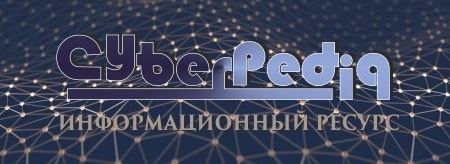
История развития хранилищ для нефти: Первые склады нефти появились в XVII веке. Они представляли собой землянные ямы-амбара глубиной 4…5 м...
Индивидуальные очистные сооружения: К классу индивидуальных очистных сооружений относят сооружения, пропускная способность которых...
Топ:
История развития методов оптимизации: теорема Куна-Таккера, метод Лагранжа, роль выпуклости в оптимизации...
Процедура выполнения команд. Рабочий цикл процессора: Функционирование процессора в основном состоит из повторяющихся рабочих циклов, каждый из которых соответствует...
Определение места расположения распределительного центра: Фирма реализует продукцию на рынках сбыта и имеет постоянных поставщиков в разных регионах. Увеличение объема продаж...
Интересное:
Распространение рака на другие отдаленные от желудка органы: Характерных симптомов рака желудка не существует. Выраженные симптомы появляются, когда опухоль...
Подходы к решению темы фильма: Существует три основных типа исторического фильма, имеющих между собой много общего...
Принципы управления денежными потоками: одним из методов контроля за состоянием денежной наличности является...
Дисциплины:
![]() |
![]() |
5.00
из
|
Заказать работу |
|
|
Подготовка кромок под сборку и сварку
Перед сборкой трубы необходимо рассортировать на группы с плюсовым и минусовым отклонением внутреннего диаметра от номинального значения.
Очистить внутреннюю полость труб и деталей от грунта, грязи, снега и других загрязнений.
Осмотреть поверхность и кромки труб, проверить геометрические размеры кромок, выправить плавные вмятины на концах труб глубиной до 3,5% наружного диаметра трубы. При температуре воздуха ниже -50С правка концов труб без их подогрева не рекомендуется.
Концы труб, имеющие трещины, надрывы, забоины, задиры фасок глубиной более 5 мм следует обрезать.
Типы, конструктивные элементы и размеры сварных соединений стальных газопроводов (рис.1) должны соответствовать ГОСТ 16037.
S=S1, мм | b, мм | c, мм | e, мм | g, мм | ||||
Номин. | Пред. откл. | Номин. | Пред. откл. | Номин. | Пред. откл. | Номин. | Пред. откл. | |
3 | 1,0 | +0,5 | 0,5 | +0,5 | 7 | +2 | 1,5 | +1,5 -1,0 |
4 | 8 | |||||||
5 | 1,5 | 1,0 | ±0,5 | 9 | ||||
6 | 11 | |||||||
8 | 2,0 | +1,0 | 13 | +3 |
Рис.1 Конструктивные элементы сварного шва по ГОСТ 16037
Зачистить до чистого металла кромки и прилегающие к ним внутреннюю и наружную поверхности трубы на ширину не менее 10 мм.
В случае использования труб с необработанными в заводских условиях торцами (после резки) подготовка кромок под стандартную разделку должна выполняться механической обработкой или газовой резкой с последующей зачисткой шлифмашинкой.
Сборка стыков
Осуществить сборку труб на инвентарных лежках с использованием наружного центратора.
Смещение кромок должно быть равномерно распределено по периметру стыка. Допускаемое смещение кромок свариваемых труб не должно превышать величины: 0,15S+0,5 мм, где S – наименьшая из толщин стенок свариваемых труб.
|
Сборку под сварку труб с односторонним продольным или спиральным сварным швом следует производить со смещением швов в местах стыковки труб не менее, чем на:
15 мм - для труб диаметром до 50 мм;
50 мм - для труб диаметром от 50 до 100 мм;
100 мм – для труб диаметром свыше 100 мм.
При сборке стыков труб должны быть обеспечены правильное фиксированное взаимное расположение стыкуемых труб и деталей, а также свободный доступ к выполнению сварочных работ в последовательности, предусмотренной технологическим процессом.
Сборка выполняется на прихватках. Их количество должно удовлетворять следующим условиям:
· для труб Ø до 80 мм – 2 шт.;
· для труб Ø свыше 80 мм до 150 мм – 3 шт.;
· для труб Ø свыше 150 мм до 300 мм– 4 шт.;
· для труб Ø свыше 300 мм – через каждые 250 мм.;
Высота прихватки должна составлять 1/3 толщины стенки трубы, но не менее 2 мм; длина прихватки – 20-30 мм при диаметре стыкуемых труб до 50 мм; 50-60 мм – при диаметре стыкуемых труб более 50 мм.
