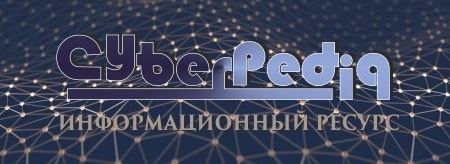
Типы сооружений для обработки осадков: Септиками называются сооружения, в которых одновременно происходят осветление сточной жидкости...
Опора деревянной одностоечной и способы укрепление угловых опор: Опоры ВЛ - конструкции, предназначенные для поддерживания проводов на необходимой высоте над землей, водой...
Топ:
Особенности труда и отдыха в условиях низких температур: К работам при низких температурах на открытом воздухе и в не отапливаемых помещениях допускаются лица не моложе 18 лет, прошедшие...
Определение места расположения распределительного центра: Фирма реализует продукцию на рынках сбыта и имеет постоянных поставщиков в разных регионах. Увеличение объема продаж...
История развития методов оптимизации: теорема Куна-Таккера, метод Лагранжа, роль выпуклости в оптимизации...
Интересное:
Национальное богатство страны и его составляющие: для оценки элементов национального богатства используются...
Искусственное повышение поверхности территории: Варианты искусственного повышения поверхности территории необходимо выбирать на основе анализа следующих характеристик защищаемой территории...
Что нужно делать при лейкемии: Прежде всего, необходимо выяснить, не страдаете ли вы каким-либо душевным недугом...
Дисциплины:
![]() |
![]() |
5.00
из
|
Заказать работу |
|
|
Для автоматической дуговой сварки под флюсом используют непокрытую электродную проволоку и флюс для защиты дуги и сварочной ванны от воздуха. Подача и перемещение электродной проволоки механизированы. Автоматизированы процессы зажигания дуги и заварки кратера в конце шва.
В процессе автоматической сварки под флюсом (рис. 4.9) дуга 10 горит между проволокой 3 и основным металлом 8. Столб дуги и металлическая ванна жидкого металла 9 со всех сторон плотно закрыты слоем флюса 5 толщиной 30…50 мм. Часть флюса расплавляется, в результате чего вокруг дуги образуется газовая полость, а на поверхности расплавленного металла — ванна жидкого шлака 4.
Рис. 4. 9. Схема процесса автоматической дуговой сварки под флюсом. Для сварки под флюсом характерно глубокое проплавление основного металла.
Действие мощной дуги и весьма быстрое движение электрода вдоль заготовки обусловливают оттеснение расплавленного металла в сторону, противоположную направлению сварки. По мере поступательного движения электрода происходит затвердевание металлической и шлаковой ванн с образованием сварного шва 7, покрытого твердой шлаковой коркой 6. Проволоку подают в дугу и перемещают ее вдоль шва с помощью механизмов подачи 2 и перемещения. Ток к электроду поступает через токопровод 1.
Основные преимущества автоматической сварки под флюсом по сравнению с ручной дуговой сваркой состоят в повышении производительности процесса сварки в 5…20 раз, качества сварных соединений и уменьшении себестоимости 1 м сварного шва. Повышение производительности достигается за счет использования больших сварочных токов (до 2000 А) и непрерывности процесса сварки. Применение непокрытой проволоки позволяет приблизить токопровод на расстояние 30…50 мм от дуги и тем самым устранить опасный разогрев электрода при большой силе тока. Плотная флюсовая защита сварочной ванны предотвращает разбрызгивание и угар расплавленного металла. Увеличение силы тока позволяет сваривать металл большой толщины (до 20 мм) за один проход без разделки кромок.
|
Повышенное качество сварных швов обусловлено получением более высоких механических свойств наплавленного металла благодаря надежной защите сварочной ванны флюсом, интенсивному раскислению и легированию вследствие увеличения объема жидкого шлака, сравнительно медленного охлаждения щва под флюсом и твердой шлаковой коркой; улучшением формы и поверхности сварного шва и постоянством его размеров по всей длине вследствие регулирования режима сварки, механизированной подачи и перемещения электродной проволоки.
