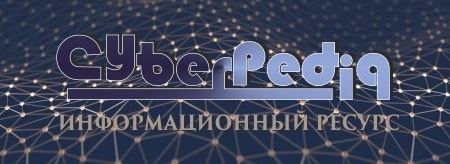
Автоматическое растормаживание колес: Тормозные устройства колес предназначены для уменьшения длины пробега и улучшения маневрирования ВС при...
История развития пистолетов-пулеметов: Предпосылкой для возникновения пистолетов-пулеметов послужила давняя тенденция тяготения винтовок...
Топ:
Оценка эффективности инструментов коммуникационной политики: Внешние коммуникации - обмен информацией между организацией и её внешней средой...
Марксистская теория происхождения государства: По мнению Маркса и Энгельса, в основе развития общества, происходящих в нем изменений лежит...
Эволюция кровеносной системы позвоночных животных: Биологическая эволюция – необратимый процесс исторического развития живой природы...
Интересное:
Подходы к решению темы фильма: Существует три основных типа исторического фильма, имеющих между собой много общего...
Национальное богатство страны и его составляющие: для оценки элементов национального богатства используются...
Что нужно делать при лейкемии: Прежде всего, необходимо выяснить, не страдаете ли вы каким-либо душевным недугом...
Дисциплины:
![]() |
![]() |
5.00
из
|
Заказать работу |
|
|
РАЗДЕЛ 4. ОБОРУДОВАНИЕ И ТЕХНОЛОГИЯ СВАРКИ
Общие сведения и классификация видов сварки
Сварка - технологический процесс получения неразъемных соединений материалов посредством установления межатомных связей между свариваемыми частями при их местном или общем нагреве, или пластическом деформировании, или совместным действием того и другого. Сваркой соединяют однородные и разнородные металлы и их сплавы, а также пластмассы. Сваркаявляетсяэкономически выгодным, высокопроизводительным технологическим процессом и широко применяется в строительстве и машиностроении. Она позволяет получать крупные сооружения (фермы мостов, резервуары). В машиностроении получают прочные, жесткие и легкие конструкции сваркой заготовок из проката, заготовок, полученных штамповкой и другими методами. Сваркой получают кузова, двери и кабины автомашин, вагонов, тракторов, сельхозмашин, детали бытовой техники, а также сварные детали станков, прессов, средств автоматизации идр. В настоящее время невозможно найти отрасль производства, где не применяется сварка.
Классификация видов сварки. Существует более 60 способов и 100 видов сварки, которую классифицируют по следующим признакам:
• степени механизации на ручную, механизированную, полу-автоматическую, автоматическую и роботизированную;
• состоянию материала в месте сваривания и методу соединения – на
сварку плавлением (электрическую, газо-электрическую, ндукционную, плазменно-лучевую, электрошлаковую, электронно0,
-лучевую, лазерную, световую, газовую, термитную, литейнуюидр.), нагреванием, пластической деформацией, термомеханическую (контактную, диффузионную, газопрессовую и др.), давлением или механическую (холодную, ультразвуковую, трением, взрывом и др.);
|
• виду используемого источника энергии - на механическую (трением и холодную), электрическую (дуговую, электрошлаковую, контактную и др.), химическую (газовую, термитную), электронно-лучевую и др.;
• способу защиты сварного шва в зоне сварки - в вакууме, в защитном газе, под флюсом, в пене, с комбинированной защитой;
• непрерывности процесса - на прерывную и непрерывную.
Такое разнообразие способов и видов сварки обусловлено многообразием свариваемых материалов (металлов, керамики, пластмасс, стекла, биологических тканей в однородных и неоднородных сочетаниях), а также условиями, в которых производятся сварочные работы.
Электрошлаковая сварка
Этот способ разработан в институте им. Е. О. Патона. Электрошлаковая сварка является процессом соединения металлов, при котором основной и электродный металлы расплавляются теплотой, выделяющейся при охлаждении электрического тока через шлаковую ванну. Схема процесса электрошлаковой сварки показана на рис. 4.11.
