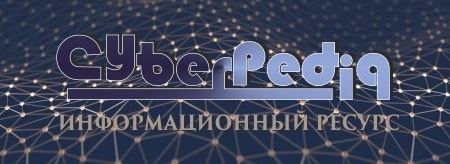
Эмиссия газов от очистных сооружений канализации: В последние годы внимание мирового сообщества сосредоточено на экологических проблемах...
Адаптации растений и животных к жизни в горах: Большое значение для жизни организмов в горах имеют степень расчленения, крутизна и экспозиционные различия склонов...
Топ:
Отражение на счетах бухгалтерского учета процесса приобретения: Процесс заготовления представляет систему экономических событий, включающих приобретение организацией у поставщиков сырья...
Эволюция кровеносной системы позвоночных животных: Биологическая эволюция – необратимый процесс исторического развития живой природы...
История развития методов оптимизации: теорема Куна-Таккера, метод Лагранжа, роль выпуклости в оптимизации...
Интересное:
Берегоукрепление оползневых склонов: На прибрежных склонах основной причиной развития оползневых процессов является подмыв водами рек естественных склонов...
Уполаживание и террасирование склонов: Если глубина оврага более 5 м необходимо устройство берм. Варианты использования оврагов для градостроительных целей...
Отражение на счетах бухгалтерского учета процесса приобретения: Процесс заготовления представляет систему экономических событий, включающих приобретение организацией у поставщиков сырья...
Дисциплины:
![]() |
![]() |
5.00
из
|
Заказать работу |
Назначение и особенности технологии
Оборудование PWT CWS.02 фирмы «Pipe Welding Technology» предназначено для односторонней автоматической сварки в защитных газах сплошной или порошковой электродной проволокой неповоротных стыков труб диаметром 426-1220 мм.
Оборудование оснащено компьютерной системой управления, позволяющей программировать режимы сварки для разных пространственных положений, диаметров и толщин стенок свариваемых труб и управлять работой сварочных головок.
Сварку корневого слоя производят на медной технологической подкладке, установленной между рядами жимков внутреннего центратора, входящего в состав оборудования.
Состав оборудования
В состав оборудования для сварки неповоротных стыков труб с использованием системы автоматической сварки CWS.02 входят:
- станок (станки) для обработки торцов труб под специальную разделку кромок;
- самоходный внутренний центратор с медным подкладным кольцом, встроенным между рядами жимков;
- система автоматической сварки CWS.02, состоящая из следующих модулей:
- сварочных головок;
- микропроцессорного блока управления сварочными головками;
- регуляторов сварочного тока;
- блока питания электронных устройств;
- блока смешивания защитных сварочных газов с расходомерами;
- системы кондиционирования электронных устройств блока управления;
- программирующего модуля на базе специализированного IBM- совместимого компьютера для программирования параметров режимов сварки шва и записи программ на специальные носители – картриджи, устанавливаемые в блоки микропроцессоров каждого из агрегатов питания. Микропроцессор через блок управления сварочной головки обеспечивает возможность автоматического регулирования, в зависимости от пространственного положения и порядкового слоя шва скорости сварки, скорости подачи электродной проволоки, напряжения на дуге, амплитуды и частоты колебаний электродной проволоки, времени задержки электрода в крайних положениях, состава и расхода защитного газа;
- направляющие пояса для перемещения сварочных автоматов;
- агрегаты энергообеспечения постов автоматической сварки, выполненные на базе колесных или гусеничных тракторов, на шасси которых смонтированы модули, входящие в состав CWS.02, двухпостовые сварочные дизель-генераторы, газовые рампы для баллонов с углекислым газом и аргоном, а также другое необходимое оборудование. Агрегаты питания снабжены гидрофицированными грузоподъемными стрелами для перемещения и установки на свариваемый стык сварочных головок и защитных палаток;
- наборы газовых редукторов, коммуникаций высокого давления, а также кабелей управления, газовых шлангов и приспособлений для монтажа оборудования на агрегатах питания;
- вспомогательное оборудование (устройства для подогрева стыков и др.).