Флюсы служат для изоляции сварочной ванны, от атмосферы воздуха, обеспечения устойчивого горения дуги, формирования поверхности шва и получения заданных состава и свойств наплавленного металла. Флюсы классифицируют по назначению, химическому составу и способу изготовления. По назначению они разделяются на флюсы для сварки низкоуглеродистых и низколегированных сталей, легированных и высоколегированных сталей.
Флюсы для сварки низкоуглеродистых и низколегированных сталей предназначены для раскисления шва и легирования его марганцем и кремнием. Для этого применяют плавленые высококремнистые марганцевые флюсы. Их шлаки имеют высокое содержание SiO2 и МnО. Флюсы получают путем сплавления марганцевой руды, кремнезема, плавикового шпата в электропечах.
Флюсы для сварки легированных и высоколегированных сталей должны обеспечивать минимальное окисление легирующих элементов в шве. Для этого применяют плавленые и керамические низкокремнистые, бескремнистые и фторидные флюсы. Их шлаки имеют высокое содержание СаО, СаF2 и А12О3. Плавленые флюсы изготовляют из плавикового шпата, алюмосиликатов, алюминатов, путем сплавления в электропечах. Их шлаки имеют основной характер. Керамические флюсы получают из порошкообразных компонентов путем замеса их на жидком стекле, гранулирования и последующего прокаливания. Основу керамических флюсов составляет мрамор, плавиковый шпат и хлориды щелочноземельных металлов. В их состав также входят ферросплавы сильных раскислителей (кремния, титана, алюминия) и легирующих элементов и чистые металла. Шлаки керамических флюсов имеют основной или пассивный характер и обеспечивают получение в металле шва заданное содержание легирующих элементов.
|
Дуговую сварку под флюсом выполняют сварочными автоматами, сварочными головками или самоходными тракторами, перемещающимися непосредственно по изделию. Назначение сварочных автоматов— подача электродной проволоки в дугу и поддержание постоянного режима сварки в течение всего процесса. Автоматическую сварку под флюсом применяют в серийном и массовом производствах для выполнения длинных прямолинейных и кольцевых швов в нижнем положении на металле толщиной 2—100 мм. Под флюсом сваривают стали различных классов. Автоматическую сварку широко применяют при изготовлении котлов, резервуаров для хранения жидкостей и газов, корпусов судов, мостовых балок и других изделий. Она является одним из основных звеньев автоматических линий для изготовления сварных автомобильных колес и станов для производства сварных прямошовных и спиральных труб.
Оборудование для сварки под флюсом. Дуга здесь горит в среде расплавленного флюса в газовом пузыре, защищающем металл капель и сварочной ванны от вредного воздействия атмосферных газов. Флюс производит металлургическую обработку (раскисление, легирование). При сварке под слоем флюса, препятствующего разбрызгиванию, сила тока может достигать 4000 А, что позволяет сваривать достаточно толстые листы без разделки кромок и в 2…8 раз увеличивает производительность по сравнению с ручной дуговой сваркой. Световое излучение дуги не воздействует на окружающих, однако отсутствие видимости места сварки относится к недостаткам ее. Флюсы состоят из оксидов кремния, марганца, алюминия, щелочных металлов, фторида кальция и др. Схема сварки под флюсом показана на рис. 4.10. Голая электродная проволока 3 подается механизмом 5 с катушки 6 в зону дуги, перед которой из бункера 4 на изделие 2 в зону стыка 1 подается флюс, не расплавившийся остаток которого отсасывается в бункер по трубке 7. Расплавившийся флюс остается на шве 9 в виде затвердевшей корки 8.
|
Автоматическая сварочная установка для сварки под слоем флюса состоит из автоматической сварочной головки, обеспечивающей зажигание и поддержание дуги непрерывной подачей проволоки, механизма для перемещения дуги вдоль шва (или детали относительно головки), источника сварочного тока, флюсовой аппаратуры, аппаратуры управления. Длина дуги поддерживается за счет изменения скорости подачи или скорости плавления электрода. В устройствах первого типа, например, при увеличении длины дуги увеличивается напряжение и система автоматического регулирования увеличивает скорость подачи электродной проволоки.