Процесс начинается с образования шлаковой ванны 3 в пространстве между кромками основного металла 6 и приспособлениями (ползунами) 7, охлаждаемыми водой, подаваемой по трубам 1, путём расплавления флюса электрической дугой, возбуждаемой между сварочной проволокой и вводной планкой 9. После накопления определённого количества жидкого шлака дуга шунтируется шлаком и гаснет, а подача проволоки 4 и подвод тока продолжаются. При прохождении тока через расплавленный шлак, являющийся электропроводящим электролитом, в нём выделяется определённое количество теплоты, достаточной для поддержания высокой температуры шлака и расплавления кромок основного металла и электродной проволоки. Проволока вводится в зазор, подаётся в шлаковую ванну с помощью мундштука 5 и служит для подвода тока и пополнения сварочной ванны 2 расплавленным металлом. Как правило, электрошлаковую сварку выполняют при вертикальном положении свариваемых деталей. По мере заполнения зазора между ними мундштук для подачи проволоки и формирующие ползуны передвигаются в вертикальном направлении, оставляя после себя затвердевший сварной шов 8.
|
В начальном и конечном участках шва образуются дефекты. В начале шва – непровар кромок, в конце шва – усадочная раковина и неметаллические включения. Поэтому сварку начинают на вводной 9, а заканчивают на выходной 10 планках, которые затем удаляют газовой резкой.
Шлаковая ванна является более распределённым источником теплоты, чем электрическая дуга. Основной металл расплавляется одновременно по всему периметру шлаковой ванны, что позволяет вести сварку металла большой толщины за один проход.
Рис. 4.11. Схемы электрошлаковой сварки одним электродом
По типу применяемого электрода различают сварку одной и тремя электродной проволокой, пластинчатым электродом и плавящимся мундштуком.
Сварка одной электродной проволокой. Эта сварка является основным методом электрошлаковой сварки прямолинейных и круговых швов на металле толщиной до 600 мм. Заготовки толщиной до 150 мм можно сваривать одним электродом, совершающим поперечные колебания в зазоре для обеспечения равномерного разогрева шлаковой ванны по всей толщине. Металл толщиной более 150 мм сваривают тремя, а иногда и большим числом проволок, исходя из использования одного электрода на 45…60 мм толщины металла. Сварку проволокой ведут специальными автоматами, обеспечивающими подачу электродных проволок и их поперечное перемещение в зазоре. Автоматы перемещаются непосредственно по свариваемому изделию (безрельсовые) или по рельсовой колонне, устанавливаемой параллельно свариваемым кромкам. Скорость движения регулируется автоматически в зависимости от скорости заполнения зазора расплавленным металлом. Для сварки применяют проволоку диаметром 2 – 3 мм. Сварочный ток составляет 750…1000 А. В качестве источников питания применяют специальные трансформаторы для электрошлаковой сварки с жесткой внешней характеристикой.
Сварка тремя электродами (рис.4.12). Вытеканию ванны вбок препятствуют медные, водоохлаждаемые башмаки 2, которые вместе с электродами перемещаются по мере сварки вверх по свариваемым частям 3 и 4. На начальном и конечном участках привариваются планки. Шлаковая ванна защищает расплавленный металл от действия газов атмосферы.
|
![]() |
Сварка пластичным электродом. Этим методом сваривают прямолинейные швы длиной не более 1,5 м. Толщина пластинчатого электрода составляет примерно ½ ширины зазора, а длина соответственно в 3,5 раза больше длины шва. Во время сварки электрод опускается в шлаковую ванну специальным механизмом. Преимуществом этого метода является простота применяемой аппаратуры и повышенная устойчивость процесса сварки. К недостаткам следует отнести необходимость мощных источников питания: на каждый пластинчатый электрод требуется ток 1500-2000 А.
Сварка плавящимся мундштуком. Этим методом сваривают прямолинейные швы на заготовках большой толщины (более 500мм) и соединяют детали сложной формы. Плавящийся мундштук представляет собой пластину толщиной 5 – 6 мм с формой и размерами свариваемого сечения. Пластина имеет каналы для направления электродных проволок в зону сварки. Плавящийся мундштук закрепляют в свариваемом зазоре и изолируют от заготовок специальными прокладками. Мундштук расплавляется в процессе сварки, а непрерывно подающаяся проволока служит присадочным металлом для заполнения зазора. Особенно целесообразен плавящийся мундштук для сварки криволинейных швов переменного сечения, так как он обеспечивает равномерное распределение присадочного металла по сечению.
