Двигатель подач; 5 - Датчик информации; I-IV – вид обратной связи
Если выходным параметром системы управления служит размер обрабатываемой детали, то задача компенсации технологических погрешностей решается наиболее полно. Это обеспечивается ОС-I, которая охватывает всю размерную цепь системы СПИД (станок – приспособление – инструмент – деталь). Устраняется влияние тепловых и силовых деформаций системы, износа режущего инструмента, кинематических погрешностей передачи, возмущающих воздействий заготовки. Погрешность определяется лишь погрешностью измерительной системы и смещением зоны контроля - запаздыванием выдачи информации по отношению к моменту ее получения.
|
В остальных видах ОС "степень замкнутости" уменьшается, размерная цепь, охваченная ОС, уменьшается, и увеличивается количество некомпенсированных влияющих факторов (возмущающих воздействий). Все остальные ОС являются ОС по положению.
ОС-II - не компенсируются деформации детали, центров, возмущающие воздействия заготовки.
ОС-III - не компенсируется всё по ОС-II и дополнительно величина износа инструмента, деформация исполнительных устройств.
ОС-IV - является наименее точной ОС, она контролирует скорость вращения двигателя привода подач.
Вместе с тем следует отметить, что в настоящее время практически не получили распространения информационные устройства, использующие информацию о размере детали и ОС-I из-за сложности ее реализации ("затемненность" зоны резания). Размер детали обеспечивается косвенным образом, в основном по положению исполнительных органов (ОС-III), иногда рабочих органов (ОС-II), что естественно приводит к неполной компенсации технологических погрешностей и снижению точности обработки.
В станках с программным управлением чаще всего используют ОС-IV с датчиками положения, контролирующими угловые перемещения вала двигателя привода подачи (коррекции) [6]. В этом случае привод выступает как локальная система управления процессом обработки изделия.
Влияние звеньев цепей обратной связи на качество
Электропривода
В общем случае в электропривод входит (рис.2) электродвигатель (М), питающийся от преобразователя (П) и приводящий в движение механизм металлорежущего станка, который включает в себя кинематическую связь (КС) и исполнительный орган (ИО) [7,8].
|
Эти элементы образуют силовую часть привода. Кроме того, электропривод как система управления замкнутого типа, включает в себя и управляющую часть, состоящую из регулятора (Р), сравнивающего устройства (СУ), реализующего в большинстве случаев отрицательную ОС, и измерительно-преобразовательной части, образующей систему обратной связи электропривода и включающей в себя датчики первичной информации (Д) и различного рода преобразующие устройства (П) (усилители, согласующие устройства, преобразователи, решающие устройства и тому подобное). При этом в замкнутой системе управления электроприводами имеют место два потока информации – сигнал управления, формирующий предписанные значения параметров технологического процесса, и сигнал обратной связи, формирующий информацию о действительном значении этих параметров посредством совокупности датчиков Д1 – Дn, первичная информация с которых является функцией пути (управление по положению), скорости (управление по скорости), тока (управление по нагрузке) и тому подобное. Совокупность этих двух потоков и формирует управляющее воздействие.
Следует также иметь в виду, что работа привода осуществляется при наличии возмущений, воздействующих на все его элементы и являющихся источником как его аддитивной, так и мультипликативной погрешности. При этом даже организация системы управления с регулированием по возмущению лишь теоретически позволяет создать полную инвариантную к возмущениям систему, практически же подобные системы нереализуемы.
![]() |
Рассматривая электропривод, как замкнутую систему управления с результирующей передаточной функцией
W(p) =Wр(p)Wсч(p)/(1+Wр(p)Wсч(p)Wипч(p)),
где W(p) – передаточная функция соответственно, Р – регулятора, СЧ - силовой части, ИПЧ – измерительно-преобразовательной части, и принимая во внимание, что в области реальных частот
½Wр(jw)½Wсч(jw)½Wипч(jw)½>> 1,
можно заключить, что выходной параметр
Xвых(p) = W-1ипч(p)Xвх(p),
зависит только от обратной передаточной функции измерительно-преобразовательной части и сигнала управления.
