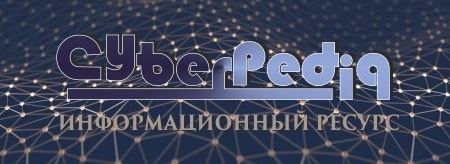
Кормораздатчик мобильный электрифицированный: схема и процесс работы устройства...
Механическое удерживание земляных масс: Механическое удерживание земляных масс на склоне обеспечивают контрфорсными сооружениями различных конструкций...
Топ:
Организация стока поверхностных вод: Наибольшее количество влаги на земном шаре испаряется с поверхности морей и океанов...
Характеристика АТП и сварочно-жестяницкого участка: Транспорт в настоящее время является одной из важнейших отраслей народного хозяйства...
История развития методов оптимизации: теорема Куна-Таккера, метод Лагранжа, роль выпуклости в оптимизации...
Интересное:
Инженерная защита территорий, зданий и сооружений от опасных геологических процессов: Изучение оползневых явлений, оценка устойчивости склонов и проектирование противооползневых сооружений — актуальнейшие задачи, стоящие перед отечественными...
Принципы управления денежными потоками: одним из методов контроля за состоянием денежной наличности является...
Лечение прогрессирующих форм рака: Одним из наиболее важных достижений экспериментальной химиотерапии опухолей, начатой в 60-х и реализованной в 70-х годах, является...
Дисциплины:
![]() |
![]() |
5.00
из
|
Заказать работу |
|
|
Исходные данные: передаточное число и, межосевое расстояние а.
1. Число витков (заходов) червяка z 1определяем в зависимости от u по рекомендации:
и...8...16 16...32 32...80
z1....4 2 1
2. Из формулы и = определяем число зубьев червячного колеса z2, округляя полученное значение до ближайшего целого числа. Уточняем значениепередаточногочисла и.
3. Выбираем коэффициент диаметра червяка q по рекомендации:
q = 0,25 · z2, принимая стандартное значение из ряда 6,3; 8; 10; 12,5; 16; 20.
4. Определяем модуль m из формулы:
Принимаем для модуля стандартное значение (мм) из ряда:
2; 2,5; 3,15; 4; 5; 6,3; 8; 10; 12,5; 16; 20.
5. Определяем основные геометрические параметры зацепления:
а) осевой шаг червяка и окружной шаг колеса р = π · т;
б) высота головки витка червяка и зуба колеса ha = т,
в)высота ножки витка червяка и зуба колеса hf = 1,2 · т.
6. Определяем основные геометрические размеры червяка:
а) делительный диаметр d 1 = m·q;
б) диаметр вершин витков da 1 = d 1 + 2 · ha;
в) диаметр впадин df 1 = d 1 – 2 · hf -;
г)угол подъема линии витка tgγ = ;
д)длина нарезанной части червяка b 1 = m · (11 + 0,06 · z2).
7. Определяем основные геометрические размеры червячного колеса:
а) делительный диаметр d2 = m · z2;
б)диаметр вершин зубьев: da 2= d 2 +2 · ha;
в) диаметр впадин: df 2 = d2 - 2 · hf;
г) наружный диаметр колеса: ae 2 =
+
д) ширина зубчатого венца колеса: b2 = 0,75 · da 1
8. Уточняем межосевое расстояние: a = .
В п.5, 6, 7 и 8 вычисления следует вести с точностью до второго знака после запятой, за исключением размеров b1, b2 и dae2, которые округляют до ближайшего целого числа.
Пример решения задачи
Исходные данные: а ω=220 мм, u =30.
|
Решение
1. Число витков (заходов) червяка z 1определяем в зависимости от u по рекомендации:
z1=2.
2. Из формулы и = определяем число зубьев червячного колеса z2, округляя полученное значение до ближайшего целого числа. Уточняем значение передаточного числа и.
z2 =2 · 30 = 60.