Режим выполнения прихватки – как для корневого слоя шва. Прихватки на стальном газопроводе должны выполняться материалами, предназначенными для сварки корневого шва.
Прямолинейность (соосность труб) в месте стыка необходимо проверять металлической линейкой длиной 400 мм, прикладывая ее в трех-четырех местах по окружности трубы. Максимально допустимое отклонение от соосности, измеряемое щупом, не должно превышать 0,5 мм на расстоянии 200 мм от шва (см. рисунок 3).
Рис. 3 Схема замера отклонений оси трубы
Сварка
Ручную дуговую сварку неповоротных и поворотных стыков труб при толщине стенок до 6 мм следует выполнять не менее чем в два слоя, при толщине стенок более 6 мм – не менее чем в три слоя.
Режимы сварки | |||||
Сварочные слои | Тип электрода | Диаметр, мм | Поляр- ность | Сварочный ток,А | |
1 | Э50А | 2,5(2,6) | обратная | 70-90 | |
2 | Э50А | 3,0(3,2) | обратная | 90 – 120 | |
3 | Э50А | 3,0/3,2 | обратная | 90 - 120 | |
Величина сварочного тока в вертикальном и потолочном положениях должна быть снижена на 10 – 15%
|
Запрещается осуществлять сварку с применением любых присадок, непосредственно подаваемых сварочную дугу или предварительно заложенных в разделку.
Запрещается зажигать дугу с поверхности трубы. Дуга должна возбуждаться и гаситься на поверхности разделки кромок или же на поверхности металла уже выполненного шва.
Удалять наружный центратор разрешается после завершения сварки 50% периметра корневого слоя шва. При этом отдельные участки шва должны быть равномерно расположены по периметру стыка. Перед продолжением сварки корневого слоя шва после снятия центратора все сваренные участки должны быть зачищены, а концы швов прорезаны шлифмашинкой.
Для предупреждения образования дефектов между слоями сварного шва перед выполнением каждого последующего слоя поверхность предыдущего слоя должна быть очищена от шлака и брызг.
Начало и конец кольцевого сварного шва должны отстоять от заводского шва трубы (детали, арматуры) не ближе:
· 50 мм – для диаметров менее 400 мм;
· 75 мм – для диаметров менее 1000 мм;
· 100 мм - для диаметров более 1000 мм.
Места начала и окончания сварки каждого слоя («замки» шва) располагают для труб диаметром 400 мм и более не ближе 100 мм от «замков» предыдущего слоя шва, а для труб диаметром менее 400 мм – не ближе 50 мм.
До полного завершения корневого слоя шва не разрешается перемещать свариваемый стык.
На сварочных стыках подземных газопроводов должна быть нанесена маркировка (клеймо сварщика) выполнившего сварку. Способ нанесения маркировки должен обеспечить ее сохранность в течение эксплуатации газопровода. При заварке стыка несколькими сварщиками, клейма проставляются на границах свариваемых участков.
Сварочные работы на открытом воздухе во время дождя, снегопада, тумана и при ветре скоростью свыше 10 м/с необходимо выполнять при условии обеспечения защиты места сварки от влаги и ветра.
Требования к контролю качества сварных соединений
В процессе сварки осуществляют контроль:
· Предварительный
1. проверка квалификации сварщиков, дефектоскопистов;
2. проверка состояния сборочно-сварочных соединений, сварочного оборудования и аппаратуры, а также оборудования для контроля и аппаратуры для контроля качества сварных соединений;
|
3. проверка качества сварочных материалов, а также материалов для дефектоскопии;
4. проверка средств измерения, включая измерительные приборы.
· Пооперационный
1. проверка качества подготовки кромок под сварку и качества сборки под сварку;
2. соблюдение технологии сварки: соответствие сварочных материалов, режим подогрева и сварки, порядок наложения швов, качество послойной зачистки швов от шлака.
· Контроль качества готовых сварных соединений
Визуально-измерительный, радиографический (РГК), ультразвуковой контроль (УЗК) качества сварных соединений, а также проверка их механических свойств (МИ) производится в соответствии с требованиями государственных стандартов и нормативно-технических документов: визуальный и измерительный методы по РД 03-606-03 «Инструкция по визуальному и измерительному контролю»; РГК по ГОСТ 7512 «Контроль неразрушающий. Соединения сварные. Радиографический метод» и ГОСТ 23055 «Контроль неразрушающий. Сварка металлов плавлением. Классификация сварных соединений по результатам радиографического контроля»; УЗК по ГОСТ 14782 «Контроль неразрушающий. Соединения сварные. Методы ультразвуковые»; МИ по ГОСТ 6996 «Сварные соединения. Методы определения механических свойств».
