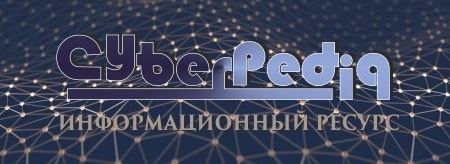
Индивидуальные очистные сооружения: К классу индивидуальных очистных сооружений относят сооружения, пропускная способность которых...
Историки об Елизавете Петровне: Елизавета попала между двумя встречными культурными течениями, воспитывалась среди новых европейских веяний и преданий...
Топ:
Методика измерений сопротивления растеканию тока анодного заземления: Анодный заземлитель (анод) – проводник, погруженный в электролитическую среду (грунт, раствор электролита) и подключенный к положительному...
Особенности труда и отдыха в условиях низких температур: К работам при низких температурах на открытом воздухе и в не отапливаемых помещениях допускаются лица не моложе 18 лет, прошедшие...
Интересное:
Как мы говорим и как мы слушаем: общение можно сравнить с огромным зонтиком, под которым скрыто все...
Мероприятия для защиты от морозного пучения грунтов: Инженерная защита от морозного (криогенного) пучения грунтов необходима для легких малоэтажных зданий и других сооружений...
Финансовый рынок и его значение в управлении денежными потоками на современном этапе: любому предприятию для расширения производства и увеличения прибыли нужны...
Дисциплины:
![]() |
![]() |
5.00
из
|
Заказать работу |
|
|
Плазменное напыление. Параметры режимов плазменного напыления и их влияние на эффективность процесса.
Температура плазменной струи зависит от силы тока, вида и расхода газа и изменяется от 10000 до 30 000 °С; скорость истечения газов 100—1500 м/с. Аргонная плазма имеет температуру 15 000—30 000 °С, азотная — 10000—15000 °С.
Формирование плазменного покрытия на рабочей поверхности деталей обусловлено влиянием многих параметров процесса напыления, к основным из которых относятся дистанция напыления, ток, напряжение дуги, расход порошкового материала, плазмообразующего и транспортирующего газов, скорость перемещения пятна напыления по поверхности детали и др. Параметры режима регулируются непосредственно оператором. С увеличением мощности дуги в дуговых плазмотронах интенсивно возрастает температура, и энтальпия плазменной струи как на срезе сопла, так и в других ее сечениях. Влияние другого важного параметра – расхода плазмообразующего газа противоположное. Мощность дуги определяется, в свою очередь, двумя параметрами: величиной тока и напряжения. Напряжение дуги зависит от ее длины, которая в основном определяется конструкцией распылителя, а также родом и частично расходом плазмообразующего газа. Расход плазмообразующего газа оказывает большое влияние на эффективность процесса напыления. С увеличением расхода возрастает распыляющая способность плазменной струи, ее скорость и, соответственно, скорость напыляемых частиц. Первоначально снижение невелико, повышение скорости частиц при этом оказывается положительным, и в целом эффективность процесса достаточно высока. При возрастании расхода плазмообразующего газа выше оптимальных значений существенно уменьшается плотность покрытий, КИП и другие показатели эффективности.
|
Плазменное напыление. Напыляемые материалы и свойства получаемых покрытий.
При плазменной металлизации в качестве наносимого материала применяют гранулированный порошок с размером частиц 50— 200 мкм. Порошок подается в зону дуги транспортирующим газом (азотом), расплавляется и переносится на деталь. Скорость полета частиц порошка 150—200 м/с, расстояние от сопла до поверхности детали 50—80 мм.
Для плазменного напыления используют проволоку, в том числе порошкового типа, порошки из черных и цветных металлов, никеля, молибдена, хрома, меди, оксиды металлов, карбиды металлов и их композиции с никелем и кобальтом, сплавы металлов, композиционные материалы (никель-графит, никель-алюминий и др.) и механические смеси металлов, сплавов и карбидов. Регулирование режима напыления позволяет наносить как тугоплавкие материалы, так и легкоплавкие. Основой для плазменного напыления могут служить металлы и неметаллы (пластмасса, кирпич, бетон, графит и др.). Для нанесения покрытий на небольшие поверхности применяется микроплазменный способ напыления, который позволяет сэкономить потери напыляемого материала (ширина напыления 1-3 мм).
Электродуговая металлизация. Электрический дуговой разряд как источник энергии.
