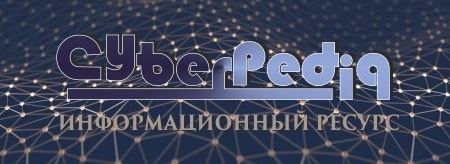
История развития пистолетов-пулеметов: Предпосылкой для возникновения пистолетов-пулеметов послужила давняя тенденция тяготения винтовок...
Кормораздатчик мобильный электрифицированный: схема и процесс работы устройства...
Топ:
Особенности труда и отдыха в условиях низких температур: К работам при низких температурах на открытом воздухе и в не отапливаемых помещениях допускаются лица не моложе 18 лет, прошедшие...
Процедура выполнения команд. Рабочий цикл процессора: Функционирование процессора в основном состоит из повторяющихся рабочих циклов, каждый из которых соответствует...
Оценка эффективности инструментов коммуникационной политики: Внешние коммуникации - обмен информацией между организацией и её внешней средой...
Интересное:
Лечение прогрессирующих форм рака: Одним из наиболее важных достижений экспериментальной химиотерапии опухолей, начатой в 60-х и реализованной в 70-х годах, является...
Инженерная защита территорий, зданий и сооружений от опасных геологических процессов: Изучение оползневых явлений, оценка устойчивости склонов и проектирование противооползневых сооружений — актуальнейшие задачи, стоящие перед отечественными...
Распространение рака на другие отдаленные от желудка органы: Характерных симптомов рака желудка не существует. Выраженные симптомы появляются, когда опухоль...
Дисциплины:
![]() |
![]() |
5.00
из
|
Заказать работу |
Требования отраслевых стандартов в сварке
Методические указания к практическим занятиям
Омск 2009
Составитель: В.А. Соколов, канд.техн.наук, доцент;
Введение
Практические занятия по курсу «Требования отраслевых стандартов в сварке» проводятся с целью получения студентами знаний по системе и требованиям отраслевых стандартов в областях производства, применяющих процессы сварки.
Настоящие методические указания предназначены для оказания помощи студентам при изучении действующих нормативных документов по различным отраслям промышленности, освоении методики составления технологических инструкций по сварке.
Общие требования
Для выполнения заданий на практических занятиях студенту выдается вариант задания (прил. 2). Вариант задания состоит из двух частей: буквенной и цифровой. Буквы обозначают группу технических устройств, по нормативным документам которой студенту предлагается составить технологическую инструкцию на сварку, а цифры – вариант задания, характеризующий конструктивные данные свариваемого изделия. В процессе выполнения задания, студент пользуется электронным вариантом базы нормативных документов, заложенной в ПК компьютерного класса кафедры. Кроме того, каждому студенту выдается вариант базы на электронном носителе.
Выполнение заданий заключается в изучении нормативных технических документов соответствующей заданию отрасли, с последующим составлением технологической инструкции в соответствии с приведенными в настоящих методических указаниях рекомендациями. Составление технология выполняется в компьютерном классе путем выборки и редактирования соответствующих разделов и положений действующих нормативных документов. Результат разработки технологии предъявляется преподавателю на проверку в электронном виде с последующей их распечаткой.
Технологические инструкции разрабатываются для групп технических устройств опасных производственных объектов, сварка которых осуществляется аттестованными сварщиками с применением аттестованных сварочных материалов, оборудования и технологий сварки.
Группы технических устройств
Котельное оборудование (КО)
1. Паровые котлы с давлением пара более 0,07 МПа и водогрейные котлы с температурой воды выше 115°С.
2. Трубопроводы пара и горячей воды с рабочим давлением пара более 0,07 МПа и температурой воды свыше 115 °С.
3. Сосуды, работающие под давлением свыше 0,07МПа.
4. Арматура и предохранительные устройства.
5. Металлические конструкции для котельного оборудования.
Нормативные материалы к заданию:
1. ПБ-03-273-99 Правила аттестации сварщиков и специалистов сварочного производства.
2. РД-03-495-03 Технологический регламент проведения аттестации сварщиков и специалистов сварочного производства.
3. РД 03-615-03 Порядок применения сварочных технологий при изготовлении, монтаже, ремонте и реконструкции технических устройств, для опасных производственных объектов.
4. РД 153-34.1-003-01 Сварка, термообработка и контроль при ремонте сварных соединений трубных систем котлов и трубопроводов при монтаже и ремонте энергетического оборудования.