Рис. 4.10. Сварка под флюсом
В устройствах второго типа скорость подачи электрода постоянна, характеристика источника сварочного тока жесткая или падающая, поэтому изменение длины дуги вызывает изменение величины сварочного тока. Например, при увеличении длины дуги ток и скорость плавления электрода уменьшаются, что уменьшает длину дуги.
Для автоматической сварки под флюсом выпускаются стационарные трансформаторы, например ТДФЖ-Ш01УЗ и ТДФЖ-2002УЗ с жесткой характеристикой, а для сварки на постоянном токе применяют выпрямители, например ВДУ-1201, ВДУ-506, ВС-600М.
Подвесные самоходные автоматы А1416 и А1412 (двухэлектродный) содержат сварочную головку, подъемный механизм, флюссоаппарат, установленные на самоходную тележку велосипедного типа.
Тракторы общего применения для автоматической сварки под флюсом, например АДФ-1002 и АДФ-1202 — переносные дуговые сварочные аппараты, самоходная тележка которых движется во время сварки по свариваемому изделию или по линейке, параллельной шву. Скорость сварки тракторов 12—120 м/ч.
Электрошлаковая сварка
Этот способ разработан в институте им. Е. О. Патона. Электрошлаковая сварка является процессом соединения металлов, при котором основной и электродный металлы расплавляются теплотой, выделяющейся при охлаждении электрического тока через шлаковую ванну. Схема процесса электрошлаковой сварки показана на рис. 4.11.
|
Процесс начинается с образования шлаковой ванны 3 в пространстве между кромками основного металла 6 и приспособлениями (ползунами) 7, охлаждаемыми водой, подаваемой по трубам 1, путём расплавления флюса электрической дугой, возбуждаемой между сварочной проволокой и вводной планкой 9. После накопления определённого количества жидкого шлака дуга шунтируется шлаком и гаснет, а подача проволоки 4 и подвод тока продолжаются. При прохождении тока через расплавленный шлак, являющийся электропроводящим электролитом, в нём выделяется определённое количество теплоты, достаточной для поддержания высокой температуры шлака и расплавления кромок основного металла и электродной проволоки. Проволока вводится в зазор, подаётся в шлаковую ванну с помощью мундштука 5 и служит для подвода тока и пополнения сварочной ванны 2 расплавленным металлом. Как правило, электрошлаковую сварку выполняют при вертикальном положении свариваемых деталей. По мере заполнения зазора между ними мундштук для подачи проволоки и формирующие ползуны передвигаются в вертикальном направлении, оставляя после себя затвердевший сварной шов 8.
В начальном и конечном участках шва образуются дефекты. В начале шва – непровар кромок, в конце шва – усадочная раковина и неметаллические включения. Поэтому сварку начинают на вводной 9, а заканчивают на выходной 10 планках, которые затем удаляют газовой резкой.
Шлаковая ванна является более распределённым источником теплоты, чем электрическая дуга. Основной металл расплавляется одновременно по всему периметру шлаковой ванны, что позволяет вести сварку металла большой толщины за один проход.
Рис. 4.11. Схемы электрошлаковой сварки одним электродом
По типу применяемого электрода различают сварку одной и тремя электродной проволокой, пластинчатым электродом и плавящимся мундштуком.
