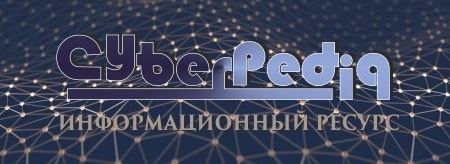
Папиллярные узоры пальцев рук - маркер спортивных способностей: дерматоглифические признаки формируются на 3-5 месяце беременности, не изменяются в течение жизни...
Механическое удерживание земляных масс: Механическое удерживание земляных масс на склоне обеспечивают контрфорсными сооружениями различных конструкций...
Топ:
Когда производится ограждение поезда, остановившегося на перегоне: Во всех случаях немедленно должно быть ограждено место препятствия для движения поездов на смежном пути двухпутного...
Особенности труда и отдыха в условиях низких температур: К работам при низких температурах на открытом воздухе и в не отапливаемых помещениях допускаются лица не моложе 18 лет, прошедшие...
Теоретическая значимость работы: Описание теоретической значимости (ценности) результатов исследования должно присутствовать во введении...
Интересное:
Что нужно делать при лейкемии: Прежде всего, необходимо выяснить, не страдаете ли вы каким-либо душевным недугом...
Распространение рака на другие отдаленные от желудка органы: Характерных симптомов рака желудка не существует. Выраженные симптомы появляются, когда опухоль...
Лечение прогрессирующих форм рака: Одним из наиболее важных достижений экспериментальной химиотерапии опухолей, начатой в 60-х и реализованной в 70-х годах, является...
Дисциплины:
![]() |
![]() |
5.00
из
|
Заказать работу |
|
|
Температурный режим
Температуру по зонам печи в зависимости от химического состава стали устанавливают по таблице 5 Температура по зонам печи в зависимости от химического состава стали (печь АОО).
Таблица 5 - Температура по зонам печи в зависимости от химического состава стали (печь АОО)
Номер тепловой зоны
Температура по зонам печи, °С
Примечание:
1. Для стали с содержанием серы ³ 0,020 мас.% устанавливают температурный режим №2.
2. Допустимое отклонение температуры ±25оС.
Газовый режим
В печь подают азотный защитный газ (АЗГ), содержащий 5,0-5,5% водорода, остальное – азот.
Пределы влажности атмосферы печи:
- 4-я, 5-я термические зоны печи – (5-13) г/м3;
- 9-я, 14-я термические зоны – (11-25) г/м3;
- 16-я термическая зона – (5-13) г/м3.
После простоя печи при выходе на температурно-газовый режим обезуглероживания, разрешается обработка металла при влажности в камере нагрева 5-14 г/м3, в камере выдержки 10-20 г/м3.
Указанную влажность обеспечивают следующими параметрами:
Общий расход АЗГ на печь - (570-680) м3/ч, в том числе:
- на камеру выдержки через скруббер № 1 - (10-30) м3/ч;
- на камеру выдержки через скруббер № 2 - (80-120) м3/ч;
- на камеру охлаждения – (480 – 560) м3/ч.
Допускается работа с отключенным 1-м скруббером. В этом случае расход АЗГ через 2-ой скруббер – (80-120) м3/ч.
Температура воды в увлажнителе газа УГ-1000 – не менее 40°С.
Температура газа после газоподогревателя не менее +50°С.
|
Давление в камерах печи – (1,8-3,8) мм водяного столба (17,6-37,3 Па).
Режим транспортировки
Скорость транспортировки полосы через печь устанавливают в соответствии с таблицей 6 Скорость транспортировки полосы через печь АОО с записью на диаграммную ленту.
Определение остаточного углерода и обработка стали по его результатам
5.4.3.1 Измерение содержания остаточного углерода производят в ГХИ ЦЗЛ руководствуясь требованиями РИ на приборе ELTRA CS-800. Для измерения содержания остаточного углеродатехнологический персонал ТУОРОпроизводит отбор двух проб в виде сегментов на неподвижной полосе вырубным штампом от кромки полосы из средней части (по длине) первого рулона стендовой партии. При наличии в стендовой партии рулонов нескольких плавок, дополнительно отбирают пробы от первого рулона каждой последующей плавки.
После простоя печи при выходе на температурно-газовый режим обезуглероживания от начала обработки стали до момента выхода агрегата на стационарный режим содержание углерода в металле определяют на каждом рулоне.