5. ПБ 10-573-03 Правила устройства и безопасной эксплуатации трубопроводов пара и горячей воды.
6. ГОСТ 10704-91 Трубы стальные электросварные прямошовные. Сортамент.
7. ГОСТ 10705-80 Трубы стальные электросварные. Технические условия.
8. ГОСТ 380-94 Сталь обыкновенного качества. Марки.
9. ГОСТ 1050-88 Сталь качественная и высококачественная.
10. ГОСТ 19281-73 Прокат из стали повышенной прочности. Общие технические условия.
11. ГОСТ 9466-75 Электроды покрытые для ручной дуговой сварки и наплавки. Общие технические условия.
12. ГОСТ 9467-75 Электроды покрытые для ручной дуговой сварки конструкционных и теплоустойчивых сталей.
13. ГОСТ 16037-80 Соединения сварные стальных трубопроводов.
14. РД 03-606-03 Инструкция по визуальному и измерительному контролю.
15. ГОСТ 7512-82 Контроль неразрушающий. Соединения сварные. Радиографические методы.
16. ГОСТ 6996-66 Соединения сварные. Методы определения механических свойств.
Газовое оборудование (ГО)
1. Трубопроводы систем внутреннего газоснабжения.
2. Наружные газопроводы низкого, среднего и высокого давления стальные и из неметаллических материалов.
3. Газовое оборудование котлов, технологических линий и агрегатов.
4. Газогорелочные устройства.
5. Емкостные и проточные водонагреватели.
6. Аппараты и печи.
7. Арматура из металлических материалов и предохранительные устройства.
Нормативные материалы к заданию:
1. ПБ-03-273-99 Правила аттестации сварщиков и специалистов сварочного производства.
2. РД-03-495-03 Технологический регламент проведения аттестации сварщиков и специалистов сварочного производства.
3. РД 03-615-03 Порядок применения сварочных технологий при изготовлении, монтаже, ремонте и реконструкции технических устройств для опасных производственных объектов.
4. СНиП 42-01-03 Строительные нормы и правила Российской Федерации. Газораспределительные системы.
5. СП 42-102-2004 Проектирование и строительство газопроводов из металлических труб.
6. СП 42-103-2003 Проектирование и строительство газопроводов из полиэтиленовых труб и реконструкция изношенных газопроводов.
6. ПБ 12-529-03 Правила безопасности систем газораспределения и газопотребления.
7. ГОСТ 10704-91 Трубы стальные электросварные прямошовные. Сортамент.
8. ГОСТ 10705-80 Трубы стальные электросварные. Технические условия.
9. ГОСТ 380-94 Сталь обыкновенного качества. Марки.
10. ГОСТ 1050-88 Сталь качественная и высококачественная.
11. ГОСТ 19281-73 Прокат из стали повышенной прочности. Общие технические условия.
12. ГОСТ 9466-75 Электроды покрытые для ручной дуговой сварки и наплавки. Общие технические условия.
13. ГОСТ 9467-75 Электроды покрытые для ручной дуговой сварки конструкционных и теплоустойчивых сталей.
14. ГОСТ 16037-80 Соединения сварные стальных трубопроводов.
15. РД 03-606-03 Инструкция по визуальному и измерительному контролю.
16. ГОСТ 7512-82 Контроль неразрушающий. Соединения сварные. Радиографические методы.
17. ГОСТ 6996-66 Соединения сварные. Методы определения механических свойств.
Нефтегазодобывающее оборудование (НГДО)
1. Промысловые и магистральные нефтепродуктопроводы, трубопроводы нефтеперекачивающих станций (НПС), обеспечивающие транспорт нефти и нефтепродуктов при сооружении, реконструкции и капитальном ремонте.
2. Промысловые и магистральные нефтепродуктопроводы, трубопроводы нефтеперекачивающих станций (НПС), обеспечивающие транспорт нефти и нефтепродуктов при текущем ремонте в процессе эксплуатации.
3. Промысловые и магистральные газопроводы и конденсатопроводы; трубопроводы для транспортировки товарной продукции, импульсного, топливного и пускового газа в следующих пределах: установок комплексной подготовки газа (УКПГ), компрессорных станций (КС), дожимных компрессорных станций (ДКС), станций подземного хранения газа (СПХГ), газораспределительных станций (ГРС), узлов замера расхода газа (УЗРГ) и пунктов редуцирования газа (ПРГ).
4. Трубопроводы в пределах УКПГ; КС; НПС; СПХГ; ДКС; ГРС; УЗРГ; ПРГ и др., за исключением трубопроводов, обеспечивающих транспорт газа, нефти и нефтепродуктов.