Питание дуги может осуществляться переменным или постоянным током. При использовании постоянного тока дуга горит непрерывно и устойчиво, поэтому по сравнению с переменным током процесс плавления более стабильный, обеспечивается высокая дисперсность частиц наносимого металла и плотность создаваемых ими покрытий. Типовые значения параметров ра - боты ЭДМ: напряжение 24...35 В, ток 75...200 А, производительность 30.300 г/мин, давление сжатого воздуха 5 атм.
Электродуговая металлизация. Механизмы плавления и распыления электродов.
Электрическая дуга возбуждается между двумя электродными проволоками 5, которые изолированы одна от другой и равномерно подаются роликовыми механизмами 4 со скоростью 0,6—1,5 м/мин через направляющие наконечники 2. Если проволоки изготовлены из разных материалов, то материал покрытия представляет собой их сплав. Расстояние от сопла до детали составляет 80—100 мм.
|
Одновременно по воздушному соплу 3 в зону дуги поступает сжатый воздух или инертный газ под давлением 0,4—0,6 МПа, который распыляет расплавленный металл и переносит его на поверхность детали 1.
Взрывное испарение-распыление. Оборудование для нанесения.
Триодная.
Стремление повысить степень ионизации рабочего газа в тлеющем разряде и тем самым увеличить количество бомбардирующих ионов способствовало созданию трёхэлектродной схемы процесса (рисунок 5.8, б). Горячий катод 7 представляет дополнительный источник электронов. Для возбуждения разряда между горячим катодом и анодом 6 прикладывают высокое напряжение (1,0–2,0 кВ). Наибольшая эффективность ионизации газа достигается за счёт придания электронам сложного движения с помощью магнитной катушки 8. Магнитное поле, воздействуя на тлеющий разряд, изменяет главным образом характер движения электронов. На более тяжелые ионы магнитное поле воздействует слабо. Величину магнитного поля выбирают с учётом существенного изменения траектории электрона минимального искривления траектории иона. В основном применяют продольное магнитное поле, параллельное электрическому полю. Под воздействием магнитного поля электроны совершают более сложные движения вокруг магнитных линий, например по спирали. Возрастает эффективная длина пути электронов и, следовательно, увеличивается степень ионизации рабочего газа.
Вспомогательный катод, анод и магнитная катушка составляют генератор плазмы, независимо от распыляемого материала и обрабатываемого изделия. Изделие для нанесения покрытия располагаю вблизи плазмы или погружают в нее. Напряжение, подаваемое на распыляемый материал (холодный катод), мало влияет на разряд между горячим катодом и анодом, образующим плазму, что позволяете регулировать ускоряющее напряжение, не прибегая к высоким его значениям. Допускается большая гибкость в выборе формы и положения распыляемого катода.
На распыляемый материал (холодный катод) подается отрицательный потенциал 0,7–1,0 кВ. Создаются условия ускорения ионов из 1 области горячего катода в направлении распыляемого материала. На изделие подается отрицательный потенциал, что предотвращает движение электронов к поверхности конденсации и снижает опасность перегрева изделия. Триодная схема процесса распыления катода в значительной мере устраняет недостатки, присущие диодной схеме. Процесс ведут при более низких давлениях рабочего газа (10-1 Па и ниже). Производительность распыления возрастает в несколько раз.
|
Магнетронная.
Дальнейшее повышение плотности ионного потока, а следовательно и скорости распыления, обеспечивают магнетронные системы (см. рисунок 5.8, в). Под распыляемым материалом (катодом) 1 располагают магниты 9.
Силовые линии в виде дуг замыкаются между полосами N–S, образуя неоднородное магнитное поле. Над катодом помещают кольцевой анод 6. При подаче постоянного напряжения (300–1000 В) между катодом и анодом возникает электрическое поле напряженностью Е и возбуждается тлеющий разряд. Силовые линии электрического поля пересекаются с магнитными силовыми линиями.
Электроны, эмитируемые катодом, под воздействием скрещенных полей движутся по циклоидальным траекториям. В плоскости, параллельной плоскости катода, образуется область замкнутого дрейфа электронов. При движении электроны испытывают многократные соударения с атомами рабочего газа и ионизируют их; потерявшие большую часть своей энергии электроны попадают на анод. Сложное, замкнутое движение электронов и обусловливает возрастание концентрации бомбардирующих ионов вблизи распыляемого материала. Зона интенсивного распыления поверхности имеет вид замкнутой дорожки, размеры и форма которой определяются геометрией магнитной системы.