Таблица 6 - Скорость транспортировки полосы через печь АОО
Содержание углерода, мас. %, (по данным ЦЗЛ) |
Толщина полосы, мм
Скорость транспортировки м/мин, не более
Примечания:
1. Для стали с содержанием серы ³ 0,020 мас.% устанавливают скоростной режим № 2.
2. При наличии в стендовой партии рулонов с разным входным содержанием углерода максимальную скорость транспортировки для всех рулонов устанавливают по большему содержанию углерода.
Таблица 6 - продолжение
3. В случае получения Сост. ³ 0,0045 мас. %, снижают скорость по 1 м/мин и расход газа через скруббер по 5 м3/час. 4. При любом изменении режима (повышение или понижение скорости, и/или расхода газа) через 20-30 минут отбирают пробы на углерод с записью результатов измерений в информационной производственной системе и в паспорте стендовой партии. 5. При выходе из строя нагревателей одной или двух зон максимальную скорость транспортировки снижают на 1-2 м/мин. При перегорании более двух зон агрегат останавливают на ремонт. |
5.4.3.2 На стендовых партиях – «разведчиках» от 1, 3 и 5 рулонов отбирают пробы: для анализа содержания углерода - согласно п.5.4.3.1 настоящей инструкции; для моделирования - листы длиной 500-700 мм от конца указанных рулонов.
|
5.4.3.3 Содержание углерода в стали после обезуглероживания не должно превышать 0,0040 мас. % при назначении на конечные толщины 0,30, 0,35 0,50 мм, 0,0035 мас. % - на 0,27 мм, и 0,0030 мас. % - на 0,23 мм.
5.4.3.4 При получении на рулоне углерода больше указанной в п.5.4.3.3 настоящей инструкции величины, углерод измеряют на последующих рулонах стендовой партии до получения его регламентированного содержания. Рулоны с повышенным остаточным углеродом обрабатывают согласно п.5.4.3.5, п.5.4.3.6 настоящей инструкции.
5.4.3.5 При получении более 0,0035 и 0,0030 мас. % углерода на рулонах стендовой партии, назначенной на 0,27 и 0,23 мм соответственно:
- на одном рулоне – рулон продолжают обрабатывать в составе стендовой партии, а в паспорте делают отметку «повышенный углерод» – «С»;
- на двух и более рулонах - стендовую партию по заданию ПДО переводят на конечную толщину 0,30 мм. Обработку рулонов продолжают с учётом требований п.5.4.3.6 настоящей инструкции.
5.4.3.6 При получении повышенного остаточного углерода:
А) 0,0045-0,0080 мас. % - рулон продолжают обрабатывать в составе стендовой партии, а в паспорте делают отметку «повышенный углерод» – «С».
Б) более 0,0080 мас. % - от конца полосы в номинальной толщине + 0,03 мм отбирают две повторные пробы. При содержании в повторной пробе углерода £ 0,0080 мас. % - см. пункт А); при содержании более 0,0080 мас. % углерода рулон отделяют от стендовой партии с оформлением сборного паспорта согласно СТП СМК 48576703-7.5-003 (или переводят в состав существующего паспорта). Отделённые рулоны обрабатывают согласно указаниям ЦЗЛ.
Дополнительные указания
5.4.4.1 Рулон после обезуглероживающего отжига должен отвечать следующим требованиям:
- иметь обвязку и маркировку на внешнем витке;
|
- иметь ровную и плотную смотку, допускаются отдельные выступающие витки и плавная телескопичность - до 5 мм;
- эллипсность не допускается, контроль осуществляют визуально;
- места подмоток или сварных швов должны быть отмечены специальной закладкой или краской;
- не допускается наличие пятен от обезжиривающих растворов, окисления по железу до цветов побежалости от бурого до синего на поверхности полосы, ржавчины.
5.4.4.2 При горячих простоях более 5 минут в паспорте стендовой партии записывают время простоя с указанием номера рулона. При простое более 20-ти минут печь переводят на сухой защитный газ.
5.4.4.3 В переходные режимы (охлаждение и разогрев печи) в печь подают заправочный металл. В качестве заправочного металла используют окончательный брак электротехнической стали или углеродистую сталь толщиной (0,7-0,8) мм, или (с разрешения главного специалиста ЦХП (по производству)) электротехническую сталь из незавершенного производства.
Порядок отключения и разогрева АРО определен в ИЭ 48576703- 013-001, АОО – в ИЭ 48576703-013-002.