Дефектация сварных соединений в соответствии с требованиями СНиП 42-01-2002 «Газораспределительные системы», СП 42-102-2004 «Проектирование и строительство газопроводов из металлических труб».
Оборудование, применяемое при контроле качества строительства, должно пройти поверку в сроки, установленные нормативной документацией. Контрольно-измерительное оборудование должно проходить метрологическую поверку в установленном порядке.
Сварные соединения подлежат визуальному и измерительному контролю с целью выявления наружных дефектов всех видов, а также отклонений по геометрическим параметрам, установленным ГОСТ 16037- 80, и взаимному расположению элементов.
Недопустимыми дефектами, выявленными при визуальном контроле сварных соединений, являются: трещины всех видов и направлений, непровары (несплавления) между основным металлом и швом, а также между валиками шва, наплывы (натеки) и брызги металла, незаваренные кратеры, свищи, прожоги, скопления включений.
|
Подрез размером 0,2 мм и менее измерению не подлежит, определяется визуально. Для газопроводов допускаются подрезы глубиной не более 5% толщины стенки трубы, но не более 0,5 мм и длиной не более 1/3 периметра стыка, но не более 150 мм.
Выявленные при визуальном и измерительном контроле дефекты, которые могут быть исправлены (удалены) без последующей заварки выборок, должны быть исправлены до проведения контроля другими методами.
Неразрушающий контроль сварных соединений (РГК, УЗК) проводится при положительных результатах визуального и измерительного контроля.
Выбор метода контроля (УЗК или РК) должен производится исходя из условий обеспечения выявления дефектов с учетом физических свойств материала.
УЗК сварных стыков стальных газопроводов применяется при условии выборочной проверки не менее 10% стыков РГК. При неудовлетворительных результатах контроля методом РГК хотя бы на одном стыке объем контроля следует увеличить до 50% от общего числа стыков. В случае повторного выявления дефектных стыков все стыки, сваренные сварщиком на объекте в течение календарного месяца и проверенные методом УЗК, должны быть проверены методом РГК.
При неудовлетворительных результатах контроля ультразвуковым методом стыковых соединений стальных трубопроводов необходимо провести проверку удвоенного числа стыков на участках, которые к моменту обнаружения брака не были приняты по результатам этого вида контроля. Если при повторной проверке хотя бы один из проверяемых стыков окажется неудовлетворительного качества, то все стыки, сваренные данным сварщиком на объекте, должны быть проверены ультразвуковым методом контроля.
По результатам проверки методом РГК стыки следует браковать при наличии следующих дефектов:
· трещин, прожогов, незаваренных кратеров;
· непровара по разделке шва;
· непровара в корне шва и между валиками глубиной более 10% толщины стенки трубы;
· непровара в корне шва и между валиками свыше 25 мм на каждые 300 мм длины сварного соединения или свыше 10% периметра при длине сварного соединения менее 300 мм;
· если размеры дефектов стыков (пор, шлака и др. включений) превышают установленные для класса 6 по ГОСТ 23055.
По результатам УЗК стыки следует браковать при наличии дефектов, площадь которых превышает площадь отверстия в стандартных образцах предприятия, а также при наличии дефектов протяженностью более 25 мм на 300 мм длины сварного соединения или на 10% периметра при длине сварного соединения менее 300 мм.
При неудовлетворительных результатах контроля качества физическими методами должна производиться проверка удвоенного числа стыков на участках газопровода, не принятых в эксплуатацию.
|
Если при повторной проверке будут обнаружены недопустимые дефекты, то все однотипные сварные соединения, сваренные сварщиком на участках газопровода не принятых в эксплуатацию, должны быть проверены физическим методом контроля.
Для стыковых сварных соединений подземных стальных газопроводов в зависимости от давления подлежат контролю физическим методом в следующих объемах (но не менее одного стыка)от общего числа стыков, сваренных каждым сварщиком на объекте:
· 10% при давлении до 0,005МПа включительно;
· 50% при давлении свыше 0,005 до 0,3 МПа включительно;
· 100% при давлении свыше 0,3 МПа.