Преимущества и недостатки электрошлаковой сварки. Электрошлаковая сварка имеет преимущества по сравнению с автоматической дуговой сваркой под флюсом:
ü повышенную производительность вследствие непрерывности процесса сварки, выполняемой за один проход при любой толщине металла, увеличения сварочного тока в 1,5 – 2 раза;
ü уменьшения расхода электродного металла, так как сваривают по зазору без разделки кромок;
ü лучшую структуру сварного соединения вследствие более однородного строения шва;
ü отсутствие многосложности и шлаковых включений;
ü меньшие затраты на выполнение 1 пог. м сварного шва (в 10 раз и более) за счёт повышенной производительности;
|
ü уменьшения расхода флюса, электроэнергии, упрощения подготовки кромок свариваемых деталей.
К недостаткам электрошлаковой сварки следует отнести образование крупнозернистой структуры шва и околошовной зоны вследствие замедленного нагрева и охлаждения. После сварки необходима термическая обработка для получения мелкозернистой структуры металла сварного соединения. Толщина свариваемого металла составляет 50-2000 мм (рис.4.13). Электрошлаковую сварку широко применяют в тяжёлом машиностроении для изготовления таких сварно-кованых и сварно-литых конструкций, как станины и детали мощных процессов и станков, коленчатые валы судовых дизелей, роторы и валы гидротурбин, котлы высокого давления и т. п.
а) архитрав пресса б) баба бесшаботного молота
Рис. 4.13. Примеры применения электрошлаковой сварки:
Способ применяется для сварки изделий толщиной свыше 16 мм. Известны случаи сварки толщин около 3 м. Сварочные токи могут здесь достигать нескольких тысяч ампер. Источники сварочного тока - стационарные трансформаторы, например ТЗШ-100-3, ТРМК-3000-1 и выпрямители, например ВДУ-1201, ВДУ-505 и другие.
Автомат А-820К выполняет электрошлаковую сварку вертикальных стыковых швов материалов толщиной 18-70 мм. Автомат А-1304 сваривает сталь до 400 мм, а сплавы алюминия – до 140 мм. Автомат А-535 предназначен для сварки толщин до 450 мм.
Электроконтактная сварка
В настоящее время широко распространена электроконтактная сварка. Этот вид сварки является основным при изготовлении кузовов автомобилестроении, корпусов потребительских товаров (холодильников, стиральных машин, электроприборов и т. п.).
Электроконтактная сваркаотносится к видам сварки с кратковременным нагревом места соединения без оплавления или с оплавлением и осадкой разогретых заготовок. Характерная особенность этих процессов - пластическая деформация, в ходе которой формируется сварное соединение.
Место соединения разогревается проходящим по металлу электрическим током до пластического состояния или до расплавления, причем максимальное количество теплоты выделяется в месте сварочного контакта, после чего свариваемые детали сжимаются внешним усилием, что обеспечивает их сваривание. Количество выделяемой теплоты определяется законом Джоуля- Ленца:
Q» I 2 R τ,
где Q - количество теплоты, выделяемой в сварочном контуре, Дж;
R - полное электросопротивление сварочного контура, Ом;
I - сварочный ток, А;
τ - время протекания тока, с.
Полное электросопротивление сварочного контура R постоит из электросопротивлений выступающих концов L свариваемых заготовок R заг, сварочного контакта R к и электросопротивления между электродами и заготовками Rэл, т.е.
|
R» R заг + R к + R эл
Время сварки - от долей секунды до нескольких десятков секунд в зависимости от способа контактной сварки, силы тока и размеров свариваемых деталей.
Полное электросопротивление сварочного контура R, Ом, состоит из свариваемых заготовок R заг сопротивления между электродами и заготовками R эл, т. е.
R» R заг + R эл.
По типу свариваемого соединения, определяющего вид сварочной машины, различают: стыковую, точечную, рельефную, Т-образную, шовную (роликовую).
Стыковая сварка - вид контактной сварки, при которой заготовки свариваются по всей поверхности соприкосновения (рис. 4.14).
При стыковой сварке свариваемые заготовки закрепляют в зажимах стыковой машины. Зажим установлен на подвижной плите. Второй зажим укреплен на не подвижной плите. Сварочный трансформатор соединен с плитами гибкими шинами и питается от сети переменного тока через включающее устройство. Перемещение плит и сжатие свариваемых деталей осуществляется под воздействием усилия, развиваемого механизмом осадки.
Рис.4.14. Схема стыковой электроконтактной сварки
Перед сваркой заготовки должны быть очищены от оксидных пленок и торцы их плотно пригнаны друг к другу. Для подгонки необходима механическая обработка торцов.
