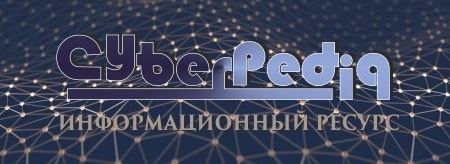
Археология об основании Рима: Новые раскопки проясняют и такой острый дискуссионный вопрос, как дата самого возникновения Рима...
Семя – орган полового размножения и расселения растений: наружи у семян имеется плотный покров – кожура...
Топ:
Эволюция кровеносной системы позвоночных животных: Биологическая эволюция – необратимый процесс исторического развития живой природы...
Основы обеспечения единства измерений: Обеспечение единства измерений - деятельность метрологических служб, направленная на достижение...
Комплексной системы оценки состояния охраны труда на производственном объекте (КСОТ-П): Цели и задачи Комплексной системы оценки состояния охраны труда и определению факторов рисков по охране труда...
Интересное:
Подходы к решению темы фильма: Существует три основных типа исторического фильма, имеющих между собой много общего...
Мероприятия для защиты от морозного пучения грунтов: Инженерная защита от морозного (криогенного) пучения грунтов необходима для легких малоэтажных зданий и других сооружений...
Искусственное повышение поверхности территории: Варианты искусственного повышения поверхности территории необходимо выбирать на основе анализа следующих характеристик защищаемой территории...
Дисциплины:
![]() |
![]() |
5.00
из
|
Заказать работу |
|
|
История развития производства сварочного электрооборудования тесно связана с историей развития дуговой электросварки.
В 1802 г. профессор физики Санкт – Петербургской медицинской академии Василий Владимирович Петров открыл явление электрической дуги.
Первым для сварки электрическую дугу применил российский изобретатель Николай Николаевич Бенардос в 1882 году. В качестве источника питания он использовал изобретенный им же аккумулятор 1, собранный из 2500 элементов (рис. 4.1). Величину тока он регулировал реостатом 2, последовательно включенным с дугой. Сварку выполнял угольным электродом 3с подачей в дугу присадочного металлического прутка 5. Обгорая, угольный электрод насыщал дугу окисью углерода СО, которая, будучи нерастворимой в жидком металле, защищала сварочную ванну от насыщения воздухом и тем предупреждала пористость шва. В 1888 году горный начальник Пермских пушечных заводов Николай Гаврилович Славянов произвел сварку металлическим электродом. Н. Г. Славянов, развивая дальше способ использования дуги В. В.Петрова для целей промышленного нагрева и сварки, впервые применил для питания дуги электрический генератор постоянного тока, включая реостат последовательно с дугой. Для защиты сварочной ванны от насыщения воздухом и предупреждения пористости наплавленного металла он применил металлургические шлаки; по сути, его способ был прообразом современной сварки под флюсом.
В 1907 году австрийский инженер Розенберг разработал первый специализированный источник питания для сварки - сварочный генератор, не нуждающийся в реостате для регулировки тока. Чем вызвана потребность в специализированных источниках? При сварке используется более низкое напряжение (40...80 В), чем в промышленных и бытовых сетях (220/380 В). Кроме того, напряжение в источниках для сварки по мере увеличения тока (нагрузки) должно снижаться, т.е. источник должен иметь падающую вольтамперную характеристику. Это делает дугу более эластичной, способной не погасать при внезапном удлинении или укорочении, что постоянно происходит при ручной сварке.
|
-----0
Рис.4.1. Схема сварки неплавящимся (угольным) электродом по методу Н.Н. Бенардоса: 1 - аккумуляторная батарея (секционированная), 2 - реостат, 3 - угольный электрод, 4 - держатель электродный, 5 - металлический пруток, 6 - изделие, 7 - электрическая (сварочная) дуга, 8 - сварочная ванна, 9 - наплавленный валик
Но падающая характеристика совершенно недопустима в большинстве других источников, например, в трансформаторах для питания сетей жилых домов. В этом случае по мере увеличения числа включенных ламп (увеличения тока) их накал уменьшался бы из-за снижения напряжения и освещенность квартир падала. И, наконец, последняя особенность источников для сварки заключается в наличии регуляторов тока, чтобы сваривать изделия различной толщины. Перечисленное убеждает, что приспособить для сварки источники питания общего назначения проблематично.