Стыковые соединения подземных стальных газопроводов диаметром менее 50 мм контролю физическим методом не подлежат.
Стыковые соединения подземных стальных газопроводов давлением свыше 0,005 до 1,2 МПа, прокладываемых вне поселений за пределами границ их перспективной застройки, подлежат контролю физическим методом в объеме 20% (но не менее одного стыка) от общего числа стыков, сваренных каждым сварщиком на объекте.
Стыковые соединения надземных стальных газопроводов всех давлений диаметром менее 50 мм контролю физическим методом не подлежат.
Стыковые сварные соединения газопроводов диаметром свыше 50 мм в ГРП и ГРУ подлежат контролю физическим методом в объеме 100%.
Стыковые соединения надземных газопроводов давлением свыше 0,005 до 1,2 МПа подлежат контролю физическим методом в объеме 5% (но не менее одного стыка) от общего числа стыков, сваренных каждым сварщиком.
Контроль радиографических снимков сварных стальных соединений, сваренных каждым сварщиком, следует осуществлять на аппаратно-программном комплексе автоматизированной расшифровки радиографических снимков в объеме 20%.
Результаты проверки сварных стыков газопровода физическими методами и механическими испытаниями оформляются протоколом, который подписывают дефектоскопист и начальник лаборатории.
Заключения, радиографические снимки, магнитные ленты или диаграммы хранятся в строительно-монтажной организации (лаборатории) после сдачи газопровода в эксплуатацию в течение года.
Нормы контроля не распространяются на угловые соединения на газопроводах условным диаметром до 500 мм, стыки приварки фланцев и плоских заглушек.
Механические испытания проводятся в соответствии с государственными стандартами при проверке механических характеристик и качества сварных соединений при сварке стыков в процессе квалификационных испытаний сварщиков (допускных) и проверке технологических параметров при аттестации технологии сварки, а также при сварке стыков газопроводов не подлежащих контролю физическими методами.
Проверка механических свойств должна производиться на образцах, выполненных из контрольных (допускных) сварных соединений (КСС) или из производственных сварных соединений, вырезаемых из изделия. Условия сварки КСС должны быть идентичны контролируемым производственным соединениям. Производственные соединения отбираются в количестве 0,5 % общего числа стыковых соединений, сваренных каждым сварщиком, но не менее 2 стыков диаметром 50 мм и менее и 1 стыка диаметром свыше 50 мм, сваренных им в течение календарного месяца.
Стыки стальных газопроводов испытывают на статическое растяжение и на изгиб или сплющивание.
Механические свойства стыков стальных труб с условным диаметром свыше 50 мм определяют испытаниями на растяжение и изгиб образцов (вырезанных равномерно по периметру каждого отобранного стыка) со снятым усилением.
Результаты механических испытаний стыка считаются неудовлетворительными, если:
· Среднее арифметическое предела прочности трех образцов при испытании на растяжение менее нормативного предела прочности основного металла трубы;
· Среднее арифметическое угла изгиба трех образцов при испытании на изгиб менее 1200 – для дуговой сварки;
· Результат испытаний хотя бы одного из трех образцов по одному из видов испытаний на 10% ниже нормативного значения прочности или угла изгиба.
Механические свойства сварных стыков стальных труб условным диаметром до 50 мм включительно должны определяться испытаниями целых стыков на растяжение и сплющивание. Для труб этих диаметров половину отобранных для контроля стыков (с неснятым усилением) следует испытывать на растяжение и половину (со снятым усилением) – на сплющивание.
Результаты механических испытаний сварного стыка считаются неудовлетворительными, если:
· Предел прочности при испытании стыка на растяжение менее нормативного предела прочности основного металла трубы;
· Просвет между сжимающимися поверхностями пресса при появлении первой трещины в сварном шве при испытании при испытании на сплющивание более 5S, где S – номинальная толщина стенки трубы.
При неудовлетворительных испытаниях хотя бы одного стыка проводят повторные испытания удвоенного количества стыков. Проверка должна производиться по виду испытаний, давшему неудовлетворительные результаты.
В случае получения при повторной проверке неудовлетворительных результатов испытаний хотя бы на одном стыке все стыки, сваренные данным сварщиком в течение календарного месяца на данном объекте газовой сваркой, должны быть удалены, а стыки, сваренные дуговой сваркой, проверены радиографическим методом контроля.