Шовная или роликовая сварка - вид контактной сварки, при которой между свариваемыми заготовками образуется прочно- плотное соединение. При шовной сварке листы также соединяются внахлестку и зажимают между медными роликами трансформатор. Шовная сварка применяется для тонколистовой стали и цветных металлов и сплавов (толщина листа 1…3 мм).
Конденсаторная сварка -вид аккумулированной сварки. Энергия в конденсаторах накапливается при их зарядке от источника постоянного тока, а затем в процессе их разрядки преобразуется в теплоту, используемую для сварки. Конденсаторную сварку применяют в производстве электроизмерительных и авиационных приборов, часовых механизмов, фотоаппаратов, радиоламп и т.д.
К оборудованию для конденсаторной сварки предъявляют требования стабильности электрических характеристик и точной дозировки тока, а также стабильности сил сжатия. Конденсаторные машины обычно состоят из батареи конденсаторов, выпрямительных устройств, сварочного трансформатора, переключателя тока, разных вспомогательных устройств.
Точечная сварка - вид контактной сварки, при которой заготовки соединяются в отдельных местах, условно называемых точками.
Размеры и структура точки, определяющие прочность соединения, зависят от формы и размеров контактной поверхности электродов, величина сварочного тока, времени его протекания через заготовки. Качественная сварная точка характеризуется наличием общего для обеих заготовок литого ядра определенных размеров.
Точечную сварку применяют для соединения заготовок из сталей различных марок (углеродистой, легированной, нержавеющей), а также из цветных металлов и их сплавов. При точечной сварке заготовки соединяют в нахлестку и зажимают с некоторым усилием Р между двумя медными электродами, подводящими ток к месту сварки (рис.4.15). Соприкасающиеся с медным электродом поверхности свариваемых заготовок нагреваются медленнее их внутренних слоев. Нагрев продолжают до пластического состояния, затем включают ток и снижают давление. В результате образуется литая сварная точка.
Точечная сварка в зависимости от расположения электродов по отношению к свариваемым деталям может быть двусторонней и односторонней.
При двусторонней сварке (рис.4.16, а) две или более заготовок сжимают между электродами точечной машины. При односторонней сварке (рис.4.16, б) ток распределяется между верхним и нижним листами, причем нагрев осуществляется частью тока, протекающей через нижний лист. Для того чтобы увеличить ток, проходящий через нижний лист, применяют медную подкладку.
Односторонней точечной сваркой можно соединять заготовки одновременно двумя точками.
Точечной сваркой можно сварить листовые заготовки одинаковой или разной толщины, пересекающиеся стержни, листовые заготовки со стержнями.
4.9. Холодная сварка
Холодную сварку выполняют без нагрева при нормальных и даже при отрицательных температурах. Физическая сущность процесса заключается в сближении свариваемых поверхностей до образования металлических связей между ними и, следовательно, в получении прочных соединений. Такое сближение достигается приложением больших удельных давлений в месте соединения. В результате возникает совместная пластическая деформация. Большое усилие сжатия обеспечивает разрыв пленки окислов на свариваемых поверхностях и образование чистых поверхностей металла. Совместная пластическая деформация обеспечивает на короткое мгновение сближение друг с другом объемов кристаллитов, расположенных перед сдавливанием в глубинных слоях металла. При холодной сварке свариваемые поверхности очищают от адсорбированных жировых пленок. Холодной сваркой выполняют точечные, шовные и стыковые соединения. На рис. 4.17, а представлен процесс холодной точечной сварки. Свариваемые заготовки 1 с тщательно зачищенной поверхностью 2 в месте соединения помещают между пуансонами 4, имеющими выступы 5. При сжатии пуансонов усилием Р выступы 5 вдавливаются в металл по всей их высоте до тех пор, пока опорные поверхности 3 пуансонов не упрутся в наружную поверхность свариваемых заготовок. Форма сваренной точки зависит от формы выступа в пуансоне (рис. 4.17, г).
Рис. 4.17. Принципиальная схема холодной сварки:
а — точечная; б — стыковая; в — по контуру; г — форма сварной точкп
При стыковой холодной сварке соединяемые заготовки 7 закрепляют в соосно расположенных зажимах 6 (рис. 4.17, б). При осадке правый и левый зажимы сближают до соприкосновения, и острый край зажима отрубает излишний выдавленный металл — грат. В процессе осадки сближающие зажимы затрудняют течение металла и позволяют увеличить давление осадки. Деформируемый металл заполняет насечку 8, которая предотвращает его смещение в зажимах. Этим методом сваривают стержни и проволоку круглого, квадратного и прямоугольного сечений.