Следующими источниками для сварки стали трансформаторы, которые, по сравнению с генераторами, проще в изготовлении и неприхотливее в эксплуатации. Однако их применение для сварки задерживалось, т. к. дуга переменного тока менее устойчива, чем постоянного. При сетевой частоте 50 Гцток 100 раз в секунду снижается до нуля, т. е. дуга энергетически погасает. Фактически, из-за тепловой инерции она сохраняется, но отсутствие энергетической подпитки снижает ее температуру и мешает стабильному горению. Первыми массовый выпуск трансформаторов с падающей характеристикой в 30-х годах наладили в Советском Союзе. Это были трансформаторы в двухкорпусном исполнении (рис.4.2). В то время экономические возможности страны не позволяли выпускать в достаточном количестве дорогостоящие генераторы. Обратиться к трансформаторам Англию и США заставила вторая мировая война, так же принуждавшая к экономии. Развитие советского электросварочного машиностроения привело к широкому использованию электродуговой сварки в промышленности.
|
Рис. 4.2. Двухкорпусный (с отдельной дроссельной катушкой) сварочный трансформатор 30-х годов завода «Электрик»: 1 — первичная обмотка; 2 — вторичная; 3 — реактивная;
В 1924 г. на заводе «Электрик» была выпущена первая советская специальная сварочная машина постоянного тока СМ-1[1]. В эти же годы выпускались сварочные трансформаторы с отдельной дроссельной (реактивной) катушкой. В 1925 г. там же, был выпущен первый однокорпусный сварочный трансформатор (рис. 4.3) конструкции В. П. Никитина (патент № 3140 за 1927г.).
В 1929 г. советский инженер- изобретатель Д. А. Дульчевский разработал способ автоматической дуговой сварки под флюсом. С 1940 г. этот способ стал внедряться в промышленность и строительство. В этом большая заслуга Института электросварки им. Е. О. Патона А. Н. УССР, в котором были разработаны теория автоматической сварки, флюсы и автоматы для сварочных работ.
.
Рис. 4.3. Однокорпусный сварочный трансформатор типа СТН-500 академика В. П. Никитина:1 — первичная обмотка; 2 — вторичная; 3 — реактивная;
В области исследования и усовершенствования сварочных генераторов и трансформаторов советские ученые и инженеры проделали большую работу. Советский инженер и ученый В. П. Никитин возглавил научную школу в этой области. Была разработана теория сварочных генераторов постоянного тока и трансформаторов и созданы новые оригинальные сварочные трансформаторы.
Еще перед Великой Отечественной войной сварка переменным током стала основным видом сварки в СССР.
В конце 40-х годов американская промышленность освоила производство твердотельных полупроводников, которые позволили создать сварочные выпрямители (трансформатор + выпрямительный блок). Выпускаемые до этого полупроводники в виде радиоламп со стеклянными корпусами из-за хрупкости последних не могли быть использованы в сварочных источниках. Выпрямители стали альтернативой сварочным генераторам, которые до тех пор были единственными источниками постоянного тока для сварки. В СССР выпуск сварочных выпрямителей был налажен позднее, лишь к концу 50-х годов.
|
В послевоенные годы развитие производства отечественного сварочного электрооборудования пошло по пути дальнейшего увеличения выпуска сварочных трансформаторов.
Лабораторией электрических сварочных машин АН СССР совместно с заводами электропромышленности была создана единая серия однокорпусных сварочных трансформаторов СТАН, СТН и ТСД для ручной и автоматической сварки, которые по своим технико-экономическим показателям превосходят зарубежные[2]. Трансформаторы СТН и ТСД (по схеме В. П. Никитина) для токов 500 А и выше; трансформаторы СТАН для токов до 500 А. Разработаны конструкции и ряда других сварочных трансформаторов.
Были сконструированы и выпускались серийно (завод «Электрик») новые сварочные генераторы с независимым самовозбуждением, с размагничивающей последовательной обмоткой, а также сварочные генераторы на малые переменные токи высокой частоты.
Были разработаны и выпускались Всесозным научно-исследовательским институтом электросварочного оборудования (ВНИИЭСО) сварочные преобразователи, состоящие из трехфазного трансформатора, дросселей и выпрямляющего устройства из полупроводниковых германиевых или селеновых выпрямителей на 100 и 120 А. Были созданы серийные конструкции с селеновыми и германиевыми выпрямителями на токи 300 А и более [3].