При этом чувствительность
S(p) = dXвых(p)/dXвх(p) = W-1ипч(p)
зависит также только от обратной передаточной функции измерительно-преобразовательной части.
|
Погрешность отработки выходного параметра, возникающая под действием m возмущающих факторов, действующих на каждое i – ое звено привода
n
Dвых(p) = -Xвх(p)S W-2ипч(p)Dm(p)
m =1
также определяется лишь измерительно-преобразовательной частью.
Мультипликативная погрешность
DS(p) = W-2ипч(p) DW(p)(p)
также определяется только измерительно-преобразоательной частью.
Статический коэффициент привода равен
K = KрKсч/(1+KрKсчKипч),
Поскольку
KрKсчKипч >> 1,
то и статическая точность определяется статической точностью измерительно-преобразовательной части привода
K» 1/Kипч,
Частотная характеристика привода
W(jw) = Wр(jw)Wсч(jw)/(1+Wр(jw)Wсч(jw)Wипч(jw))
С учетом принятых допущений амплитудно-частотная характеристика (АЧХ) привода определяется выражением
W(jw)» 1/Wипч(jw),
Как видно АЧХ привода определяется частотными характеристиками его измерительно-преобразовательной части.
Следует иметь в виду, что все это не означает, что прямой тракт передачи энергии не оказывает влияния на характеристики электропривода в целом, а лишь подчеркивает значение его измерительно-преобразовательной части.
Таким образом, измерительно-преобразовательная часть, обеспечивающая в контуре управления электроприводом металлорежущих станков обратную связь (метрологическую интерструктуру), является в значительной мере оределяющей в обеспечении качества его работы.
Требования к цепям обратной связи электроприводов являются, с учетом их важности, традиционно высокими.
Таким образом, цепи ОС, являясь неотъемлемой частью системы управления электроприводом и играя решающую роль в формировании его передаточной функции в целом, в значительной степени определяют его статические и динамические характеристики.
Заданной точности обработки
Основным критерием при выборе датчика положения является необходимая (заданная) точность обработки изделия (размер). Для обеспечения заданной точности обработки в поле допуска детали (ряда деталей) выбирается соответствующий станок с ЧПУ. По ГОСТ 8-82Е станки по точности (в порядке ее увеличения) разделяют на 6 классов с присвоением соответствующей буквы алфавита.
|
Класс точности | 1 | 2 | 3 | 4 | 5 |
Обозначение по ГОСТ 8-82Е | Н | П | В | А | С |
В зависимости от требований, предъявляемых к точности металлорежущих станков с ЧПУ, различные требования предъявляются и к точностным характеристикам измерительных преобразователей. В табл. (приложение 2) приведены нормы точности для систем измерения линейных и угловых перемещений, полученные на основе известных норм точности различных классов станков и допустимых погрешностей средств контроля [3].
Установлено, что погрешность ДП должна составлять от предельной погрешности станков: не более 45% - для класса С, не более 35% - для классов В и А, не более 30% - для классов Н и П.
Поэтому, учитывая допустимую погрешность обработки заданных деталей, можно определить класс точности измерительных средств как линейного, так и углового перемещения (табл.2,3 – приложение 2) с учетом их систематической погрешности.
Таким образом, если известны допустимые при обработке изделий погрешности, можно определить диапазон допустимых погрешностей измерительной системы с датчиками перемещения и его класс точности. Наиболее высокую точность и наименьшую дискрету имеет 6 класс, а самые низкие показатели - 1 класс. Класс точности выбираемого датчика положения должен соответствовать или быть выше класса точности станка.