Место сварка получается чистым и не требует последующей обработки.
Для холодной шовной сварки применяют специальные ролики. Непрерывное шовное соединение может быть получено за счет сдавливания одновременно по всей длине соединения пли за счет прокатывания ролика. Швы, образующие замкнутый контур небольшой длины в виде кольца, прямоугольника и т. п., получают контурной сваркой. На рис. 4.17, в дана схема сварки полых деталей по контуру.Пуансоны 9 и 10строго центрируют с помощью корпуса 11. Холодной сваркой сваривают металлы и сплавы толщиной 0,2 — 15 мм. Удельные давления, зависящие от состава и толщины свариваемого материала, в среднем составляют 150 — 1000 МН/м2.
Холодной сваркой в основном сваривают металлы и сплавы, обладающие высокой пластичностью при комнатной температуре, с крупнозернистой отожженной структурой.
В недостаточно пластичных металлах при больших деформациях могут образоваться трещины. Высокопрочные металлы и сплавы холодной сваркой не сваривают, так как для этого требуются очень большие удельные давления, которые практически трудно осуществить.
Хорошо свариваются сплавы алюминия, дюралюминия, сплавы кадмия, свинца, меди, никеля, золота, серебра, цинка и тому подобные металлы и сплавы в однородных и разнородных сечениях. К преимуществам этого способа относятся малый расход энергии
незначительное изменение свойств металла, высокая производительность, возможность автоматизации.
Холодной сваркой сваривают алюминиевую оболочку кабелей. Ее применяют при изготовлении бытовых приборов из алюминия, корпусов полупроводниковых приборов и т. д., в электромонтажном производстве.
Оборудование. Для соединения внахлестку могут быть попользованы любые прессы (винтовые, гидравлические, рычажные, эксцентриковые). Кроме того, выпускают специализированные установки типа МХСА-50, МСХС-60, МСХС-30 и др. для стыковой холодной сварки.
Термокомпрессионная сварка. Термокомпрессионная сварка является разновидностью холодной сварки, причем в отличие от нее место соединения подогревают до температуры ниже температуры образования эвтектики соединяемых материалов и затем сжимают. Сваривают за счет направленной пластической деформации, аналогичной деформации при холодной сварке. На качество соединения при термокомпрессионной сварке влияет окисление поверхностей, поэтому целесообразно сваривать в защитной атмосфере (аргоне, смеси аргона с азотом и т. п.).
Термокомпрессионной сваркой сваривают высокоэлектропроводные материалы в виде круглых и плоских проводников с электропроводными тонкими пленками, направленными на хрупкие диэлектрические подложки.
Процесс весьма стабилен, легко контролируется. Основными параметрами являются усилие сжатия, температура нагрева и продолжительность выдержки. Оборудование очень простое и состоит из рабочего столика и рабочего инструмента (пуансона). Необходимый нагрев при сварке можно выполнять за счет нагрева рабочего инструмента или столика. Не требуется флюсов и припоев.
К недостатку этого способа можно отнести ограниченность сочетаний свариваемых материалов и размеры соединяемых деталей. Применяют этот способ в основном в приборостроительной промышленности.
Сварка трением.
Мировой лидер
Первая машина для сварки металлов трением «МСТ-1» была разработана во ВНИИЭСО и внедрена для сварки заготовок инструмента на Сестрорецком инструментальном заводе в 1959 г.
В Институте разработано несколько десятков типоразмеров оборудования, в том числе ряд «МСТ-23», «МСТ-35», «МСТ-41» и «МСТ-51» с пневмогидравлическим приводом мощностью от 10 до 75 кВт, охватывающий диапазон свариваемых диаметров стальных заготовок от 10 до 70 мм, и ряд «МСТ-0401», «МСТ-2001», «МСТ-6001», «МСТ-120.01» с гидравлическим приводом мощностью от 4 до 160 кВт и диапазоном диаметров свариваемых стальных изделий от 5 до 120 мм.
Организован выпуск первого ряда машин на Волковысском заводе литейного оборудования, машины «МСТ-2001» - на Гомельском станкостроительном заводе и «МСТ-120.01» - на Краматорском заводе тяжелого станкостроения.