3. Выбираем коэффициент диаметра червяка q по рекомендации:
q = 0,25 · 60 = 15.
4.Определяем модуль m из формулы:
m = = 5,87 мм, принимаем m=6,3 мм.
5. Определяем основные геометрические параметры зацепления:
р = 3,14 ∙6,3 = 19,78 мм; ha = 6,3 мм;
hf = 1,2 · 6,3 = 7,56 мм.
6. Определяем основные геометрические размеры червяка:
d 1=6,3 ·15 = 94,5 мм;
dal =94,5 + 2 · 6,3 = 107,1 мм;
df 1 = 94,5 - 2 · 7,56 = 79,38 мм;
tgγ = = 0,133, отсюда γ = 7,58°;
b 1 = 6,3 · (11 + 0,06 · 60) = 91,98 мм, принимаем b 1= 92 мм.
7. Определяем основные геометрические размеры червячного колеса:
d 2 = 6,3 · 60 = 378 мм;
da 2 = 378 + 2 · 6,3 = 390,6 мм;
df 2= 378 - 2 · 7,56 = 362,88 мм;
ae 2 =
+
= 400,05 мм, принимаем dae 2 =400 мм;
b2 =0,75 ·107,1 = 80,3 мм, принимаем b 2 = 80 мм.
8. Уточняем межосевое расстояние:
аω = =236,25 мм.
Содержание отчета
1. Титульный лист в соответствии СТП 1.2-2005
2. Цель работы
3. Задание
4. Определение геометрических параметров передач
5. Ответы на контрольные вопросы
6. Вывод
Контрольные вопросы:
1. В каких случаях целесообразно применять червячную передачу?
2. Охарактеризуйте самотормозящую червячную передачу
3. Какие передачи прямозубые или непрямозубые, предпочтительнее применять при высоких скоростях и почему?
4. Почему не рекомендуется принимать число зубьев шестерни менее 17?
5. Почему рекомендуется принимать для шестерни материал лучшего качества, чем для колеса?
Практическая работа № 11
Тема: Подбор подшипников качения по динамической грузоподъемности
Цель работы: научиться подбирать подшипники качения по динамической грузоподъемности
Задание:
1. Для вала редуктора подобрать подшипники качения. Нагрузка нереверсивная, спокойная. Рабочая температура подшипникового узла не должна превышать 650С. Ресурс подшипника =12
103. Исходные данные взять из таблицы 1 согласно номера в журнале
|
2. Зарисовать схему подшипникового узла
3. Письменно ответить на контрольные вопросы
4. Сделать вывод
Таблица 1
Исходные данные
Номер варианта | Величина осевой нагрузки, | Реакция опор | Диаметр вала вместе посадки подшипников, d, мм | Угловая скорость вала, w, рад/с | ||
RAY | RBY | RAX=RBX | ||||
1 | 325 | 124 | 691 | 1105 | 35 | 20 |
2 | 541 | 11 | 1284 | 1750 | 40 | 18 |
3 | 1620 | -356 | 4508 | 5599 | 65 | 8 |
4 | 242 | -15 | 574 | 797 | 30 | 36 |
5 | 298 | 56 | 802 | 1154 | 30 | 26 |
6 | 401 | 380 | 844 | 1376 | 35 | 10 |
7 | 483 | -194 | 1233 | 1640 | 30 | 15,8 |
8 | 495 | -18 | 1207 | 1598 | 30 | 13,9 |
9 | 451 | -148 | 652 | 1802 | 30 | 11,52 |
10 | 407 | 9 | 950 | 1389 | 35 | 24,7 |
11 | 325 | 124 | 691 | 1105 | 40 | 26 |
12 | 541 | 11 | 1284 | 1750 | 60 | 26 |
13 | 1620 | -356 | 4508 | 5599 | 40 | 36 |
14 | 242 | -15 | 574 | 797 | 65 | 20 |
15 | 298 | 56 | 802 | 1154 | 35 | 18 |