Большое участие в дальнейшем развитии теории и технологии сварки принимают Центральный научно- исследовательский институт технологии машиностроения (ЦНИИТМаш), Московское высшее техническое училище им. Н. Э. Баумана, ВНИИЭСО, Всесоюзный научно- исследовательский институт автогенного машиностроения (ВНИИИавтогенмаш), завод ”Электрик”, Уралмашзавод и др.
В 90-е годы СССР по объему работ и по уровню развития сварочного производства занимал одно из ведущих мест в мире. Сегодня сварка заняла важное место в различных отраслях промышленности и строительства благодаря своим преимуществам перед другими способами производства изделий.
В начале 80-х годов финская фирма “Кемпи” начала производить инверторные сварочные выпрямители. В них с помощью транзисторов сетевое напряжение частотой 50 Гц преобразовывается в высокочастотное до 50 кГц. Это позволяет заменить железный сердечник сварочного трансформатора на ферритный, что уменьшает массу выпрямителя в 2…3 раза.
|
Кроме того, увеличение частоты сварочного тока повышает стабильность горения дуги, снижает разбрызгивание металла. До 90-х годов инверторные выпрямители выпускались на малые токи, преимущественно для бытовых нужд. Однако появление нового поколения тиристоров, рассчитанные на большие токи, позволило в последнее время наладить выпуск более мощных инверторных выпрямителей для сварки.
В последние годы разработаны способы сварки, для которых необходимы источники с жесткими и возрастающими внешними характеристиками в рабочей части, а нашей отечественной электропромышленностью выпускаются источники для питания сварочной дуги только с падающими внешними характеристиками.
Проводится работа по созданию источников питания сварочной дуги с применением новейших материалов и современной автоматической аппаратуры, а также аппаратов для питания сварочной дуги постоянным и переменным током с применением полупроводниковых выпрямителей. В частности, разрабатываются источники питания сварочной дуги, в которых можно будет в широких пределах управлять формой внешней характеристики. Новые источники питания сварочной дуги должны иметь более высокие технико-экономические показатели, лучшие статические характеристики и динамические качества [2].
В настоящее время в промышленном применении имеются все вышеперечисленные типы источников питания: генераторы, трансформаторы, выпрямители. В данном курсе изучаются их устройство, принципы работы, способы настройки на заданный режим и области применения.
Одним из самых распространенных видов сварки является электродуговая.
4.2. Свойства сварочной дуги и требования к источникам питания
4.2.1. Физические процессы в сварочной дуге. Сварочная дуга – установившийся мощный электрический разряд между электродами в ионизированной смеси газов, паров металлов и веществ, входящих в состав электродных покрытий, флюсов и других защитных средств. По сути, сварочная дуга представляет собой светящийся газообразный проводник электрического тока. На практике чаще встречаются проводники электрического тока в виде твердого тела, например медные электрические провода. Газовая же среда при нормальных условиях является электрически непроводящей. Электронная теория дуги[4] отвечает на вопрос, как диэлектрическая газовая (воздушная, аргоновая и пр.) среда превращается в проводник тока.
|
Газы при нормальных условиях состоят из электрически нейтральных атомов или молекул. Но для протекания электрического тока необходимы заряженные частицы. Их образование в газовом промежутке между электродом и изделием происходит следующим образом. Для зажигания дуги кратковременно касаются электродом изделия, т. е. производят короткое замыкание электрической цепи. Это приводит к протеканию по цепи тока большой величины, который разогревает соприкасающиеся поверхности электрода и изделия из-за их большого контактного сопротивления. После отрыва электрода от изделия, благодаря тепловой энергии, с поверхности электрода происходит испускание (эмиссия) электронов. Они подхватываются электрическим полем и уносятся в сторону анода (изделия), где сталкиваются с нейтральными атомами газовой среды и ионизируют их. В результате в газовой среде между электродом и изделием появляется необходимое для протекания электрического тока количество заряженных частиц. Одновременно возможно протекание обратного процесса - рекомбинации (рис. 4.4). Ток в дуге складывается из движения электронов в сторону анода и движения положительных ионов в сторону катода. Принято считать, что ток дуги преимущественно электронный, т. к. подвижность электронов из-за меньшей массы существенно выше, чем подвижность тяжелых положительно заряженных ионов. Направленное движение заряженных частиц в дуговом промежутке приводит к тому, что вблизи катода, на расстоянии свободного пробега электронов, образуется избыток положительных ионов (объемный положительный заряд), а вблизи анода, на расстоянии свободного пробега положительных ионов, - избыток электронов (объемный отрицательный заряд). Концентрация заряженных частиц вызывает катодное (~ 20 В) и анодное (~ 4 В) падения напряжений, которые влияют на распределение тепловой энергии. Падение напряжения в катодной области выше, чем в остальных областях дуги, поэтому производительность плавления электрода на прямой полярности (электрод является катодом) больше, чем на обратной.