Первые публикации по сварке трением дали толчок к началу успешных работ этого направления в ряде стран Западной Европы и США. Тем не менее, ВНИИЭСО (вместе со своим «наследником» - Институтом сварки России) остался автором и ведущей организацией по сварке металлов трением.
В текущем году в Институте начаты экспериментальные работы по предложенной Британским институтом сварки сварке трением перемешиванием. Этот процесс сварки не имеет ничего общего с описанными выше способами и предназначен для стыковой сварки листов из алюминия и его сплавов. Вращающийся инструмент с заплечиками и штырем в центре, выступающим на величину чуть меньше толщины металла, вдавливается в жестко закрепленные листы и перемещается по линии их стыка. При этом нагретый до пластического состояния металл перемещается из зоны перед штырем в зону за ним, формуется заплечиками и образует сварное соединение в процессе охлаждения. Процесс похож на прессовую сварку и обеспечивает соединения, отвечающие самым высоким требованиям. Успешно используется при изготовлении изделий в автомобиле-, вагоно-, корабле- и ракетостроении.
В настоящее время в ОАО «Институт сварки России» изготовлен экспериментальный макет, который после отладки будет использован для исследования технологии сварки трением перемешиванием.
Сварка трением происходит в твердом состоянии при взаимном скольжении двух твердых тел, сжатых силой Р. Работа, совершаемая силами трения при скольжении, превращается в теплоту, что приводит к интенсивному нагреву трущихся поверхностей.
Рис. 4.18. Типы сварных соединений сварки трением:
а-стержневой встык; б-труб встык; в-встык стержня с трубой; г-стержня с листом; д-трубы с листом; е-стержня с массивной деталью.
Трение поверхностей осуществляется вращением или возвратно-поступательным перемещением свариваемых заготовок, сжимаемых силой Р. В результате нагрева и сжатия возникает совместная пластическая деформация. Сварное соединение образуется в результате возникновения металлических связей между чистыми (ювенильными) контактирующими поверхностями свариваемых заготовок. Окисные пленки, имеющиеся на металлических поверхностях в месте соединения, разрушаются в результате трения и удаляются за счет пластической деформации в радиальных направлениях.
Основными параметрами сварки трением являются скорость относительного перемещения свариваемых поверхностей, продолжительности нагрева, удельное давление, прилагаемое к свариваемым поверхностям, пластическая деформация, т. е. осадка. Необходимый для сварки нагрев при прочих равных условиях обусловлен скоростью вращения и осевым усилием. Здесь важно быстрое прекращение движения заготовки. Часто для получения качественного соединения необходимо приложение в конце процесса повышенного давления (проковки). Параметры режима сварки трением зависят от свойств свариваемого металла, площади сечения и конфигурации изделия. Сваркой трением соединяют однородные и разнородные металлы и сплавы с различными свойствами, например медь со сталью, медь со сплавами ковар, медь с алюминием, алюминий с титаном и др. В промышленности сварку трением применяют при изготовлении режущего инструмента, различных валов, штоков с поршнями, пуансопов и т. п. При сварке трением по сравнению с контактной стыковой сваркой снижаются затраты энергии и требуемые мощности. Так, например, при сварке стали трением энергии расходуется в 5…10 раз меньше, чем при контактной сварке.
Для сварки трением выпускают специальное оборудование, обеспечивающее работу при достаточно больших скоростях вращения и осевых усилиях и позволяющее производить быстрый запуск и мгновенную остановку шпинделя машины; это оборудование, ванне имеет достаточно высокую прочность для восприятия и гашения значительных радиальных вибраций.
Выпускают серийные машины для сварки трением типа МСТ-23, МСТ-35 и МСТ-41 мощностью 10, 20 и 40 кВт; в виде исключения после соответствующей реконструкции используют обычные металлорежущие станки.