5. Резервуары для хранения нефти и нефтепродуктов, газгольдеры газовых хранилищ при сооружении и ремонте.
Нормативные материалы к заданию:
1. ПБ-03-273-99 Правила аттестации сварщиков и специалистов сварочного производства.
2. РД-03-495-03 Технологический регламент проведения аттестации сварщиков и специалистов сварочного производства.
3. РД 03-615-03 Порядок применения сварочных технологий при изготовлении, монтаже, ремонте и реконструкции технических устройств для опасных производственных объектов.
4. ВСН 006-89 Ведомственные строительные нормы. Строительство магистральных и промысловых трубопроводов. Сварка.
5. ВСН 012-88 Ведомственные строительные нормы. Строительство магистральных и промысловых трубопроводов. Контроль качества и приемка работ.
6. СНиП III-42-80 Строительные нормы и правила. Магистральные трубопроводы.
7. ГОСТ 380-94 Сталь обыкновенного качества. Марки.
8. ГОСТ 1050-88 Сталь качественная и высококачественная.
9. ГОСТ 19281-73 Прокат из стали повышенной прочности. Общие технические условия.
10. ГОСТ Р 52079-2004 Трубы стальные сварные для магистральны газопроводов, нефтепроводов и нефтепродуктопроводов.
11. ГОСТ 9466-75 Электроды покрытые для ручной дуговой сварки и наплавки. Общие технические условия.
12. ГОСТ 9467-75 Электроды покрытые для ручной дуговой сварки конструкционных и теплоустойчивых сталей.
13. ГОСТ 16037-80 Соединения сварные стальных трубопроводов.
14. РД 03-606-03 Инструкция по визуальному и измерительному контролю.
15. ГОСТ 7512-82 Контроль неразрушающий. Соединения сварные. Радиографические методы.
16. ГОСТ 6996-66 Соединения сварные. Методы определения механических свойств.
Рекомендации по составлению инструкции
1. Введение
Во введении приводятся сведения о назначение инструкции, области ее применения. Указанные сведения должны соответствовать группе устройств, для работы с которыми, разрабатывается данная инструкция, а также варианту задания, установленному преподавателем. В области применения также указывается виды работ (изготовление, монтаж, ремонт), способ сварки, диапазон диаметров труб, толщин стенки и группа материала трубы.
Приводится краткая характеристика объекта, в сооружении которого применяются данная группа устройств, а также характеристика самой группы устройств.
Далее приводится перечень нормативных документов, на основании которых разрабатывается данная технология (ГОСТы, ОСТы, ТУ, ПБ, РД, НТД и пр.) и принятые в инструкции обозначения и сокращения.
2.Технические требования.
2.1. Требования к основным материалам
Требования к основным материалам должны содержать перечень применяемого металлопроката (труба, лист, профиль) с указанием ГОСТов, ТУ, в соответствии с которыми они изготавливаются, а также марок применяемых при этом сталей, с указанием соответствующих им ГОСТов. Приводятся требования о наличии сертификата и правила приемки материалов при отсутствии сертификата. Подробно описывается порядок выполнения и требования по входному контролю основных материалов.
2.2.Требования к сварочным материалам
В зависимости от применяемого способа сварки приводятся требования к электродам плавящимся (тип электрода, его марка, вид покрытия в соответствии с ГОСТ и НТД); сварочная проволока (марка материала, диаметр, вид поставки); электроды неплавящиеся (марка, диаметр); защитные газы; флюс (марка). По всем материалам приводятся ГОСТы на их изготовление, требования к качеству, к условиям их хранения и входному контролю.
2.3. Требования к сварочному и вспомогательному оборудованию
При составлении требований к оборудованию, приводится: состав сварочного поста (вид и тип оборудования, марки, ГОСТ на изготовление, требования к эксплуатации), необходимость применения средств механизации (сборочно-сварочные приспособления, механическое оборудование - вид и тип, марка), состав оборудования для выполнения подогрева и термообработки, прокалки и сушки электродов (вид и тип, марка, ГОСТ на изготовление, аппаратура для проведения контроля (вид и тип, марка, ГОСТ), описание применяемой оснастки и инструментов (вид и тип, марка, ГОСТ на изготовление).
2.4. Требования к квалификации персонала.
Требования к квалификации персонала включают в себя требования к квалификации сварщика (разряд, уровень, правила допуска к сварке, условия присвоения клейма), в соответствии с действующими по данному направлению нормативными документами.