Сварочные материалы
Марки проволок сплошного сечения для автоматической системы CWS.02 приведены в п. 8.1.2.1 настоящего РД.
Требование к смесям газов приведены в таблице 8.8 настоящего РД.
5.6.4 Состав и содержание основных технологических операций
Перед началом сварки разработанная для конкретного объекта технология вносится в компьютер, входящий в состав комплекса оборудования, записывается на носители специальной конструкции, которые устанавливается в блоки управления процессом сварки, смонтированные на агрегатах питания.
Технологический процесс сварки неповоротных стыков труб с применением оборудования CWS.02 включает следующие основные операции:
- раскладку труб на бровке траншеи;
- обработку на торцах труб специальной разделки кромок кромкострогальными станками и зачистку участков поверхности труб прилегающих к торцам;
- установку на торце каждой трубы направляющих поясов для сварочных автоматов;
- просушку или предварительный подогрев концов труб;
- сборку стыка;
- автоматическую сварку стыка.
5.6.4.1 Раскладка труб на бровке траншеи
5.6.4.1.1 Трубы или трубные секции укладывают на инвентарных лежках под углом 15-20 градусов к оси траншеи таким образом, чтобы обеспечивалась возможность обработки торцов кромкострогальными станками. Для этого высота инвентарных лежек должна обеспечивать расстояние между грунтом и нижней образующей поверхности трубы не менее 450 мм.
5.6.4.1.2 В процессе раскладки необходимо провести осмотр труб, исправить или вырезать участки труб с поверхностными дефектами в соответствии с требованиями раздела 5.1 настоящего РД.
5.6.4.2 Обработка на торцах труб специальной разделки кромок
5.6.4.2.1 Обработку торцев труб следует производить специальными кромкострогальными станками, входящими в состав оборудования.
5.6.4.2.2 Если обработка торца осуществляется после газовой резки, следует зашлифовать «заподлицо» с внутренней поверхностью трубы внутреннее усиление заводского шва на длину не менее 100 мм от торца. При зашлифовке продольных швов толщина стенки не должна быть выведена за пределы минусового допуска.
5.6.4.2.3 Схема разделки кромок под автоматическую сварку неповоротных стыков труб приведена на рис. 5.6.4.1.
Рис. 5.6.4.1 Схема и размеры разделки кромок
Условные обозначения и величины геометрических параметров:
С = 10 –2;
D = 1,0 ± 0,2 мм;
E = 1,0 ± 0,2 мм;
F = 2,0 ± 0,2 мм;
G = 25 ± 1°;
R = 6,0+2 мм;
H1 = 7,0 мм.
Неуказанные предельные отклонения размеров ± 0,3 мм.
5.6.4.3 Установка на трубах направляющих поясов для сварочных автоматов.
Установку поясов производят с помощью шаблонов, задающих одинаковое расстояние поясов от торца трубы. Пояс устанавливается на торец трубы, обращенный в сторону движения сварочно-монтажной колонны.
5.6.4.4 Предварительный подогрев осуществляется в соответствии с разделом 5.1 настоящего РД.
5.6.4.5 Сборка стыка
5.6.4.5.1 Сборку стыка следует производить на специальном внутреннем пневматическом центраторе, входящем в состав комплекса оборудования. Центратор устанавливают таким образом, чтобы медная технологическая подкладка находилась в плоскости стыка.
5.6.4.5.2 Перед началом работ следует произвести с помощью газовой горелки просушку медного подкладного кольца путем нагрева его секторов до температуры 20-50 0С.
5.6.4.5.3 Стык следует собирать без зазора. Допускаются локальные зазоры не более 1,0 мм. В случае, если при сборке не удается закрыть зазор в стыке, то рекомендуется собрать стык таким образом, чтобы локальные зазоры, величиной не более 1,0 мм, располагались в верхней части стыка.