Ультразвуковая сварка. Ультразвуковая сварка также относится к процессам, в которых используют давление, нагрев и взаимное трение свариваемых поверхностей. Силы трения возникают в результате действия на заготовки, сжатые осевой силой Р, механических колебаний с ультразвуковой частотой. При ультразвуковой сварке для получения механических колебаний высокой частоты используют магнитострикционный эффект, заключающийся в изменении размеров некоторых металлов, сплавов и керамических материалов под действием переменного магнитного поля. Изменения размеров магнитострикционных материалов очень незначительны, поэтому для увеличения амплитуды и концентрации энергии колебаний и для передачи механических колебаний к месту сварки используют волноводы, в большинстве случаев суживающейся формы. На рис. 4.19 показана простейшая схема ультразвуковой сварки. Свариваемые заготовки 5 размещают на опоре б. Наконечник 4 инструмента 3 соединен с двигателем магнитострикционногопреобразования 1 через трансформатор 2 продольных упругих колебаний, представляющих вместе с рабочим инструментомволновод. Нормальная сжимающая сила Р создается моментом М в узле колебаний. В результате ультразвуковых колебаний в тонких слоях контактирующих поверхностей создаются сдвиговые деформации, разрушающие поверхностные пленки. Тонкие поверхностные слои металла нагреваются, металл в этих слоях немного размягчается и под действием сжимающего усилия пластически деформируется. При сближении поверхностей на расстояние действия межатомных сил между ними возникает прочная связь. Сравнительно небольшое тепловое воздействие на свариваемые материалы обеспечивает минимальное изменение их структуры, механических и других свойств. Например, при сварке меди температура в зоне контакта не превышает 600 °С, а при сварке алюминия — 200—300 °С. Это особенно важно при сварке химически активных металлов, а также металлов, которые в результате высокотемпературного нагрева делаются хрупкими.
Ультразвуковой сваркой можно получать точечные и шовные соединения внахлестку, а также соединение по контуру. Шовные соединения получают на машинах, аналогичных машинам для точечной сварки. Отличие заключается в том, что их рабочий инструмент и опору выполняют в форме роликов.
При сварке по контуру, например по кольцу, в волновод вставляют конический штифт, имеющий форму полой трубки. При равномерном поджатии заготовок к свариваемому штифту получают герметическое соединение по всему контуру (рис.4.20). Ультразвуковой сваркой можно сваривать заготовки толщиной до 1 мм и ультратонкие заготовки толщиной до 0,001 мм, а также приваривать тонкие листы и фольгу к заготовкам неограниченной толщины. Снижение требований к качеству свариваемых поверхностей позволяет сваривать плакированные и оксидированные поверхности и металлические изделия, покрытые различными изоляционными пленками. Этим методом можно сваривать металлы в однородных и разнородных сочетаниях, например алюминий с медью, медь со сталью, цинк с оловом и т. п.
Прочность соединения, выполненного ультразвуковой сваркой достаточно высока (не менее 90 % от наиболее прочного металла в этом соединении).
Ультразвуковым методом сваривают и пластмассы, однако в отличие от сварки металлов ультразвуковые колебания здесь подводятся к заготовкам не тангенциально, а вертикально.
Оборудование. Установка ультразвуковой сварки состоит из сварочной машины и ультразвукового генератора. В Советском Союзе выпускают ультразвуковые машины типа УЗСМ-1 и УЗСМ-2.
Ультразвуковую сварку применяют в приборостроении, радиоэлектронике, авиационной промышленности и других отраслях.
Сварка взрывом. Сварку взрывом можно отнести к способам сварки с оплавлением при кратковременном нагреве на воздухе, так как на отдельных участках наблюдаются зоны металла, нагретые до оплавления. Однако на других участках температура может быть невысока, и здесь процесс приближается к холодной сварке.
Большинство технологических схем сварки взрывом основано на использовании направленного (кумулятивного) взрыва. Соединяемые поверхности (рис. 4.21) двух заготовок 4 и 3, в частности пластин, одна из которых неподвижна и является основанием, располагают под углом друг к другу на расстоянии h0. На заготовку 3 кладут взрывчатое вещество 2 толщиной Н, а со стороны, находящейся над вершиной угла, устанавливают детонатор 1. Сваривают на жесткой опоре. Давление в продуктах детонации, возникающее в результате взрыва, сообщает импульс расположенной под зарядом пластине. Детонация — это процесс, при котором разложение взрывчатого вещества с выделением газов и теплоты происходит с большой скоростью (несколько тысяч метров в секунду).
Пластина 3 метается со скоростью 1000 м/с па поверхность неподвижной пластины. В месте соударения метаемой пластины с основанием образуется угол, у, который перемещается вдоль соединяемых поверхностей. При соударении из вершины угла выдуваются тонкие поверхностные слои, окисные пленки и другие загрязнения. Соударение пластин вызывает течение металла в их поверхностных слоях, а в точках соударения происходит процесс совместного волнообразования. Поверхности сближаются до расстояния действия межатомных сил сцепления, и происходит схватывание по всей площади соединения. Продолжительность сварки взрывом не превышает нескольких микросекунд. Этого времени недостаточно для протекания диффузионных процессов, сварные соединения не образуют промежуточных химических составляющих между разнородными металлами и сплавами.