Поверхность анода бомбардируется электронами, а поверхность катода -ионами. Благодаря значительной массе последние вызывают разрушение поверхностного слоя катода, в том числе окисных и других поверхностных пленок, расположенных на нем. Это явление получило название «катодной очистки». Оно имеет важное значение для образования качественного сварного шва при сварке алюминия или наплавке алюминистой бронзы, т. е. в случаях, когда наплавляемая поверхность неизбежно «загрязнена» тугоплавкой окисной пленкой.
В 1844 году русский ученый Э. Х. Ленц[5] и независимо от него английский физик Джоуль установили тепловое действие тока при прохождении его через проводник. Этот закон справедлив и для такого проводника электрического тока, каким является сварочная дуга. Выделяемая в дуге теплота, концентрируясь в небольшом объеме, вызывает повышение температуры до нескольких (два - шесть) тысяч градусов, что позволяет расплавлять большинство металлов.
4.2.2. Требования к источникам питания электрической дуги. Ток для электрической дуговой сварки не может быть получен простым присоединением к электрической сети, так как сетевое напряжение (220 или 330 В) смертельно для сварщика; сила тока во многих осветительных сетях (6…15А) недостаточна для сварки (для ручной и полуавтоматической сварки требуется 50…500 А, а для автоматической 400…1200 А). Кроме того, сеть не может выдерживать коротких замыканий, сопровождающих процесс сварки. Таким образом, источники сварочного тока должны иметь напряжение холостого хода не выше 75 В (достаточное для зажигания дуги, но безопасное для сварщика), противостоять короткому замыканию, иметь достаточную мощность для сварки на рекомендуемых режимах, а также устройства для регулировки тока дуги и соответствующую внешнюю характеристику (зависимость тока от напряжения). Так, при ручной сварке, ведущейся на режимах, соответствующих тем участкам вольт- амперных характеристик дуг (рис. 4.5), которые параллельны оси токов, источник должен иметь крутопадающую характеристику. В этом случае при неизбежных колебаниях длины дуги в некоторых пределах (от L 1 до L 2) изменение сварочного тока D I будет малым по сравнению с источниками, имеющими жесткую характеристику D I ж. Таким образом, крутопадающая характеристика источника обеспечивает при ручной сварке большее постоянство значения сварочного тока, а следовательно большую стабильность процесса.
Источник должен обеспечивать легкое и надежное возбуждение дуги и устойчивое ее горение. Процесс сварки состоит в периодическом повторении: рабочего режима (горение дуги, сопровождающиеся образованием и ростом капли), короткого замыкания (при переходе капли в ванну; при этом ток резко возрастает); повторного зажигания дуги (после отделения капли напряжение возрастает и дуга вновь зажигается). Следовательно, источник должен обеспечивать возможность быстрого изменения напряжения и тока, т. е. обладать необходимыми динамическими свойствами.
Устойчивость дуги в установившемся режиме обеспечивается при ручной сварке крутопадающей вольт- амперной характеристикой источника. При небольшом отклонении силы тока от значения устойчивого равновесия параметры процесса самопроизвольно возвращаются к значениям равновесия. Если в точке А сила тока уменьшится, напряжение источника окажется больше того, которое необходимо для горения дуги — произойдет увеличение тока, и процесс горения вернется в точку А. Если сила тока увеличится, то напряжение источника станет меньше требуемого; это повлечет снижение силы тока, и горение дуги «вернется» в точку А.
Пригодность источника тока для питания сварочной дуги оценивают внешней вольт-амперной характеристикой, представляющей собой зависимость напряжения на клеммах источника от тока во внешней (сварочной) цепи. Обычные машины и трансформаторы непригодны для дуговой сварки, так как они имеют жесткую характеристику (рис.4.5, прямая линия С),при которой напряжение U остается постоянной величиной и не зависит от силы тока.
Источник питания сварочной дуги для ручной сварки имеет внешнюю крутопадающую характеристику (рис.4.5, кривые b и b 1), т. е. с возрастанием силы тока в цепи напряжение на клеммах источника уменьшается.