Требования к квалификации специалистов сварочного производства (уровень, допуск), требования к термистам (разряд, допуск к работам).
Требования к специалистам неразрушающего контроля (разряд, уровень, допуск к работе).
3. Технологический процесс сварки
3.1. Подготовка кромок (труб или места) под сборку и сварку.
При описании мероприятий по подготовке труб к сборке приводятся правила по сортировке основного материала на группы с плюсовым и минусовым отклонениями от номинальных значений (внутренний диаметр, толщина); правила резки (газопламенная, плазменная, воздушно-дуговая, механическая) основного материала, способ и глубина обработки при механической зачистке кромок;
Приводятся сведения о необходимость применения подогрева при резке основного металла и обработки кромок, а также применяемые при этом режимы и оборудование.
Приводятся требования к форме подготовки кромок (ГОСТ, ТУ) и величине зачищаемой поверхности.
3.2. Сборка стыков
Требования к сборке включают:
- описание правил применения приспособлений (тип, марки); проверку точности сборки (соосность, перпендикулярность торцов, отклонения от номинальных значений, смещения);
-требования к наложению прихваток (расположение, размеры и количество прихваток, режим выполнения прихваток, диаметр электрода (проволоки), род и полярность тока, тип электрода, сила тока, положение при сварке, требования к подогреву, необходимость удаления прихваток);
- требования к контролю за сборкой и качеством прихваток (кто выполняет, какие документы оформляет);
- последовательность выполнения подогрева (при необходимости);
- контроль за температурой подогрева, режим подогрева (температура, толщина, марка стали) - где и чем измеряется.
3.3. Сварка
При описании требований к сварке указывается:
- количество слоев в сварном шве;
- диаметр электрода, которым выполняют сварку корня сварного шва;
- диаметр электрода, которым выполняют заполняющие и облицовочные сварные швы;
- требования к месту начала и окончания валика сварного шва;
- последовательность наложения сварных швов;
- режим сварки для различных пространственных положений при сварке и диаметрах электрода;
- схема последовательного наложения швов;
- правила выполнения сварных швов в различных пространственных положениях;
- требования к зачистке швов, при многослойной сварке;
- правила и место клеймения сварного шва.
Кроме того, при необходимости, приводятся специальные требования к сварке различных групп (марок) стали.
3.4. Термообработка сварного соединения
При необходимости термической обработки сварного соединения, приводятся сведения по виду термообработки; применяемому при этом оборудованию для термообработки; режимы термообработки, последовательность выполнения операций; контроль качества термообработки.
4. Требования к контролю качества сварных соединений.
При описании операций контроля процесса сварки и качества сварных соединений необходимо привести данные по требованиям:
а) к предварительному контролю:
- правила и порядок проверки квалификации персонала;
- правила и периодичность проверки сборочно-сварочных приспособлений, оборудования для сварки, термообработки и контроля качества;
- требования к проверке качества основных материалов (входной контроль);
- требования к проверке качества сварочных материалов (входной контроль);
- проверка качества материалов для дефектоскопии;
б) к пооперационному контролю:
- проверка качества подготовки кромок и качество сборки;
- проверка режимов сварки и последовательность наложения швов;
в) к готовому сварному соединению:
-проверка качества соединения визуально измерительным контролем;
-методика и нормы дефектности для ультразвуковой дефектоскопии;
- методика и нормы дефектности для рентгенографического контроля;
- правила и объем механических испытаний.
Выбор методов и объемов контроля выполняется разработчиком инструкции на основании требований соответствующей нормативной документации.
5. Мероприятия по охране труда
Мероприятия по охране труда должны содержать сведения (с приведением ссылок на источник) по организации рабочего места, требования по инструктажу на рабочем месте, правила выполнения работ на высоте, в замкнутых пространствах. Требования к электрозащитным и предохранительным средствам.
Правила заземления оборудования и освещения рабочего места.
Технологическая инструкция разрабатывается для определенных группы технических устройств и на один из применяемых способов сварки. Кроме того, в области назначения инструкции указываются значения диапазонов диаметров труб, толщин стенки, групп свариваемых материалов.