Вторая холодная прокатка
5.5.1 Вторую холодную прокатку производят на двадцативалковых станах «1200-1,2» на толщины (номинальная – задание САРТ в диапазоне):
- 0,50 мм – на 0,480 + 0,01 мм;
- 0,35 мм – на 0,340 + 0,01 мм;
- 0,30 мм – на 0,285 + 0,005 мм;
- 0,27 мм – на 0,255 + 0,005 мм;
- 0,23 мм – на 0,220 + 0,005 мм,
либо на стане кварто «1200-4» на толщины (номинальная – фактическая):
- 0,50 мм – на 0,480 ± 0,01 мм;
- 0,35 мм – на 0,340 ± 0,01 мм;
- 0,30 мм – на 0,290 ± 0,005 мм;
- 0,27 мм – на 0,260 ± 0,005 мм;
- 0,23 мм – на 0,225 ± 0,005 мм.
Режимы обжатий для станов «1200-1,2» приведены в таблице 7Режимы обжатий для станов «1200-1,2», для стана «1200-4» в таблице 8Режимы обжатий для стана «1200-4».
Таблица 7 - Режимы обжатий для станов «1200-1,2»
№ прохода (по толщинам) |
Толщина полосы, мм
Обжатие
Мм с 0,80 мм
Мм с 0,75 мм
Мм с 0,70 мм
Мм с 0,75 мм
Мм с 0,70 мм
|
Мм с 0,65 мм
Мм с 0,60 мм
Мм с 0,75 мм
Мм с 0,70 мм
Мм с 0,70 мм
Мм с 0,65 мм
Мм с 0,60 мм
Мм с 0,55 мм
Мм с 0,7 5 мм
Таблица 7 - продолжение
№ прохода (по толщинам) |
Толщина полосы, мм
Обжатие
Мм с 0,7 5 мм
Мм с 0,70 мм
Мм с 0,70 мм
Мм с 0,65 мм
Мм с 0,65 мм
Мм с 0,60 мм
Мм с 0,55 мм
Мм с 0,7 0 мм
Мм с 0,7 0 мм
Мм с 0, 65 мм
Мм с 0, 65 мм
Таблица 7 - продолжение
№ прохода (по толщинам) |
Толщина полосы, мм
Обжатие
Мм с 0,60 мм
Мм с 0,60 мм
Мм с 0,55 мм
Мм с 0,50 мм
Примечание:
1. Допускается перераспределение обжатий по проходам до 5%.
2. Натяжения при прокатке устанавливаются оператором стана на основании указанных диапазонов значений:
- для толщины 0,23 мм переднее натяжение 6,0-9,0 т, заднее натяжение 7,0-11,0 т.;
- для толщины 0,27 мм переднее натяжение 6,0-9,0 т, заднее натяжение 8,0-12,0 т.;
- для толщины 0,30 мм переднее натяжение 7,0-12,0 т, заднее натяжение 9,0-14,0 т.;
|
- для толщины 0,35 мм переднее натяжение 7,0-14,0 т, заднее натяжение 9,0-15,0 т.;
- для толщины 0,50 мм переднее натяжение 8,0-15,0 т, заднее натяжение 10,0-16,0 т.;
3. Скорость прокатки не более 5 м/сек.
Таблица 8 - Режимы обжатий для стана «1200-4»
№ |
Прохода
Толщина полосы, мм
Обжатие
Абсолютное натяжение
0,23 мм с 0,65 мм**
0,27 мм с 0,70 мм*
Таблица 8 - продолжение
№ |
Прохода
Толщина полосы, мм
Обжатие
Абсолютное натяжение
После
Прохода
Суммарное,
%
Переднее,
т
0,27 мм с 0,70 мм**
0,700
38,6
38,6
0,430
39,5
62,9
0,27 мм с 0,70 мм**
0,700
62,9
62,9
0,30 мм с 0,70 мм*
0,700
31,4
31,4
0,480
29,2
51,4
0,340
14,7
58,6
0,30 мм с 0,70 мм**
0,700
37,1
37,1
0,440
34,1
58,6
0,30 мм с 0,70 мм**
0,700
58,6
58,6
0,35 мм с 0,70 мм*
0,700
32,9
32,9
0,470
27,7
51,4
0,50 мм с 0,70 мм**
0,700
32,9
32,9
* - при прокатке на эмульсоле «Универсал» или близком ему по трибологическим свойствам.
** - при прокатке на эмульсоле «Quakerol» или близком ему по трибологическим свойствам.
Примечание:
1. Допускается перераспределение обжатий и натяжений по проходам
до 5%.
2. Скорость прокатки и температура полосы на выходе из клети не должны превышать 8 м/с и 100 оС соответственно.