Сварка одной электродной проволокой. Эта сварка является основным методом электрошлаковой сварки прямолинейных и круговых швов на металле толщиной до 600 мм. Заготовки толщиной до 150 мм можно сваривать одним электродом, совершающим поперечные колебания в зазоре для обеспечения равномерного разогрева шлаковой ванны по всей толщине. Металл толщиной более 150 мм сваривают тремя, а иногда и большим числом проволок, исходя из использования одного электрода на 45…60 мм толщины металла. Сварку проволокой ведут специальными автоматами, обеспечивающими подачу электродных проволок и их поперечное перемещение в зазоре. Автоматы перемещаются непосредственно по свариваемому изделию (безрельсовые) или по рельсовой колонне, устанавливаемой параллельно свариваемым кромкам. Скорость движения регулируется автоматически в зависимости от скорости заполнения зазора расплавленным металлом. Для сварки применяют проволоку диаметром 2 – 3 мм. Сварочный ток составляет 750…1000 А. В качестве источников питания применяют специальные трансформаторы для электрошлаковой сварки с жесткой внешней характеристикой.
|
Сварка тремя электродами (рис.4.12). Вытеканию ванны вбок препятствуют медные, водоохлаждаемые башмаки 2, которые вместе с электродами перемещаются по мере сварки вверх по свариваемым частям 3 и 4. На начальном и конечном участках привариваются планки. Шлаковая ванна защищает расплавленный металл от действия газов атмосферы.
![]() |
Сварка пластичным электродом. Этим методом сваривают прямолинейные швы длиной не более 1,5 м. Толщина пластинчатого электрода составляет примерно ½ ширины зазора, а длина соответственно в 3,5 раза больше длины шва. Во время сварки электрод опускается в шлаковую ванну специальным механизмом. Преимуществом этого метода является простота применяемой аппаратуры и повышенная устойчивость процесса сварки. К недостаткам следует отнести необходимость мощных источников питания: на каждый пластинчатый электрод требуется ток 1500-2000 А.
Сварка плавящимся мундштуком. Этим методом сваривают прямолинейные швы на заготовках большой толщины (более 500мм) и соединяют детали сложной формы. Плавящийся мундштук представляет собой пластину толщиной 5 – 6 мм с формой и размерами свариваемого сечения. Пластина имеет каналы для направления электродных проволок в зону сварки. Плавящийся мундштук закрепляют в свариваемом зазоре и изолируют от заготовок специальными прокладками. Мундштук расплавляется в процессе сварки, а непрерывно подающаяся проволока служит присадочным металлом для заполнения зазора. Особенно целесообразен плавящийся мундштук для сварки криволинейных швов переменного сечения, так как он обеспечивает равномерное распределение присадочного металла по сечению.
Преимущества и недостатки электрошлаковой сварки. Электрошлаковая сварка имеет преимущества по сравнению с автоматической дуговой сваркой под флюсом:
ü повышенную производительность вследствие непрерывности процесса сварки, выполняемой за один проход при любой толщине металла, увеличения сварочного тока в 1,5 – 2 раза;
ü уменьшения расхода электродного металла, так как сваривают по зазору без разделки кромок;
ü лучшую структуру сварного соединения вследствие более однородного строения шва;
ü отсутствие многосложности и шлаковых включений;
ü меньшие затраты на выполнение 1 пог. м сварного шва (в 10 раз и более) за счёт повышенной производительности;
ü уменьшения расхода флюса, электроэнергии, упрощения подготовки кромок свариваемых деталей.
К недостаткам электрошлаковой сварки следует отнести образование крупнозернистой структуры шва и околошовной зоны вследствие замедленного нагрева и охлаждения. После сварки необходима термическая обработка для получения мелкозернистой структуры металла сварного соединения. Толщина свариваемого металла составляет 50-2000 мм (рис.4.13). Электрошлаковую сварку широко применяют в тяжёлом машиностроении для изготовления таких сварно-кованых и сварно-литых конструкций, как станины и детали мощных процессов и станков, коленчатые валы судовых дизелей, роторы и валы гидротурбин, котлы высокого давления и т. п.