Точки пересечения (В, В1 В' и В") внешних вольт-амперных характеристик b и b 1со статическими вольт-амперными характеристиками дуги а и а 1соответствуют режиму устойчивого горения дуги (рис.4.5).
Источники питания дуги для ручной сварки должны соответствовать следующим требованиям:
1)напряжение холостого хода не выше 65…75 В; оно дол-жно быть достаточным для зажигания дуги и относительно безопасным для работы сварщика;
2) сила тока короткого замыкания не должна превышать сварочный (рабочий) ток более чем на 40…50 %;
3) необходимо, чтобы источник питания обладал хорошими динамическими свойствами и быстро реагировал на все изменения режима дуги;
4) эксплуатация источника должна быть простой и надежной, а регулирование тока должно осуществляться ступенчато и плавно.
Рис.4.5 Внешние характеристики источников питания сварочной дуги (L ~ длина дуги)
Динамические свойства выпрямительных установок лучше, чем у генераторов постоянного тока.
Для сварки неплавящимся электродом в защитных газах применяют источники постоянного и переменного тока. При сварке плавящимися электродами в защитных газах используют специальные преобразователи с жесткой и возрастающей внешними вольт-амперными характеристиками и сварочные выпрямители с жесткой внешней характеристикой.
При сварке малогабаритных деталей и узлов рабочее место сварщика огораживается специальными перегородками или брезентовыми шторами. Чтобы уменьшить отражение лучей электрической дуги, перегородки окрашивают в темные матовые тона, а брезентовые шторы пропитывают огнестойкой краской.
Оборудование поста для ручной электродуговой сварки состоит из сварочного аппарата или генератора, рабочего стола или стенда, щитка, инструмента, электрододержателя с гибким кабелем и сборочно-сварочных приспособлений.
Для защиты сварщика от действия инфракрасных и ультрафиолетовых лучей электрической дуги, а также от брызг металла служат щиток или шлем с защитными стеклами, специальный костюм, фартук и рукавицы.
При сварке в защитных газах кроме указанного оборудования устанавливают баллон с защитным газом и соответствующую регулировочную аппаратуру.
4.3. Основные типы источников питания сварочной дуги и их условное обозначение (маркировка)
В комплект оборудования для электродуговой сварки входят источники питания переменного (сварочные трансформаторы, агрегаты) или постоян-ного тока (выпрямители, преобразователи, специализированные источники постоянного тока), блок управления сварочным процессом, устройства и приспособления для механической подачи присадочного материала и сварочного инструмента в процессе сварки.
Сварочные трансформаторы преобразуют переменное сетевое напряжение (380 В) в переменное пониженное (40...80 В) - необходимое для сварки. Это наиболее простые в изготовлении и неприхотливые при эксплуатации источники, нашедшие широкое применение в промышленности. Дуга переменного тока менее устойчива, чем постоянного, но она не отклоняется под воздействием магнитных полей и ферро-магнитных масс.
Сварочные генераторы являются источниками постоянного тока, который, по сравнению с переменным, обеспечивает более устойчивое горение дуги. Чтобы привести генератор в работу, его якорю (ротору) необходимо сообщить вращательное движение. Это осуществляется с помощью двигателей переменного тока или двигателей внутреннего сгорания. Комбинация сварочного генератора с двигателем переменного тока называется сварочным преобразователем, а с двигателем внутреннего сгорания - сварочным агрегатом. Последние используются в основном для сварки в монтажных или полевых условиях, где отсутствуют электрические сети.
Если источник предназначен для питания одной дуги, то его называют однопостовым, а если от него питаются несколько дуг — «многопостовым».
Однопостовые сварочные генераторы постоянного тока имеют падающую внешнюю вольт-амперную характеристику и хорошие динамические свойства. Они имеют ступенчатое регулирование сварочного тока, производимое смещением щеток по коллектору или включением различного числа секций одной из обмоток. Плавное регулирование в пределах каждой ступени осуществляется с помощью реостата.
Многопостовые генераторы имеют жесткую вольт-амперную характеристику. Получение падающей вольт-амперной характеристики осуществляется на каждом сварочном посту. Плавное регулирование тока достигается включением в цепь каждого поста (дуги) балластного реостата. Схема питания сварочных постов от многопостового преобразователя показана на (рис.4.6, а).