Прочность соединений, выполненных сваркой взрывом, выше прочности соединяемых материалов. Разрушение при испытании происходит на некотором расстоянии от плоскости соединения по наименее прочному металлу. Это объясняется упрочнением тонких слоев металла, прилегающих к соединенным
поверхностям, при их пластической деформации.
Параметрами сварки взрывом являются скорость детонации,нормальная скорость, метаемой пластины при соударении с основанием и углом у их встречи при соударении. Скорость детонации, определяемая типом взрывчатого вещества и толщиной его слоя, должна обеспечивать образование направленной (кумулятивной) струи без возникновения опасных для металла ударных волн:
Сварку взрывом используют при изготовлении заготовок для проката биметалла, плакировке поверхностей конструкционных сталей металлами и сплавами с особыми физическими и химическими свойствами, при сварке заготовок из разнородных материалов. Целесообразно сочетание сварки взрывом со штамповкой и ковкой.
Газоэлектрическая сварка
Одним из способов защиты расплавленного металла шва от вредного действия газов атмосферы (кислорода, водорода, азота) является защита сварочной ванны подачей в зону сварки защитного газа - аргона или углекислого газа.
Сварка плавящимся электродом в аргоне применяется для специальных сталей алюминиевых, магниевых, титановых сплавов и др. позволяет обходиться без флюсов. Сварка плавящимся электродом в среде углекислого газа — самый дешевый способ качественной дуговой сварки стали. Сварка неплавящимся вольфрамовым электродом в аргоне широко применяется для изделий из коррозионно- и жаростойких сталей, алюминиевых, медных, магниевых сплавов и активных металлов и производится также без флюсов. Сварка в защитных газах отличается следующим:
- высокая производительность;
- высокая эффективность защиты металла шва;
- возможность наблюдения за сваркой;
- широкий диапазон свариваемых толщин (от десятых долей до десят-ков миллиметров);
- ненадобность флюсов и обмазок;
- возможность сварки в различных пространственных положениях;
- широкие возможности механизации и автоматизации.
Сила тока обычно не превышает 600 А во избежание разбрызгивания расплавленного металла.
Источниками переменного тока для газоэлектрической сварки вольфрамовым электродом в среде аргона являются установки с крутопадающей характеристикой УДГ-301-1 и УДГ-501-1, включающие трансформатор, магнитный усилитель, устройство сварки кратера, батарею конденсаторов и возбудитель дуги. Применяются также источники переменного тока ТИР-300Д, УДГУ-301 и др.
Источниками постоянного сварочного тока при газоэлектрической сварке являются выпрямители с жесткой характеристикой для полуавтоматической сварки RC ЗООБ, ВСЖ-ЗОЗ, ВДГ-303, ВС-600М; универсальные ВДУ-505... ВДУ-601, которые могут работать как с жесткой, так и с крутопадающей характеристикой и применяются для сварки стали плавящимся электродом в среде углекислого газа и ручной дуговой сварки штучными электродами, а также ВДУ-1201 и ВДУ-1602 -для сварки в газовой среде, под флюсом, открытой дугой и порошковой проволокой на автоматах, с зависимой и независимой от напряжения дуги скоростью подачи электрода; многопостовые выпрямители В ДМ-1001, ВДМ-1601, ВДМ-4Х301 - для ручной сварки ВМГ-5000 - в основном для сварки в углекислом газе, а также ВДГИ-02 (для импульсной сварки); В
|
|
История развития пистолетов-пулеметов: Предпосылкой для возникновения пистолетов-пулеметов послужила давняя тенденция тяготения винтовок...
Опора деревянной одностоечной и способы укрепление угловых опор: Опоры ВЛ - конструкции, предназначенные для поддерживания проводов на необходимой высоте над землей, водой...
Адаптации растений и животных к жизни в горах: Большое значение для жизни организмов в горах имеют степень расчленения, крутизна и экспозиционные различия склонов...
Эмиссия газов от очистных сооружений канализации: В последние годы внимание мирового сообщества сосредоточено на экологических проблемах...
© cyberpedia.su 2017-2024 - Не является автором материалов. Исключительное право сохранено за автором текста.
Если вы не хотите, чтобы данный материал был у нас на сайте, перейдите по ссылке: Нарушение авторских прав. Мы поможем в написании вашей работы!