Как уже говорилось выше, наибольшее применение в станках с ЧПУ нашли фотоэлектрические импульсные ДП и электромагнитные ДП: ВТ, редуктосины, сельсины и индуктосины (линейные и круговые). Для станков класса точности Н и П применяют оптические круговые ДП (типа ВЕ - 178), ВТ, редуктосины и сельсины; для станков класса В - линейные оптические (типа ВЕ - 164) и индуктосины. Причем предельное значение точности привода подач в полной мере определяется параметрами измерительных преобразователей ОС по пути (положению). Обобщенные показатели точности угловых ДП указаны в табл.4 (приложение 2).
Таким образом, после выбора станка с учетом необходимой величины контролируемого перемещения и точности обрабатываемых деталей по табл.1 (приложение 2) определяем допустимую погрешность измерительных преобразователей (линейных или угловых) и соответствующий класс точности (табл.2,3 – приложение 2). Тип необходимого ДП находим, учитывая рекомендации табл.4 (приложение 2) и более точно определяемся с техническими характеристиками ДП по табл.1-5 (приложение 1) с учетом эксплуатационных и конструктивных требований, определяемых типов привода подач АО.
|
Определившись с типом выбранного по критерию обеспечения заданной точности ДП, необходимо обеспечить заданную разрешающую способность устройства, то есть дискретность информационного сигнала (величину минимального перемещения, информация о котором передается в систему управления).
Все приведенные выше технические характеристики (табл.1-4 – приложение 1) справедливы для электромагнитных ПП датчиков перемещения, выдающих на выходе гармонический сигнал, и только для фотоэлектрических ДП (табл.5 – приложение 1) параметры характеризуют датчик в сборе, то есть его ПП и электронный блок, выдающий на выходе двоичный код.
Выходные сигналы статорных обмоток сельсинов, СКВТ и других электромагнитных ПП преобразуются в цифровой код с помощью вторичных преобразователей электронного блока.
В нашей стране вторичные преобразователи серийно не выпускаются, поэтому требуют разработки в каждом конкретном случае.
В связи с тем, что большинство ПП аналоговые, именно АЦП, преобразующие гармонический сигнал ПП в последовательность импульсов и далее в цифровой код, обеспечивает необходимую дискретность информации, то есть разрешающую способность ДП.
Результаты расчета
Обобщенная желательность | Желательность по каждому из параметров | |||||
Датчик | Значение | Параметр | Д1 | Д2 | Д3 | Д4 |
Д1 Д2 Д3 Д4 | 0,64142 0,60764 0,56750 0,44237 | У1 У2 УЗ У4 У5 У6 | 0,752 0,543 0,618 0,800 0,613 0,563 | 0,547 0,543 0,556 0,800 0,622 0,612 | 0,800 0,624 0,618 0,691 0,370 0,423 | 0,693 0,370 0,370 0,370 0,556 0,383 |
Приложение 1
Таблица 4-1
Величина интервала координатного перемещения, мм | Предел допустимой погрешности, мкм (для класса точности 3, 4, 5, соответственно), при температуре | ||
20±5ºС | 20±1ºС | 20±2ºС | |
До 10 | 2.5 | 5.0 | 9.0 |
Свыше 10 до 32 | 2.5 | 5.0 | 10.0 |
32-125 | 3.0 | 6.0 | 12.0 |
125-200 | 3.5 | 7.0 | 13.0 |
200-320 | 4.0 | 7.0 | 14.0 |
320-500 | 4.0 | 8.0 | 16.0 |
500-800 | 5.0 | 10.0 | 18.0 |
800-1250 | 5.5 | 11.0 | 20.0 |
1250-2000 | 6.0 | 13.0 | 24.0 |
2000-3200 | 7.0 | 15.0 | 29.0 |
При использовании преобразователя на длинах, превышающих 3200 мм, гарантируется погрешность, соответствующая 5-му классу точности по ГОСТ 20965-75.