Кроме того, питание сварочной дуги можно осуществить постоянным током от выпрямительных установок, собранных из полупроводниковых элементов. По сравнению с генераторами они более просты в эксплуатации, экономичны, имеют меньшую массу и габариты
Рис. 4.6. Схема многопостового генератора: Д — синхронный двигатель; СГ — сварочный генератор; 1 — 3 — сварочные посты
Сварочные выпрямители состоят из трансформатора и выпрямительного блока на полупроводниках. В сварочном выпрямителе переменное напряжение сети сначала понижается до сварочного, а затем выпрямляется и подается на дугу.
Классификация и маркировка источников питания / 1,с.8; 2,с.45, табл. 1/.
Источники питания сварочной дуги классифицируют по таким признакам:
1) назначению - на универсальные и специализированные;
2) роду тока - переменного или постоянного;
3) способу установки - на стационарные, передвижные и встроенные.
Для электросварочного оборудования, выпускавшегося в СССР, с 1975 года принята единая система обозначений (маркировка) источников питания. Их обозначение содержат буквы и цифры (табл. 4.1).
Первая буква маркировки сварочного оборудования обозначает тип изделия: Т — трансформатор (ТД-500; ТДП-1; ТСП-2; ТРПШ-500 и др.); В — выпрямитель (ВД-301; ВД-502; ВДУ-500; ВДМ-1001 и др.); Г — генератор (ГД-303); П - преобразователь, А – агрегат (АСБ-303М; АСБ-300-7 и др.); У — установка для сварки неплавящимся электродом (УДГ-301, УДГ-50);
вторая буква — вид сварки: Д — дуговая; П — плазменная;
третья буква — способ сварки: Ф — под флюсом; Г — в защитных газах; У — источник с универсальными внешними вольтамперными характеристиками для нескольких способов;
отсутствие буквы означает, что источник предназначен для ручной сварки штучными электродами);
четвертая дает дальнейшие пояснения назначения источника (О –однопостовой, М - для многопостовой сварки, И - для импульсной).
Таблица 4.1
Условное обозначение сварочного оборудования /2,с. 45/
№ позиции в условном обозначении | Значение позиции | Буквенные и цифровые обозначения | Расшифровка обозначений |
1-я буква | Тип источника | Т | Трансформатор |
Г | Генератор | ||
В | Выпрямитель | ||
П | Преобразователь | ||
А | Агрегат | ||
У | Специализированный источник питания | ||
2-я буква | Вид сварки | Д | Дуговая |
П | Плазменная | ||
| Способ сварки | Ф | Под флюсом |
Г | В защитных газах | ||
У | Универсальные источники | ||
Отсутствие | Ручная дуговая | ||
4-я буква | Вид внешней характеристики | Ж | Жесткая |
П | Падающая | ||
Назначение источника | М | Для многопостовой сварки | |
Отсутствие | Для однопостовой сварки | ||
И | Для импульсной сварки | ||
5-я позиция | Разделитель | - | - |
6-я цифра | Мощность | Две или одна цифра | Номинальный сварочный ток (в сотнях ампер) |
7-я цифра | Регистрация | Регистрационный номер изделия | |
8-я цифра | Исполнение | Хл | Для холодного климата |
У | Для умеренного климата | ||
Т | Тропическое исполнение | ||
9-я цифра | Категория размещения | 1 | Для работы в открытом воздухе |
2 | Для работы под навесом | ||
3 | Для работы в не отапливаемом помещении | ||
4 | Для работы в отапливаемом помещении | ||
5 | В помещении с повышенной влажностью |
Две цифры после букв и тире — номинальный сварочный ток в сотнях ампер; в аппаратах ручной сварки — в десятках. Затем следует две цифры — регистрационный номер изделия. Дальнейшие буквы и цифры указывают климатическое исполнение (ХЛ - для холодного климата, У - для умеренного климата, Т - для тропического климата) и категорию размещения (1 - для работы на открытом воздухе; 2 - в помещениях, где колебания температуры и влажности несущественно отличаются от колебаний на открытом воздухе (под навесом); 3 - в помещении с естественной вентиляцией; 4 — в помещении с принудительной вентиляцией и отоплением, т. е. с искусственным регулированием климатических условий; 5 - в помещении с повышенной влажностью).
Пример: На специальной табличке, прикреплённой к сварочной установке может быть надпись: ВДГМ-1602УЗ, которая расшифровывается следующим образом: В - выпрямитель, Д - для дуговой сварки, Г - в защитных газах, М - многопостовой, 16 - номинальный ток 1600 А, 02 - источник второй модификации, У - предназначен для работы в районах с умеренным климатом, 3 - следует размещать в закрытых помещениях.