3. В случае наличия на полосе окисленных участков после простоя на АРО-1, 2 или АОО-1А, прокатку осуществлять за 2-3 прохода.
4. Усилие прокатки не должно превышать 20000 кН.
5.5.2 Измерение толщины прокатываемой полосы производится автоматически бесконтактными толщиномерами. Запись показаний толщиномеров на двадцативалковых станах ведётся на диаграммную ленту, на стане «1200-4» запись осуществляется в электронном виде на два жёстких диска, расположенных на сервере в помещении систем автоматики и управления стана. Проверку правильности показаний толщиномеров производят в соответствии с требованиями ИЭ 48576703-013-006 не менее трёх раз в смену и не менее одного раза из них – в присутствии дежурного радиоизотопной лаборатории, который вносит результаты проверки в производственный журнал.
5.5.3 Прокатка при неисправной САРТ запрещается. Для настройки САРТ допускается прокатка отдельных полос с составлением акта и записью в производственном журнале и паспорте стендовой партии.
5.5.4 В процессе прокатки старший вальцовщик постоянно контролирует качество поверхности и плоскостность полосы: при прокатке на пониженной скорости и при перемотке на выходном участке стана – визуально, при прокатке на стане «1200-4» плоскостность полосы контролируется постоянно по показаниям стрессометрического ролика на главном посту управления. Старший вальцовщик тщательно осматривает поверхности полосы и валков после каждого обрыва полосы.
5.5.5 В процессе прокатки необходимо обеспечить:
- продольную и поперечную разнотолщинность - не более ½ суммы предельных отклонений по толщине, указанных в п.5.6.2 настоящей инструкции;
- отсутствие остаточной кривизны;
- отсутствие местной коробоватости (при её проявлении в паспорте стендовой партии делают отметку «местная коробоватость» с указанием места расположения дефекта по ширине полосы).
- на стане «1200-4» разность вытяжек по ширине полосы в диапазоне ±20 I-Unit (±0,2 мм/м);
Разность вытяжек по ширине полосы на стане 1200-4 контролируется по показаниям стрессометрического ролика. Остальные параметры измеряются в соответствии с ГОСТ 26877.
При прокатке рулонов с окисленными участками полосы в случае отслоения последние не прокатывают, а вырезают на АПР-8.
5.5.6 В качестве технологической смазки при прокатке на станах «1200-1,2» используют масло ТМС-6, или Укринол-207 соответствующие требованиям ТУ 0258-023-34686523.
Проверку масел на загрязненность производят три раза в неделю. Допускается загрязненность технологической смазки механическими примесями до 200 мг/л.
В качестве технологической смазки при холодной прокатке на стане «1200-4» используют водную эмульсию на основе эмульсола «Универсал ТС» соответствующую требованиям ТУ 0258-001-45846757-01 или «Quakerol VIZ 2.0». Эмульсия должна отвечать следующим требованиям:
- рН 7-9;
- содержание эмульсола от 2% до 8%;
- механические примеси в эмульсии до 100 мг/л;
- содержание неэмульгированных масел до 1%.
Проверку масел и эмульсии совершают в утреннюю смену. Отбор проб, их доставку в ГХИ ЦЗЛ и передачу результатов анализа начальнику ПУ ЦХП осуществляют специалисты механической службы ЦТОиР. Пробы эмульсии отбирают пять раз в неделю. Анализ проб проводят специалисты ГХИ ЦЗЛ руководствуясь требованиями МВИ Х-29/04-09 и МВИ Х-29/04-10. Полученные результаты анализа лаборант химического анализа записывает в журнал «Результаты анализа масел».
Диапазон изменения температуры эмульсии в процессе прокатки от 40°С до 60°С. Температура эмульсии поддерживается автоматически системой управления стана «1200-4».
5.5.7 Профилировку и перевалку прокатных валков станов «1200-1,2» производят согласно ИЭ 48576703-013-004.
Профилировку рабочих валков для стана «1200-4» выполняют с непрерывно изменяемой кривизной (CVC), с выпуклой бочкой и с цилиндрической бочкой (по указанию старшего мастера ПУ ЦХП). Рабочие валки должны иметь чистоту обработки поверхности с показателем Ra не более 0,32 мкм, опорные – Ra не более 1,25 мкм. Чистота обработки поверхностей валков контролируется в соответствии с ИЭ 48576703-013-004. Количество прокатываемого металла между перевалками рабочих и опорных валков для стана «1200-4» (т):
- Рабочие – 250÷270 – на один проход (цикл);
- Опорные – 8000÷8500 – на один проход (цикл).