Приложение 1
Пример составления типовой технологической инструкции
|
|
Технологическая инструкция
Шифр ТИ -1С-М01
Разработал
Студент группы
Проверил
Омск, 2009
Содержание
1. Введение
1.1. Назначение инструкции
1.2.Характеристика сооружаемого объекта
1.3 Использованная документация
2. Технологические указания. Общие положения
2.1. Технические требования
2.1.1. Требования к основным материалам
2.1.2. Входной контроль труб и соединительных деталей
2.1.3 Требования к сварочным материалам
2.1.4. Требования к сварочному и вспомогательному оборудованию
2.1.5. Требования к квалификации персонала
2.2. Технологический процесс сварки
2.2.1. Подготовка кромок под сборку и сварку
2.2.2. Сборка стыков
2.2.3. Сварка
2.3. Требования к контролю качества сварных соединений
3. Техника безопасности
Введение
Назначение инструкции
Данная инструкция устанавливает требования к подготовке, сборке, сварке, контролю качества сварных соединений выполняемых при монтаже газового оборудования.
1.2.Характеристика сооружаемого объекта:
Трубопроводы систем внутреннего газоснабжения.
Использованная документация
В настоящей инструкции использованы ссылки на следующие документы:
· СНиП 42-01-2002 «Газораспределительные системы»;
· СП 42-102-2004 «Проектирование и строительство газопроводов из металлических труб»;
· ПБ 12-529-03 «Правила безопасности систем газораспределения и газопотребления»;
· ГОСТ 1050-88 «Прокат сортовой, калиброванный, со специальной отделкой поверхности из углеродистой качественной конструкционной стали. Общие технические условия»;
· ГОСТ 8731-74 «Трубы стальные бесшовные горячедеформированные. Технические требования»;
· ГОСТ 8732-78 «Трубы стальные бесшовные горячедеформированные. Сортамент»;
· ГОСТ 10704-91 «Трубы стальные электросварные прямошовные. Сортамент»;
· ГОСТ 10705-91 «Трубы стальные электросварные прямошовные. Технические условия»;
· ГОСТ 16037-80 «Соединения сварные стальных трубопроводов. Основные типы, конструктивные элементы и размеры»;
· 9466-75 «Электроды покрытые металлические для ручной дуговой сварки сталей и наплавки. Классификация и общие технические условия»;
· ГОСТ 9467-75 «Электроды покрытые металлические для ручной дуговой сварки конструкционных и теплоустойчивых сталей. Типы»;
· РД 03-606-03 «Инструкция по визуальному и измерительному контролю»;
· ГОСТ 7512 «Контроль неразрушающий. Соединения сварные. Радиографический метод»;
· ГОСТ 23055 «Контроль неразрушающий. Сварка металлов плавлением. Классификация сварных соединений по результатам радиографического контроля»;
· ГОСТ 14782 «Контроль неразрушающий. Соединения сварные. Методы ультразвуковые»;
· ГОСТ 6996 «Сварные соединения. Методы определения механических свойств»;
· ГОСТ 12.3.003-86 «Система стандартов безопасности труда. Работы электросварочные. Требования безопасности»;
· ПОТ РМ-020-2001 «Межотраслевые правила по охране труда при электро- и газосварочных работах».
Технологические указания. Общие положения
2.1. Технические требования
Требования к основным материалам
Характеристика основного материала | ||||
Марка стали |
Номер ТУ, ГОСТа |
Эквивалент Углерода, % | ||
На трубы, детали трубопроводов | На сталь | |||
ТРУБА | 10, 20, 10Г2 | ГОСТ 8731, ГОСТ 8732 | ГОСТ 1050 | Не более 0,46 |
10, 20 | ГОСТ 10704, ГОСТ 10705 | ГОСТ 1050 | ||
09Г2С | ТУ 14-3-1128 | ГОСТ19281 | ||
Заглушки | 20 |
ГОСТ17379 | ГОСТ 1050 | |
09Г2С | ГОСТ19281 | |||
Переходы | 20 |
ГОСТ17378 | ГОСТ 1050 | |
09Г2С | ГОСТ19281 | |||
Отводы | 20 | ГОСТ17375 | ГОСТ 1050 |
Требования к сварочным материалам
Электроды должны подбираться в соответствии с маркой свариваемой стали и технологией сварки, а также с температурой окружающего воздуха, при которой осуществляется строительство газопровода.
Электроды должны иметь сертификаты завода-изготовителя с указанием типа, марки, механических свойств, и химического состава наплавленного металла.
Перед применением качество электродов и их технологические свойства должны быть проверены на соответствие требованиям ГОСТ 9466-75.
Электроды до употребления должны храниться в сухих отапливаемых помещениях при температуре не ниже 150С с относительной влажностью не более 50%.