Полуавтоматическая и автоматическая сварки - основные виды сварки в современном производстве, обладают высокой производительностью. Их классифицируют по таким признакам: способу защиты зоны дуги, виду электродной проволоки, способу регулирования, конструктивному исполнению, роду применяемого тока и др. Марки полуавтоматов: ПДГ-302-1, ПДШ-500С и др., автоматов: АДСП-1, АДФ-501, АПА-301 и др. специального назначения.
Наиболее важные параметры источников. Номинальный ток I H— главный параметр, на который рассчитывается источник, выбирают из рекомендованного ряда номинальных токов по ГОСТ 10594-80: 50, 80, 125, 160, 200, 250, 315, 400, 500, 630, 800, 1000, 1250, 1600, 2000, 2500, 3150, 4000 и 5000 А.
Номинальное напряжение U H, например, при ручной дуговой сварке вычисляется из соотношения U H= 20 + 0,04 J H.
Коэффициент полезного действия ηприводится обычно для номинального режима.
Коэффициент мощности cos φ обязательно указывается для трансформаторов (с первичной стороны).
4.4. Электроды для ручной электродуговой сварки Электрод представляет собой металлический стержень с нанесенным на его поверхность слоем специального покрытия. Тонкое покрытие состоит из ионизирующих и связывающих компонентов, а в состав среднего толстого и особо толстого покрытий входят ионизирующие, газообразующие, шлакообразующие, раскисляющие, легирующие и связывающие компоненты. Длина металлического стального стержня в зависимости от его диаметра по ГОСТ 9466—75 может составлять 250…450 мм.
Процесс изготовления электродов состоит в следующем. Электродную проволоку необходимого диаметра и химического состава правят, очищают и режут на стержни заданной длины. Компоненты электродного покрытия, измельченные до тонкого порошка, в соответствии с рецептурой взвешивают и тщательно перемешивают, а затем на растворе жидкого стекла делают замес, который наносят на стержень.
В случае, если покрытие наносят на стержень окунанием (ручной процесс), то паста должна иметь консистенцию густой сметаны.
Если покрытие наносят опрессовкой стержней пастой (механизированный процесс), то пасту приготовляют более густой. После нанесения покрытия электроды сушат, прокаливают, сортируют, упаковывают и отправляют потребителю.
Основными факторами, определяющими свойства электрода, являются химический состав электродного стержня и покрытия. Химический состав электродной стальной проволоки выбирают в соответствии с химическим составом и свойствами металла свариваемого изделия, и он регламентируется ГОСТ 2246—70.
В зависимости от химического состава проволоку разделяют на низкоуглеродистую (6 марок), легированную (30 марок) и высоколегированную (39 марок). Всего в ГОСТ включено 75 марок проволоки диаметром 0,3—12 мм. Обозначение марок электродной проволоки состоит из букв и цифр, например Св-08 или Св-З0ХГСА. Первые две буквы Св указывают на назначение проволоки — сварочная для изготовления электродов, а следующие за буквами две цифры и буквы с цифрами аналогичны обозначениям, принятым для углеродистых качественных машиностроительных сталей Состав электродного покрытия устанавливают в соответствии с химическим составом металлов электродного стержня и изделия. При этом электродное покрытие должно обеспечивать хорошую ионизацию дуги, надежную защиту расплавленного металла сварочной ванны от воздействия внешней среды, раскислять и легировать металл шва.
Требования, предъявляемые к электродам для сварки углеродистых и легированных конструкционных сталей, содержатся в ГОСТ 9467—75, а для высоколегированных — в ГОСТ 10052—75. Правила приема и методы испытания электродов предусмотрены ГОСТ 9466—75.
При ручной сварке используют электроды, которые подразделяются на четыре группы в зависимости от отношения диаметра D электрода с покрытием к диаметру d металлического стержня: М — с тонким покрытием (D/ d ≤ 1,20), С — со средним покрытием (1,20< D/ d ≤1,45), Д—с толстым покрытием (1,45 < D/d ≤1,80), Г — с особо толстым покрытием (1,45< D/ d ≤1,80).
Электроды для сварки и наплавки разделяют на пять групп: У — для сварки углеродистых и легированных конструкционных сталей; Л — для сварки легированных и конструкционных сталей с временным сопротивлением разрыву свыше 60 кгс/мм2; Т — для сварки легированных теплоустойчивых сталей; В — для сварки высоколегированных с особыми свойствами; Н — для наплавки поверхностных слоев с особыми свойствами.