5.6.4.5.4 Величина распределенного смещениия кромок в собранном стыке - не более 2 мм. Если распределенное смещение кромок выше 2 мм и качество сборки не может быть улучшено поворотом стыкуемой трубы вокруг горизонтальной оси, то следует заменить трубу, подаваемую на сборку. Допускаются локальные смещения кромок не более 3 мм при их суммарной длине £ 1/12 периметра трубы. При этом максимальная величина смещения не должна превышать значений, регламентированных п. 5.1.16.
5.6.4.5.5 После сборки стыка следует простучать его по всему периметру кувалдой с ударной частью из цветного металла для более плотного прилегания секторов медного подкладного кольца к внутренней поверхности трубы. Зазоры между элементами медного подкладного кольца и внутренней поверхностью трубы не должны превышать 0,5 мм.
5.6.4.6 Сварка стыка
5.6.4.6.1 Сварку всех слоев шва производят «на спуск». На стыке при сварке каждого слоя работают два автомата. Каждый автомат производит сварку одного из полупериметров трубы относительно вертикальной оси. Типовая схема сварки и последовательность сварки отдельных участков приведена на рис. 5.6.4.2.
5.6.4.6.2 Параметры режима сварки каждого слоя предварительно запрограммированы и записаны на картриджах специальной конструкции, установленных в блоки управления каждого агрегата питания. Перед началом сварки конкретного слоя сварщик-оператор с помощью переключателя, установленного на сварочной головке, задает порядковый номер свариваемого слоя.
5.6.4.6.3 В процессе сварки стыка сварщик имеет возможность с пульта дистанционного управления корректировать положение электродной проволоки поперек стыка, вылет, и в узких пределах амплитуду колебаний электродной проволоки и напряжение на дуге.
Дискретность регулирования положения электродной проволоки поперек стыка, вылета и амплитуды колебаний – 0,5 мм, напряжения на дуге – 0,2 В.
5.6.4.6.4 Сварку корневого слоя выполняют снаружи трубы. Формирование корневого шва происходит на медной технологической подкладке, установленной на центраторе.
5.6.4.6.5 Сварку корневого шва на участках с зазорами следует производить при увеличенном (до 15 мм) вылете электродной проволоки. При этом сварку корневого слоя следует производить в следующей последовательности:
- произвести сварку участков стыка, собранных без зазора;
- произвести сварку участков стыка с зазорами.
5.6.4.6.6 После окончания сварки корневого слоя следует сжать жимки центратора, уложить приваренную трубу на инвентарную лежку и переместить центратор на очередную позицию сборки.
![]() |
Рис. 5.6.4.2 Схема сварки и последовательность сварки отдельных участков шва
Принятые обозначения:
К1, К2 – участки корневого слоя на левом и правом полупериметрах трубы.
Зп 1.1 – заполняющие слои. Первая цифра обозначает номер слоя, вторая – последовательность сварки в пределах слоя.
Обл.1 – облицовочный слой. Цифра обозначает – последовательность сварки в пределах слоя
5.6.4.6.7 Интервал времени между окончанием сварки корневого шва и началом сварки 1-го заполняющего шва не должен превышать 10 мин.
5.6.4.6.8 Сварку заполняющих и облицовочного слоев шва выполняют «на спуск» с поперечными колебаниями электродной проволоки одновременно двумя сварочными автоматами, при этом каждый автомат сваривает половину стыка.
5.6.4.6.9 В процессе сварки всех слоев шва участки замков следует зашлифовывать для предотвращения образования дефектов типа непроваров и удаления кратерных трещин.
5.6.4.6.10 Амплитуду колебаний при сварке облицовочного шва назначают из расчета перекрытия швом разделки по ширине не менее чем на 1,0¸2,5 мм в каждую сторону.
5.6.4.6.11 Допускается сварку облицовочного слоя выполнять за 2 прохода.
5.6.4.6.12 Схема сварного шва приведена на рис. 5.6.4.3.