Электроды перед использованием должны быть прокалены при температуре 300 - 350 0С в течение 1 часа, с обязательным дальнейшим термостатированием. Количество прокалок не более трех.
Требования к сварочному и вспомогательному оборудованию
Для реализации современных технологий сварки и обеспечения качества сварных соединений, источники сварочного тока должны отвечать следующим требованиям:
* обеспечение возможности ручной дуговой сварки электродами с различным типом покрытия, применяемыми в трубопроводном строительстве;
* устойчивая работа источника при ручной дуговой сварке во всем диапазоне рабочих токов, в том числе при минимальных, начиная с 40 А;
* возможность регулирования внешних вольтамперных характеристик и настройки тока короткого замыкания в зависимости от типа покрытия электрода при сварке различных слоев шва и в разных пространственных положениях;
* высокие динамические свойства, обеспечивающие время перехода от короткого замыкания к рабочему режиму не более 0,01 секунды;
* наличие малогабаритных дистанционных регуляторов сварочного тока, удобно размещаемых в руке сварщика и обеспечивающих возможность регулирования тока, не обрывая дуги;
* эффективное регулирование сварочного тока с пульта дистанционного управления при длине кабеля подключения до 40 метров;
* возможность использования источников тока в составе передвижных и самоходных агрегатов при пониженном качестве автономной электросети переменного тока, характерного для сетей ограниченной мощности;
* минимальные колебания установленных значений сварочного тока и напряжения из-за взаимного влияния постов (не более ± 10 % от установленных значений) при использовании источников тока для компоновки многопостовых систем питания сварочным током в самоходных и передвижных агрегатах;
* возможность эксплуатации источников в диапазоне температур от плюс 40 0С до минус 40 0С;
Требования к квалификации персонала
1. К руководству и техническому контролю за производством сварочных работ допускаются специалисты, аттестованные в соответствии с «Правилами аттестации сварщиков и специалистов сварочного производства» ПБ 03-273-99.
2. К производству сварочных работ допускаются сварщики, аттестованные в соответствии с «Правилами аттестации сварщиков и специалистов сварочного производства» ПБ 03-273-99, имеющие удостоверение на право производства работ и квалификационный разряд не ниже 5-го. Сварщики (по любому виду сварки), впервые приступающие к сварке трубопроводов на монтаже данного объекта или имевшие перерыв в своей работе более 2 мес, а также все сварщики в случаях применения новых сварочных материалов или оборудования, независимо от наличия у них документов об аттестации, должны заварить пробные стыки в условиях, тождественных с теми, в которых производится сварка трубопроводов на данном объекте. Каждый сварщик должен иметь личное клеймо с номером.
3. Специалисты неразрушающего контроля должны быть аттестованы в соответствии с требованиями «Правил аттестации специалистов неразрушающего контроля» ПБ 03-440-02.
Подготовка кромок под сборку и сварку
Перед сборкой трубы необходимо рассортировать на группы с плюсовым и минусовым отклонением внутреннего диаметра от номинального значения.
Очистить внутреннюю полость труб и деталей от грунта, грязи, снега и других загрязнений.
Осмотреть поверхность и кромки труб, проверить геометрические размеры кромок, выправить плавные вмятины на концах труб глубиной до 3,5% наружного диаметра трубы. При температуре воздуха ниже -50С правка концов труб без их подогрева не рекомендуется.
Концы труб, имеющие трещины, надрывы, забоины, задиры фасок глубиной более 5 мм следует обрезать.
Типы, конструктивные элементы и размеры сварных соединений стальных газопроводов (рис.1) должны соответствовать ГОСТ 16037.
S=S1, мм | b, мм | c, мм | e, мм | g, мм | ||||
Номин. | Пред. откл. | Номин. | Пред. откл. | Номин. | Пред. откл. | Номин. | Пред. откл. | |
3 | 1,0 | +0,5 | 0,5 | +0,5 | 7 | +2 | 1,5 | +1,5 -1,0 |
4 | 8 | |||||||
5 | 1,5 | 1,0 | ±0,5 | 9 | ||||
6 | 11 | |||||||
8 | 2,0 | +1,0 | 13 | +3 |
Рис.1 Конструктивные элементы сварного шва по ГОСТ 16037
Зачистить до чистого металла кромки и прилегающие к ним внутреннюю и наружную поверхности трубы на ширину не менее 10 мм.