Техника безопасности
Требования безопасности при ручной дуговой сварке должны соответствовать ГОСТ 12.3.003-86 «Система стандартов безопасности труда. Работы электросварочные. Требования безопасности», ПОТ РМ-020-2001 «Межотраслевые правила по охране труда при электро- и газосварочных работах» и иных действующих нормативных документов в области безопасности и охраны труда.
Приступить к работе по электросварке можно при условии, если оборудование, индивидуальные средства защиты и предохранительные приспособления соответствуют технологии и санитарно-гигиеническим условиям труда.
Ручную дуговую сварку следует производить по возможности на стационарных постах, оборудованных устройствами местной вытяжной вентиляции. Объем удаляемого воздуха для стандартного сварочного стола от одного поста следует принимать не менее 1500м3/ч, причем скорость всасывания в точке сварки должна быть не менее 0,2 м/с. При невозможности производства сварочных работ на стационарных постах для локального удаления пыли и газообразных компонентов аэрозоля от сварочной дуги следует применять местные отсосы.
Рабочие места, расположенные выше 1,3 м от уровня земли или сплошного перекрытия, должны быть оборудованы ограждениями высотой не менее 1,1м, состоящими из поручня, одного промежуточного элемента и бортовой доски шириной не менее 0,15 м.
Кабели (провода) электросварочных машин должны располагаться от трубопроводов кислорода на расстоянии не менее 0,5 м, а от трубопроводов ацетилена и других горючих газов - не менее 1 м.
Отдельные элементы сварочной цепи, а также отрезки сварочных кабелей при наращивании длины должны быть соединены разъемными соединительными муфтами. Запрещается применять соединения сварочной цепи скрутками с оголенным кабелем. Токоведущие кабели сварочной цепи должны быть по всей длине изолированы и защищены от механических повреждений.
Для дуговой сварки необходимо применять изолированные гибкие кабели, рассчитанные на надежную работу при максимальных электрических нагрузках с учетом продолжительности цикла сварки. Подключение кабелей к сварочному оборудованию должно осуществляться при помощи спрессованных или припаянных кабельных наконечников
Электрододержатели, применяемые при ручной дуговой электросварке металлическими электродами, должны соответствовать требованиям действующих стандартов.
Корпус любой электросварочной установки необходимо заземлять. Машины, в которых осуществление защитного заземления представляет трудности, должны быть оснащены устройствами защитного отключения, обеспечивающего отключение всех фаз сети при появлении в сварочной цепи напряжения сети. Для присоединения заземляющего провода на электросварочном оборудовании должен быть предусмотрен болт, расположенный в доступном месте, с надписью «Земля» (при условном обозначении «Земля»). Последовательное включение в заземляющий проводник нескольких аппаратов запрещается.
Присоединение и отсоединение от сети электросварочных установок, а также наблюдение за их исправным состоянием в процессе эксплуатации должен выполнять электротехнический персонал данного предприятия, имеющий квалификационную группу по электробезопасности не ниже III. Электросварщикам, прошедшим специальное обучение, может присваиваться в установленном порядке квалификационная группа по электробезопасности III и выше с правом присоединения и отсоединения электросварочных установок.
По окончании газо- и электросварочных работ, наплавки, резки работник не должен покидать рабочее место, не убедившись в отсутствии очага, способного вызвать пожар на месте проведения работы и в смежных помещениях. Все работающие должны быть обучены правилам ликвидации первичных очагов пожара и правильному применению первичных средств пожаротушения.
Спецодежда должна быть безвредной, удобной, не стеснять движения работающего, не вызывать неприятных ощущений, защищать от искр и брызг расплавленного металла, свариваемого изделия, влаги, производственных загрязнений, механических повреждений, отвечать санитарно-гигиеническим требованиям и условиям труда. Выбор спецодежды в зависимости от методов сварки и условий труда должен производиться в соответствии с рекомендациями ГОСТ 12.4.044, ГОСТ 12.4.045 и ГОСТ 12.4.010. Для защиты рук при сварке, наплавке, ПН и резке работники должны обеспечиваться рукавицами, рукавицами с крагами или перчатками, изготовленными из огнестойкого материала с низкой электропроводностью. Для защиты ног от ожогов брызгами расплавленного металла, механических травм, переохлаждения при работе на открытом воздухе зимой, перегревания при сварке изделий с подогревом, а также от поражения электрическим током, особенно при работе в закрытых сосудах, отсеках, работники должны обеспечиваться специальной обувью. Применять спец-обувь с открытой шнуровкой и металлическими гвоздями не допускается.