а) архитрав пресса б) баба бесшаботного молота
Рис. 4.13. Примеры применения электрошлаковой сварки:
Способ применяется для сварки изделий толщиной свыше 16 мм. Известны случаи сварки толщин около 3 м. Сварочные токи могут здесь достигать нескольких тысяч ампер. Источники сварочного тока - стационарные трансформаторы, например ТЗШ-100-3, ТРМК-3000-1 и выпрямители, например ВДУ-1201, ВДУ-505 и другие.
Автомат А-820К выполняет электрошлаковую сварку вертикальных стыковых швов материалов толщиной 18-70 мм. Автомат А-1304 сваривает сталь до 400 мм, а сплавы алюминия – до 140 мм. Автомат А-535 предназначен для сварки толщин до 450 мм.
Электроконтактная сварка
В настоящее время широко распространена электроконтактная сварка. Этот вид сварки является основным при изготовлении кузовов автомобилестроении, корпусов потребительских товаров (холодильников, стиральных машин, электроприборов и т. п.).
Электроконтактная сваркаотносится к видам сварки с кратковременным нагревом места соединения без оплавления или с оплавлением и осадкой разогретых заготовок. Характерная особенность этих процессов - пластическая деформация, в ходе которой формируется сварное соединение.
Место соединения разогревается проходящим по металлу электрическим током до пластического состояния или до расплавления, причем максимальное количество теплоты выделяется в месте сварочного контакта, после чего свариваемые детали сжимаются внешним усилием, что обеспечивает их сваривание. Количество выделяемой теплоты определяется законом Джоуля- Ленца:
Q» I 2 R τ,
где Q - количество теплоты, выделяемой в сварочном контуре, Дж;
R - полное электросопротивление сварочного контура, Ом;
I - сварочный ток, А;
τ - время протекания тока, с.
Полное электросопротивление сварочного контура R постоит из электросопротивлений выступающих концов L свариваемых заготовок R заг, сварочного контакта R к и электросопротивления между электродами и заготовками Rэл, т.е.
R» R заг + R к + R эл
Время сварки - от долей секунды до нескольких десятков секунд в зависимости от способа контактной сварки, силы тока и размеров свариваемых деталей.
Полное электросопротивление сварочного контура R, Ом, состоит из свариваемых заготовок R заг сопротивления между электродами и заготовками R эл, т. е.
R» R заг + R эл.
По типу свариваемого соединения, определяющего вид сварочной машины, различают: стыковую, точечную, рельефную, Т-образную, шовную (роликовую).
Стыковая сварка - вид контактной сварки, при которой заготовки свариваются по всей поверхности соприкосновения (рис. 4.14).
При стыковой сварке свариваемые заготовки закрепляют в зажимах стыковой машины. Зажим установлен на подвижной плите. Второй зажим укреплен на не подвижной плите. Сварочный трансформатор соединен с плитами гибкими шинами и питается от сети переменного тока через включающее устройство. Перемещение плит и сжатие свариваемых деталей осуществляется под воздействием усилия, развиваемого механизмом осадки.
Рис.4.14. Схема стыковой электроконтактной сварки
Перед сваркой заготовки должны быть очищены от оксидных пленок и торцы их плотно пригнаны друг к другу. Для подгонки необходима механическая обработка торцов.
Шовная или роликовая сварка - вид контактной сварки, при которой между свариваемыми заготовками образуется прочно- плотное соединение. При шовной сварке листы также соединяются внахлестку и зажимают между медными роликами трансформатор. Шовная сварка применяется для тонколистовой стали и цветных металлов и сплавов (толщина листа 1…3 мм).
Конденсаторная сварка -вид аккумулированной сварки. Энергия в конденсаторах накапливается при их зарядке от источника постоянного тока, а затем в процессе их разрядки преобразуется в теплоту, используемую для сварки. Конденсаторную сварку применяют в производстве электроизмерительных и авиационных приборов, часовых механизмов, фотоаппаратов, радиоламп и т.д.