Электроды для сварки углеродистых и легированных конструк-ционных сталей классифицируют по механическим характеристикам металла шва и сварного соединения; электроды для сварки легированных теплоустойчивых сталей классифицируют по механическим характеристикам металла шва и сварного соединения и по химическому составу металла шва. Первая группа содержит 14 типов электродов с Э-38 по Э-150. Здесь буква Э — электрод для электродуговой сварки, а следующая за буквой цифра показывает минимально гарантируемый предел прочности металла шва (в кгс/мм2). К одному типу электрода могут быть отнесены одна или несколько марок электродов. Так, к электроду типа Э-42 относятся электроды марок АНО-1, ОЗС-3, УОНИ-13/45 и др.
Согласно ГОСТ 9467—75 предусмотрены следующие основные виды покрытий: А—кислое; Б — основное; Ц—целлюлозное; Р — рутиловое; П — прочие виды; при покрытии смешанного вида используют соответствующее двойное обозначение.
Кислые покрытия А на основе железных или марганцевых руд. При использовании электродов с руднокислыми покрытиями металл шва содержит больше кислорода, азота и водорода, чем при использовании покрытия другого типа. Этим объясняется повышенная склонность металла шва к «старению», т. е. к снижению вязкости и сопротивления удару в процессе эксплуатации. Этот вид покрытий применяют для сварки малоуглеродистых сталей. Типичными электродами этой группы являются электроды ОММ-5 и ЦМ-7.
Рутиловые покрытия Р содержат большое количество рутила TiO2.
Это соединение титана с кислородом очень устойчиво в плавильном пространстве дуги и не насыщает металла шва кислородом и азотом в такой степени, как электроды с руднокислым покрытием. К рутиловым электродам относят электроды ОЗС-3, МР-3 и др.
Фтористокальциевые покрытия содержат в основе мрамор СаСО3 и плавиковый шпат CaF2, которые являются шлакообразующими компонентами покрытия этого типа электродов. В плавильном пространстве дуги мрамор распадается на оксид кальция и оксид углерода (IV), которые создают надежную газовую защиту плавильного пространства.
Плавиковый шпат при высоких температурах частично распадается и выделяет фтор, который, соединяясь с водородом сварочной ванны, очищает металл шва от водорода. Фтористокальциевые покрытия позволяют легировать металл шва в широких пределах и обеспечивают получение металла с высокими прочностными свойствами и высокой ударной вязкостью. К этой группе относят электроды УОНИ-13, УП-1/45, УП-2/45. Сварка электродами этого типа проводится преимущественно постоянным током обратной полярности. Электроды с фтористокальциевым покрытием применяют для сварки конструкционных, нержавеющих, окалиностойких, жаропрочных и других специальных сталей.
Целлюлозные покрытия Ц содержат значительное количество органических соединений (до 50—60 %). Эти соединения, сгорая, выделяют СО2, Н2 и другие вещества, защищающие плавильное пространство дуги. В качестве газообразующего вещества в этих покрытиях используется электродная целлюлоза. К электродам этого типа относят электроды ВСНБ; ОЗЦ-1 и др.
Требования, предъявляемые к электродам для сварки высоколегированных сталей с особыми свойствами, содержатся в ГОСТ 10052—75. Он регламентирует следующие свойства наплавленного металла: химический состав, механические свойства, содержание ферритной фазы и стойкость против межкристаллитной коррозии. Эти электроды изготавливают только с покрытием типа Ф. Сварка производится постоянным током обратной полярности на минимально короткой дуге и на пониженной погонной энергии.
|
|
Таксономические единицы (категории) растений: Каждая система классификации состоит из определённых соподчиненных друг другу...
Особенности сооружения опор в сложных условиях: Сооружение ВЛ в районах с суровыми климатическими и тяжелыми геологическими условиями...
История создания датчика движения: Первый прибор для обнаружения движения был изобретен немецким физиком Генрихом Герцем...
Общие условия выбора системы дренажа: Система дренажа выбирается в зависимости от характера защищаемого...
© cyberpedia.su 2017-2024 - Не является автором материалов. Исключительное право сохранено за автором текста.
Если вы не хотите, чтобы данный материал был у нас на сайте, перейдите по ссылке: Нарушение авторских прав. Мы поможем в написании вашей работы!