Посторонним лицам запрещается находиться в местах, где производятся сварка, наплавка, резка.
Необходимо предусмотреть ограждения, защищающие сварщиков, работающих рядом или ниже ярусом, от излучений, искр и брызг расплавленного металла, случайного падения огарков электродов и др.
При производстве работ по сварке, наплавке и резке металлов на открытом воздухе над установками и сварочными постами должны быть сооружены укрытия (навесы) от непогоды. Сварочное оборудование размещается в металлических контейнерах. При отсутствии навесов работы по сварке, наплавке и резке во время дождя или снегопада должны быть прекращены.
Работы по резке металла с применением пропан-бутана или природного газа, а также с применением открытого огня от других источников допускаются на расстоянии (по горизонтали) не менее:
от групп баллонов (более двух) -10м; от отдельных баллонов с кислородом и горючими газами -5м; от газопроводов горючих газов, а также газоразборных постов, размещенных в металлических шкафах: при ручных работах –З м; при механизированных работах -1,5м.
К работам по контролю качества сварных соединений допускаются лица не моложе 18 лет, имеющие специальную подготовку, и действующее квалификационное удостоверение, прошедшие медицинский осмотр и не имеющие медицинских противопоказаний.
Требования безопасности при производстве работ по рентгеновской дефектоскопии сварных соединений должны соответствовать санитарным правилам СП 2.6.1.1283-03 "Обеспечение радиационной безопасности при рентгеновской дефектоскопии", санитарным правилам СП 2.6.1.758-99 "Ионизирующее излучение, радиационная безопасность. Нормы радиационной безопасности (НРБ-99)", с анитарным правилам СП 2.6.1.799-99 "Основные санитарные правила обеспечения радиационной безопасности (ОСПОРБ-99)"
На открытых площадках и в полевых условиях радиационно-опасная зона должна быть ограждена и замаркирована предупреждающими плакатами (надписями), отчетливо видимыми с расстояния не менее 3-х метров.
Во время проведения работ по рентгеновской дефектоскопии оператору запрещается оставлять без присмотра пульт управления аппарата.
Приложение 2
Варианты заданий на разработку технологий
Задание №1 Котельное оборудование (КО)
Разработать инструкцию и технологические карты на выполнение сварочных работ при монтаже и ремонте трубных систем котлов и трубопроводов.
Исходные данные к заданию:
Вариант 1
Способ сварки - РД(111)
Материал трубы – Сталь Ст2, Ст3
Диапазон диаметров – 57 - 108 мм
Диапазон толщин стенки – 3 – 5 мм
Тип шва - стыковой (СШ)
Вариант 2
Способ сварки - РД(111)
Материал трубы – Сталь Ст2, Ст3
Диапазон диаметров –108 - 219 мм
Диапазон толщин стенки –6 - 8 мм
Тип шва - стыковой (СШ)
Вариант 3
Способ сварки - РД(111)
Материал трубы – Сталь 10; 20
Диапазон диаметров – 108 - 219 мм
Диапазон толщин стенки – 3 – 5 мм
Тип шва - стыковой (СШ)
Вариант 4
Способ сварки - РД(111)
Материал трубы – Сталь 09Г2С
Диапазон диаметров –219 - 372 мм
Диапазон толщин стенки –8 - 12 мм
Тип шва - стыковой (СШ)
Вариант 5
Способ сварки - РД(111)
Материал трубы – Сталь 09Х1МФ
Диапазон диаметров – 57 - 108 мм
Диапазон толщин стенки – 3 – 5 мм
Тип шва - стыковой (СШ)
Вариант 6
Способ сварки - РАД (131)
Материал трубы – Сталь 13Х5М
Диапазон диаметров – 57 - 108 мм
Диапазон толщин стенки – 3 – 5 мм
Тип шва - стыковой (СШ)
Вариант 7
Способ сварки - РАД (131)
Материал трубы – Сталь 09Х1МФ
Диапазон диаметров –108 - 159 мм
Диапазон толщин стенки – 5-8 мм
Тип шва - стыковой (СШ)
Вариант 8
Способ сварки - Г (311)
Материал трубы – Сталь Ст2, Ст3
Диапазон диаметров – 57 - 108 мм
Диапазон толщин стенки – 3 – 5 мм
Тип шва - стыковой (СШ)
Вариант 9
Способ сварки - РД(111)
Материал трубы – Сталь 16Г2АФ
Диапазон диаметров – 372 - 530 мм
Диапазон толщин стенки – 8 - 12 мм
Тип шва - стыковой (СШ)
Вариант 10
Способ сварки - МП (111)
Материал трубы - Сталь 09Г2С
Диапазон диаметров 372 - 530 мм
Диапазон толщин стенки 10 -14 мм
Тип шва - стыковой (СШ)
Задание № 2 Газовое оборудование (ГО)
Разработать инструкцию и технологические карты на выполнение сварочных работ при строительстве трубопроводов систем газораспределения.