К оборудованию для конденсаторной сварки предъявляют требования стабильности электрических характеристик и точной дозировки тока, а также стабильности сил сжатия. Конденсаторные машины обычно состоят из батареи конденсаторов, выпрямительных устройств, сварочного трансформатора, переключателя тока, разных вспомогательных устройств.
Точечная сварка - вид контактной сварки, при которой заготовки соединяются в отдельных местах, условно называемых точками.
Размеры и структура точки, определяющие прочность соединения, зависят от формы и размеров контактной поверхности электродов, величина сварочного тока, времени его протекания через заготовки. Качественная сварная точка характеризуется наличием общего для обеих заготовок литого ядра определенных размеров.
Точечную сварку применяют для соединения заготовок из сталей различных марок (углеродистой, легированной, нержавеющей), а также из цветных металлов и их сплавов. При точечной сварке заготовки соединяют в нахлестку и зажимают с некоторым усилием Р между двумя медными электродами, подводящими ток к месту сварки (рис.4.15). Соприкасающиеся с медным электродом поверхности свариваемых заготовок нагреваются медленнее их внутренних слоев. Нагрев продолжают до пластического состояния, затем включают ток и снижают давление. В результате образуется литая сварная точка.
Точечная сварка в зависимости от расположения электродов по отношению к свариваемым деталям может быть двусторонней и односторонней.
При двусторонней сварке (рис.4.16, а) две или более заготовок сжимают между электродами точечной машины. При односторонней сварке (рис.4.16, б) ток распределяется между верхним и нижним листами, причем нагрев осуществляется частью тока, протекающей через нижний лист. Для того чтобы увеличить ток, проходящий через нижний лист, применяют медную подкладку.
Односторонней точечной сваркой можно соединять заготовки одновременно двумя точками.
Точечной сваркой можно сварить листовые заготовки одинаковой или разной толщины, пересекающиеся стержни, листовые заготовки со стержнями.
4.9. Холодная сварка
Холодную сварку выполняют без нагрева при нормальных и даже при отрицательных температурах. Физическая сущность процесса заключается в сближении свариваемых поверхностей до образования металлических связей между ними и, следовательно, в получении прочных соединений. Такое сближение достигается приложением больших удельных давлений в месте соединения. В результате возникает совместная пластическая деформация. Большое усилие сжатия обеспечивает разрыв пленки окислов на свариваемых поверхностях и образование чистых поверхностей металла. Совместная пластическая деформация обеспечивает на короткое мгновение сближение друг с другом объемов кристаллитов, расположенных перед сдавливанием в глубинных слоях металла. При холодной сварке свариваемые поверхности очищают от адсорбированных жировых пленок. Холодной сваркой выполняют точечные, шовные и стыковые соединения. На рис. 4.17, а представлен процесс холодной точечной сварки. Свариваемые заготовки 1 с тщательно зачищенной поверхностью 2 в месте соединения помещают между пуансонами 4, имеющими выступы 5. При сжатии пуансонов усилием Р выступы 5 вдавливаются в металл по всей их высоте до тех пор, пока опорные поверхности 3 пуансонов не упрутся в наружную поверхность свариваемых заготовок. Форма сваренной точки зависит от формы выступа в пуансоне (рис. 4.17, г).
Рис. 4.17. Принципиальная схема холодной сварки:
а — точечная; б — стыковая; в — по контуру; г — форма сварной точкп
При стыковой холодной сварке соединяемые заготовки 7 закрепляют в соосно расположенных зажимах 6 (рис. 4.17, б). При осадке правый и левый зажимы сближают до соприкосновения, и острый край зажима отрубает излишний выдавленный металл — грат. В процессе осадки сближающие зажимы затрудняют течение металла и позволяют увеличить давление осадки. Деформируемый металл заполняет насечку 8, которая предотвращает его смещение в зажимах. Этим методом сваривают стержни и проволоку круглого, квадратного и прямоугольного сечений.