16 | 401 | 380 | 844 | 1376 | 40 | 11,52 |
17 | 483 | -194 | 1233 | 1640 | 45 | 24,7 |
18 | 495 | -18 | 1207 | 1598 | 50 | 40 |
19 | 451 | -148 | 652 | 1802 | 55 | 40 |
20 | 407 | 9 | 950 | 1389 | 60 | 36 |
21 | 325 | 124 | 691 | 1105 | 35 | 26 |
22 | 541 | 11 | 1284 | 1750 | 45 | 25 |
23 | 1620 | -356 | 4508 | 5599 | 65 | 30 |
24 | 242 | -15 | 574 | 797 | 65 | 11,52 |
25 | 298 | 56 | 802 | 1154 | 50 | 18 |
26 | 401 | 380 | 844 | 1376 | 45 | 36 |
27 | 483 | -194 | 1233 | 1640 | 35 | 26 |
28 | 495 | -18 | 1207 | 1598 | 45 | 40 |
29 | 451 | -148 | 652 | 1802 | 45 | 13,9 |
30 | 407 | 9 | 950 | 1389 | 65 | 40 |
Пояснения к работе
Подш и пник кач е ния, опора вращающейся части механизма или машины, работающая в условиях преобладающего трения качения.Подшипники качения (рис.1) обычно состоят из двух колец: внутреннего 3, насаженного на вал, и наружного1, закрепленного в корпусе подшипника; тел качения – шариков или роликов 2, катящихся по беговым дорожкам колец на некотором расстоянии друг от друга, и сепаратора 4, разделяющего тела качения и направляющего их движение.
Рисунок – 1 Конструкция подшипника качения
Классификация подшипников качения осуществляется по следующим признакам:
Ø по направлению воспринимаемой нагрузки;
Ø по форме тел качения;
Ø по числу рядов тел качения;
Ø по способу самоустановки.
На подшипнике качения ставят клеймо – условное обозначение подшипника, состоящее из ряда цифр и букв. Последние две цифры указывают шифр диаметра внутреннего кольца подшипника: …00-d=10мм; …01-d=12мм; …02-d=15мм; …03-d=17мм; и т.д. Начиная от …04(d=20мм) и кончая …99(d=495мм) для получения размера диаметра внутреннего кольца подшипника в миллиметрах необходимо две последние цифры его условного обозначения умножить на 5.
|
Третья цифра справа условного обозначения указывает на серию подшипника: особо легкая – 1; легкая – 2; средняя – 3; тяжелая – 4 и т.д.
Четвертая цифра справа обозначает тип подшипника: радиальный шариковый однорядный – 0 (если левее 0 нет цифр, то 0 не указывают), радиальный шариковый двухрядный – 1;…., роликовый конический (радиально-упорный) -7; упорный шариковый – 8 и т.д.
Пятая и шестая цифры справа условного обозначения характеризуют конструктивные особенности подшипника – с закрепительной втулкой, неразборный, с защитной шайбой и.д.
Седьмая цифра справа характеризует серию подшипника по ширине – нормальная, узкая, широкая.
Класс точности маркируется слева от условного обозначения подшипника.
Кольца и тела качения изготовляют из шарикоподшипниковой стали с высоким содержанием хрома (ШХ4, ШХ6, ШХ15, ШХ15ГС) и других легированных сталей, например 12Х2Н4А. Сепараторы изготовляют из сталей Ст1; Ст2; 08; 10, а также из латуни, бронзы, капрона, текстолита.