Таблица 5
Технические характеристики фотоэлектрических датчиков
Тип датчика | Назначе-ние | Число периодов на оборот, дискретность | Погреш-ность | Максимальная скорость перемещения | Максимальная величина перемещения, мм |
ВЕ-106 ВЕ-51В | Угловой Угловой | 1000-1924 1000-5000 | 5 мин 1 мин | 3000 об/мин 3000-6000 об/мин | |
ВЕ-178 | Угловой | 100-2500 | 3 мин | 300-3000 об/мин | |
ПДФ-3М | Угловой | 200-2000 | 30 с | 3000 об/мин | |
ПДФ-10 | Угловой | 310-2500 | 10 с | 3000 об/мин | |
ИЗГ-452 | Угловой | 16200, 18000 | 5 с | 30 об/мин | |
Mini ROD | Угловой | 100-3500 | до 2 с | 10000 об/мин | |
ROD | Угловой | 360-36000 | 6000-12000 об/мин | ||
ERO715 | Угловой | 18000-36000 | |||
ВЕ-162 | Линейный | 0,02 мм | 5-6 мкм | 15 м/мин | 250-450 |
ВЕ-163 | Линейный | 0,002-0,004 мм | 3,5-5,5 мкм | 10-15 м/мин | 220-1020 |
LS | Линейный | шаг 20-40 мкм | 5-10 мкм | 48 м/мин | 170-3040 |
LIDA | Линейный | 1-10 мкм | 1500-20000 | ||
Mini LIDA | Линейный | 0,1-10 мкм | 50-20000 | ||
ULS-200 | Линейный | 0,5 мкм | 150-500 |
Приложение 2
Таблица 1
Нормы точности для систем контроля линейных и угловых перемещений
Величина контролируемого перемещения, мм | Класс точности станка | ||||
Н | П | В | А | С | |
Допустимое отклонение устройств путевого контроля (для линейных преобразователей), мкм | |||||
До 125 Свыше 125 до 200 Свыше 200 до 320 Свыше 320 до 500 Свыше 500 до 800 Свыше 800 до 1250 Свыше 1250 до 2000 Свыше 2000 до 3000 | 8.0 10.0 12.0 15.0 19.0 25.0 30.0 37.0 | 4.0 5.0 6.0 8.0 10.0 12.0 15.0 19.0 | 2.0 3.0 3.5 4.0 6.0 7.0 9.0 11.0 | 1.0 1.5 2.0 2.0 3.0 3.5 4.0 6.0 | 1.0 1.0 1.0 1.5 2.0 2.5 3.0 4.0 |
Диаметр круговой шкалы измерительной системы, мм | Допустимое отклонение (для угловых преобразователей в пределах 360° угла поворота), угл. с. | ||||
До 125 Свыше 125 до 200 Свыше 200 до 320 Свыше 320 до 500 Свыше 500 до 800 Свыше 800 до 1250 Свыше 1250 до 2000 | 60.0 50.0 35.0 30.0 25.0 20.0 15.0 | 30.0 25.0 20.0 15.0 12.0 10.0 7.0 | 15.0 12.0 10.0 8.0 6.0 5.0 3.0 | 7.0 6.0 5.0 4.0 3.0 2.0 2.0 | 3.0 3.0 2.0 2.0 1.0 1.0 1.0 |
Таблица 2
Обратные связи в системах управления автоматизированным
|
|
Особенности сооружения опор в сложных условиях: Сооружение ВЛ в районах с суровыми климатическими и тяжелыми геологическими условиями...
Двойное оплодотворение у цветковых растений: Оплодотворение - это процесс слияния мужской и женской половых клеток с образованием зиготы...
Архитектура электронного правительства: Единая архитектура – это методологический подход при создании системы управления государства, который строится...
Состав сооружений: решетки и песколовки: Решетки – это первое устройство в схеме очистных сооружений. Они представляют...
© cyberpedia.su 2017-2024 - Не является автором материалов. Исключительное право сохранено за автором текста.
Если вы не хотите, чтобы данный материал был у нас на сайте, перейдите по ссылке: Нарушение авторских прав. Мы поможем в написании вашей работы!