В случае использования труб с необработанными в заводских условиях торцами (после резки) подготовка кромок под стандартную разделку должна выполняться механической обработкой или газовой резкой с последующей зачисткой шлифмашинкой.
Сборка стыков
Осуществить сборку труб на инвентарных лежках с использованием наружного центратора.
Смещение кромок должно быть равномерно распределено по периметру стыка. Допускаемое смещение кромок свариваемых труб не должно превышать величины: 0,15S+0,5 мм, где S – наименьшая из толщин стенок свариваемых труб.
Сборку под сварку труб с односторонним продольным или спиральным сварным швом следует производить со смещением швов в местах стыковки труб не менее, чем на:
15 мм - для труб диаметром до 50 мм;
50 мм - для труб диаметром от 50 до 100 мм;
100 мм – для труб диаметром свыше 100 мм.
При сборке стыков труб должны быть обеспечены правильное фиксированное взаимное расположение стыкуемых труб и деталей, а также свободный доступ к выполнению сварочных работ в последовательности, предусмотренной технологическим процессом.
Сборка выполняется на прихватках. Их количество должно удовлетворять следующим условиям:
· для труб Ø до 80 мм – 2 шт.;
· для труб Ø свыше 80 мм до 150 мм – 3 шт.;
· для труб Ø свыше 150 мм до 300 мм– 4 шт.;
· для труб Ø свыше 300 мм – через каждые 250 мм.;
Высота прихватки должна составлять 1/3 толщины стенки трубы, но не менее 2 мм; длина прихватки – 20-30 мм при диаметре стыкуемых труб до 50 мм; 50-60 мм – при диаметре стыкуемых труб более 50 мм.
Режим выполнения прихватки – как для корневого слоя шва. Прихватки на стальном газопроводе должны выполняться материалами, предназначенными для сварки корневого шва.
Прямолинейность (соосность труб) в месте стыка необходимо проверять металлической линейкой длиной 400 мм, прикладывая ее в трех-четырех местах по окружности трубы. Максимально допустимое отклонение от соосности, измеряемое щупом, не должно превышать 0,5 мм на расстоянии 200 мм от шва (см. рисунок 3).
Рис. 3 Схема замера отклонений оси трубы
Сварка
Ручную дуговую сварку неповоротных и поворотных стыков труб при толщине стенок до 6 мм следует выполнять не менее чем в два слоя, при толщине стенок более 6 мм – не менее чем в три слоя.
Режимы сварки | ||||
Сварочные слои | Тип электрода | Диаметр, мм | Поляр- ность | Сварочный ток,А |
1 | Э50А | 2,5(2,6) | обратная | 70-90 |
2 | Э50А | 3,0(3,2) | обратная | 90 – 120 |
3 | Э50А | 3,0/3,2 | обратная | 90 - 120 |
Величина сварочного тока в вертикальном и потолочном положениях должна быть снижена на 10 – 15% |
Запрещается осуществлять сварку с применением любых присадок, непосредственно подаваемых сварочную дугу или предварительно заложенных в разделку.
Запрещается зажигать дугу с поверхности трубы. Дуга должна возбуждаться и гаситься на поверхности разделки кромок или же на поверхности металла уже выполненного шва.
Удалять наружный центратор разрешается после завершения сварки 50% периметра корневого слоя шва. При этом отдельные участки шва должны быть равномерно расположены по периметру стыка. Перед продолжением сварки корневого слоя шва после снятия центратора все сваренные участки должны быть зачищены, а концы швов прорезаны шлифмашинкой.
Для предупреждения образования дефектов между слоями сварного шва перед выполнением каждого последующего слоя поверхность предыдущего слоя должна быть очищена от шлака и брызг.
Начало и конец кольцевого сварного шва должны отстоять от заводского шва трубы (детали, арматуры) не ближе:
· 50 мм – для диаметров менее 400 мм;
· 75 мм – для диаметров менее 1000 мм;
· 100 мм - для диаметров более 1000 мм.
Места начала и окончания сварки каждого слоя («замки» шва) располагают для труб диаметром 400 мм и более не ближе 100 мм от «замков» предыдущего слоя шва, а для труб диаметром менее 400 мм – не ближе 50 мм.
До полного завершения корневого слоя шва не разрешается перемещать свариваемый стык.
На сварочных стыках подземных газопроводов должна быть нанесена маркировка (клеймо сварщика) выполнившего сварку. Способ нанесения маркировки должен обеспечить ее сохранность в течение эксплуатации газопровода. При заварке стыка несколькими сварщиками, клейма проставляются на границах свариваемых участков.