Смазка подшипников
Для смазки подшипников применяются жидкие (И-40А-насосы, двигатели, компрессоры, зубчатые передачи; И-70А, И-50А-машины с большими нагрузками, зубчатые и червячные редукторы) или пластичные (солидол марок С, УС-2; ЦИАТИМ 201, 202) смазочные материалы. Вода применяется для смазки подшипников скольжения с вкладышами из пластмасс, дерева, резины. Графит, слюда и некоторые другие твердые смазочные материалы применяют в подшипниках и материалах тогда, когда по условиям производства нельзя использовать жидкую или пластичную смазку(пищевые машины, ткацкие станки и др.). В некоторых подшипниках скольжения быстроходных и малонагруженных валов применяют газовую смазку.
Периодическое смазывание жидким смазочным материалом без принудительного давления осуществляют с помощью масленок с поворотной или шариковой крышкой. Заправку этих масленок маслом выполняют масленками- лейками и шприцами. Применяют их в механизмах, работающих периодически при малых скоростях и нагрузках.
Непрерывное смазывание без принудительного давления осуществляют с помощью фитильной и капельной масленки с регулировочно-запорной иглой и вращающимся кольцом. Фитильная масленка обеспечивает непрерывную передачу и фильтрацию масла фитилем даже при невращающейся цапфе(недостаток). Капельная масленка перемещением иглы позволяет регулировать смазку, а при остановке машины – прекратить подачу масла.
|
Периодическое смазывание пластичными смазочными материалами осуществляют: колпачковыми масленками; пресс-масленки.
Непрерывное смазывание пластичными смазочным материалом производят с помощью автоматически действующих масленок, в которые мазь подается поршнем, находящихся под действием пружины.
Смазку поверхностей трения жидкими или пластичными смазочными материалами можно осуществлять под давлением. Смазка подшипников качения жидкими смазочными материалами обычно осуществляется путем разбрызгивания масла зубчатыми колесами, окунающимися в масляную ванну, или брызговиками. Внутри корпуса редуктора создается масляные туман, и капли масла непрерывно падают в подшипники, обеспечивая их смазку. В некоторых ответственных масляных ванн, уровень масла которых должен быть выше центра нижнего шарика или ролика.
При смазке подшипников качения пластичными смазочными материалами их набивают при сборке в подшипниковую камеру, а через 6…10 месяцев промывают подшипник и камеру и закладывают свежую порцию смазочного материала. Иногда устанавливают пресс-масленки, позволяющие пополнять смазочные материал в период между разборкой или промывкой сборочной единицы.
Как при жидкостной, так и при полужидкостной смазке подшипниковый узел должен быть надежно изолирован от внешней среды, чтобы смазочный материал не вытекал и в подшипник не попадали грязь и пыль. Жидкостная смазка более эффектна. Она существенно уменьшает потери на трение и износ, способствует отводу теплоты от подшипника.Для ограничения попадания в подшипниковую камеру жидкого масла из корпуса редуктора применяют специальные вращающиеся шайбы или маслосбрасывающие кольца.
При смазке пластичными смазочными материалами подшипники надо изолировать не только от внешней среды, но и от внутренней плоскости корпуса редуктора, в противном случае содержащееся в корпусе жидкое масло вымывает густую смазку из подшипниковой камеры. С этой целью применяют мазеудерживающие кольца, специальные кольца из стали и нейлона, пластмассовые или металлические неподвижные шайбы.
|
|
Семя – орган полового размножения и расселения растений: наружи у семян имеется плотный покров – кожура...
Особенности сооружения опор в сложных условиях: Сооружение ВЛ в районах с суровыми климатическими и тяжелыми геологическими условиями...
Организация стока поверхностных вод: Наибольшее количество влаги на земном шаре испаряется с поверхности морей и океанов (88‰)...
Поперечные профили набережных и береговой полосы: На городских территориях берегоукрепление проектируют с учетом технических и экономических требований, но особое значение придают эстетическим...
© cyberpedia.su 2017-2024 - Не является автором материалов. Исключительное право сохранено за автором текста.
Если вы не хотите, чтобы данный материал был у нас на сайте, перейдите по ссылке: Нарушение авторских прав. Мы поможем в написании вашей работы!