Перевалку производят в той смене, в которой количество прокатанного металла достигло нижней границы указанных интервалов. Внеплановые перевалки производят при травмировании в процессе прокатки рабочей поверхности валков (выкрошки, порезы, надавы, и т.п.), а также при их аварийных отказах (отслоение, поломка бочки, шейки).
5.5.8 После перевалки или простоя стана прокатку начинают на предварительно подогретых валках. На двадцативалковых станах подогрев рабочих и опорных валков производят в течение 3-5 минут прокатным маслом, подогретым до 40 + 5°С, подаваемой на пирамиду валков. На стане «1200-4» подогрев валков осуществляют прокаткой первого рулона в 1-2-х проходах на малой скорости (2-3 м/с).
5.5.9 Прокатанный рулон должен отвечать следующим требованиям:
- обвязка и маркировка на внешнем витке;
- ровная и плотная смотка, допускаются выступающие витки до 100 мм в местах подмоток и до 20 мм в остальных местах;
- телескопичность не более 40 мм;
- предельные отклонения полосы по толщине не должны превышать норм для нормальной точности (исключая утолщенные концы), установленных ГОСТ 21427.2-83 и СТО 05757665-008-2007; допускаются выпады по толщине в районе сварных швов и на участках полос с дефектами по металлу;
- местная волнистость (елочка) не допускается, за исключением участков длиной до 50 м от мест расположения дефектов и от концов полосы;
- допускается коробоватость до 6 мм, волнистость по кромкам до 4 мм.
Примечание: коробоватость и волнистость контролируют при нанесении термоизоляционного покрытия в соответствии с требованиями п.5.7.2 настоящей инструкции.
Подготовка рулонов после второй холодной прокатки
5.6.1 При подготовке рулонов производят вырезку участков полосы с дефектами и толщиной не соответствующими НД, сварку полосы в соответствии с ТИ 13.18.
5.6.2 Допустимые отклонения по толщине составляют: для толщин полос 0,23-0,30 мм – не более + 0,02 мм; для 0,35-0,50 мм – не более + 0,03 мм. Среднюю фактическую толщину при необходимости определяют в соответствии с таблицей Приложения Ж.
5.6.3 Подготовка рулона:
5.6.3.1 На концах рулона обрезают участки длиной 300-400 мм (только мятое от дорна);
5.6.3.2 В середине рулона вырезают участки полосы с выпадами на толстое более допусков по п.5.6.2 настоящей инструкции, выпады по толщине на тонкое не вырезают;
5.6.3.3 Подготовку концов полосы под сварку производят по допускам в соответствии с требованиями п.5.6.2 настоящей инструкции.
5.6.3.4 Дефекты по длине полосы:
- единичные кромочные глубиной ≤ 12мм – вырубают одиночным заходом штампа;
- множественные кромочные дефекты глубиной ≤ 12мм, кромочные дефекты глубиной >12мм, а также, дефекты по ширине полосы – вырезают дефектный участок с последующей сваркой полосы на сварочной машине.
5.6.4 Рулон после подготовки должен отвечать следующим требованиям:
- масса - не более 9,8 т, при необходимости рулоны переформировывают внутри стендовой партии;
- состоять из единой сваренной полосы без подмоток;
- обвязан обручкой с замком и замаркирован на внешнем витке;
- ровно и плотно смотан, допускаются отдельные выступающие витки до 10 мм у сварных швов, телескопичность не более 40 мм;
- места сварных швов должны быть отмечены закладками;
- осевое смещение сваренных полос не допускается, контролируется визуально;
- рванины, единичные дыры, замятая кромка, ржавчина и другие явные дефекты не допускаются.
|
|
Организация стока поверхностных вод: Наибольшее количество влаги на земном шаре испаряется с поверхности морей и океанов (88‰)...
Двойное оплодотворение у цветковых растений: Оплодотворение - это процесс слияния мужской и женской половых клеток с образованием зиготы...
Индивидуальные и групповые автопоилки: для животных. Схемы и конструкции...
Поперечные профили набережных и береговой полосы: На городских территориях берегоукрепление проектируют с учетом технических и экономических требований, но особое значение придают эстетическим...
© cyberpedia.su 2017-2024 - Не является автором материалов. Исключительное право сохранено за автором текста.
Если вы не хотите, чтобы данный материал был у нас на сайте, перейдите по ссылке: Нарушение авторских прав. Мы поможем в написании вашей работы!