Рис. 5.6.4.3 Схема сварного шва выполненного автоматической сваркой на оборудовании CWS.02
5.6.4.6.13 После завершения сварки следует провести визуальную оценку качества облицовочного слоя. Обнаруженные недопустимые внешние дефекты сварного шва (участки с порами, подрезами свыше 0,5 мм, наплывы металла шва на участках замков и др.) следует вышлифовать и устранить сваркой до неразрушающего контроля.
5.6.4.6.14 Усредненные режимы сварки неповоротных стыков труб диаметром 1020 ¸ 1220 с толщинами стенок 10 ¸ 14 мм приведены в таблице 5.6.4.1. Режимы сварки автоматическиизменяются через каждые 15 градусов при отсчете положения головки от зенита стыка труб в угловых координатах.
Таблица 5.6.4.1 - Режимы сварки стыков диаметром 1020 ¸ 1220 мм
Параметры | Режимы сварки | |||||
Наименование слоя | ||||||
Корневой | 1-й заполня-ющий | 2-й заполня-ющий | 3-й заполня-ющий | 4-й заполня-ющий | Облицо-вочный | |
1 | 2 | 3 | 4 | 5 | 6 | 7 |
Направление сварки | на спуск | На спуск | На спуск | на спуск | На спуск | на спуск |
Скорость сварки, м/ч | 34,8-51,6 | 27,0-30,0 | 21,0-23,4 | 20,4-22,8 | 19,2-22,8 | 6,6-13,8 |
Диаметр проволоки, мм | 1,0 | 1,0 | 1,0 | 1,0 | 1,0 | 1,0 |
Скорость подачи электродной проволоки, м/мин | 11-11,6 | 9,4-11,0 | 9,5-10,3 | 9,5-10,3 | 7,1-8,0 | 3,0-6,2 |
Вылет электрода, мм | 8-12 | 10-14 | 10-14 | 10-14 | 10-14 | 8-12 |
Продолжение таблицы 5.6.4.1
1 | 2 | 3 | 4 | 5 | 6 | 7 |
Защитный газ Ar/CО2 * | 0/100 | 0/100 | 40/60 | 40/60 | 40/60 | 60/40 |
Расход газа, л/мин. | 25-28 | 25-28 | 25-28 | 25-28 | 25-28 | 25-28 |
Сила тока, А | 240-290 | 220-270 | 200-245 | 200-245 | 200-245 | 119-170 |
Напряжение на дуге, В | 22,2-23,8 | 21,8-22,4 | 20,6-21,0 | 20,6-21,2 | 19,0-20,0 | 15,8-18,8 |
Скорость колебаний электрода, см/мин. | 176-200 | 260-270 | 250-270 | 250-270 | 220-254 | 90-180 |
Амплитуда колебаний электрода, мм | 0,5-1,5 | 4,0-4,5 | 5,0-5,5 | 6,0-6,5 | 7,0-7,5 | 9,0-9,5 |
Задержка электрода в крайних положениях, с | 0,00-0,32 | 0,24-0,32 | 0,20-0,24 | 0,20-0,26 | 0,20-0,32 | 0,00-0,38 |
Угол наклона электрода, градус | ±5 | ±5 | ±5 | ±5 | ±5 | ±5 |
Примечание - * допускаются отклонения процентного содержания компонентов в газовой смеси в пределах ± 10 % от указанного в таблице. |
Типы оградительных сооружений в морском порту: По расположению оградительных сооружений в плане различают волноломы, обе оконечности...
Наброски и зарисовки растений, плодов, цветов: Освоить конструктивное построение структуры дерева через зарисовки отдельных деревьев, группы деревьев...
Особенности сооружения опор в сложных условиях: Сооружение ВЛ в районах с суровыми климатическими и тяжелыми геологическими условиями...
Автоматическое растормаживание колес: Тормозные устройства колес предназначены для уменьшения длины пробега и улучшения маневрирования ВС при...
© cyberpedia.su 2017-2024 - Не является автором материалов. Исключительное право сохранено за автором текста.
Если вы не хотите, чтобы данный материал был у нас на сайте, перейдите по ссылке: Нарушение авторских прав. Мы поможем в написании вашей работы!