В кольцеобразной зоне степень ионизации рабочего газа приближается к 100 %, что позволяет получать высокие плотности ионного тока (10–20 мА/см2). Благодаря высоким плотностям тока скорость распыления приближается к скоростям при электронно-лучевом термическом испарении или взрывном испарении-распылении катода дугой низкого давления. Предельная скорость распыления определяется теплопроводностью распыляемого материала и условиями его охлаждения. Водяное охлаждение материала катода предотвращает её высокий нагрев и оплавление. Магнетронные системы с различными пространственными формами мишени позволяют наносить покрытия на сложные поверхности изделий, например наружные или внутренние цилиндрические.
|
Подготовка поверхности упрочняемых изделий: механическая, химическая вакуумная.
К физическим (механическим) способам подготовки поверхности под склеивание относятся абразивная обработка струйными методами и зачистка поверхностей шлифовальными шкурками. При выборе метода подготовки поверхности необходимо учитывать габариты технического средства, вид материала, используемого для получения покрытия, техническое оснащение предприятия и экономическую целесообразность применения коррозионной защиты.
Для удаления с защищаемой поверхности ржавчины и окалины и придания ей шероховатости используются методы химического и электрохимического травления в растворах минеральных и органических кислот и их смесей.
Поверхности, используемые для вакуумных видов применения, должны подготавливаться таким образом, чтобы они не вызывали загрязнение в системе.
Металлы.
В зависимости от своего химического состава присадочные материалы обеспечивают формирование на поверхности детали следующих покрытий:
Износостойкие покрытия, обеспечивающие более длительную работу деталей в рабочих условиях, на основе:
-сталей и сплавов на железной основе,
-композиционных материалов;
Коррозионностойкие покрытия, обеспечивающие стойкость поверхности детали при работе в активных средах, на основе:
-высоколегированных сталей,
-цветных металлов и сплавов на их основе;
Технологические покрытия, обеспечивающие защиту поверхности деталей при технологическом переделе;
Конструкционные покрытия, с помощью которых восстанавливаются размер и форма детали.
Для восстановления изношенных поверхностей напылением и напылением с оплавлением широкое применение получили порошковые самофлюсующиеся сплавы системы Ni-Cr-В-Si, в которые нередко добавляют карбиды, бориды тугоплавких металлов (вольфрам, ванадий, хром, молибден) для образования композиционных сплавов с более высокими физико-механическими свойствами.
Для напыления, в основном, применяют проволоку из сталей Ст3; У 7; 40Х; 50ХФА и др. Однокомпонентные порошки содержат частицы, полученные из одного металла (алюминия, титана, молибдена и др.) или сплава (Ре-С; Ni-Al; W-С; Ni-Cr; Ni-Cr-B-Si и др.). Структура частиц может быть как гомогенной, так и гетерогенной. Обычно однокомпонентные порошки получают: механическим измельчением, которое предпочтительно для хрупких материалов (Si, Cr, Mn, ферросплавов);
|
Твердые сплавы различают по металлам карбидов вольфрама — ВК2, ВК3,ВК3М, ВК4В, ВК6М, ВК6, ВК6В, ВК8, ВК8В, ВК10 и др. Они обозначаются буквами ВК и цифрой, показывающей содержание кобальта. Например, твёрдый сплав ВК3 содержит около 3% кобальта и 97% карбида вольфрама.
По химическому составу твердые сплавы классифицируют:
вольфрамокобальтовые твердые сплавы (ВК);
титановольфрамокобальтовые твердые сплавы (ТК);
титанотанталовольфрамокобальтовые твердые сплавы (ТТК)
Титановольфрамовые сплавы (группа ТК) - двухкарбидные. В их состав входят карбид титана, карбид вольфрама и связка - кобальт. В условном обозначении цифра, стоящая после буквы Т, показывает процентное содержание карбидов титана, после буквы К — кобальта, остальное — карбиды вольфрама.
Композиционный износостойкий материал на основе сверх высокомолекулярного полиэтилена дополнительно содержит 4 мас.% нано дисперсного модификатора, в качестве которого использован или карбосил, или оксид вольфрама WO3, или карбид кремния SiC, или оксид алюминия Аl2О3. Получают композиционный материал, обладающий морозоустойчивостью, высокой стойкостью к истиранию.
Одним из распространенных способов защиты металлов от корро-зии являются металлические покрытия. Они делятся на анодные и ка-тодные.
К анодным покрытиям относятся покрытия металлами, например, цинком, кадмием, имеющими потенциал более электроотрицательный, чем потенциал основного металла. В этом случае, например сталь, защищается от коррозии не только механически, но и электрохимически, так как, являясь анодом, покрытие корродирует, анодно поляризуется и тем защищает открытые участки стали.