Сварочные работы на открытом воздухе во время дождя, снегопада, тумана и при ветре скоростью свыше 10 м/с необходимо выполнять при условии обеспечения защиты места сварки от влаги и ветра.
Требования к контролю качества сварных соединений
В процессе сварки осуществляют контроль:
· Предварительный
1. проверка квалификации сварщиков, дефектоскопистов;
2. проверка состояния сборочно-сварочных соединений, сварочного оборудования и аппаратуры, а также оборудования для контроля и аппаратуры для контроля качества сварных соединений;
3. проверка качества сварочных материалов, а также материалов для дефектоскопии;
4. проверка средств измерения, включая измерительные приборы.
· Пооперационный
1. проверка качества подготовки кромок под сварку и качества сборки под сварку;
2. соблюдение технологии сварки: соответствие сварочных материалов, режим подогрева и сварки, порядок наложения швов, качество послойной зачистки швов от шлака.
· Контроль качества готовых сварных соединений
Визуально-измерительный, радиографический (РГК), ультразвуковой контроль (УЗК) качества сварных соединений, а также проверка их механических свойств (МИ) производится в соответствии с требованиями государственных стандартов и нормативно-технических документов: визуальный и измерительный методы по РД 03-606-03 «Инструкция по визуальному и измерительному контролю»; РГК по ГОСТ 7512 «Контроль неразрушающий. Соединения сварные. Радиографический метод» и ГОСТ 23055 «Контроль неразрушающий. Сварка металлов плавлением. Классификация сварных соединений по результатам радиографического контроля»; УЗК по ГОСТ 14782 «Контроль неразрушающий. Соединения сварные. Методы ультразвуковые»; МИ по ГОСТ 6996 «Сварные соединения. Методы определения механических свойств».
Дефектация сварных соединений в соответствии с требованиями СНиП 42-01-2002 «Газораспределительные системы», СП 42-102-2004 «Проектирование и строительство газопроводов из металлических труб».
Оборудование, применяемое при контроле качества строительства, должно пройти поверку в сроки, установленные нормативной документацией. Контрольно-измерительное оборудование должно проходить метрологическую поверку в установленном порядке.
Сварные соединения подлежат визуальному и измерительному контролю с целью выявления наружных дефектов всех видов, а также отклонений по геометрическим параметрам, установленным ГОСТ 16037- 80, и взаимному расположению элементов.
Недопустимыми дефектами, выявленными при визуальном контроле сварных соединений, являются: трещины всех видов и направлений, непровары (несплавления) между основным металлом и швом, а также между валиками шва, наплывы (натеки) и брызги металла, незаваренные кратеры, свищи, прожоги, скопления включений.
Подрез размером 0,2 мм и менее измерению не подлежит, определяется визуально. Для газопроводов допускаются подрезы глубиной не более 5% толщины стенки трубы, но не более 0,5 мм и длиной не более 1/3 периметра стыка, но не более 150 мм.
Выявленные при визуальном и измерительном контроле дефекты, которые могут быть исправлены (удалены) без последующей заварки выборок, должны быть исправлены до проведения контроля другими методами.
Неразрушающий контроль сварных соединений (РГК, УЗК) проводится при положительных результатах визуального и измерительного контроля.
Выбор метода контроля (УЗК или РК) должен производится исходя из условий обеспечения выявления дефектов с учетом физических свойств материала.
УЗК сварных стыков стальных газопроводов применяется при условии выборочной проверки не менее 10% стыков РГК. При неудовлетворительных результатах контроля методом РГК хотя бы на одном стыке объем контроля следует увеличить до 50% от общего числа стыков. В случае повторного выявления дефектных с
Организация стока поверхностных вод: Наибольшее количество влаги на земном шаре испаряется с поверхности морей и океанов (88‰)...
Механическое удерживание земляных масс: Механическое удерживание земляных масс на склоне обеспечивают контрфорсными сооружениями различных конструкций...
Архитектура электронного правительства: Единая архитектура – это методологический подход при создании системы управления государства, который строится...
Историки об Елизавете Петровне: Елизавета попала между двумя встречными культурными течениями, воспитывалась среди новых европейских веяний и преданий...
© cyberpedia.su 2017-2024 - Не является автором материалов. Исключительное право сохранено за автором текста.
Если вы не хотите, чтобы данный материал был у нас на сайте, перейдите по ссылке: Нарушение авторских прав. Мы поможем в написании вашей работы!