Место сварка получается чистым и не требует последующей обработки.
Для холодной шовной сварки применяют специальные ролики. Непрерывное шовное соединение может быть получено за счет сдавливания одновременно по всей длине соединения пли за счет прокатывания ролика. Швы, образующие замкнутый контур небольшой длины в виде кольца, прямоугольника и т. п., получают контурной сваркой. На рис. 4.17, в дана схема сварки полых деталей по контуру.Пуансоны 9 и 10строго центрируют с помощью корпуса 11. Холодной сваркой сваривают металлы и сплавы толщиной 0,2 — 15 мм. Удельные давления, зависящие от состава и толщины свариваемого материала, в среднем составляют 150 — 1000 МН/м2.
Холодной сваркой в основном сваривают металлы и сплавы, обладающие высокой пластичностью при комнатной температуре, с крупнозернистой отожженной структурой.
В недостаточно пластичных металлах при больших деформациях могут образоваться трещины. Высокопрочные металлы и сплавы холодной сваркой не сваривают, так как для этого требуются очень большие удельные давления, которые практически трудно осуществить.
Хорошо свариваются сплавы алюминия, дюралюминия, сплавы кадмия, свинца, меди, никеля, золота, серебра, цинка и тому подобные металлы и сплавы в однородных и разнородных сечениях. К преимуществам этого способа относятся малый расход энергии
незначительное изменение свойств металла, высокая производительность, возможность автоматизации.
Холодной сваркой сваривают алюминиевую оболочку кабелей. Ее применяют при изготовлении бытовых приборов из алюминия, корпусов полупроводниковых приборов и т. д., в электромонтажном производстве.
Оборудование. Для соединения внахлестку могут быть попользованы любые прессы (винтовые, гидравлические, рычажные, эксцентриковые). Кроме того, выпускают специализированные установки типа МХСА-50, МСХС-60, МСХС-30 и др. для стыковой холодной сварки.
Термокомпрессионная сварка. Термокомпрессионная сварка является разновидностью холодной сварки, причем в отличие от нее место соединения подогревают до температуры ниже температуры образования эвтектики соединяемых материалов и затем сжимают. Сваривают за счет направленной пластической деформации, аналогичной деформации при холодной сварке. На качество соединения при термокомпрессионной сварке влияет окисление поверхностей, поэтому целесообразно сваривать в защитной атмосфере (аргоне, смеси аргона с азотом и т. п.).
Термокомпрессионной сваркой сваривают высокоэлектропроводные материалы в виде круглых и плоских проводников с электропроводными тонкими пленками, направленными на хрупкие диэлектрические подложки.
Процесс весьма стабилен, легко контролируется. Основными параметрами являются усилие сжатия, температура нагрева и продолжительность выдержки. Оборудование очень простое и состоит из рабочего столика и рабочего инструмента (пуансона). Необходимый нагрев при сварке можно выполнять за счет нагрева рабочего инструмента или столика. Не требуется флюсов и припоев.
К недостатку этого способа можно отнести ограниченность сочетаний свариваемых материалов и размеры соединяемых деталей. Применяют этот способ в основном в приборостроительной промышленности.
Сварка трением.
|
|
Кормораздатчик мобильный электрифицированный: схема и процесс работы устройства...
Индивидуальные очистные сооружения: К классу индивидуальных очистных сооружений относят сооружения, пропускная способность которых...
Механическое удерживание земляных масс: Механическое удерживание земляных масс на склоне обеспечивают контрфорсными сооружениями различных конструкций...
Типы сооружений для обработки осадков: Септиками называются сооружения, в которых одновременно происходят осветление сточной жидкости...
© cyberpedia.su 2017-2024 - Не является автором материалов. Исключительное право сохранено за автором текста.
Если вы не хотите, чтобы данный материал был у нас на сайте, перейдите по ссылке: Нарушение авторских прав. Мы поможем в написании вашей работы!