Вариант 1
Способ сварки - РД(111)
Материал трубы – Сталь Ст2, Ст3
Диапазон диаметров – 57 - 108 мм
Диапазон толщин стенки – 3 – 5 мм
Тип шва - стыковой (СШ)
Вариант 2
Способ сварки - РД(111)
Материал трубы – Сталь Ст2, Ст3
Диапазон диаметров –108 - 219 мм
Диапазон толщин стенки –6 -8 мм
Тип шва - стыковой (СШ)
Вариант 3
Способ сварки - РД(111)
Материал трубы – Сталь 10; 20
Диапазон диаметров – 108 - 219 мм
Диапазон толщин стенки – 3 – 5 мм
Тип шва - стыковой (СШ)
Вариант 4
Способ сварки - РД(111)
Материал трубы – Сталь 09Г2С
Диапазон диаметров –219 - 372 мм
Диапазон толщин стенки –8 - 12 мм
Тип шва - стыковой (СШ)
Вариант 5
Способ сварки НИ
Материал трубы Полиэтилен ПЭ 80, ПЭ100
Диапазон диаметров 63-225 мм
Диапазон толщин стенки 5,8 – 20,5 мм
Тип шва – стыковой (СБ)
Вариант 6
Способ сварки – ЗН
Материал трубы полиэтилен ПЭ80, ПЭ100
Диапазон диаметров 63-225 мм
Диапазон толщин стенки 5,8-20,5 мм
Тип шва - нахлесточный
Вариант 7
Способ сварки - Г(311)
Материал трубы – Сталь Ст-0; Ст-2
Диапазон диаметров – 57 - 108 мм
Диапазон толщин стенки – 3 – 5 мм
Тип шва - стыковой (СШ)
Вариант 8
Способ сварки - Г (311)
Материал трубы – Сталь 10; 20
Диапазон диаметров –25 - 57 мм
Диапазон толщин стенки – 2-3,5 мм
Тип шва - стыковой (СШ)
Вариант 9
Способ сварки - Г (311)
Материал трубы – Сталь Ст3пс
Диапазон диаметров –108 - 159 мм
Диапазон толщин стенки – 4-6 мм
Тип шва - стыковой (СШ)
Вариант 10
Способ сварки - Г (311)
Материал трубы – Сталь Ст2, Ст3
Диапазон диаметров – 57 - 108 мм
Диапазон толщин стенки – 3 – 5 мм
Тип шва - стыковой (СШ)
Задание №3 Нефтегазодобывающее оборудование (НГДО)
Разработать инструкцию и технологические карты на выполнение сварочных работ при строительстве магистральных трубопроводов транспортирующих нефть, нефтепродукты газ и газовый конденсат.