К катодным покрытиям относятся покрытия металлами, напри-мер, свинцом, оловом, никелем, медью, имеющими более электропо-ложительный потенциал, чем основной металл. В этом случае разру-шение, например, стали, покрытой никелем, будет происходить только при нарушении покрытия или его пористости из-за возникновения кор-розионного гальванического элемента (во влажном воздухе).
КОГЕЗИЯ – (от лат. cohaesus — связанный, сцепленный), сцепление друг с другом частей одного и того же тела, обусловленное действием сил межмолекулярного взаимодействия.
АДГЕЗИЯ – (от лат. adhaesio — прилипание), возникновение связи между поверхностными слоями двух разнородных (твёрдых или жидких) тел (фаз), приведённых в соприкосновение.
Строение структура и эксплуатационные свойства покрытий.
Классифицированные по назначению.
Защитные покрытия – основное назначение связано с их разнообразными защитными функциями. Большое распространение получили коррозионностойкие, жаростойкие и износостойкие покрытия. Широко применяются также теплозащитные, электроизоляционные и отражающие покрытия.
Конструкционные покрытия и пленки – выполняют роль конструктивных элементов в изделиях. Особенно широко также используются при производстве изделий в приборостроении, радиоэлектронной аппаратуры, интегральных схем, в турбореактивных двигателях - в виде срабатываемых уплотнений в турбине и компрессоре и др.
Технологические покрытия – предназначаются для облегчения технологических процессов при производстве изделий. Например, нанесение припоев при пайке сложных конструкций; производстве полуфабрикатов в процессе высокотемпературного деформирования; сварке разнородных материалов и т.д.
Декоративные покрытия – исключительно широко применяются при производстве бытовых изделий, украшений, повышении эстетичности промышленных установок и приборов, протезировании в медицинской технике и др.
Восстановительные покрытия – дают огромный экономический эффект при восстановлении изношенных поверхностей изделий, например гребных валов в судостроении; шеек коленчатых валов двигателей внутреннего сгорания; лопаток в турбинных двигателях; различного режущего и прессового инструмента.
Оптические покрытия – уменьшают отражательную способность по сравнению с массивными материалами, в основном, благодаря геометрии поверхности. Профилеметрирование показывает, что поверхность некоторых покрытий представляет собой совокупность шероховатостей, высота которых колеблется от 8 до 15 мкм. На отдельных макронеровностях формируются микронеровности, высота которых колеблется от 0,1 до 2 мкм. Таким образом, высота неровностей соизмерима с длиной волны падающего излучения.
Отражение света от такой поверхности происходит в соответствии с законом Френкеля.
В литературных источниках встречаются различные принципы классификации методов нанесения покрытий. Хотя следует отметить, что единой системы классификации методов нанесения покрытий нет.
Хокинг и ряд других исследователей предложили три классификации методов нанесения покрытий:
1. По фазовому состоянию среды, из которой происходит осаждение материала покрытия;
2. По состоянию наносимого материала;
3. По состоянию процессов, которые определяют одну группу методов нанесения покрытий.
Использование покрытий позволяет значительно повысить эксплуатационные характеристики изделий: износостойкость, коррозионостойкость, жаропрочность, жаростойкость и др.
3. Плазменное напыление. Плазмообразующие газы.
Плазменное напыление основано на использовании энергии плазменной струи как для нагрева, так и для переноса частиц металла. Плазменную струю получают путем продувания плазмообразующего газа сквозь электрическую дугу и обжатия стенками медного водоохлаждаемого сопла.
1 — порошковый дозатор; 2 — катод; 3 — изоляционная прокладка; 4 — анод; 5 — транспортирующий газ; 6 — охлаждающая жидкость; 7 — плазмообразующий газ.
Плазмообразующими газами служат азот, гелий, аргон, водород, их смеси и смесь воздуха с метаном, пропаном или бутаном.
|
|
Общие условия выбора системы дренажа: Система дренажа выбирается в зависимости от характера защищаемого...
Механическое удерживание земляных масс: Механическое удерживание земляных масс на склоне обеспечивают контрфорсными сооружениями различных конструкций...
Эмиссия газов от очистных сооружений канализации: В последние годы внимание мирового сообщества сосредоточено на экологических проблемах...
Состав сооружений: решетки и песколовки: Решетки – это первое устройство в схеме очистных сооружений. Они представляют...
© cyberpedia.su 2017-2024 - Не является автором материалов. Исключительное право сохранено за автором текста.
Если вы не хотите, чтобы данный материал был у нас на сайте, перейдите по ссылке: Нарушение авторских прав. Мы поможем в написании вашей работы!