Вариант 1
Способ сварки - РД(111)
Материал трубы – Сталь 20
Диапазон диаметров –108-219 мм
Диапазон толщин стенки –6-8 мм
Тип шва - стыковой (СШ)
Вариант 2
Способ сварки - РД(111)
Материал трубы – Сталь 20
Диапазон диаметров –219-530 мм
Диапазон толщин стенки –8-12 мм
Тип шва - стыковой (СШ)
Вариант 3
Способ сварки - РД(111)
Материал трубы – Сталь 10; 20
Диапазон диаметров – 530 - 920 мм
Диапазон толщин стенки – 12-16 мм
Тип шва - стыковой (СШ)
Вариант 4
Способ сварки - РД(111)
Материал трубы – Сталь 09Г2С
Диапазон диаметров – 372 -920 мм
Диапазон толщин стенки –16-20 мм
Тип шва - стыковой (СШ)
Вариант 5
Способ сварки - РД(111)
Материал трубы – 13ГС-У
Диапазон диаметров – 800 -1020 мм
Диапазон толщин стенки – 16-24 мм
Тип шва - стыковой (СШ)
Вариант 6
Способ сварки - РД (111)
Материал трубы – Сталь 16Г2АФ
Диапазон диаметров 1020-1420 мм
Диапазон толщин стенки – 24-32 мм
Тип шва - стыковой (СШ)
Вариант 7
Способ сварки - МП (135)
Материал трубы – Сталь 09Г2С
Диапазон диаметров –1020-1220 мм
Диапазон толщин стенки – 16-24 мм
Тип шва - стыковой (СШ)
Вариант 8
Способ сварки - МП (135)
Материал трубы – Сталь 20
Диапазон диаметров – 372-530 мм
Диапазон толщин стенки – 8-12 мм
Тип шва - стыковой (СШ)
Вариант 9
Способ сварки - РД(111)
Материал трубы – Сталь 16Г2АФ
Диапазон диаметров – 372 - 530 мм
Диапазон толщин стенки – 8 - 12 мм
Тип шва - стыковой (СШ)
Вариант 10
Способ сварки - МП (111)
Материал трубы - Сталь 09Г2С
Диапазон диаметров 219- 372 мм
Диапазон толщин стенки 10 -14 мм
Тип шва - стыковой (СШ)
Задание №4 Оборудование химического и нефтеперерабатывающего производства (ОХНВП)
Разработать инструкцию и технологические карты на выполнение сварочных работ при монтаже трубопроводов на объектах химического и нефтеперерабатывающего производства
Вариант 1
Способ сварки - РД(111)
Материал трубы – Сталь Ст2, Ст3
Диапазон диаметров – 57 - 108 мм
Диапазон толщин стенки – 3 – 5 мм
Тип шва - стыковой (СШ)
Вариант 2
Способ сварки - РД(111)
Материал трубы – Сталь Ст2, Ст3
Диапазон диаметров –108 - 219 мм
Диапазон толщин стенки –6 - 8 мм
Тип шва - стыковой (СШ)
Вариант 3
Способ сварки - РД(111)
Материал трубы – Сталь 10; 20
Диапазон диаметров – 108 - 219 мм
Диапазон толщин стенки – 3 – 5 мм
Тип шва - стыковой (СШ)
Вариант 4
Способ сварки - РД(111)
Материал трубы – Сталь 09Г2С
Диапазон диаметров –219 - 372 мм
Диапазон толщин стенки –8 - 12 мм
Тип шва - стыковой (СШ)
Вариант 5
Способ сварки - РД(111)
Материал трубы – Сталь 09Х1МФ
Диапазон диаметров – 57 - 108 мм
Диапазон толщин стенки – 3 – 5 мм
Тип шва - стыковой (СШ)
Вариант 6
Способ сварки - РАД (131)
Материал трубы – Сталь 13Х5М
Диапазон диаметров – 57 - 108 мм
Диапазон толщин стенки – 3 – 5 мм
Тип шва - стыковой (СШ)
Вариант 7
Способ сварки - РАД (131)
Материал трубы – Сталь 09Х1МФ
Диапазон диаметров –108 - 159 мм
Диапазон толщин стенки – 5-8 мм
Тип шва - стыковой (СШ)
Вариант 8
Способ сварки - Г (311)
Материал трубы – Сталь Ст2, Ст3
Диапазон диаметров – 57 - 108 мм
Диапазон толщин стенки – 3 – 5 мм
Тип шва - стыковой (СШ)
Вариант 9
Способ сварки - РД(111)
Материал трубы – Сталь 16Г2АФ
Диапазон диаметров – 372 - 530 мм
Диапазон толщин стенки – 8 - 12 мм
Тип шва - стыковой (СШ)
Вариант 10
Способ сварки - МП (111)
Материал трубы - Сталь 09Г2С
Диапазон диаметров 372 - 530 мм
Диапазон толщин стенки 10 -14 мм
Тип шва - стыковой (СШ)
|
|
Типы сооружений для обработки осадков: Септиками называются сооружения, в которых одновременно происходят осветление сточной жидкости...
Механическое удерживание земляных масс: Механическое удерживание земляных масс на склоне обеспечивают контрфорсными сооружениями различных конструкций...
Адаптации растений и животных к жизни в горах: Большое значение для жизни организмов в горах имеют степень расчленения, крутизна и экспозиционные различия склонов...
Эмиссия газов от очистных сооружений канализации: В последние годы внимание мирового сообщества сосредоточено на экологических проблемах...
© cyberpedia.su 2017-2024 - Не является автором материалов. Исключительное право сохранено за автором текста.
Если вы не хотите, чтобы данный материал был у нас на сайте, перейдите по ссылке: Нарушение авторских прав. Мы поможем в написании вашей работы!